塑料油壶盖的模具设计
39页 14000字数+说明书+任务书+开题报告+外文翻译+10张CAD图纸【详情如下】
型腔镶块.dwg
塑料油壶盖.dwg
塑料油壶盖总装图.dwg
塑料油壶盖的模具设计开题报告.doc
塑料油壶盖的模具设计说明书.doc
外文翻译塑料模具的发展.doc
定位圈.dwg
导套.dwg
导柱.dwg
拉料杆.dwg
浇口套.dwg
申报表正面.doc
申报表背面.doc
登记表背面.doc
螺纹型芯.dwg
限位拉杆.dwg



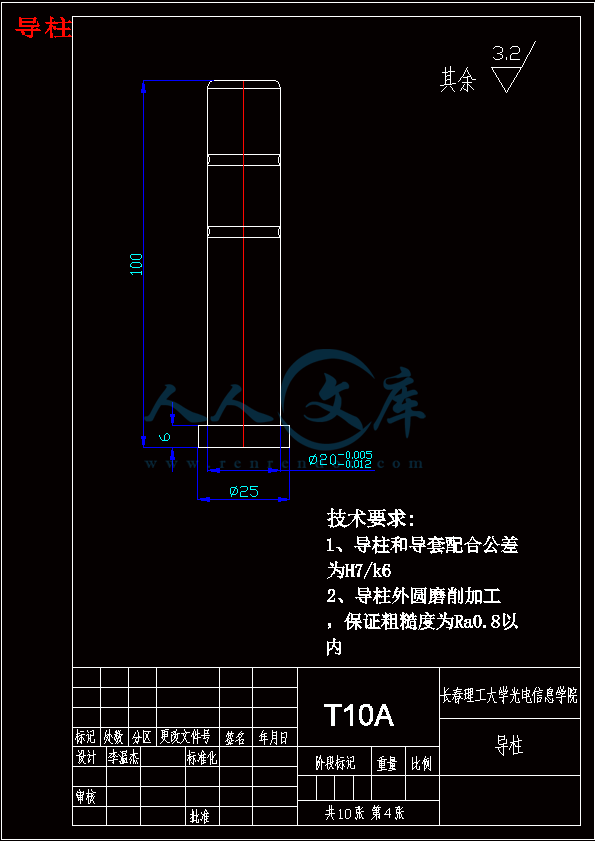
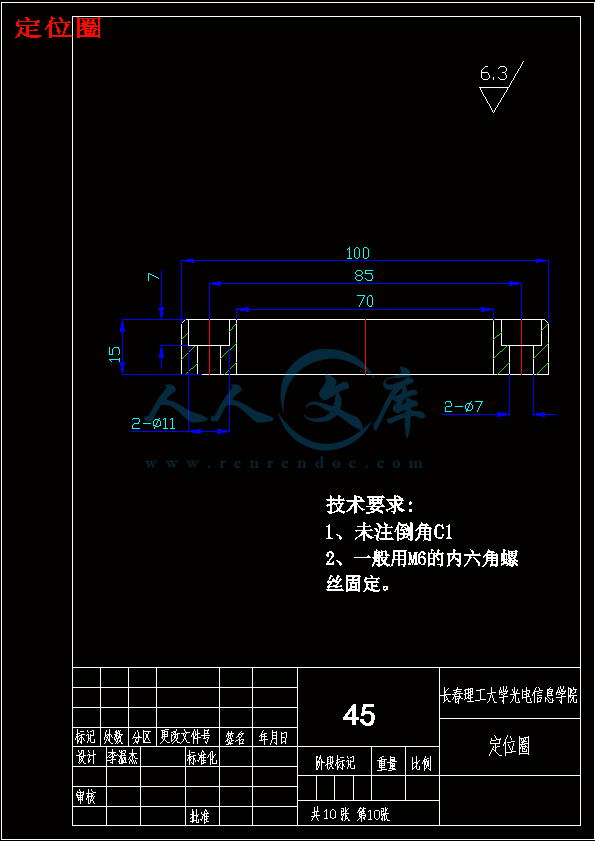

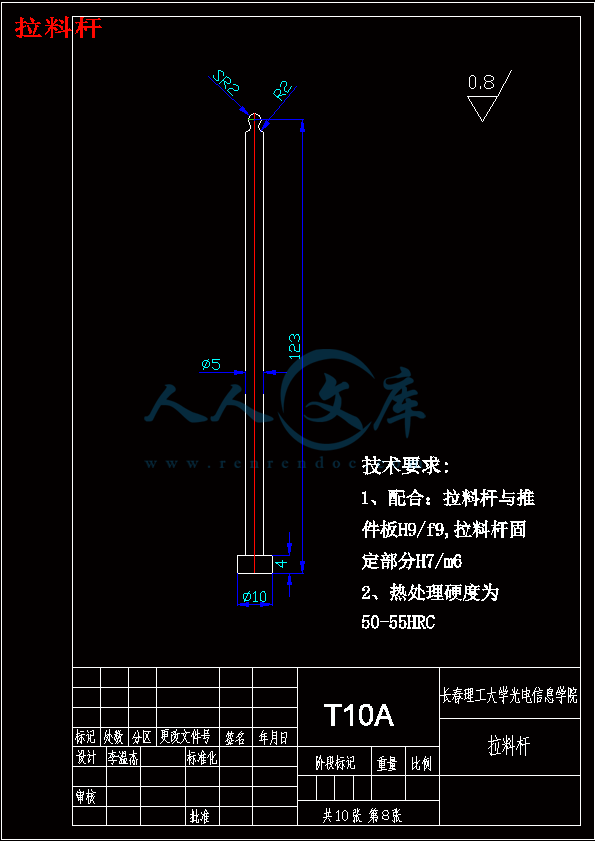
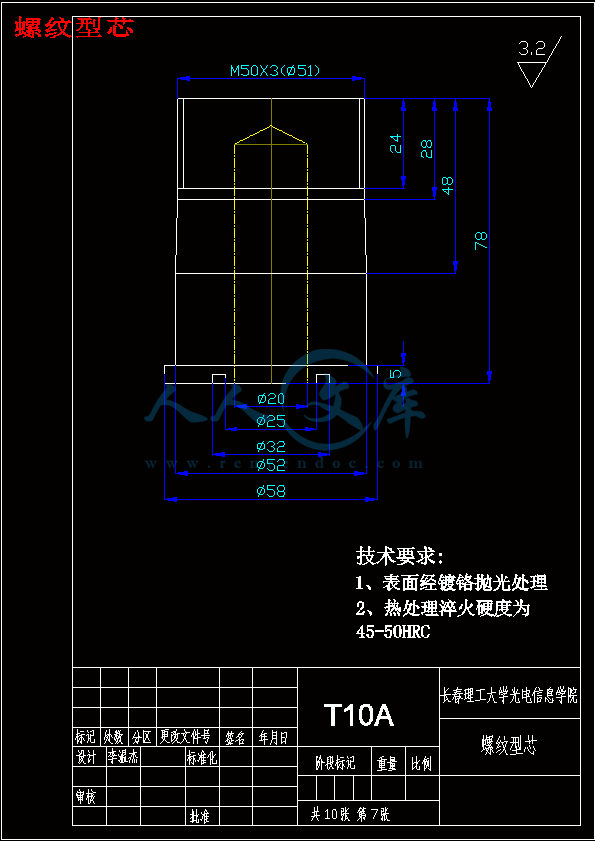
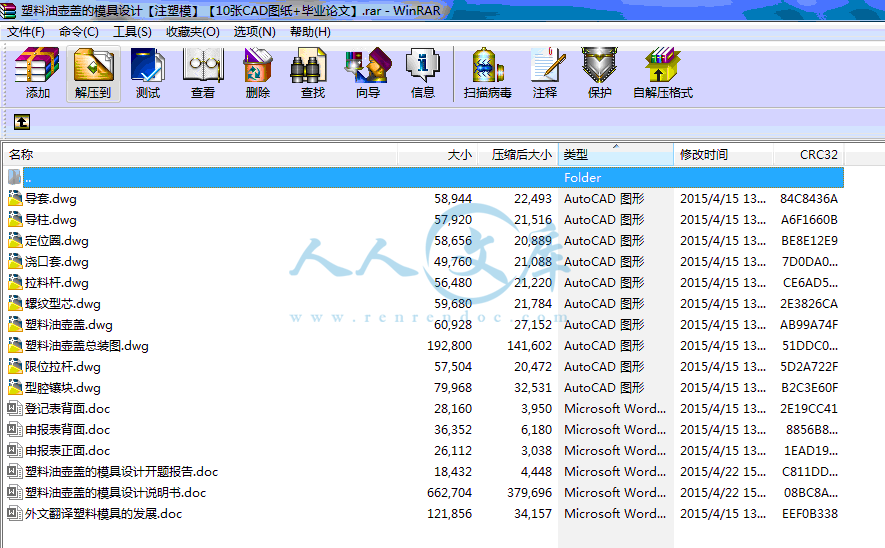

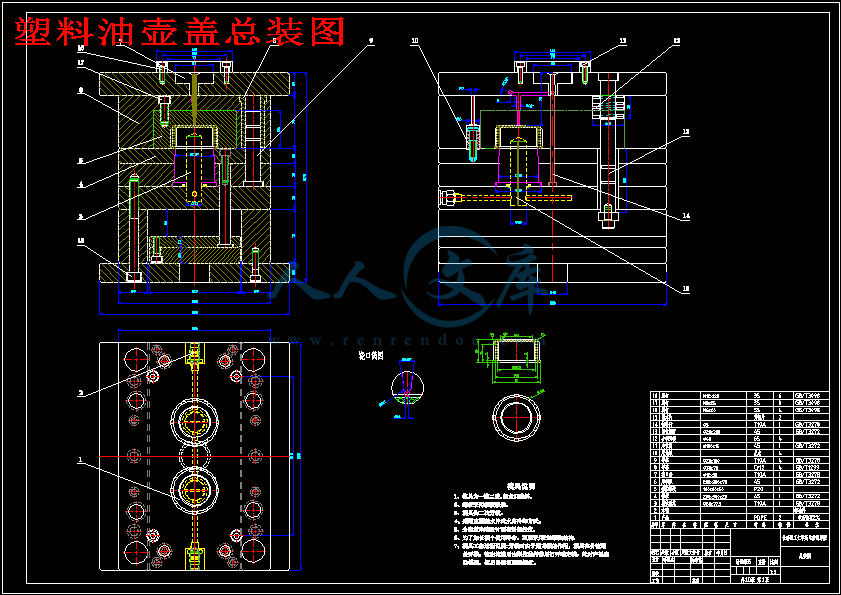
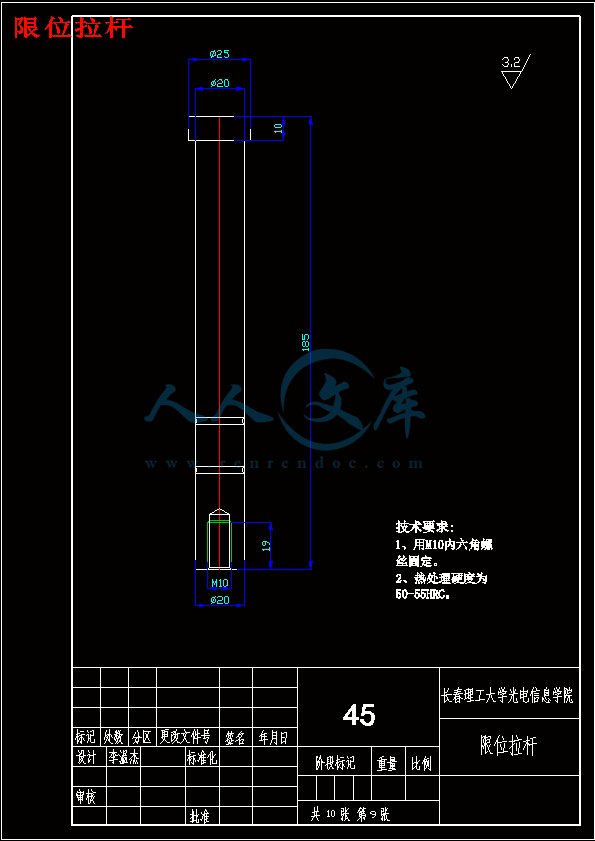
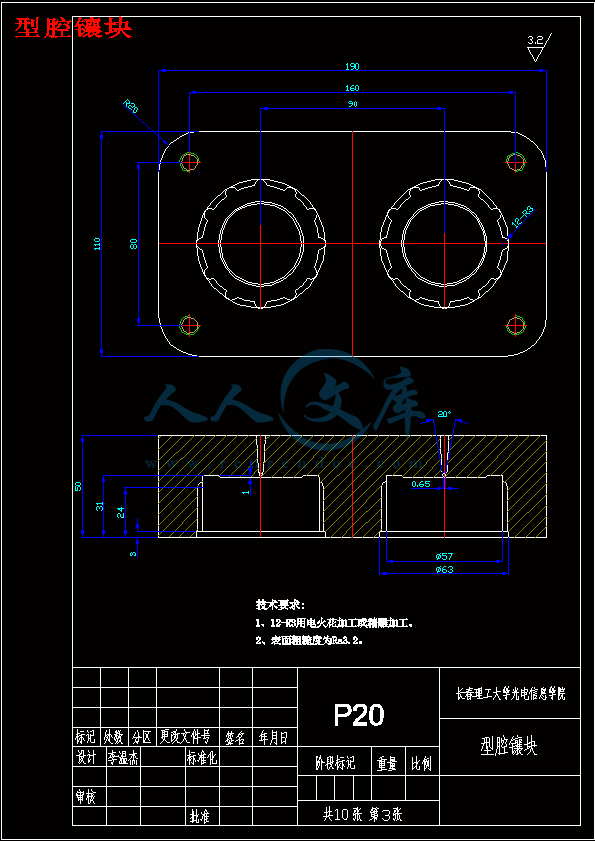
摘 要
随着现代社会的发展,模具行业也发展越来越快,模具加工精度,模具的应用范围都越来越广,因此模具在社会发展中的作用和地位也越来越大,越来越高。塑料注射模具是成型塑料制件的一种重要工艺装备,在塑料制品的生产中起着关键作用,在生产实践中得到了较为广泛的应用。本次毕业设计以塑料油壶盖为例,通过对塑件进行制品分析及材料工艺性,初选了注射机的型号与规格,确定塑件注射工艺参数,设计注射模的结构等这一过程,讲述了模具的设计过程与设计方法。通过这一过程,不但了解和掌握塑料模具设计的基本原则、方法,而且能较为熟练的使用计算机CAD绘图软件,为今后从事设计工作打下坚实的基础。
关键词:塑料油壶盖模具 二次开模 拉料杆 螺纹强脱 试模
Abstract
With the development of modern society, the mold industry has developed more and more fast, precision mold, mold application range are more and more widely, and the status of the mold in the social development in the role is also growing, more and more high. The plastic injection mold is an important tooling molding plastic articles, plays a key role in the production of plastic products, has been widely used in production practice. The graduation design in plastic pot cover as the example, through the process of product analysis and material of plastic parts, primary models and specifications of the injection machine, determine the injection molding process parameters, the process design of the injection mold structure, describes the design process and design of mould method. Through this process, not only to understand and master the basic principles, methods of plastic mold design, but also can use the computer CAD drawing software more skilled, engaged in design work for the future and lay a solid foundation.
Keywords: Plastic oiler cover mold the two opening pulling rod strong screw removal test mode
目 录
绪 论........................................................................1
第一章 塑件分析.............................................................4
1.1塑件结构材料分析.........................................................4
1.2 塑件材料分析.............................................................5
1.3 塑件成型工艺分析.........................................................6
第二章 初选注射机的型号和规格..............................................8
2.1注射机概要................................................................8
2.2注射机分类................................................................8
2.3注射机选择................................................................8
第三章 塑件注射工艺参数的确定............................................10
3.1塑件的结构工艺性.........................................................10
3.1.1塑件的尺寸精度分析...................................................10
3.1.2塑件表面质量分析.....................................................10
3.1.3塑件的结构工艺性分析.................................................10
3.2塑件的生产批量...........................................................11
3.3有关计算分析.............................................................11
3.3.1计算塑件体积和质量...................................................11
3.3.2确定型腔数量.........................................................11
3.3.3确定注射成型的工艺参数...............................................11
第四章 注射模的结构设计..................................................13
4.1 确定分型面..............................................................13
4.2确定浇注系统............................................................13
4.2.1浇注系统设计要点...................................................13
4.2.2主流道设计..........................................................14
4.2.3分流道设计..........................................................14
4.2.4点浇口设计料穴设计.................................................15
4.3确定型腔、型芯的结构及固定方式.......................................17
4.3.1型腔、型芯的结构设计...............................................17
4.3.2固定方式............................................................19
4.4型腔和型芯的工作尺寸计算..............................................19
4.4.1型腔尺寸计算........................................................19
4.4.2固定方式............................................................20
4.5型腔壁厚和底板厚度计算................................................20
4.5.1模具型腔壁厚的确定.................................................20
4.5.2动模垫板厚度理论计算公式..........................................20
4.5.3模具型腔模板总体尺寸的确定........................................21
4.6螺纹脱出方式的设计.....................................................21
4.7确定模具的导向机构.....................................................22
4.8冷却方式................................................................25
第五章 注射机有关设计的校核..............................................26
5.1模具闭合高度的确定......................................................26
5.2模具闭合高度的校核................................................... 26
5.3模具安装部分的校核.....................................................26
5.4模具开模行程的校核.....................................................26
5.5注射量的校核............................................................26
第六章 模具装配和试模..............................................28
结 论..............................................................32
参考文献............................................................33
致 谢.…....................................................................34
如上图所示,从图中可以看出,该塑件形状并不是很复杂,产品结构较为简单,主要结构特点表现为,外侧有12个防滑筋,内侧有内螺纹M50×3。
该零件尺寸均为一般重要性尺寸,这些尺寸精度为MT7级(GB/T1486—1993)便可,螺纹主,大径,小径要控制好,保证以后好装配。
产品外面要求较高,所以采用细水口进料,去浇口后,浇口痕很小。该零件不属于受力部件,无特殊受力要求。
1.2塑件材料分析
塑料成型原料的选取应该综合考虑多方面因素,首先要了解塑件的用途、使用环境,在满足以上要求后,并考虑使用塑料的成本、成型加工的难易程度等要求。可选择一下材料见表1-1
表1.1注塑塑料对比
塑料名称低密度聚乙烯ABS
材料特性结晶部分多时,塑料硬度高、韧性大、抗拉强度高,但整体尺寸变小,耐冲击强度及断裂强度低。较大的机械强度和良好的综合性能。
成型工艺特点低密度聚乙烯制件最显著的特点是收缩率大,这与材料的可结晶性和模具温度有关。定型后塑件在强的收缩牵引作用下,可令制件变形和翘曲。ABS的吸湿性和对水分子的敏感性较大,在加工前必须进行充分的干燥和预热。原料控制水分在0.3%以下。
注射温度低密度聚乙烯的注射温度一般在160-240℃之间,温度超过300℃时,收缩率会明显增大。ABS塑料的温度与熔融粘度的关系比较独特,在达到塑化温度后再继续盲目升温,必须将ABS的热降解。
注射速度及压力低密度聚乙烯的注射压力一般选择在68.6-137.2Mpa之间。注射速度不易过快,已保证结晶程度高。ABS采用中等注射速度效果较好,注射时需要采用较高的注射压力,其溢边料为0.04mm左右。并需要调配好保压时间。
模具温度由于模具温度对收缩率影响很大,因此要经常保持模具相对恒定的温度,一般在35-65℃之间。ABS的模具温度相对较高,一般调节在75-85℃,为缩短生产周期,应维持模具温度的相对稳定,制件在取出后可采用冷水浴等方法来补偿冷固定型时间。
经以上两种备选材料的性能对比,并考虑到制件的使用环境,本设计之间采用低密度聚乙烯材料。
1.3塑件的成型工艺
低密度聚乙烯(LDPE)是高压下乙烯自由基聚合而获得的热塑性塑料。LDPE是树脂中的聚乙烯家族中最老的成员,二十世纪四十年代早期就作为电线包皮第一次商业生产。LDPE综合了一些良好的性能:透明、化学惰性、密封能力好,易于成型加工。这决定了LDPE是当今高分子工业中最广泛使用的材料之一。
低密度聚乙烯(LDPE)又称高压聚乙烯,为支链分子结构的热塑性塑料。其结晶度为55%-65%,相对分子质量较小,密度为0.91-0.94g/cm3,缩比为1.84-2.3,比热为2.30J/(g.℃)。低密度聚乙烯的化学稳定性较高,能耐大多数酸、碱的腐蚀,但不耐强氧化酸的腐蚀;除苯及汽油外,一般不溶于有机溶剂。低密度聚乙烯耐低温性能好,在-60℃下仍能具有较好的力学性能,但其使用温度不高(在80℃以下)。低密度聚乙烯在热、光及氧的作用下会发生老化变脆,力学性能和电性能下降。在成型时,氧化会引起熔体粘度下降和变色,产生条纹,影响塑件质量。因此需添加抗氧化剂及紫外5、注塑机操作过程注意事项
养成良好的注塑机操作习惯对提高机器寿命和生产安全都大有好处[16]。
开机之前:(1)检查电器控制箱内是否有水、油进入,若电器受潮,切勿开机。应由维修人员将电器零件吹干后再开机。(2)检查供电电压是否符合,一般不应超过±15%。(3)检查急停开关,前后安全门开关是否正常。验证电动机与油泵的转动方向是否一致。(4)检查各冷却管道是否畅通,并对油冷却器和机筒端部的冷却水套通入冷却水。(5)检查各活动部位是否有润滑油(脂),并加足润滑油。(6)打开电热,对机筒各段进行加温。当各段温度达到要求时,再保温一段时间,以使机器温度趋于稳定。保温时间根据不同设备和塑料原料的要求而有所不同。 (7)在料斗内加足足够的塑料。根据注塑不同塑料的要求,有些原料最好先经过干燥。(8)要盖好机筒上的隔热罩,这样可以节省电能,又可以延长电热圈和电流接触器的寿命。
操作过程中:(1)不要为贪图方便,随意取消安全门的作用。(2)注意观察压力油的温度,油温不要超出规定的范围。液压油的理想工作温度应保持在45~50℃之间,一般在35~60℃范围内比较合适。(3)注意调整各行程限位开关,避免机器在动作时产生撞击。
工作结束时:(1)停机前,应将机筒内的塑料清理干净,预防剩料氧化或长期受热分解。(2)应将模具打开,使肘杆机构长时间处于闭锁状态。(3)车间必须备有起吊设备。装拆模具等笨重部件时应十分小心,以确保生产安全。
结 论
1.本模具内螺纹采用了强脱方式脱模,螺纹脱模方很还有用齿轮旋转脱模,用嵌件方式手动脱模。
2.为了加长模个使用寿命,型腔采用P20镶块结构.
通过对本模具的总体结构的精心设计,加深了对模具各部件及模具生产中的条个环节的了解,加强了专业知识的实际运用能力。
此次毕业设计,让我学到了许多知识,包括课本上学不到的知识。当然,在设计过程中也出现一些难题。通过我翻阅相关的书籍,在网上寻找答案和经过指导老师张广杰老师的悉心指教和帮助最终才得以解决。本次设计,也让我学会了齐心协力、共同协作、努力创新,自始至终都抱着一颗坚定的信念,经过了漫长而又短暂的设计工作,我的设计终于出成效了。在设计过程中用到了很多以前上课时学的知识,尤其是老师上课教给我们的一些分析问题、解决问题的思想在这次设计中得到了很好的印证,使我在这鞋方面能够很快的领会。即将毕业的我,在以后的工作中将面临许多的问题和麻烦。我们应该善于采集和利用各种信息资源,扩展知识面和能力;培养严谨、科学、创新与创业、艰苦奋斗、团体协作的精神;增强环境保护意识,做到清洁生产和文明生产,以最大限度的获取企业效益和社会效益。
参考文献
[1]廖月莹.塑料模具设计指导与资料汇编[M].大连:大连理工大学出版社,2007.
[2]曲华昌.塑料成型工艺与模具设计[M].北京:高等教育出版社,2009.
[3]伍先明.塑料模具设计指导[M].北京:国防工业出版社,2006.
[4]邹继强.塑料模具设计参考资料汇编[M].北京:清华大学出版社,2006.
[5]王鹏驹.塑料模具技术手册[M].北京:机械工业出版社,1999.
[6]李德群.塑料成型模具设计[M].武汉:华中理工大学出版社,1990.
[7]许发樾.实用模具设计与制造手册[M].北京:机械工业出版社,2001.
[8]祁红志.模具制造工艺 [M].北京:化学工业出版社,2009.
[9]丁浩.塑料工业实用手册 [M].北京:化学工业出版社,1995.
[10]曼格斯.塑料注射成型模具的设计与制造 [M].北京:中国轻工业出版社,1993.
[11]董国耀.机械制图 M].北京:北京理工大学出版社,1998.
[12]李志刚.模具CAD/CAM [M]. 北京:机械工业出版社,1999.
[13]田野.互换性与测量技术[M].北京:化学工业出版社,2006.
[14]Barber,Antony. Pneumatic handbook. Trade & Technical Press.1999.
[15]Shigley J E.Theory of Machines and Mechanisms.McGraw-Hill Book Company.1980.
[16]IF TOMM International Micro mechanism Symposium. Tokyo Institute of Thechnology.to-kyo.June 1-3,1993.