珩磨柴油机机体缸孔专机设计
48页 17000字数+说明书+实习报告+开题报告+2张CAD图纸【详情如下】
内封.doc
加工示意图.dwg
加工示意图.exb
实习报告机械.doc
摘要.doc
珩磨柴油机机体缸孔专机设计开题报告.doc
珩磨柴油机机体缸孔专机设计说明书.doc
目录.doc
设计总图.dwg
设计总图.exb
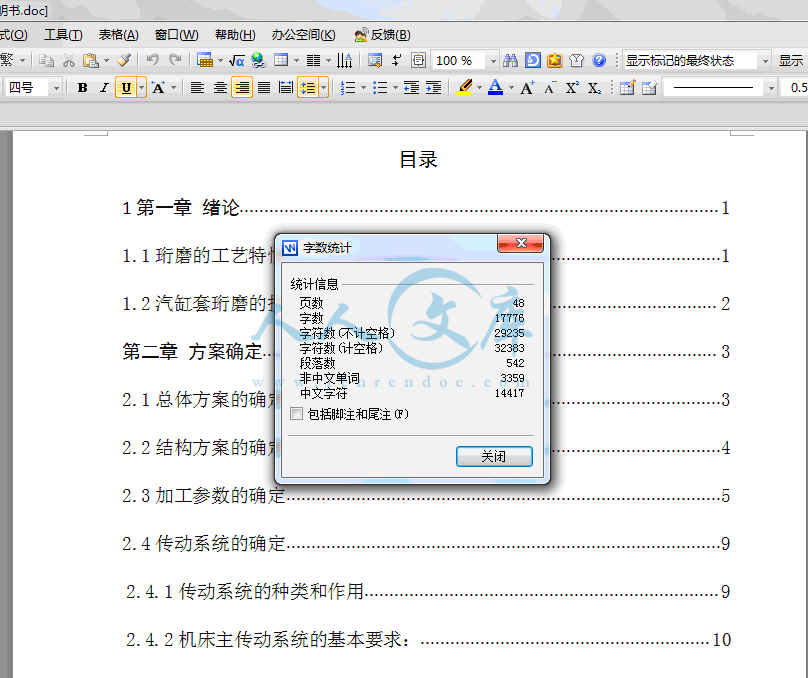
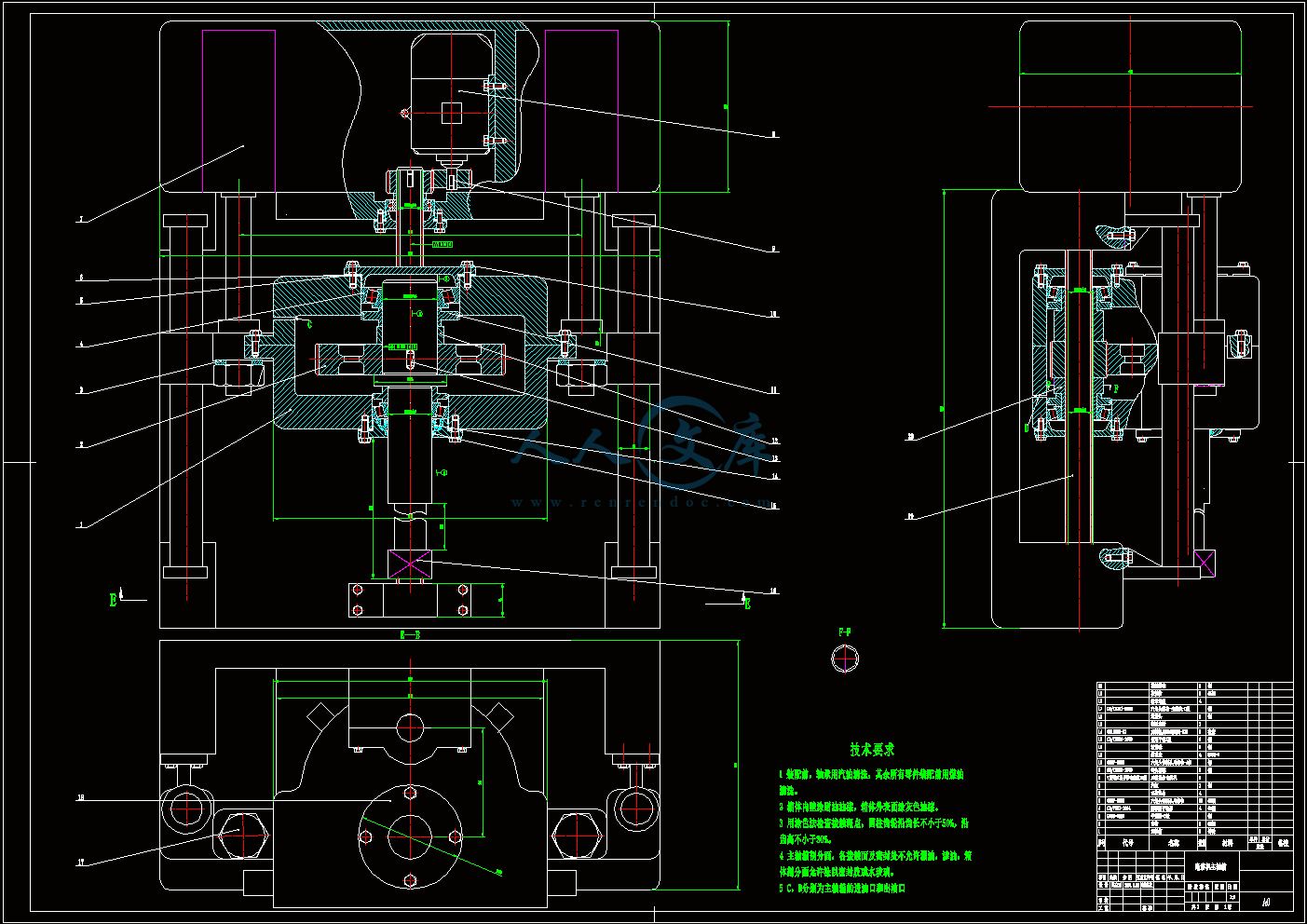
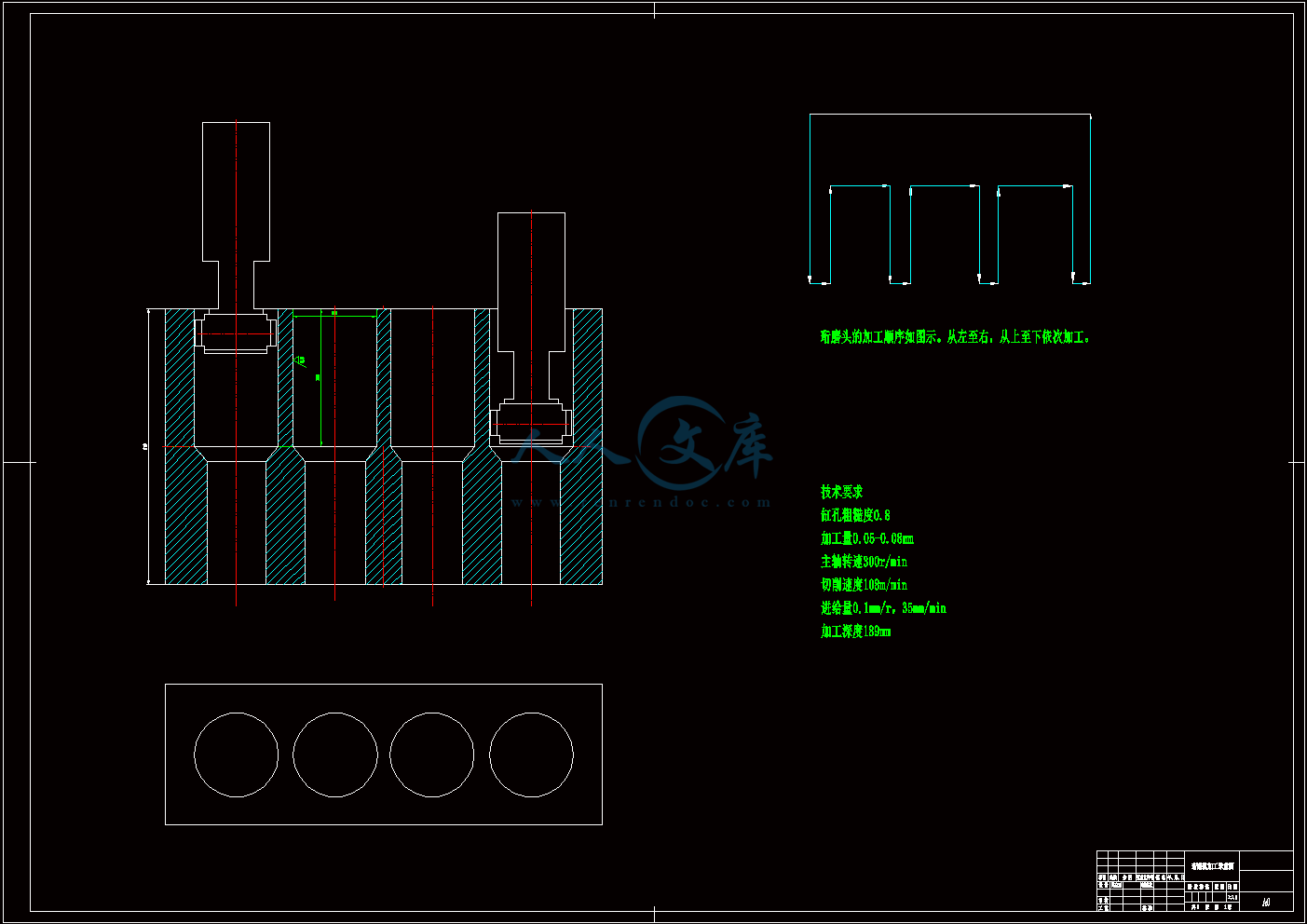
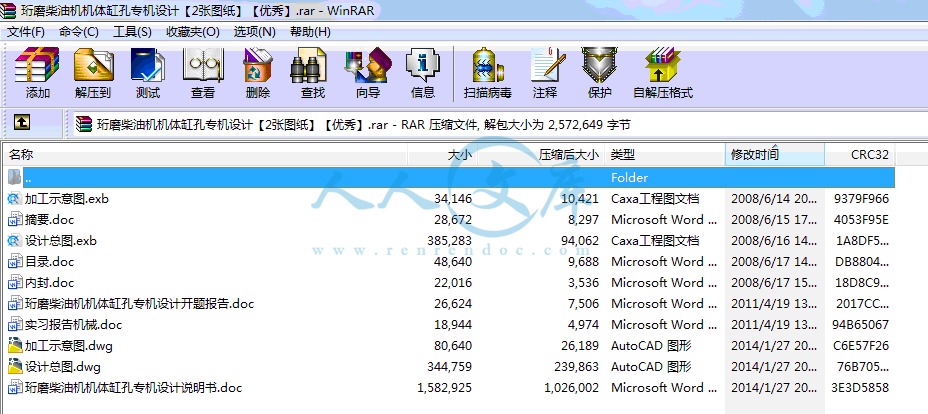
目录
1第一章 绪论1
1.1珩磨的工艺特性1
1.2汽缸套珩磨的技术要点2
第二章 方案确定3
2.1总体方案的确定3
2.2结构方案的确定4
2.3加工参数的确定5
2.4传动系统的确定9
2.4.1传动系统的种类和作用9
2.4.2机床主传动系统的基本要求:10
第三章 主轴箱零件的设计及计算11
3.1轴承盖的设计11
3.2垫圈的设计13
3.3主轴的设计14
3.3.1轴按受载情况的分类14
3.3.2设计过程15
3.4花键轴的选择19
3.5齿轮的选择19
3.5.1圆柱齿轮传动设计步骤:20
3.5.2传动比的确定20
3.5.3齿面接触疲劳强度计算21
3.5.4齿面接触疲劳强度的校核21
3.5.5 齿根弯曲疲劳强度的校核24
3.6 轴承的选择26
3.7电动机的选择26
3.7.1选择电机系列26
3.7.2电动机的选择27
3.7.3电动机结构形式的选择。28
第四章 主轴箱的装配图和加工示意图29
4.1 CAXA的特点29
4.2 CAXA电子图板设计中的应用29
4.2.1机床主轴箱的绘制29
4.2.2加工示意图的绘制30
4.2.3机床的总图的绘制31
结 论33
致 谢34
参考文献35
附 录36
摘要
本次设计的题目是珩磨柴油机机体缸孔专机设计——主轴箱部分。内容有主轴箱的设计,加工示意图的绘制。本次设计的意义在于通过用CAXA等软件绘制机床主轴箱等机床零件来达到后期的机械工艺流程。
主轴箱是工序集中的,高效的机床的重要专用部件之一,是用于布置机床工作主轴及其传动零件和相应的附加机构。本次设计的珩磨机的动力传动为两极传动,由电动机到花键轴再到主轴的方式。主轴箱的工作原理是在液压缸的压力推动下,主轴箱随之上下运动,从而达到主轴箱带动珩磨头往复运动加工缸体的目的。
在这次设计中采用了大量的计算,主要有主轴,齿轮,轴承,电机等的计算和校核。通过计算来验证所选的零件为最佳选择。
在本设计中采用了CAXA软件来具体的设计了珩磨机主轴箱的结构及实体造型。用CAXA用来画二维图,设计确定主轴箱外型尺寸和基本位置定位。
关键词:主轴箱;零件的选择;珩磨
汽缸套珩磨的技术要点
汽缸套的珩磨质量主要取决于珩磨规范,砂条材料,磨头的运动轨迹及负荷。
现分述如下:
1.珩磨规范:磨头往复运动速度,一般可按其圆周速度的1/3~1/5选取,如磨头转速在150-180r/min,往复运动速度为80-100mm/r,砂条的压力一般在4.9MPa 左右,以用手不能转动主轴,而能在轴线方向上下移动为宜。
2.砂条材料的选择:目前常见的砂条材料有碳化硅和氧化铝,前者可珩磨铸铁类汽缸套,后者可珩磨钢质汽缸套。一般粗磨时选用硬度为中软,粒度为80—240粒(视磨削量大小而定);精磨则选用软砂条,其粒度为300-4000磨条的长度可选为汽缸套长度的1/2~1/3。
3.磨头的往复行程:珩磨砂条伸出汽缸套上、下口之外的长度,应不大于砂条全长的1/3,不小于1/5,因为伸出量太大,易使汽缸套出现喇叭口;伸出量太小,易出现腰鼓形。
4.珩磨时用煤油或柴油作冷却剂,以便散热,并冲去铁屑,提高街磨质量。
为了提高珩磨质量,还可用硫酸铜磨缸法,其方法如下:
(1)将汽缸套珩磨到修理尺寸时,取下磨头上的砂条,换上毛毡条,然后将毛毡条浸以香蕉水,放在汽缸套内转动数周。以除去缸壁上的油污。
(2)将硫酸铜溶液(每升水中含硫酸铜300-400g)滴在毡条上少许,珩磨1分钟左右,待被置换的铜均匀地覆盖在汽缸套内表面上时,再用碱水冲下多余的硫酸铜,以防腐蚀。用此法磨过的汽缸套,内径尺寸没有变化,表面为紫铜色。能提高汽缸套内表面质量,改善汽缸套与活塞及活塞环的磨合性能延长使用寿命。
第二章 方案确定
2.1总体方案的确定
在机床诸多零件中,主轴箱和主轴箱前盖与机床密切相关,是机床的重要组成部件。主轴箱是选用通用零件,按专用要求设计的,所以是机床设计过程中工作量较大的零部件之一。就主轴箱设计来说,工作量主要集中在传动系统的设计上。由于通常采用一根动力轴带动多根主轴的工作方式,因此各传动轴必须设法在有限的标准箱体空间中找到适宜的分布位置。本设计中采用两级传动,轴的分布相对简单,其分布必须保证各轴的转速、旋向、强度和刚度。
制定工艺方案是设计组合机床最重要的一步。工艺方案制定得正确与否,将决定机床能否达到“体积小,重量轻,结构简单,使用方便,效率高,质量好”的要求。为了使工艺方案制定得合理、先进,必须从认真分析被加工零件(或同类零件)图纸开始,深入现场全面了解被加工零件的结构特点、加工部位、尺寸精度、表面粗糙度和技术要求,定位、夹紧方式,工艺方法和加工过程所采用的刀具、辅具,切削用量情况及生产率要求等,分析其优缺点,总结设计,制造,使用单位和操作者丰富的实践经验,以求理论紧密联系生产实际,从而确定零件在组合机床上完成的工艺(工序)内容及方法,决定刀具种类、结构型式、数量及切削用量等。