【温馨提示】 购买原稿文件请充值后自助下载。
[全部文件] 那张截图中的文件为本资料所有内容,下载后即可获得。
预览截图请勿抄袭,原稿文件完整清晰,无水印,可编辑。
有疑问可以咨询QQ:414951605或1304139763
摘 要
现代汽车事业的发展日益壮大,使得人们对于汽车的要求越来越大,相对应的人们对于汽车的各个部分的要求也越来越大。然而随着,带来的安全问题也越来越引起人们的注意,而制动系统则是汽车主动安全的重要系统之一。从汽车诞生时起,车辆制动系统在车辆的安全方面就扮演着至关重要的角色。近年来,随着汽车保有量的增加,车辆技术的进步和汽车行驶速度的提高,这种重要性表现得越来越明显。因此,如何开发出高性能的制动系统,为安全行驶提供更高的保障。
本文在绪论中阐述了乘用车制动系统设计的目的和意义、发展状况以及应用前景。接着分析论证了制动系统设计的总体方案,对其鼓式制动器及盘式制动器的选取进行了详细说明论述。还包括制动主缸分路系统的选取方案分析和选择进行了分析。对制动系统及驱动机构进行了分析和计算,最后并对制动性能进行了计算表明制动性能满足要求。
关键词:制动;鼓式制动器;盘式制动器;制动主缸;管路布置
ABSTRACT
The development of modern automobile business growing, make people more and more the requirement for a car, corresponding people for the car parts of the requirements are increasingly large. However, with security problems, bring more and more is also arouse people's attention, and brake system is the important system car one of active safety. Born from cars, braking system plays in the vehicle's safety aspects will play a crucial role. In recent years, with the increase of auto possession, vehicle technology progress and vehicle speed increase, this importance played more and more apparent. Therefore, how to develop high-performance braking system for safe driving provide higher security.
This paper expounded in the introduction of passenger car brake system design of purpose and meaning, development situation and application prospect. Then the paper analysis the braking system design, the overall scheme of the drum brake disc brake and the selection of discussed a detailed illustration. Also includes braking monitor system, the selection of main cylinder scheme analysis and choice are analyzed. For brake system and driving mechanism is analyzed and calculated, the last of brake performance and the calculation shows that the braking performance meet the requirements.
Keywords: brake; Drum brake; Disc brakes; Braking main cyli;Pipeline layout
目 录
摘要 I
Abstract II
第1章 绪论 1
1.1 制动系统介绍 1
1.2 制动系统发展现状 2
1.3 制动系统设计的目的及意义 3
1.4 设计主要内容 4
第2章 设计方案的确定 5
2.1 制动器简介 5
2.1.1鼓式制动器介绍 5
2.1.2盘式制动器介绍 7
2.1.3制动器的选择 8
2.2 制动驱动机构 9
2.2.1简单制动系 9
2.2.2动力制动系 9
2.2.3伺服制动系 10
2.3 分路系统的形式选择 10
2.4 制动主缸的选取 12
2.5 本章小结 12
第3章 制动系统设计 14
3.1 设计主要参数 14
3.2 同步附着系数的选择 14
3.3 制动器有关计算 14
3.3.1确定前后轴制动力矩分配系数β 14
3.3.2 制动器制动力矩确定 15
3.3.3 后轮制动器的结构参数及摩擦系数的选取 15
3.3.4 前轮盘式制动器主要参数选定 16
3.4 制动器有关计算 17
3.5 制动器主要零部件的选定 18
3.5.1 制动盘选定 18
3.5.2 制动钳选定 18
3.5.3 制动块选定 18
3.5.4 摩擦材料选定 18
3.5.5 制动鼓选定 18
3.5.6 制动蹄选定 19
3.5.7 制动底板选定 19
3.5.8 制动蹄支承选定 19
3.5.9 制动轮缸选定 19
3.6 本章小结 20
第4章 制动驱动机构的设计计算 21
4.1 后轮制动轮缸直径与工作容积的设计计算 21
4.2 前轮盘式制动器驱动机构计算 21
4.3 制动主缸与工作容积设计计算 22
4.4 制动踏板力与踏板行程 23
4.4.1 制动踏板力 23
4.4.2 制动踏板行程 23
4.5 本章小结 24
第5章 制动性能分析及校核 25
5.1 概述 25
5.2 制动效能及制动性能评价指标 25
5.3 摩擦衬片的磨损计算 25
5.4 制动距离计算 27
5.5 制动减速度计算 27
5.6 驻车制动计算 28
结论 29
参考文献 30
致谢 31
附录 32
第1章 绪 论
1.1 制动系统介绍
汽车上用以使外界(主要是路面)在汽车某些部分(主要是车轮)施加一定的力,从而对其进行一定程度的强制制动的一系列专门装置统称为制动系统。汽车制动系是用以强制行驶中的汽车减速或停车、使下坡行驶的汽车车速保持稳定以及使已停驶的汽车在原地(包括在斜坡上)驻留不动的机构。对汽车起制动作用的只能是作用在汽车上且方向与汽车行驶方向相反的外力,而这些外力的大小都是随机的、不可控制的,因此汽车上必须装设一系列专门装置以实现上述功能。随着高速公路的迅速发展和车速的提高以及车流密度的日益增大,为了保证行车安全,汽车制动系的工作可靠性显得日益重要。也只有制动性能良好、制动系工作可靠的汽车,才能充分发挥其动力性能。汽车制动系至少应有两套独立的制动装置,即行车制动装置和驻车制动装置;重型汽车或经常在山区行驶的汽车要增设应急制动装置及辅助制动装置;牵引汽车应有自动制动装置。 行车制动装置用作强制行驶中的汽车减速或停车,并使汽车在下短坡时保持适当的稳定车速。其驱动机构常采用双回路或多回路结构,以保证其工作可靠。驻车制动装置用于使汽车可靠而无时间限制地停驻在一定位置甚至斜坡上,它也有助于汽车在坡路上起步。驻车制动装置应采用机械式驱动机构而不用液压或气压式的,以免其产生故障。应急制动装置用于当行车制动装置意外发生故障而失效时,则可利用
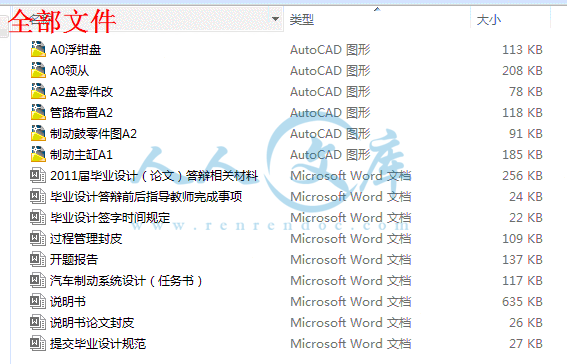
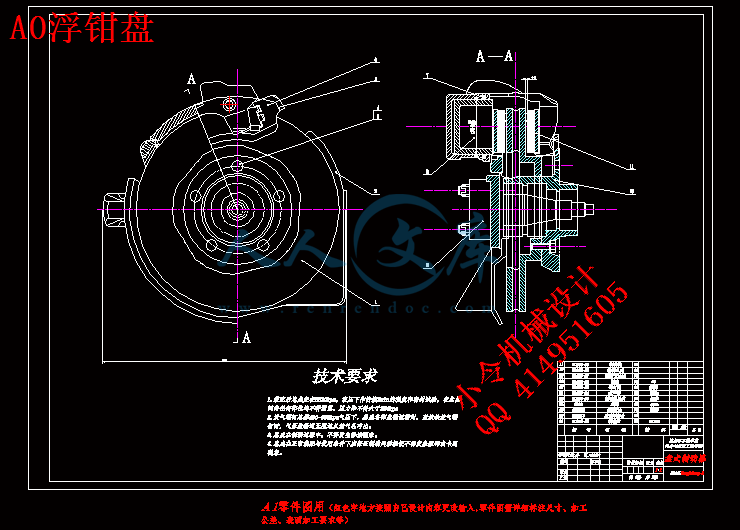
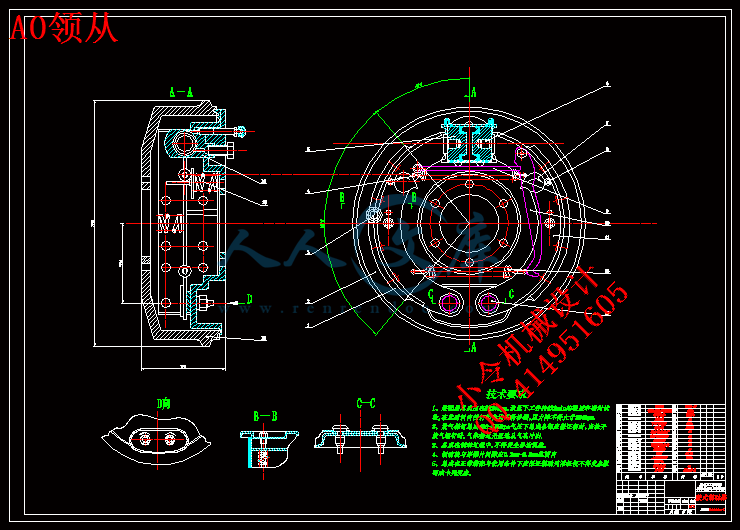



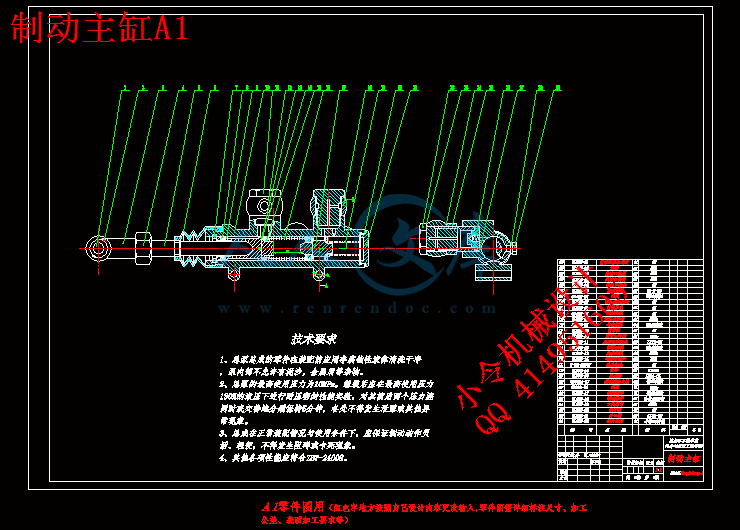
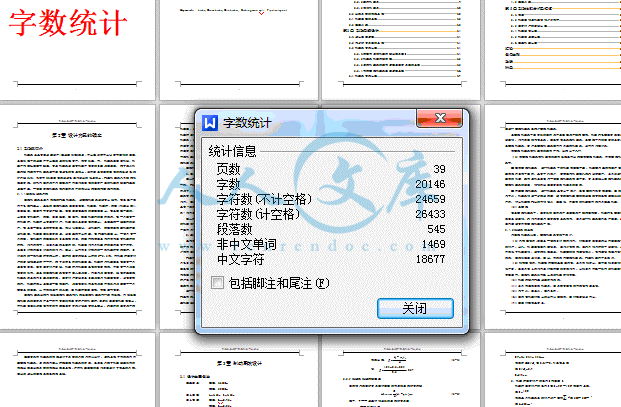