冲压式管端成型处理机构的设计
45页 16000字数+说明书+开题报告+实习报告+8张CAD图纸【详情如下】
上冲头A4.dwg
上冲头A4.exb
上模A3.dwg
上模A3.exb
下模A3.dwg
下模A3.exb
内封.doc
冲压式管端成型处理机构的设计开题报告.doc
冲压式管端成型处理机构的设计说明书.doc
定位体A4.dwg
定位体A4.exb
定位架A2.dwg
定位架A2.exb
总装图A0.dwg
总装图A0.exb
摘要.doc
机架体A1.dwg
机架体A1.exb
机械毕业设计实习报告.doc
液压原理图A2.dwg
液压原理图A2.exb
目录.doc


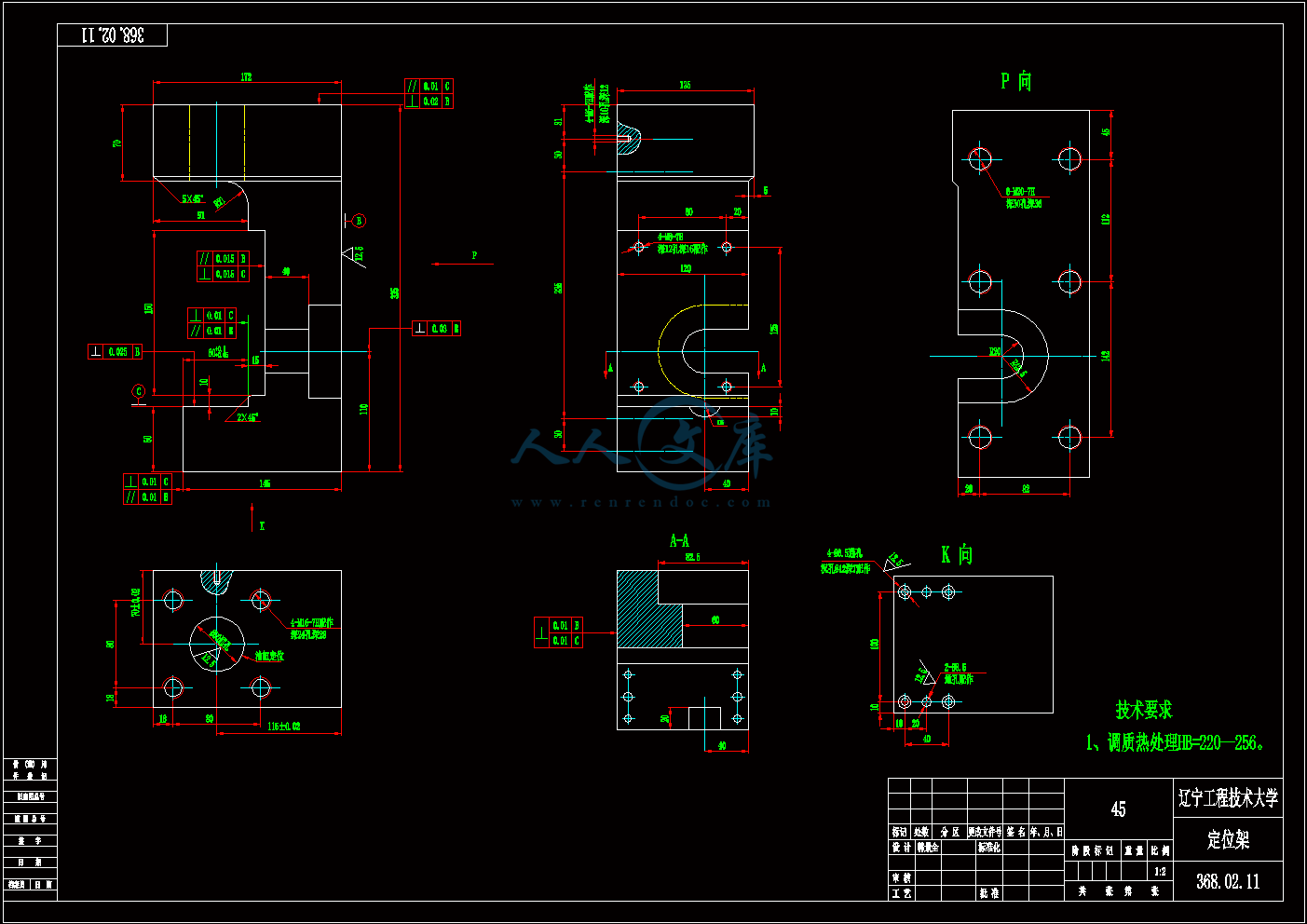

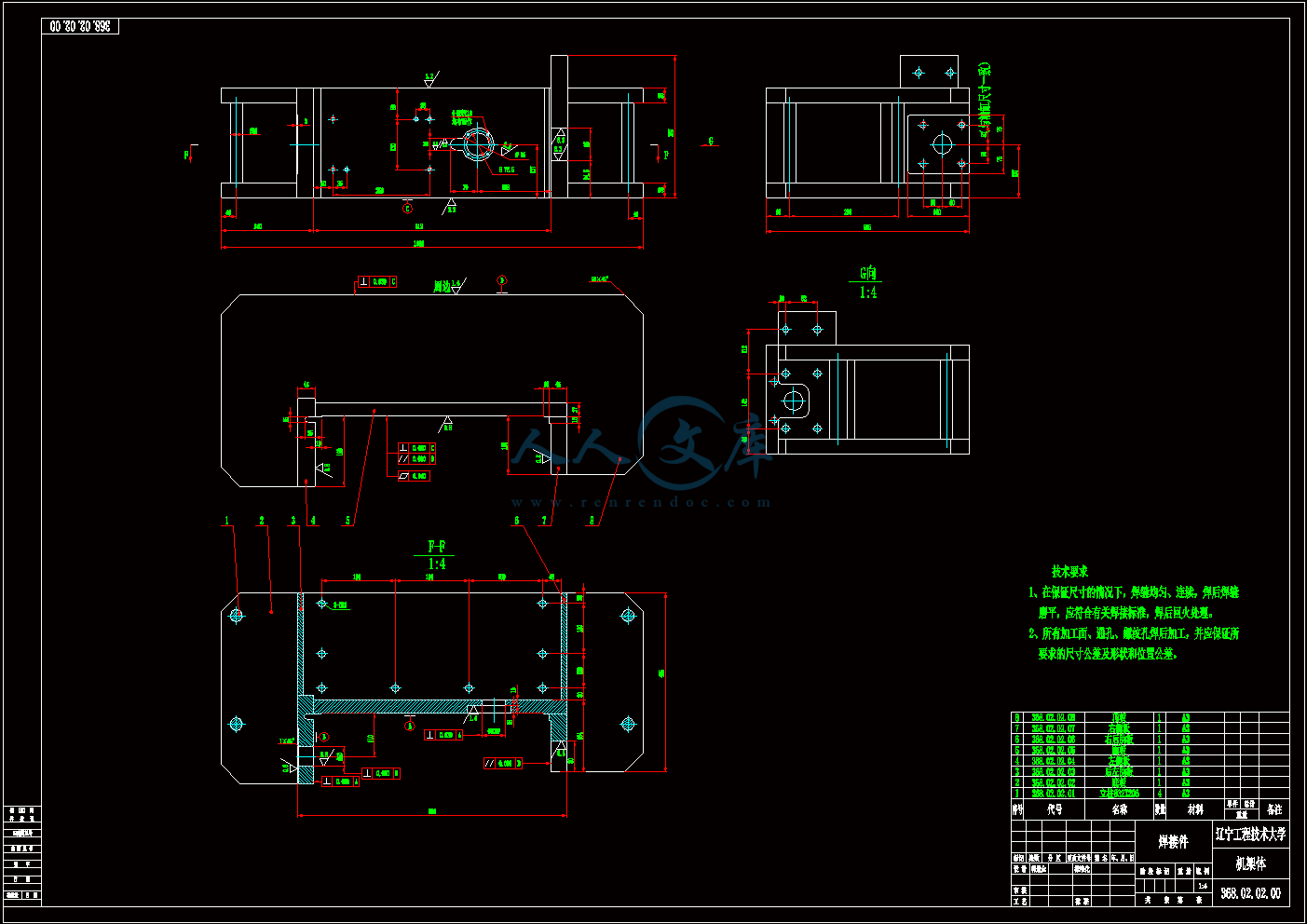


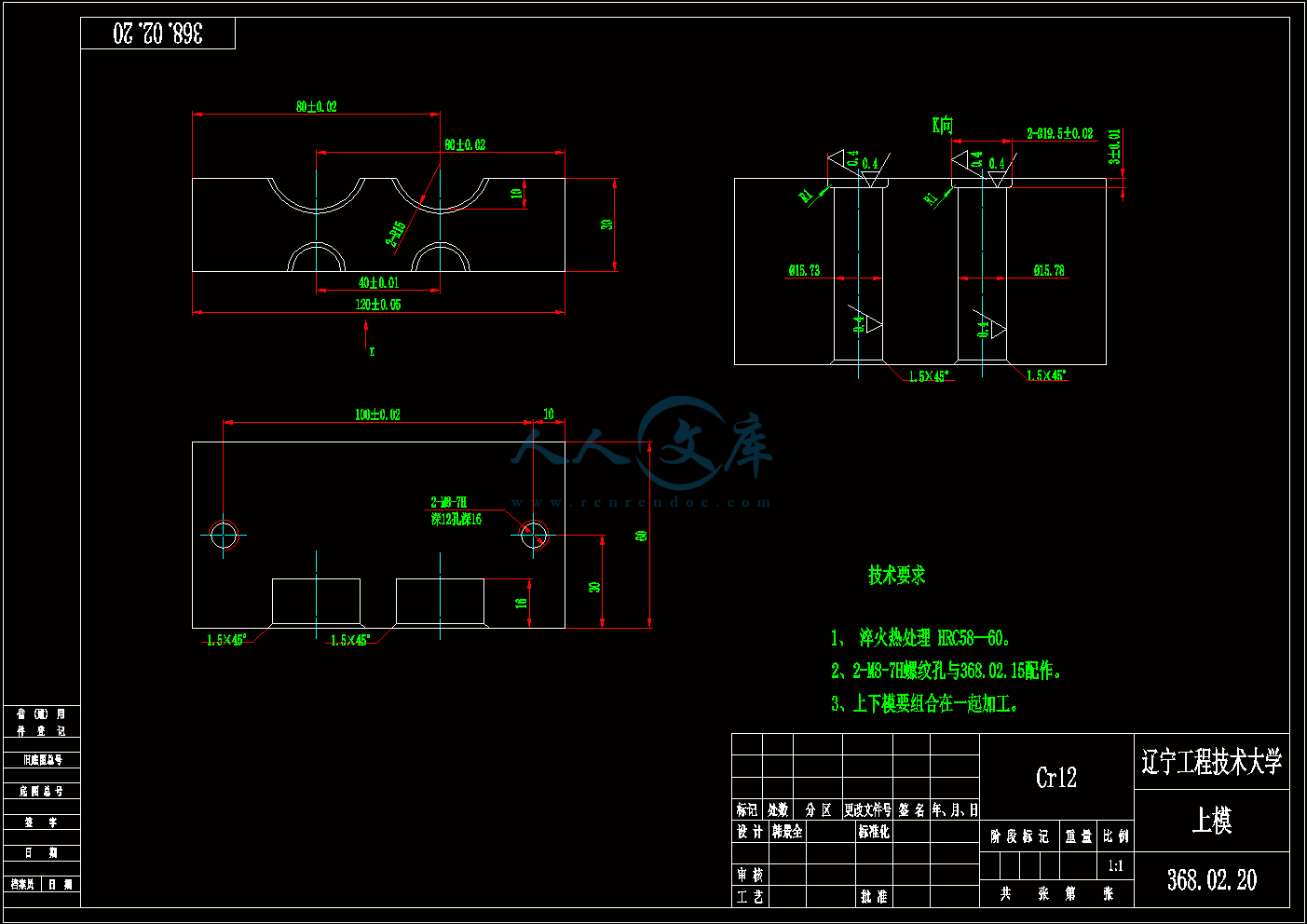
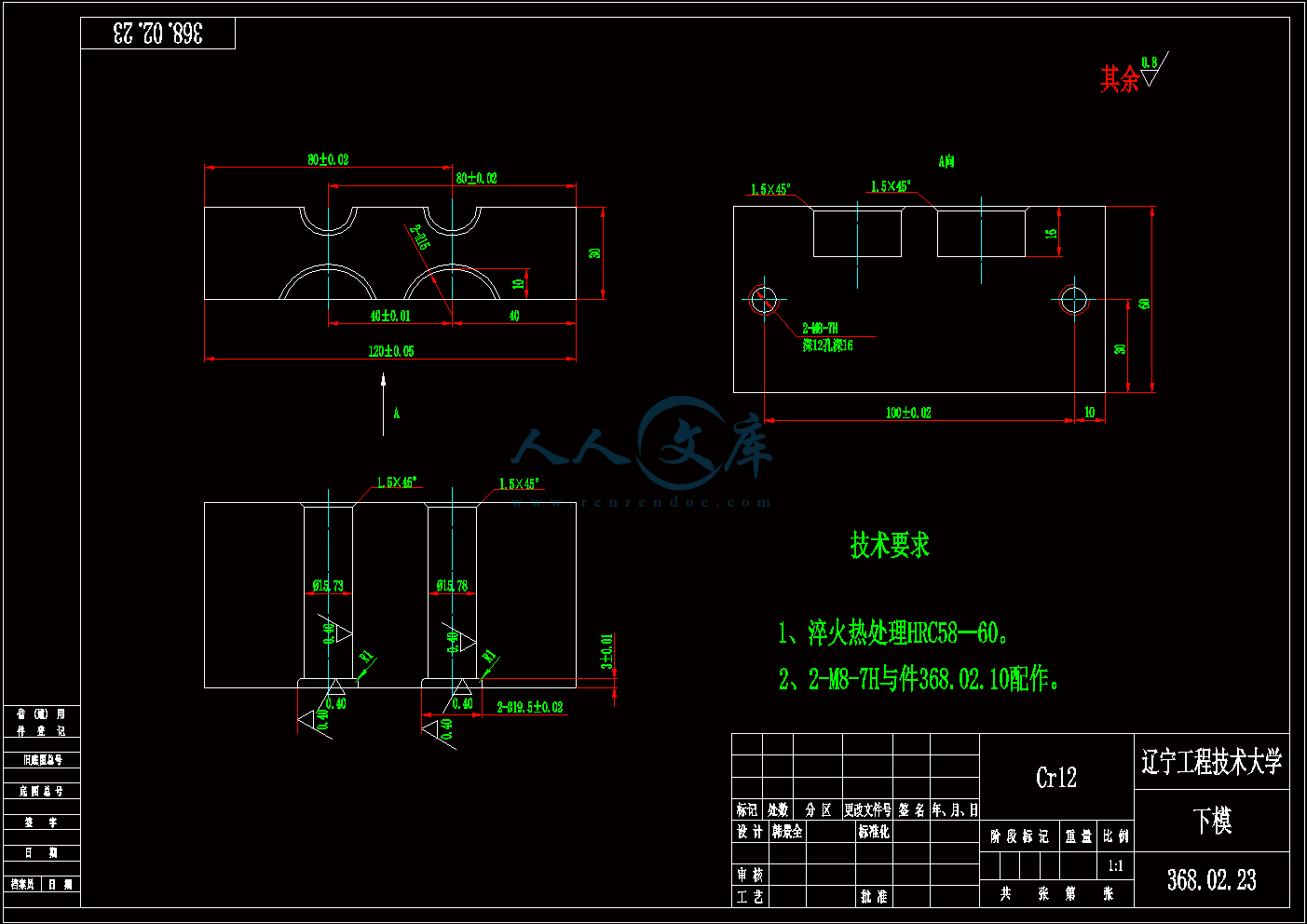
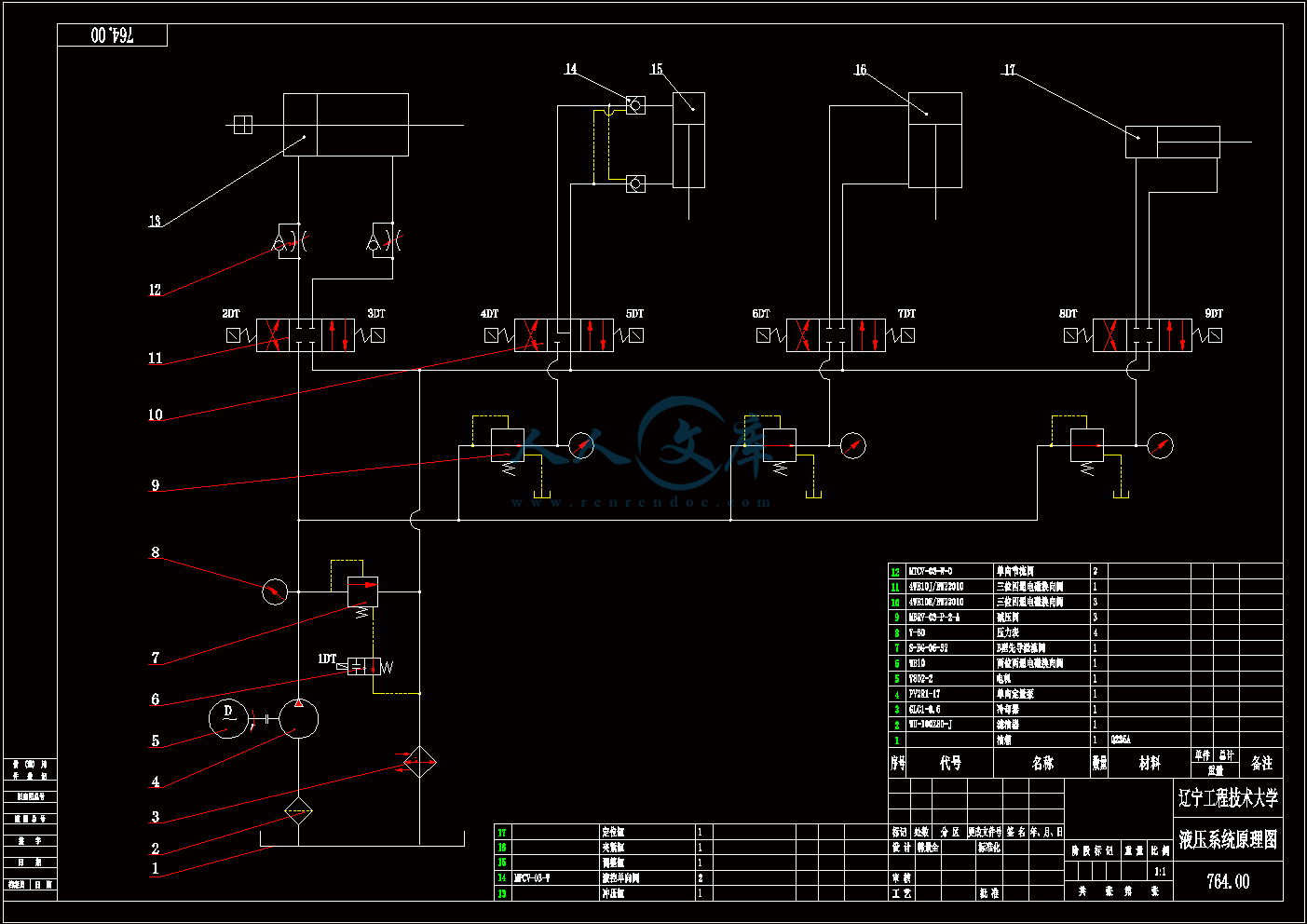
目录
前言1
1 管端成型机总体方案的选定2
1.1无模成型2
1.2 管端偏心回转成型2
1.3 利用NC工作机的管端成型3
1.4 机械成型3
1.5 确定所选方案3
1.6 管端成型处理机构的组成3
2 主机整体结构及各主要工作机构的设计与计算5
2.1 主机整体结构的一般布置5
2.2 管端成型机主机的工作原理6
2.3 机架的结构设计7
2.4 夹紧模具的设计8
2.4.1 材料的选择9
2.4.2 夹紧模具的强度计算10
2.5 冲头的设计10
2.5.1 材料的选择12
2.5.2 冲头的强度计算12
3 管端成型机的液压系统设计13
3.1 设计规格、性能及对液压系统的要求13
3.2 管端成型机的液压系统分析14
3.2.1各液压缸的载荷分析14
3.2.2 管端成型机的液压系统原理图14
3.2.3 液压系统工作循环分析15
3.3 液压元件的选用17
3.3.1 液压阀的选用17
3.3.2 辅助元件的选用18
3.3.3 执行元件的确定19
3.3.4 电动机的选择19
4 管端成型机的液压缸设计计算和泵的参数计算21
4.1 液压缸的设计计算21
4.1.1 液压缸的选用21
4.1.2 胀形力的计算21
4.1.3 冲压缸载荷计算21
4.1.4 冲压缸结构尺寸计算24
4.1.5 计算液压缸的主要结构尺寸24
4.1.6 油缸强度计算27
4.1.7 夹紧油缸的设计计算30
4.1.8 油缸强度计算31
4.1.9 调整油缸和定位油缸的选择33
4.2 泵的参数计算34
4.2.1 泵的选用34
4.2.2 泵的压力计算34
4.2.3 计算所需要的泵的流量34
5 液压系统性能验算36
6 经济技术分析38
结论39
致 谢40
参考文献41
1、处理管径(铜管或铝管):8X1mm;9.5X1.2mm;12.7X1.2mm; 15.8X1.2mm;19X1.5mm。
2、循环节拍:小于18秒(即油缸伸缩速度)。
3、工作方式:冲压方式。
4、操作方式:手工上料. 自动成形。
5、工作压力:≤5Mpa。
6、外形尺寸:≤1450mmX1335mmX1537mm。
管端成型机的工作过程,包括将工件定位、夹紧、冲压和整机冲头工作位置四项主要动作。管端成型机的一个作业循环的组成包括:
定位—工件以手动方式送入夹紧模具体,通过定位油缸推动定位体将工件进行定位。
夹紧—将定位好的工件通过夹紧油缸推动夹紧模具进行夹紧。
冲压—定位油缸退回,由冲压油缸推动滑块体、冲头进行冲压成型。工作结束后各油缸复位。
调整冲头—当有些工件不能一次成型时,可调整下一个冲头进行工作,调整冲头位置是通过油缸推动滑块来实现的。
随着我国汽车行业的不断发展壮大,对汽车空调的需求也随之增大,再加上目前全球气候的变暖,导致民用空调的需求也大大增加。然而,目前国内做空调设备的企业确非常少,而且多数采用进口设备进行加工,这样使空调制造企业的成本增加了许多。空调加工设备有弯管机、冲孔机、折弯机、管端成型机等。管端成型机作为空调加工设备的一种,在整个空调制造过程中起到了关键的作用。
本文研究设计管端成型机主要用于将铝管(还可用于铜管)的管端通过冲压的方式将其收口或扩口、加工成所需的管端形状。管端成型技术主要应用于空调机热交换器或汽车空调热交换器的管端连接。该设备适用于批量生产,可以完成直径为8X1mm;9.5X1.2mm;12.7X1.2mm; 15.8X1.2mm;19X1.5mm的铝管(或铜管)的管端成型加工。目前,国内专门制造用于管端成型的通用机床比较少,大多数都是专用机床,生产效率比较高,但是灵活性小,对于不同管件的加工具有一定的局限性。因此,有必要设计这样一种可以适应不同管件胀形加工的通用机床,并且在不需要进行大批量生产的情况下,代替了小批量单件生产时的手工胀管,而且可以节省时间和生产消耗,提高单件的生产效率,及时满足产品零部件的需要。因此本课题设计的这一产品具有较高的使用价值和普遍性。
关键词: 管端成型机;液压系统;主机; 随着我国汽车行业的不断发展壮大,对汽车空调的需求也随之增大,再加上目前全球气候的变暖,导致民用空调的需求也大大增加。然而,目前国内做空调设备的企业确非常少,而且多数采用进口设备进行加工,这样使空调制造企业的成本增加了许多。空调加工设备有弯管机、冲孔机、折弯机、管端成型机等。管端成型机作为空调加工设备的一种,在整个空调制造过程中起到了关键的作用。
目前国内管端成型方法主要分为管端偏心回转成型、利用NC工作机的管端成型、无模成型、机械成型四种方法。
机械成型是管端成型方法中比较普遍又经济,容易实现工作要求,原理简单易操作。
该设计用于将铝管管端加工铝管管端通过冲压的方式将其收口或扩口、加工成所需的管端形状,这一过程即管端成型过程。管端成型技术主要应用于空调机热交换器或汽车空调热交换器的管端连接。该设备适用于批量生产,可以完成直径为8X1mm;9.5X1.2mm;12.7X1.2mm; 15.8X1.2mm;19X1.5mm的铝管的管端成型加工。目前,国内专门制造用于管端成型的通用机床比较少,大多数都是专用机床,生产效率比较高,但是灵活性小,对于不同管件的加工具有一定的局限性。因此,有必要设计这样一种可以适应不同管件胀形加工的通用机床,并且在不需要进行大批量生产的情况下,代替了小批量单件生产时的手工胀管,而且可以节省时间和生产消耗,提高单件的生产效率,及时满足产品零部件的需要。因此本课题设计的这一产品具有较高的使用价值和普遍性。