QTZ125塔式起重机总体 臂架、变幅机构设计(63m吊臂)【全套CAD图纸+WORD毕业论文】【工程机械】
收藏
资源目录
压缩包内文档预览:
编号:395874
类型:共享资源
大小:16.39MB
格式:RAR
上传时间:2015-01-14
上传人:好资料QQ****51605
认证信息
个人认证
孙**(实名认证)
江苏
IP属地:江苏
45
积分
- 关 键 词:
-
qtz125
塔式起重机
总体
整体
臂架
机构
设计
63
吊臂
全套
cad
图纸
word
毕业论文
工程机械
- 资源描述:
-
【温馨提示】 购买原稿文件请充值后自助下载。
[全部文件] 那张截图中的文件为本资料所有内容,下载后即可获得。
预览截图请勿抄袭,原稿文件完整清晰,无水印,可编辑。
有疑问可以咨询QQ:414951605或1304139763
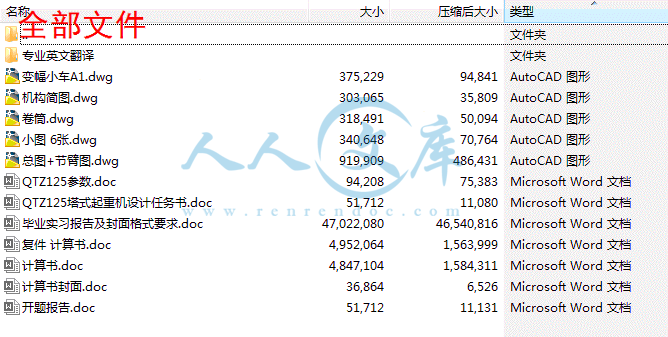
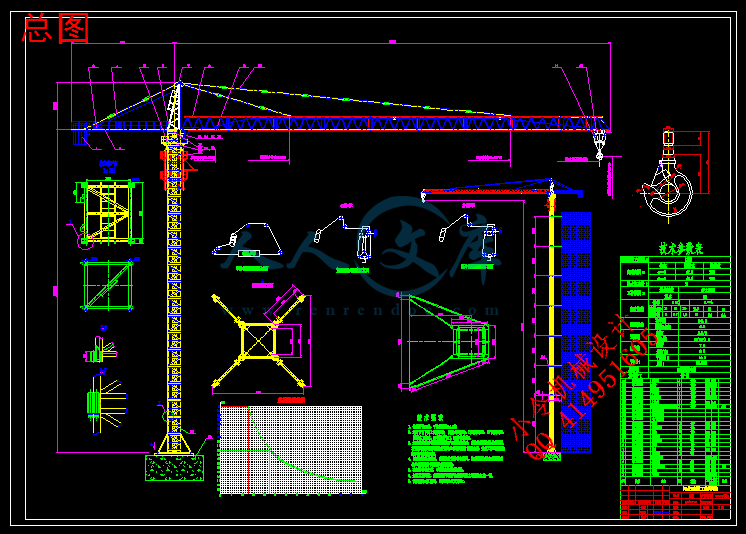


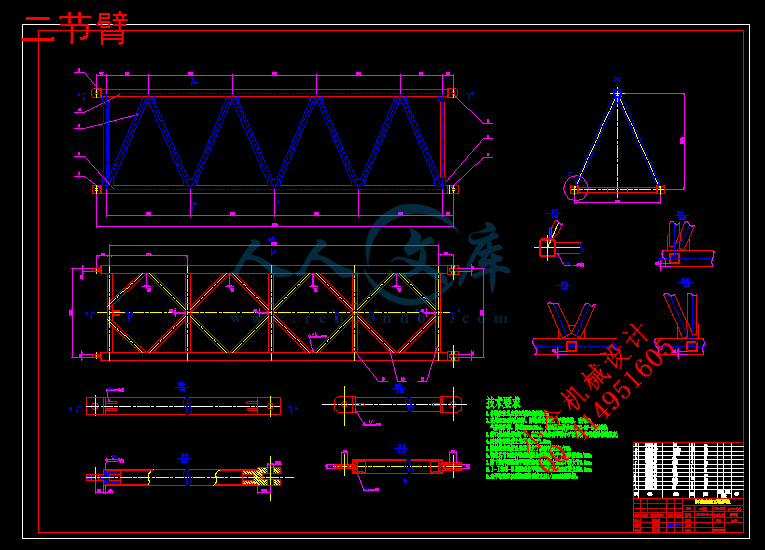

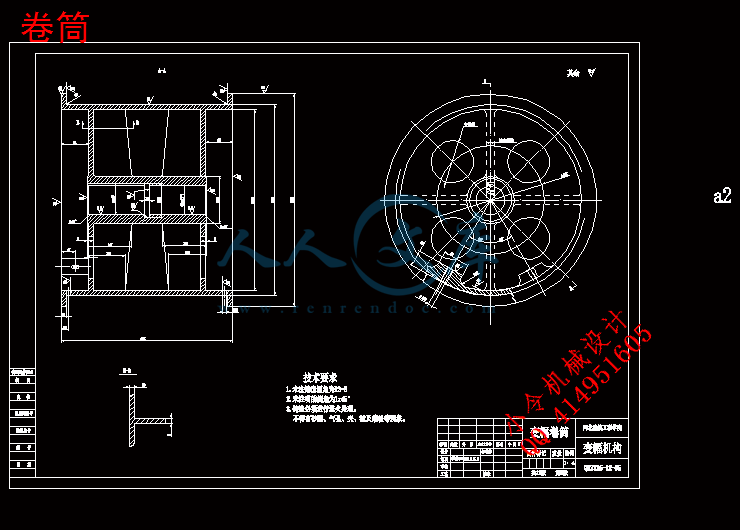
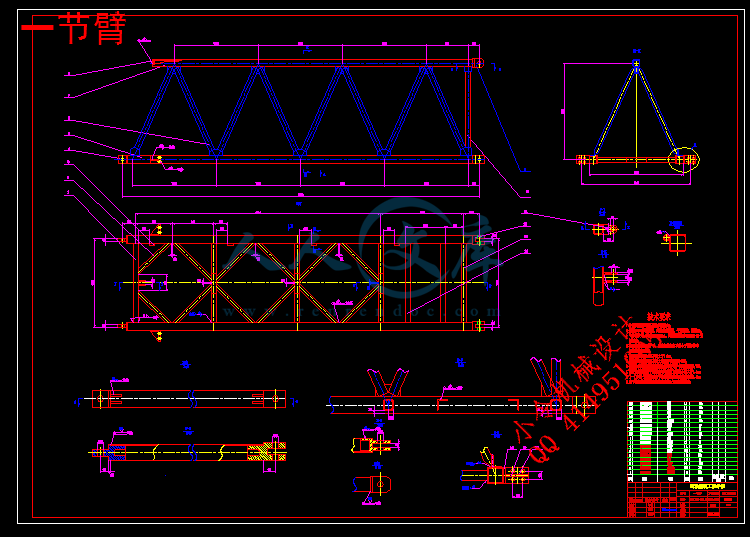
1、毕业设计(论文)目的:
本次毕业设计是对机械专业学生在毕业前的一次全面训练,目的在于巩固自己所学知识并把所学知识运用到实际设计当中,真正明白知识如何应用。训练学生综合运用所学知识分析和解决问题的能力。将所学知识应用与实际培养独立工作能力。毕业设计要求每个学生在工作过程中,要独立思考,刻苦钻研,有所创新、解决相关技术问题。通过毕业设计,使学生掌握塔式起重机的总体设计、塔身的设计、整体稳定性计算等内容,为今后步入社会、走上工作岗位打下良好的基础。
2、毕业设计(论文)任务内容和要求(包括原始数据、技术要求、工作要求等):
(1)设计任务:
①总体参数的选择(QTZ125级别)
②结构形式
(2)总体设计
①主要技术参数性能
②设计原则
③平衡重的计算
④塔机的风力计算
⑤整机倾翻稳定性的计算
(3)变幅机构的设计和计算
① 建立变幅机构的数学模型
② 钢丝绳的选择和校核
③ 卷筒的设计和绕绳系统的计算
④ 验算实际变幅速度
⑤ 电动机的选择
⑥ 蜗轮蜗杆减速器的设计
(4) 臂架的设计和计算
① 分析单双吊点的优缺点
② 吊点位置的选择
③ 臂架结构参数选择
④ 臂架主参数选择与计算
(5)变幅的设计和计算
(6) 要求
① 主要任务:学生应在指导教师指导下独立完成一项给定的设计任务,编写符合要求的设计说明书,并正确绘制机械与电气工程图纸,独立撰写一份2500~~3500字毕业设计小论文,并绘制有关图表。
② 知识要求:学生在毕业设计工作中,应综合运用多学科的理论、知识与技能,分析与解决工程问题。通过学习、钻研与实践,深化理论认识、扩展知识领域、延伸专业技能。
③ 能力培养要求:学生应学会依据技术课题任务,完成资料的调研、收集、加工与整理,正确使用工具书;培养学生掌握有关工程设计的程序、方法与技术规范,提高工程设计计算、图纸绘制、编写技术文件的能力;培养学生掌握实验、测试等科学研究的基本方法;锻炼学生分析与解决工程实际问题的能力。
④ 综合素质要求:通过毕业设计,学生应掌握正确的设计思想;培养学生严肃认真的科学态度和严谨求实的工作作风;在工程设计中,应能树立正确的生产观、经济观与全局观。
⑤ 设计成果要求:
1)凡给定的设计内容,包括说明书、计算书、图纸等必须完整,不得有未完的部分,不应出现缺页、少图纸现象。
2)对设计的全部内容,包括设计计算、机械构造、工作原理、整机布置等,均有清晰的了解。对设计过程、计算步骤有明确的概念,能用图纸完整的表达机械结构与工艺要求,有比较熟练的认识图纸能力。对运输、安装、使用等亦有一般了解。
3)说明书、计算书内容要精练,表述要清楚,取材合理,取值合适,设计计算步骤正确,数学计算准确,各项说明要有依据,插图、表格及字迹均应工整、清楚、不得随意涂改。制图要符合机械机械制图标准,且清洁整齐。小论文要符合论文书写规范。
4)对国内外塔式起重机情况有一般的了解,对各种塔式起重机有一定的分析、比较能力。
其他各项应符合本资料有关部分提出的要求。
3、毕业设计(论文)成果要求(包括图表、实物等硬件要求):
① 计算说明书一份
内容包括:设计任务要求的选型、设计计算内容、毕业实习报告等。作到内容完整,论证充分(包括经济性论证),字迹清楚,插图和表格正规(分别进行统一编号)、批准,字数要求不少于2万字;撰写中英文摘要;提倡学生应用计算机进行设计、计算与绘图。
② 图纸一套
1)总图一张(0号)
2)变幅机构图一张(0号)
3)臂架图一张(0号)
4)零件图至少三张(2,3,4号)
③ 3000字左右的毕业设计小论文一篇
4、主要参考文献:
要求按国标GB 7714—87《文后参考文献著录规则》书写。
[1] 哈尔滨建筑工程学院主编.工程起重机.北京:中国建筑工业出版社
[2] 董刚、李建功主编.机械设计.机械工业出版社
[3] 机械设计手册.化学工业出版社(5册)
[4] GB/T9462—1999 塔式起重机技术条件
[5] GB/T13752—1992 塔式起重机设计规范
[6] GB5144—1994 塔式起重机安全规程
[7] 濮良贵、纪名刚主编.机械设计(第八版).高等教育出版社
目录
第一章 前言··················································································1
1.1塔式起重机概述············································································1
1.2塔式起重机的发展趋势····································································3
第二章 总体设计············································································4
2.1 概述························································································4
2.2 总体设计方案的确定······································································5
2.2.1金属结构·················································································5
2.2.2工作机构················································································25
2.3 总体设计原则············································································29
2.3.1 整机工作级别··········································································32
2.3.2 机构工作级别··········································································32
2.3.3 主要技术性能参数····································································32
2.4平衡臂与平衡重的计算···································································33
2.5起重特性曲线·············································································35
2.6塔机风力计算·············································································37
2.6.1工作工况Ⅰ············································································38
2.6.2工作工况Ⅱ·············································································42
2.6.3工作工况Ⅲ·············································································44
2.6.4非工作工况Ⅳ···········································································46
2.7整机的抗倾翻稳定性·····································································48
2.7.1工作工况Ⅰ·············································································49
2.7.2工作工况Ⅱ·············································································50
2.7.3非工作工况Ⅲ···········································································51
2.7.4工作工况Ⅳ·············································································51
第三章 塔身的设计计算·································································52
3.1塔身的总体模型···········································································52
3.2 塔身的受力分析及验算··································································53
3.2.1.塔身的受力分析·······································································53
3.2.2 塔身内力计算及组合··································································56
3.2.3 塔身整体稳定性和强度验算··························································59
第四章 变幅机构的设计和计算························································71
4.1变幅机构的形式··········································································71
4.2 确定卷筒尺寸············································································71
4.2.1 卷筒名义直径··········································································71
4.2.2 多层绕卷筒相关参数计算····························································72
4.3选择电动机、减速器、制动器、联轴器····················································72
4.3.1选择电动机·············································································72
4.3.2 选择减速器············································································73
4.3.3 变幅机构制动器的选择·······························································74
4.3.4变幅机构联轴器的选择································································75
4.4. 验算变幅速度···········································································77
4.5验算起、制动时间验算····································································77
4.6电动机发热校验···········································································79
4.7 校验卷筒强度············································································80
第五章 变幅小车的设计·······························································80
5.1 变幅小车的形式··········································································80
5.2 变幅小车的设计··········································································81
5.2.1 绳索牵引式小车构造及其驱动方式················································81
5.2.2运行小车牵引力计算···································································82
5.2.3 牵引绳最大张力·······································································85
5.2.4 选择牵引绳············································································86
5.2.5 牵引卷筒计算··········································································86
第六章 毕业设计小结····································································89
致谢····························································································90
参考书目·······················································································92
- 内容简介:
-
-
- 温馨提示:
1: 本站所有资源如无特殊说明,都需要本地电脑安装OFFICE2007和PDF阅读器。图纸软件为CAD,CAXA,PROE,UG,SolidWorks等.压缩文件请下载最新的WinRAR软件解压。
2: 本站的文档不包含任何第三方提供的附件图纸等,如果需要附件,请联系上传者。文件的所有权益归上传用户所有。
3.本站RAR压缩包中若带图纸,网页内容里面会有图纸预览,若没有图纸预览就没有图纸。
4. 未经权益所有人同意不得将文件中的内容挪作商业或盈利用途。
5. 人人文库网仅提供信息存储空间,仅对用户上传内容的表现方式做保护处理,对用户上传分享的文档内容本身不做任何修改或编辑,并不能对任何下载内容负责。
6. 下载文件中如有侵权或不适当内容,请与我们联系,我们立即纠正。
7. 本站不保证下载资源的准确性、安全性和完整性, 同时也不承担用户因使用这些下载资源对自己和他人造成任何形式的伤害或损失。

人人文库网所有资源均是用户自行上传分享,仅供网友学习交流,未经上传用户书面授权,请勿作他用。