基于ProE及ANSYS的轻型载货汽车车架结构设计与静力学分析
30页 9000字数+说明书+任务书+开题报告+6张CAD图纸【详情如下】
中梁.dwg
任务书.doc
前横梁.dwg
发动机后悬置横梁.dwg
基于ProE及ANSYS的轻型载货汽车车架结构设计与静力学分析开题报告.doc
基于ProE及ANSYS的轻型载货汽车车架结构设计与静力学分析说明书.doc
导师指导记录.doc
开题报告封皮.doc
横纵梁联接件.dwg
装配图.dwg
说明书封皮.doc
过程管理材料.doc
过程管理材料封皮.doc
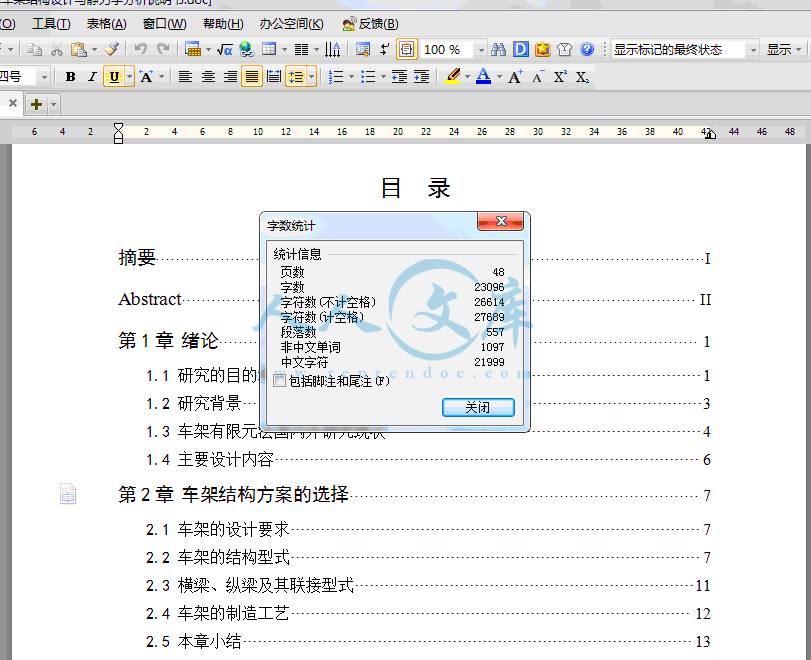
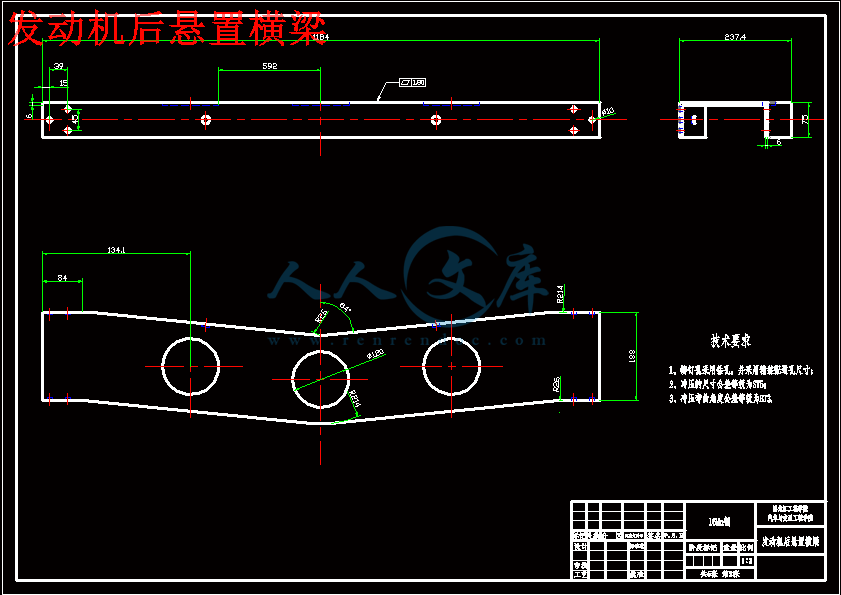

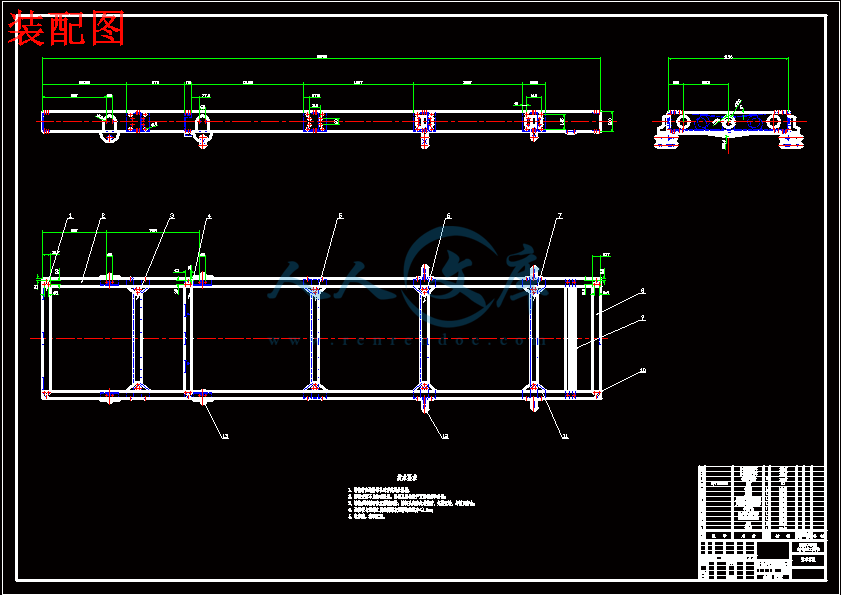


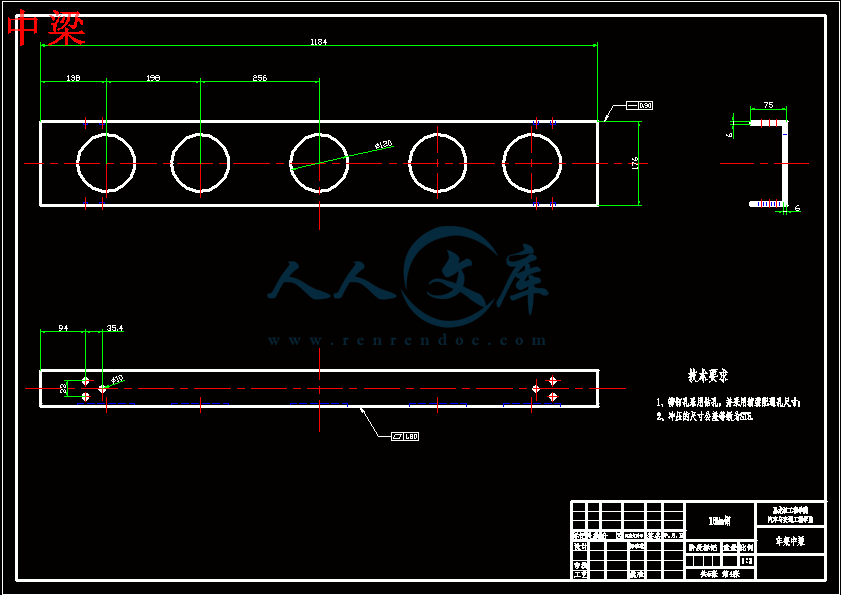
摘 要
车架工作状态比较复杂,无法用简单的数学方法对其进行准确的分析计算,而采用有限元方法可以对车架的静动态特性进行较为准确的分析,从而使车架设计从经验设计进入到科学设计阶段。
首先确定轻型货车的总体布置形式,在此基础上选择各总成的相关参数。然后初选车架横、纵梁的尺寸参数,运用材料力学对车架进行强度与刚度校核。经过优化完成对车架的结构设计。
其次,运用Pro/E软件建立车架三维模型。在满足结构力学特征的前提下,对车架结构进行了保留主要承载横梁的简化。
最后,使用有限元分析软件ANSYS 12.0从弯曲和扭转两大方向对车架进行强度、刚度分析。结合车架工作实际,对其进行了满载、前侧偏载、单侧偏载和单侧扭转、双侧扭转等工况的分析及对比,保证了车架结构满足实际使用要求。
关键词:车架;Pro/E;ANSYS;强度;刚度
ABSTRACT
In addition, the work condition of carrier car is extremely bad, and stress condition is also complex, it is unable to use simple mathematical method for accurate analysis of the calculation, and the finite element method can be used to analyze the static and dynamic performance of the frame more accurately, so that the design of frame will go from the experience design into the scientific design stage.
Firstly, the overall layout of LGV is determined, on this basis, selected parameters of every assembly. Then beams and stringers’ dimensions of the frame are selected, the strength and stiffness on the frame are checked by Mechanics of Materials. After all, the frame is designed after feedback.
Secondly, the 3D model is created used Pro/E. In faithful of the structure’s mechanical characteristics, it is necessary to simplify the geometry.
Finally, on two directions of the bending and the reverse to analyze the strength and stiffness on the frame used ANSYS 12.0. With the frame’s actual work characteristics, the frame is analyzed under the full, the front side of the partial load, the unilateral partial load and the unilateral reverse, the reverse sides conditions, guarantee the frame structure meet the mechanical requirements.
Key words:Frame; Pro/E; ANASYS ; Strength; Stiffne
目 录
摘要I
AbstractII
第 1 章 绪论1
1.1 研究的目的和意义1
1.2 研究背景3
1.3 车架有限元法国内外研究现状4
1.4 主要设计内容6
第 2 章 车架结构方案的选择7
2.1 车架的设计要求7
2.2 车架的结构型式7
2.3 横梁、纵梁及其联接型式11
2.4 车架的制造工艺12
2.5 本章小结13
第 3 章 车架的结构设计14
3.1 车架横、纵梁设计14
3.2 车架的弯矩及弯曲应力计算15
3.3 车架的挠度计算18
3.4 纵梁钢板弹簧跨度计算19
3.5 本章小结20
第 4 章 车架三维模型的建立21
4.1 Pro/E软件介绍21
4.2 三维模型的建立22
4.3 本章小结25
第 5 章 车架静态有限元分析26
5.1 有限元概述26
5.2 ANSYS Workbench 12.0概述30
5.3 车架有限元模型的建立32
5.4 车架弯曲工况分析34
5.4.1 满载工况分析34
5.4.2 前侧偏载工况分析35
5.4.3 单侧偏载工况分析36
5.5 局部分析37
5.6 车架扭转工况分析38
5.6.1 单侧扭转工况分析38
5.6.2 双侧扭转工况分析40
5.7 各工况分析结果总结41
5.8 本章小结41
结论42
参考文献43
致谢44
研究的目的和意义
在汽车制造市场竞争日益激烈的今天,汽车制造技术越来越先进,作为载货汽车主要承载结构的车架,它们的质量和结构形式直接影响车身的寿命和整车性能,如动力性、经济性、操纵稳定性。汽车的轻量化,就是在保证汽车的强度和安全性能的前提下,尽可能地降低汽车的整备质量,从而提高汽车的动力性,减少燃料消耗,降低排气污染。实验证明,汽车质量降低一半,燃料消耗也会降低将近一半。当前,由于环保和节能的需要,汽车的轻量化已经成为世界汽车发展的潮流。轻量化是21世纪整车发展趋势之一,减轻汽车质量意味着节约了能源和材料。车辆设计中,在满足载货汽车运营中对车架的刚度、强度及工艺改造等因素要求的同时,应当尽可能减轻它们的质量和降低制造成本。
车架结构设计的主要目的在于确保车架强度、刚度和动态性能的前提下,减轻车架的质量,由此不仅可以减少钢材和燃油的消耗,减少污染排放,提高车速,改善汽车起动和制动性能,而且可有效减少振动和噪声,增加汽车和公路使用寿命。但我国的汽车工业存在自己的特殊性:一是引进国外设计,国产化生产;二是仿制或改装设计,自己独立开发设计的新产品很少。国内许多厂家在载货汽车的设计、制造和改进过程中仍主要依靠和沿用传统的手工设计方法和设计理念,从而造成产品存在缺陷或结构设计的不合理,目前国产载货汽车普遍存在的问题是整车协调性较差;局部材料强度余量较大,无法预先判断,造成材料的浪费;在车辆实际使用过程中出现局部强度不足。所以,产品国产化或改装后,在使用过程中往往会出现强度、寿命、振动、噪声等方面的问题。这些问题影响了我国载货汽车产品质量,造成了使用中的安全隐患。由于缺乏必要的理论分析,我国载货汽车制造厂家对有问题的区域往往采取局部加强的方法,这不但需要进行多次全面的实车试验才能确定其有效性,而且会导致整车整备质量的不断增加。另外,对一些结构上的改进和优化,由于缺少一定的理论依据,往往得不到很好的实施,因此开展载货汽车车架结构强度的计算工作,在满足结构强度和刚度的前提下,合理地进行结构设计,以达到轻量化的目的、对车架结构设计具有重要意义。此外,为了加速企业的新产品开发,进一步提高产品的性能和科技含量,必须对现有的车型进行结构强度、刚度分析计算和动态特性分析研究工作,为新车型的研制开发提供借鉴和校核方法[1]。随着经济全球化进程的加快,汽车工业的竞争日益加剧,汽车巨头们都在加紧新车型的设计开发,由于发动机、底盘设计制造技术基本成熟,新车型便主要体现在电子设备和车架造型的更新上。同时,为减少新车型的开发成本、缩短新车型的开发周期、提高新产品的市场竞争力,全球各大汽车公司普遍实施了“平台战略”,车架的开发便是该战略的主要组成部分。 作为载货汽车重要组成部分的车架,应有足够的弯曲刚度,以使装在其上的有关机构之间的相对位置在汽车行驶过程中保持不变并使车身的变形最小;也应有足够的强度,以保证其有足够的可靠性与寿命,纵梁等主要零件在使用期内不应有严重的变形和开裂。本设计就是在此要求下进行的,具体结论如下:
1、通过对车架的多种结构型式、横纵梁联接型式和车架的制造工艺分析对比,完成轻型货车车架的设计,并对其进行了校核。经过强度与刚度校核,车架能够满足设计要求;
2、根据设计数据运用Pro/E软件创建车架三维模型时,为了下一步的网格划分对其结构进行了简化。尽管这样会使分析结果与实际情况存在一定的偏差,但并不影响总体目标的实现;
3、通过弯曲工况的满载工况、前侧偏载工况、单侧偏载工况和扭转工况的单侧扭转工况、双侧扭转工况五种工况对车架有限元模型进行静力分析。根据应变和应力两个指标对设计车架的力学性能进行评判,进一步保证了车架满足实际使用要求。
综上所述,设计完成的车架能够达到预期的承载要求。但是,轻量化是车架设计中必须要考虑的问题,本设计缺少对车架结构轻量化的研究。下一步可以考虑在静态分析的基础上,适当改变横梁及横纵梁联接件结构,经过反复修改、分析,最终达到车架轻量化德目的。
参考文献
[1]杨忠敏.探现代汽车的材料及其轻量化技术[ J].汽车研究与开发,2003,6:51-55.
[2]李波.某载货车车架结构分析与优化设计[D].合肥工业大学硕士学位论文,2009.
[3]叶勤.轻型载货汽车车架有限元分析与优化[D].武汉理工大学硕士学位论文,2007.
[4]靳福来.汽车轻量化技术现状[J].汽车技术,1995,7:56—58.
[5]华润兰.论汽车轻量化[J].汽车工程,1994,209(6):375—383.
[6]刘惟信.汽车设计[M].北京.清华大学出版社,2001.
[7]成大先.机械设计手册[M].化工工业出版社,2001.
[8]杨中明.EQ1040型汽车架结构性能研究[D].华中科技大学硕士学位论文,2005.
[9]西南交通大学应用力学与工程系.工程力学教程[M].高等教育出版社,2004.
[10]于志伟,李明.Pro/ENGINEER完全手册[M].人民邮电出版社,2007.
[11]大久保信行.机械模态分析[M].尹传家译.上海交通大学出版社,2001.
[12]浦广益.ANSYS Workbench 12.0基础教程和实例详解[M].中国水利水电出版社,2010.
[13]宋允祁,王中亭.解放CA1040系列轻型货车构造与维修[M].吉林科学技术出版社,1995.
[14]黄贵东,沈光烈.汽车车架有限元分析模型的改进与应用[J].装备制造技术,2007.
[15]曲昌荣,郝玉莲,戚洪涛.汽车车架的有限元分析[J].轻型汽车技术,2008.
[16]刘新田,黄虎,刘长虹,郭辉,范平清.基于有限元的汽车车架静态分析[J].上海工程技术大学学报,2007.
[17]冯宝林,赵韩,董晓慧.基于参数化有限元分析的某客货两用汽车车架的改型研究[J].农业工程学报,2008.
[18]钟佩思,孙雪颜,赵丹,魏群,苏超.基于ANSYS的货车车架的有限元静态分析[J].拖拉机与农用运输车,2008.
[19]Burnett, David S. Finite element analysis. Addison-Wesley Pub[J].1987.
[20]Eilabu, Zahavi. The Finite Element Method in machine design[J]. New jersey Prentice—Hall, 1992.
[21]Cheng z Q et a1. Experience in Reverse-engineering of a Finite Element Automobile Crash Model[J]. Finite Elements in Analysis and Design,2001(37).