液压式数控分度工作台的设计【12张图纸】【优秀】
收藏
资源目录
压缩包内文档预览:
编号:422371
类型:共享资源
大小:2.26MB
格式:RAR
上传时间:2015-04-02
上传人:上***
认证信息
个人认证
高**(实名认证)
江苏
IP属地:江苏
39
积分
- 关 键 词:
-
液压式
数控
分度
工作台
设计
液压式数控分度工作台
图纸
数控工作台
分度工作台
- 资源描述:
-
液压式数控分度工作台的设计
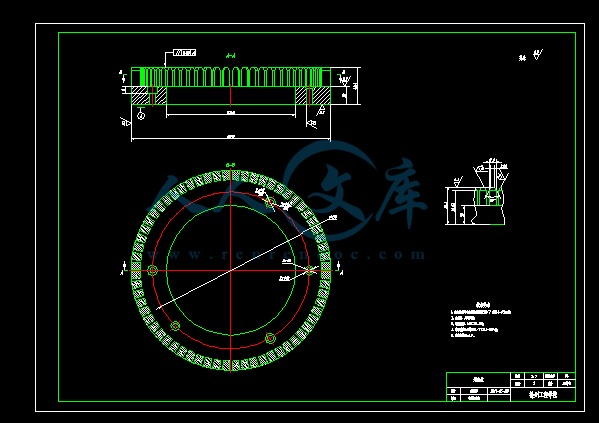
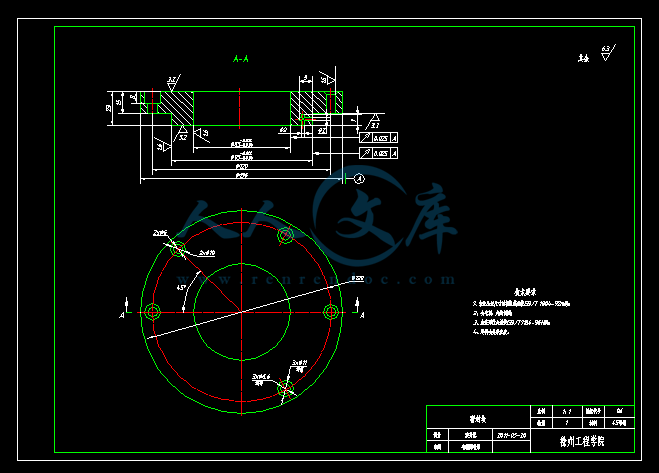

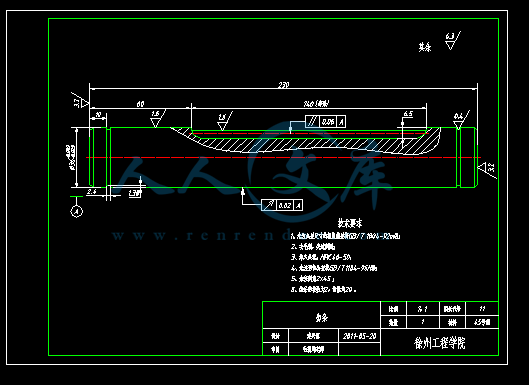

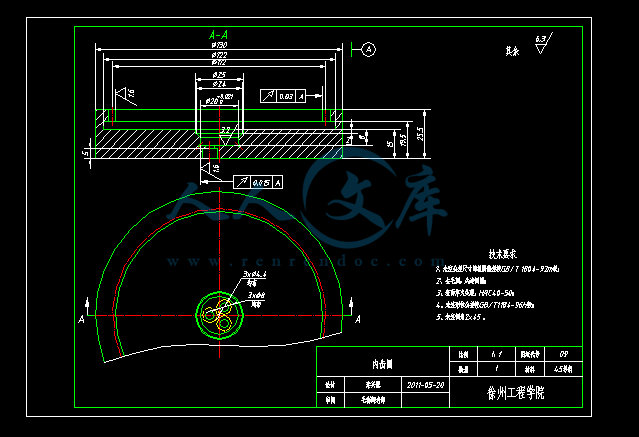
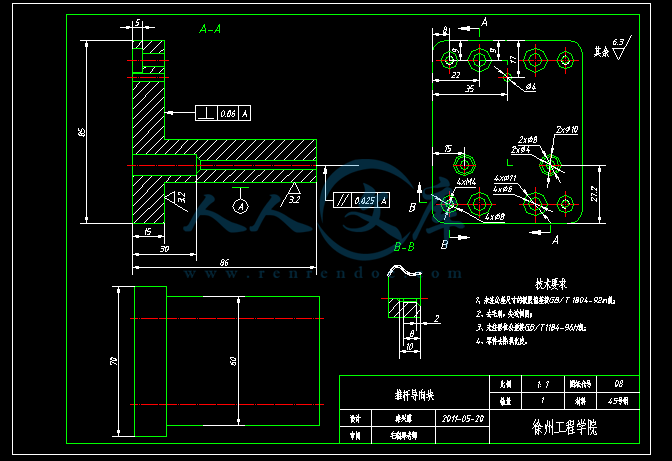


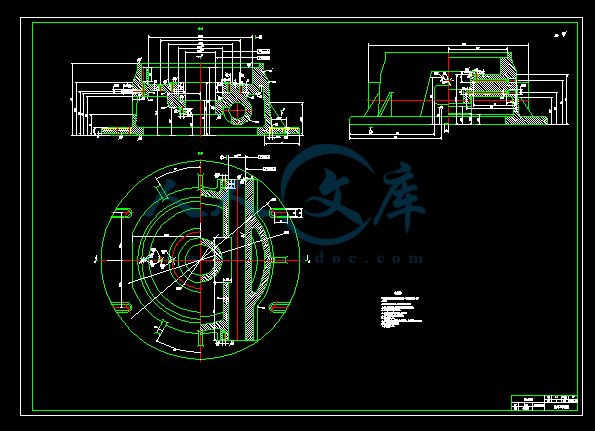
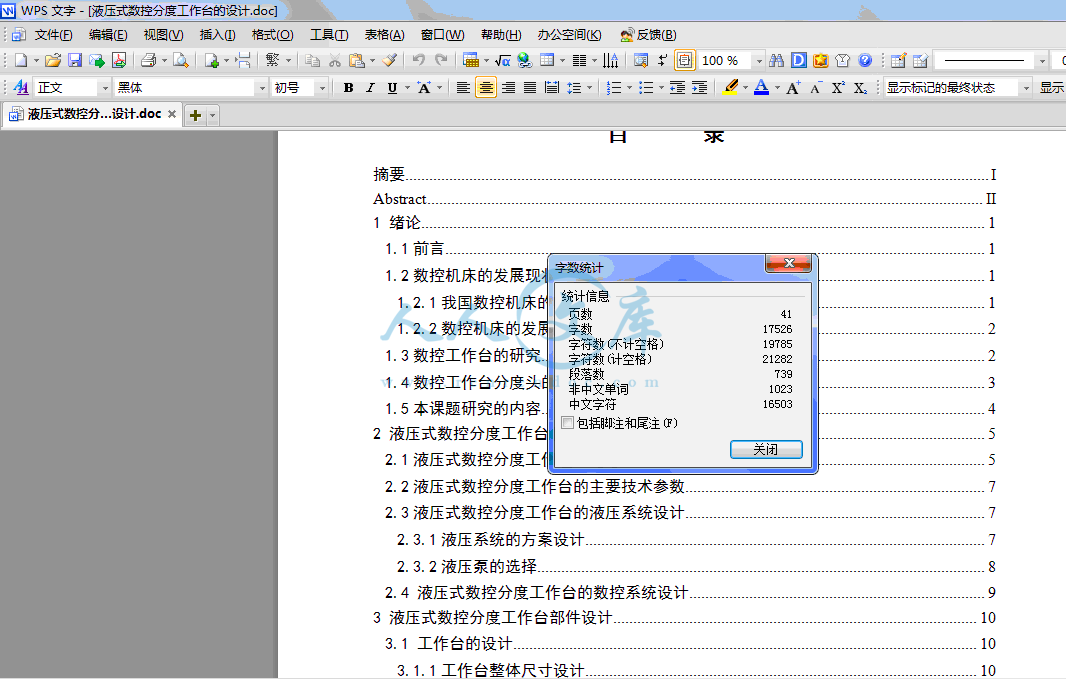
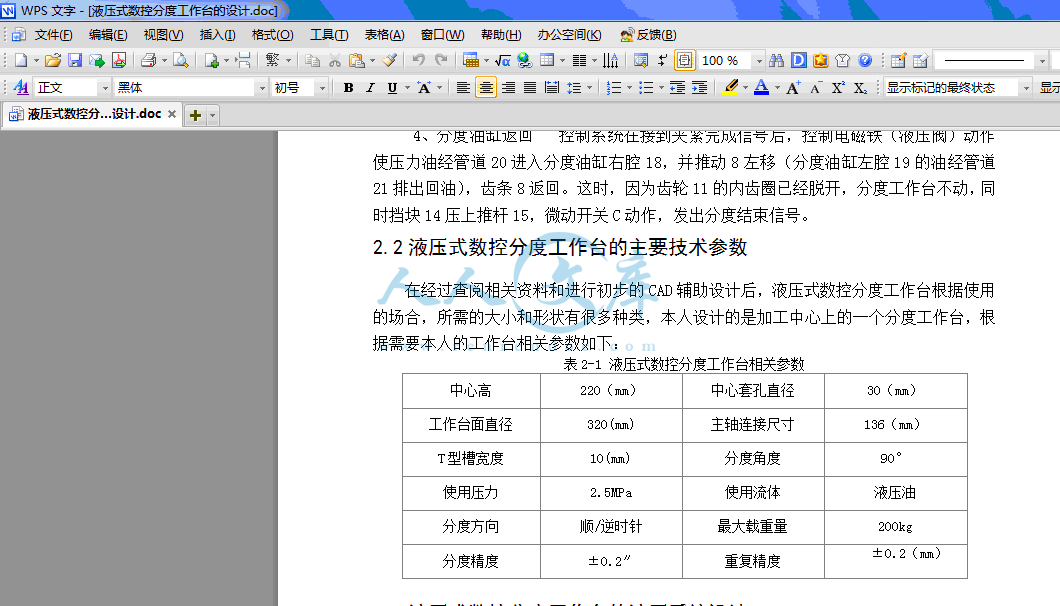

目录
摘要I
AbstractII
1 绪论1
1.1前言1
1.2数控机床的发展现状和趋势1
1.2.1我国数控机床的发展现状1
1.2.2数控机床的发展趋势2
1.3数控工作台的研究2
1.4数控工作台分度头的研究3
1.5本课题研究的内容4
2 液压式数控分度工作台总体方案设计5
2.1液压式数控分度工作台原理设计5
2.2液压式数控分度工作台的主要技术参数7
2.3液压式数控分度工作台的液压系统设计7
2.3.1液压系统的方案设计7
2.3.2液压泵的选择8
2.4 液压式数控分度工作台的数控系统设计9
3 液压式数控分度工作台部件设计10
3.1 工作台的设计10
3.1.1工作台整体尺寸设计10
3.1.2工作台T形槽设计10
3.1.3工作台中心孔设计10
3.1.4工作台螺孔分布设计10
3.2端齿盘设计11
3.3中心轴设计13
3.3.1中心轴尺寸设计13
3.3.2中心轴轴承选择14
3.4活塞设计14
3.5传动系统设计16
3.5.1传动系统总体方案设计16
3.5.2齿轮齿条设计计算17
3.5.4齿圈设计23
3.6工作台底座设计24
3.6.1材料选择24
3.6.2壁厚选择25
3.6.3铸造斜度25
3.6.4加强筋25
3.6.5定位设计26
3.7活塞密封块设计27
3.8推杆导向块设计27
3.9工作台分度工作原理和结构28
3.9.1工作台定位原理和结构28
3.9.2工作台松开、夹紧原理和结构29
3.9.3工作台分度原理和结构29
4 液压式数控分度工作台受力校核31
4.1工作台螺栓受力校核31
结论34
致谢35
参考文献36
1 绪论
1.1前言
数控技术及装备是发展新兴高新技术产业和尖端工业(如信息技术及其产业、生物技术及其产业、航空、航天等国防工业产业)的使能技术和最基本的装备。马克思曾经说过“各种经济时代的区别,不在于生产什么,而在于怎样生产,用什么劳动资料生产。”制造技术和装备就是人类生产活动的最基本的生产资料,而数控技术又是当今先进制造技术和装备最核心的技术。当今世界各国制造业钢钒采用数控技术,以提高制造能力和水平,提高对动态多变市场的适应能力和竞争能力。此外世界上各工业发达国家还将数控技术及数控装备列为国家的战略物资,不仅采取重大措施来发展自己的数控技术及其产业,而且在“高精尖”数控关键技术和装备方面对我国实行封锁和限制政策。总之,大力发展以数控技术为核心的先进制造技术已成为世界各发达国家加速经济发展、提高综合国力和国家地位的重要途径。
数控机床是装备制造业的工作母机,是实现制造技术和装备现代化的基石,是保证高技术产业发展和国防军工现代化的战略装备。纵观振兴装备制造业的16个关键领域,每个领域的振兴都需要大批先进的数控机床来装备,如发展大型火力发电和核电机组、制造大型化工设备、开发大型海洋运输船舶、研制大型薄板冷热连轧成套设备、发展高速列车、新型地铁和轨道交通车辆等,都需要大批高速、精密、高效和专用数控机床来加工制造。同时,数控机床作为国防军工的战略装备,是各种武器装备最重要的制造手段,是国防军工装备现代化的重要保证。国际上一些发达国家意志把高性能数控机床作为战略物资而严加控制,限制我国进口高性能数控机床。
目前,由于我国数控机床产业发展相对滞后,已经制约了整个装备制造业的发展,直接影响到国防军工的产业安全。国内外装备制造业的发展经验表明,发展装备制造业,数控机床是基础,因此,全面落实科学发展观,加快发展我国数控机床产业,具有基础性、前瞻性、全局性的战略意义。
1.2数控机床的发展现状和趋势
1.2.1我国数控机床的发展现状
我国对数控机床及数控技术的研究和开发始于1958年,一直到20世纪60年代中期还处在研制、开发时期。1965年,国内开始研制晶体管数控系统。20世纪60年代末至70年代研制成功立式数控铣床、CJK-18数控系统和数控非圆齿轮插齿机。从20世纪70年代开始,我国的数控技术在车、铣、镗、磨、齿轮加工、电加工等领域全面展开,数控加工中心在上海、北京研制成功。但由于稳定性未得到解决,因此没有得到广泛推广。在这一时期,数控线切割机床由于结构简单、使用方便、价格低廉,在模具数控加工中得到了广泛应用和推广。20世纪80年代,我国从日本FANUC公司引进了部分数控系统和直流伺服电动机、直流主轴电机技术,以及从美国、欧洲等发达国家引进一些新的技术,并进行了国产商品化生产,这些数控系统可靠性高、性能稳定、功能齐全,推动了我国数控机床稳定发展,使我国的数控机床在性能和质量上产生了一个质的飞跃。
“十五”期间,我国机床工业连续几年快速发展,到2005年我国机床产值从“九五”末期列世界第八位,跃居到世界第三位。其中,2005年数控金切机床产量达到6万台,是2000年1.4万台的4.3倍。以“高速、精密、智能、复合”为方向,科技创新和产品开发取得了显著进步,开发了多轴联动加工中心、复合加工机床、高速精密数控机床等多项新产品,在国民经济建设中发挥了重要作用。目前,数控机床品种达到了1500多种。机床行业通过国内企业和企业集团,如沈阳机床(集团)公司和大连机床集团公司机床年销额已进入世界机床企业前十五名。“十五”期间,我国机床工业的加速发展为振兴装备制造业初步奠定了发展基础。
但从总体来看,我国机床工业与世界先进水平相比,差距仍然十分明显:一是国产高档数控机床在品种、水平和数量上远远满足不了国内发展需求,高档数控机床目前仍然大量进口;二是数控机床功能部件和数控系统发展滞后,成为我国数控机床产业发展瓶颈;三是机床制造企业技术装备水平不高,制造能力、综合管理和服务能力等方面不能满足市场快节奏发展的要求。
1.2.2数控机床的发展趋势
- 内容简介:
-
Machine tool numerical control reformsFirst, CNC systems and the development trend of history1946 birth of the worlds first electronic computer, which shows that human beings created to enhance and replace some of the mental work tools. It and human agriculture, industrial society in the creation of those who merely increase compared to manual tools, from a qualitative leap for mankinds entry into the information society laid the foundation. Six years later, in 1952, computer technology applied to the machine in the United States was born first CNC machine tools. Since then, the traditional machine produced a qualitative change. Nearly half a century since the CNC system has experienced two phases and six generations of development. 1.1, Numerical Control (NC) phase (1952 to 1970)Early computers computational speed low and the prevailing scientific computing and data processing is not affected, but can not meet the requirements of real-time control machine. People have to use digital logic circuit tied into a single machine as a dedicated computer numerical control system, known as the hardware connection NC (HARD-WIRED NC), called the Numerical Control (NC). With the development of components of this phase after three generations, that is, in 1952 the first generation - tube; 1959 of the second generation - transistor; 1965 of the third generation - small-scale integrated circuits.1.2, Computer Numerical Control (CNC) phase (1970 to present)To 1970, GM has been a small computer and mass-produced. So it transplant system as the core component of NC, have entered a Computer Numerical Control (CNC) stage (in front of the computer should be universal word omitted). To 1971, the United States INTEL company in the world will be the first time the two most core computer components - computing and controller, a large-scale integrated circuit technology integration in a chip, called the microprocessor (MICROPROCESSOR) , also known as the central processing unit (CPU).1974 microprocessor to be used in CNC system. This is because the function of the computer is too small to control a machine tool capacity affluent (the time has been used to control more than one machine, called Group Control), as a reasonable economic use of the microprocessor. Minicomputer reliability and then not ideal. Early microprocessor speed and functionality while still not high enough, but can be adopted to solve the multi-processor architecture. As microprocessor core is a general computer components, it is still known as the CNC.By 1990, PC machines (personal computers, domestic habits that computer) performance has been developed to a high stage, as a CNC system to meet the requirements of the core components. NC system based on PC has now entered the stage.In short, CNC has also experienced a stage three generations. That is, in 1970s fourth generation - small computer; 1974 of the fifth generation - microprocessors and the sixth-generation 1990 - Based on the PC (called PC-BASED abroad).Also pointed out that, although the foreign computer has been renamed NC (CNC), but China still customary said Numerical Control (NC). Therefore, we stress the day-to-day NC, in essence, is that computer numerically controlled.1.3, the trend of future development of NC1.3.1 continue to open, the sixth generation of PC-based developmentBased on the PC with the open, low-cost, high reliability, rich in resources such as hardware and software features, and more CNC system manufacturers will embark on this path. At least it used PC as a front-end machine, to deal with the human-machine interface, programming, networking and communications problems, the former NC Some systems have the mandate. PC machine with the friendly interface, will be universal to all CNC system. Remote communications, remote diagnostics and maintenance will be more widespread.1.3.2 high-speed and high-precision DevelopmentThis is to adapt to high-speed and high-precision machine tools to the needs of the development direction.1.3.3 intelligent direction to the development With artificial intelligence in the computer field infiltration and the continuing development of the intelligent numerical control system will be continuously improved.(1)adaptive control technologyCNC system can detect some important information in the process, and automatically adjust system parameters to improve the system running state purposes.(2)the introduction of expert guidance processing systemthe experience of skilled workers and experts, processing and the general rules of law of special deposit system, the process parameters to the database as the foundation, and establish artificial intelligence expert system.(3)introduction of Fault Diagnosis Expert System(4)intelligent digital servo drivesAutomatic Identification can load, and automatically adjust parameters to get the best drive system operation.Second, CNC of the need for transformation2.1, microscopic view of the necessity of From the micro perspective, CNC machine tools than traditional machines have the following prominent superiority, and these advantages are from the NC system includes computer power.2.1.1 can be processed by conventional machining is not the curve, surface and other complex partsBecause computers are superb computing power can be accurately calculated instantaneous each coordinate axis movement exercise should be instantaneous, it can compound into complex curves and surfaces.2.1.2 automated processing can be achieved, but also flexible automation to increase machine efficiency than traditional 3 to 7 times.Because computers are memory and storage capacity, can be imported and stored procedures remember down, and then click procedural requirements to implement the order automatically to achieve automation. CNC machine tool as a replacement procedures, we can achieve another work piece machining automation, so that single pieces and small batch production can be automated, it has been called flexible automation.2.1.3 high precision machining parts, the size dispersion of small, easy to assemble, no longer needed repair.2.1.4 processes can be realized more focused, in part to reduce the frequent removal machine.2.1.5 have automatic alarm, automatic control, automatic compensation, and other self-regulatory functions, thus achieving long unattended processing.2.1.6 derived from the benefits of more than five.Such as: reducing the labor intensity of the workers, save the labor force (one can look after more than one machine), a decrease of tooling, shorten Trial Production of a new product cycle and the production cycle, the market demand for quick response, and so on.These advantages are our predecessors did not expect, is a very major breakthrough. In addition, CNC machine tools or the FMC (Flexible Manufacturing Cell), FMS (flexible manufacturing system) and CIMS (Computer Integrated Manufacturing System), and other enterprises, the basis of information transformation. NC manufacturing automation technology has become the core technology and basic technology.2.2, the macro view of the necessity From a macro perspective, the military industrial developed countries, the machinery industry, in the late 1970s, early 1980s, has begun a large-scale application of CNC machine tools. Its essence is the use of information technology on the traditional industries (including the military, the Machinery Industry) for technological transformation. In addition to the manufacturing process used in CNC machine tools, FMC, FMS, but also included in the product development in the implementation of CAD, CAE, CAM, virtual manufacturing and production management in the implementation of the MIS (Management Information System), CIMS, and so on. And the products that they produce an increase in information technology, including artificial intelligence and other content. As the use of information technology to foreign forces, the depth of Machinery Industry (referred to as information technology), and ultimately makes their products in the international military and civilian products on the market competitiveness of much stronger. And we in the information technology to transform traditional industries than about 20 years behind developed countries. Such as possession of machine tools in China, the proportion of CNC machine tools (CNC rate) in 1995 to only 1.9 percent, while Japan in 1994 reached 20.8 percent, every year a large number of imports of mechanical and electrical products. This also explains the macro CNC transformation of the need.Third, CNC machine tools and production lines of the transformation of the market 3.1, CNC transformation of the market My current machine total more than 380 million units, of which only the total number of CNC machine tool 113,400 Taiwan, or that Chinas CNC rate of less than 3 percent. Over the past 10 years, Chinas annual output of about 0.6 CNC machine tools to 0.8 million units, an annual output value of about 1.8 billion yuan. CNC machine tools annual rate of 6 per cent. Chinas machine tool easements over age 10 account for more than 60% below the 10 machines, automatic / semi-automatic machine less than 20 per cent, FMC / FMS, such as a handful more automated production line (the United States and Japan automatic and semi-automatic machine, 60 percent above). This shows that we the majority of manufacturing industries and enterprises of the production, processing equipment is the great majority of traditional machine tools, and more than half of military age is over 10 years old machine. Processing equipment used by the prevalence of poor quality products, less variety, low-grade, high cost, supply a long period, in view of the international and domestic markets, lack of competitiveness, and a direct impact on a companys products, markets, efficiency and impact The survival and development of enterprises. Therefore, we must vigorously raise the rate of CNC machine tools. 3.2, import equipment and production lines of the transformation of NC market Since Chinas reform and opening up, many foreign enterprises from the introduction of technology, equipment and production lines for technological transformation. According to incomplete statistics, from 1979 to 1988 10, the introduction of technological transformation projects are 18,446, about 16.58 billion US dollars. These projects, the majority of projects in Chinas economic construction play a due role. Some, however, the introduction of projects due to various reasons, not equipment or normal operation of the production line, and even paralyzed, and the effectiveness of enterprises affected by serious enterprise is in trouble. Some of the equipment, production lines introduced from abroad, the digestion and absorption of some bad, spare parts incomplete, improper maintenance, poor operating results; only pay attention to the introduction of some imported the equipment, apparatus, production lines, ignore software, technology, and management, resulting in items integrity, and potential equipment can not play, but some can not even start running, did not play due role, but some production lines to sell the products very well, but not because of equipment failure production standards; because some high energy consumption, low pass rate products incur losses, but some have introduced a longer time, and the need for technological upgrading. Some of the causes of the equipment did not create wealth, but consumption of wealth. These can not use the equipment, production lines is a burden, but also a number of significant assets in stock, wealth is repaired. As long as identifying the main technical difficulties, and solve key technical problems, we can minimize the investment and make the most of their assets in stock, gain the greatest economic and social benefits. This is a great transformation of the market. Fourth, NC transformation of the content and gifted missing 4.1, the rise of foreign trade reform In the United States, Japan and Germany and other developed countries, and their machine transform ation as new economic growth sector, the business scene, is in a golden age. The machine, as well as technology continues to progress, is a machine of the eternal issue. Chinas machine tool industry transformation, but also from old industries to enter the CNC technology mainly to the new industries. In the United States, Japan, Germany, with CNC machine tools and technological transformation of production lines vast market, has formed a CNC machine tools and production lines of the new industry. In the United States, transforming machine tool industry as renewable (Remanufacturing) industry. Renewable industry in the famous companies: Borsches engineering company, atoms machine tool company, Devlieg-Bullavd (Bo) services group, US equipment companies. Companies in the United States-run companies in China. In Japan, the machine tool industry transformation as machine modification (Retrofitting) industry. Conversion industry in the famous companies: Okuma engineering group, Kong 3 Machinery Company, Chiyoda Engineering Company, Nozaki engineering company, Hamada engineering companies, Yamamoto Engineering Company. 4.2, the content of NC Machine tools and production line NC transformation main contents of the following: One is the restoration of the original features of the machine tools, production line of the fault diagnosis and recovery; second NC, in the ordinary machine augends significant installations, or additions to NC system, transformed into NC machine tools, CNC machine tools; its Third, renovation, to improve accuracy, efficiency and the degree of automation, mechanical, electrical part of the renovation, re-assembly of mechanical parts processing, restore the original accuracy of their production requirements are not satisfied with the latest CNC system update; Fourth, the technology updates or technical innovation, to enhance performance or grades, or for the use of new technology, new technologies, based on the original technology for large-scale update or technological innovation, and more significantly raise the level, and grades of upgrading. 4.3, NC transformation of the gifted missing 4.3.1 reduce the amount of investment, shorter delivery time Compared with the purchase of new machine, the general can save 60% to 80% of the costs and transforming low-cost. Especially for large, special machine tools particularly obvious. General transformation of large-scale machine, spent only the cost of the new machine purchase 1 / 3, short delivery time. But some special circumstances, such as high-speed spindle, automatic tray switching systems and the production of the installation costs too costly and often raise the cost of 2 to 3 times compared with the purchase of new machine, only about 50 percent of savings investment. 4.3.2 stable and reliable mechanical properties, structure limitedBy the use of bed, column, and other basic items are heavy and solid casting components, rather than kind of welding components of the machine after the high-performance, quality, and can continue to use the new equipment for many years. But by the mechanical structure of the original restrictions, it is not appropriate to the transformation of a breakthrough. 4.3.3 become familiar with the equipment, ease of operation and maintenanceThe purchase of new equipment, new equipment do not know whether to meet the processing requirements. Transformation is not, can be used to calculate the machine processing capacity; In addition, since the use of many years, the operator of the machine has long been understood that in the operation, use and maintenance of the training time is short, quick. Transformation of the machine tools installed, we can achieve full load operation. 4.3.4 can take full advantage of the existing conditions Take full advantage of the existing foundation, not like buying new equipment as necessary to build a foundation. 4.3.5 can be used as control technologyAccording to the development speed of technological innovation and in a timely manner increased level of automation in production equipment and efficiency, improve the quality of equipment and grades, and the old machine will be replaced by the current level of machine. Fifth, the choice of NC System NC system are the three major types of transformation, in accordance with specific circumstances Choose. 5.1, stepper motor drive the open-loop system The servo drive system is stepper motor, stepper motor power, such as electro-hydraulic pulse motor. NC system by sending commands to the progress of pulse, the drive control and power amplifier circuit, the stepper motor rotate through the gears with ball screw drive of the implementation of parts. As long as control commands the number of pulses, frequency and electricity sequence can control the implementation of parts of the displacement movement, speed and direction of movement. Such a system does not require the test will be the actual position and velocity feedback to the input, so called open-loop system, the system accuracy of the displacement in the major decisions of the stepper motor angular displacement accuracy, transmission gear and other components of the leads crew pitch accuracy, the accuracy of the lower displacement. The system is simple, convenient debugging maintenance, reliable, low cost, easy modification success. 5.2, or asynchronous motor DC Motor Drive, grating feedback loop measurement NC system And the open-loop system is the difference between a system: from the grating, such as position sensors for simultaneous detection device measured the actual position feedback signals, at any time and to compare the value will be the difference between the two enlarge and change, driven implementing agencies , given the speed of elimination of bias towards the direction of movement, until a given position feedback and the actual location of the margin of zero. Feed the closed-loop system in the structure than to the open-loop system into the complex, high-cost, strict requirements on the environment at room temperature. Design and debugging difficult than open-loop system. However, can be compared to the open-loop system into higher accuracy, faster speed, greater power drive characteristic indicators. Under the technological requirements and decide whether or not to adopt this system. 5.3, AC / DC servo motor drive, the semi-encoder feedback loop NC system Semi-closed-loop system detection devices installed in the middle of transmission, the implementation of indirect measurement components position. It can only be part of the internal loop compensation system components of the error and, therefore, it compared the accuracy of the closed-loop system of low accuracy, but its structure and debug than simple closed-loop system. Will be in the angular displacement detection devices and speed detection devices and make a servo motor when there was no need to consider the overall position of the installation of detection devices. NC system for the current production companies more manufacturers, such as the famous German company SIEMENS, Japan FANUC companies; Everest domestic companies such as China, Beijing Aerospace CNC System Corporation, Shenyang and the central high-grade companies NC National Engineering Research Center.NC selection system is based mainly CNC machine modified to achieve the various precision, motor-driven power and user requirements. Sixth, the transformation of NC modification of the main mechanical components A new CNC machine tools in the design to achieve: a high static and dynamic stiffness of movement of the friction coefficient between small, transmission without clearance; big power; easy operation and maintenance. CNC transformation should be possible to achieve the above requirements. NC devices that can not be connected together with the general machine tools to reach the requirements of the NC machine tool, should also be major components corresponding to the transformation of up to a certain design requirements can be anticipated adaptation. 6.1, sliding Guideway On the NC lathe, in addition to a general guide lathes and precision of sexual orientation, but also a good Naimaca, wear characteristics, and reduce the frictional resistance to the death zone. At the same time there must be enough stiffness to reduce rail deformation on the impact of machining accuracy, a reasonable guide protection and lubrication. 6.2, deputy Gear General Machine concentrated in the main gear box and gearbox in the spindle. In order to ensure transmission accuracy, the use of CNC machine tool accuracy of gear higher grades than the general machine tools. In the structure must be able to achieve seamless transmission, thus transforming, machine main gear must meet the requirements of CNC machine tools, in order to ensure accuracy machining. 6.3, and the ball screw sliding leadscrew Screw-drive directly related to the transmission chain accuracy. Screw selection depends largely on the accuracy of the processing of requests and drag torque requirements. Accuracy is the main requirement of processing may be sliding Screw, but should check the leadscrew wear, such as pitch and pitch error accumulated error and match Nut Gap. Sliding leadscrew general should not be less than six, the nut is too large gap replacement nut. The use of a sliding leadscrew relatively lower prices of ball screw, but it is difficult to meet the high precision machining. Ball screw friction losses small, high efficiency, the transmission efficiency of more than 90% of high accuracy, long life; starting torque and the torque of close campaigns, starting torque motor can be reduced. So to meet high precision machining requirements. 6.4, security Efficiency must be security as the prerequisite. Machine transformation in the light of the actual situation, we should take corresponding measures must not be ignored. Ball screw is sophisticated components, work to prevent dust particular chip and hard sand into the raceway. Screw in the vertical can also increase overall plate shields. And the extension units at both ends of the sliding contact surface Guide to seal well, absolutely rigid Coarse prevent the entry of foreign matter sliding surface damage Guide. Seventh, the main steps of CNC machine tools 7.1, for the determination of transformationThrough analysis of the feasibility of transforming the future, we can against a Taiwan or a few machines determine the current status of reform programmes, which are generally include: 7.1.1 mechanical and electrical repair of combining Generally speaking, the need for a transformation of the electrical machine, are subject to mechanical repairs. Repairs to determine the requirements, scope, content must be decided by electrical machinery required to transform the structure of the request; transformation to determine electrical and mechanical repair, alteration between the staggered time requirements. The mechanical properties of intact electrical transform the basis of success. 7.1.2 easy first, and to the overall situation after the first localThe removal of the original system must control the original drawings, carefully, to make drawings in a timely manner marked to prevent the demolition or omission (of local circumstances). In the process of demolition will discover some new system design in the gaps, and that should be promptly added, removed and parts of the system should be disaggregated, safekeeping, in case of failure or partial failure reinstated. There is a definite value, and can be used for spare parts for other machines. Must not extravagantly used and misplaced. 7.2 reasonable arrangements for a new location and routing system Under the new system design drawings and reasonable new system configurations, including fixed box, panel installation, alignments, and the fixed position adjustment components, sealing and necessary, such as decoration. Connection must be a clear division of work, it was reviewed inspection to ensure connectivity of norms, diameter appropriate, accurate, reliable handsome. 7.3 Debugging Commissioning must be identified in advance by the steps and requirements. Debugging should be cool-headed, keep records, in order to identify a nd solve problems. Commissioning of the first test sensitivity security protection systems to prevent physical, equipment accidents. Debugging the scene must be cleaned, no superfluous items; coordinates extension units in the campaign centre of the whole trip; empty can test, first empty after loading; can simulate the test, after the first real dynamic simulation; can manually the upper hand After moving automatically. 7.4, acceptance and post-work Acceptance of the work to employ the staff to join, has been developed in accordance with the acceptance criteria. The transformation of the late work is also very important, it is conducive to enhancing the level of technical projects and equipment as soon as possible so that production. Acceptance and post include: 7.4.1 machine mechanical properties acceptanceAfter mechanical repairs and maintenance as well as a full transformation, the mechanical properties of the machine tools should meet the requirement, in the geometric accuracy should be within the limits prescribed. 7.4.2 electrical control function and control accuracy acceptance Electrical control the various functions of action must be normal, sensitive and reliable. Application control accuracy of the system itself functions (such as stepping dimensions, etc.) and standard measurement apparatus (such as laser interferometer, coordinate measurement machines) inspection, the scope of accuracy achieved. At the same time also and the transformation of the former machine tool accuracy of the various functions and to contrast, poor access to quantifiable indicators. 7.4.3 specimen cutting Acceptance You can refer to the CNC machine tool cutting at home and abroad specimen standards, qualified operatives, with the programming staff to test cutting. Acceptance specimen cutting machine stiffness can be cutting, noise, trajectory, and other related actions, the general should not be used for product components specimen use. 7.4.4 drawings, information acceptance Machine transformation of the latter should be timely drawings (including schematics, layout plans, wiring diagram, ladder diagram, etc.), information (including various brochures), the transformation of files (including the transformation before and after the various records) summary, collating, transfer to stall. Maintain data integrity, effective, continuous, and that the future stability of the equipment running is very important. 7.4.5 summing up, enhancing After the end of each should be promptly summed up, helps improve the operational level of technical personnel, but also conducive to the whole enterprise technical progress. 8, several examples of NC1, use of X53 milling SIEMENS 810M 1998, the company invested 200,000 yuan, with Germanys Siemens 810 M CNC system, 611 A AC servo drive system for the companys X53 as a model of the milling machine for X, Y, Z three-axis NC transformation of the original reservation Spindle and cooling systems; transformation of the three-axis machine used in the roller screw and gear drive mechanism. Transformation of the entire work includes mechanical design, electrical design, PLC and the establishment of procedures for debugging, machine overhaul and, finally, the components are installed and debug. Milling After the transformation, processing effective itinerary X / Y / Z-axis respectively 880/270/280 mm; maximum speed X / Y / Z-axis respectively 5000/1500/800 mm / min; manual speed X / Y / Z-axis respectively 3000/1000/500 mm / min; machining accuracy of 0.001mm. Coordinate machine can be linked to complete all kinds of complex curves and surfaces processing.2, and Step by GSK980T driven system of the C6140 Lathe1999, the company invested 80,000 yuan, a Guangzhou NC plant production GSK980T NC system, DY3 hybrid stepping drive unit for the companys C6140 longer a lathe X and Z axes to transform the two retention The main axis of the original system and the cooling system; transformation of the two-axis machine used in the roller screw and belt drive mechanism. Transformation of the entire work includes mechanical design, electrical design, machine overhaul and the components are installed and debug. Lathe After the transformation, processing effective itinerary X / Z-axis respectively 390/1400 mm; maximum speed X / Z-axis respectively 1200/3000 mm / min; manual speed of 400 mm / min; manual for the rapid X / Z-axis respectively for the 1200/3000 mm / min; machine smallest mobile units of 0.001 mm. 3, and GSK980T with AC servo drive system of the C6140 Lathe 2000, NC plant in Guangzhou with production GSK980T NC system, DA98 AC servo unit and 4-position automatic tool carrier of a motor factory lathe C6140-X, Z two-axis NC transformation of the original reservation the spindle and cooling systems; transformation of the two-axis machine used in the roller screw and belt drive mechanism. Transformation of the entire work includes mechanical design, electrical design, machine overhaul and the components are installed and debug. Lathe After the transformation, processing effective itinerary X / Z-axis respectively 390/730 mm; maximum speed X / Z-axis respectively 1200/3000 mm / min; manual speed of 400 mm / min; manual for the rapid X / Z-axis respectively for the 1200/3000 mm / min; machine smallest mobile units of 0.001 mm. 4, use of X53 milling SIEMENS 802S 2000, the company invested 120,000 yuan, with Germanys Siemens 802 S CNC system, stepping drive system for the companys another model of the X53 milling machine for X, Y, Z three-axis NC transformation of the original reservation Spindle and cooling systems; transformation of the three-axis machine used in the roller screw and gear drive mechanism. Transformation of the entire work includes mechanical design, electrical design, machine overhaul and, finally, the components are installed and debugged . Milling After the transformation, processing effective itinerary X / Y / Z-axis respectively 630/240/280mm; maximum speed X / Y / Z-axis respectively 3000/1000/600mm / min; manual feed rate X / Y / Z-axis respectively 2000/800/500mm / min; smallest mobile units of 0.001mm. 9, NC transformation of the issues and recommendations Through several of CNC machine work, there are also found in many of the issues, as demonstrated by: First, departments, staff development duties uncertainty, organizational chaos, seriously affecting the progress of reform; Second, the work of the development process and the development plan are mostly use their experience, not reasonable; Third, the training of relevant personnel not in place, resulting in improved process machine will be no programming, the operator of the machine operator unskilled, and other issues. Based on the above issues, a few suggestions: First, the staff responsible for the transformation of clear responsibilities, reward and punishment clear, and fully mobilize the enthusiasm of the staff; Second, cultivate a number of high-quality applications and maintenance personnel, selected staff on education and learn advanced technology; Third, we need to pay attention to users, maintaining CNC system technical training, the establishment of the technical resources at home and abroad NC. 机床数控改造一、数控系统发展简史及趋势1946年诞生了世界上第一台电子计算机,这表明人类创造了可增强和部分代替脑力劳动的工具。它与人类在农业、工业社会中创造的那些只是增强体力劳动的工具相比,起了质的飞跃,为人类进入信息社会奠定了基础。6年后,即在1952年,计算机技术应用到了机床上,在美国诞生了第一台数控机床。从此,传统机床产生了质的变化。近半个世纪以来,数控系统经历了两个阶段和六代的发展。1.1、数控(NC)阶段(19521970年)早期计算机的运算速度低,对当时的科学计算和数据处理影响还不大,但不能适应机床实时控制的要求。人们不得不采用数字逻辑电路搭成一台机床专用计算机作为数控系统,被称为硬件连接数控(HARD-WIRED NC),简称为数控(NC)。随着元器件的发展,这个阶段历经了三代,即1952年的第一代-电子管;1959年的第二代-晶体管;1965年的第三代-小规模集成电路。1.2、计算机数控(CNC)阶段(1970年现在)到1970年,通用小型计算机业已出现并成批生产。于是将它移植过来作为数控系统的核心部件,从此进入了计算机数控(CNC)阶段(把计算机前面应有的通用两个字省略了)。到1971年,美国INTEL公司在世界上第一次将计算机的两个最核心的部件-运算器和控制器,采用大规模集成电路技术集成在一块芯片上,称之为微处理器(MICROPROCESSOR),又可称为中央处理单元(简称CPU)。到1974年微处理器被应用于数控系统。这是因为小型计算机功能太强,控制一台机床能力有富裕(故当时曾用于控制多台机床,称之为群控),不如采用微处理器经济合理。而且当时的小型机可靠性也不理想。早期的微处理器速度和功能虽还不够高,但可以通过多处理器结构来解决。由于微处理器是通用计算机的核心部件,故仍称为计算机数控。到了1990年,PC机(个人计算机,国内习惯称微机)的性能已发展到很高的阶段,可以满足作为数控系统核心部件的要求。数控系统从此进入了基于PC的阶段。总之,计算机数控阶段也经历了三代。即1970年的第四代-小型计算机;1974年的第五代-微处理器和1990年的第六代-基于PC(国外称为PC-BASED)。还要指出的是,虽然国外早已改称为计算机数控(即CNC)了,而我国仍习惯称数控(NC)。所以我们日常讲的数控,实质上已是指计算机数控了。1.3、数控未来发展的趋势1.3.1继续向开放式、基于PC的第六代方向发展基于PC所具有的开放性、低成本、高可靠性、软硬件资源丰富等特点,更多的数控系统生产厂家会走上这条道路。至少采用PC机作为它的前端机,来处理人机界面、编程、联网通信等问题,由原有的系统承担数控的任务。PC机所具有的友好的人机界面,将普及到所有的数控系统。远程通讯,远程诊断和维修将更加普遍。1.3.2向高速化和高精度化发展这是适应机床向高速和高精度方向发展的需要。1.3.3向智能化方向发展随着人工智能在计算机领域的不断渗透和发展,数控系统的智能化程度将不断提高。(1)应用自适应控制技术数控系统能检测过程中一些重要信息,并自动调整系统的有关参数,达到改进系统运行状态的目的。将熟练工人和专家的经验,加工的一般规律和特殊规律存入系统中,以工艺参数数据库为支撑,建立具有人工智能的专家系统。(2)引入专家系统指导加工(3)引入故障诊断专家系统(4)智能化数字伺服驱动装置可以通过自动识别负载,而自动调整参数,使驱动系统获得最佳的运行。二、机床数控化改造的必要性2.1、微观看改造的必要性从微观上看,数控机床比传统机床有以下突出的优越性,而且这些优越性均来自数控系统所包含的计算机的威力。2.1.1 可以加工出传统机床加工不出来的曲线、曲面等复杂的零件。由于计算机有高超的运算能力,可以瞬时准确地计算出每个坐标轴瞬时应该运动的运动量,因此可以复合成复杂的曲线或曲面。2.1.2 可以实现加工的自动化,而且是柔性自动化,从而效率可比传统机床提高37倍。由于计算机有记忆和存储能力,可以将输入的程序记住和存储下来,然后按程序规定的顺序自动去执行,从而实现自动化。数控机床只要更换一个程序,就可实现另一工件加工的自动化,从而使单件和小批生产得以自动化,故被称为实现了柔性自动化。2.1.3 加工零件的精度高,尺寸分散度小,使装配容易,不再需要修配。2.1.4 可实现多工序的集中,减少零件 在机床间的频繁搬运。2.1.5 拥有自动报警、自动监控、自动补偿等多种自律功能,因而可实现长时间无人看管加工。2.1.6 由以上五条派生的好处。如:降低了工人的劳动强度,节省了劳动力(一个人可以看管多台机床),减少了工装,缩短了新产品试制周期和生产周期,可对市场需求作出快速反应等等。以上这些优越性是前人想象不到的,是一个极为重大的突破。此外,机床数控化还是推行FMC(柔性制造单元)、FMS(柔性制造系统)以及CIMS(计算机集成制造系统)等企业信息化改造的基础。数控技术已经成为制造业自动化的核心技术和基础技术。2.2、宏观看改造的必要性从宏观上看,工业发达国家的军、民机械工业,在70年代末、80年代初已开始大规模应用数控机床。其本质是,采用信息技术对传统产业(包括军、民机械工业)进行技术改造。除在制造过程中采用数控机床、FMC、FMS外,还包括在产品开发中推行CAD、CAE、CAM、虚拟制造以及在生产管理中推行MIS(管理信息系统)、CIMS等等。以及在其生产的产品中增加信息技术,包括人工智能等的含量。由于采用信息技术对国外军、民机械工业进行深入改造(称之为信息化),最终使得他们的产品在国际军品和民品的市场上竞争力大为增强。而我们在信息技术改造传统产业方面比发达国家约落后20年。如我国机床拥有量中,数控机床的比重(数控化率)到1995年只有1.9,而日本在1994年已达20.8,因此每年都有大量机电产品进口。这也就从宏观上说明了机床数控化改造的必要性。三、机床与生产线数控化改造的市场3.1、机床数控化改造的市场我国目前机床总量380余万台,而其中数控机床总数只有11.34万台,即我国机床数控化率不到3。近10年来,我国数控机床年产量约为0.60.8万台,年产值约为18亿元。机床的年产量数控化率为6。我国机床役龄10年以上的占60以上;10年以下的机床中,自动/半自动机床不到20,FMC/FMS等自动化生产线更屈指可数(美国和日本自动和半自动机床占60以上)。可见我们的大多数制造行业和企业的生产、加工装备绝大数是传统的机床,而且半数以上是役龄在10年以上的旧机床。用这种装备加工出来的产品普遍存在质量差、品种少、档次低、成本高、供货期长,从而在国际、国内市场上缺乏竞争力,直接影响一个企业的产品、市场、效益,影响企业的生存和发展。所以必须大力提高机床的数控化率。3.2、进口设备和生产线的数控化改造市场我国自改革开放以来,很多企业从国外引进技术、设备和生产线进行技术改造。据不完全统计,从19791988年10年间,全国引进技术改造项目就有18446项,大约165.8亿美元。这些项目中,大部分项目为我国的经济建设发挥了应有的作用。但是有的引进项目由于种种原因,设备或生产线不能正常运转,甚至瘫痪,使企业的效益受到影响,严重的使企业陷入困境。一些设备、生产线从国外引进以后,有的消化吸收不好,备件不全,维护不当,结果运转不良;有的引进时只注意引进设备、仪器、生产线,忽视软件、工艺、管理等,造成项目不完整,设备潜力不能发挥;有的甚至不能启动运行,没有发挥应有的作用;有的生产线的产品销路很好,但是因为设备故障不能达产达标;有的因为能耗高、产品合格率低而造成亏损;有的已引进较长时间,需要进行技术更新。种种原因使有的设备不仅没有创造财富,反而消耗着财富。这些不能使用的设备、生产线是个包袱,也是一批很大的存量资产,修好了就是财富。只要找出主要的技术难点,解决关键技术问题,就可以最小的投资盘活最大的存量资产,争取到最大的经济效益和社会效益。这也是一个极大的改造市场。四、数控化改造的内容及优缺4.1、国外改造业的兴起在美国、日本和德国等发达国家,它们的机床改造作为新的经济增长行业,生意盎然,正处在黄金时代。由于机床以及技术的不断进步,机床改造是个永恒的课题。我国的机床改造业,也从老的行业进入到以数控技术为主的新的行业。在美国、日本、德国,用数控技术改造机床和生产线具有广阔的市场,已形成了机床和生产线数控改造的新的行业。在美国,机床改造业称为机床再生(Remanufacturing)业。从事再生业的著名公司有:Bertsche工程公司、ayton机床公司、Devlieg-Bullavd(得宝)服务集团、US设备公司等。美国得宝公司已在中国开办公司。在日本,机床改造业称为机床改装(Retrofitting)业。从事改装业的著名公司有:大隈工程集团、岗三机械公司、千代田工机公司、野崎工程公司、滨田工程公司、山本工程公司等。4.2、数控化改造的内容机床与生产线的数控化改造主要内容有以下几点:其一是恢复原功能,对机床、生产线存在的故障部分进行诊断并恢复;其二是NC化,在普通机床上加数显装置,或加数控系统,改造成NC机床、CNC机床;其三是翻新,为提高精度、效率和自动化程度,对机械、电气部分进行翻新,对机械部分重新装配加工,恢复原精度;对其不满足生产要求的CNC系统以最新CNC进行更新;其四是技术更新或技术创新,为提高性能或档次,或为了使用新工艺、新技术,在原有基础上进行较大规模的技术更新或技术创新,较大幅度地提高水平和档次的更新改造。4.3、数控化改造的优缺4.3.1减少投资额、交货期短同购置新机床相比,一般可以节省6080的费用,改造费用低。特别是大型、特殊机床尤其明显。一般大型机床改造,只花新机床购置费用的1/3,交货期短。但有些特殊情况,如高速主轴、托盘自动交换装置的制作与安装过于费工、费钱,往往改造成本提高23倍,与购置新机床相比,只能节省投资50左右。4.3.2机械性能稳定可靠,结构受限所利用的床身、立柱等基础件都是重而坚固的铸造构件,而不是那种焊接构件,改造后的机床性能高、质量好,可以作为新设备继续使用多年。但是受到原来机械结构的限制,不宜做突破性的改造。4.3.3熟悉了解设备、便于操作维修购买新设备时,不了解新设备是否能满足其加工要求。改造则不然,可以精确地计算出机床的加工能力;另外,由于多年使用,操作者对机床的特性早已了解,在操作使用和维修方面培训时间短,见效快。改造的机床一安装好,就可以实现全负荷运转。4.3.4可充分利用现有的条件可以充分利用现有地基,不必像购入新设备时那样需重新构筑地基。4.3.5可以采用最新的控制技术可根据技术革新的发展速度,及时地提高生产设备的自动化水平和效率,提高设备质量和档次,将旧机床改成当今水平的机床。五、数控系统的选择数控系统主要有三种类型,改造时,应根据具体情况进行选择。5.1、步进电机拖动的开环系统该系统的伺服驱动装置主要是步进电机、功率步进电机、电液脉冲马达等。由数控系统送出的进给指令脉冲,经驱动电路控制和功率放大后,使步进电机转动,通过齿轮副与滚珠丝杠副驱动执行部件。只要控制指令脉冲的数量、频率以及通电顺序,便可控制执行部件运动的位移量、速度和运动方向。这种系统不需要将所测得的实际位置和速度反馈到输入端,故称之为开
- 温馨提示:
1: 本站所有资源如无特殊说明,都需要本地电脑安装OFFICE2007和PDF阅读器。图纸软件为CAD,CAXA,PROE,UG,SolidWorks等.压缩文件请下载最新的WinRAR软件解压。
2: 本站的文档不包含任何第三方提供的附件图纸等,如果需要附件,请联系上传者。文件的所有权益归上传用户所有。
3.本站RAR压缩包中若带图纸,网页内容里面会有图纸预览,若没有图纸预览就没有图纸。
4. 未经权益所有人同意不得将文件中的内容挪作商业或盈利用途。
5. 人人文库网仅提供信息存储空间,仅对用户上传内容的表现方式做保护处理,对用户上传分享的文档内容本身不做任何修改或编辑,并不能对任何下载内容负责。
6. 下载文件中如有侵权或不适当内容,请与我们联系,我们立即纠正。
7. 本站不保证下载资源的准确性、安全性和完整性, 同时也不承担用户因使用这些下载资源对自己和他人造成任何形式的伤害或损失。

人人文库网所有资源均是用户自行上传分享,仅供网友学习交流,未经上传用户书面授权,请勿作他用。