铸铁机的辅助装置设计【6张CAD图纸+毕业论文】
收藏
资源目录
压缩包内文档预览:
编号:424142
类型:共享资源
大小:2.07MB
格式:RAR
上传时间:2015-04-10
上传人:上***
认证信息
个人认证
高**(实名认证)
江苏
IP属地:江苏
39
积分
- 关 键 词:
-
铸铁机
辅助
装置
设计
cad图纸
毕业论文
辅助装置
铸铁机辅助装置
- 资源描述:
-
铸铁机的辅助装置设计
50页 15000字数+说明书+6张图纸
主动链轮装配图.dwg
从动轮及拉紧装置装配图.dwg
传动轴.dwg
目 录.doc
轴(从动).dwg
铸铁机前方支柱装配图.dwg
铸铁机的辅助装置设计说明书.doc
链带车轮.dwg

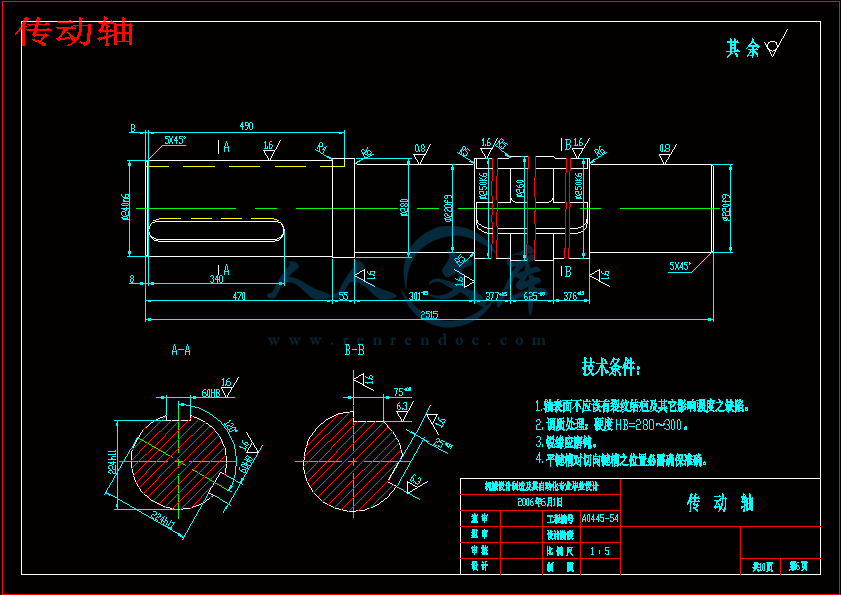

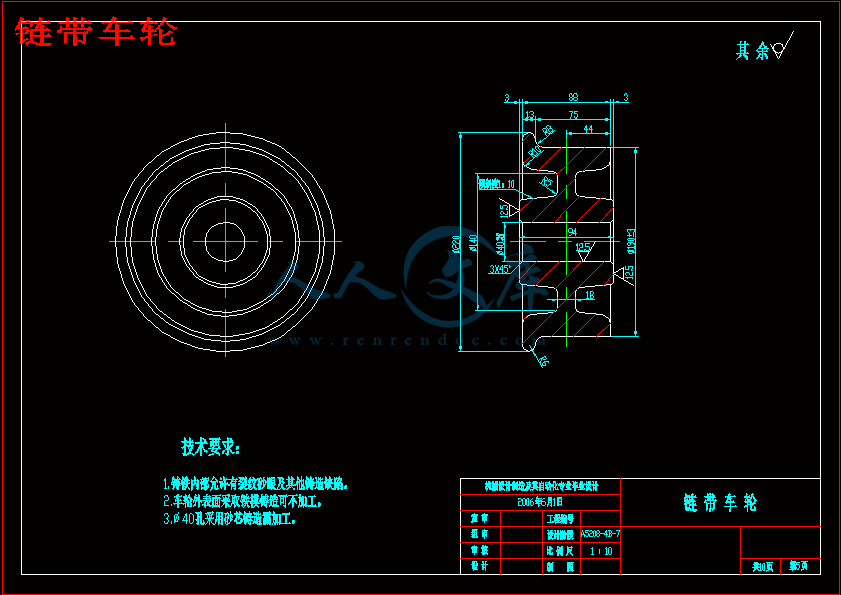


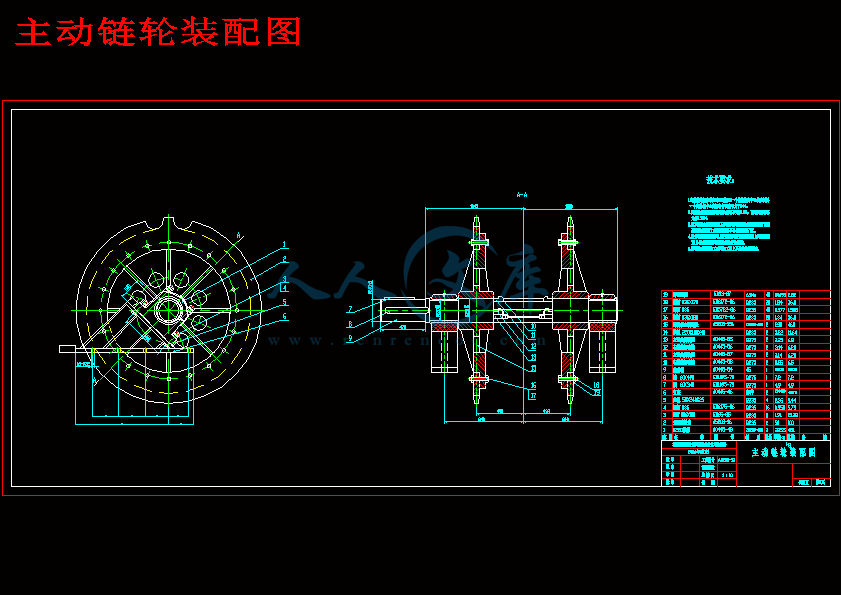

目 录
摘 要Ⅰ
КонспектⅡ
第一章 概述1
1.1铸铁机前的铁水运输1
1.2工艺要求和设备选型2
1.3铸铁机的发展5
第二章 铸铁机生产能力确定及链带受力分析16
2.1铸铁机生产能力的确定17
2.2铸铁机每条链带的电动机功率的确定17
2.3电动机功率的确定21
2.4电机及其减速器的选择21
第三章 铸铁机的零件设计22
3.1主动链轮轴的设计22
3.1.1 选择轴的材料22
3.1.2初步估算轴径22
3.1.3轴的结构设计23
3.1.4轴的强度验算26
3.2从动轮轴的设计29
3.2.1选择轴的材料30
3.2.2初步估算轴径30
3.2.3轴的强度验算30
3.2.4轴的结构设计33
第四章 链带及铸铁模的设计36
4.1铸铁模36
4.2链带36
第五章 铸铁机的辅助装置设计38
5.1张紧装置38
5.2铸铁块的冷却系统38
5.3铸铁模喷浆装置39
5.4前方支柱39
第六章 铸铁机室的布置40
6.1铸铁机室的布置形式41
6.2铁路布置41
6.3铸铁机中心距的确定41
6.4操作室,前方支柱及机前机后操作人员的操作台41
第七章 创新设计43
7.1采用双电机驱动43
7.2 采用挡板防滚轮卡死43
结束语45
参考文献46
第一章概述
1.1 铸铁机前的铁水运输
铸铁机是为了将铁水连续铸造成铁块而设置的。在高炉车间出铁场上由铁水罐车或混铁车贮存的铁水经铁路运到铸铁机前的前方支柱旁以备浇注。
国内高炉铁水的运输设备大部分采用铁水罐车,它是由梨形的铁水罐和承载车二部分组成。它的走行是靠机车头的牵引,它的吊装与倾翻是由专用的起重机来操作的。国内常用的有65吨铁水罐车、ZT—100—1型铁水罐车、ZT—140—1型铁水罐车。
65吨铁水罐车的铁水罐容量为65吨.椭载时罐体总重86吨,罐体中之耐火砖重10吨,车架总重17.5吨。ZT—100—1型铁水罐车队铁水罐容量为100吨,满载时罐体总重128吨,罐体中之耐火砖重14.3吨,车架总重22吨。ZT—140—l型铁水罐车的铁水罐容量140吨,满载时罐体总重171吨,罐体中之耐火砖重16.5吨,车架总重28.5吨。这三种铁水罐车负载时的最大运行速度为20千米/小时,在道岔处允许最大运行速度10千米/小时,铁道轨距1435毫米。
在现代化的大型高炉车间里,生产的铁水量很大,铁水罐已不能满足运输的要求,因而改用混铁车来完成运输和贮藏铁水的工作。它较之铁水罐车有以下优点:1)容量大,使运输和周转减少,注入和倾出铁水方便,可提高生产率;2)铁水在罐中的保温性能好,使铁水的保温时间得到延长,利于调度;3)减少了罐口结瘤、结壳的铁水损耗,也减少了罐子的清理和维修的工作量;4)对铁水还起到了调配混匀的作用。
国内最新采用的320吨混铁车。
320吨混铁车它是由雪茄式混铁罐、承载车和倾翻机构三大部分组成的。雪茄式混铁罐是由二边对称的截头圆锥与中间圆柱体组成的锥简形罐体,可绕中心偏上70毫米的回转轴转动,这是为了使罐体与铁水的合成重心落在回转中心的下方。它保证了罐体的稳定,不会发生自行倾翻的事故,即使在倾翻时发生停电事故,重心也可使罐体自行复位。承载车由16组轮对组成,每四组轮对组成一个小回转架,每八组轮对组成—个大回转架,弓形大车架就支承在二个大回转架上,承载车全长25.8米。倾翻机构有二种速度,在铸铁时采用低速倾翻,倾翻速度为0.015一0.0015转/分;在炼钢车间倾倒铁水时采用高速倾翻,倾翻速度为0.15转/分。它的传动方式采用双电机行星齿轮减速器,低速时采用直流电机可调速驱动,高速时采用直流、交流双电机同时驱动。由于混铁车的回转中心与空罐或满罐时的合成重心相接近,故它的倾翻力矩大大低于铁水罐车,它的倾翻力矩为55吨力米,倾翻电机功率低速时为1.5千瓦,高速时为11千亿。它的供电方式为插销式,插座设在车端部,插销设在翻罐操作处。该车新罐时可装320吨铁水,后期罐可装370吨铁水,空车自重260吨,车辆的走行由机车头牵引,走行速度为8—15千米/小时,轨距为1435毫米,钢轨为60公斤/米,混铁车轮轴的承载为40吨/轴。
- 内容简介:
-
目 录摘 要第一章 概述11.1铸铁机前的铁水运输11.2工艺要求和设备选型21.3铸铁机的发展5第二章 铸铁机生产能力确定及链带受力分析162.1铸铁机生产能力的确定172.2铸铁机每条链带的电动机功率的确定172.3电动机功率的确定212.4电机及其减速器的选择21第三章 铸铁机的零件设计223.1主动链轮轴的设计223.1.1 选择轴的材料223.1.2初步估算轴径223.1.3轴的结构设计233.1.4轴的强度验算263.2从动轮轴的设计293.2.1选择轴的材料303.2.2初步估算轴径303.2.3轴的强度验算303.2.4轴的结构设计33第四章 链带及铸铁模的设计364.1铸铁模364.2链带36第五章 铸铁机的辅助装置设计385.1张紧装置385.2铸铁块的冷却系统385.3铸铁模喷浆装置395.4前方支柱39第六章 铸铁机室的布置406.1铸铁机室的布置形式416.2铁路布置416.3铸铁机中心距的确定416.4操作室,前方支柱及机前机后操作人员的操作台41第七章 创新设计437.1采用双电机驱动437.2 采用挡板防滚轮卡死43结束语45参考文献46本科生毕业设计说明书(毕业论文)题 目:铸铁机设计学生姓名: 学 号:专 业:机械设计制造及其自动化摘要毕业设计作为大学学习最后阶段的教学环节,是对我们四年来理论和实践学习的一次全面、整体、深刻的校验,也是我首次系统地将理论知识应用到工程实际中的一次考验。机械工业担负着装备国民经济各个部门的重任。在改革开放过程中,机械工业又将要发挥重要的作用,为此提高机械工业的产品质量、提高经济效益迫在眉睫。本设计说明书中所涉及的是铸铁机一种滚轮移动式铸铁机。主要内容有铸铁机的工作原理,主要零件的设计,铸铁机链带受力分析。铁水从高炉中出来后,为了解决运输及储存问题而使用的一个将液态铁水铸成小块铸铁块的机械。在设计过程中,实地考察了实习工厂的设备,并借阅了大量的工厂的实际图纸,也参阅了大量的关于矫直机的资料,进行了反复的比较,取长补短,从而完成了自己的毕业设计。 进行大规模的整机的设计,对我个人来说,尚属首次,加之经验不足,知识缺乏,所以在设计中难免会出现错误和考虑不到的地方,我衷心的恳请各位老师给予批评和指正。谢谢。 , 4 , , , . . , , , - -. , , 。 , . , , , , , , . , , , , , , , . .目 录摘 要第一章 概述11.1铸铁机前的铁水运输11.2工艺要求和设备选型21.3铸铁机的发展5第二章 铸铁机生产能力确定及链带受力分析162.1铸铁机生产能力的确定172.2铸铁机每条链带的电动机功率的确定172.3电动机功率的确定212.4电机及其减速器的选择21第三章 铸铁机的零件设计223.1主动链轮轴的设计223.1.1 选择轴的材料223.1.2初步估算轴径223.1.3轴的结构设计233.1.4轴的强度验算263.2从动轮轴的设计293.2.1选择轴的材料303.2.2初步估算轴径303.2.3轴的强度验算303.2.4轴的结构设计33第四章 链带及铸铁模的设计364.1铸铁模364.2链带36第五章 铸铁机的辅助装置设计385.1张紧装置385.2铸铁块的冷却系统385.3铸铁模喷浆装置395.4前方支柱39第六章 铸铁机室的布置406.1铸铁机室的布置形式416.2铁路布置416.3铸铁机中心距的确定416.4操作室,前方支柱及机前机后操作人员的操作台41第七章 创新设计437.1采用双电机驱动437.2 采用挡板防滚轮卡死43结束语45参考文献46第一章概述1.1 铸铁机前的铁水运输铸铁机是为了将铁水连续铸造成铁块而设置的。在高炉车间出铁场上由铁水罐车或混铁车贮存的铁水经铁路运到铸铁机前的前方支柱旁以备浇注。国内高炉铁水的运输设备大部分采用铁水罐车,它是由梨形的铁水罐和承载车二部分组成。它的走行是靠机车头的牵引,它的吊装与倾翻是由专用的起重机来操作的。国内常用的有65吨铁水罐车、ZT1001型铁水罐车、ZT1401型铁水罐车。65吨铁水罐车的铁水罐容量为65吨椭载时罐体总重86吨,罐体中之耐火砖重10吨,车架总重175吨。ZT1001型铁水罐车队铁水罐容量为100吨,满载时罐体总重128吨,罐体中之耐火砖重143吨,车架总重22吨。ZT140l型铁水罐车的铁水罐容量140吨,满载时罐体总重171吨,罐体中之耐火砖重16.5吨,车架总重28.5吨。这三种铁水罐车负载时的最大运行速度为20千米小时,在道岔处允许最大运行速度10千米小时,铁道轨距1435毫米。在现代化的大型高炉车间里,生产的铁水量很大,铁水罐已不能满足运输的要求,因而改用混铁车来完成运输和贮藏铁水的工作。它较之铁水罐车有以下优点:1)容量大,使运输和周转减少,注入和倾出铁水方便,可提高生产率;2)铁水在罐中的保温性能好,使铁水的保温时间得到延长,利于调度;3)减少了罐口结瘤、结壳的铁水损耗,也减少了罐子的清理和维修的工作量;4)对铁水还起到了调配混匀的作用。国内最新采用的320吨混铁车。320吨混铁车它是由雪茄式混铁罐、承载车和倾翻机构三大部分组成的。雪茄式混铁罐是由二边对称的截头圆锥与中间圆柱体组成的锥简形罐体,可绕中心偏上70毫米的回转轴转动,这是为了使罐体与铁水的合成重心落在回转中心的下方。它保证了罐体的稳定,不会发生自行倾翻的事故,即使在倾翻时发生停电事故,重心也可使罐体自行复位。承载车由16组轮对组成,每四组轮对组成一个小回转架,每八组轮对组成个大回转架,弓形大车架就支承在二个大回转架上,承载车全长258米。倾翻机构有二种速度,在铸铁时采用低速倾翻,倾翻速度为0.015一0.0015转分;在炼钢车间倾倒铁水时采用高速倾翻,倾翻速度为0.15转分。它的传动方式采用双电机行星齿轮减速器,低速时采用直流电机可调速驱动,高速时采用直流、交流双电机同时驱动。由于混铁车的回转中心与空罐或满罐时的合成重心相接近,故它的倾翻力矩大大低于铁水罐车,它的倾翻力矩为55吨力米,倾翻电机功率低速时为15千瓦,高速时为11千亿。它的供电方式为插销式,插座设在车端部,插销设在翻罐操作处。该车新罐时可装320吨铁水,后期罐可装370吨铁水,空车自重260吨,车辆的走行由机车头牵引,走行速度为815千米小时,轨距为1435毫米,钢轨为60公斤米,混铁车轮轴的承载为40吨轴。1.2 工艺要求和设备选型 铸铁机是为了将铁水连续铸造成铁块而设置的。当铁水内铁水罐车经铁路运至铸铁机前的前方支柱旁时,这时由铁水罐翻罐卷扬的吊钩将铁水罐的下部吊耳吊起,并使其支爪搭在前方支柱的支承轴上,此时吊钩提升渐渐倾翻铁水罐,铁水经流铁槽流入铸铁机的二排铸铁模内。当铁水由混铁车经铁路运至铸铁机前时,则不需要前方支柱,可直接驱动混铁车的倾翻机构,使罐内铁水徐徐注入到流铁槽内,再经流铁槽流入铸铁机的二排铸铁模内。铸铁模内铁块随着传动链的运行而逐渐被冷却,直至到链带的终端,这时凝固的铸铁块翻落在卸料槽中,沿槽壁沿入收集车内。当传动链返回时,在铸铁机的下部设有喷灰装置,可将石灰浆喷洒在铸铁模上,以防铸造时铁水与模子发生粘连,每台铸铁机均设有二条传动链,同时运转工作。对铸铁机的设计要求有:1)在浇铸过程中应尽量减少铁水的飞溅损失和防止铁水从铸铁模中溢出的损失,高铁水收得率,并应保证铸铁块的质量。2)加强铁水在铸铁模中的冷却速度,缩短铸铁块的冷却时间,可以提高铸铁机生产率,并降低设备重量。3)提高铸铁机设备的零件寿命,减少设备故障,选择经济有效的设备结构形式。4)减轻设备重员,提高机械化程度,尽力降低铸造每吨生铁所消耗的备件重量,并应降低单位重量备件所需的加工台时值。为了减少铁水在浇铸时的飞溅损失,在铁水罐的浇注口下设有流铁槽。为了减低铁水流的落差,流铁槽的底面坡度一般为3%, 流铁槽的出口和铸铁模之间的落差应尽量小,一般都不超过50毫米,铁水流应呈薄而宽的瀑布状注入铁模,这样可减少铁水的飞溅损失和铁流对铸铁模的冲刷。国内现在采用的铸铁机共有二种型式,滚轮移动式和滚轮固定式。 这两种型式的铸铁机都采用铸铁模平行排列、相互塔接方式,模子二端与两边的链条联结,组成一条封闭循环的运输带。链带的前部为浇铸部分,有的设有5米长并与水平组成10一14倾角的浇铸链带,这样在较大倾角的链带上,铁水能更好地越过各铸铁模的搭接口均匀充满各模子,链带的其余部分倾角为6一10左右,这样可防止运行时铁水从模子中溢出造成损耗。在链带的前部还设有可调节链带张紧的装置,当链带销孔磨损时可调节张紧力;当链节需要更换时,应放松张紧装置。在链带的后部,还设有铸铁块的抛卸装置。它用锤子不断敲击端部模子里的铁块,使其脱落铸铁模落入溜槽内。铸铁机的产量,取决于单位时间内铸造出的铁块量。因此铸铁机的产量与链带的运行速度成正比。当提高了链带速度时,往往可使铸铁块在脱莫时还不能很好地冷却下来。其解决办法处采用加长链带的长度或采取喷水强迫冷却等措施。喷水冷却装置都设在链带的中后部,喷水量应先小后入,逐步增加。以免会影响铸铁块的表面质量。当铸铁机链带长度与冷却条件固定时,铸铁机的产量实际上决定于铸铁块在该条件下凝团所需的时间,并且可依凝固所需的时间计算出最高产量时的链带速度值。实际生产证明:滚轮移动式和滚轮固定式的铸铁机都能满足生产要求。它们各有优缺点,滚轮移动式因滚轮随链带移动,由于滚轮与链带加工较粗糙,滚轮在工作肘往往容易掉道,并且在轮轴处温度变化很大。当注入铁水时,铁水温度为12501300c,卸料时铁块温度为500一600c。因此滚轮轴承与链条的轴销处在高温辐射下,润滑困难,磨损很快,许多厂矿都采用人工注油,每班一次。为了改善滚轮的工作条件,设计了滚轮固定式的结构,由于将滚轮固定在基础两上,滚轮可采用滚动轴承干油集中润滑,滚轮的工作条件得以改善,链条则支承在滚轮上移动,链片的底面成为工作面,因此链片的上下两面都必需加工平整,这样就增加了链片的加工量。为了适当减少支承链带的滚轮数量,链带的节距也比滚轮移动式增加了一倍。滚轮移动式为每个链节设了一个铸铁模。滚轮固定式为每个链节设二个铸铁模,这样链板的外形尺寸和重量都较滚轮移动式增大了。由于两个铸铁模都固定在一个链节上,工作时受热应力和变形的影响,滚轮固定式链片与铸铁模的连接处容易破坏,铸铁模的使用寿命也较滚轮移动式为低,此外滚轮固定式设备重量大,零件的加工量较多,但是使用中滚轮固定式的维修工作量少,使用周期长,事故也较少,当更换备品时所需的加工量较大。国内各厂滚轮移动式和滚轮固定式都有采用,工艺流程的布置大致相同。国内各铸铁机的链带首尾链轮的距离为30一60米长,链带运行速度为612米分,最高可达15米分。上部工作部分链带倾斜角为6一10左右。链轮的节圆直径滚轮移动式为1000一1200毫米,滚轮固定式为1500一2000毫米。相邻两铁模间的小心距为280一305毫米。铸铁块的重量为2535公斤左右。链带轨道中心距为870l000毫米。最近国内许多厂都开始生产小块铸铁块,颇受用户欢迎。它的优点是: 1)小块铁在再熔化时可较大块铁节省焦炭约5%以上;2)搬运、装卸方便,使用时不需要再破碎。这是一种新的发展趋势。过去由于铸铁块块度大,冷却成型需要校长的时间,因此铸铁机一般都设计得很长,产量较大的铸铁机最长可达60米以上,设备重量也很大。如果采用小块铸铁,铁块的厚度减小。在同样产量时,冷却面积将大大增加,因此成型需要的时间可大为缩短。这样当产量不变,链带速度相同时,所需的链带长度将可大大缩短。当链长不变时,可大大提高链带的运行进度。小块铁用的铸铁模。它是每模六小块,每小块重3545公斤,铁模材料用HT2547制造,每次铁模内浇铸铁水2l一27公斤。当采用小块铁铸铁模生产时由于小块铁散热面大,冷却快并且铸铁模的周转周期短,相应的铸模温度比大块铁模要高。在相同的冷却条件下,大块铁模在回程时的温度约为100c,而小块铁模温度可达200c,因而必须加强小块铁模的冷却措施。为了提高小块铁模的使用寿命,一般都选用厚度大的铸铁模或铸钢模。为了能保证顺利脱模,应适当增加喷浆的浓度。根据使用单位介绍,以小块铁为原料的化铁炉,可获得以下有利条件:1)铁水温度可提高40c,最高可达1400C左右;2)熔铁时间可缩短,可提高日产量20%左右;3)可节省焦炭5%左右;4)由于铁水温度提高,合金元素Si,Mn烧损可大为减小;5)由于铁水温度提高,铸件废品率可降低30左右。1.3铸铁机的发展铸造用的生铁和炼钢用的生铁要铸成种达20公斤的铁块。在中国常遇到的一些旧高炉车间里就在浇铸场的砂型里铸造铁块;铸完以后将凝固了的铁块打开并将他们收集起来。为了达到这个目的,常采用造型和收集的设备。这种方法的生产率很低的。随着高炉生产的发展,开始采用带有活动铸铁斗的铸铁机。带有铸铁斗的转动台(图1.1)是这种铸铁机最早的构造之一。随着台的转动铁水在铸铁斗中凝固,然后落在车皮上。这种机器很笨重,因此没有得到发展。图1.1 带有铸铁斗的转动台后来在美国出现了带式铸铁机,这种铸铁机在欧洲和苏联也得到了广泛应用。第一架 铸铁机是尤林克铸铁机( ),它的出现在1983年,由两条互相平行而倾斜的带子组成,带子附有铸铁斗,为了冷却铁块起见在铸铁斗后面装有板式运输机。带子速度为3.9公尺/分。运输机的水平部分穿过存有水的槽;其后面向上倾斜部分把铁块运到车皮中。在链带无载的一边喷上石灰水以防止铁水和斗粘上。铸铁机很长,约70公尺;板式运输机要求装设很长的传动轴,这些都使装置变得很复杂化。在后来的构造中板式运输机被取消了;而后来用水浇洒铸铁斗来进行必要的冷却。起初机器是用带有行走滚子的链条传动,后来将它简化,改用链条沿着固定的轮子移动。不过这样的简化在最初的第一种构造中并没有什么益处,因为在那里链条的跳动常把铁水弄出,只是在过了很长时间以后,这种构造才被乌拉尔重型机器制造厂改进而采用。现在来叙述一下目前采用的新式铸铁机。“大卡恩雷斯”和密大利斯脱“工厂的铸铁机。这种铸铁机每昼夜产量为1200吨。这种装置和装在车间附近的旧装置不一样,它是装在车间以外单独的厂房里。有专供铁水罐将铁水到入铸铁机和进行铁水罐修理工作的厂房,在那里有铁路通过;分为:铸铁机的厂房和耐火材料仓库。铸铁块仓库就在铸铁机旁边。在准备工段里有起重机和倾翻卷扬机,起重机的起重量为75/15吨;铸完铁块以后起重机用来清除铁水罐中的废铁和渣;清扫厂房,修理铁水罐,清除大渣块,并当倾翻卷扬机损坏时还来代替它的工作。每一铸铁机都放在一个单独的跨间里。在厂房里有倾翻铁水罐时用的台柱,及铸铁部分用的露天工作平台,工作平台旁边有铸铁工人室和司机室,司机室内有铸铁机操纵台。通往铸铁带张紧装置去的通道必须宽畅;从机器下面清除碎铁必须很方便。地面和铸铁带下面部分之间的距离(考虑到有铸铁斗)必须不小于500厘米。铸铁带的过道是一有钢筋混凝土地面的封闭长廊,铸铁带的二边留有宽10002000厘米的通道。轨道和通道地面之间有250300厘米的距离,以便于从铸铁带下面取出碎铁来。通道墙上盖有曲形铁板。窗上有活动百叶窗。在顶上有引出蒸汽的天窗。厂房的铸铁路上装有拉铁和小车的绞盘,为了能不用机车来调度铁水罐和小车。绞盘是一带有平滑垂直滚筒的绞车,在绞车出来的绳子上带有几个抓子来拉动车辆。这是最好用循环绳索的绞盘。在大多数工厂里修理铁水罐的地方直接就在铸铁机旁边,这里有砌砖用的坑,烘干铁水罐的活动装置,加工车间和混凝土车间,还有起重量75吨的吊铁水罐的起重机。铸铁机由二条循环的带组成铸铁用的链带。每一条带是由二条链条及链条上的铸铁斗组成,铸铁斗组成,铸铁斗之间相互紧靠在一起。铸铁斗本身也是铸铁制成的。每一铸铁斗能装4550公斤铁水。链条绕在链轮上,主动链轮放在卸载的一端,它们支流电动机(40千瓦,6001000转/分钟)或交流电动机(20.5千瓦,速度不变)通过四级圆柱齿轮组成的减速器和安全连轴节带动。当一个电动机坏了的时候,连轴节就将链轮轴连接起来,使得第二架电动机能同时带动二条铸铁带,铸铁带统一操纵室操纵,操纵室就在铸铁机浇铸部分的旁边。张力装置的螺丝可以使头部轴承移动,而移动头部轴承就可调节带的张力大小(图1.2)。链带轴的水平距离为43公尺;带长为90280厘米;一根带上的铸铁斗数目为296个;滚子间的距离为305厘米。导轨的末端部分是弯曲的,使得带的滚子能很平稳地从轨道上过到链轮上去。轨道的下面部分有5公尺长是和水平线成14的角度。这样使浇铸时液体生铁在铸铁斗里分布得均匀。铸铁带其他部分的倾斜角度为6。液体生铁经过浇铸槽到二边的铸铁带上,浇铸槽是由一个四角形的漏斗,中间延长部分(其轴线和铸铁机的轴线平行)以及二根直角形的支槽组成。槽的各部分都涂有耐火泥,上面还有砂子。图1.2 链子张力装置流铁槽能使铁水直接注在铸铁斗的整个表面上(这样使铸铁斗磨损得均匀些)。铸铁斗和铸铁槽之间的空隙不能超过50厘米。在某些情况下,在卸铁块的一面装有抛卸装置(),表示在图1.3上,它对铁块的落下起着某些阻挡作用。由于弹簧发热,有时失去弹性,因此这种装置工作得不好,它会卡住铁块,而这样就会使铸铁带发生撞击。图1.3抛卸装置在卸铁块的一边还装有固定槽,在固定槽下面有用绳轮带动而绕横轴转动的槽,这些槽上必须盖有用钢轨做的铺板或锰钢制的孔板台柱的用途是(图1.4)在倾斜铁水罐时使口的移动减到最小。如果流槽直接放在铸口之下的话,则可避免铁水的喷溅。台柱可以是铸铁的,亦可用钢板焊接成。它们的尺寸根据铁水罐方面传来的力来计算。下面研究一下铸铁机的零件。老式链条的部件(图1.5)是由二金属片组成,每一部分和其上面的连接板铸成一个整体,但留有一孔以供螺栓与铸铁斗凸耳固定之用。这种有一片金属片坏了就要换去整个部件。在部件的槽中放有连接板5,铸铁斗的凸耳6用螺栓固定在它们上面(因此,二个部件和一块连接板像铸成整体一样)。连接板5被焊接在其上面的筋7上,连接板8和开口销9固定着。保护板10的作用事使铁水不致溅入部件和轮子之间。老式链轮是制成整体的,这样也很不方便,因为如果一个齿磨损以后,必须将整个链轮图1.4 铸铁机的台柱图1.5 老式链条部件换去。新式链轮是合成的,它由铸铁圆盘和钢齿圈组成,尺圈由一些弓形片组成,它们通过螺栓固定在圆盘上,而且更换它们时不需要将铸铁带卸下。在铸铁机链带的上方有冷却装置(图1.6),其中第一冷却系统由二个直径为43公尺的输水管和一个(中间的)直径为51厘米的管子组成,后者将水输送到冷却系统去。图1.6 冷却水的管路系统1冷却装铁水的铸铁斗;2冷却后部;3冷却前部输送管的下部有许多直径为1.53厘米的小孔,他们分布成布棋式,水就通过这些小孔射在铸铁斗上。在离张紧链轮1/3带长度的地方开始洒水。铁块冷却到600左右从铸铁带上落下,经过落槽落到平板车上。在每一铁路线上都有六个喷水头用来进行再次冷却.图1.6机器前部轨道的冷却倾斜的保护板和轨道也都要冷却。在图1.6上表现的是轨道冷却方法之一,图中符号:1固定在轨道上的板;2用水冷却的孔腔。水通过专门的支管进入备制石灰水的房间内。铸铁机上水的总消耗量大约是每一吨生铁需要1.52立方公尺水。喷石灰水装置就在铸铁带的下面,这是一个紧靠在轨道上的水箱,水箱上有喷射器和清洁用的孔(图1.7)喷射器锥体的下面放在有石灰溶剂的箱中。图1.7 喷石灰液的喷嘴蒸汽通过里面的管子,从喷嘴出来,同时把石灰液也带了出来,石灰液再进入锥形喷嘴的环形槽中去,然后被喷出来,喷成扇形,这时在喷口上面通过的翻倒过来的铸铁斗内表面就溅满可石灰水。每一条带下面有三个喷口。石灰液在一间单独的房子里制造,表示在图1.8上,石灰从铁路上运来倒在容积20吨的钢筋混凝土料仓里,然后用提升机将石灰从这一料仓送往另一料仓(是铁制的,在上面),随后再送往混料箱,混料箱里有一混料器,它用轮叶将石灰和水混在一起。提升机和混料器由功率为4.5千瓦,n1400转/分的电动机带动。石灰溶液从混料箱经过管子进入放有喷射装置的水箱内,这种水箱在上面已经叙述过了。往铸铁斗上喷石灰水的目的是使铁块不致黏在料斗上面。希连珂指出最好用喷射枪(在喷涂铁水罐时用的)来代替上述装置,因为它可以使料斗上图上比较厚的一层石灰液(达2公分)。铁水车将铁水送往铸铁机,为了使支撑凸耳12对准台柱,因此铁水车停下时必须使铁水罐的中心和铸铁机轴线重合,然后,铸铁带开始走动,同时,利用图1.8准备石灰液倾翻卷扬机或起重机使铁水罐慢慢地倾翻,铁水经过受料漏斗立即流在二条带上。带的运动速度612公尺/分,有时达到15公尺/分,这样就要加强冷却。铸铁斗(图1.9)必须制成这样:即每一铸铁斗的边缘1必须盖住前一铸铁斗的边缘2。如果铸铁斗装得太满(铁水超出aa面)的话,铁水就会流到下面的铸铁斗中去。其余的边缘都比这水平高,而边缘1的形状是带有边缘3的槽,边缘3插在前一铸铁斗的侧边缘4之间。当铸铁斗从斜度14(铸铁机尾部之处)转到6时,铁水表面的位置为(bb)。图1.9 铸铁斗的铸铁斗铸铁斗的斗体内部铸入一些圆的钢棒5。它们用来使裂开的铸铁斗不致断开。铸铁斗用下列材料制成:a)珠光体铸铁,成份:C3.53.6%;Si1.82.0%;Mn0.81.0;用砂型铸造(不是用铁模);b)铸铁,高铬铸铁,铬锰铸铁,铬铜铸铁,含铅铸铁;c)退火后的铸钢。如果要得到平滑的平面,铸铁斗最好是用软钢冲压制成。为了减少磨损起见,小轴用轧制钢材制成,它的成份为:C0.45%;Si0.19%;Mn0.6%;Cr0.58%;Ni0.12%;P0.014%;S0.02;小轴放在830850的油里淬火,淬火后,用大约400500的温度回火,小轴的硬度350H。链条的金属板和滚子用“加脱非力特”锰钢( )制成,成分如下:C0.97%;Si0.36;Mn11.95。为了减少硬度,钢经过退火(将硬度从H=450降到H=220)。齿圈用铸钢制成,而链轮的圆盘用铸铁制成。为了延长铸铁斗的寿命,在注铁水以前将它们加热到6080,否则,由于热铁水的关系,由于铁水的增加和敲出黏住铁块时的冲击,会产生横向裂纹,在吊耳断面上裂开。由于螺栓延伸的缘故,铸铁带的空载部分会产生下垂现象。为了消灭螺栓延伸现象;工程师鲁新()建议用带有抓钩的夹子来将铸铁斗固定在链条上。图649 螺栓的延伸和铸铁斗与链条固定的破坏情形图650用抓钩的夹板固定铸铁斗和链条(没有螺栓)很多铸铁机链带的滚子和小轴都用重油进行人工润滑,这样使不合理的,因为会落进一些杂物使套筒和滚子磨损,使它们之间产生打16厘米的空隙,因而破坏了铸铁斗间连接的紧密性,结果造成铁水的损失。其他情况下,用黄油润滑,每昼夜往小轴的圆柱槽中加一次油,油由此经过小轴的轴向流槽流往工作表面。图651,a,上得阀用来防止漏油。图651,b,表示的是一种比较合理的阀门构造,它的杆子没有倾斜的可能。图651用于润滑行走滚子轴的阀门上面已经介绍了铸铁机的形式及其构造,下面对铸铁机进行设计计算。第二章 铸铁机生产能力确定及链带受力分析2.1 铸铁机生产能力的确定由于本铸铁机是双链带滚轮移动式,所以其生产能力可按下式计算: 式中 铸铁机生产能力,吨/昼夜。 铸铁块重量,公斤。 两个铁模的中心距离,米。 链带速度,米/分。 铸一罐铁水的浇注时间与铸一罐铁水的总时间比。 铸铁机作业率,可取0.69。 铁水收得率,可取0.975。 2.88 单位换算系数,即 其中: 式中: 提升铁水罐时间为2分钟。 浇注时间为25分钟。 落罐时间为3分钟。 调车对罐时间为10分钟。代入上式 : = = 代入双链带铸铁机的生产能力公式 中得: 吨/昼夜2.2 铸铁机每条链带功率的确定 计算数据: 链带的速度 运输机长度 链节距 链带倾角 链轮齿数 链节每节所有零件的总重 铁块重量 计算: 图2.1 铸铁机计算简图从2点开始确定各段链带的运行阻力,在这一点链带的拉力将是最小的,此拉力由张紧装置控制。 取 : 链带21段的运行阻力 式中: 带重的分量 摩擦力的分量阻力 取负号 ,因为在21段中它向着驱动装置的方向。链带每米的自重由下面的方法确定: 每米链带上的节数 每米链带的重量 kg阻力系数: 式中:C组件与滚轮轮缘的摩擦系数,考虑到歪斜取从C=4。 滚轮轴承的摩擦系数,考虑到磨损和不利的工作条件取0.4。 滚轮踏面的滚动摩擦系数,0.08 轴承直径,40 滚轮直径,190 0.067 代入上述数值得: = N链条在1点的拉力:从2点顺着链带运动方向继续算下去,并假定由于链轮上有阻力,链条张力的提高是绕上端的10%,因而得:作用在张紧装置上的力: 在34段上的阻力: 式中: 每米链带上铸铁模中生铁的重量 = 链条在点4的拉力: 考虑到磨损,设在驱动链轮上的损失,则带子的链条拉力的计算值为:在两个驱动链轮上的圆周力: 加速过程中链条的附加动力: 式中加速度: 其中: 链条节距 =0.382链轮齿数 =20两跟链条总的最大拉力为:2.3电动机功率的确定当稳定运动时链条轴上的功率:考虑到四级减速器的效率,电动机功率为:鉴于在链条表面磨损和歪斜的情况下工作的可能性把电动机功率增大到1.5倍: 由于两跟链条是由一个电机带动,所以电机功率增大2倍:2.4电机及其减速器的选择电动机选用冶金起重用的三相异步电动机,型号:YZR315M-10 功率:75KW 额定转速:579r/min。减速器由厂家自己制作,选用四级减速器,其速比为38.6。效率为0.848。第三章 铸铁机的零件设计3.1主动链轮轴的设计3.1.1选择轴的材料该轴用于载荷较大,而无很大冲击的重要轴,因而选用调质处理的40Cr,其力学性能。3.1.2初步估算轴径(1)与主动链轮连接处轴的最小轴径由于此处受到链轮圆周力给它的扭应力又受到链带拉力给它的弯应力,所以按弯扭合成强度估算最小轴径。此轴为实心转轴应该使用公式:式中:轴的直径。 轴在计算截面所受的弯矩 轴在计算截面所受的扭矩 为校正系数 =1计算和 带入公式: 由于此轴在连接主动链轮处有两个键槽,轴径应增加10%,轴径d=200.4+20.=220.4mm。但此轴的工作环境较为恶劣实际应力变化也较大,所以应根据现场工作环境适当提高安全系数增大轴径,将轴径增大到d=250mm。(2)与连轴器连接处轴的最小轴径由于与连轴器连接处轴只受扭矩的作用,所以应按扭转强度估算最小直径。材料40Cr查表知取C=110,输出轴的功率,为四级减速器的效率,=0.848,为电动机实际输出功率,输出轴的转速。 按扭转强度估算最小直径的公式为:此轴有两个键槽,直径应该增加10%,。但此轴的工作环境也较为恶劣,实际应力变化也较大,所以应根据现场工作环境提高安全系数,轴径增大为d=220mm。3.1.3 轴的结构设计根据轴的受力简图和主要零件的布置图,初步估算轴径,进行轴的结构设计。 图3.1 轴上主要零件的布置图(1)轴上零件的轴向定位齿轮的一端靠轴承套定位,另一端靠轴肩定位,装拆,传力均较方便。两端轴承常用同一尺寸,以便于加工,安装和维修。连轴器靠轴肩定位。为了便于装拆轴承,轴承处轴肩不宜过高,左边轴承的两侧均由轴肩定位。 图3.2轴上零件的装配方案(2)轴上零件的周向定位连轴器与轴的周向定位采用两个平键连接。根据轴的直径查相关设计手册查得,其一是普通半圆端平键,另一个采用普通半圆端平键。两个链轮与轴的配合均为。两个轴承套与轴的配合均为。链轮与轴的周向定位采用4个右边切向键和4个左边切向键固定,其结构如图3.3所示。左边切向键右边切向键右边切向键左边切向键图3.3切向键(3)确定各段轴径和长度定位轴肩的高度。对于轴长可根据轴径相关设计手册,所以对于轴径,右取。对于轴长,取决于轴上零件的宽度及它们的相对位置。与连轴器相连部分的长度为,考虑到连轴器与轴承不能靠的过近,要保持一定的距离,取连轴器与轴承间的定位轴肩长度为,轴承套的宽度为,所以取取轴承套配合段轴的长度为。与链轮配合这段轴的长度为,另一段链轮与轴的配合长度也为。两链轮间距离,主要由铁水模的宽度确定,其间距可定为。根据以上考虑可确定每段轴长,并可算出轴承与齿轮,连轴器间的跨度。 图3.4 轴的结构设计3.1.4 轴的强度验算作出轴的受力简图(即力学模型)如图3.5a所示,取集中载荷作用于齿轮及轴承的中点。(1) 齿轮作用力的大小转矩:圆周力: (2)求作用在轴上的力工作拉力: 图3.5 轴的强度计算(3)求轴承上的支反力(4)画弯矩图截面G处的弯矩为: 截面D处的弯矩为:(5)画转矩图截面D处的转矩:截面C处的转矩:截面E处的转矩:(6)按弯扭合成应力校核轴的强度对于同时受到弯矩和转矩作用的转轴,可针对某些危险截面(即计算弯矩大或有应力集中或截面直径相对较小的截面),按转矩和弯矩的合成强度进行校核计算。根据第三强度理论,其强度条件为:但此轴是实心圆轴,上式变为:式中:W轴的抗弯截面系数 轴的抗扭截面系数 =2W则上式可写为:其中,为计算弯矩或当量弯矩,考虑到弯矩M所产生的弯曲正应力和转矩T所产生的扭转切应力性质不同,将上式修正为:其中为考虑转矩性质的应力校正系数。截面G,D受的弯矩最大,截面G处即受的转矩最大又受的弯矩也最大,故截面G为可能危险截面,查表得。以知:,因此轴为单向回转轴,视转矩为脉动循环。则:代入公式:中得:所以其强度足够。截面E处虽仅受转矩,但其直径最小,故该截面亦可能危险截面。所以其强度足够。3.2从动轮轴的设计3.2.1选择轴的材料该轴无特殊要求,因而选用调质处理的45号纲。3.2.2初步估算轴径此轴只承受弯矩,可按弯扭强度估算轴径。此轴为实心转轴,应使用公式:式中:轴的直径。 轴在计算截面所受的弯矩 轴在计算截面所受的扭矩 为校正系数 为许用弯曲应力 计算E,D截面的M及T此轴只受转矩,故T=0。代入公式:此轴与链轮连接处有一个键槽,故直径增大5%,但此轴的工作环境较主动链轮轴还要恶劣,实际应力变化也较大,且受高温铁水模背面的烘烤,故应根据现场环境提高安全系数,轴径增大为d=175mm。3.2.3 轴强度的验算作出轴的受力简图,如图3.6a所示,取集中载荷作用于齿轮及轴承的中点。图3.6轴的强度计算齿轮作用力大小圆周力:求作用在轴上的力工作拉力:求轴承上的支反力画弯矩图截面E处的弯矩为:截面D处的弯矩为:按弯扭合成应力校核轴的强度对于同时受到弯矩和转矩作用的转轴,可针对某些危险截面(即计算弯矩大或有应力集中或截面直径相对较小的截面),按转矩和弯矩的合成强度进行校核计算。根据第三强度理论,其强度条件为:但此轴是实心圆轴,上式变为:式中:W轴的抗弯截面系数 轴的抗扭截面系数 =2W则上式可写为:其中,为计算弯矩或当量弯矩,考虑到弯矩M所产生的弯曲正应力和转矩T所产生的扭转切应力性质不同,将上式修正为:其中为考虑转矩性质的应力校正系数。截面G,D受的弯矩最大,故截面G,D为可能危险截面查表知。以知此轴只受弯矩和,其不受转矩故T=0,两截面所受弯矩相同,只需校核一个截面即可。将其代入式中得:故其强度足够。3.2.4轴的结构设计根据轴的受力简图和主要零件的布置图(图3.7),初步估算轴的轴径,进行轴的结构设计。轴上零件的轴向定位齿轮的一端靠轴肩定位,另一端靠轴套定位,装拆,传力均较方便。两端轴承常采用同一尺寸,以便于加工安装和维修,轴承与齿轮间设置一个轴肩。如图3.8。图3.7 轴上主要零件布置图轴上零件的周向定位齿轮与轴的周向定位均采用平键连接,根据轴的直径由有关设计手册查得齿轮与轴的连接键选用半圆端平键。轴与链轮的配合为,轴与轴承套的配合公差为,轴承套与轴承的配合为。图3.8 轴上零件的装配方案确定各段直径和长度(图3.9)图3.9 轴的结构设计定位轴肩的高度从相关设计手册可查得,所以从左边取轴径,。对于轴长取决于轴上零件的宽度及它们的相对位置,所以左边与轴承配合的轴段长为261mm。与链轮配合的轴段长取决与链轮的宽,取其长为377mm。两链轮间的长度主要取决于铸铁模的宽度,取长为625mm。考虑轴的结构设计工艺性考虑轴的结构工艺性,在轴的左端与右端制成倒角,为了与轴承套配合,靠近链轮处制出R=5mm的圆角,为了使链轮的安装方便安装链轮主的轴肩制出的倒角,由于左右零件的布置对称,所以另一侧也按上面的尺寸进行加工。第四章 链带及铸铁模的设计4.1铸铁模铸铁模(图4.1)做成能容4555kg重的生铁模子。每个模子的边缘1必须盖住前一个模子的边缘2上,如果模中铁水装得太满(铁水面超过a-a面)时,铁水就流到下面的铸铁模中去。铸铁模用铸铁铸成。铸铁的模子里铸入加固用的圆钢棒,它用来使有裂纹的铸铁模不致断开。也有用钢模的寿命比铁模的长一些。铸铁模常因为高温应力产生的裂纹而报废。图4.1 铸铁模4.2链带链带结构主要有两种形式,一种是滚轮移动式,另一种是滚轮固定式。该设计铸铁机采用的是滚轮移动式,其结构如图4.2所示。部件1用小轴2在两边联接,小轴2上有转动的滚轮3。当链带运动时,滚轮3就在导轨4上滚动。在部件1的槽中放有连接板5,铸铁模的凸耳6用螺栓固定在它们上面。连接板上面焊有筋7,盖板8用开口销9固定住。这种结构形式的链带,由于滚轮是移动式的,所以滚轮的润滑是比较困难的。 图4.2 铸铁机的链带结构第五章 铸铁机的辅助装置设计5.1张紧装置在铸铁机的头部(浇注铁水部分)装有调节链节松紧用的张紧链轮,它借助螺旋张紧装置可以移动,行程可达600mm。图5.1 从动轮张紧装置5.2铸铁块的冷却系统铸铁块的冷却系统有下面带有小孔的水管组成,水管装在铸铁模链带上方(如图5.2),长度为链带的2/3。同时在靠近卸铁端的1/3长度增加水管的数目,以便于加强铸铁块的冷却。图5.2 铸铁模上面的喷水管道配置图为了不使冷却水喷到铸铁模外面,并且使水流分布均匀,有时在靠近卸铁块端的链带上面装上罩子(图5-3)。在罩子上面开有孔2,以便放出蒸气。 图5.3 喷水管上面的罩子1罩子;2排蒸汽的孔;3喷水管;4铸铁模铸铁块从铸铁机卸铁端的铸铁模中掉出来时,其温度可达600左右,所以在导槽和铁路平车上还要对生铁进行继续冷却。5.3铸铁模喷浆装置为了使生铁块不致粘在铸铁模上,须在铸铁模内表面上喷一层石灰浆,滚筒式喷浆装置如图4-4所示。滚筒以高速旋转()将石灰溶液抛射到铸铁模内表面上,这里没有喷嘴,不致产生堵塞问题,因此石灰液的浓度可大些。5.4前方支柱前方支柱设置在铁水罐车铁路线旁铸铁机的前方,以支持铁水罐的支爪。当倾翻铁水罐时,应使罐口的移动尽可能地减小。这样铁水注入铁水流槽时造成的喷溅损失也就减少了,前方支柱结构如图5.5所示。前方支柱两侧的支承轴中心线安装位置,标高与两边支柱的中心距离必须与铁水罐,铁水罐车相适应,前方支柱所承受的载荷为翻罐过程中罐车水重量之一部分,在整个翻罐过程中负荷是变化的,应按最大负荷来设计前方支柱的支承,图5.4 滚筒式喷浆装置并按倾翻力矩值校验地脚螺钉。由于前方支柱处在高温下工作,应确保有足够的强度和刚度。还必须提到的是在设计支撑轴套时,应保证轴套的停位必须向下。有的曾发生由于支承轴套下部的翼缘外翘,从而进入铁路允许通行的净空间尺寸范围。当铁水车移动时会造成碰撞事故。在设计时应保证支承轴套的断面重心落在下部翼缘上,支承轴套的轴孔与轴的配合应选择灵活松动的配合,保证支承轴套在翻后能自动复位,防止翼缘外翘而发生事故。图5.5 前方支柱第六章 铸铁机室的布置6.1铸铁机室的布置形式铸铁机室一般具有两种形式:一种是与铁水罐修理库合在一起的,这种布置形式可取消机前调车设备和检修吊车。操作灵活以及投资较省,但布置较拥挤。另一种形式是与铁水罐修理分开,这种布置设备和投资较多。6.2铁路布置当铸铁机室具有二台铸铁机时,厂房内应设有三条铁路。一条翻罐线,一条走行线,一条为清理机前残渣残铁的尽头线。每台铸铁机机后应设有单独的铁块车皮停放线。机前翻罐线与机后铁块车停放线的布置与前方支柱和机后流槽相配合。铁路线之间的中心距应符合铁路净空的要求。6.3铸铁机中心距的确定为了方便于对罐及调车,两台铸铁机之间的中心距离应为罐车长度的三倍并加12米的脱钩距离。6.4操作室,前方支柱及机前机后操作人员的操作台操作室的布置位置保证室内操作人员在操作台处能方便地看
- 温馨提示:
1: 本站所有资源如无特殊说明,都需要本地电脑安装OFFICE2007和PDF阅读器。图纸软件为CAD,CAXA,PROE,UG,SolidWorks等.压缩文件请下载最新的WinRAR软件解压。
2: 本站的文档不包含任何第三方提供的附件图纸等,如果需要附件,请联系上传者。文件的所有权益归上传用户所有。
3.本站RAR压缩包中若带图纸,网页内容里面会有图纸预览,若没有图纸预览就没有图纸。
4. 未经权益所有人同意不得将文件中的内容挪作商业或盈利用途。
5. 人人文库网仅提供信息存储空间,仅对用户上传内容的表现方式做保护处理,对用户上传分享的文档内容本身不做任何修改或编辑,并不能对任何下载内容负责。
6. 下载文件中如有侵权或不适当内容,请与我们联系,我们立即纠正。
7. 本站不保证下载资源的准确性、安全性和完整性, 同时也不承担用户因使用这些下载资源对自己和他人造成任何形式的伤害或损失。

人人文库网所有资源均是用户自行上传分享,仅供网友学习交流,未经上传用户书面授权,请勿作他用。