目 录
摘 要··································································Ⅲ
ABSTRACT····························································Ⅳ
1 前 言
1.1 选题背景·····························································1
1.2课题设计思路·························································1
1.3设计过程中的难点·····················································2
2 工艺分析及计算
2.1工件的基本信息分析···················································3
2.2工艺分析·····························································3
2.2.1工序计算 ·························································4
2.2.2计算毛坯直径······················································5
2.2.3工艺方案的确定·····················································7
2.2.4排样及搭边·························································8
2.3工艺计算·····························································9
2.3.1工艺力的计算及压力机的选择········································9
2.3.2主要工作部分尺寸计算··············································12
3模具设计
3.1落料拉深复合模的设计················································15
3.1.1落料拉深复合模结构设计············································15
3.1.2落料拉深复合模主要零件设计········································16
3.2冲孔模设计··························································19
3.2.1冲孔模结构设计····················································19
3.2.2冲孔模主要零件设计················································20
3.3翻边模设计··························································22
3.3.1翻边模结构设计····················································22
3.3.2翻边模主要零件设计················································22
3.4切边整形复合模的设计················································24
3.4.1切边整形复合模结构设计············································24
3.4.2切边整形复合模主要零件设计········································25
3.5扩口压平复合模的设计················································27
3.5.1扩口压平复合模结构设计············································27
3.5.2扩口压平复合模主要零件设计········································27
4 结 论································································31
谢 辞··································································32
参考文献·······························································33
摘 要
本文是对拉深件进行工艺分析及模具设计。该工件是一个圆筒形拉深件,另外该工件的底部带有通孔,需进行冲孔翻边,虽然形状不太复杂但肯定不能一次成形。通过对零件各部分进行计算分析后才能最终确定加工工序。工件整个成形过程所涉及的工序有:落料、拉深、冲孔、翻边等四步。通过计算分析得翻边能一次成形,所以不需进行预拉深,而计算可知拉深可一次成形,所以确定最终工艺方案为:落料与拉深复合,冲孔、翻边复合。在确定工艺方案的基础上对主要模具进行设计,分析工件成型过程,设计模具的结构并画出模具装配图及零件图。在本次设计中主要对落料拉深复合模以及冲孔、翻边模进行设计。
关键词:拉深;落料拉深复合模;
ABSTRACT
The thesis is focus on the process analysis and mold design of the drawing.The workpiece we design is a cylinder-shaped drawing parts,which has a hole at the bottom.The workpiece should be punched and flanged.Although the shape is not very complex,it couldn’t be shaped by one step.We can determine the processing by analyzing the parts of the workpiece.The process include several steps:blanking,drawing,punching and flanging.By analysis,we know that the flanging can be finished by one step.There should not be a pre-drawing.However,the drawing can be achieved easily.Therefore,the final process is compounding the blanking with the drawing, the punching die and flanging die.Besides,we should design the main die,analyse the process,design the structure of the die and draw the assembly and workpiece picutures.In this graduation project,we mainly design the blanking drawing die, the punching die and flanging die.
Key words: drawing die; blanking drawing compound die;
1前 言
1.1选题背景
带轮是带传动机构中重要的零件之一。它是一种用途十分广泛、年需求量很大的机械传动零件。
随着机械工业特别是汽车制造业的发展,节约原材料,降低能耗,提高整机的质量是普遍关注的大问题。因此,对作为机械传动零件的带轮如何优化设计,改革加工方法,对促进机械工业的发展具有特别重要的意义。对于发达的现代工业来说,笨重的铸铁带轮已较难适应现代工业化发展的需求。为此人们一直寻求一种新的替代品,进而突破传统工艺。
采用钢板冲压制作的皮带轮在这种时代背景下应运而生,采用钢板制作的皮带轮是一种轻型结构的带轮(通称钣制带轮)。冲压皮带轮作为皮带轮的一种新型的结构型式,以其精度高、重量轻、节能、节材、动平衡好、生产效率高,无环境污染等特点,己被汽车工业广泛应用,铸铁等型式的传统皮带轮将会逐渐减少使用,产生了良好的社会效益和经济效益。
同其他制造带轮的工艺方法相比,冲压带轮的有着巨大的优势:
(1)在具有足够刚度的条件下,冲压皮带轮重量轻,比铸铁带轮轻3/4以上。
(2)材料密度和壁厚均匀。因其是整体结构,成形工艺合理,尺寸精度高(即槽面径向跳动量一般在0.1一0. 2 ),动平衡性好,惯量小。
(3)同胀压法相比,所用工具和模具的费用低(为胀压模具费的1/5),而且强度高,寿命长,同时这种冲压成形的皮带轮具有可通用性,在工序周转和运输过程中的损坏率低。
(4)节能、节料、低成本。冲工艺能耗低,优于铸铁带轮的铸造与退火等能耗工序,节约能源材料在50%以上,效率高,每分钟可加工数件。
(5)无环境污染。工人劳动条件好,劳动强度低。
1.2课题设计思路
本设计为一多工序生产的筒形翻边件,该零件为一阶梯圆筒形拉深件,其形状虽然简单但成形工序较多,且产品批量较大,不宜采用单一工序生产,而用级进模结构太复杂,所以尽量采用复合模。
设计模具前首先通过计算确定方案的可行性,对工件进行工艺分析,计算毛坯寸,进而确定工艺方案,进行模具设计。
通过分析此工件,可以发现虽然其结构简单,但是所需的工序较多,有落料、拉深、冲孔、翻边、扩口、压平六个工序,因此如何确定工序顺序及各工序的复合成为此课题的关键。
1.3设计过程中的难点
本设计为一多工序生产的零件,筒形拉深成形时, 采用一次或多次成形工艺方法,同时要考虑到翻边能否一次完成,保证零件能够通过制定的工序生产出来。在该工艺过程中, 考虑材料在各个变形方向的成形极限, 从而预留足够的坯料。考虑工艺可行性与零件性能,选择较合理的工艺顺序是本次设计的一个难点,分析各个工序对材料性能以及零件精度的影响。再就是在扩口翻边工序进行时对模具的设计要求较高,需要用到斜楔滑块机构,必须保证模具设计的可行性,这是另一个难点。






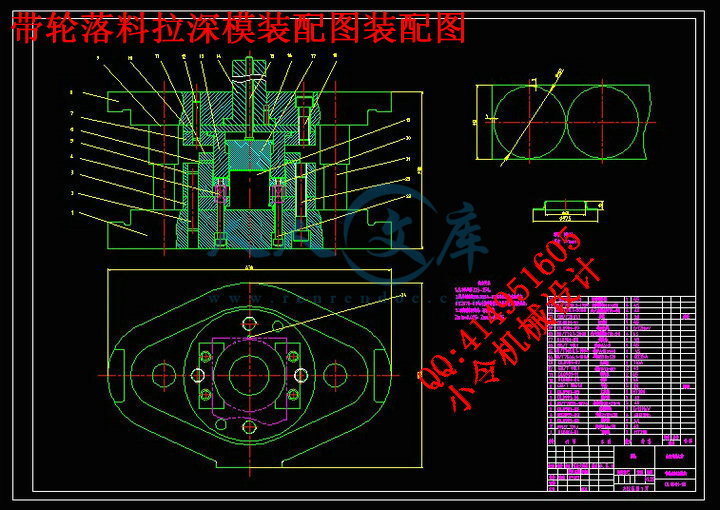