【温馨提示】 购买原稿文件请充值后自助下载。
[全部文件] 那张截图中的文件为本资料所有内容,下载后即可获得。
预览截图请勿抄袭,原稿文件完整清晰,无水印,可编辑。
有疑问可以咨询QQ:414951605或1304139763
低速载货汽车变速器的设计
摘 要:课题来源于生产实际,依据《机动车安全技术条件》和《汽车机械变速器总成技术条件》,针对低速载货汽车的运行特点而设计。参与了汽车的总体设计,确定了汽车的质量参数,选择了合适的发动机,并且计算出汽车的最高速度。
关于变速器的设计,首先选择标准的齿轮模数,在总档位和一档速比确定后,合理分配变速器各档位的速比,接着计算出齿轮参数和中心距,并对齿轮进行强度验算,确定了齿轮的结构与尺寸,绘制出所有齿轮的零件图。根据经验公式初步计算出轴的尺寸,然后对每个档位下轴的刚度和强度进行验算,确定出轴的结构和尺寸,绘制出各根轴的零件图。根据结构布置和参考同类车型的相应轴承后,按国家标准选择合适的轴承,然后对轴承进行使用寿命的验算,最终完成了变速器的零件图和装配图的绘制。
此变速器的齿轮都为标准齿轮,档位数和传动比与发动机参数匹配,保证了汽车具有良好的动力性和经济性。该变速器具有操纵简单、方便、传动效率高、制造容易、成本低廉、维修方便的特点,适合低速载货汽车的使用。
关键词:低速载货汽车;变速器;设计
Design The Transmission of Low-speed Truck
Abstract: The topic comes from the production reality, which is based on the safety specifications for power driven vehicles operating on roads and the specifications for the automobile mechanical transmission. It designs the low-speed truck’s movement characteristic. The automobile quality parameters are determined, according to the automobile system design, choosing the appropriate engine, and calculating the maximum speed.
When design the transmission, first, we choose the standard gear modulus and determine all speed’s proportions after we choose the number of the transmission’s gears and the first gear, then calculate the gear’s parameter and the center distance, and the gear needs the intensity checking calculation. We determine gear’s structure, then complete drawing of the gears’ component. According to the empirical formula, we preliminary carry on the checking calculation to each gear’s rigidity and the intensity to determine the axis’ structure and size, and thus draw up various axis’ component drawing. After arranged structure and compared with the similar type of vehicle’s bearing, according to the national standard, we select the appropriate bearings, and then calculate the service life of the bearings. Finally drawing of the component and the assembly of the transmission are completed.
Because the transmission gear is the standard gear and the number of gears and speed’s proportions match to the engine conditions, which ensure the necessary power and economy. This transmission has many merits of simple operation, efficient, easy manufacturing, low cost, and convenient.
Key words: Low-speed Truck;Transmission;Design目 录
1 前言 1
2 低速载货汽车主要参数的确定 3
2.1 质量参数的确定 3
2.2 发动机的选型 3
2.3 车速的确定 4
3 变速器的设计与计算 6
3.1 设计方案的确定 6
3.1.1 两轴式 6
3.1.2 三轴式 6
3.1.3 液力机械式 6
3.1.4 确定方案 6
3.2 零部件的结构分析 7
3.3 基本参数的确定 8
3.3.1 变速器的档位数和传动比 8
3.3.2 中心距 10
3.3.3 变速器的轴向尺寸 11
3.3.4 齿轮参数 11
3.3.5 各档齿轮齿数的分配 14
3.4 齿轮的设计计算 16
3.4.1 几何尺寸计算 16
3.4.2 齿轮的材料及热处理 17
3.4.3 齿轮的弯曲强度 17
3.4.4 齿轮的接触强度 18
3.5 轴的设计与轴承的选择 21
3.5.1 轴的设计 21
3.5.2 轴承的选择 33
4 结论 40
参 考 文 献 41
致 谢 42
1 前言
低速载货汽车是一种特殊的货车,特殊在于它以前叫农用运输车,GB7258-2004[1]将“四轮农用运输车”更名为“低速货车”,明确“农用运输车”实质上是汽车的一类。GB18320-2001[2]规定以柴油机为动力装置,中小吨位、中低速度,从事道路运输的机动车辆,包括三轮农用运输车和四轮农用运输车等,但不包括轮式拖拉机车组、手扶拖拉机车组和手扶变型运输机。农用运输车最高设计车速不大于70km/h,最大设计总质量不大于4500kg,长小于6m、宽不大于2m和高不大于2.5m。
我国农用运输车诞生于20世纪80年代初。我国农村运输的特点是运量小、运距短、货物分散、道路条件差。由于同吨位的柴油车较汽油车运载能力强,燃油价格低,且柴油保管无须特殊设备,又为广大农民所熟悉,所以,农用运输车均选用柴油机为动力。农用运输车的载质量一般不超过1.5t。当前四轮农用
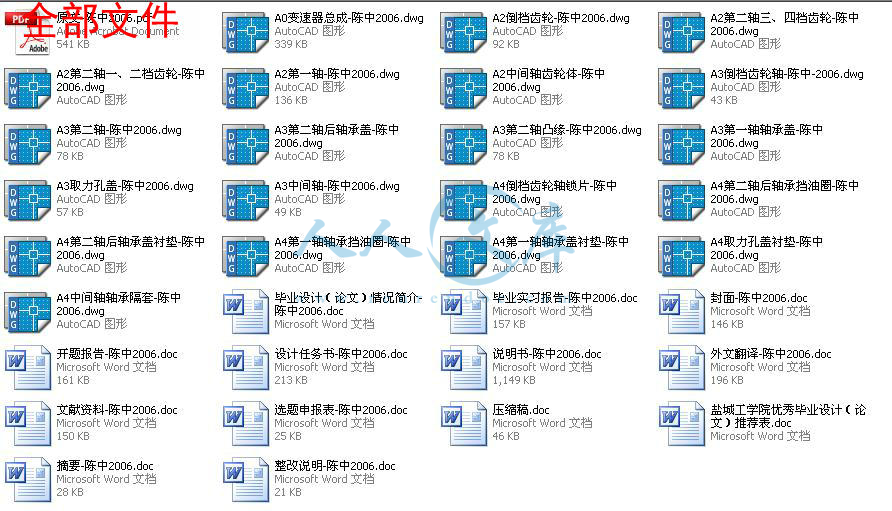



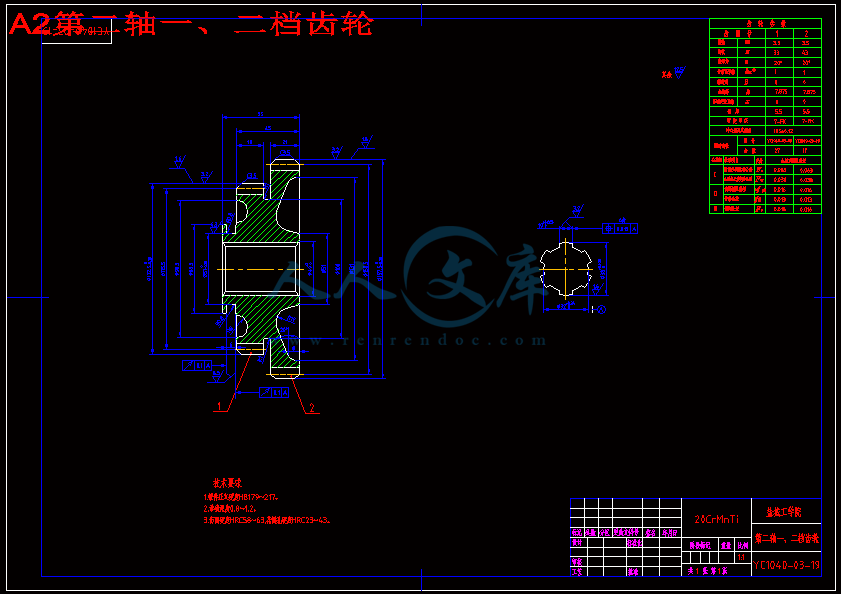




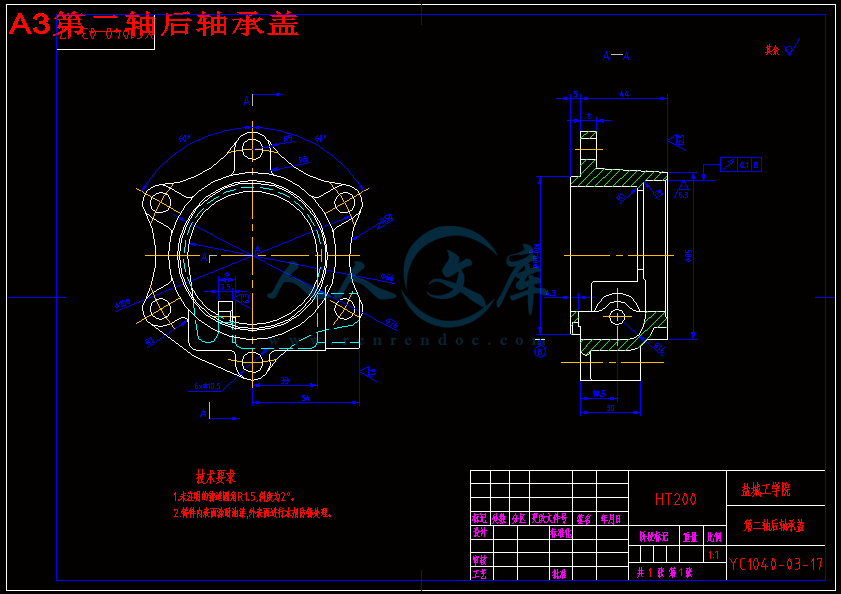