摘 要
模具作为一种成型工具,其设计、制造水平的高低,直接关系到产品的质量与更新换代,是衡量一个国家产品制造水平的重要标志。
本文主要介绍的是晾衣叉注塑模具的设计方法。首先分析了晾衣叉制件的工艺特点,包括材料性能、成型特性与条件、结构工艺性等,并选择了成型设备。接着系统介绍了晾衣叉注塑模的分型面的选择、型腔数目的确定及布置,重点介绍了浇注系统、成型零件、侧向抽芯机构、合模导向机构、脱模机构、定距分型机构以及冷却系统的设计。然后选择标准模架和模具材料,并对注射机的工艺参数进行相关校核。最后对模具的工作原理进行阐述,以及在安装调试过程中可能出现的问题进行总结、分析,并给出了相应的解决方法。本文论述的晾衣叉注塑模具采用两板式结构,采用一模二腔的型腔布置,最后利用推杆将制件推出。
关键词:晾衣叉;注塑模;二板模;浇注系统
Abstract
Die as a tool for molding, its design, manufacture level are of direct bearing on the quality of products and replacement, an important indicator to measure a country's level of manufacturing.
The designing methods of injection mould of clothes fork are mainly introduced in this paper. First, the technological characteristics are analyzed, including material properties, forming characteristics and conditions, the process of the structure, the forming equipment is selected. Then the parting line is selected, the number of cavities is determined. The specific introduction are made on gating system, cooling system, Molding parts, Steering mechanism, moulding mechanism, and spacer parting institutions. Then the standard mould bases and mould materials are selected, and the technological parameters of the forming equipment is checked. Finally, problems that may emerge during the mold installation process are analyzed and the appropriate solutions are provided.Two pence mould is used on the design of charger shell. there are two cavities in this mould, finally a stripper plate is used to push off the clothes fork.
Keyword: Clothes fork; Injection mould; Two pence mould; Gating system;
目 录
引言1
1 塑件结构及尺寸3
1.1 本塑件的材料分析3
1.2 本塑件的工艺参数4
1.3 本塑件的产品结构4
1.4 塑件的公差5
1.5 塑件的壁厚5
1.6 塑件的脱模斜度6
2 模具结构的设计7
2.1 确定型腔数目的方法7
2.2 型腔排列方式的确定8
3 注射机型号的确定8
3.1 注塑机定义8
3.2 注塑机的类型9
3.3 注塑机的结构9
3.4 注塑机的选择10
3.4.1所需注射量的计算、塑件质量、体积计算10
3.4.2浇注系统凝料体积的初步估算11
3.5 注塑机的校核11
3.5.注射压力校核11
3.5.2锁模力校核12
3.5.3开模行程和模板安装尺寸校核12
4 成型零件的设计13
4.1 分型面的设计13
4.2 成型零部件的结构设计14
4.2.1型芯和型腔的结构设计14
4.2.2注射模强度要求15
4.3 型芯型腔的确定16
5 侧向分型与抽芯机构16
5.1 侧向抽芯机构的分类及组成16
5.2 确定抽芯距18
5.3 抽芯力的计算18
5.4 斜导柱设计20
6 浇注系统的设计21
6.1 浇注系统的组成21
6.2 浇注系统的作用21
6.3 浇注系统设计影响因素21
6.4 主流道的设计22
6.4.1主流道的材料23
6.4.2主流道的表面精度23
6.5 分流道设计23
6.6 浇口设计25
6.6.1浇口的选用26
6.6.2浇口位置的选用26
6.6.3浇注系统的平衡28
6.6.4排气的设计28
7 标准模架的选取28
8 合模导向机构的设计30
8.1 导柱导向机构设计要点30
9 脱模机构的设计32
9.1 脱模机构设计的总原则32
9.2 推杆设计32
9.2.1推杆的形状32
9.2.2推杆的位置和布局33
9.3 推件板设计的要点33
10 冷却系统的设计34
10.1 冷却系统的计算34
10.2 冷却系统的设计准则34
11 典型零件的制造工艺35
11.1 浇口套加工35
11.2 定模座板加工36
11.3 动模模套加工37
11.4 导柱的加工38
12 结语39
谢 辞40
参考文献41
引言
作为工业生产基础工艺装备的模具,在国民经济中占有重要的地位,模具技术也已成为衡量一个国家产品制造水平的重要标志之一。
第十一五规划中指出,模具是工业生产的基础工艺装备,国民经济的五大支柱产业——机械、电子、汽车、石化、建筑都要求模具工业发展与之相适应。模具因其生产效率高、产品质量好、材料消耗低、生产成本低而获得广泛应用,与其他加工制造业所无法比拟的。从工业产品生产行业看,模具是现代工业,特别是汽车、摩托车、航空、仪表、仪器、医疗器械、电子通讯、兵器、家用电器、五金工具、日用品等工业必不可少的工艺装备。据资料统计,利用模具制造的零件数量,在飞机、汽车、摩托车、拖拉机、电机、电器、仪器仪表等机电产品中占80%以上;在电脑、电视机、摄像机、照相机、录像机、传真机、电话及手机等电子产品中占85%以上;在电冰箱、洗衣机、空调、微波炉、吸尘器、电风扇、自行车、手表等轻工业产品中占90%以上;在子弹、枪支等兵器产品中占95%以上。
我国模具工业在政府十分重视及关怀下,并提出相应的优惠政策进行模具技术开发,在模具工业中大量采用先进技术和设备,努力提高模具设计和制造水平,取得显著的经济效益。另外,从资料获悉,目前,美国、日本、德国等发达国家的模具总产值都已超过机床总产值。模具技术的进步极大地促进了工业产品的生产发展,模具是“效益放大器”,用模具生产最终产品的价值将超过自身价格的几十倍乃至百倍及上千倍。

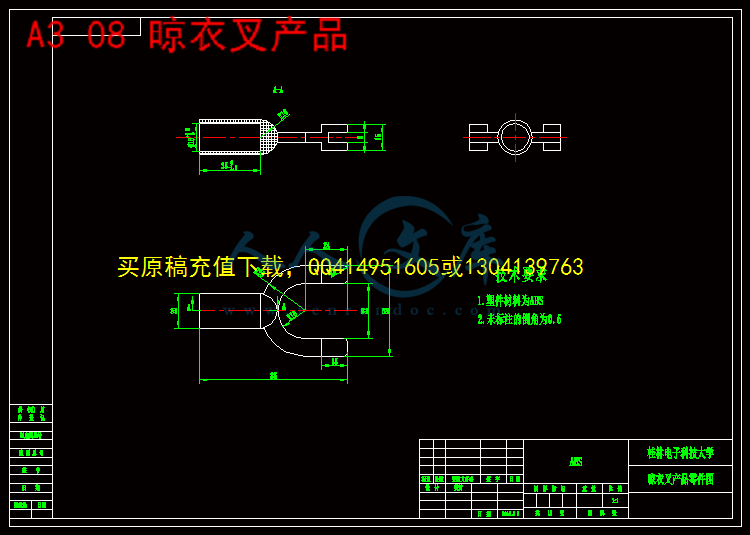
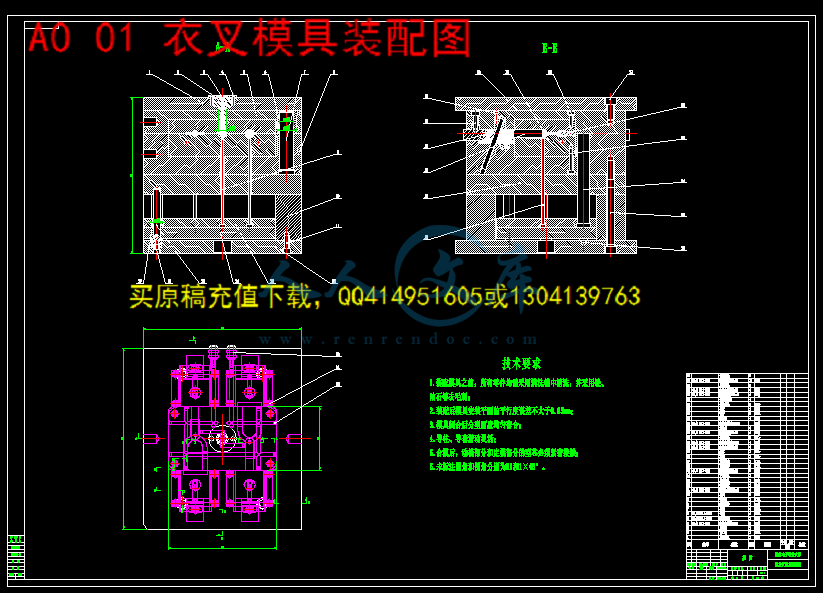

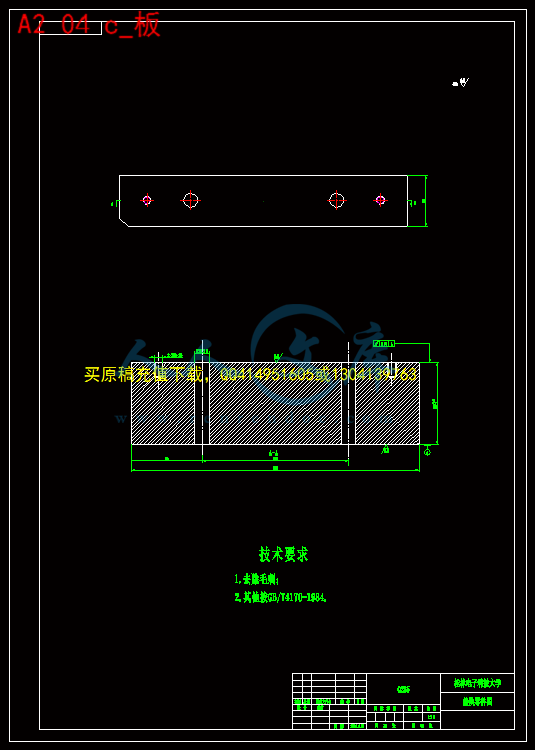
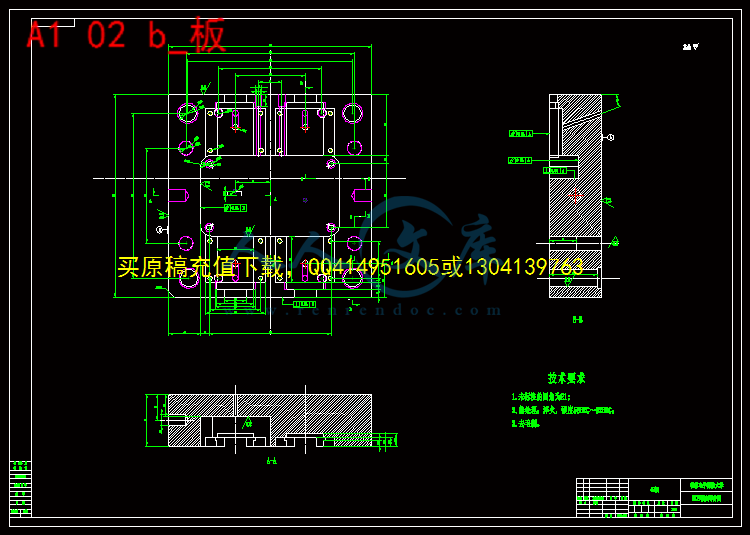