果蔬篮注塑模具设计
45页 16000字数+说明书+外文翻译+12张CAD图纸【详情如下】
动模座板A2.dwg
型腔A2.dwg
型芯A2.dwg
果蔬篮注塑模具设计说明书.doc
塑件图A1.dwg
外文翻译--一种基于网络智能化设计系统的注射模 中文版.doc
外文翻译--一种基于网络智能化设计系统的注射模 英文版.pdf
定位圈.dwg
定模座板A2.dwg
导套A4.dwg
总装图A0.dwg
推杆固定板A2.dwg
推板A2.dwg
斜导柱A4.dwg
浇口套A4.dwg
说明书.doc
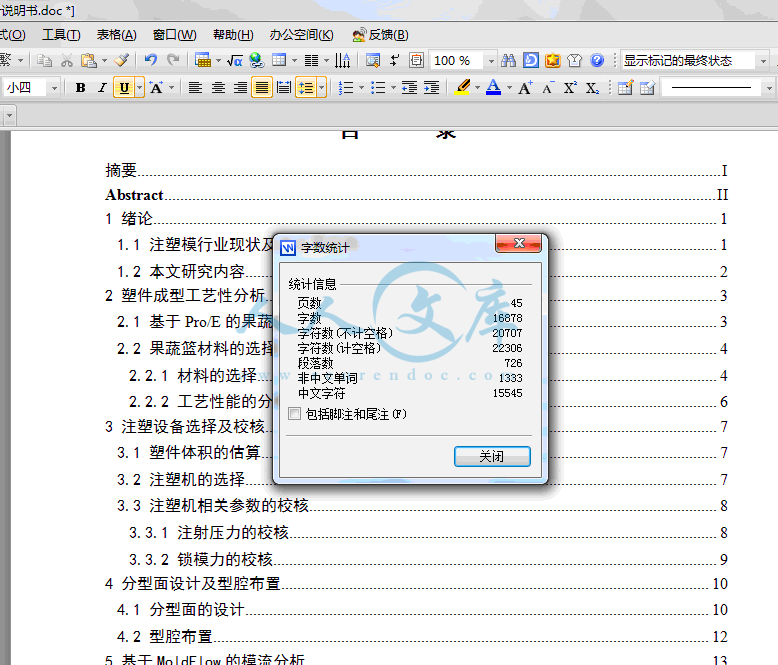
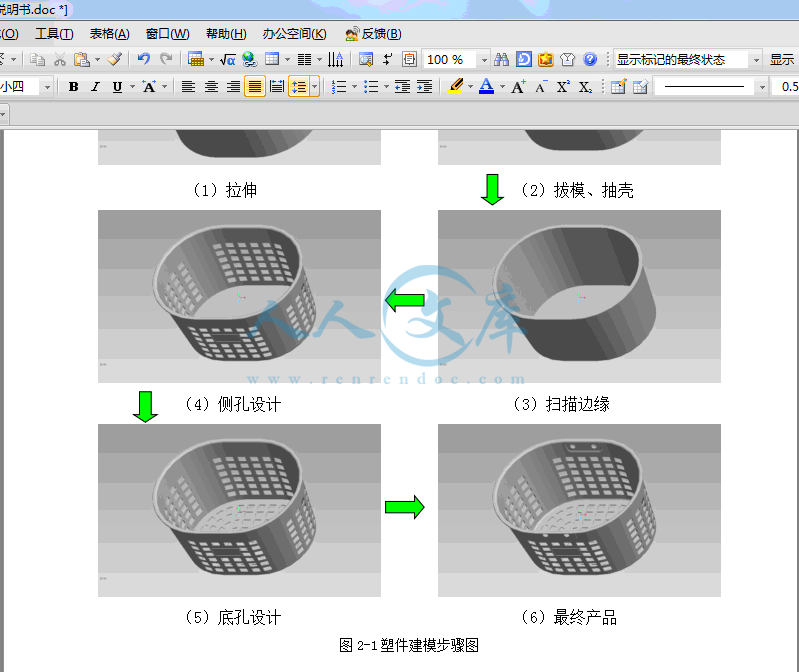

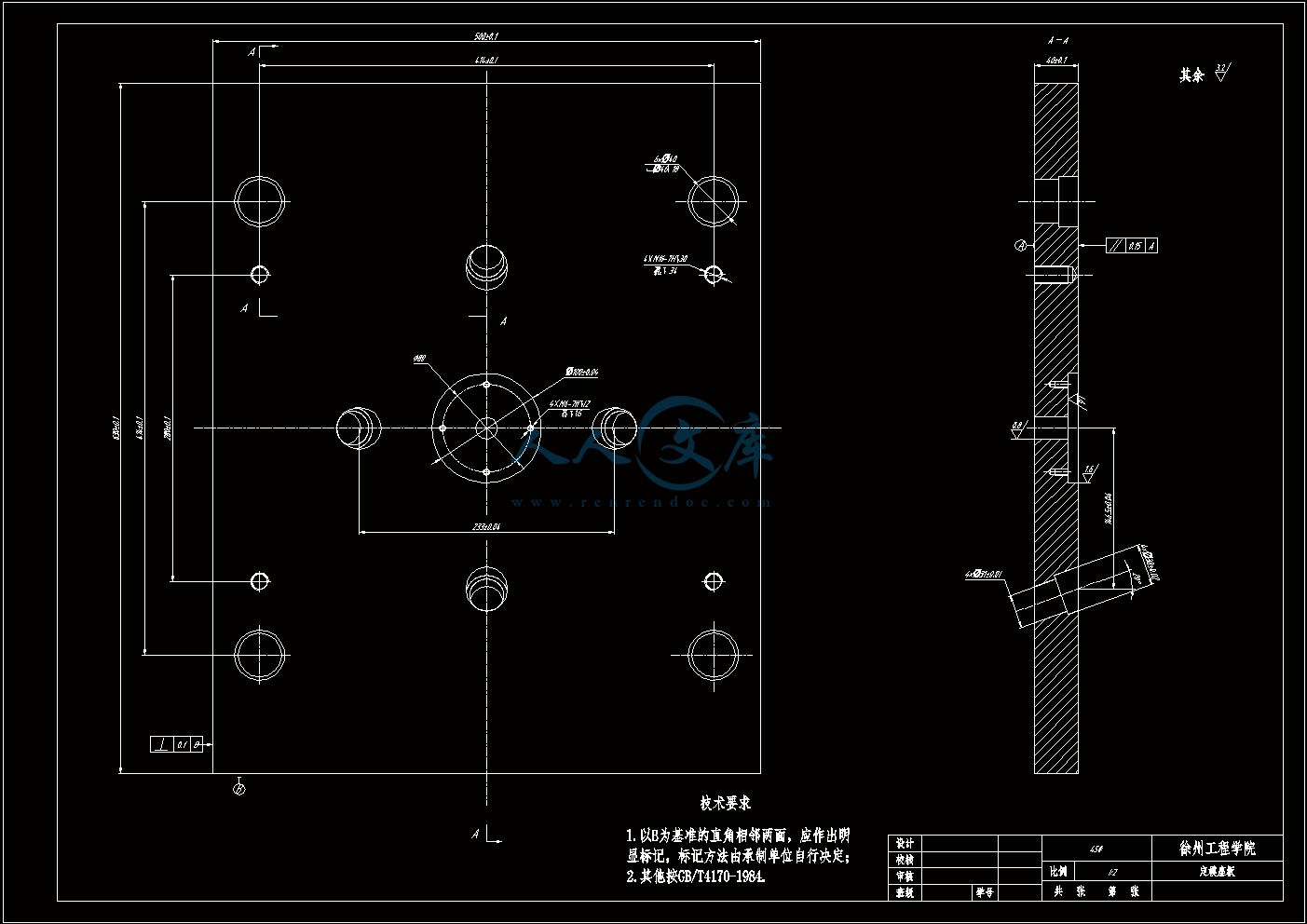
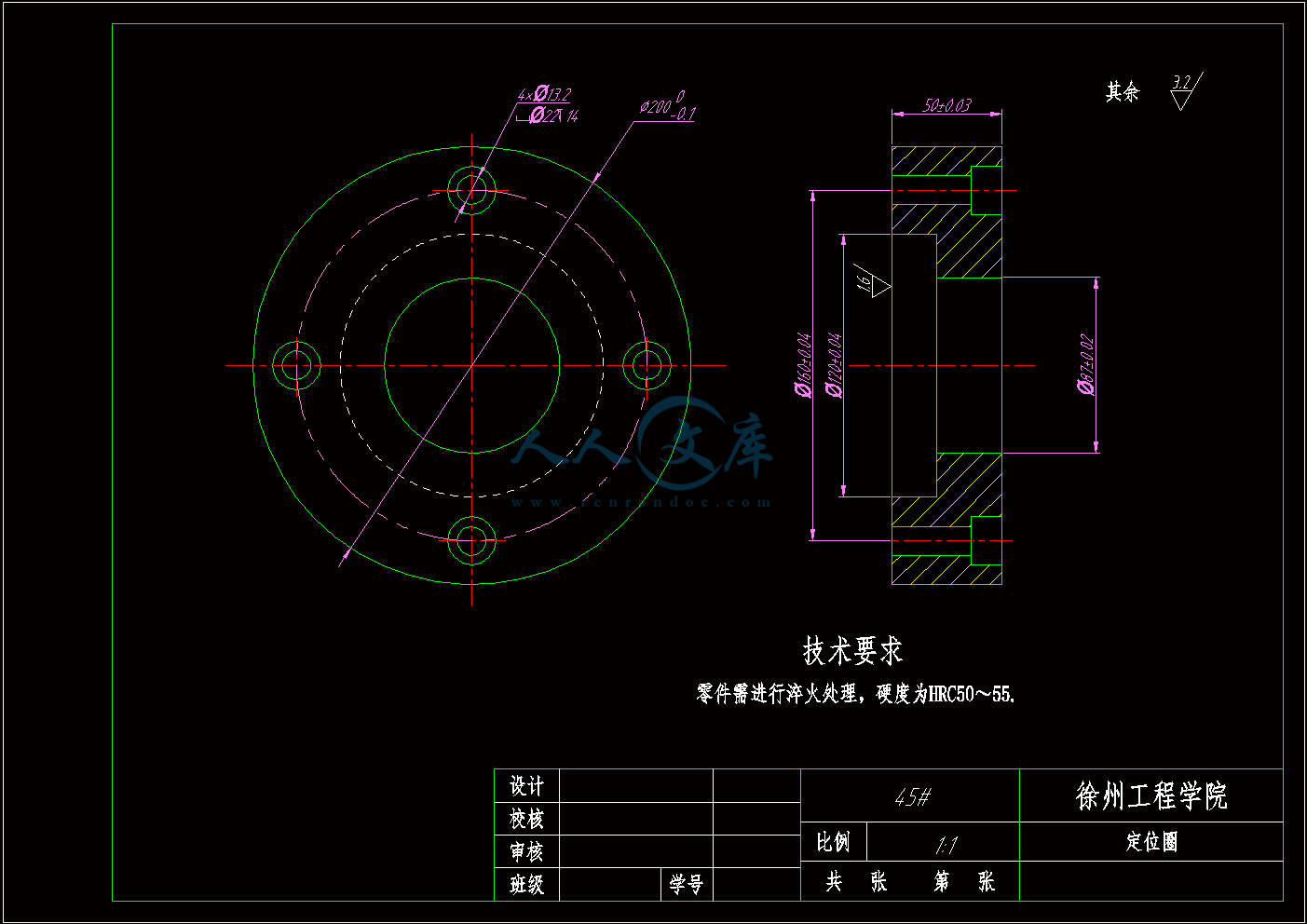


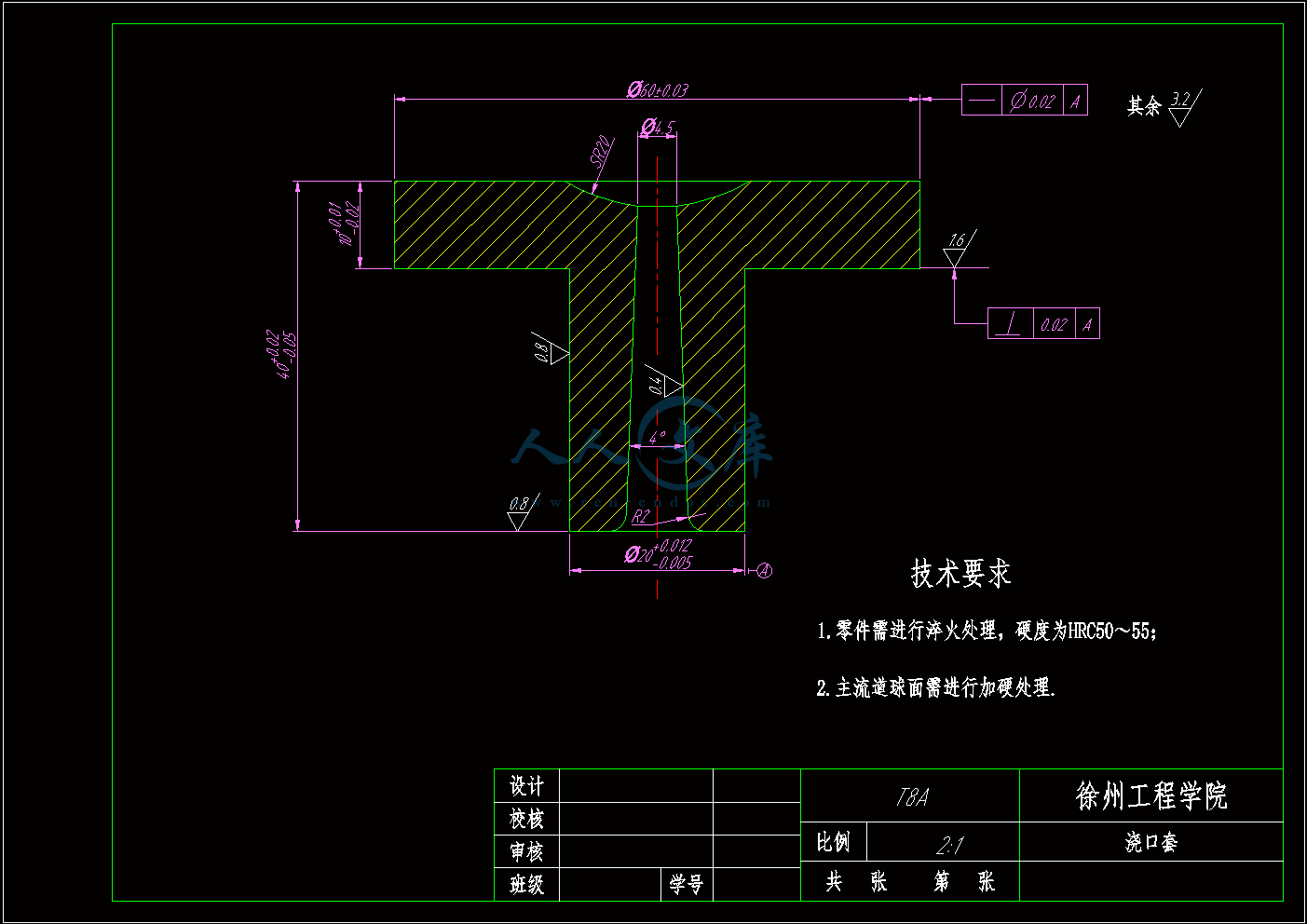

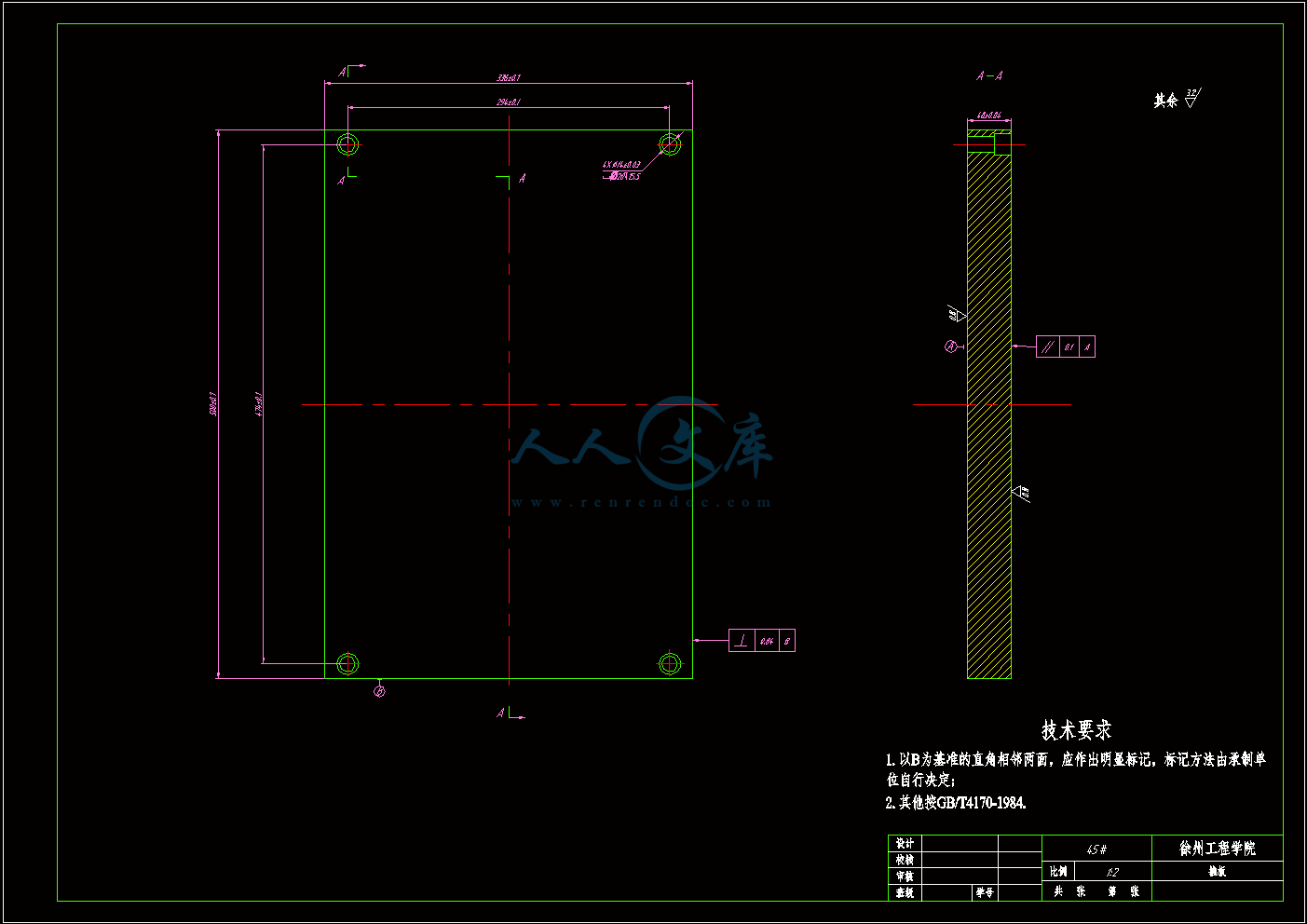
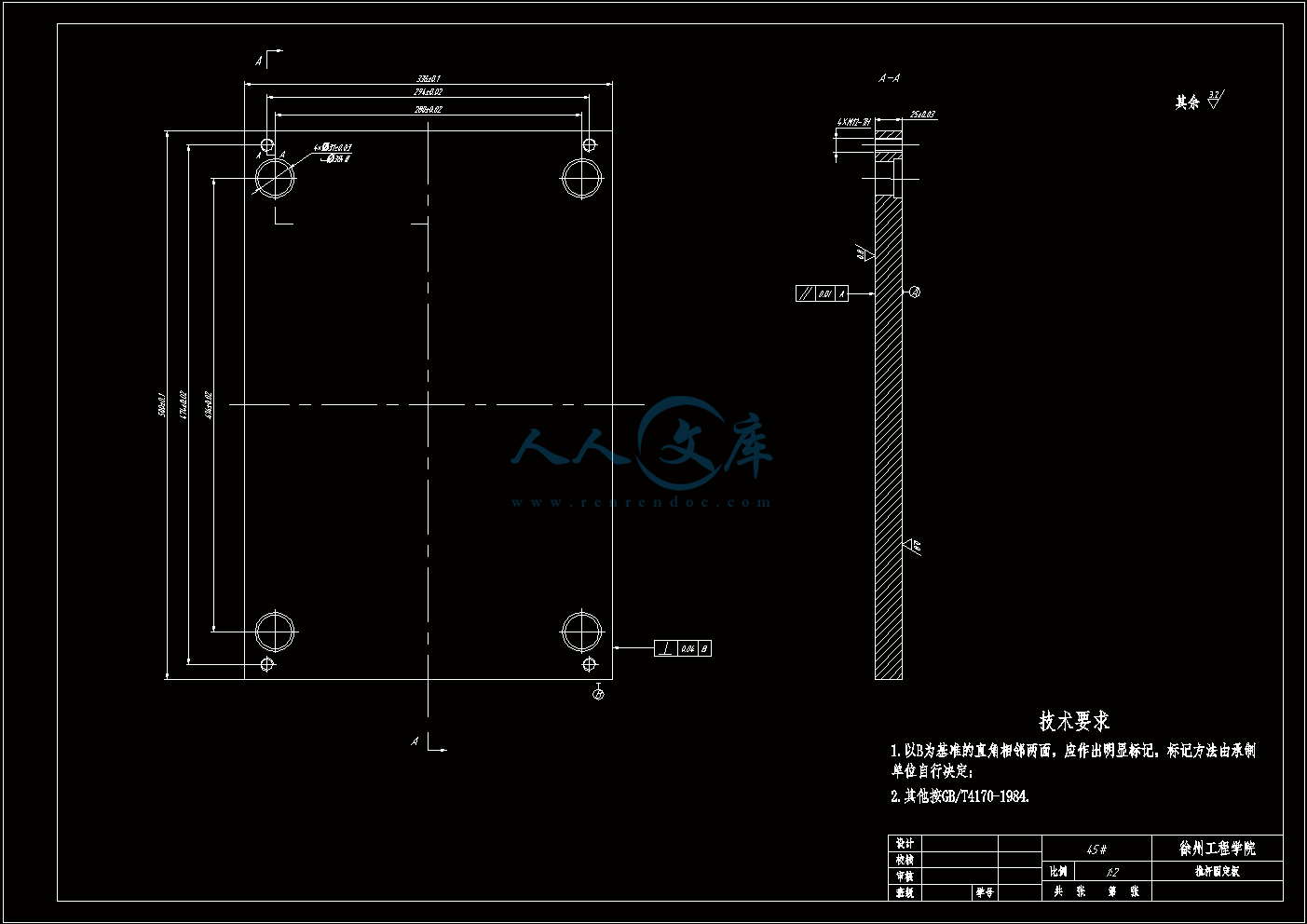

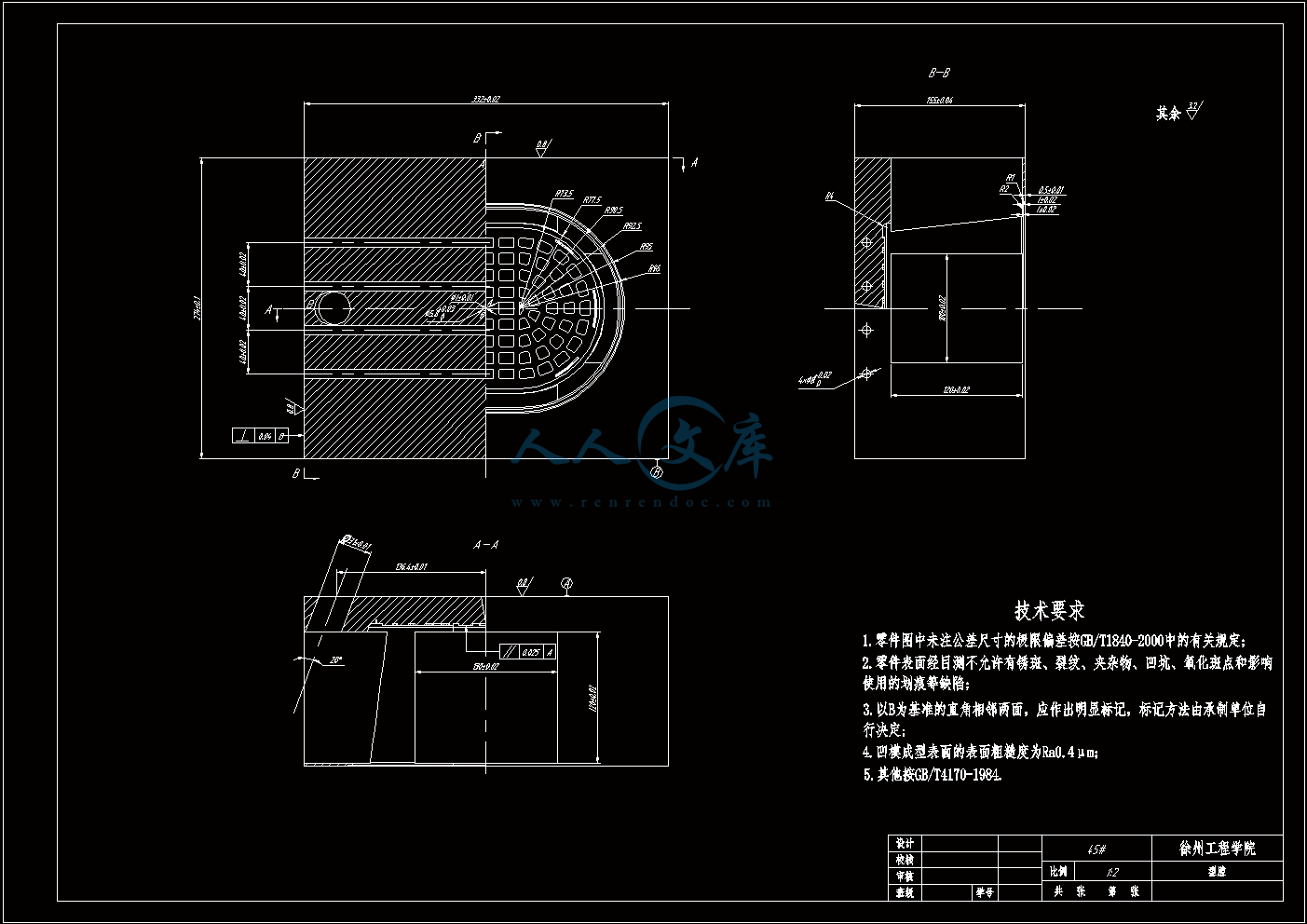
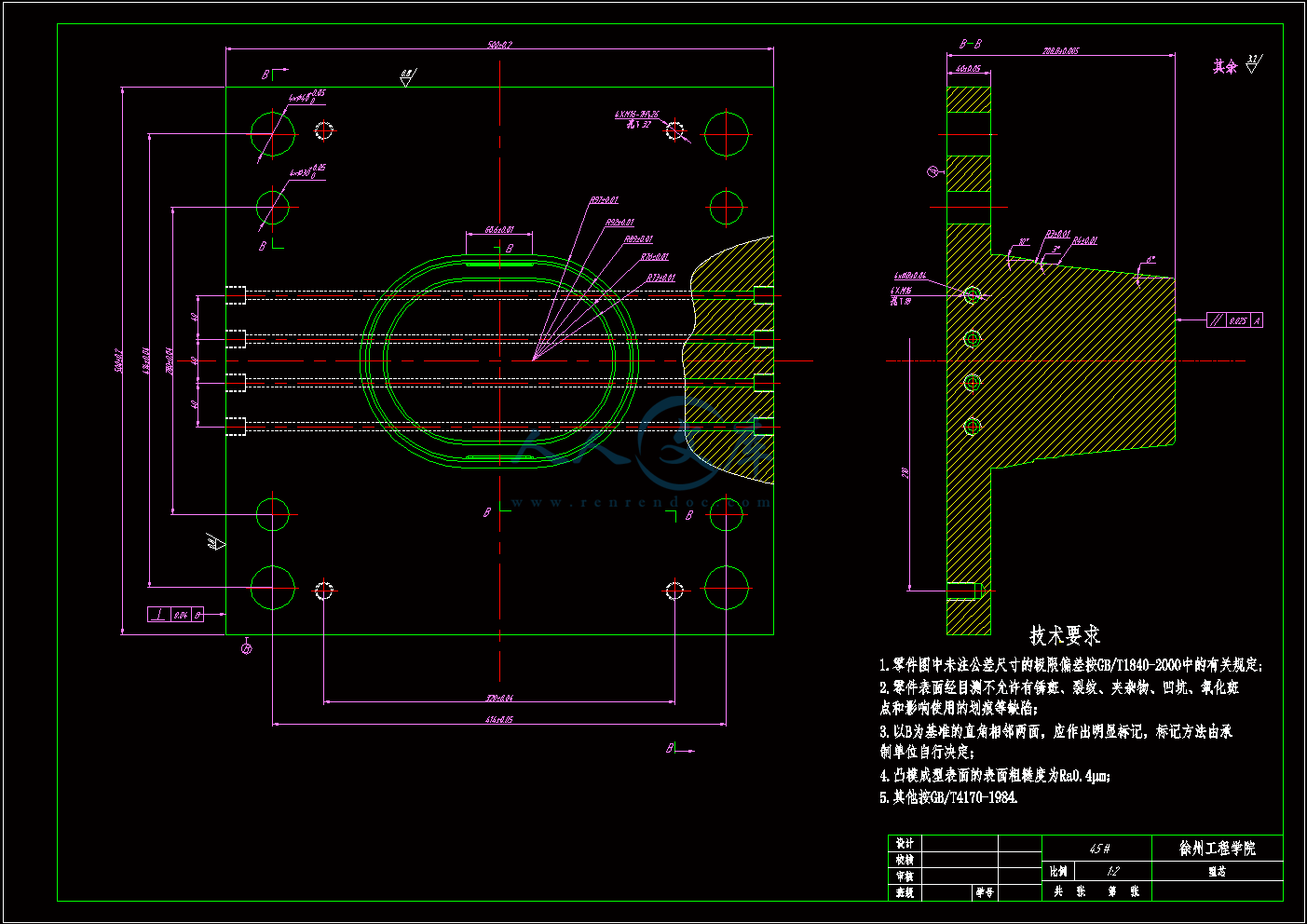

目录
摘要I
AbstractII
1 绪论1
1.1 注塑模行业现状及其发展趋势1
1.2 本文研究内容2
2 塑件成型工艺性分析3
2.1 基于Pro/E的果蔬篮三维建模3
2.2 果蔬篮材料的选择及工艺性能的分析4
2.2.1 材料的选择4
2.2.2 工艺性能的分析6
3 注塑设备选择及校核7
3.1 塑件体积的估算7
3.2 注塑机的选择7
3.3 注塑机相关参数的校核8
3.3.1 注射压力的校核8
3.3.2 锁模力的校核9
4 分型面设计及型腔布置10
4.1 分型面的设计10
4.2 型腔布置12
5 基于MoldFlow的模流分析13
5.1 MoldFlow软件简介13
5.2 网格的划分与处理13
5.3 塑件的最佳浇口位置分析15
5.4 塑件的翘曲分析15
5.5 塑件的流动性分析16
5.5.1 气穴、熔接痕和分子表面取向16
5.5.2 充填时间分析18
5.5.3 锁模力和螺杆速度18
5.6 塑件的冷却分析19
6 浇注系统设计20
6.1 浇注系统概述20
6.2 普通浇注系统的设计21
6.2.1 主流道的设计21
6.2.2 分流道的设计22
6.2.3 浇口的设计23
7 成型零部件设计及模架选择24
7.1 成型零部件设计24
7.1.1 成型零件的结构设计24
7.1.2 成型零件工作尺寸的计算24
7.2 模架的选择25
8 相关机构设计27
8.1 脱模机构的设计27
8.1.1 脱模力的计算27
8.1.2 塑件脱出机构27
8.1.3 凝料脱出机构28
8.2 合模导向机构的设计29
8.2.1 合模导向机构的作用29
8.2.1 导向机构的设计29
8.3 注塑模侧向抽芯机构设计30
8.3.1 机构抽芯距和抽芯力的计算30
8.3.2 斜导柱的设计31
9 冷却系统及排气系统的设计33
9.1 冷却系统的设计33
9.1.1 冷却系统的设计原则33
9.1.2 冷却系统的设计33
9.2 排气系统的设计35
10 模具的总装36
结论38
致谢39
参考文献40
1 绪论
1.1 注塑模行业现状及其发展趋势
模具是工业产品生产用的重要工艺装备,在现代工业生产中,60%~90%的工业产品需要使用模具,模具工业已成为工业发展的基础,许多新产品的开发和研制在很大程度上都依赖于模具生产,汽车、摩托车、轻工、电子、航空等行业尤为突出。注塑模是其典型代表。随着工业塑料制件和日用塑料制件的品种和需求量的日益增加,这些产品更新换代的周期越来越短,因此对塑料的品种、产量和质量都提出了越来越高的要求。
现代模具技术的发展,在很大程度上依赖于模具标准化、对优质模具材料的研究、先进的设计与制造技术、专用的机床设备,更重要的是生产技术的管理等。21世纪模具行业的基本特征是高度集成化、智能化、柔性化和网络化。追求的目标是提高产品的质量及生产效率,缩短设计及制造周期,降低生产成本,最大限度地提高模具行业的应变能力,满足用户需要。可见,未来我国模具工业和技术的主要发展方向主要表现在以下几个方面。
● 大力普及、广泛应用CAD/CAE/CAM技术,逐步走向集成化。现代模具设计制造不仅应强调信息的集成,更应该强调技术、人和管理的集成。
● 提高大型、精密、复杂与长寿命模具的设计与制造技术,逐步减少模具的进口量,增加模具的出口量。
● 在塑料注射成型模具中,积极应用热流道,推广气辅或水辅注射成型,以及高压注射成型技术,满足产品的成型需要。
● 提高模具标准化水平和模具标准件的使用率。模具标准件是模具基础,其大量应用可缩短模具设计制造周期,同时也显著提高模具的制造精度和使用性能,大大提高模具质量。我国模具商品化、标准化率均低于30%,而先进国家均高于70%,每年从国外进口相当数量的模具标准件,其费用约占年模具进口额的3%~8%。
● 发展快速制造成型和快速制造模具,即快速成型制造技术,迅速制造出产品的原型与模具,降低成本,推向市场。
● 积极研究与开发模具的抛光技术、设备与材料,满足特殊产品的需要。
● 推广应用高速铣削、超精度加工和复杂加工技术与工艺,满足模具制造的需要。
● 开发优质模具材料和先进的表面处理技术,提高模具的可靠性。
● 研究和应用模具的高速测量技术、逆向工程与并行工程,最大限度地提高模具的开发效率与成功率。
● 开发新的成型工艺与模具,以满足未来多学科多功能综合产品开发设计技术。
1.2 本文研究内容
本文参考了大量文献,在理论基础和实践基础上主要做了以下工作:
1.基于PRO/E的塑件模型重构。
2.塑件的工艺性分析。
3.注射机的选择与校核。
4.分型面的选择与创建,型腔数目的确定。
5.基于MoldFlow的模流分析:包括最佳浇口位置分析、翘曲分析、流动分析和冷却
分析。
6.浇注系统的设计。
7.注射模具成型零件及模具体的设计。
8.冷却系统及排气系统的设计。