摘要
本设计为打印机盒盖注塑模的设计。设计中采用一模一腔,浇口采用点胶口,分型面选在截面最大处,塑件成型后利用推杆将成型制品从动模上推出,回程时利用复位杆复位。
设计中需要对塑件的尺寸进行计算,确定尺寸精度,然后进行注射机的初步选取。以及对注塑机的浇注系统、成型零件的结构、成型零件的尺寸、脱模推出机构、排气系统、温度调节系统进行了设计与计算。并且对注射机参数进行校核,包括模具闭合厚度、模具安装尺寸、模具开模行程、注射机的锁模力等。各个参数都满足要求后才能确定注射机的型号。
在设计过程中,为了更清楚的表达模具的内部结构,因此附有动模镶块、定模镶块、定模推板的二维零件图和模具三维爆炸图。
关键词:打印机盒盖;分型面;浇口;工艺分析
Ink jet printer cover injection mold design
Abstract
This design is the design of injection mould for the cabinet. The design uses two mold cavity, type of the sprue is latent gate, the parting surface is chosen in the maximum section of the plastics. After plastics are molded, molding products are driven by putting from dynamic model,then using reset stem returned.
In the design ,The need to calculate the size design, determine the size precision, the preliminary selection and the injection machine. And the injection molding machine of gating system, forming part of the structure, forming part of the size, mold release mechanism, exhaust system, temperature control system design and calculation. And to check the injection machine parameters, including the thickness of mold closing, mold installation size, mold opening stroke, the clamping force injection molding machine etc.. All the parameters meet the requirements to determine the type of injection machine.
In the design process, in order to express more clearly the internal structure of the mold, so a moving die insert, fixed die insert, the fixed mould push plate 2D part drawing and 3D map explosion.
Keywords: Cabinet;Parting;surface;Runner;Process analysis
目 录
1 绪论……………………………………………………………………………1
1.1 题目背景………………………………………………………………………1
1.2 题目国内外相关研究情况……………………………………………………1
1.2.1 国内研究的情况…………………………………………………………1
1.2.2 国外研究情况……………………………………………………………2
1.3中国与国外先进技术的差距…………………………………………………2
1.4塑料模具发展走势……………………………………………………………2
2 产品分析……………………………………………………………………4
2.1 塑件分析……………………………………………………………………4
2.1.1结构分析…………………………………………………………………4
2.1.2尺寸精度分析……………………………………………………………5
2.1.3 塑件厚度检测……………………………………………………………5
2.1.4 表面质量分析……………………………………………………………5
2.2 塑件材料选择………………………………………………………………6
2.2.1 物理性能…………………………………………………………………6
2.2.2 ABS的主要性能指标…………………………………………………6
2.2.3 ABS成型塑件的主要缺陷及消除措施…………………………………6
3 拟定模具结构形式及注射机的初步选择………………………………7
3.1 分型面位置的确定…………………………………………………………7
3.1.1模具的分型面…………………………………………………………7
3.1.2 分型面的确定…………………………………………………………7
3.2 塑件相关计算……………………………………………………………8
3.2.1塑件相关计算…………………………………………………………9
3.3 型腔数量的确定…………………………………………………………10
3.4 初步选择注塑机…………………………………………………………11
4 浇注系统的设计……………………………………………………………13
4.1浇注系统 ……………………………………………………………………13
4.1.1浇注系统的作用………………………………………………………13
4.1.2 浇注系统布置…………………………………………………………13
4.2 浇注系统设计…………………………………………………………13
4.2.1 浇口套的设计…………………………………………………………13
4.2.2 浇注系统的设计………………………………………………………16
4.2.3 分流道与浇口…………………………………………………………17
4.3 浇口设计……………………………………………………………………18
4.3.1 浇口的类型………………………………………………………………18
4.3.2 浇口的位置 ……………………………………………………………18
5 成型零件的工作尺寸计算……………………………………………20
5.1 成型零件工作尺寸的计算………………………………………………20
6 成型零件结构设计…………………………………………………………24
6.1 PRO/E中的模具模块设计………………………………………………24
6.1.1 凹模结构设计……………………………………………………………25
6.1.2 凸模结构设计…………………………………………………………25
7导向机构设计………………………………………………………………27
7.1导向机构………………………………………………………………………27
7.1.1 导柱…………………………………………………………………27
7.1.2 导套………………………………………………………………………28
7.1.3 导柱与导套的配用………………………………………………………29
7.1.4 导柱布置…………………………………………………………………30
7.2 定位装置…………………………………………………………………30
7.2.1 拉杆………………………………………………………………………30
7.3 尼龙开闭器装置……………………………………………………………30
8 脱模推出机构的设计………………………………………………………32
8.1 在设计脱模推出机构是应遵循下列原则…………………………………32
8.2 脱模力的计算……………………………………………………………32
8.3 推出机构设计……………………………………………………………32
8.3.1 推杆布置…………………………………………………………………32
8.3.2推杆结构及固定………………………………………………………33
8.3.3 推杆强度交核……………………………………………………………33
8.4 拉料机构…………………………………………………………………34
9 排气系统设计……………………………………………………………36
10 温度调节系统设计………………………………………………………37
10.1 对温度调节系统的要求…………………………………………………37
10.2 冷却系统设计……………………………………………………………37
10.2.1 冷却回路的布置………………………………………………………37
10.2.1 设计原则………………………………………………………………37
10.2.2 冷却时间的确定…………………………………………………38
10.3 模具冷却系统的计算…………………………………………………39
11 注塑机的校核………………………………………………………………40
11.1 最大注塑量的校核………………………………………………………40
11.2 锁模力的校核 ……………………………………………………………40
11.3 喷嘴尺寸校核……………………………………………………………40
11.4 定位圈尺寸校核……………………………………………………………41
11.5 模具外形尺寸校核………………………………………………………41 11.6 模具厚度校核……………………………………………………………41
11.7 模具安装尺寸校核………………………………………………………41
11.8 开模行程的校核……………………………………………………………41
12 模具工作过程……………………………………………………………43
12.1 模具总体结构………………………………………………………………43
12.2 开合模动作…………………………………………………………………45
13 模具可行性分析…………………………………………………………46
13.1 本模具的特点……………………………………………………………46
13.2 市场效益及经济效益分析…………………………………………………46
结论……………………………………………………………………………… 47致谢…………………………………………………………………………… 48
参考文献……………………………………………………………………… 49
毕业设计(论文)知识产权声明…………………………………………… 50
毕业设计(论文)独创性声明………………………………………… 51
附录………………………………………………………………………………52
1 绪论
1.1 题目背景
近年来,我国塑料模具业发展相当快,目前,塑料模具在整个模具行业中约占30%左右,而在整个塑料模具市场以注塑模具需求量最大。随着模具制造行业的发展,许多企业开始追求提高产品质量及生产效率,缩短设计周期及制造周期,降低生产成本,最大限度地提高模具制造业的应变能力等目标。新兴的模具CAD技术很大程度上实现了企业的愿望。近年来,CAD技术的应用越来越普遍和深入, 大大缩短了模具设计周期, 提高了制模质量和复杂模具的制造能力[][1]。
1.2题目国内外相关研究情况
1.2.1 国内研究的情况
80 年代以来,在国家产业政策和与之配套的一系列国家经济政策的支持和引导下,我国模具工业发展迅速,年均增速均为13%,在未来的模具市场中,塑料管件在模具总量中的比例还将逐步提高。经过半个世纪的发展,模具水平有了较大提高。在塑料管件模具方面已能生产19 万吨,上规模,高水平的企业越来越多,由于他的抗腐蚀、廉价等优秀品质,被应用于我国现代化建设的各个领域。精密塑料模具方面,已能生产医疗塑料件模具、多型腔小模数齿轮模具及塑封模具。所生产的这类塑件的尺寸精度、同轴度、跳动等要求都达到了国外同类产品的水平。还能生产厚度仅为0.08mm的一模两腔的航空杯模具和难度较高的塑料门窗挤出模等等。注塑模型腔制造精度可达0.02mm~0.05mm表面粗糙度Ra0.2μm模具质量、寿命明显提高了。非淬火钢模寿命可达10~30 万次。淬火钢模达50~1000 万次,交货期较以前缩短,但和国外相比仍有较大差距。成型工艺方面,多材质塑料成型模、高效多色注射模、镶件互换结构和
抽芯脱模机构的创新方面也取得较大进展。气体辅助注射成型技术的使用更趋成熟,如青岛海信模具有限公司、采用内热式或外热式热流道装置,少数单位采用具有世界先进水平的高难度针阀式热流道模具。但总体上热流道的采用率达不到10%,与国外的50%~80%相比,差距较大。在制造技术方面,CAD/CAM/CAE 技术的应用水平上了一个新台阶,陆续引进了相当数量的CAD/CAM 系统,如美国EDS 的UGⅡ、美国Parametric Technology 公司的Pro/Emgineer 软件等等[][2]。这些系统和软件的引进,实现了CAD/CAM 的集成,并能支持CAE 技术对成型过程,取得了一定的技术经济效益,促进和推动了我国模具CAD/CAM 技术的发展。
1.2.2 国外研究情况
我国模具生产厂中多数是自产自配的工模具车间、分厂自产自配比例高达60%左右,而国外模具超过70%属商品模具。专业模具厂大多是“大而全”、“小而全”的组织形式,而国外大多是“小而专”、“小而精”。国内大型、精密、复杂、长寿命的模具占总量比例不足30%而国外在50%以上。2004年,我国模具进出口之比为3.7:1,进出口相抵后的净进口额达13.2亿美元,为世界模具净进口量最大的国家。注塑成型是最大量生产塑料制品的一种成型方法。二十多年来,国外的注塑模CAD 技术发展相当迅速。70年代已开始应用计算机对熔融塑料在圆形、管形和长方形型腔内的流动情况进行分析。80 年代初,人们成功采用有限元法分析三维型腔的流动过程,使设计人员可以依据理论分析并结合自身的经验,在模具制造前对设计方案进行评价和修改,以减少试模时间,提高模具质量。近十多年来。
注塑模CAD 技术在不断进行理论和试验研究的同时,十分注意向实用化阶段发展,一些商品软件逐步推出,并在推广和实际应用中不断改进[][3]。
1.3中国与国外先进技术的差距
面对国外先进技术与高质量制品的挑战,中国塑模企业不仅要加快产业集群化,发挥规模效应,还要注重模具产业链的前端研发、人才建设和产业链后端的检测以及信息服务,尽快缩短技术、管理、工装水平与国际水准的差距。这是塑料模具企业在发展中必须解决的重要问题。并且也要注意当前整个工业生产的发展特点(产品品种多、更新快、市场竞争激烈)[][4]。为了适应用户对模具制造的短交货期、高精度、低成本的迫切要求,我们必须学习国外先进技术,改善我们操作和管理方面的各种问题。

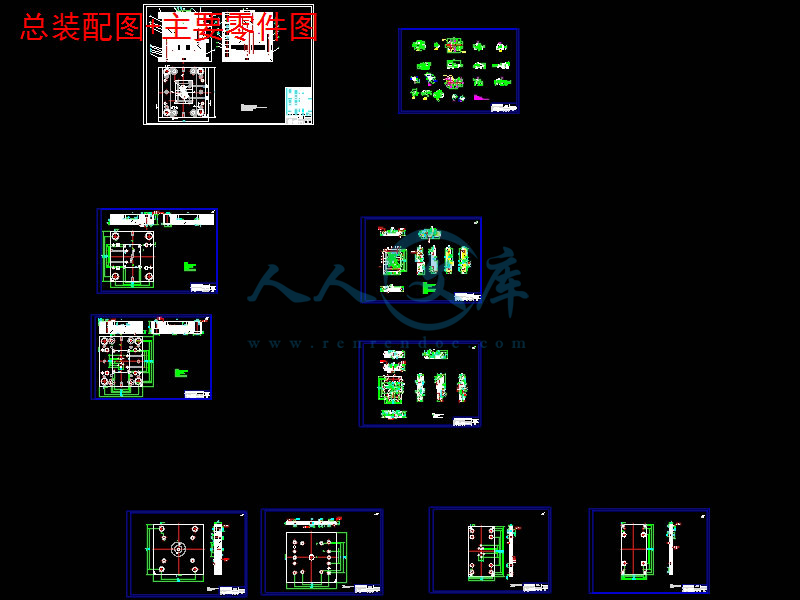
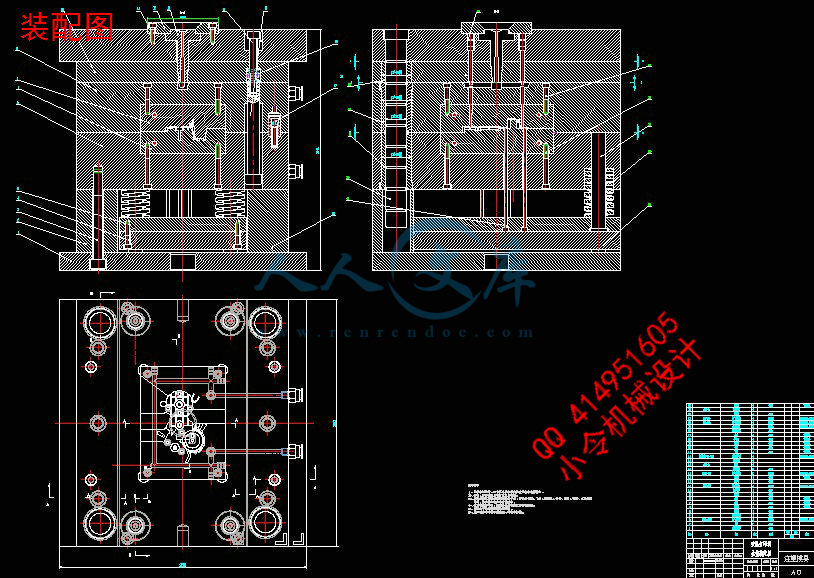

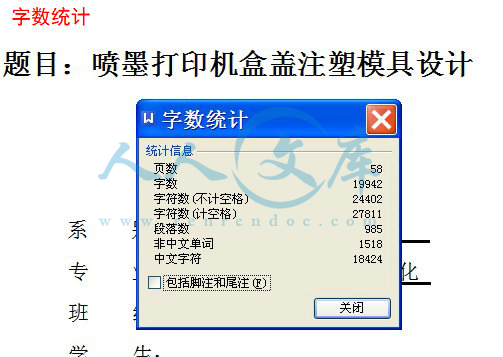