电话机外壳下盖注塑模具设计【17张CAD图纸+WORD毕业论文+PPT答辩稿】【斜顶抽芯】
收藏
资源目录
压缩包内文档预览:(预览前20页/共53页)
编号:408816
类型:共享资源
大小:1.57MB
格式:RAR
上传时间:2015-03-03
上传人:好资料QQ****51605
认证信息
个人认证
孙**(实名认证)
江苏
IP属地:江苏
45
积分
- 关 键 词:
-
电话机
外壳
注塑
设计
cad
图纸
word
毕业论文
模具
- 资源描述:
-
【温馨提示】 购买原稿文件请充值后自助下载。
[全部文件] 那张截图中的文件为本资料所有内容,下载后即可获得。
预览截图请勿抄袭,原稿文件完整清晰,无水印,可编辑。
有疑问可以咨询QQ:414951605或1304139763
摘 要:
分析了电话机外壳下盖的塑件工艺特点。介绍了电话机外壳下盖注射成型结构及模具的工作过程和电话机外壳下盖注射模具结构的设计方法。分析了模芯零件的选材、热处理、下盖的塑件的机构要素,塑件的尺寸公差和精度选择。此电话机外壳注射设计特点是:点浇口形式的双分型面的注射模,采用斜杆导滑的斜滑块分型抽芯机构。
关 键 字 :电话机外壳下盖;滑块; 注射模具
Abstract
Analyzed under the telephone outer covering to cover models the craft characteristic. Introduced under the telephone outer covering covers the injection to take shape the structure and the mold work process and under the telephone outer covering covers the injection mold structure the design method. Analyzed the mold core components selection, the heat treatment, under has covered models the organization essential factor, modelled the size common difference and the precision choice. This telephone outer covering injection design characteristic is: Runner form duplex profile injection mold,Uses the strut to lead the slippery slanting slide minute to pull out the core organization.
Keywords : Under the telephone outer covering covers; Slide; Injects the mold
目录
前言 2
第一章 塑件分析设计 3
第1.1节 塑料材料的选择 3
1.1.1选材依据 3
1.1.2 选材方法 4
1.1.3 材料选择 5
第1.2节 塑料制品的结构设计 5
1.2.1 塑件的尺寸精度与精度 5
1.2.2 表面质量 6
1.2.3 结构设计及工艺性 6
第二章 方案的选择 7
第三章 注射机的选择 9
第四章 注塑模设计 10
第4.1节 塑料制件在模具中的位置 11
4.1.1 型腔数的确定 11
4.1.2 分型面的选择 11
第4.2节 浇注系统和排溢系统的设计 12
4.2.1 主流道及主流道衬套 12
4.2.2 冷料井的设计 13
4.2.3 分流道设计 14
4.2.4 浇口的设计 15
4.2.5 排气系统的设计 16
第4.3节 成型零件的设计 17
4.3.1成型零件的结构设计 17
4.3.2 成型零件工作尺寸计算 18
4.3.3 型腔壁厚和底板厚度计算 21
第4.4节 侧向抽芯机构设计 22
4.4.1 抽芯距确定和抽拔力计算[3] 22
4.4.2斜推杆导滑的斜滑块分型抽芯机构设计 23
第4.5节 温度调节系统的设计 24
4.5.1 模温对塑件的影响 24
4.5.2、制品所需的成型周期的计算 24
4.5.3 冷却参数的计算 25
4.5.3 冷却回路设计 26
第4.6节 合模导向机构设计 26
4.6.1概述 26
4.6.2 导柱导向机构设计 27
4.6.3导套的设计要点 27
第4.7节 塑件脱模机构 28
4.7.1 脱模机构设计一般应遵循下述原则: 28
4.7.2 脱模力的计算 29
4.7.3推杆的设计 29
第4.8节 工艺参数的校核 30
4.8.1 最大注射量的校核 31
4.8.2 注射压力的校核 31
4.8.3 锁模力的校核 31
4.8.4 开模行程的校核 31
4.8.5 安装尺寸的校核 32
第五章 结 论 33
参考文献 33
致谢: 35
外文翻译 36
前言
塑料材料只有通过成型才能成为具有使用价值的各种制品,而塑料的成型一般通过模具来成型,因此在塑料生产过程中模具是必不可少的。塑料模具对实现成型工艺要求和塑件使用要求起着十分重要的作用。任何塑件的生产和更新换代都是以模具的制造和更新为前提的,由于目前工业和民用塑件的产量猛增,质量要求越来越高,因而导致了塑料模具研究、设计和制造技术的迅猛发展。
我国具工业从起步到飞跃发展,历经了半个多世纪,近几年来,我国模具技术有了很大发展,模具水平有了较大提高。大型、精密、复杂、高效和长寿命模具又上了新台阶。大型复杂冲模以汽车覆盖件具为代表,我国主要汽车模具企业,已能生产部分轿车覆盖件模具。
体现高水平制造技术的多工位级进模、覆盖面大增,已从电机、电铁芯片模具,扩大到接插件、电子零件、汽车零件、空调器散热片等家电零件模具上。塑料模已能生产34"、48"大展幕彩电塑壳模具,大容量洗衣机全套塑料模具及汽车保险杠和整体仪表板等塑料模具。
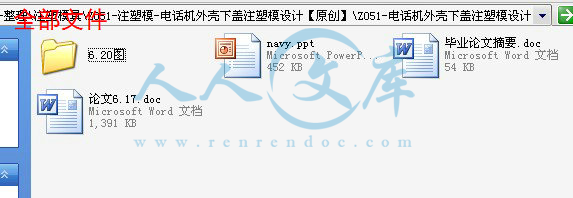
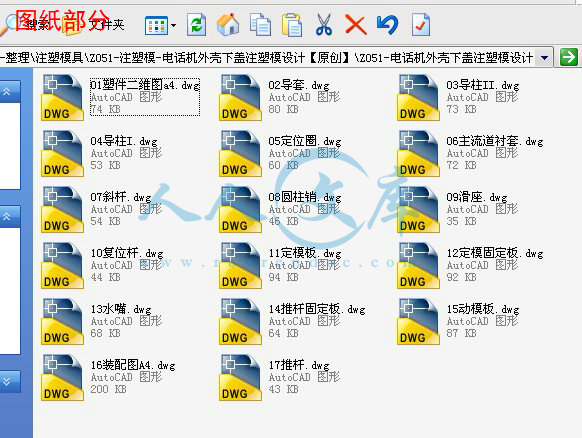

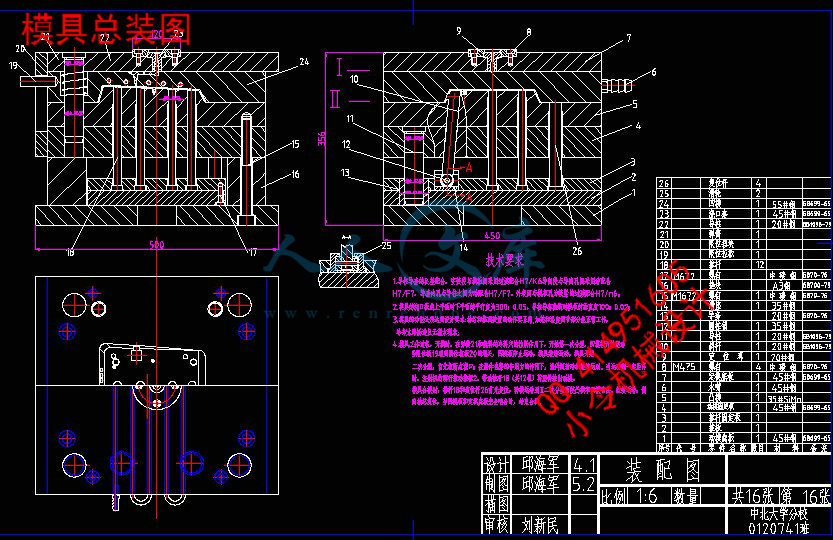
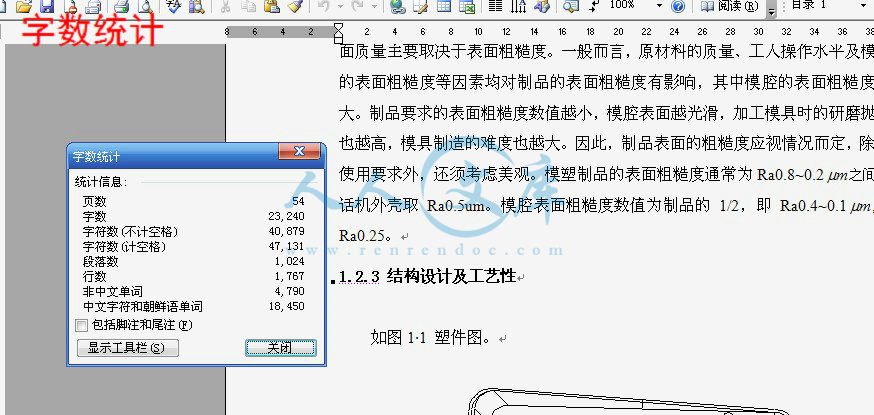
- 内容简介:
-
产品 电话机外壳下盖注射模具设计指导老师 刘新民设计人 邱海军 一 塑件分析二 方案的选择三 注塑机的选择四 模具示意图五 结束语六 致谢 一 塑件分析 产品I塑件图 1 塑件所需性能 使用要求 这里我们设计的塑料制件是电话机外壳下盖注射模的设计 属一般的室内用塑料件 对耐候性要求不高 需要有一定的刚度 并对制品表面的粗糙度也有一定要求 2 ABS的部分性能 1 A 丙烯腈 有高的良好的耐热和耐腐蚀性 B 丁二烯 很高的韧性和低温条件S 苯乙烯 使ABS具有良好的成型工艺性 刚性和着色性 2 ABS五毒 无味 密度为 1 02 1 08g cm 吸水性很小 1 3 使用温度范围为 40 110 力学性能优良 耐疲劳 冲击硬度好 4 化学性能稳定性好 耐酸 耐碱 耐盐的化学腐蚀 5 着色性良好 电缘性也很好 6 表面可以电镀 喷漆 印刷 绘画 二 方案的选择1 手动侧向分型机构这类机构操作不方便 工人劳动强度大 生产效率较低 抽拔力有限 但模具的结构比较简单 加工制造成本低 因此常用于产品的试制 小批量生产或无法采用其他侧向分型与抽芯机构的场合 2 液压 气压 侧向分型机构这类机构的主要特点是抽拔距离长 抽拔力大 动作灵活 不受开模过程限制 常在大型注射模具中使用 3 机动侧向分型抽芯机构这类机构虽然结构比较复杂 但分型与抽芯无需手工操作 生产效率高 经济性好 动作可靠 实用性强 其主要形式有 弹簧分型抽芯 斜销分型抽芯 弯销分型抽芯 斜滑块分型抽芯等 2 抽芯方案的确定为了提高经济性 我们采用机动侧向抽芯 由于电话机外壳的矩形孔抽拔距离短 抽拔力小 故本设计采用斜推杆导滑的斜滑块内侧抽芯 这种抽芯机构多用于抽拔力不大的场合 优点是它占位小 既可用于外侧抽芯 也可用于内侧抽芯 注射机的选择塑件制品的质量大约为m 148g 本设计选用中国海太机械厂生产的HDL1380注塑机 四 设计模具示意图 1 模具的装配图 2 模具的开模过程 注射成型后 开模时在弹簧和凝料的冷料井的拉紧的作用下开始分型 第一次分型开始凹模板运动到限位挡板碰到限位拉板 第一次分型结束 模具继续运动 模具开始第二次分型 首先是拉断点浇口 在塑件包紧凸模的包紧力的作用下 塑件继续运动 当运动到一定距离时 注射机的顶杆推动推板 带动推杆和斜杆将塑件推出动模 同时完成对矩形孔的抽芯 五 结束语 该模具设计巧妙的利用了斜杆导滑的斜滑块内侧抽芯 从而保证能够完成塑件内侧抽芯过程 提高了生产效率 由于塑件是壁厚较薄而均匀的塑件 而且 凸模部分有孔和凸台 有较大的包紧力 为保证塑件的推出 故设计12根推杆来平衡推出力 该模具的试制成功可以为斜杆导滑的斜滑块内侧抽芯模具提供一个有益的范例 在此向所有老师表示衷心的感谢 对我的授课老师刘新民和谭英杰表示深深的敬意 特别感谢我的指导老师 刘新民老师对我设计的的指导和帮助 中北大学分校毕业设计(论文)摘 要:分析了电话机外壳下盖的塑件工艺特点。介绍了电话机外壳下盖注射成型结构及模具的工作过程和电话机外壳下盖注射模具结构的设计方法。分析了模芯零件的选材、热处理、下盖的塑件的机构要素,塑件的尺寸公差和精度选择。此电话机外壳注射设计特点是:点浇口形式的双分型面的注射模,采用斜杆导滑的斜滑块分型抽芯机构。关 键 字 :电话机外壳下盖;滑块; 注射模具Abstract Analyzed under the telephone outer covering to cover models the craftcharacteristic. Introduced under the telephone outer covering coversthe injection to take shape the structure and the mold work processand underthe telephone outer covering covers the injection moldstructure the design method. Analyzed the mold core componentsselection, the heat treatment, under has covered models theorganization essential factor, modelled the size common difference andthe precision choice. This telephone outer covering injection designcharacteristic is: Runner form duplex profile injection mold,Uses the strut to lead the slippery slanting slide minute to pull outthe core organization.Keywords : Under the telephone outer covering covers; Slide; Injects the mold1中北大学分校毕业设计(论文)目录前言2第一章 塑件分析设计3第1.1节 塑料材料的选择31.1.1选材依据31.1.2 选材方法41.1.3 材料选择5第1.2节 塑料制品的结构设计51.2.1 塑件的尺寸精度与精度51.2.2 表面质量61.2.3 结构设计及工艺性6第二章 方案的选择7第三章 注射机的选择9第四章 注塑模设计10第4.1节 塑料制件在模具中的位置114.1.1 型腔数的确定114.1.2 分型面的选择11第4.2节 浇注系统和排溢系统的设计124.2.1 主流道及主流道衬套124.2.2 冷料井的设计134.2.3 分流道设计144.2.4 浇口的设计154.2.5 排气系统的设计16第4.3节 成型零件的设计174.3.1成型零件的结构设计174.3.2 成型零件工作尺寸计算184.3.3 型腔壁厚和底板厚度计算21第4.4节 侧向抽芯机构设计224.4.1 抽芯距确定和抽拔力计算322442斜推杆导滑的斜滑块分型抽芯机构设计23第4.5节 温度调节系统的设计244.5.1 模温对塑件的影响244.5.2、制品所需的成型周期的计算244.5.3 冷却参数的计算254.5.3 冷却回路设计26第4.6节 合模导向机构设计264.6.1概述264.6.2 导柱导向机构设计274.6.3导套的设计要点27第4.7节 塑件脱模机构284.7.1 脱模机构设计一般应遵循下述原则:284.7.2 脱模力的计算294.7.3推杆的设计29第4.8节 工艺参数的校核304.8.1 最大注射量的校核314.8.2 注射压力的校核314.8.3 锁模力的校核314.8.4 开模行程的校核314.8.5 安装尺寸的校核32第五章 结 论33参考文献33致谢:35外文翻译36前言 塑料材料只有通过成型才能成为具有使用价值的各种制品,而塑料的成型一般通过模具来成型,因此在塑料生产过程中模具是必不可少的。塑料模具对实现成型工艺要求和塑件使用要求起着十分重要的作用。任何塑件的生产和更新换代都是以模具的制造和更新为前提的,由于目前工业和民用塑件的产量猛增,质量要求越来越高,因而导致了塑料模具研究、设计和制造技术的迅猛发展。我国具工业从起步到飞跃发展,历经了半个多世纪,近几年来,我国模具技术有了很大发展,模具水平有了较大提高。大型、精密、复杂、高效和长寿命模具又上了新台阶。大型复杂冲模以汽车覆盖件具为代表,我国主要汽车模具企业,已能生产部分轿车覆盖件模具。体现高水平制造技术的多工位级进模、覆盖面大增,已从电机、电铁芯片模具,扩大到接插件、电子零件、汽车零件、空调器散热片等家电零件模具上。塑料模已能生产34、48大展幕彩电塑壳模具,大容量洗衣机全套塑料模具及汽车保险杠和整体仪表板等塑料模具。近几年来塑料成型模具的产量和水平发展十分迅速,高效率、自动化、大型、精密、长寿命模具在模具总产量中所占比例越来越大,塑料模热流道技术更臻成熟,气体铺助注射技术已开始采用。压铸模方面已能生产自动扶梯整体梯级压铸 模及汽车后轿齿轮箱压铸模等模具质量、模具寿命明显提高;模具交货期较前缩短。CAD/CAM/CAE技术相当广泛地得到应用,并开发出了自主版权的模具CAD/CAE软件。电加工、数控加工在模具制造技术发展上发挥了重要作用。模具加工机床品种增多,水平明显提高。快速经济制模技术得到了进一步发展,尤其这一领域的高新技术快速原型制造技术(RPM)进展很快,国内有多家已自行开发出达到国际水平的相关设备。模具标准件应用更加广泛,品种有所扩展。模具材料方面,由于对模具寿命的重视,优质模具钢的应用有较大进展。正由于模具行业的技术进步,模具水平得以提高 ,模具国产化取得了可喜的成就。历年来进口模具不断增长的势头有所控制,模具出口稳步增长。在新世纪来到之际,我国模具工业的发展将面临新的机遇和挑战。回顾以往,展望未来,我们满怀信心期待模具技术在“十五”期间有更快的发展。实施标准化、专业化推动了我国塑料模具加工工业的发展,并将继续为我国塑料模具生产企业提高技术水平、增强竞争实力、加快融入国际大市场的步伐提供必要的技术保障。做为新世纪的大学生,我一定要学好模具的专业知识,用心做好每一个模具设计,努力为国家的模具设计事业作出我一点贡献。设计者:邱海军2005年6月13日第一章 塑件分析设计一个完美的塑料制件,要根据制品的使用要求和外观要求从力学性能、美术造型和成型工艺、塑料模具设计和制造等多方面进行考虑。塑件的物理力学性能,如刚度、强度、韧性、弹性、吸水性、以及对应力的敏感性。设计塑件时尽量发挥其优点,避免和补偿其缺点。塑料的成型工艺,如流动性、成型收缩率及收缩率的各项差异等。塑件的形状应有益于脱模、排气、补缩,同时能使热塑性塑料制品达到高效、均匀冷却。塑件结构应是模具结构尽可能简单,特别是避免侧向分型抽芯机构和简化脱模机构。使模具机构符合制造工艺要求。第1.1节 塑料材料的选择注射塑料制品的选材要求主要取决于使用要求,为达到均衡选材还需考虑材料的注射工艺性和模具的结构工艺性。1.1.1选材依据(1)塑料件所需性能(使用要求)。使用要求是一个综合性的问题。这里我们设计的塑料制件是电话机外壳下盖注射模的设计,属一般的室内用塑料件,对耐候性要求不高。需要有一定的刚度,并对制品表面的粗糙度也有一定要求。已确定采用注射模塑成型,对原材料性能的最低要求如表11:表11 原材料性能项目的最低数值清单:抗压强度50 MPa弯曲模量900 MPa热变形温度80 带缺口悬臂冲击强度2 kJ/m2断裂伸长率5 %(2)几种塑料性能比较,见表12。(3)塑料材料性能排序,见表13。表12 几种塑料的性能比较材料名称密度(g/cm3)强度极限b(kg/mm2)比强度b/弹性模量E(kg/mm2)比刚度(E/)价格元/吨PE0.9639.541.21078.71123.76600PP0.9032.335.91274.81416.47450PS1.0648.645.93137.92905.87850ABS1.0548.045.12059.31961.210100POM1.4160.442.82745.71947.315000PA-61.1381.071.72745.72418.3116900PA-661.1478.368.61274.81118.218900PC1.2061.851.52353.41961.120100表13 几种常用塑料的使用性能排序序号性能说 明塑料代号排序1强度刚度高 低PA POM PSU PET EP ABS PS PVC PMMA PP PE2耐磨减磨好 差PA PAR PP PBT PC FEP POM ABSPVC PS PMMA PSU3耐化学性好 可PCTFEF3 PEEK PPS PENTON PTFE PPSU PPO ABS HDPE PB PA PC PMMA 4耐热性高 低PTFE EP PSU PC PP PE POM PMMA ABS PS PVC5尺寸稳定性精 粗PENTON PVC PSF PS PMMA ABS PC PA PSU PPO PP PE6抗老化性强 弱FEP F46 PTFE UEMWPE PEEK PMMA PAR PBT PC POM7阻燃性好 差PTFE PVC PI PPO PC PVF PEC EP PMMA PE PP8电性能低 高PTFE PE PVC PET PMMA PI PBT PPS PA TTE PPP 9透明性好 劣PMMA PS PC PCTFEF3 PA PA-10101.1.2 选材方法经验法。按选材经验和推荐使用情况综合考虑使用要求,选取合适的材料,其中还须考虑经济成本和材料来源。1.1.3 材料选择根据经验和推荐电话机外壳采用材料ABS。ABS的特性、注射工艺及模具条件介绍:特性:(1) (丙烯腈)ABS有高的良好的耐热和耐腐蚀性。 B(丁二烯)很高的韧性和低温条件S(苯乙烯)使ABS具有良好的成型工艺性,刚性和着色性(2) ABS五毒、 无味,密度为1.021.08g/cm,吸水性很小1%。(3) 使用温度范围为-40110,力学性能优良,耐疲劳、冲击硬度好(4) 化学性能稳定性好,耐酸、耐碱、耐盐的化学腐蚀(5) 着色性良好,电缘性也很好(6) 表面可以电镀、喷漆、印刷、绘画注塑工艺及模具条件:干燥处理:ABS材料具有吸湿性,在注射成型前进行干燥处理。建议干燥条件:8090下最小干燥2h,且材料温度波动应保证小于0.1。熔化温度:210280建议温度:245模具温度:2570 注射压力:50100MP注射速度:中高速度第1.2节 塑料制品的结构设计1.2.1 塑件的尺寸精度与精度 塑料制品的尺寸精度与塑料制品品种有关,根据各种塑料收缩率不同,可将各种塑料的公差等级分为高精度、一般精度和低精度。对于塑料制品技术要求和尺寸精度尽量降低,采用一般精度。电话机外壳选用的尺寸精度等级一般为4级,根据GB/T14486-1993标准;公差为0.74mm 。1.2.2 表面质量塑件表面质量包括表面粗糙度和表观缺陷状况(缺料、溢料、凹陷、熔接痕、银纹、浇口处发浑、翘曲、粘膜和粘流道等)。如果不考虑表观缺陷状况,则制品的表面质量主要取决于表面粗糙度。一般而言,原材料的质量、工人操作水平及模具型腔的表面粗糙度等因素均对制品的表面粗糙度有影响,其中模腔的表面粗糙度影响最大。制品要求的表面粗糙度数值越小,模腔表面越光滑,加工模具时的研磨抛光要求也越高,模具制造的难度也越大。因此,制品表面的粗糙度应视情况而定,除了考虑使用要求外,还须考虑美观。模塑制品的表面粗糙度通常为Ra0.80.2之间,此电话机外壳取Ra0.5um。模腔表面粗糙度数值为制品的1/2,即Ra0.40.1,这里取Ra0.25。1.2.3 结构设计及工艺性如图11 塑件图。图11 塑件图(1) 塑件的壁厚电话机外壳底座塑件如图1.1所示,其壁厚是最重要的结构要素。塑件的壁厚对熔体充满模具型腔的流程影响很大,壁太厚就很难达到完全均匀的硬度,且易产生气泡、缩孔等缺陷;太薄则刚度差,在脱模、装配、使用中会发生变形,影响塑件的使用和装配的正确性。塑件不均匀,将导致塑件各个部件固化收缩不均匀,易在塑件上产生气孔、裂纹,引起内应力及变形等缺陷。塑件壁厚一般在13mm范围内,最常用的是23mm,大型塑件也有更厚的。根据所设计的电话机外壳的材料、结构、强度等要求,取塑件壁厚为2mm。(2) 塑件的圆角为防止塑件转角处的应力集中,改善其成型加工过程中的充模特性,增强相应位置模具和塑件的力学性能,需在塑件的转角出和内部联结处,采用圆角过度。实验证明,当圆弧半径大于塑件壁厚1/4时,其应力集中系数小于2,当此比值增大到1/2,应力集中系数可减至1.5。塑件内外表面转角处,采用圆弧过渡,可以有效减少内应力。当塑件结构不允许有圆角时,圆角半径视具体情况可取0.20.5mm.(3)的脱模斜度 塑件冷却时的收缩率会使它紧包住模具型芯或型腔中的凸起部分。因此,为了便于从塑料中抽出型芯或从型腔中脱出塑件,防止脱模时拉伤塑件;在设计时,必须使塑件内外表面沿着脱模方向留有足够的斜度,从表查得ABS塑件脱模斜度,型腔为30130,型芯为351。脱模斜度取决于塑件的形状、壁厚、及塑料的收缩率。成型型芯越长或型腔越深,则斜度应取偏小值;反之可选用偏大值。因此,此次设计的电话机外壳的脱模斜度型腔取1型芯取40。(4) 塑件的孔塑件上常用的孔有通孔、盲孔、自攻螺钉和形状复杂的孔等。这些孔不宜设在可能削弱塑件的强度的部位,孔之间及边壁之间,应均匀留有足够的距离。第二章 方案的选择由于塑件内部存在很多孔和侧向有矩形孔,针对这种情况本设计模具的凸模和凹模都采用整体结构,比较紧凑。针对侧孔本设计采用抽芯,具体采用何种经过以下的分析和比较,我采用了二次分型斜杆导滑的斜滑块内侧抽芯的结构。侧向分型或侧向抽芯机构是塑料注塑模的一个重要组成部分,在塑件上凡是脱出方向和开模方向不同的侧孔或侧凹除少数浅侧凹外,都需要进行侧向抽芯或侧向分型方能将塑件顺利脱出。手动侧向分型抽芯机构是利用人力将模具侧向分型或把侧向型芯从成型塑件中抽出。,这类机构操作不方便,工人劳动强度大,生产效率较低,抽拔力有限,但模具的结构比较简单,加工制造成本低,因此常用于产品的试制、小批量生产或无法采用其他侧向分型与抽芯机构的场合。这里不适合。液压(气压)侧向分型抽芯机构系指以压力油(或压缩空气)作为动力来源,驱动模具进行侧向分型、抽芯及其复位的机构。这类机构的主要特点是抽拔距离长,抽拔力大,动作灵活,不受开模过程限制,常在大型注射模具中使用。如注射机本身带有备用的液压缸,尤为适用。但缺点是液压或气动装置成本较高。在这里抽拔距离短,故不适合采用。机动侧抽芯一般系指借助注射机的开模力或顶出力与合模力进行模具侧向分型、抽芯及其复位动作的机构。这类机构虽然结构比较复杂,但分型与抽芯无需手工操作,生产效率高,经济性好,动作可靠,实用性强,其主要形式有:弹簧分型抽芯、斜销分型抽芯、弯销分型抽芯、斜滑块分型抽芯、齿轮齿条抽芯等。为了提高经济性,我们采用机动侧向抽芯。弹簧分型抽芯采用弹簧(或硬橡皮)实现抽芯动作,结构简单。但它只适合抽拔距小、抽拔力不大的场合。斜导柱分型抽芯机构是利用斜导柱等零件把开模力传递给侧型芯或侧向成型块,使之产生侧向运动完成抽芯与分型动作。这类机构结构紧凑、加工制造方便、动作安全可靠。它的拔力和抽芯距受到模具结构的限制,一般使用于抽芯力不大且抽拔距小于6080mm的场合。所以这里不适合采用此方法。 斜推杆导滑的斜滑块分型抽芯机构是在成型滑块的底部连接一根斜杆(矩形或圆形均可),推出时斜杆在斜孔内运动,使斜滑块一面上升一面完成分型动作。由于斜杆刚度较差,多用于抽拔力不大的场合,优点是它占位小,既可用于外侧抽芯,也可用于内侧抽芯。由于电话机的矩形孔抽拔距离短,抽拔力小,故本设计采用斜推杆导滑的斜滑块内侧抽芯。第三章 注射机的选择注塑成型机类型和规格很多,卧式注塑机是目前使用最广泛的注塑成型机,其注塑柱塞或螺杆与模板的合模运动均沿水平方向装设,并且多数在一条直线上,其优点是机体较低,容易操纵和加料,制件推出模具后可自动坠落,故意实现全自动化操作,机床重心较低安装稳定,一般大中型注塑机均采用这种形式。此处就采用卧式螺杆式注塑机。模具设计时需要考虑注射机技术的规范有:最大注射量、最大注射压力、最大锁模力、模具安装尺寸和开模行程等。由于同一规格的注射机,生产厂家不同,技术规格也有所不同,所以设计时最好查阅注射机生产厂家提供的注射机使用说明书上标明的技术规格。根据ABS的注射容量,m=148g/cm或注射容积V=140.95cm3,初选如下: 浙江塑料机械厂生产SZ-1000/ZT,SZ-1000/ZC注射机的主要参数名称单位螺杆直径Mm45理论注射量Cm3259注射压力Mp200锁模力Kn1600模具厚度MmMax480min175模板行程mm385模板最大开距Mm865顶出力Kn45顶出行程mm125 中国海太机械厂生产的HDL1380注塑机的主要参数项目项目名称单位HD1380B注射装置螺杆直径mm45理论注射容量cm3238注射重量g222注射速率g/s130塑化能力g/s19注射压力MPa155螺杆转速rpm190合模装置合模力kN1380移模行程mm380拉杆间距mm450*450最大模厚mm460最小模厚mm170顶出行程mm115顶出力kN33其它最大油泵压力MPa14油泵马达功率kW13电热功率kW7.2外形尺寸(长*宽*高)m4.6*1.5*1.8机器重量t3.8根据塑件要求本设计选择第二种注射机方案图31 注塑机的安装尺寸第四章 注塑模设计第4.1节 塑料制件在模具中的位置4.1.1 型腔数的确定经天平测量,测的塑件的质量m=148g,根据手册知ABS的密度为1.021.08g/cm3所以平均密度为,所以可计算的注射容积为V=140.95cm3初选一模一腔(1)型腔数确定这里根据所选注塑机的技术规范及塑件的技术经济要求,计算可以选择的型腔数。注塑机的最大的注塑量按国际惯例是指注塑在常温下密度为的普通聚苯乙烯的对空注射量,实际的注射量取机器的最大注塑量的85%实际注射量:,为理论的最大的注射量对于其它的非聚苯乙烯的塑料,其最大的注塑量为: , (4-1) 1个 所以,注射机的最大注射量是合格,型腔数的选择也是可行的。4.1.2 分型面的选择模具上用以取出制品及浇注系统凝料的可分离的接触面称分型面分型面是决定模具结构形式的重要因素,它与模具的整体结构和模具的制造工艺有密切关系,并且直接影响着塑料熔体的流动充模特性及塑件的脱模,因此,分型面的选择是注塑模具设计的一个重要问题。常见的取出塑件的主分行面,与开模方向垂直。分型面的选择不仅关系到塑件的正常成型和脱模,而且涉及模具的结构与制造成本。在选择分型面时,应遵守以下规则: (1):分型面应该选择在塑件的最大的截面处; (2):尽可能地将塑件留在动模一侧。因为在动模一侧设置和制造脱模机构简便易行; (3):有利于保证塑件的尺寸精度; (4):有利于保证塑件的外观的质量; (5):考虑满足塑件的使用要求。注塑件在模塑过程中,有一些很难避免的工艺缺陷,如拔模斜度、分型面上飞边及顶杆与浇口的痕迹等。在设计分型面时,应从使用角度避免这些工艺缺陷影响塑件的功能; (6):尽量减少塑件在合模平面上的投影面积,以减少所需的锁模力; (7):长芯应置于开模方向; (8):有利于排气,应有利于简化模具。考虑以上几方面,因侧向合模锁紧力较小,故对于投影面积较大的大型制品,应将投影面积大的分型面放在动,定模的合模主平面上,而将投影面积较小的分型面作侧向分型面。本模具的分型面选择在塑件的大平面出。大致结构如简图:图41 分型面第4.2节 浇注系统和排溢系统的设计4.2.1 主流道及主流道衬套为了有效地传递压力,浇注系统主流道及其附近的塑料熔体应该最后固化,主流道与分型面垂直,为便于流道凝料拔出,设计成2(24)锥角的圆锥形。内壁粗糙度,内壁研磨抛光时不形成与开模方向垂直的划痕,以免造成脱模困难。主流道与喷嘴接触处作半球形凹坑,二者配合严密,避免高压塑料熔体溢出,凹坑球半径R2比喷嘴球头半径R1大0.51.5mm,R2=R1+(0.51.5)=16mm,主流道小端直径比注塑机喷嘴孔径大0.51mm,取5mm。大端直径比分流道深度大1.5mm以上。台阶转角半径R宜大一些,以免淬火开裂或应力集中,取R=3mm。由于主流道与注塑机的高温喷嘴反复接触和碰撞,所以设计成独立的主流道衬套。选用优质钢材T8A制作,并经热处理淬火+低温回火提高硬度至5055HRC。单位:mmDdD1LL1385183010流道锥角 =2喷嘴球半径SR15喷嘴口孔径4 图42主流道衬套4.2.2 冷料井的设计当注射机未注射塑料之前,喷嘴最前端的熔融塑料的温度较低,形成冷料渣,为了集存这部分料渣,在进料口的末端的动模板上开设一洞穴或者在流道的末端开设洞穴,这个洞穴就叫冷料穴。在注射时必须防止冷料渣进入流道或者模具型腔内,否则将会堵塞流道和减缓料流速度,进入模具型腔就会造成塑料制品上的冷把或冷斑。因此在模具设计时设计一个冷料穴。4.2.3 分流道设计影响分流道设计的因素很多,制品的几何形状、壁厚、尺寸大小及尺寸的稳定性,内在质量和外在质量要求,塑料的种类,注射机的压力,加热温度,注射速度,主流道及分流道的拉料及脱落方式,型腔布置及浇口形式的选择都能影响分流道的设计。在设计分流道时考虑以下几点:1. 塑料流经分流道时的压力损失及温度损失要小。2. 分流道的固化时间应稍后于制品的固化时间,以利于压力的传递及保压。3. 保证塑料迅速而均匀的进入各个型腔。4. 分流道的长度应尽可能短,其容积要小。5. 要便于加工及刀具的选择。(1)分流道截面分析圆形截面分流道 其优点是表面积与体积之比值为最小,在容积相同的分流道中圆形截面分流道的塑料与模具接触的面积最小,因此其压力损失及温度损失小,有利于塑料的流动及压力传递,其缺点是圆形截面分流道必须在动、定模上分别设计两个半圆形,因此给模具加工带来一定难度。抛物面截面(U形截面) 其截面的形状接近于圆形截面,同时此种截面的分流道只在模具一面加工。但缺点是与圆形截面相比,热损失较大,流道废料较多。梯形截面 此种截面是抛物线形截面的变形,与以上两种截面相比,其热损失较大,但便于分流道的加工及刀具的选择。因而,这里选择圆形截面分流道。查表得到ABS的圆形截面分流道直径为 D=4.79.5mm,这里取D=4.8mm。a. 圆形截面 b. U形截面 c.梯形截面图43 分流道截面4.2.4 浇口的设计浇口是连接流道与型腔之间的一段细短的通道。它是浇注系统的关键部分。浇口的设计或选择恰当与否,直接关系制品能否被完好的注射成型。浇口种类有直浇口,侧浇口,扇形浇口,环行浇口及点浇口。根据制品的结构要求,本设计采用点浇口形式。点浇口是一种尺寸很小的浇口。物料通过时有很高的剪切速率,这对于降低假塑性流体的表观黏度是有益的,熔体粘度在高速剪切力场中减小后,将在一段时间内继续保持该粘度进入型腔,尽管这时型腔中的剪切速率已经降低。同时熔融物料通过小浇口时还有摩擦生热提高料温的作用,使粘度进一步降低。点浇口的主要尺寸及浇口图: l=0.752,此处选l=1 c=0.3x45,=2D1D=4.8直径按经验公式计算:d= (46)式中 凹模边型腔表面积,即塑件外表面积mm。 n-塑料类常数 K-系数 =211118=24898mmd=2.56mm 4.2.5 排气系统的设计 开设排气系统的目的 塑料注射模具的型腔,在熔融塑料的填充的过程中,除了模具型腔内有空气外,还有因塑料受热而产生的气体,尤其在高速注射成型时产生的气体更多,因此在模具设计时必须设置排气槽。 排气系统的作用排气系统对确保塑件成型质量起着至关重要的作用。塑料制品在注射成型过程中,除了型腔原有的空气之外,还有塑料受热后挥发出来的气体。这些气体必须随着塑料的进入而排出模外,否则会引起缩孔,出现熔接线和冲料不足,烧灼等缺陷,对于流动性好的塑料,更应考虑排气效果。此塑件选用分型面进行排气,排气效果比较好。在注射模试模生产中常会出现填充不足。压缩空气灼伤、制品内部很高的内应力、表面流线和熔合线等现象。对于这些现象除了应首先调整注塑工艺外,还要考虑模具浇口是否合理。当注塑工艺和浇口这两个问题都排除以后;那么模具的排气就是主要的问题了,解决这一问题的主要手段是开设排气槽。排气槽的作用排气槽的作用主要有两点。一是在注射熔融物料时,排除模腔内的空气;二是排除物料在加热过程中产生的各种气体。越是薄壁制品,越是远离浇口的部位,排气槽的开设就显得尤为重要。另外对于小型件或精密零件也要重视排气槽的开设,因为它除了能避免制品表面灼伤和注射量不足外,还可以消除制品的各种缺陷,减少模具污染等。那么,模腔的排气怎样才算充分呢?一般来说,若以最高的注射速率注射熔料,在制品上却未留下焦斑,就可以认为模腔内的排气是充分的。本模具为中小型的简单型腔,且设有推杆定出机构和侧向抽芯机构,可以利用推杆、活动型芯与模板的配合间隙进行排气,其间隙可取在0.030.05mm之间,这里取0.04mm。排气槽如图所示:第4.3节 成型零件的设计4.3.1成型零件的结构设计(1)凹模的结构设计整体式凹模有一整块金属切削而成,结构牢固、不易变形。这里模具型腔结构并不复杂,可以采用整体式凹模。模板一般采用45#钢制作,但是45#钢在局部淬火时容易变形,所以定模板加工时,留修模余量,对型腔部分作局部淬火,后再次对模板进行修模。模板材料45#钢正火,硬度170210HBS,表面粗糙度:。型腔表面淬火,硬度4348HBS,表面粗糙度:图.凹模结构图(2)型芯的结构设计由于模具的凸模部分存在很多孔和槽,故凸模也才用整体试结构,比较紧凑。型芯的材料是35SiMn合金结构钢,调质220260HBS。表面的粗糙度:。图4.7凸模结构图4.3.2 成型零件工作尺寸计算按平均收缩率计算成型尺寸比较简便易行,是最常用的计算方法,这里采用此方法。ABS平均收缩率,塑件制造公差,对应模具制造公差。(1)型腔径向尺寸计算 (47) (48)式中 型腔(孔)的最小尺寸型腔使用过程中允许的最大磨损量(取塑件总误差的1/6,一般在0.020.05mm之间)成型零件制造误差(正值)塑件(轴)的最大尺寸 塑件公差(负值)出于修模考虑,对型腔径向尺寸来说易修大,预留一负修模余量,标上制造公差得型腔径向名义尺寸: =+ 对于注塑模,型腔磨损量很小时,可用下式计算:= + (49)塑件径向尺寸=213mm, =212.59mm;213.86mm模具型腔按级精度制造,其制造偏差=0.185mm,=(213.86-0.185)+0.185=213.67+0.185mm(2)型芯径向尺寸计算=标上制造公差得型芯径向名义尺寸:=-对于注塑模,型腔磨损量很小时修模余量也很小时可用下式计算:=- (410)塑件尺寸=195mm,=195+=195.41mm;=196.59mm模具制造偏差=0.185mm,(196.59+0.185)-0.185=196.78-0.185 mm塑件尺寸=220mm,=220+=220.41mm;221.74mm模具制造偏差=0.185mm,(221.74+0.185)-0.185=221.92-0.185 mm (3)型腔深度尺寸计算+若取修模余量为,则型腔容易修浅 + (411)塑件大端尺寸=36mm,36=35.87mm;=36.09mm模具制造偏差=0.100mm,型腔易修浅,36.09+0.100mm。塑件小端尺寸=26mm,26=25.88mm;=26.04mm模具制造偏差=0.084mm,型腔易修浅,26.04+0.084mm。(4)型芯高度尺寸的计算 -型芯容易修长- (412)塑件大端高度尺寸=34mm,34=34.13mm;=34.34mm模具制造偏差=0.100mm,型腔易修长,34.34+0.100mm。塑件大端高度尺寸=24mm,24=24.11mm;=24.25mm模具制造偏差=0.084mm,型腔易修长,24.25+0.084mm。4.3.3 型腔壁厚和底板厚度计算(1)型腔侧壁厚度计算 型腔为不规则形状,近似于矩形,按整体式矩形型腔进行计算。但塑料熔体注入时,其最大变形发生在自由边的中点。变形量为 (413)式中 由而定的常数,;侧壁内侧边长211mm;侧壁内侧边高(型腔深度)36mm。模腔压力=50100 Pa,为注塑压力。 (414) 1.438 26.3 mm 故侧壁厚选26.3 mm。(2)底板厚度计算 允许变形量已知,按刚度条件计算 (415)型腔内壁短边长常数,由 而定。 =1.8,查表得c,= p=80MP =0.05=34.4mm按许用应力计算最大应力集中在底板中心和长边中点处,而以长边中点处的应力最大,应力为 按许用应力计算底板最小厚度(mm)为 (417)式中 由决定的常数,查表取=0.487。 61.9 mm 故底板厚度选61.9 mm。第4.4节 侧向抽芯机构设计4.4.1 抽芯距确定和抽拔力计算 侧向分型与抽芯机构简称侧抽芯机构,用来成型具有外侧凸起,凹槽和孔的塑料件,成型壳体制品的内侧的局部凸起,凹槽和盲孔。侧抽机构必须在开模方向塑料件脱模之间完成抽拔动作。斜导柱的侧向抽芯距:mm h-活动型芯安全脱出成型部位的距离mm k-抽芯安全系数 查得k=2 s=2+2=4mm 注塑成型后,塑件在模具内冷却定型,由于体积的收缩,对型芯产生包紧力,塑件要从模腔中脱出,就必须克服因包紧产生的摩擦力。对于不带通孔的壳类塑件,脱模时还要克服大气压力。一般而论,塑件刚开始脱模时,所需克服的阻力最大,即所需的脱模力最大。图46为不带通孔的壳类塑件脱模时型芯的受力分析。脱模力可以按图46来估算。根据力平衡原理,列出平衡方程式:=0则: Ft + Fb sin = Fcos式中 Fb塑件对型芯的包紧力; F脱模时型芯所受的摩擦阻力; Ft脱模力; 型芯的脱模斜度。又 F = Fb于是 Ft = Fb(cos- sin)而包紧力为包容型芯的面积与单位面积上包紧图48力之积,即:Fb =A p由此可得: Ft =A p(cos- sin) (418)式中 塑料对钢的摩擦系数,约为0.10.3; A塑件包容型芯的面积; P塑件对型芯单位面积上的包紧力,一般情况下,模外冷却的塑件p约取2.43.9107Pa;模内冷却的塑件p约取0.81.2107Pa。 抽拔力的计算也一样,假设制件为不带通孔的壳体类塑件,应用此公式计算得到Ft =(121210-6)1.2107(0.2cos 1-sin1) =316.24 N考虑塑件得形状是由式(418) 可以看出:脱模力的大小随塑件包容型芯的面积增大而增大,随脱模斜度的增大而减小。由于影响脱模力大小的因素很多,如推出机构(抽芯机构)本身运动时的摩擦阻力,塑料与钢材间的粘附力、大气压力及成型工艺条件的波动等等,因此要考虑到所有因素的影响较困难,而且也只能是个近似值,所以式(418)只能做粗略的估计。442斜推杆导滑的斜滑块分型抽芯机构设计 在成型滑块的底部连接着一根斜杆(矩形或圆形),推出时斜杆在斜孔内运动,使斜滑块一面上升一面完成抽芯分型动作。斜杆的头部成型制品的矩形孔,其下端装有滑轮,在推板上滑动,脱模时制件一面离开主型芯,同时完成抽芯动作。采用铰链连接的办法也可以避免斜杆下端与推板之间的摩擦。本设计斜推杆采用矩形而不是圆形,因为圆形感推出时容易发生转动,同时为了避免复位时发生困难。第4.5节 温度调节系统的设计4.5.1 模温对塑件的影响热塑性塑料熔体注入型腔后,释放大量热量而凝固。不同的塑料品种,需要模腔维持在某一适当温度。模温对塑件质量的影响主要表现在如下六个方面。(1)改善成型性 每一种塑料都有其适宜的成型模温,在生产过程中若能始终维持相适宜的模温,则其成型性可得到改善。若模温过低,会降低塑料熔体流动性,使塑件轮廓不清,甚至充模不满;模温过高,会使塑件脱模时和脱模后发生变形,使其形状和尺寸精度降低。(2) 成型收缩率 利用模温调节系统保持模温恒定,能有效减少塑料成型收缩的波动,提高塑件的合格率。采用允许的低模温,有利于减小塑件的成型收缩率,从而提高塑件的尺寸精度。并可缩短成型周期,提高生产率。(3) 塑件变形 模具型芯与型腔温差过大,会使塑件收缩不均匀,导致塑件翘曲变形。尤以壁厚不均和形状复杂的塑件为甚。需采用合适的冷却回路,确保模温均匀,消除塑件翘曲变形。(4) 尺寸稳定性 对于结晶性塑料,使用高模温有利于结晶过程的进行,避免在存放和使用过程中尺寸发生变化;对于柔性塑料采用低模温有利于塑件尺寸稳定。(5) 力学性能 适当的模温,可使塑件力学性能大为改善。例如,过低模温会使塑件内应力增大,或产生明显的熔接痕。对于粘性大的刚性塑料,使用高模温,可使其应力开裂大大降低。(6) 外观质量 适当提高模具温度能有效地改善塑件外观质量。过低的模温会使塑件轮廓不清,产生明显的银丝,云纹等缺陷,表面无光泽或粗糙度增加等。4.5.2、制品所需的成型周期的计算注入模具内的塑料熔体所带入的热量通过模具模板进入冷却介质,少量散发到大气中,它们之间的热交换速度是决定制品冷却时间的决定因素。由公式(3-9-3)可得: 式中 S制品的壁厚(mm) ,这里取S=2.0mm 塑料注塑温度() ,这里取=260 塑料注塑温度() ,这里取=60 塑料的热扩散系数(),查表可得 =所以制品的注塑时间为: 由产品得知,厚度为2mm,故制品的在模内冷却时间应以制品厚度为计算依据。查表得,得到制品在模内冷却时间为9s。所以塑件成型周期为:T=9+2.18=11.18s 所以每小时注射的次数 (次)塑件的质量为148g,所以每小时注射总量:4.5.3 冷却参数的计算(1)求塑件每小时在模内释放的热量Q查表(3-41)得:ABS成型时放出的热量所以 (2)求冷却水的体积流量V,由式(3-8)得设水进出口温度,其中 水出模具时的温度,水进模具时的温度 (9.5)(3)求冷却水孔的直径根据体积流量V,由表(3-44)查找,取冷却水孔的直径d=8mm(4)求水在水孔内的流速 (9.6)(5)求冷却水孔壁与冷却水间的传热系数由表(3-38)查得25时水的=7.95,所以由式(3-79)得 (6)冷却水流动状态校核当平均水温为22.5时,由图(3-319)查得水的运动粘度,所以由式(3-91)得 (9.10)所以冷却处于湍流,冷却效果好。 4.5.3 冷却回路设计由前面计算得到冷却孔数5,孔径8mm。取冷却水孔中心线与型腔壁距离15mm,冷却通道之间中心距35mm。型腔较浅,可以采用最简单的直通式冷却水路,动、定模冷却水路布置相同。图49冷却水到分布简图第4.6节 合模导向机构设计4.6.1概述 导向机构是保证塑料注射模具的动模和定模的正确定位和导向的重要零件。它可以保证塑料模闭合时型腔形状和尺寸的精确性,使之按一定的方向和位置合模。最常见的导向定位机构是在模具型腔四周设2-4对相互配合的导向和导向孔, 导向机构主要有导向,定位和承受注塑时产生侧压力三个作用。4.6.2 导柱导向机构设计导柱的直径任何一副模具在定、动模之间都设有导向机构,起着定位、导向、承载和保持运动平稳的作用。按经验,导柱直径和模板宽度之比=0.060.1,圆整后其标准值,模具选尺寸=450450。选择导柱直径。导柱的形状 导柱的端部做成了锥形,锥形头高度取与其相邻圆柱直径的,前端倒了角,使起能顺利进入导向孔。导柱的配合公差 安装段与模板间采用过渡配合H7/K6,导向段和导向孔间采用动配合H7/f7。粗糙度 固定段表面用Ra0.8m,导向段表面用Ra0.4m。导柱的材料 导柱应具有硬而耐磨的表面,坚韧而不易折断的芯部,因此在本设计中所选导柱的材料为20#钢,渗碳0.50.8,淬硬5660HRC。导柱的示意图:4.6.3导套的设计要点形状 为了方便导套压入模板的同时便于导柱进入导套,在导套端面内外倒圆角,模具上的导向孔做成了通孔,这样合模时孔中的空气易排出,这样就避免形成附加阻力,同时也便于排除意外落入的塑料废屑。公差配合与表面粗糙度 导套内孔与导柱之间为动配合H7/f7,外表面与模板孔为较紧的过渡配合H8/k7(带轴肩导套),其前端设计为一长3mm的引导部分,按松动配合H8/e8制造,其粗糙度内外表面可用Ra0.8m。导套的材料 导套的材料可用耐磨材料,在本设计中采用的是20#钢,:热处理5055HRC,渗碳0.50.8,淬硬5660HRC。导套的示意图:第4.7节 塑件脱模机构4.7.1 脱模机构设计一般应遵循下述原则:(1)塑件滞留于动模边,以便借助于开模力驱动脱模装置,完成脱模动作,致使模具结构简单。 (2)防止塑件变形或损坏,正确分析塑件对模腔的粘附力的大小及其所在的部位,有针对性地选择合适的脱模装置,使推出重心与脱模阻力中心相重合。由于塑料收缩时包紧型芯,因此推出力作用点应尽量靠近型芯,同时推出力应施于塑件刚性和强度最大的部位,作用面积也应尽可能大一些,以防塑件变形或损坏。(3)力求良好的塑件外观,在选择顶出位置时,应尽量设在塑件内部或对塑件外观影响不大的部位。在采用推杆脱模时,尤其要注意这个问题。(4)结构合理可靠,脱模机构应工作可靠,运动灵活,制造方便,更换容易,且具有足够的强度和刚度。4.7.2 脱模力的计算脱模力由以下公式计算: 其中: E 塑料的拉伸模量(MPa),查得为0.2110 MPa; 塑料成型平均收缩率(%),查得为0.5%;t 塑件的平均壁厚(mm);t=2mmL 塑件包容型芯的长度(mm);L=36mm 塑料的泊松比,查得为0.42; 脱模斜度(塑件侧面与脱模方向之夹角);=1f 塑料与钢材之间摩擦系数,查得为0.2B 塑件在与开模方向垂直的平面上的投影面积(cm2)B=211118100=248.98K1 由f和决定的无因次数,由下式计算: 计算得 Q=15004N注射模必须有准确可靠的脱模机构,以便在每一个循环中将塑件从型腔内或型芯上自动的脱出模外,实现生产的自动化、半自动化。 推杆是推出机构中最简单最常见的一种形式。它加工简单、安装方便、维修容易、使用寿命长、脱模效果好,因此在生产中广泛应用。这里才用这种形式,但考虑到它与推杆的接触面积较小,为了避免应力集中或塑件变形,采用直杆式圆柱形推杆。4.7.3推杆的设计稳定裕度:试中对钢推杆,n=2 试中 E-弹性模量2.1 J-取推杆截面中心惯矩中的最小值, L-推杆全长127mm -稳定系数,取20.19常见: 本设计d取16mm推杆如图所示:图4.9推杆示意图装配时,推杆端面应和型腔在同一平面或比型腔平面高出0.050.1mm,以免影响塑件外形。推杆孔的配合段用H7/h7,推杆与固定板采用轴肩连接,两者的配合间隙0.8mm。安装时推杆轴线可做少许位移,确保与型腔上配合孔的同心度。材料采用T8A,头部局部淬火,推杆上段表面硬度HRC6065,配合段表面粗糙度Ra0.8,其余Ra1.6。第4.8节 工艺参数的校核4.8.1 最大注射量的校核注射模一次成型的塑料重量(塑件和流道凝料重量之和)应在公称注射量的35%75%范围内,最大达80%,最低不小于10%。既保证塑件质量,有充分发挥设备的能力。选在50%80%范围内为好。实际一次成型的塑料重量为182+14=50g ,是公称注射量的100%=73.7% ,在最佳范围内,合适。4.8.2 注射压力的校核所选注射机的注射压力必须大于成型塑件所需的注射压力。成型所需的压力与塑料品种、塑件形状尺寸、注射机类型、喷嘴及模具流道的阻力等因素有关。根据经验,这里成型的塑件形状一般,精度要求一般,塑料熔体流动性较好,所需注射压力一般在50100MPa,小于注射机的注射压力155MPa,符合要求。4.8.3 锁模力的校核 选用注塑机的锁模力必须大于型腔压力产生的开模力,否则模具分型面会在注射压力下分开而产生溢料。对于螺杆式注射机压力损失较小,所以型腔压力较大。锁模力和成型面积的关系由下式确定: (3.2)式中 -锁模力(N); -型腔压力,一般为40-50MP ,这里取=50MP; S-浇道、进料口和塑件的投影面积();经过计算:S=32214mm 所以,理论的需要的压力:而实际注塑机的锁模力为=550KN 因为,F ,所以注塑机的锁模力是合格的。4.8.4 开模行程的校核 开模取出塑件所需的开模距离必须小于注射机的最大开模行程。肘杆式锁模机构,其最大行程不受模板厚度影响,对于单分型面注塑模具,开模行程可按下式校核: (437)式中 塑件脱模(推出距离)距离,mm塑件高度,包括浇注系统在内,mm=270mm31+52+10=93mm合适。综合分析考虑抽芯机构、制件高度、脱模距离、模厚等因素,开模行程合适。4.8.5 安装尺寸的校核(1)喷嘴尺寸 注射模主流道衬套在设计时就根据注射机喷嘴尺寸得到的,所以这里不再校核。(2)定位圈尺寸 选用的注射机定模板台面上的定位孔孔径120mm,注射模端面凸台径向尺寸120mm,与定位孔呈间隙配合,便模具安装并使主流道喷嘴同心,模具端面凸台高度5mm小于定位孔深度。合适。(3)模具外形注射机拉杆内间距450450,模具宽450mm,可以移去四根中的一根拉杆间的空间装固在注射机工作台面上。 (4)模具厚度(闭合高度) 模具厚度必须满足以下关系: (438)式中 所设计的模具厚度,mm 注射机允许的最小模具厚度,mm注射机允许的最大模具厚度,mm 170356116Ls2c=Lm2+(Dz+Dc)(1-Smin)=56.37+0.13+0.065(1-0.6%)=56.1856It proves this size of one of radials of type confirmed of formula cant be full to check Foot designing requirement The same is mould type 76 for a of depth measurement correctly. 490+0. 10mm! 24. 140+0. 08mm is checked , hasHs1c=Hm1+(Dz-Dc)(1-Smin)=76.49+0.095-0.05(1-0.6%)=76.29976Hs2c=Hm2+(Dz-Dc)(1-Smin)=24.14+0.08-0.04(1-0.6%)=24.1124It proves this size of a of profundity of type confirmed of formula cant be full to check Foot designing requirement To type core, it is with the size of minimum limit when the type core is made, the wearing and tearing amount reaches the wearing and tearing amount Dc making the public errand of limit promptly =At the Dz/2, produce mould type of piece core minimum , the ultra difference probably, 36 to calculating mould type core radial measurement according to shrinking equally rate as Fig. 8 shows now. 3-0. 060mm and 16. 14-0. 060mm is checked , hasls1c=lm1-(Dz+Dc)(1-Smin)=36.3-(0.06+0.03)(1-0.6%)=35.9436ls2c=lm2-(Dz+Dc)(1-Smin)=16.14-(0.06+0.03)(1-0.6%)=15.9524The type core is high qualified that the size is checked hs2c=hm2-(Dz+Dc)(1-Smin)=68.37-(0.15+0.075)(1-0.6%)=67.7468Type core high size check not up to standard to may be found out from the computational analysis of the above, adopt person who shrink calculate result of calculation that receive equally , person who shrink change range to be relatively heavy! Shaping mould size of piece heavy situation appear mould result of calculation , shaping of size ultra a poor one often, this kind exceed difference phenomenon often person designed It neglect or not at all it is without realizing can not like this mould designed to make Cant meet the design and instructions for use Design calculating to the mould shaping measurement of moulding one by way of limit public errand now, confirm the public errand of every shaping measurement at first , to the size of radial, type core and type are all as follows,D=(Smax-Smin)Ls+Dz+DcThen it is qualified that the mould is checked, can reach the designing requirement , therefore can confirm Dz ! when elected fluctuating the too big material with the shrinking rate, Dz confirmed for the value of Dc! Dc person who calculate too light, machining when the difficult designing requirement of reaching , may change and mould a material in time in the course of designing, choose and adopt person who shrink not to fluctuate light plastic raw materials come satisfied and high The precision moulds the demand for one As to type core high size and type of depth size, because the wearing and tearing amount can ignore , they are all as follows,D=(Smax-Smin)Ls+DzThen it is qualified that the mould is checked, can reach the designing requirement , therefore can confirm the value of Dz Most greatly have wearing and tearing amount Dc =0. 04mm, can get like Fig. 9 ! Illustrated in Fig. 10 mould shaping size and public errand picture Calculate mould type a of size in limit public errand of Fig. 9Calculate the mould type size of core in limit public errand of Fig. 10Every size is it check to go on to 9 Fig. now, can is it mould pieces of heavy size most that may appear within the fixed range of dimensional tolerance allowing to know, the size of radial can be checked from the leaving type:Ls1c=Lm1+(Dz+Dc)(1-Smin)=116.58+0.054+0.04(1-0.00=115.974116Ls1It is qualified to check the sizeLs2c=Lm2+(Dz+Dc)(1-Smin)=56.16+0.12+0.065(1-0.006=55.98Ls2It is qualified to check the sizeThe size of a of profundity of the type can be checked from the leaving type:Hs1c=Hm1-SminHs-=76.3-0.00676-0.46=75.384Hs1It is qualified to check the sizeHs2c=Hm2-SminHs-=24.06-0.00624-0.2=23.716Hs2It is qualified to check the sizeSame,for mould at 10 of Fig.s the every size of the coreses check going on, it is mould pieces of limit size not minimum that may appear too within dimensional tolerance range not fixed that allow not to know Therefore, while calculate in design which carry on the shaping measurement of the mould , when the shrink rate moulding a material fluctuates greater, it is medium-sized or larger to mould the size of one at the same time, public errand caused to fluctuate change range to be relatively heavy by person who shrink, adopt person who shrink result received to calculate appear ultra difference phenomenon often equally, should adopt biggest ! Minimum person who shrink and limit shaping calculation formula of size that public errands analysing get and check formula go on the calculation and check of size, Can fix the public errand of the working size of mould shaping accurately like this, when the public errand is too little , processing is difficult , can change materials , small plastics respond to the request that high accuracy moulds one to choose and adopt the shrinking rate and fluctuate, guarantee that can find the mould is in the question of the size of shaping during the course of designing, reduce the reprocessing rate of the mould List of references: 1Peng JianSheng, Qin XiaoGang. Mould technological question and answer M . Beijing: The publishing house of the mechanical industry, 2000. 2Fan DeLiang. Public errand and technology are measured M . Liaoning: The science tech publishing house of Liaoning, 1983.3University of Science and Technology of Chengdu. Plastic shaping mould M . Beijing: China Light Industry Press, 1992. 4Ma JinJu. Plastic mold design (revised edition ) M . Beijing: China Science Tech Publishing House, 1994.5Yang ShiYing, old one is spread. Engineering plastics manual M . Beijing: The publishing house of the mechanical industry, 1994.注射模成型零件工作尺寸计算方法分摘要:通过对2种注射模成型零件工作尺寸计算方法的理论分析,指出了采用平均收缩率法论缺陷和实际模具设计中存在的问题,对极限公差法计算模具成型尺寸和公差作了分析和实说明了该计算方法能够较好地保证在注射模设计中成型尺寸和公差计算的正确性。关键词:注射成型;模具设计;工作尺寸;公差 注射模成型零件工作尺寸是指成型零件上直接用于成型塑件部分的尺寸。其主要类型有:型腔和型芯的径向尺寸(包括矩形或异形的型腔和型芯的长、宽等尺寸)、型腔或型芯的深度和高度尺寸、型芯之间或成型孔之间中心尺寸、螺纹型芯及螺纹型环尺寸。重点讨论前面3种尺寸的计算方法,这是在注射模成型零件工作尺寸计算中应用最多的尺寸计算。目前绝大部分的塑料注射模设计手册、教材和参考资料均采用平均收缩率法,这种计算方法虽然简便,但存在一定的误差,当所设计的塑件在使用和装配中有配合要求,或塑件的尺寸精度要求较高时就难以达到设计目的。对于图1所示的典型零件,在应用平均收缩率计算成型零件工作尺寸时,型腔和型芯采用如下的计算公式:径向尺寸:型腔:Lm=Ls+LsScp-(3/4)型芯:lm=ls+lsScp+(3/4) 高度尺寸:型腔:Hm=Hs+HsScp-(2/3) 型芯:hm=hs+hsScp+(2/3) 中心距尺寸:Cm=Cs+CsScp 式中-塑件的允许公差值Scp-塑件材料的平均收缩率-模具制造公差对于以上所列的模具工作尺寸的计算公式,如果塑件上的原有公差的标注方法与图1的不相符合应按一定的方法转换为图1中塑件所标注公差的形式,然后再按以上公式进行模具工作尺寸的计算。但是这些公式的推导依据是以塑件的平均收缩率、模具成型部分的平均制造公差值和模具许用总磨损量()作为设定参数得出的结论。即模具制造公差Dz值取塑件允许公差值的1/3(Dz=/3)和模具许用总磨损量Dc取塑件的允许公差值的1/6(=/6)。而在实际的模具工作状态下,其实际磨损量通常取0.020.05mm,其制造公差值通常取IT3IT6级作为模具制造公差。此外,由于塑件的收缩率是波动的,其波动值随塑件尺寸的增大而成正比增加;制造误差随塑件的尺寸增加呈立方根关系增大;但总磨损量随塑件的尺寸的增加其增加缓慢。由此可见大尺寸塑件收缩率的波动是影响塑件公差的主要因素,应稳定注射工艺条件和选用收缩率波动小的塑料。相反,对于小尺寸的塑件,影响塑件公差的主要因素则是模具成型零件的制造公差和成型零件表面的磨损量。但这些公式中却没能体现出这些因素对模具工作尺寸的影响,因此以上公式存在着一定使用上的局限性和理论上的缺陷。在室温下模具型腔径向尺寸和塑件径向尺寸的公差带关系如图2所示。图中:Ls为塑件名义尺寸;Lm为型腔名义尺寸;为塑件允许公差;D为塑件实际公差。通过分析图2,塑件偏差以负值表示,型腔偏差以正值表示,可以得到模具型腔尺寸与塑件的外形尺寸公差尺寸的公差如下:Lm=Ls-+Sma(Ls-)略去二阶微小项,整理可得:Lm=(1+Sma)Ls-标注制造偏差后为:Lm=(1+Sma)Ls- 由图2中左侧公差带示意图可知塑件可能出现的最大尺寸是否在允许公差带的规定范围之内,则可由下式进行校核(Lsc为校核计算尺寸):Lsc=Lm+ + -SminLsLs或计算塑件的实际公差D得到其另外的校核公式:D=Sma(Ls-)+ + -SminLs-(+D)略去二阶微小值,整理可得:(Sma-Smin)Ls+ (7)由此可见,按以上型腔径向尺寸制造的模具所生产出的塑件能满足使用要求。同时由图2可知,当校核符合要求时,塑件的径向尺寸是符合要求的,这时塑件径向尺寸的波动范围在规定的波动范围之内,且偏下限,这不但有益于延长型腔的使用寿命,而且给以后的试模或修模带来方便。这是因为对于模具型腔来说,修大容易,修小则较为困难。当收缩率的波动较大,或模具的制造公差及允许的磨损量过大,而塑件的允许公差较小时,则往往不能校核合格,这时应该提高型腔的制造精度,降低许用磨损量,尽可能地采用收缩率波动小的塑料来满足塑件高精度要求,可见在塑件设计时就应该对塑件的关键尺寸加以校核。如塑件的材料相同、壁厚相近、形状相似等,用获得的收缩率波动数据来进行设计计算。同样对于模具型芯也可以由图3得到模具型芯径向尺寸和塑件的径向尺寸的公差带关系。图中:ls为塑件名义尺寸;lm为型芯名义尺寸;为塑件允许公差;D为塑件实际公差。图3设定塑件型孔的公差值为正偏差,模具型芯尺寸的公差值为负偏差,可以得到如下公差关系式lm=ls+Smin(ls+)略去二阶微小值,可得lm=ls+Sminls=(1+Smin)ls+标注制造偏差后为:lm=(1+Smin)ls+- (8)由图3中左侧公差带示意图可知塑件可能出现的最大尺寸是否在允许公差带的规定范围之内,则可由下式进行校核(lsc为校核计算尺寸):lsc=lm-( +Dc)-Smalsls (9)或D=(Sma-Smin)ls+ (10)由此可见,按以上型芯径向尺寸制造的模具所生产出的塑件即能满足使用要求。同时由图3可知,
- 温馨提示:
1: 本站所有资源如无特殊说明,都需要本地电脑安装OFFICE2007和PDF阅读器。图纸软件为CAD,CAXA,PROE,UG,SolidWorks等.压缩文件请下载最新的WinRAR软件解压。
2: 本站的文档不包含任何第三方提供的附件图纸等,如果需要附件,请联系上传者。文件的所有权益归上传用户所有。
3.本站RAR压缩包中若带图纸,网页内容里面会有图纸预览,若没有图纸预览就没有图纸。
4. 未经权益所有人同意不得将文件中的内容挪作商业或盈利用途。
5. 人人文库网仅提供信息存储空间,仅对用户上传内容的表现方式做保护处理,对用户上传分享的文档内容本身不做任何修改或编辑,并不能对任何下载内容负责。
6. 下载文件中如有侵权或不适当内容,请与我们联系,我们立即纠正。
7. 本站不保证下载资源的准确性、安全性和完整性, 同时也不承担用户因使用这些下载资源对自己和他人造成任何形式的伤害或损失。

人人文库网所有资源均是用户自行上传分享,仅供网友学习交流,未经上传用户书面授权,请勿作他用。