
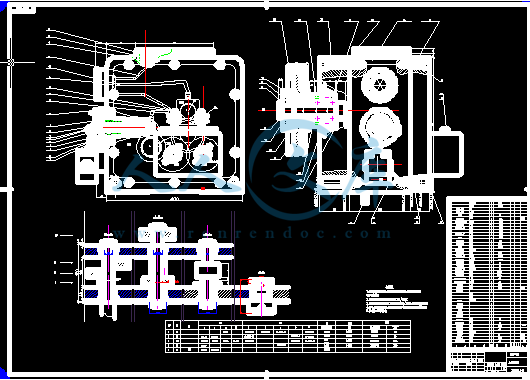


毕 业 设 计 说 明 书
ZH1105柴油机连杆
攻丝专机总体及主轴箱设计
专业 机械设计制造及其自动化
学生姓名
班级
学号
指导教师
完成日期
目录
1 引言..................................................................................................................................... 1
1.1 概述.................................................................................................................................. 1
1.2 课题设计的总体思路...................................................................................................... 1
2 组合机床总体设计............................................................................................................. 3
2.1 总体方案论证.................................................................................................................. 3
2.1.1 被加工零件的特点....................................................................................................... 3
2.1.2 工艺路线的确立........................................................................................................... 3
2.1.3 机床配置型式的选择................................................................................................... 4
2.1.4 定位基准的选择........................................................................................................... 5
2.1.5 选用滑台传动型式....................................................................................................... 5
2.2 总体设计计算.................................................................................................................. 5
2.2.1 丝锥的切削负荷........................................................................................................... 5
2.2.2 攻丝扭矩的计算........................................................................................................... 5
2.2.3 主轴直径的确定........................................................................................................... 6
2.2.4 切削速度的确定........................................................................................................... 6
2.2.5 切削功率的确定........................................................................................................... 6
2.2.6 攻螺纹主转速的计算................................................................................................. 6
2.2.7 确定主轴箱轮廓尺寸................................................................................................. 7
2.2.8 生产率计算................................................................................................................... 7
2.2.9 通用部件的选择........................................................................................................... 9
2.2.10零部件的设计............................................................................................................ 10
3 组合机床主轴箱设计....................................................................................................... 11
3.1 主轴箱原始依据图的绘制............................................................................................ 11
3.2主轴结构型式的选择和动力计算................................................................................. 12
3.3 主轴箱传动系统的设计与计算.................................................................................... 12
3.3.2 主轴箱传动路线的拟订............................................................................................. 13
3.3.3 传动轴位置及齿轮齿数的确定................................................................................. 13
3.3.4轴的校核...................................................................................................................... 15
3.3.5 齿轮的校核................................................................................................................. 16
3.3.6 轴承的寿命校核......................................................................................................... 18
3.3.7 键的强度计算............................................................................................................. 18
3.4 主轴箱前、后盖及箱体设计........................................................................................ 19
3.5 附件的选择.................................................................................................................... 19
4 结论................................................................................................................................... 21
附件清单............................................................................................................................... 24
1 引言
1.1 概述
组合机床是由万能机床和专用机床发展来的,它既有专用机床、结构简单的特点,又有万能机床能够重新调整,以适应新工件加工。组合机床是用按系列化标准化设计的通用部件和按被加工零件的形状及加工工艺要求设计的专用部件组成的专用机床。组合机床是集机电于一体的综合自动化程度较高的制造技术和成套工艺装备。它的基本组成是以大量通用部件为基础,配以少量专用部件组成的一种高效专用机床。它的特征是高效、高质、经济实用,因而被广泛应用于工程机械、交通、能源、军工、轻工、家电等行业。组成组合机床的通用部件有如下几类:动力部件——动力头、动力滑台和动力箱;工件运送部件——回转工作台、移动工作台和回转鼓轮;支承部件——立柱,床身,底座和滑座等。控制系统有通用的液压传动装置、电气柜、操纵台等。
本组合机床是一台加工柴油机连杆攻丝组合机床,该机床可适用于一定批量的生产。课题来源于江淮动力股份有限公司,是针对目前该公司对ZH1105柴油机机体三面攻螺纹而设计的,以提高其的生产效率、加工精度,从而降低加工成本。
国内主要组合机床厂对主机的质量普遍比较重视,但由于与主机配套的液压件,稳定性受到了严重的影响。许多厂存在着刀具和辅助设计制造能力差的问题。目前, 国内组合机床通用部件由于多家引进了不同国别的技术, 标准还没有统一, 行业归口部门要进一步做工作, 尽快统一起来,这无论对生产通用部件的企业, 还是对用户的选型、维修都有积极的意义。然后着手重点扶持一批有一定基础的中、小企业定点专业化生产, 以稳定质量, 降低成本。瞄准国际同类产品水准, 在行业中创出中国名牌供应国内外市场。
组合机床的设计,目前基本上有两种情况:其一,是根据具体加工对象的具体情况进行专门设计,这是当前最普遍的做法。其二,随着组合机床在我国机械行业的广泛使用,广大工人总结自己生产和使用组合机床的经验,发现组合机床不仅在其组成部件方面有共性,可设计成通用部件,而且一些行业在完成一定工艺范围内组合机床是极其相似的,有可能设计为通用机床,这种机床称为“专能组合机床”。这种组合机床就不需要每次按具体加工对象进行专门设计和生产,而是可以设计成通用品种,组织成批生产,然后按被加工的零件的具体需要,配以简单的夹具及刀具,即可组成加工一定对象的高效率设备。组合机床行业的产品技术现状与激烈竞争的市场以及与用户需求之间的差距是比较大的, 在市场经济的新形势下, 切实解决存在的薄弱环节, 完善售后服务体系, 以求得行业企业的大发展, 前景是美的。
1.2 课题设计的总体思路
课题来源:盐城市江动集团;
课题研究的内容:设计一台加工柴油机连杆攻丝组合机床,具体进行总体、夹具部装图、零件图设计;
加工内容有:连杆材料为40Cr ,调质处理硬度为HBS255-293,本道工序主要加工连杆大端的2×M12×1.25-5H↓18;
生产纲领:年产20万只;
批量:本机床设计、制造一台。
设计要求:
A.总体设计
a.制定工艺方案,确定机床配置型式及结构方案。
b.三图一卡设计,包括:a)被加工零件工序图,b)加工示意图,c)机床联系尺寸图,d)生产率计算卡,e)有关设计计算、校核。
B.主轴箱部装图设计
a 主轴箱部装图设计;b零件图设计;有关计算、校核等。
C.撰写毕业设计说明书。
设计思路:
根据工艺方案确定机床的型式和总体布局。在选择机床配置型式时,既要考虑实现工艺方案,保证加工精度,技术要求及生产效率;又要考虑机床操作、维护、修理是否良好;还要注意被加工零件的生产批量,以便使设计的组合机床符合多快好省的要求。其制定过程应从以下的几个方面考虑:1、加工的工序和加工精度的要求。2、被加工零件的特点3工件的生产方式, 在加工连杆过程中,还必须考虑到加工零件特点对配置型式和结构方案的影响。在加工精度要求影响方面,不仅提高原始精度,提高工件的定位基准和减少夹压变形等措施。设计的主要思路是把原有的多道工序的单孔加工改为多孔同时加工,这样设计主要是为了解决由多次装夹引起的定位误差问题,保证孔的位置精度
2 组合机床总体设计
组合机床的总体设计要注重工件及其加工的工艺分析,制订出合理的工艺方案,才能设计出合理的专用机床。根据指定的加工要求,提出若干个工艺方案,选择最优的。工艺方案的确定决定了专用机床的结构、性能、运动、传动、布局等一系列问题。所以,工艺方案设计是专用机床的重要环节。
2.1 总体方案论证
2.1.1被加工零件的特点
该组合机床的加工对象是连杆,材料是40Cr,硬度为HBS255-293.本道工序主要加工连杆大端的2×M12×1.25-5H深18。
2.1.2工艺路线的确立
被加工零件需要在组合机床上完成的加工工序,以及应保证的加工精度是制定机床方案的主要依据。如图2-1:被加工对象为ZH1105型柴油机连杆,材料为40Cr。
本次加工的零件是柴油机机体,其主要加工工序是:
A.粗铣底面;
B.粗铣左、右端面;
C.粗铣前、后端面;
D.半精铣底面;
E.半精铣左、右端面;
F.半精铣前、后端面;
G.粗镗孔;
H.精镗孔;
I.钻左、右、后面的孔;
J.攻螺纹。
本道工序为第10道工序,主要攻连杆大端上的2个螺纹孔。具体加工内容是:螺纹孔2×M12×1.25-5H深18,一次装夹一个零件,2个螺纹孔同时加工。
2.1.3机床配置型式的选择
根据选定的工艺方案,确定机床的配置型式时,既要考虑能实现工艺方案,以确保零件的加工精度、技术要求及生产率,又要考虑机床的操作方便可靠,易于维修,且冷却、排屑情况良好。
机床的配置型式有立式和卧式两种,如图2-2和图2-3两种
图2-3 立式组合机床结构
立式机床的优点是占地面积小,自由度大,操作方便,其缺点是机床重心高,振动大。卧式机床的优点是加工和装配工艺性好,振动小,运动平稳,机床重心较低,精度高,安装方便,其缺点是削弱了床身的刚性,占地面积大。机床的配置型式在很大程度上取决于被加工零件的大小、形状及加工部位等因素。
卧式机床多用于加工孔中心线与定位基准面平行的情况,而立式机床则适用于加工定位基面是水平的,而加工的孔与基面相垂直的工件。考虑到汽车变速箱箱体的结构为卧式长方体,从装夹的角度来看,卧式平放比较方便,也减轻了工人的劳动强度。
通过以上的比较,考虑到卧式机床振动小,装夹方便等因素,选用卧式组合机床。
2.1.4定位基准的选择
组合机床是针对某种零件或零件某道工序设计的。正确选择定位基准,是确保加工精度的重要条件,同时也有利于实现最大限度的集中工序。本机床加工时采用的定位方式是一面两孔定位,以底面为定位基准面,限制三个自由度;用圆柱定位销,限制两个自由度;用削边销限制剩下的一个转动自由度,符合六点定位规律,满足相容条件。夹紧方式采用右面用气缸夹紧。
2.1.5选用滑台传动型式
动力滑台是由滑座、滑鞍和驱动装置等组成、实现直线进给运动的动力部件。根据驱动和控制方式不同,滑台分为液压滑台、机械滑台和数控滑台三种类型。
液压滑台采用双轨结构型式,以单导轨两侧面导向,导向的长宽比较大,导向性好;在相当大的范围内可以无级调速;可以获得较大的进给力;由于液压驱动,零件磨损小,使用寿命长;工艺上要求多次进给时,通过液压换向阀,很容易实现;过载保护简单可靠;由行程调速阀来控制的快进转工进,转换精度高,工作可靠。机械滑台采用滚珠丝杠传动,进给量稳定,慢速无爬行,高速无振动,可以降低加工工件的表面粗糙度;具有较好的抗冲击能力,断续铣削、钻头钻通孔将要出口时,不会因冲击而损坏刀具;运行安全可靠,易发现故障,调整维修方便。故选择液压滑台。
2.2总体设计计算
2.2.1丝锥的切削负荷
丝锥的切削负荷与丝锥每一刀齿切下切削厚度以及同时工作刀齿数有关。丝锥的每齿负荷不取决于机床进给机构,而是由本身结构参数所决定。
2.2.2攻丝扭矩的计算
丝锥工作时其主要抗力为扭矩,攻丝扭矩由切削扭矩、丝锥与已加工表面之间的摩擦扭矩和切削阻塞在容削槽中产生的扭矩。在正常切削条件下,主要的是切削扭矩。
根据文献[6]第134页表6-20可