变速箱壳体组合机床夹具设计【12张CAD图纸+毕业答辩论文】
收藏
资源目录
压缩包内文档预览:(预览前20页/共27页)
编号:449916
类型:共享资源
大小:1.61MB
格式:RAR
上传时间:2015-07-06
上传人:好资料QQ****51605
认证信息
个人认证
孙**(实名认证)
江苏
IP属地:江苏
45
积分
- 关 键 词:
-
变速箱
壳体
组合
机床
夹具
设计
全套
cad
图纸
毕业
答辩
论文
- 资源描述:
-
变速箱壳体组合机床的夹具设计
摘 要:变速箱壳体组合机床采用卧式双面加工方案。用于钻削被加工零件左侧面上的8个∅8.5的孔,1个∅11.9的孔,右侧6个∅8.5的孔,2个∅9.8的孔。主要包括总体设计和夹具设计两个部分。左侧主轴箱用来加工这9个孔,右侧主轴箱用来完成剩下的8个孔的加工,两主轴箱的中间是夹具部分。机床采用液压滑台实现刀具的进给,以保证进给速度的稳定可靠。工件选用“一面两孔”的定位方案,能够保证工件的位置精度要求,同时便于工件装夹,又有利于夹具的设计与制造。采用气压夹紧方式。为保证工件上被加工孔的位置精度,采用了导向装置。因工件批量较大,导向装置中的钻套容易磨损,所以采用了可换钻套。夹具体材料采用HT150,并在夹具体上开设排屑槽以防止切屑在定位元件工作表面上或其他装置中堆积而影响工件的正确定位和夹具的正常工作。
关键词:组合机床;总体设计;夹具
The fixture design of modular machine tool for transmission body based on 3D method
Abstract: The modular machine tool for transmission body uses the horizontal-type and two-side processing plan.It is used for drilling these holes in the work piece: eight holes with the diameter 8.5mm and depth 24mm, one hole with the diameter 11.9mm and depth 25mm on the left side,six diameter 8.5m holes and their bottom surfaces on the right surface, two diameter 9.8mm holes.The topic includes two parts, the general design and fixture design of the machine tool. The left spindle box is used for machining nine tappet holes, the right spindle box is used for machining eight holes, and a fixture is between two spindle boxes.To achieve stable and reliable feed, hydraulic pressure sliding tables are used in this machining tool.The work piece is located at the fixture through "a face two holes",which can ensure the position precision needs of the work piece and be beneficial to design the fixture.The combination machine is clamped by atmospheric pressure devices.To ensure position precision, the guiding devices are used. Replaceable guiding sleeves are chosen, because they are easy wearing in large quantities of production. The material of clamp body is HT150. Chip troughs which are in the clamp body are free of chip falling onto the working surface of positioning components or accumulating on other devices, and ensure the work piece correct positioning and the fixture normal working.
Key words: combination machine; design; fixture
目 录
1前 言1
1.1 本课题的意义1
1.2 国内发展概况1
1.3 课题由来及所需基本条件2
2组合机床总体设计3
2.1 总体方案论证3
2.1.1 加工内容及要求3
2.1.2 机床配置型式的选择3
2.1.3 定位基准的选择3
2.1.4 滑台型式的选择4
2.2 确定切削用量及选择刀具4
2.2.1 切削用量的选择4
2.2.2 计算切削力、切削扭矩及切削功率 5
2.2.3 刀具结构的选择5
2.3 总体设计—“三图一卡”6
2.3.1 被加工零件工序图6
2.3.2 加工示意图6
2.3.3 机床尺寸联系总图7
2.3.4 机床生产率计算卡9
3 组合机床夹具设计12
3.1 夹具设计的基本要求和步骤12
3.1.1 夹具设计的基本要求12
3.1.2 夹具设计的步骤12
3.2 定位方案的确定13
3.2.1 零件的工艺性分析13
3.2.2 定位方案论证13
3.2.3 误差分析13
3.2.4 校核加工精度15
3.3导向装置15
3.4 夹紧方案的确定16
3.4.1 夹紧装置的确定16
3.4.2 夹紧力的确定18
3.4.3 气缸的选择19
3.5 夹具体的设计20
3.6 夹具三维设计20
3.6.1 三维建模及三维软件介绍20
3.6.2 基于三维的夹具设计过程21
4 结论24
参 考 文 献25
致 谢26
附 件 清 单27
1 前言
1.1 本课题的意义
组合机床是由大量的通用部件和少量专用部件组成的工序集中的高效率专用机床。它能够对一种(或几种)零件进行多刀、多轴、多面、多工位加工。在组合机床上可以完成钻孔、扩孔、铰孔、镗孔、攻丝、车削、铣削、磨削及滚压等工序,生产效率高,加工精度稳定。因此,在现代化大生产中,要使零件加工具有高的生产效率,良好的加工精度、精度稳定性,好的经济性,采用组合机床加工是一个和好的选择。而如何设计一台好的组合机床就成为了关键,机床夹具是在金属切削加工中,用以准确地确定工件位置,并将其牢固地夹紧,以接受加工的工艺装备。它的主要作用是:可靠地保证工件的加工质量,提高加工效率,减轻劳动强度,充分发挥和扩大机床的工艺性能。因此,机床夹具在机械制造中占有重要的地位,这正是本课题需要解决的问题。
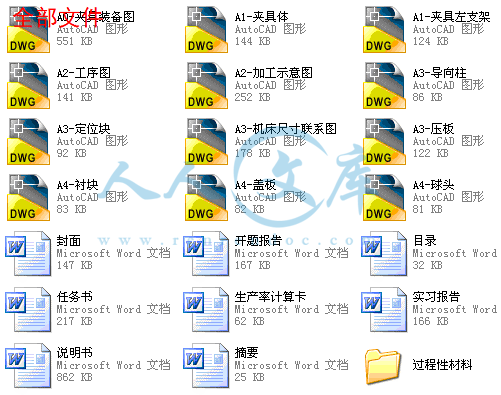
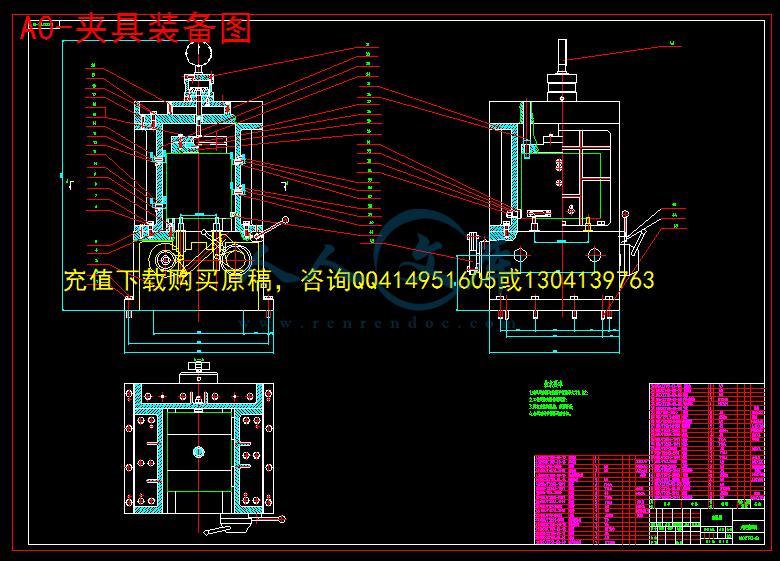
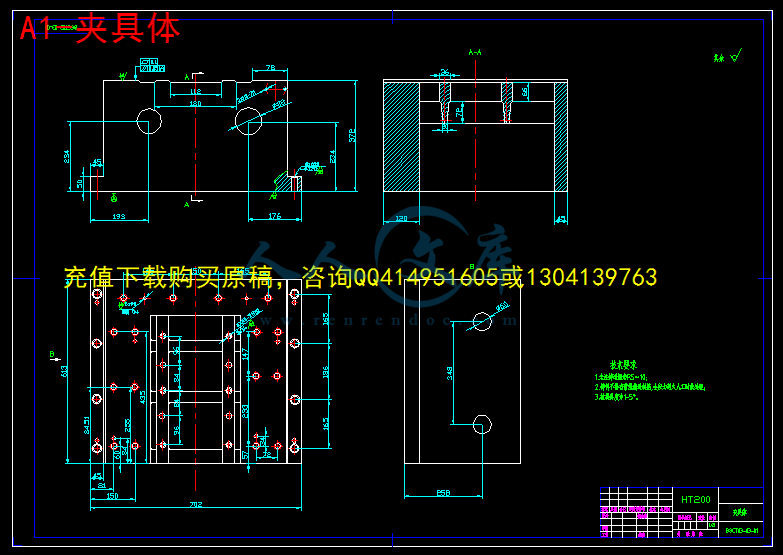
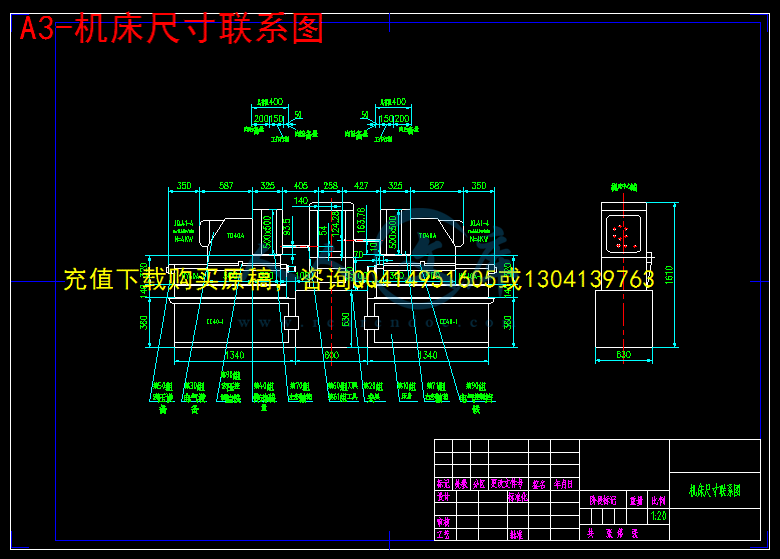
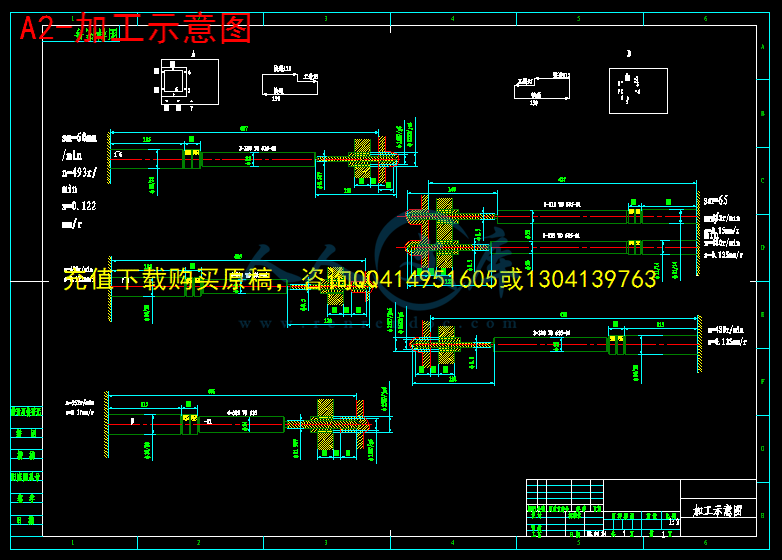
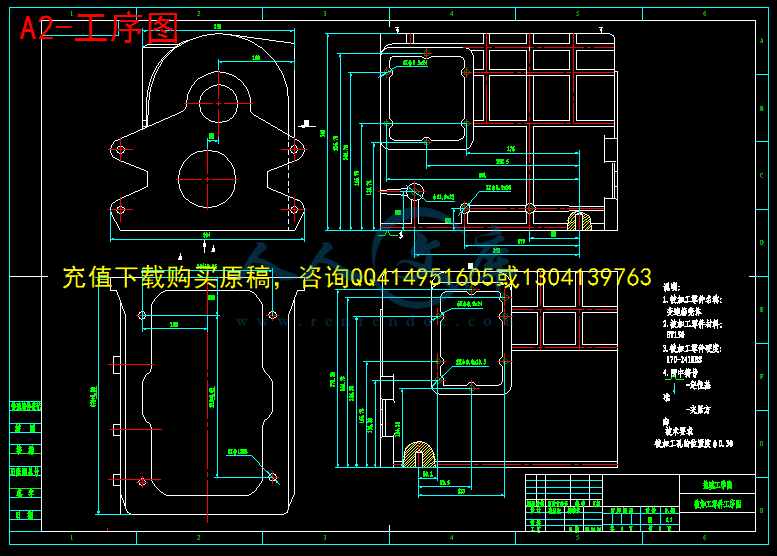
- 内容简介:
-
盐城工学院毕业设计说明书 2008 1 1 前言 1.1 本课题的意义 组合机床是由大量的通用部件和少量专用部件组成的工序集中的高效率专用机床。它能够对一种(或几种)零件进行多刀、多轴、多面、多工位加工。在组合机床上可以完成钻孔、扩孔、铰孔、镗孔、攻丝、车削、铣削、磨削及滚压等工序,生产效率高,加工精度稳定。因此,在现代化大生产中,要使零件加工具有高的生产效率,良好的加工精度、精度稳定性,好的经济性,采用组合机床加工是一个和好的选择。而如何设计一台好的组合机床就成为了关键,机床夹具是在金属切削加工中,用以准确地确定工件位置,并将其牢固地夹 紧,以接受加工的工艺装备。它的主要作用是:可靠地保证工件的加工质量,提高加工效率,减轻劳动强度,充分发挥和扩大机床的工艺性能。因此,机床夹具在机械制造中占有重要的地位,这正是本课题需要解决的问题。 1.2 国内发展概况 目前,组合机床在机械制造工业中应用越来越普遍,并已显示出其巨大的优越性。主要表现在以下几个方面:高速度、高精度、柔性化、 模块化、高生产率 等方向发展。 因此组合机床装备的发展思路必须是以提高组合机床加工精度、组合机床柔性、组合机床工作可靠性和组合机床技术的成套性为主攻方向。一方面,加强数控技术的 应用,提高组合机床产品数控化率;另一方面,进一步发展新型部件,尤其是多坐标部件,使其模块化、柔性化,适应可调可变、多品种加工的市场需求。同时,高性能的组合机床的应用也越来越多,诸如被广泛应用于工程机械、交通、能源、军工、轻工、家电等行业。我国传统的组合机床及组合机床自动线主要采用机、电、气、液压控制,它的加工对象主要是生产批量比较大的大中型箱体类和轴类零件,完成钻孔、扩孔、铰孔,加工各种螺纹、镗孔、车端面和凸台,在孔内镗各种形状槽,以及铣削平面和成形面等。 随着技术的不断进步,一种新型的组合机床 柔性组合机 床越来越受到人们的青睐,它应用多位主轴箱、可换主轴箱、编码随行夹具和刀具的自动更换,配以可编程序控制器( PLC)、数字控制( NC)等,能任意改变工作循环控制和驱动系统,并能灵活适应多品种加工的可调可变的组合机床。另外,近年来组合机床加工中心、数控组合机床、机床辅机(清洗机、装配机、综合测量机、试验机、输送线)等在组合机床行业中所占份额也越来越大。 夹具方面,随着科学技术的进步和市场需求的变化,现代机械制造业得到了较快的发展。多品种、小批量生产方式将成为今后的主要生产形式,制造系统正向着柔性化、集成化、智能化 方向发展,机床愈来愈多地采用先进的技术,加工效率不断地提高。机械产品的加工精度日益提高,高精度的机床大量出现 。为了适应生产发展的需要 ,机床夹具正在向柔性化、高效化、自动化、精密化、标准化方向发展。 nts基于三维的变速箱壳体组合机床夹具设计 2 1.3 课题由来及基本条件 a)设计内容 设计一台变速箱壳体双面组合机床 ; 总体设计:制定工艺方案,确定机床配置型式及结构方案,“三图一卡”设计; 部件设计:组合机床夹具设计 b)设计依据 被加工零件: 变速箱壳体(附零件图) 工件材料: HT150 加工内容:一侧钻削 8 8.5 深 24 的孔, 11.9 深 25 的孔 ;另一侧 6 8.5 深 24的孔, 2 9.8 深 18.5 的孔。 生产纲领: 大批大量 nts盐城工学院毕业设计说明书 2008 3 2 组合机床总体设计 2.1 总体方案论证 本设计的加工对象为变速箱壳体,材料是 HT150,硬度 HBS170-241,重量 21Kg,属于箱体零件,结构复杂。 2.1.1 加工内容及要求 根据先粗后精、先基准面后其它表面、先主要表面后次要表面的机械加工工序安排的设计原则,对变速箱壳体的工艺路线作如下设计: a)粗铣底面; b)粗铣左、右端面; c)粗铣前、后端面; d)半 精铣底面; e)半精铣左、右端面; f)半精铣前、后端面; g)粗镗孔; h)精镗孔; i)钻左、右面的孔; j)攻丝。 本道工序为第 9 道工序,主要加工左右二面上的 17个孔。具体加工内容是:左侧面 9个孔, 钻削 8 8.5 深 24 的孔, 1 11.9 深 25 的孔 ;钻右侧面上 8个孔,钻削 6 8.5 深 24 的孔, 2 9.8 深 18.5 的孔 2.1.2 机床配置型式选择 根据任务书的要求:设计的组合机床要满足加工要求、保证加工精度;尽可能用通用件、以降低成本;各动力部件用电气控制。因此根据任务书要求和变速箱壳体 的特点初定两种设计方案: a) 卧式组合机床 特点:卧式组合机床重心低、振动小运作平稳、加工精度高、占地面积大。 b)立式组合机床 特点:立式组合机床重心高、振动大、加工精度低、占地面积小。 通过以上的比较,考虑到卧式床身振动小,装夹方便等优点,选用卧式组合机床。 2.1.3 定位基准的选择 组合机床是针对某种零件或零件某道工序设计的。正确选择定位基准,是确保加工精度的重要条件,同时也有利于实现最大限度的集中工序。本机床加工时采用的定位方式是以底面为定位基准面,限制三个自由度;用两个挡铁限制两个 自由度;在左侧有一个支承针,限制剩下的一个自由度。 nts基于三维的变速箱壳体组合机床夹具设计 4 2.1.4 滑台型式的选择 本组合机床采用的是液压滑台。与机械滑台相比较,液压滑台具有如下优点:在相当大的范围内进给量可以无级调速;可以获得较大的进给力;由于液压驱动,零件磨损小,使用寿命长;工艺上要求多次进给时,通过液压换向阀,很容易实现;过载保护简单可靠;由行程调速阀来控制滑台的快进转工进,转换精度高,工作可靠。但采用液压滑台也有其弊端,如:进给量由于载荷的变化和温度的影响而不够稳定;液压系统漏油影响工作环境,浪费能源;调整维修比较麻烦。本课题的 加工对象是变速箱壳体左、右两个面上的 17个孔,位置精度和尺寸精度要求较高,因此采用液压滑台。 由此,根据已定的工艺方案和机床配置形式并结合使用及修理等因素,确定机床为卧式两面单工位液压传动组合机床,液压滑台实现工作进给运动,选用配套的动力箱驱动主轴箱钻孔、镗孔主轴。 . 2.2 确定切削用量及选择刀具 2.2.1 切削用量的选择 对于 17个被加工孔,采用查表法选择切削用量,从 1P130表 6-11 中选取。由于钻孔、镗孔的切削用量还与孔深度有关,随孔深的增加而逐渐递减,其递减值按1P131 表 6-12 选取 。降低进给量的目的是为了减小轴向切削力,以避免钻头、镗头折断。孔深度较大时,由于冷却排屑条件都较差,是刀具寿命有所降低。降低切削速度主要是为了提高刀具寿命,并使加工较深孔时钻头、镗头的寿命与加工其他浅孔时钻头、镗头的寿命比较接近。 A. 对左面上 9个孔的切削用量的选择 a)钻孔 1孔 8 8 8.5,盲孔, l=24mm 由 d 6 12,硬度大于 170 241HBS,选择 v=10 18m/min ,f 0.1 0.18mm/r,又 d=8.5mm,取定 v=13.2m/min , f=0.122mm/r,则由 (2-1) 得: n=1000 13.2/8.5 =493r/min b)钻孔 9 1 11.9,盲孔, l=25mm 由 d 6 12,硬度大于 170 241HBS,选择 v=10 18m/min, f 0.1 0.18mm/r,又 d=11.9mm,取定 v=13.2m/min , f=0.17mm/r, 则 n=1000 13.2/11.9 =352r/min B. 对右面上 8个孔的切 削用量的选择 a)钻孔 1、 2、 4、 5、 6、 8 6 8.5,盲孔, l=24mm 由 d 6 12,硬度大于 170 241HBS,选择 v=10 18m/min, f 0.1 0.18mm/r,又 d=8.5mm,取定 v=12.8m/min, f=0.135mm/r, d vn 1000nts盐城工学院毕业设计说明书 2008 5 则 n=1000 12.8/8.5 =480r/min b)钻孔 3、 7 2 9.8,盲孔, l=18.5mm 由于精镗,加工材料为铸铁,硬度大于 170 241HBS,选择 v=10 18m/min, f 0.1 0.18mm/r,又 d=9.8mm,取定 v=13m/min, f=0.15mm/r, 则 n=1000 13/9.8 =422r/min (孔的编号见被加工零件工序图) 2.2.2 计算切削力、切削扭矩及切削功率 钻孔:根据 91341 P 表 6-20中公式 6.08.026 HBDfF 6.08.09.110 HBfDT DTvP 9740 式中, F 切削力( N); T 切削转矩( N); P 切削功率( Kw); v 切削速度( m/min); f 进给量( mm/r); D 加工(或钻头)直径( mm); HB 布氏硬度 ,,在本设计中, max 241HB , min 170HB , 得 HB=217.3。 由以上公式可 得: 左面 单根 1 8轴 F=1036.9N T=2736.65Nmm P=0.139Kw 9轴 F=1892.85N T=6762.9Nmm P=0.2453Kw 右面 单根 1、 2、 4、 5、 6、 8轴 F=1124.3N T=2967.56Nmm P=0.1461Kw 单根 3、 7轴 F=1410N T=4230.95Nmm P=0.1835Kw (轴编号与孔编号相对应 ) 总的切削功率:即求各面上所有轴的切削功率之和 左面 Pw=8 0.139+0.2453=1.3573Kw 右面 Pw=6 0.1461+2 0.1835=1.2436Kw 实际切削功率 根据 1, P=(1.5 2.5)Pw,因为是多轴加工,故取定 P=2Pw 则 P左 =2 1.3573=2.7146Kw P右 =2 1.2436=2.4872Kw 2.2.3 刀具结构的选择 根据工艺要求及加工精度的要求, 17个加工孔的刀具采用标准锥柄麻花钻 . 2.3 总体设计 “三图一卡” 2.3.1 被加工零件工序图 )(31 m inm a xm a x HBHBHBHB nts基于三维的变速箱壳体组合机床夹具设计 6 被加工零件工序图是根据制定的工艺方案,表示所设计的组合机床(或自动线)上完成的工艺内容,加工部位的尺寸、精度、表面粗糙度及技术要求,加工用的定位基准、夹压部位以及被加工零件的材料、硬度和在本机床加工前加工余量、毛坯或半成品情况的图样 。除了设计研制合同外,它是组合机床设计的具体依据,也是制造、使用、调整和检验机床精度的重要文件。 2.3.2 加工示意图 零件加工的工艺方案要通过加工示意图反映出来。加工示意图表示被加工零件在机床上的加工过程,刀具、辅具的布置状况以及工件、夹具、刀具等机床各部件间的相对位置关系,机床的工作行程及工作循环等。 A. 刀具的选择 刀具直径的选择应与加工部位尺寸、精度相适应。孔 8.5选择刀具 8.5G7;孔 11.9选择刀具 11.9G7;孔 9.8选择刀具 9.8G7。 B. 导向结构的选择 组合机床钻孔时,零件上孔的位置精度主要是靠刀具、接杆的导向装置来保证的。导向装置的作用是:保证刀具相对工件的正确位置;保证刀具相互间的正确位置;提高刀具系统的支承刚性。 本课题中加工 9个孔时导向表面旋转线速度均小于 20m/min,所以导向装置选用固定导套。 对于加工 8.5孔,选择的导套尺寸为: D=15mm, D1=22mm, D2=26mm,L=25mm, l=8mm, l1=3, e=18.5mm,配用的螺钉 M6。 对于加工 11.9孔,选择的导套尺寸为: D=18mm, D1=26mm, D2=30m, L=25mm,l=8mm, l1=3, e=22mm,配用的螺钉 M8。 对于加工 9.8孔,选择的导套尺寸为: D=15mm, D1=22mm, D2=26mm,L=25mm, l=8mm, l1=3, e=18.5mm,配用的螺钉 M6。 C. 确定主轴、尺寸、外伸尺寸 在该课题中,主轴用于钻孔、镗孔,选用滚珠轴承主轴。又因为浮动卡头与刀具刚性连接,所以该主轴属于长主轴。故本课题中的主轴均为滚珠轴承长主轴。 根据由选定的切削用量计算得到的切削转矩 T,由公式 943P 4 102.6 Td (2-5) 式中, d 轴的直径(); T 轴所传递的转矩( N m); B 系数,本课题中主轴为非刚性主轴,取 B=6.2。 由公式可得: 左面 1 8轴 d=14.2 9轴 d=17.78 右面 1、 2、 4、 5、 6、 8轴 d=14.47 3、 7轴 d=15.8 nts盐城工学院毕业设计说明书 2008 7 考虑到安装过程中轴的互换性、安装方便等因素,除右面 2、 6 轴径取为 15 外,其余 15根主轴轴径均取为 20。 根据主轴类型及初定的主轴轴径,查 9P44 表 3-6 可得到主轴外伸尺寸及接杆莫氏圆锥号。主轴轴径 d=15 时,主轴外伸尺寸为: 16/25/ 1 dD ,L=85 ;接杆莫氏圆锥号为。主轴轴径 d=20时,主轴外伸尺寸为: 20/32/ 2 dD ,L=115;接杆莫氏圆锥号为。 D. 动力部件工作循环及行程的确定 a) 工作进给长度工L的确定 工作进给长 度工L,应等于加工部位长度 L(多轴加工时按最长孔计算)与刀具切入长度 1L 和切出长度 2L 之和。切入长度一般为 5 10,根据工件端面的误差情况确定。钻孔时切出长度按 946P 表 3-7 )83(32 dL (2-6) 计算式中, d为钻头直径。两个面上钻孔时的工作进 给长度见下表 : 表 2-1 两个面上钻孔的工作进给长度 L 1L d 2L 工L左主轴箱 47 8 8.5 10 65 右主轴箱 10.2 5 11.5 8 23.2 b) 快速进给长度的确定 快速进给是指动力部件把刀具送到工作进给位置。初步选定两个主轴箱上刀具的快速进给长度为 115。 c) 快速退回长度的确定 快速退回长度等于快速进给和工作进给长度之和。由已确定的快 速进给和工作进给长度可知,两面快速退回长度为 150。 d) 动力部件总行程的确定 动力部件的总行程为快退行程与前后备量之和。两面的前备量取 30,后备量取 190,则总行程为 400。 2.3.3 机床尺寸联系总图 A. 选择动力部件 a) 动力滑台型号的选择 根据选定的切削用量计算得到的单根主轴的进给力,按式 962P ni iFF 1多轴箱 (2-7) 式中,iF 各主轴所需的 向切削力,单位为 N。 nts基于三维的变速箱壳体组合机床夹具设计 8 则 左主轴箱 NF 05.1 0 1 8 885.1 8 9 29.1 0 3 68 多轴箱右主轴箱 NF 8.9 3 6 31 4 1 023.1 1 2 46 多轴箱实际上 ,为克服滑台移动引起的摩擦阻力,动力滑台的进给力应大于 多轴箱F 。又考虑到所需的最小进给速度、切削功率、行程、主轴箱轮廓尺寸等因素,为了保证工作的稳定性,由 991P 表 5-1,左、右两面的液压滑台均选用 1HY40A-I型。台面宽400mm,台面长 800mm,行程长 400mm,滑台及滑座总高 320mm,滑座长 1240mm,允许最大进给力 20000N,快速行程速度 8m/min,工进速度 12.5 500mm/min。 b) 动力箱型号的选择 由切削用量计算得到的各主轴的切削功率的总和切削P,根据公式 847P 切削多轴箱PP (2-8) 式中 , 切削P 消耗于各主轴的切削功率的总和( kW) ; 多轴箱的传动效率 ,加工黑色金属时取 0.8 0.9,加工有色金属时取 0.70.8;主轴数多、传动复杂时取小值,反之取大值。本课题中,被加工零件材料为灰铸铁,属黑色金属,又主轴数量较多、传动复杂,故取 8.0 。 左主轴箱: kW7146.2切削P则 3 . 3 9 3 2 5 k W0 . 87146.2 多轴箱P右主轴箱: kW4872.2切削P则 kW109.30 . 84872.2 多轴箱P根据液压滑台的配套要求,滑台额定功率应大于电机功率的原则,查 9115114P 表5-38得出动力箱及电动机的型号 表 2-2 动力箱及电动机型号 动力箱型号 电动机型号 电动机功率(kW) 电动机转速(r/min) 输出轴转速(r/min) 左主轴箱 1TD40I Y132S-4 5.5 1440 720 右主轴箱 1TD40I Y132S-4 5.5 1440 720 c) 配套通用部件的选择 侧底座 CC401,其高度 H=560,宽度 B=600,长度 L=1350。 B. 确定机床装料高度 H 装料高度是指机床上工件的定位基准面到地面的垂直距离。本课题中,工件最低孔位置 mmh 5.1032 ,主轴箱最低主轴高度 mmh 5.931 ,所选滑台与滑座总高mmh 3203 ,侧底座高度 mmh 5604 ,夹具底座高度 mm370h 5 ,中间底座高度mm630h 6 ,综合以上因素,该组合机床装料高度取 H=880。 nts盐城工学院毕业设计说明书 2008 9 a) 确定主轴箱轮廓尺寸 主要需确定的尺寸是主轴箱的宽度 B和高度 H及最低主轴高度 1h 。主轴箱宽度 B、高度 H的大小主要与被加工零件孔的分布位置有关,可按下式计算: 12bbB (2-9) 11 bhhH (2-10) 式中, b 工件在宽度方向相距最远的两孔距离(); 1b 最边缘主轴中心距箱外壁的距离(); h 工件在高度方向相距最远的两孔距离(); 1h 最低主轴高度()。 其中, 1h 还与工件最低孔位置( mmh 5.1032 )、机床装料高度( H=880)、滑台滑座总高( mmh 3203 )、侧底座高度( mmh 5604 )、滑座与侧底座之间的调整垫高度( mmh 57 )等尺寸有关。对于卧式组合机床, h1要保证润滑油不致从主轴衬套处泄漏箱外,通常推荐 mmh 140851 ,本组合机床按式 1 2 3 7 4( 0 . 5 )h h H h h h (2-11) 计算,得: mmh 981 。 b=180mm,h=242.78mm,取1 60b mm,则求出主轴箱轮廓尺寸: mmbbB 3 0 06021 8 02 1 mmbhhH 78.400609878.24211 根据上述计算值 ,按主轴箱轮廓尺寸系列标准,最后确定主轴箱轮廓尺寸为 B H=500 500。 2.3.4 机床生产 率计算卡 已知:工作行程为 150 进刀量为 8000 /min 辅助时间夹紧 0.5min 机动时间 0.582min 装料时间 0.5min 卸料时间 0.5min 单件工时 2.158min/件 A.理想生产率 Q(件 /h) 理想生产率是指完成年生产纲领(包括备品及废品率)所要求的机床生产率。用公式 851P ktNQ(2-12) 计算,式中, N 年生产纲领(件),本课题中 N=55000件; kt 全年工时总数,本课题以单班 7小时计,则 htk 2350。 则 h4.23235055000 件 ktNQB.实际生产率 Q1(件 /h) 实际生产率是指所设计的机床每小时实际可生产的零件数量。即公式 851P nts基于三维的变速箱壳体组合机床夹具设计 10 单TQ 601 (2-13) 式中,单T 生产一个零件所需时间( min)。 则 8.27158.2 601 Q件 /h C.机床负荷率 机床负荷率为理想生产率与实际生产率之比。即公式 852P 1QQ(2-14) 则 根据以上算得的数据,填写机床生产率计算卡,详见表 2-3。 %1.84%1 0 0.827 4.231 QQnts盐城工学院毕业设计说明书 2008 11 表 2-3 机床生产率计算卡 被加工零件 图号 毛胚种类 铸 件 名称 变速箱壳体 毛胚重量 21kg 材料 HT150 硬 度 170241HBS 工序名称 钻两侧面 工序号 序 号 工步名称 被加 工零 件数 加 工 直径 mm 加工 长度 mm 工作 行程 mm 切削 速度 m/min 转速 r/min 每转 进给量 mm/r 每分钟 进给量 mm/min 工 时 min 机动 时间 辅助 时间 共计 1 装入工件 1 0.5 2 工件定位夹紧 0.5 3 左动力部件 快进 115 5000 0.023 钻 8.5 孔 8.5 24 35 13.2 493 0.122 60.164 0.582 钻 11.9 孔 11.9 25 35 13.2 352 0.17 59.84 0.585 死挡铁停留 0.02 快退 150 5000 0.03 4 右动力部件 快进 115 5000 0.023 钻 8.5 孔 8.5 24 35 12.8 480 0.135 64.8 0.540 钻 9.8 孔 9.8 25 35 13 422 0.15 63.3 0.553 死挡铁停留 0.02 快退 150 5000 0.03 5 松开工件 0.2 6 卸下工件 0.3 备 注 单位工时 2.158min 机床实际生产率 Q1 27.80 件 /h 机床理想生产率 Q 23.4 件 /h 负荷率 84.2% nts基于三维的变速箱壳体组合机床夹具设计 12 3 组合机床夹具设计 3.1 夹具设计的基本要求和步骤 3.1.1 夹具设计的基本要求 A.提高生产率、降低成本 夹具设计方案应与生产纲领相适应。在大批量生产时,为了缩短辅助时间,提高生产率,尽量采用快速、高效的结构和自动控制装置;在批量生产和满足夹具功能的前提下,尽量使夹具结构简单,容易制造,以降低夹具的制造成本。 B.保证工件的加工精度 夹具设计的最基本要求是保证工件的加工精度。关键是确定定位方案、夹紧方案,和合理地设计夹具的尺寸、公差和技术要求,必要时应进行误差的分析和计算。 C.便于排屑 夹具的排屑是一个很重要的问题,切屑积集在夹具中,会破坏工件正确的定位;切屑带来的大量热量会引起夹具和工件的热变形,影响加工质量;切屑的的清扫又会增加辅助时间,降低生产率。切屑积集严重 时,还会造成设备事故或工伤事故。因此,在夹具设计时排屑问题必须给予充分的注意。 D.操作方便、省力和安全 夹具的操作要尽量做到方便、省力,尽可能采用气动、液压及其他机械化夹紧装置、以减轻工人的劳动强度,控制好夹紧力。夹具操作位置应符合操作工人的习惯,应有安全保护装置,确保使用安全。 E.有良好的结构工艺性 夹具的结构应简单、合理,便于加工、装配、检验和维修,尽可能多选用标准部件和标准元件。 夹具设计通常可以在参阅有关资料的情况下,按加工要求设计方案,绘制图样,经修改确定夹具的结构。 3.1.2 夹具设计的步骤 A.设计前的准备 分析产品零件图及装配图,分析零件的作用、形状、结构特点、材料和技术要求;分析零件的加工工艺规程,工艺装备设计任务书,对任务书所提出的要求进行可行性研究;了解所用机床的规格、性能、精度以及与夹具选择动力部件 B.方案设计 在分析各种原始资料的基础上,确定夹具的类型、定位设计、夹紧方式、导向方案 、连接方式、总体布局和夹具的结构形式。绘制方案设计图,进行工序精度分析,对动力夹紧装置进行夹紧力的计算。 C.审核 检查夹具的各项功能是否符合设计要求。 D.总体设计 根据所定方案 绘制夹具装配图,应将夹具的工作原理、结构和各种元件的装配nts盐城工学院毕业设计说明书 2008 13 关系表达清楚。用双点划线绘制工件外形轮廓。合理选择材料,标注尺寸、公差和技术要求。 E.夹具零件设计 F.夹具的装配、调试和验证 3.2 定位方案的确定 3.2.1 零件的工艺性分析 夹具是组合机床的重要组成部分,是根据机床的工艺和结构方案的具体要求而专门设计的。它用于实现被加工零件的准确定位、夹压、刀具的导向以及装卸工件时的限位。 变速箱壳体材料为 HT150,其硬度为 170 241HBS,在本工序之前工件主要表面已加工完毕。本道工序一侧钻削 8 8.5 深 24 的孔, 11.9 深 25 的孔;另一侧6 8.5 深 24 的孔, 2 9.8 深 18.5 的孔。 3.2.2 定位方案论证 箱体零件的定位方案一般有两种,“一面两销”和“三平面”定位方法。 A“一面两销”的定位方法 它的特点是:可以简便地消除工件的六个自由度,使工件获得稳定可靠定位。有同时加工零件五个表面的可能,既能高度集中工序,又有利于提高各面上孔的位置精度。“一面双孔”可作为零件从粗加工到精加工全部工序的定位基准,使零件整个工艺过程基准统一,从而减少由基准转换带来的累积误差,有利于保证零件的 加工精度。同时,使机床各个工序(工位)的许多部件实现通用化,有利于缩短设计、制造周期,降低成本。易于实现自动化定位、夹紧,并有利于防止切削落于定位基面上。 B“三平面”定位方法 它的特点是: 可以简便地消除工件的六个自由度,使工件获得稳定可靠定位。有同时加工零件两个表面的可能,能高度集中工序。 被加工零件为变速箱壳体属箱体类零件,本工序加工为双面加工零件,加工工序集中、精度要求高,故选用“一面两销”定位方法,采用“一面两销”定位方法,能够保证工件的位置精度要求,同时便于工件装夹,又有利于夹具的设计与制造 。 3.2.3 误差分析 用夹具装夹工件进行机械加工时,其工艺系统中影响工件加工精度的因素很多,与夹具有关的因素有: A. 定位误差 D ; B. 对刀误差 T ; C. 夹具的安装误差 A ; D. 夹具误差 J ; E. 在机械加工工艺系统中,影响加工精度的其它因素综合称为加工方法误差G ; F. 上述各 项误差均导致刀具相对工件的位置不精确而形成总的加工误差。 nts基于三维的变速箱壳体组合机床夹具设计 14 具体误差分析如下: A. 定位误差 D a) 基准不重合误差B基准不重合误差是由于定位基准和工序基准不重合而引起的工序基准相对于定位基准在加工尺寸上的最大位置变动范围。在本设计中,由于定位误差和工序基准是重合的,所以基准不重合误差B= 0。 b) 基准位移误差W基准位移误差是由于定位元件和定位基面本身的误差而引起的定位基准在加工尺寸上的误差。 当支承面即工件底面对夹具的安装基准(底面)有平行度误差,被加工孔的定位误差取: 02.0Wmm D = B + W = 0.02mm B. 对刀误差 T 因为刀具相对于对刀或导向元件的位置不精确而造成的加工误差,称为对刀误差。 钻 套导向孔尺寸 8.5G7( mm02.0005.05.8 ),钻头尺寸为 8.5h9( mm0036.05.8 )对刀误差为钻头于导向孔的最大的间隙 : mmXT 0 5 6.00 3 6.002.0m a x C. 夹具的安装误差 A 因夹具在机床上的安装不精确而造成的加工误差,称为夹具的安装误差。 夹具的安装基面为平面,因而没有安装误差, A =0 D. 夹具误差J因夹具上定位元件、对刀或导向元件及安装基面三者之间(包括导向元件与导向元件之间)的位置不精确而造成的加工误差,称为夹具误差,夹具误差大小取决于夹具零件的加工精度的夹具装配时的调整和修配精度。 夹具误差J主要包括定位元件相对于安装基准的尺寸或位置误差1J;定位元件相对于对刀或导向元件(包括导向元件之间)的尺寸或位置误差2J;导向元件相对于安装基准的 尺寸或位置误差3J。 1J=0.02mm 2J、3J与1J在公差上兼容,只需计算其中较大的一项即可。 J=0.02mm E. 加工方法误差 G 加工方法误差是指在切削加工过程中,因机床、刀具质量、工件材质以及由于切削 力、切削热的作用而引起的工艺系统弹性变形、热变形等因素使加工表面位置发生变化,从而造成的加工尺寸误差。因该项误差影响因素很多,又不便于计算,所以常根据经验为它留出工件公差的31。计算时可设 G3k(3-1) nts盐城工学院毕业设计说明书 2008 15 式中:k 工件位置公差取 0.30mm G= mmk 10.030.0313 3.2.4 校核加工精度 工件在夹具中加工时,总加工误差 为上述各项误差之和。由于上述误差均为独立随机误差,应用概率法相加,根据文献 7375工件加工精度的条件为: kGJATD 22222(3-2) 2222222222 10.002.00056.002.0 GJATD = 0.118mm k= 0.30mm 即工件总加工误差 应不大于工件的加工尺寸公差k,由以上得知,本夹具完全可以保证加工精度。 为保证夹具有一定的使用寿命,防止夹具因磨损而过早报废,在分析计算工件加工精 度时需留出一定精度储备量cJ,因此将上式改为: k cJ 或 cJ=k 0 ( 3-3) 当cJ 0时夹具能满足加工要求,根据以上得: cJ=k =0.30-0.118=0.182 0 所以夹具完全可以满足加工所要的要求。 3.3 导向装置 导向装置的作用在于保证刀具对于工件的正确位置;保证各刀具相互间的正确位置和提高刀具系统的支承刚性。 变速箱壳体的两面钻组合机床的刀具导向装置是设计在夹具支架上的,由于是大批生产,所以采用可换式导套,是刀 具在钻套内工作的。 钻套的主要参数包括:钻套的直径和公差配合,钻套的长度,钻套至工件端面的距离。 钻套的配合间隙对于孔的位置精度有较大的影响。为了提高加工的精度,应选择较紧的配合。 变速箱壳体两面钻孔是在精密的导套中进行的,因此要求较高的位置精度,达到 0.05mm,而且导套应尽量接近被加工表面,力求选用较高的精度和较紧的配合。 导套结构如图 3-1 所示。 nts基于三维的变速箱壳体组合机床夹具设计 16 图 3-1 导套结构图 固定钻套的尺寸可查文献 2的 175页的表 8-4: 对于加工 8.5孔,选择的导套尺寸为: mmD 81 , mmD 261 , mmD 302 , mmL 16 。 配合尺寸为: 6/781 gH , 6/726 nH 配用的螺钉 M6 对于加工 9.8孔,选择的导套尺寸为: mmD 16 , mmD 261 , mmD 302 , mmL 16 。 配合尺寸为: 6/781 gH , 6/726 nH 配用的螺钉 M6 对于加工 11.9孔,选择的导套尺寸为: mmD 81 , mmD 621 , mmD 302 , mmL 16 。 配合尺寸为: 6/781 gH , 6/762 nH 配用的螺钉 M8 3.4 夹紧方案的确定 3.4.1 夹紧装置的确定 A 夹紧装置的组成 本设计中夹紧装置采用气压夹紧装置,由气源装置、中间传力机构、夹紧元件三部分组成。其组成部分的相互关系,如图 3-2 的方框图所示。 nts盐城工学院毕业设计说明书 2008 17 图 3-2夹紧装置组成的方框图 B夹紧装置设计的基本要求 a)夹紧过程中,不改变工件定位后占据的正确位置。 b)夹紧力的大小要可靠和适当, 既要保证工件在整个加工过程中位置稳定不变,振动小,又要使工件不产生于过大的夹紧变形。 c)夹紧装置的自动化和复杂程度应与生产纲领相适应,在保证生产率的前提下,其结构要力求简单,以便于制造和维修。 d)夹紧装置的操作应当方便、安全、省力。 C夹紧装置的选择 通常应用的夹紧装置有气压装置和液压装置两种,各有其优越性,要根据实际情况来选择用哪种装置。 a.液压装置 液压装置的特点是: a)液压油油压高、传动力大,在产生同样原始作用力的情况下,液压缸的 结构尺寸比气压小了许多。 b)液压油的不可压缩性可使夹具刚度高,工作平稳、可靠。 c)液压传动噪声小,劳动条件比气压的好。 但是,油压高容易导致漏油,液压元件的材质和制造精度的要求高,故夹具成本高。 b.气压装置 气压 夹紧装置 气源装置 中间传力机构 夹紧元件 工件 nts基于三维的变速箱壳体组合机床夹具设计 18 气压装置以压缩空气为力源,应用比较广泛,与液压相比有以下优点: a)动作迅速,反应快。气压为 0.5aMP时,气缸活塞速度为 110 /ms,夹具每小时可连续松夹上千次。 b)工作压力低(一般为 0.40.6aMP)。传动结构简单,对装置所用材料及制造精度要求不高,制造成本低。 c)空气粘度小,在管路中的损失较少,便于集中供应和远距离输送,易于集中操纵或程序控制等。 d)空气可就地取材,容易保持清洁,管路不易堵塞,也不会污染环境,具有维护简单,使用安全、可靠、方便等特点。 主要缺点是空气压缩性大,夹具的刚度和稳定性较差;在产生相同原始作用力的条件下,因工作压力低,其动力装置的结构尺寸大。此外,还有较大的排气噪声。 通过对以上两种夹紧装置优缺点的比较,结合加工工件的精度要求、工人的劳动强度和环境要求、企业的实际情 况,本设计中夹紧装置采用气压夹紧装置。 3.4.2 夹紧力的确定 A.夹紧力确定的基本原则 a.夹紧力的方向 夹紧力的方向应有助于定位稳定,主夹紧力应朝向主要定位基面。夹紧力的方向应有利于减小夹紧力。夹紧力的方向应是工件刚度较高的方向。 b.夹紧力的作用点 夹紧力的作用点应落在定位元件的支承范围内。夹紧力的作用点应选在工件刚度较高的部位。夹紧力的作用点应尽量靠近加工表面。 B.夹紧方案 根据以上要求及原则,工件属于箱体类零件,夹紧力的方向应垂直于最重要的定位基面是底面,并将工件压向该面,而不宜与其他方面进行 夹紧。由于工件为薄壁件,易受力变形,故采用多点同时压向工件,均匀分布压紧力,起到减少受力变形的效果。夹紧力为气压缸驱动。用推杆将压力传递至板,然后由压板将压力分散到工件压紧表面,从而将工件压紧。 C.夹紧力的预算: 根据工件所受切削力、夹紧力的作用情况,找出加工过程中对夹紧最不利的状态,来确定夹紧力。 根据文献 2P19 页查得夹紧力 Wk 的 计算公式如下 21 ffKPWk ( 3-4) 式中 K 安全系数; P 切削力; 1f 压板和工件表面间的摩擦系数; 2f 工件和定位支承块间的摩擦系数。 nts盐城工学院毕业设计说明书 2008 19 根据文献 2的表 2.2-1 查得安全系数 K 按下式计算 6543210 KKKKKKKK ( 3-5) 式中,0K6K为各种因素的安全系数, 0K 考虑工件材料及加工余量均匀性的基本安全系数,取0K=1.5; 1K 加工性质,取 1K 2.1 ; 2K 刀具钝化程度,取 2K =1.15; 3K 切削特点,取3K=1.2 4K 夹紧力的稳定性,取 4K 0.1 ; 5K 夹紧时的位置 ,取5K 0.1; 6K 仅有力矩使工件回转时工件与支承面的接触情况,取6K=1.0。 6543210 KKKKKKKK 5.1 5.2 查文献 2表 3-34 摩擦系数 1f , 2f 均为 0.16。 由于,右动力箱快进距离较左动力箱短,因此,先进 入工进阶段。右动力箱的钻削力方向指向夹具体左面的定位面,钻削力不影响工件定位。当左动力箱也进入工进时,两方向的钻削力相互抵消一部分,左动力箱钻削力稍大,因此,夹紧力只需要消除这部分力对工件定位的影响即可。 根据 2.2.2 节切削力的计算结果,取 P=左P-右P=2714.6-2487.2=227.4N, 由公式( 3- 6) 得: 21 ffKPQ ( 3- 6) =16.016.0 4.2275.2 =1776.5625N 3.4.3 气缸的选择 气缸的工作压力取决于工作气压和气缸的工作面积。工厂采同一气源,则其气压也就相对稳定,其工作气压为 1.0aMP。根据文献 814则气缸直径: D=pP4 ( 3-7) 式 中: p 气缸工作压力( Pa) 气缸的机械效率(取 0.80) P 气缸输出推力( N ) D 气缸直径( m ) 气缸输出推力应大于等于实际所需的加紧力 则取 P=1776.5625N nts基于三维的变速箱壳体组合机床夹具设计 20 代入公式 (3-7)得: D=pP4 =8.01015625.177646 =0.053m 本设计所用气缸采用通用件。根据文献 3668的表 3.4-18,选用气缸直径为100mm ,其工作推力产生的夹紧力可达到 3100N ;根据文献 3 668查表 3.4-18得另一辅助定位气缸直径为 50mm 。推力可达到 1000N 。 3.5 夹具体的设计 夹具体是用来将夹具的各个部分联结成整体的元件,它是夹具上最大的和最复杂的元件。在它上面要安装定位元件、夹紧装置、刀具引导件以及其它各种装置和元件。此外,在夹具体上还应有夹具在机床上安装用的定位部分,以保证夹具在机床上获得所需的相互位置,夹具体也是承受负荷最大的元件,承受着工作时的切削力、夹紧力等。 夹具体设计的基本要求有: a)有适当的精度和尺寸稳定性。 b)有足够的强度和刚度。 c)结构工艺性好。 d)排屑方便。 e)保证装卸工件方便。 f)在机床上安装稳定可靠。 本设计方案中的夹具体是由左右钻模板与夹具顶板构成的框架式夹具体,采用机械联结,具有良好的刚度,材料为 HT150,基本尺寸: 702 613 370mm,各安装面经铣削达到相应精度要求,左右钻模板的平行度不大于 0.02。底部设计排屑装置,具体见夹具装配图 BSXCT-03-03。 3.6 夹具三维设计 3.6.1 三维建模及三维软件介绍 三维建模从过程上讲就是在空间建立立体模型的一种方法。从结果上来讲,简单的说就是建立的模型具有空间感的,能看到上下前后左右的。“维”是几何学及空间理论的 基本概念。构成空间的每一个因素就叫做一维,普通的空间就是三维的。三维建模基于二维建模可以使构造的模型更具立体感和直观感,便于设计和加工。 目前,应用比较广泛的三维软件有 Pro/e、 SolidEdge、 UG等。设计中采用的三维软件是由美国 PTC 公司研发的 Pro/e wildfire3.0 软件。该软件包括了在工业设计和机械设计等方面的多项功能,还提供了目前所能达到的最全面、集成最紧密的产品开发环境。 nts盐城工学院毕业设计说明书 2008 21 3.6.2 基于三维的夹具设计过程 通过前面的计算和校核,可以得出夹具的尺寸大小,而且通过装配图及各零件图的数据,可以在 Pro/e 软件中画出各零件的三维模型,最后经组装后,可得到夹具的三维造型图。如图 3-3、 3-4、 3-5、 3-6、 3-7 所示。 图 3-3 夹具总装配图( 1) 图 3-4 夹具总装配图( 2) nts基于三维的变速箱壳体组合机床夹具设计 22 图 3-5夹具总装配图( 3) 图 3-6 夹具体装配图 nts盐城工学院毕业设计说明书 2008 23 图 3-7夹具右支架装配图 nts基于三维的变速箱壳体组合机床夹具设计 24 4 结论 本
- 温馨提示:
1: 本站所有资源如无特殊说明,都需要本地电脑安装OFFICE2007和PDF阅读器。图纸软件为CAD,CAXA,PROE,UG,SolidWorks等.压缩文件请下载最新的WinRAR软件解压。
2: 本站的文档不包含任何第三方提供的附件图纸等,如果需要附件,请联系上传者。文件的所有权益归上传用户所有。
3.本站RAR压缩包中若带图纸,网页内容里面会有图纸预览,若没有图纸预览就没有图纸。
4. 未经权益所有人同意不得将文件中的内容挪作商业或盈利用途。
5. 人人文库网仅提供信息存储空间,仅对用户上传内容的表现方式做保护处理,对用户上传分享的文档内容本身不做任何修改或编辑,并不能对任何下载内容负责。
6. 下载文件中如有侵权或不适当内容,请与我们联系,我们立即纠正。
7. 本站不保证下载资源的准确性、安全性和完整性, 同时也不承担用户因使用这些下载资源对自己和他人造成任何形式的伤害或损失。

人人文库网所有资源均是用户自行上传分享,仅供网友学习交流,未经上传用户书面授权,请勿作他用。