摘 要
曲轴是最重要的锻件之一。曲轴锻造技术是微车曲轴锻造成形工艺的重要发展趋势。对于精密锻造的微车曲轴,非调制钢将逐渐替代其它原材料。曲轴锻后只进行可控冷却,而不需要进行热处理,避免了热处理变形,节约了能源消耗。精锻后的曲轴只需少量加工就可直接使用,提高了生产效率及材料利用率,降低了生产成本,因此大大提高了曲轴的市场竞争能力。
从80年代发展至今,许多发达国家在曲轴生产过程中,广泛运用CAD/CAM,CAE技术,采用生产管理信息系统和集成制造系统,实现了锻造生产对原材料、工艺和工艺装备最佳方案的选择和整个过程的控制,其锻造生产的合理化、自动化程度很高。
微型车曲轴成形工艺及模具的设计这一课题研究的主要内容有:曲轴的国内外现状,曲轴毛坯成形方法及特点的比较,曲轴结构的设计,曲轴锻造工艺及工艺方案的确定,曲轴模具的设计。
因此,通过课题的研究过程掌握汽车发动机曲轴模具的设计过程,了解锻造的基本工艺,熟练应用PROE、CAD等绘图软件,并具有一定的实验技能和生产实践知识。
关键词:曲轴;成形;工艺;模具设计;模锻
ABSTRACT
The crankshaft is the most important one of the forgings. The crankshaft forging technology is microcar crankshaft forging an important development trend forming process. For precision forging microcar crankshaft, the modulation of the steel will gradually replace other raw materials. The crankshaft forging only controlled cooling after heat treatment. without the need to avoid the heat treatment deformation, save the energy consumption. After precise forging the crankshaft small quantities processing can be used directly. improve the production efficiency and material utilization and reduced production cost, thus greatly improve the market competition ability of the crankshaft.
From the 1980s development so far. many developed countries in the crankshaft production process. the widely used CAD/CAM. CAE technology. using production management information system and integrated manufacturing system. realize the forging production material. process and process equipment best options and the entire process control. the forging production rationalization, high degree of automation.
Microcar forming technology and crankshaft mold design and the subject of research contents include: of the crankshaft situation at home and abroad. crankshaft blank forming methods and characteristics of comparison. crankshaft structure design. crankshaft forging process and technology strategy decision. crankshaft die design.
Therefore. through the topic research process master automobile engine crankshaft mould design process, understand the basic process. skilled forging PROE. such as CAD application of the drawing software. and has certain experiment skill and production practice knowledge.
Key words: The Crankshaft; Forming; Craft; Mold Design; Mould Forging
目 录
摘要 ………………………………………………………………………………………Ⅰ
Abstract ………………………………………………………………………………Ⅱ
第1章 绪论……………………………………………………………………………1
1.1曲轴成形国内外研究现状………………………………………………………1
1.1.1国内研究现状…………………………………………………………1
1.1.2国外研究现状…………………………………………………………2
1.2曲轴毛坯成形方法及特点比较………………………………………………3
1.2.1铸造成形………………………………………………………………3
1.2.2 锻压成形………………………………………………………………5
1.3 选题意义………………………………………………………………………7
第2章 曲轴结构的设计………………………………………………………8
2.1 曲轴的工作条件和设计要求…………………………………………………8
2.2 曲轴结构设计的主要内容………………………………………………………9
2.2.1 曲轴的材料及结构型式的选择………………………………………9
2.2.2 曲轴主要尺寸的确定…………………………………………………9
2.3 本章小结………………………………………………………………………14
第3章 曲轴锻造工艺及工艺方案的确定………………………………………15
3.1 曲轴锻造工艺概述………………………………………………………………15
3.1.1曲轴的自由锻工艺……………………………………………………16
3.1.2曲轴的模锻工艺………………………………………………………16
3.1.3曲轴的全纤维锻造工艺………………………………………………17
3.2曲轴精密模锻成形工艺……………………………………………………18
3.2.1精密模锻主要应用……………………………………………………18
3.2.2锻件材料特性…………………………………………………………19
3.2.3 曲轴精锻工艺分析……………………………………………………19
3.3热锻件图尺寸的确定………………………………………………………21
3.4预锻件的设计……………………………………………………………………24
3.5设备吨位的选择………………………………………………………………26
3.6毛坯尺寸的确定…………………………………………………………………27
3.7本章小结………………………………………………………………………27
第4 章 曲轴锻模设计………………………………………………………………28
4.1模具结构设计…………………………………………………………………28
4.2锻模材料和热处理规范概述……………………………………………………32
4.3曲轴模具加工工艺………………………………………………………………33
4.4本章小结…………………………………………………………………………33
结论………………………………………………………………………………………34
参考文献 ………………………………………………………………………………35
致谢………………………………………………………………………………………37
附录………………………………………………………………………………………38
第1章 绪 论
1.1曲轴成形国内外研究现状
汽车曲轴是汽车发动机的主要运动部件,工作情况极其复杂,他的性能优劣直接影响着发动机的可靠性和寿命。曲轴作为内燃机中承受冲击载荷传递动力的关键零件,是内燃机5大件(机体、缸盖、曲轴、连杆、凸轮轴)中最难以保证加工质量的零部件。曲轴恶劣的工况条件,对其材质、毛坯加工技术、精度、表面粗糙度、热处理和表面强化、动平衡等要求都十分严格。其中任何一个环节的质量对曲轴的寿命和整机的可靠性都有很大的影响。因此世界各国十分重视技术研究,不断改进曲轴加工工艺,最大可能地提高曲轴寿命。由于曲轴的锻造工艺复杂,如何降低载荷、提高模具的使用寿命都是制定曲轴成形工艺所必须重点考虑的,因此,优化曲轴模具结构、消除成形缺陷、提高材料利用率、改善曲轴精密模锻工艺不但可以提高生产效率,也可以为同类曲轴相关模具设计提供理论和实践依据。
1.1.1国内研究现状
近年来,我国汽车生产企业以及曲轴专业生产厂家通过对引进技术的消化吸收和自行开发,总体水平有了较大的提高。例如东风汽车公司载重汽车曲轴是在一条由德国奥姆科公司生产的自动线上,运用纤维墩锻法实现锻造的。锻件重量150 kg。自动线由6台主机和相配套的机械手组成。毛坯经中频感应加热后送入930 mm的辊锻机,经辊锻备坯后由机械手送入1.2万t楔式热模锻压力机模锻,模锻成型、切边后送入800t机械式切边压力机切边, 180t液压曲轴扭转机扭出曲拐转角,最后将曲轴送入1600t液压校正机对锻件进行精压。整条线的工作完全自动化,单件生产节拍40S。中国第一汽车集团公司于1991年装备了一条大体上相同的锻造自动线,用于锻造载重汽车曲轴。这条自动线是由德阳第二重型机器厂按照德国的生产许可证生产的。
在引进技术、走跨越式发展道路的同时,我们也看到,国内曲轴制造技术的发展受到诸多方面的限制,距世界先进水平仍相差很远,甚至于还满足不了我国汽车制造业发展速度的需要。我国曲轴专业生产厂家不是很多。且整体规模小、专业化程度低、企业设备陈旧、产品设计和工艺落后、性能寿命和可靠性差、品种杂乱和“三化”程度低,这些都影响了汽车整车的技术需要和运行稳定性要求。目前,国内虽已有一批先进的锻造设备,但由于数量少,加之模具制造技术和其他一些设施跟不上,使一部分先进设备来充分发挥应有的作用。从总体上讲,改造和更新陈旧的普通锻造设各、改进落后的曲轴制造工艺、推广应用曲轴设计先进技术,在我国锻造业尤其是汽车制造领域,显得尤为急迫。
从大环境看,我国锻造业具有悠久的历史,对我国国民经济和社会主义现代化建设做出了巨大贡献,但是,整个锻造行业的发展与我国乃至世界信息化进程的速度相比,还很不适应。就锻造技术而言,还有不少落后的工艺、能耗高、科学化及现代化水平低,与国外先进水平相比尚有较大差距;就锻造设备而言,既有微机控制的自动锻造生产线,也有使用了近百年的夹杆锤。因此,我国的锻件总量可谓世界前列,但锻造业的发展并非世界强国,主要表现有:自动化水平低,设备重复建设,利用率偏低,特别是大型锻造设备,布局不合理:人均劳动生产率低:大锻件、模锻件的产量大,但锻件精度低,能耗高,材料利用率低;研究方法比较落后,新工艺推广慢,信息化与科技武装尚处于起步阶段。
二十世纪九十年代中后期,锻造技术在中国大陆得到了快速发展,研究前沿主要在以下方面:(1)突出发展精密净形成型,发展少无切削技术。国内部分企业热精锻的齿轮精度己达rr7.9级,冷精锻的尺寸精度可达0.02-0.05ram。(2)塑性加工的智能化。在国内塑性加工业界,现代信息技术受到普遍重视,CAD/CAM/CAE技术的应用日益广泛,计算机模拟成为国内塑性加工中一个最为活跃的领域。部分科研单位采用这一技术来进行塑性加工工艺过程的模拟,达到预知金属的流动、应变、应力、温度分布、模具受力、可能的缺陷及失效形式的目的。有科研人员开发的应用软件或者对已有软件进行的二次开发,甚至可以预知产品的显微结构、性能以及残余应力,这对于优化工艺参数和模具结构、缩短产品研制周期、降低研制成本具有重要意义。(3)复合技术。如铸锻复合工艺、冲锻复合工艺、冷热复合锻造工艺以及轧锻复合工艺等,这些工艺的发展带动国内锻造行业不断探索新的工艺和新的设备与技术。(4)液压成型技术。近年来由于国内汽车工业的发展,在液压成型汽车零部件方面有了新的进展。液压成型技术的应用,简化了模具结构,缩短了产品的生产周期,同时还可以制造出其它方法所不能制造的复杂工件。(5)激光成型技术。激光在制造业得到越来越广泛的重视,国内锻造行业正在积极探索以激光成型技术为基础的快速原型制造。(6)新材料精密成型工艺。为了减轻机械设各和汽车的重量,轻合金(铝、镁合金等)新材料的应用越来越多,这些新材料的精密成型技术是中国急需发展的重要技术方向,目前国内已着手研究具有自主知识产权的串行工艺和装备,以期进入世界竞争的行列。
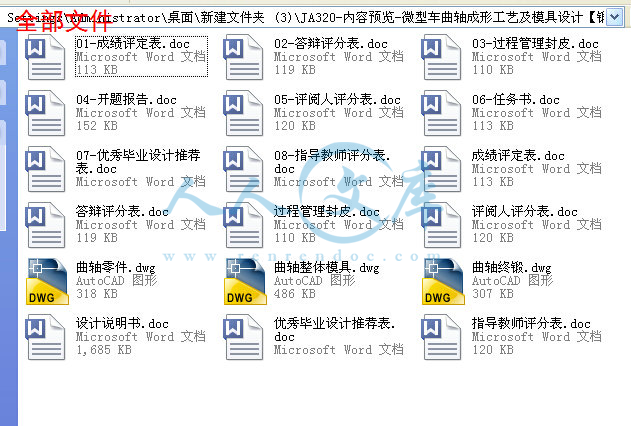



