摘 要
电解加工又称电化学加工,是金属工件在电解液中发生阳极溶解的一种加工过程。电解加工对难加工材料可以以柔克刚,对形状复杂的零件可以一次成型,并以表面质量好、生产率高、无工具损耗、无切削应力等优点,在制造业中发挥着重要作用。论文通过对高温合金零件进行分析,设计出一套电解加工工装。电解加工工装包括阴极的设计计算、流场的设计计算以及零件的定位等。阴极的设计采用等间隙分布的原则,在零件原有尺寸上缩小一定的间隙,来设计阴极。根据不同的加工方式可以有不同的加工间隙,这里取加工间隙为0.5mm。对于流场的设计,根据零件的特点采用侧流式加工,在流场设计时还要确定电解液流速和进口压力。另外,流场的设计要均匀,均匀性是指加工面上各处流量充足、均匀,不发生流线相交和其他流场缺陷——如空穴现象、分离现象等。另外,工装的设计要保证良好的密封性。通过设计电解加工工装加工高温合金零件比机械切削加工省时省力,与机械切削加工相比电解加工的表面质量好,且加工范围广,没有切削应力。
关键词:电解加工;阴极设计;流场;工装
High temperature alloy parts electrochemical machining tooling design
Abstract
Electrochemical machining is also called electrochemical machining, metal wor-
kpiece in the electrolyte is an anodic dissolution process. Electrochemical machining of difficult-to-machine materials can, with parts of complex shape can be a forming, and with good surface quality, high productivity, tool wear, cutting stress, plays an important role in manufacturing. Paper through the analysis of high temperature alloy parts, design a set of electrochemical machining tools. Electrochemical machining fixtures including the design of the cathode flow field calculation, design calculation and the positioning parts. Cathode design based on the principle of distribution of intermittent, reduced a certain gap on the parts in the original size, to design the cat-
hode. According to the different processing methods can have different process- sing clearance, here take machining gap is 0.5 mm. To the design of the flow field, accor- ding to the characteristics of the parts with side flow processing, even when in the flow field design to determine the electrolyte flow rate and inlet pressure. In addition, the design of the flow field to uniform and adequate flow throughout uniformity refers to processing surface, uniform, not line intersect and other defects, such as cavitation flow field and separation phenomenon, etc. In addition, the tooling design to ensure good sealing. Through electrochemical machining tooling design than mechanical machining time, high temperature alloy parts compared with mechanical machining electrolytic machining surface quality is good, and the processing range is wide, no cutting stress.
Key Words: Electrochemical machining; The cathode design; The flow field; tooling
目 录
1 绪论1
1.1 电解加工的原理1
1.2 电解加工的特点及分类3
1.3 电解加工的应用及研究现状5
1.4本课题主要研究的目的、意义以及重点和难点6
1.5电解加工的研究方法以及电解加工新技术8
1.6 电解加工的设备以及工艺发展8
2 高温合金零件电解加工阴极的设计与计算10
2.1 电解加工成型规律的研究10
2.2 电解加工阴极设计的方法10
2.3 高温合金零件阴极的设计与计算12
2.4 阴极设计的二维图与三维图15
3 高温合金零件电解加工的流场设计17
3.1电解液的流动形式17
3.2 电解液流速和进口压力的确定18
3.2.1 电解液流速的确定18
3.2.2电解液压力的确定20
3.3 流场均匀性的设计21
4 高温合金零件电解加工工装的设计以及总体工装夹具23
4.1电解加工工装的功能及特殊要求23
4.2高温合金零件阴极的定位与连接24
4.3高温合金零件电解加工底座的设计24
4.4 阴极连接杆的设计25
4.5 电解加工工装的特殊技术要求26
4.6 电解加工的导流和导电方式26
4.7 高温合金零件电解加工的总体设计及工作过程27
5 结论30
5.1 总结30
5.2 体会31
参考文献32
致 谢33
毕业设计(论文)知识产权声明34
毕业设计(论文)独创性声明35
1 绪论
1.1 电解加工的原理
电解加工(Electrochemical machining,ECM)作为机械加工的的补充手段走过了半个世纪。电解加工的基本原理是电化学阳极溶解,而这一电化学过程又是建立在电解加工间隙中特定的电场、流场分布的基础上的,故电场理论、流场理论以及电化学阳极溶解理论构成了研究电解加工工艺的三大基础理论。[2]电解加工以其在难切削材料、复杂形状的零件加工中体现出的特殊优点,较好的适应了军事工业中若干重要关键产品的特殊需要,首先成为军工生产中不可缺少的重要手段和关键技术,在工业发达国家中获得了较好的应用效果,而我国则是世界上应用电解加工最多的国家只一。


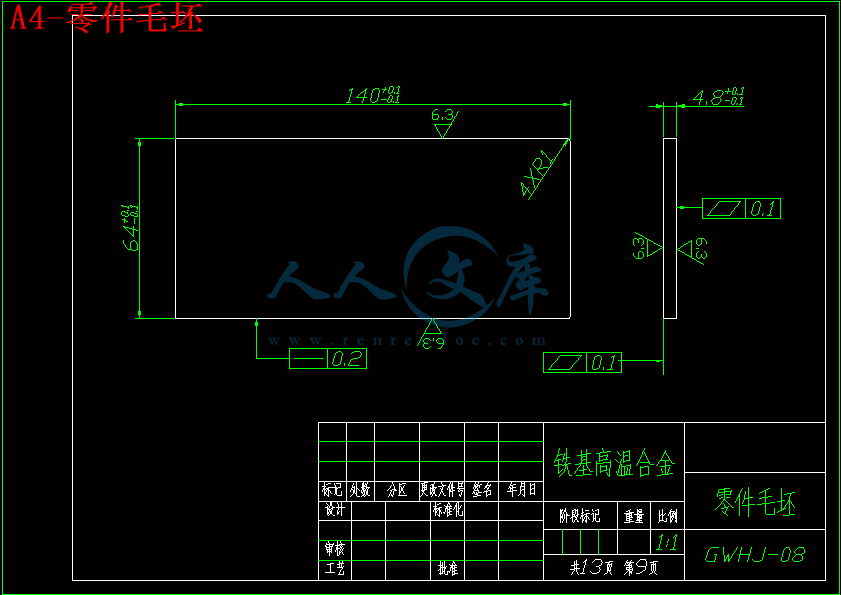
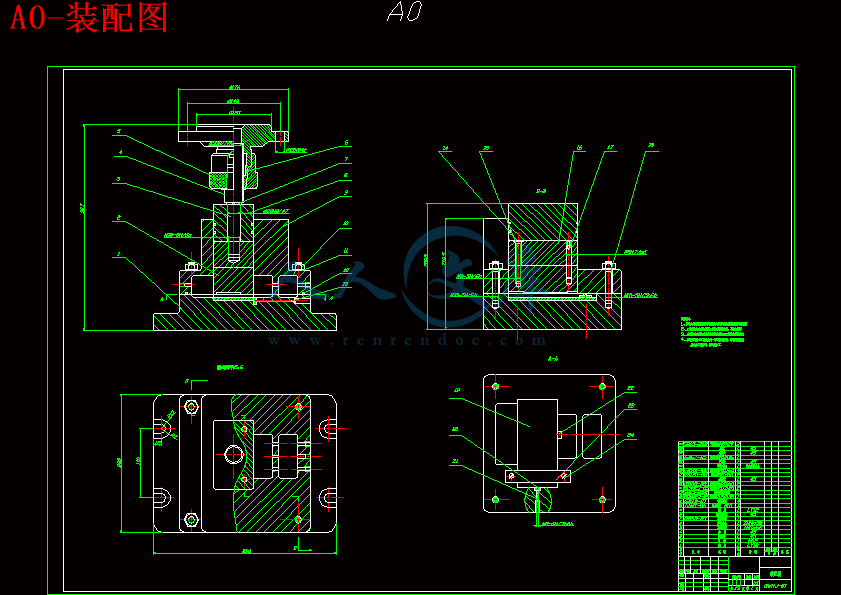

