人人文库网 > 图纸下载 > 毕业设计 > 中型船式拖拉机(机耕船)传动系统设计【优秀含12张CAD图纸+Word全套机械毕业设计】
船式拖拉机(机耕船)及其传动系统概述--文献综述.doc
中型船式拖拉机(机耕船)传动系统设计【优秀含12张CAD图纸+Word全套机械毕业设计】
收藏
资源目录
压缩包内文档预览:
编号:450314
类型:共享资源
大小:5.80MB
格式:ZIP
上传时间:2015-07-06
上传人:小***
认证信息
个人认证
林**(实名认证)
福建
IP属地:福建
50
积分
- 关 键 词:
-
中型
拖拉机
机耕
传动系统
设计
优秀
优良
12
十二
cad
图纸
word
全套
机械
毕业设计
- 资源描述:
-
机械毕业设计 中型船式拖拉机(机耕船)传动系统设计
论文说明书共45页,字数总计:16617
资料简介:
A3-变速器第二轴.dwg
变速器第一轴.dwg
A3-变速器中间轴.dwg
A3-第二轴滑移齿轮.dwg
A3-动力输出从动齿轮.dwg
A3-动力输出主动轴.dwg
A3-二三档接合套(渐开线啮合套).dwg
A1-分动器装配图.dwg
A3-分动箱.dwg
A1-离合器装配图.dwg
A0-总装图.dwg
外文翻译.docx
外文翻译原文.pdf
毕业设计评审表.doc
中期检查表.doc
毕业论文.docx
文献综述.docx
开题报告书.docx
毕业设计任务书.docx
目 录
摘 要III
关键词III
ABSTRACTIV
KEY WORDSIV
1引言1
1.1课题研究的目的和意义1
1.2本课题的研究现状和发展趋势1
1.2.1研究现状1
1.2.2发展趋势2
1.3课题研究的主要内容3
2离合器的选用3
2.1离合器的功用和类型3
2.2动力输出轴4
2.3综合分析与选用5
3 传动方案设计5
3.1 变速器结构形式的选择5
3.2 分动器的类型选择7
3.3 传动方案的确定8
4 变速器设计9
4.1 初始设计数据10
4.2 总传动比计算与分配10
4.3 中心距的确定12
4.4 齿轮的设计计算13
4.4.1 齿轮参数13
4.4.2 各档齿轮及动力输出齿轮齿数的分配14
4.4.3 传动装置运动和动力参数的计算18
4.4.4 齿轮强度的计算与校核20
4.5 轴的设计计算25
4.5.1 变速器第一轴的设计25
4.5.2 动力输出主动轴的设计26
4.5.3 变速器第二轴的设计27
4.5.4 其他各轴最小直径的确定与轴承选择28
4.6 换挡结合套及操纵机构的设计28
4.6.1 啮合套的设计28
4.6.2 变速器操纵机构29
5 分动器设计30
5.1 设计初步分析30
5.2 传动装置运动和动力参数的计算31
5.3 齿轮设计32
5.4 轴的设计计算32
6 总结与讨论33
6.1 结论33
6.2 讨论34
参考文献35
致 谢37
中型船式拖拉机(机耕船)传动系统设计
摘 要
本文分析了本课题研究的目的及意义,对机耕船传动系统的发展现状与研究趋势进行了初步探讨。在对机耕船的作业环境以及农艺需求进行研究分析之后,进行了离合器的选型和动力输出方式的选择。在此基础上选择机耕船四驱传动系统中变速器与分动器的结构形式并确定了传动方案。依照所确定的传动方案,展开变速器与分动器具体结构以及内部零部件的设计计算,包括传动齿轮、轴以及换挡装置的设计。该四驱传动系统主要根据我国目前机耕船的发展现状而设计,为改善目前主要生产的后轮驱动三轮式机耕船,加大了牵引功率,四驱系统对深泥脚水田以及旱田的农艺适应性更强,提高劳动生产率,有利于减轻劳动强度。四轮驱动机耕船是今后机耕船的发展趋势。
关键词
机耕船;传动系统;变速器;分动器
ABSTRACT
This paper analyzes the purpose and significance of researching this project, and gives a preliminary discussion on the current development and research trends of transmission system of boat tractor. After analyzing the operating environment and the agronomic needs of the boat tractor, this paper shows the selection of clutch and the form of Power Take Off. On these basis, choosing the structure of gearbox and Sub-actuator in system of the boat tractor to determine the transmission scheme. According to the determined transmission scheme, expand the design of gearbox and Sub-actuator and the internal parts in them, including the design of the transmission gears, shaft and shifting device. This design of the four-wheel drive transmission system is primarily based on the current development status of the boat tractor in our Country, to improve the rear-wheel drive three-wheel boat tractor which is now being mainly produced. In this new transmission system, the traction power is increased and it enhances the tractor’s adaptability in the working environment, which can increase labor productivity and reduce labor intensity. The four-wheel drive boat tractor will be the trend of development in this field.
KEY WORDS
Boat tractor; Transmission system; Gearbox; Sub-actuator



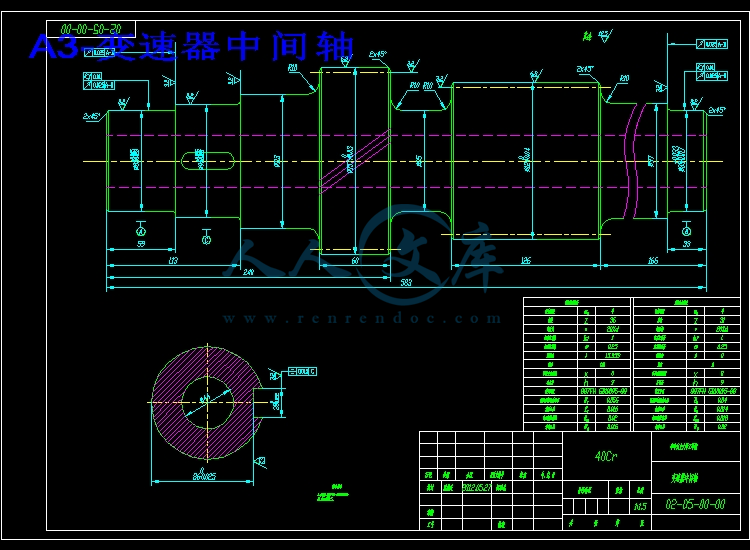
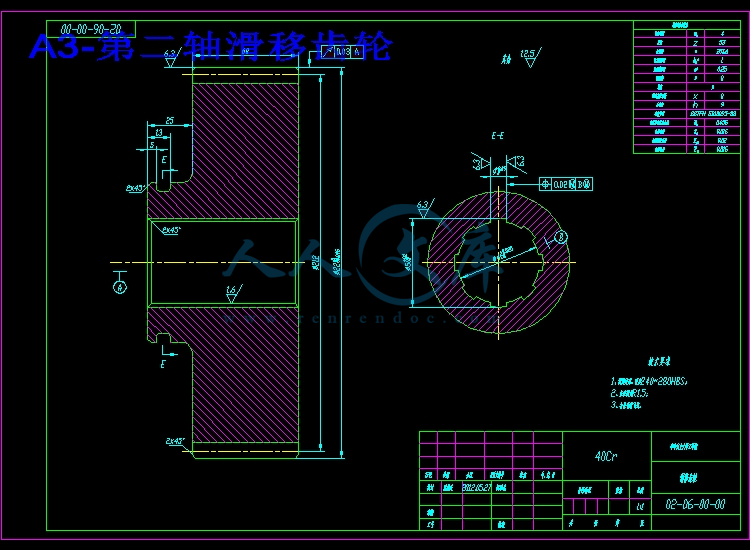



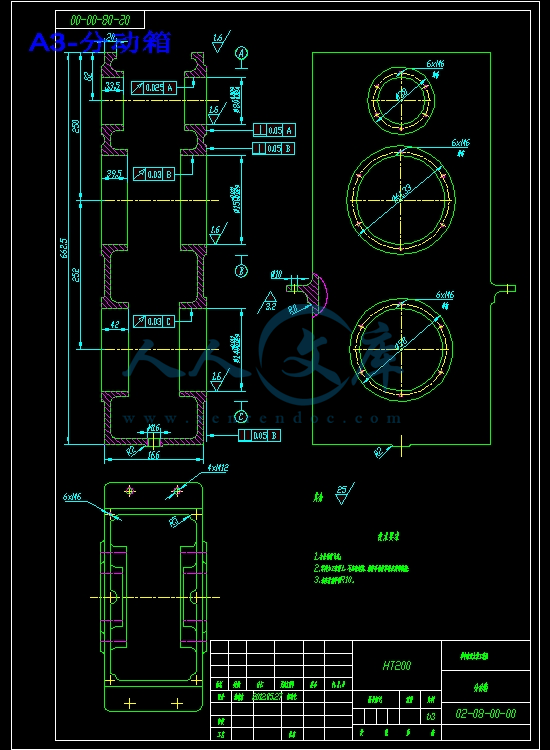




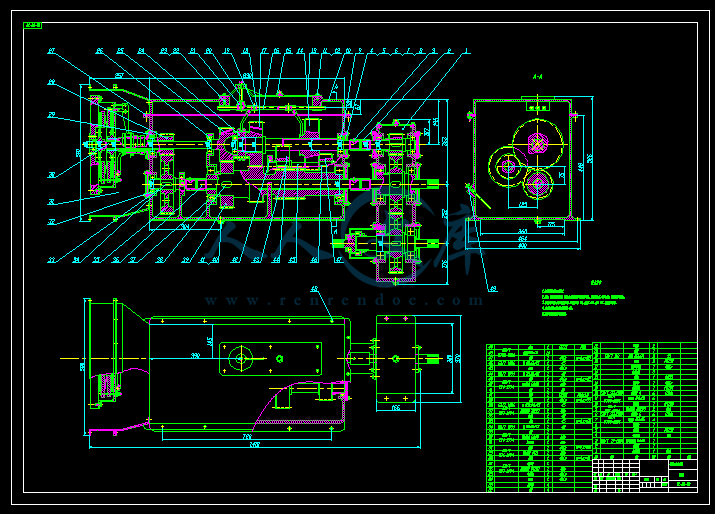
- 内容简介:
-
本科毕业设计 题 目 中型船式拖拉机(机耕船)传动系统设计 Transmission system design of medium-sized boat tractor (tractor-plowing boat) 二一二年六月ntsnts I 目 录 摘 要 . I 关键词 . I ABSTRACT . II KEY WORDS . II 1 引言 . 1 1.1 课题研究的目的和意义 . 1 1.2 本课题的研究现状和发展趋势 . 1 1.2.1 研究现状 . 1 1.2.2 发展趋势 . 2 1.3 课题研究的主要内容 . 3 2 离合器的选用 . 3 2.1 离合器的功用和类型 . 3 2.2 动力输出轴 . 4 2.3 综合分析与选用 . 5 3 传动方案设计 . 5 3.1 变速器结构形式的选择 . 5 3.2 分动器的类型选择 . 7 3.3 传动方案的确定 . 8 4 变速器设计 . 9 4.1 初始设计数据 . 10 4.2 总传动比计算与分配 . 10 4.3 中心距的确定 . 12 4.4 齿轮的设计计算 . 13 4.4.1 齿轮参数 . 13 4.4.2 各档齿轮及动力输出齿轮齿数的分配 . 14 4.4.3 传动装置运动和动力参数的计算 . 18 4.4.4 齿轮强度的计算与校核 . 20 4.5 轴的设计计算 . 25 4.5.1 变速器第一轴的设计 . 25 4.5.2 动力输出主动轴的设计 . 26 4.5.3 变速器第二轴的设计 . 27 4.5.4 其他各轴最小直径的确定与轴承选择 . 28 4.6 换挡结合套及操纵机构的设计 . 28 4.6.1 啮合套的设计 . 28 4.6.2 变速器操纵机构 . 29 5 分动器设计 . 30 nts II 5.1 设计初步分析 . 30 5.2 传动装置运动和动力参数的计算 . 31 5.3 齿轮设计 . 32 5.4 轴的设计计算 . 32 6 总结与讨论 . 33 6.1 结论 . 33 6.2 讨论 . 34 参考文献 . 35 致 谢 . 37 nts I 中型船式拖拉机(机耕船)传动系统设计 摘 要 本文分析了本课题研究的目的及意义,对机耕船 传动系统的发展现状与研究趋势进行了初步探讨。在对机耕船的作业环境以及农艺需求进行研究分析之后,进行了离合器的选型和动力输出方式的选择。在此基础上选择机耕船四驱传动系统中变速器与分动器的结构形式并确定了传动方案。依照所确定的传动方案,展开变速器与分动器具体结构以及内部零部件的设计计算,包括传动齿轮、轴以及换挡装置的设计。该四驱传动系统主要根据我国目前机耕船的发展现状而设计,为改善目前主要生产的后轮驱动三轮式机耕船,加大了牵引功率,四驱系统对深泥脚水田以及旱田的农艺适应性更强,提高劳动生产率,有利于减轻劳动强度 。四轮驱动机耕船是今后机耕船的发展趋势。 关键词 机耕船;传动系统;变速器;分动器 nts II ABSTRACT This paper analyzes the purpose and significance of researching this project, and gives a preliminary discussion on the current development and research trends of transmission system of boat tractor. After analyzing the operating environment and the agronomic needs of the boat tractor, this paper shows the selection of clutch and the form of Power Take Off. On these basis, choosing the structure of gearbox and Sub-actuator in system of the boat tractor to determine the transmission scheme. According to the determined transmission scheme, expand the design of gearbox and Sub-actuator and the internal parts in them, including the design of the transmission gears, shaft and shifting device. This design of the four-wheel drive transmission system is primarily based on the current development status of the boat tractor in our Country, to improve the rear-wheel drive three-wheel boat tractor which is now being mainly produced. In this new transmission system, the traction power is increased and it enhances the tractors adaptability in the working environment, which can increase labor productivity and reduce labor intensity. The four-wheel drive boat tractor will be the trend of development in this field. KEY WORDS Boat tractor; Transmission system; Gearbox; Sub-actuator nts 1 1 引言 1.1 课题研究的目的和意义 我国是农业大国,但传统的耕作方式相对落后,劳动生产率与作物产量都偏低,而农民劳动强度大,劳动繁重。因此农业机械化在农业可持续发展中起着巨大的作用,其中水田作业机械的地位尤为突出,而深泥脚水田机械化又是水田机械化中的一大难题(史滦平, 1990)。这种挑战下诞生了机耕船,突破了这一大难题。 传动系统是机耕船的一个重要 组成部分,布置在发动机和驱动轮之间。传动系统的可靠性直接关系到耕作的效果和生产效率以及驾驶员的操作舒适性( Mara Tanelli , Giulio Panzani ,2010)。机耕船自诞生以来至今,除发展初期有较大发展以外,近二三十年一直没有太大的发展,受全国范围内水田分布复杂等多方面原因影响,只是小批量小功率机型的生产。主打产品为后轮驱动三轮式机耕船。但随着科学技术以及农业技术农艺要求的发展,机耕船的发展开始渐渐出现脱节现象,产品供不应求,作业效率勉强满足要求。因此,机耕船急待进一步发展,而传动系统的改进是至关重要的一部分。本课题设计四轮驱动传动系统,旨在改进上世纪七十年代以来的两轮驱动式三轮小功率机耕船,提高机耕船的牵引动力性以及行驶通过性进而适应更加复杂的深泥脚水田或沤田作业,提高机耕船作业效率,提高劳动生产力,改善作业难度以及机耕船驾驶舒适性,降低农民劳动强度。四轮驱动在机耕船上的运用将是机耕船发展新的转折点,水田机械化的发展也将因此取得重大突破进而跟上现代农业发展的节奏。 1.2 本课题的研究现状和发展趋势 1.2.1 研究现状 所谓四驱技术,就是汽车前后轮都有动力,目的是使车辆按行驶路面状态的不同 将发动机输出扭矩按不同比例分布在前后车轮上,以提高汽车的行驶能力。在早期四轮驱动技术大多用在越野车上,现在很多轿车以及拖拉机也都越来越多的装备了这项技术。 nts 2 对于机耕船的研究,国外基本上还没有涉足。国内的机耕船诞生于上世纪六十年代,最早的是一台船形履带式沤田拖拉机,其传动系统非常简单,动力由一级皮带轮传动经两边撞块式离合器、减速箱传至行走机构( 武汉工学院拖拉机教研室机耕船研究室, 1980)。后来逐渐发展成拥有一个前端导向轮的后轮驱动机耕船,采用皮带轮传动,经减速箱至驱动轮,单边离合进行转向。八十年代以后至今, 机耕船的发展有所停滞,一直保持着小功率三轮皮带传动模式,皮带传动效率低功率损耗大,田间耕作效率也不是很高。最早的四驱机耕船是万县 -12 型四轮驱动机耕船,牵引力大、越野性好、能适应多种土壤( 武汉工学院拖拉机教研室机耕船研究室,1980)。但之后也没有其他机型的四轮驱动机耕船,说明四轮驱动机耕船的深入发展遇到严重阻碍,应用中仍然以三轮式为主。直到去年年底,湖北金驰机器有限公司试制出一台 JC-489 型四驱多功能机耕船,四驱机耕船的研究才有所突破,但仍处于初期阶段,有待更深入的研究发展。 1.2.2 发展趋势 进入 80 年代,随着国民经济的调整和农村经济体制的改革,机耕船的产销出现了较大幅度的下降(史滦平, 1990)。到现如今,产销虽有增幅,但也只是小批量订做式生产,水田作业提出的需求又是机耕船出现了供不应求的局面。这说明机耕船在水田机械化中仍具有强大的生命力。由此可见,机耕船的结构与质量改进与扩大规模生产迫在眉睫,机耕船的优点和它在水田机械化中的作用是不容忽视的。 机耕船传动系统的组成与结构与拖拉机相似,功用也基本相同,但由于机耕船机构简单,传动系结构相对拖拉机传动系简单。目前的机耕船传动系主要包括皮带传动、离合器、变 速箱、中央传动和最终传动五个部分( 武汉工学院拖拉机教研室机耕船研究室, 1980)。传动系可按传动比变化情况分为有极式传动和无级式传动,现有的机耕船绝大多数都采用有级式传动。目前机耕船主要是两轮驱动外加一个导向轮,随着机耕船的继续发展,机耕船已经逐渐向四轮驱动发展,可将拖拉机的传动系统运用到机耕船上,使得两者之间基本实现结构、原理通用,这样机耕船牵引能里增大,工作效率会进一步提高,将机耕船的发展推向新的阶段。 以往的历史表明,由于机耕船产品生产的批量上不去,直接影响了产品的质量、成本和生产厂的经济效益。经验表 明,机耕船中某些部件完全可以与拖拉机通用,nts 3 只是传动系负荷大小不同。目前亟待解决的问题就是要实现机耕船设计的系列化、标准化、通用化,提高机耕船的质量与生产批量,往更先进更实用的方向发展,进一步解放劳动力与提高劳动生产率。拖拉机零部件与机耕船零部件的通用性也将是一个极具发展前景的方向。最终实现在一条生产线上可以既生产拖拉机,又生产机耕船,这样就可以使生产厂的产量上去,对保证机耕船的质量和降低成本也有决定性的作用,这无疑是我国发明的机耕船得以继续发展的一条行之有效的途径(史滦平, 1990)。 机耕船是我国在解决水 田机械化中的一项卓有成效的发明,随着农业体制改革的深入,农业生产力进一步发展,机耕船必将在水田机械化事业中发挥更大的作用。 1.3 课题研究的主要内容 针对我国南方水田和旱地耕整的农艺要求,设计一种既可进行水田水耕,又可进行水田旱耕、旱田旱耕的四轮驱动中型船式拖拉机。设计的中型船式拖拉机具有动力输出装置,可在简易公路运输和田间作业转移,有 3 个前进挡位和 1 个后退挡位。其主要研究内容如下: ( 1) 根据功能要求,确定四驱传动方案; ( 2) 离合器的选择; ( 3) 变速器的设计计算; ( 4) 分动箱的设计计算; ( 5) 总装图、部装图、零件图的绘制。 2 离合器的选用 2.1 离合器的功用和类型 在汽车拖拉机传动系统中,离合器是与发动机直接关联的重要部件。离合器通常装在发动机与变速器之间,其主动部分与发动机飞轮相连,从动部分与变速器相连。离合器的主要功用是切断和实现发动机与传动系平顺的接合,确保汽车平稳起步;在换挡时将发动机与传动系分离,减少变速器中换档齿轮间的冲击;在工作中nts 4 受到较大的动载荷时,能限制传动系所承受的最大转矩,以防止传动系个零部件因过载而损坏(李文哲,许绮川, 2006)。 目前,用于车辆上的离合器主要有摩擦式离合器;液力耦合器;电磁离合器等三类。 汽车和拖拉机至今主要是广泛的采用摩擦式离合器,按其结构及工作特点又有不同的分类:按摩擦片数目分为单片式、双片式和多片式;按压紧装置的结构分为弹簧压紧式、杠杆压紧式、液力压紧式和电磁力压紧式;按摩擦表面工作条件分为干式和湿式;按离合器在传动系统中的作用分为单作用式和双作用式。 2.2 动力输出轴 本课题设计的是船式拖拉机传动系统,包含动力输出轴的传动与布置。动力输出轴一般都是布置在拖拉机的后面,也有布置在前面的。国家标准后置式动力输出轴离地高度在 500 到 700mm 范围内,并在拖拉机纵向对称面内左右偏差不得超过500mm(李文哲,许绮川, 2006)。轴端都采用八齿矩形花键。根据转速数,动力输出轴可分为标准式动力输出轴和同步式动力输出轴。 同步式动力输出轴的动力传动齿轮都位于变速箱第二轴之后,无论变速箱换入那个档速,动力输出轴的转速总是与驱动轮的转速“同步”,如上海 -50 等拖拉机上都具有同步式动力输出方式。同步式动力输出轴用来驱动那些转速需适应拖拉机行驶速度的农机具,如播种机和施肥机等,以保证播量均匀。同步动力输出轴的操纵由主离合器控制。 与同步式不同,标准式动力输出轴动力由发动机或经离合器直接传递,动力输出转速只取 决于拖拉机的发动机转速。根据标准式动力输出轴操纵方式不同,输出轴又可分为独立式动力输出轴、半独立式动力输出轴和非独立式动力输出轴三种。非独立式动力输出轴没有单独的操纵机构,它的传动和操纵都通过主离合器。半独立式输出轴的的传动和操纵由双作用离合器中的动力输出轴离合器控制,但操纵机构仍与主离合器共用,因此工作过程中不能单独停止动力输出轴的工作。独立式动力输出轴的传动和操纵都有单独的机构来完成,与主离合器的工作不发生关系。在采用独立式动力输出轴的拖拉机上装有一个主离合器和副离合器布置在一起的双联离合器,用两套操纵 机构分别操纵主副离合器。动力输出轴由副离合器控制,既可以改善拖拉机发动机因起步而导致的过大负荷,又能满足不同农机具的作业要求。 nts 5 2.3 综合分析与选用 目前,农用拖拉机基本上都是配用的双作用离合器,主副离合器分别控制传动系统和动力输出的动力。主要区别在于部分采用主副离合器用一套操纵机构按顺序操纵(联动双作用离合器),另一部分主副离合器用别用两套操纵机构操纵(双联离合器)。双联离合器之于联动双作用离合器,附加转动惯量小,发动机性能保持性好,操纵轻便灵活;离合器滑摩与发热指数同比减小,有利于提高可靠性;双作用状态稳定性差,但属于空载操作频次低,影响较小;操纵轻便省力,农艺适应好,具有相对优势(沈崇鑫, 1998)。 机耕船主要在深泥脚或沤田中工作,条件恶劣,因此就要求传动的农艺适应性好,操纵机构方便省力,提高操纵的舒适度。综合分析,选择动力输出轴独立控制的双联离合器。经过查阅文献资料,选用获得国家专利的东风 300 拖拉机独立操纵式双作用离合器。 3 传动方案设计 3.1 变速器结构形式的选择 本设计采用的是机械式变速器。机械式变速器又分为有级变速器和无级变速器。有级变速器与无级变速器相比,其结构简单、制造低廉,具有高的 传动效率( =0.960.98),因此在各类车辆上均得到广泛的应用。本设计选用有级式变速器。 有级变速器的传动效率与所选用的传动方案有关,包括传递动力的齿轮副数目、转速、传递的功率、润滑系统的有效性、齿轮及轴以及壳体等零件的制造精度、刚度等。变速器齿轮传动结构方案基本上有两种:通过一对齿轮变速的两轴式和通过两对齿轮变速的三轴式。 三轴式变速器如图 3-1 所示,其第一轴的常啮合齿轮与第二轴的各档齿轮分别与中间轴的相应齿轮相啮合,且第一、第二轴同心。将第一、第二轴直接连接起来传递扭矩则称为直接档。此时,齿轮、轴 承及中间轴均不承载,而第一、第二轴也传递转矩。因此,直接档的传递效率高,磨损及噪音也最小,这是三轴式变速器的主要优点。其他前进档需依次经过两对齿轮传递转矩。因此。在齿轮中心距(影响nts 6 变速器尺寸的重要参数)较小的情况下仍然可以获得大的一档传动比,这是三轴式变速器的另一优点。其缺点是:处直接档外其他各档的传动效率有所下降。 图 3-1 三轴式变速器 Fig.3-1 Three-axis gearbox 1 第一轴; 2 第二轴; 3 中间轴 两轴式变速器如图 3-2 所示。与三轴式变速器相比,其结构简单、轮廓尺寸小、布置方便等优点。轿车多采用前置发动机前轮驱动的布置,因为这种布置使汽车的动力 -传动系统紧凑、操纵性好且可使汽车质量降低 6%10%。两轴式变速器则方便于这种布置且传动系的结构简单。如图 3-2 所示,两轴式变速器的第二轴(即输出轴)与主减速器主动齿轮做成一体,当发动机纵置时,主减速器可用螺旋锥齿轮或双面齿轮;当发动机横置时则可用圆柱齿轮,从而简化了制造工艺,降低了成本。各档的同步器多装在第二轴上,这是因为一档的主动齿轮尺寸小,装同步器有困难;而高档的同步器也可以装在第一轴的后端,如图示。两轴式变速器没有直接档, 因此在高档工作时,齿轮和轴承均承载,因而噪声比较大,也增加了磨损,这是它的缺点。另外,低档传动比取值的上限也受到较大限制 ,但这一缺点可通过减小各档传动比同时增大主减速比来取消。 图 3-2 两轴式变速器 Fig.3-2 Two-axis gearbox 1 第一轴; 2 第二轴; 3 同步器 nts 7 对于发动机前置后轮驱动或者四轮驱动车辆上,变速器一般都采用三轴式,其结构布置最为典型。因此,本设计中变速器采用三轴式布置。变速器第一轴(输入轴)后端与长啮合主动齿轮做成一体,第二轴(输出轴)前端经轴承支承在第一 轴后端的孔内,且保持两轴线在同一条直线上,经啮合套将它们连接后可得到直接档。 变速器换挡方式有三种:滑移齿轮式,接合套式、同步器式。采用滑动齿轮滑档,结构简单、紧凑,容易制造。对于这种形式来说,大多采用直齿滑动齿轮的方案,它的缺点在于换挡时由于各档齿轮角速度不同而产生冲击,影响行驶安全性,要求驾驶者技术熟练(张炳力, 2011)。由于变速器第二轴与中间轴齿轮处于常啮合状态,所以可以用移动啮合套换挡,较滑移齿轮而言减少了啮合齿轮的磨损,延长了齿轮寿命,但不能消除冲击,适用某些要求不高的档位及重型货车变速器。使用同步器能保证迅速、无冲击、无噪声换挡,而与操作熟练程度无关,从而提高汽车的加速性、经济性和行驶安全性。通常运用于行驶速度较快以及档位速度差较大的车辆上。变速器中常采用以上三种换挡方式的两两组合。由于拖拉机作业与行驶速度较低,各挡速度差也较低,因此,本设计中长啮合齿轮传动的档位用啮合套来实现,一档和倒档采用滑移齿轮换挡。 3.2 分动器的类型选择 分动器的基本作用是,能在一般传动系统中通过它向外做功率输出。它主要用于多轴车辆,通过它吧发动机输出的动力合理的分配到各驱动桥。分动器一般布置在变速器之后,它的传动方 式通常为齿轮传动,因此它可兼具有副变速器的作用。故其结构上有许多方面和变速器有相似之处(徐石安, 2008)。 用于多轴传动车辆上的分动器结构基本有如下两类。 ( 1) 带轴间差速器的分动器。由于各驱动轴上的车轮转速(因轮胎气压、路面高低不一样等原因)不可能完全保持一致,装用了轴间差速器就能保证各驱动轴的转动不相互干扰。这样就避免了可能产生的轴间功率循环,使传动系零件超载、油耗增加和轮胎加速磨损等问题。但若用轴间差速器也有它的弱点,即若一旦一个驱动轴车轮发生打滑,则其他驱动轴将受其牵连,不能继续驱动车轮,此时需要用差速 锁锁住差速器。 nts 8 ( 2) 不带轴间差速器的分动器,如图 3-3 所示,其结构简单,使用可靠。虽然这种分动器容易引起轴间传动系功率的循环,但它一般用于四轮驱动汽车上。一般在公路上行驶时,不使前轮驱动,只有后轮驱动,避免了功率循环。只有当需要越野行驶时,才挂上前桥,让四轮全部驱动,以提高其通过能力。 图 3-3 分动器 Fig.3-3 Sub-actuator 本设计为船式拖拉机传动系统,田间作业复杂,综合比较以上两种分动器形式,选择不带轴间差速器的分动器。田间作业时挂上前桥,四轮驱动,运输作业时只需后桥驱动,避免功率循环 。 3.3 传动方案的确定 本课题研究的传动系统主要包括离合器、变速器以及分动器。根据设计要求,需设置三个前进挡和一个倒档,并且工作机为四驱。离合器将发动输出的动力分配给变速器和动力输出轴,变速器实现设计中的档位要求并将动力传递给分动箱,分动箱将动力分配给前后驱动桥并起副减速作用。再根据变速器与分动器的选型确定本设计传动方案。 下图为本设计传动系统简图: nts 9 图 3 4 传动路线 Fig.3-4 Transmission route 1.变速器第一轴常啮合齿轮 2.中间轴常啮合齿轮 3.变速器第二轴 II 挡空套齿轮 4.中间轴挡齿轮 5.变速器第二轴 I、倒档滑动齿轮 6. 中间轴 I、倒挡齿轮 7、 8.倒挡中间齿轮 9.动力输出主动齿轮 10.动力输出被动齿轮 11.分动箱主动齿轮 12.分动箱中间齿轮 13.分动箱被动齿轮 A.离合器 B.分离轴承 C.动力输出主动轴 D. 变速箱第一轴 E、 O.接合套 F.变速器第二轴 G.滑动齿轮 H.连接套 I.分动箱第一轴 J.变速器 中间轴 K.分动箱中间轴 L. 动力输出轴 M.倒档轴 N.箱体 P.分动箱第二轴 Q.万向联轴器 该传动系统中,离合器为主副独立控制。变速器为三轴式,齿轮 1 与第一轴制成一体,齿轮 3 空套在第二轴上,齿轮 5 是采用花键连接并能通过操纵结构轴向滑动的 I、倒档公用的从动齿轮,齿轮 6 是与中间轴制成一体的 I、倒档公用的主动齿轮。分动箱第二轴上的接合套可以通过操纵机构实现工作机在四驱与两驱之间转换。 4 变速器设计 根据传动方案的设计,动力输出 的布置与传动与变速器结构与传动密切相关,因此动力输出装置与变速器一同设计。 nts 10 4.1 初始设计数据 ( 1)发动机:见表 4-1; ( 2)水田轮半径 R0=450mm,胶轮半径 r=450mm; ( 3)传动效率:见表 4-2; ( 4)根据设计要求,变速箱三个前进档一个倒档。动力输出设一个档,动力输出轴取标准值 720r/min。根据农艺要求初选各档速度:见表 4-3。 表 4-1 发动机参数 Table 4-1 Engine parameters 型号 额定功率 /转速 kw(ps)/(r/min) 柴油机怠速 (r/min) 最大扭矩 /转速 (N.m)/(r/min) D226B 3 37(50)/2200 700 50 193/1440 1660 表 4-2 传动效率 Table 4-2 Transmission efficiency 离合器(平摩擦传动))( 离 滚动轴承 (滚) 圆柱齿轮传动( 6、 7 级精度)( 齿 0.850.92 0.99 0.980.99 表 4-3 格挡行驶速度 Table 4-3 Speed of each stalls 档位 I 档 II 档 III 档 倒档 行驶速度 (km/h)/(m/s) 5.4/1.5 9/1.5 12.6/3.5 21.6/6 4.2 总传动比计算与分配 传动系总传动比是根据农艺要求的机耕船速度来确定的。用驱动水田轮顶圆半径 R0 的某档水田计算速度 Vj 与总传动 比的关系是: nts 11 1 0 0 06020 ienj inRV 因此,总传动比应为 jeni V Rni 0337.0( 4 1) 式中 Vj 某档的计算速度( km/h); nen 发动机标定转速( r/min); R0 水田轮顶圆半径( m)。 根据式( 5 1)算得: i 倒 =69.12; i =41.45; i =29.62; i =17.28。 在确定了传动方案和总传动比后, 需要把总传动比合理的分配到各个传动部件上。系统总传动比 i i 等于各部件传动比之乘积,即: mzbii iiii ( 4 2) 式中 ibi 变速箱第 i 档传动比; iz 中央传动的传动比; im 最终传动的传动比。 在不使变速箱过于增速的情况下,传动比分配应按前小后大、前密后疏的原则来确定。即在结构布置允许的条件下,尽量的把最终传动、中央传动的传动比取大些,是零件数目较多的变速箱有较小的工 作载荷和较小的重量,已达到减轻整机重量的目的。 根据上述原则,参照一些机耕船的数据, iz 和 im 大致在下列范围内; 单级最终传动时 im=2.55; 两级最终传动时 im=58.5; 中央传动传动比 iz=2.35.5。 因为本设计中变速器的结构为中间轴式,设有直接档,即 档,从而变速箱三档传动比 nts 12 ib =1, 得到 28.17bmz iiii , 根据式( 4 2)计算得到: ib 倒 =4; ib =2.339; ib =1.714。 再根据分配原则,取中间传动传动比 iz=3,从而最终传动传动比 im=5.76。 将以上算得的结果列表,如表 4-4 所示。 表 4-4 传动比分配 Table4-4 Transmission ratio distribution 档位 变速箱传动比 中央传动比 最终传动比 总传动比 档 1.714 3 5.76 41.45 档 2.339 29.62 档 1 17.28 倒档 4 69.12 动力输出传功比为 056.372022000 i 4.3 中心距的确定 对中间轴式变速器,中心距 A 是指中间轴与输出轴(第二轴)轴线之间的距离。该基本参数的大小不仅对变速器的外形尺寸、体积和质量大小有影响,而且对齿轮的接触强度有影响。 可根据经验公式初选中心距 A,即 3 1m a x geA iTKA ( 4 3) 式中 A 为变速器中心距( mm); nts 13 KA 为中心距系数,乘用车取 KA=8.99.3,商用车 KA=8.69.6,多档变 速器KA=9.511; Temax 为发动机最大转矩( N.m); i1 为变速器一档传动比; g 为变速器传动效率,取 0.96(张炳力, 2011)。 取 KA=11,则,根据式( 4 3)得 95.8396.03 9 9.21 9 311 3 A mm 该数值仅作为参考,乘用车变速器中心距在 6585mm 范围内变化,而商用车的变速器中心距在 80170mm 范围内变化。原则上总质量小的车辆,变速器中心距也小些。由于本设计为机耕船传动系中的变速器,与拖拉机类似,行驶速度 低,总传动比大,传动件承受载荷更大,因此在商用车变速器中心距范围内选择。本设计中取A=168mm。 4.4 齿轮的设计计算 档位高的齿轮采用常啮合齿轮传动,一档和倒档采用滑动直齿轮传动。 4.4.1 齿轮参数 ( 1)模数 m 齿轮模数是一个重要参数,并且影响它的选取因素有很多,如齿轮的强度、质量、噪声、工艺要求等。变速器低档齿轮应选用大些的模数,其他档位选用另一种模数。一些情况下变速器各档齿轮选择相同的模数。本设计中齿轮模数初定为 4mm。 接合套的接合齿多数采用渐开线齿形,本设计中,接合套模数初选为 3mm。 ( 2)压力角 遵照国家规定取齿轮压力角为 20 ,接合套压力角为 30 。 ( 3)螺旋角 为了不使轴承受过大的轴向力,斜齿圆柱齿轮传动的螺旋角不宜选得过大,常在 208 时间选择(濮良贵、纪名刚, 2006)。 nts 14 ( 4)齿宽 b 齿宽对变速器的轴向尺寸、齿轮的工作平稳性、齿轮强度和和齿轮工作时的受力程度等均有影响。选用较小的齿宽可以缩短变速器的轴向尺寸和减轻重量,但齿宽减少使斜齿轮传动平稳的优点被削弱,齿轮的工作应力增加;选用较大的齿宽,工作时会因轴的变形导致齿轮倾斜,使齿轮沿齿宽方向受力不均并在齿宽方向磨损不均匀。齿宽在进行齿轮强度校核的时候再进行选择。 ( 5)齿顶高系数 f0 齿顶高系数值取为 1.0。 4.4.2 各档齿轮及动力输出齿轮齿数的分配 确定变速器各档齿轮齿数时应考 虑: 符合动力性、经济性对各档传动比的要求; 最少齿数应至少不产生根切(否则应考虑设计变位齿轮传动); 为使齿面磨损均匀,相互啮合的齿轮齿数互为质数; 齿数多,可降低齿轮传动噪声。 变速器传动方案如图 4-1,下面进行各档齿轮齿数分配。 图 4-1 变速器传动方案 Fig.4-1 gearbox transmission scheme ( 1)确定一档齿轮的齿数 一档传动比 6152zz zzib ( 5 4) 如果 z5、 z6 的齿数确定了,则 z2 与 z1 的传动比可求出,为了求 z2、 z1 的齿数,先求nts 15 其齿数和 zh: mAzh 2( 5 5) 因模数 m=4mm,从而 8441682 hz。 中间轴上的 一档小齿轮的齿数尽可能小些,以使 z5/z6 的传动比 大些在 ib 一定的条件下,的传动比可分配小一些,使第一轴常啮合齿轮的齿数多些,一边在其内腔设置第二轴的前轴承并保证轮辐足够的厚度。 取 z6=53, z5=zh-z6=53。 ( 2)对中心距进行修正,因 zh 刚好是整数,无需修正。 A=168mm 作为各档齿轮齿数分配的依据。 ( 3)确定常啮合齿轮副的齿数 初选螺旋角 14 。 由式( 4 4)求出常啮合传动齿轮的传动比 403.15612 zzizz b ( 4 6) 而常啮合传动齿轮的中心距和一档齿轮的中心距相等,即 co s2)( 21 zzmA n ( 4 7) 解方程式( 4 6)和( 4 7),取 z2=46, z1=33。 核算一档传动比 382.26152 zz zzi b , 与原传动比 2.399 相差不大,无需调整。再根据 z1、 z2 算出螺旋角 值 868.192 )(a r c c o s 212 A zzm n ( 4)确定二档齿轮的齿数 初选螺旋角 14 。 当螺旋角 4 与 2 不同时,有 nts 16 714.14132 zz zzi b ( 4 8) 而 1 68c os2 )(443 zzmA n mm ( 4 9) 此外,从抵消或减少中间轴上的轴向力出发,并按端面参数计算可得 )1(t a nt a n432124242 zzzz zrr ( 4 10) 联解以上三个方程式可求出3z、 4z 和 4 三个参数。采用试凑法,先选定螺旋角4 ,求出 3z 、 4z ,再带回式( 4 10)检查至符合要求为止。 取 453 z, 364 z ,带回算得 358.154 。 带回式( 4 10)得 3157.1358.15t a n 868.19t a nt a nt a n42 3101.1)1(43212 zzzz z两数值相差很小,可不再调整。 核算二档传动比 74.14132 zz zzi b 与原传动比 1.714 相差不大,无需进行调整。 ( 5)确定倒档齿轮齿数 倒档布置方案如图 5-2,齿轮 5 为 、倒档滑动齿轮,与齿轮 6 啮合挂入一档,与齿轮 8 啮合挂入倒档。齿轮 5 与齿轮 6 啮合时要保证齿轮 5 与齿轮 7 齿顶间的间隙,但实际上 z7 大于 z8,从而该齿顶间隙不能保证。为解决此问题,将中间轴上的 、倒档齿轮做成一体,即将齿轮 6 宽度加大,安装时齿轮 7 与齿轮 6 左端保持常啮合,挂入以当时齿轮 8 与齿轮 6 右端啮合,从而保证齿轮 5 与齿轮 7 不产生干涉。设齿轮 6、 7 的中心距为 A1,齿轮 5、 8 中心距为 A2。因为齿轮 5、 6 的模数为 4mm,nts 17 从而齿轮 7、 8 的模数也应为 4mm。 图 4-2 倒档布置方案 Fig.4-2 Reverse layout 倒档传动比为 4861572 zzz zzzi 倒 ( 4 11) 代入已知数值得到 678.187 zz 根据齿数选择的原则,取 z7=42, z8=25。 从而 mmzzmA 1462 )( 761 ( 4 12) mmzzmA 1562 )( 852 ( 4 13) ( 6)动力输出齿轮齿数的确定 动力输 出的减速传动采用直齿轮传动。由于本设计结构的要求,动力输出主动轴与从动轴的中心距和变速箱中心距同,即 mmzzmA 1682 )( 109 ( 4 14) 取模数 m=4mm,又因 i 倒 =3.056 nts 18 得到 z9+z10=84, 取 z9=21, z10=63。 动力输出传动比调整为 3倒i。 4.4.3 传动装置运动和动力参数的计算 ( 1)各轴转速 动力输出主动轴 min )/(22001 rn 动力输出从动轴 mi n )/(3.73322001092 rzzn 变速器第一轴 min )/(22003 rn 变速器中间轴 mi n)/(3.15 7822 00214 rzzn 变速器第二轴(一档) mi n)/(1.92 322 0052615 rzz zzn 变速器第 二轴(二档) mi n )/(6.1 2 6 22 2 0 032415 rzz zzn 变速器第二轴(三档) min )/(22005 rn 变速器第二轴(倒档) mi n )/(5.5 4 92 2 0 05728615 rzzz zzzn 变速器倒档轴 mi n)/(11 6522 0072616 rzz zzn ( 2)各轴功率 动力输出主动轴 )(3.331 kwPP e 离动力输出从动轴 )(3.322 kwPP e 齿滚离 变速器第一轴 )(3.3313 kwPP nts 19 变速器中间轴 )(3.3224 kwPP 变速器第二轴(一、二档) )(345.31225 kwPP e 齿滚离 变速器第二轴(三档) )(9 6 7.325 kwPP e 滚离 变速器第二轴(倒档) )(4.30335 kwPP e 齿离 变速器倒档轴 )(345.31226 kwPP e 齿滚离 ( 3)各轴扭矩 动力输出主动轴 ).(55.1449华中农业大学本科毕业论 文 (设计 )中 期进展情况检查表 2012 年 3 月 20 日 课题名称 中型船式拖拉机(机耕船)传动系统设计 学生姓名 沈瑞东 学 号 2008307202893 专 业 农业机械化及自动化 指导教师 夏俊芳 职 称 教授 主要研究内容及进展 主要研究内容 针对我国南方水田和旱地耕整的农艺要求,设计一种既 可进行水田水耕,又可进行水田旱耕、旱田旱耕的中型船式拖拉机。设计的中型船式拖拉机具有动力输出装置,可在简易公路运输和田间作业转移,有 3个前进挡位和 1个后退挡位。 进展 查阅并学习相关资料,完成了任务书、外文翻译、开题报告以及文献综述; 拟定并论证了传动方案,初步计算了各档总传动比及其分配,绘制了传动路线图 ; 尚须完成的任务 零部件性能和结构计算 ; 零部件草图绘制及修订 ; 完成总装图及零件图的绘制 ; 撰写设计说明书及修改设计图样 ; 整理资料准备毕业答辩 ; 存在的主要问题及解决措施 主要问题 由于传动要求的非通用性,变速箱与分动箱不能进行选用; 解决措施 自行设计计算,选用齿轮进行组合装配; 指导教师审查意见 nts 1 / 19 题 目 动力换挡农用拖拉机的传动控制设计与最终自动调整 二一二 年 二 月 nts 2 / 19 动力换挡农用拖拉机的传动控制设计与最终自动调整 Mara Tanelli , Giulio Panzani , Sergio M. Savaresi , Carlo Pirola a Dipartimento di Elettronica e Informazione, Politecnico di Milano, Piazza L. da Vinci, 32, 20133 Milano, Italy b SAME Deutz-Fahr Group, Viale F. Cassani, 15, 24047 Treviglio (Bergamo), Italy 摘 要 : 本文涉及大功率变速农用拖拉机传动控制系统的分析和设计 。具体地说,对所有涉及单离合器与双离合器正确操纵换档的临界情况都进行了研究,并提出一个在所有操纵条件下能提供良好换挡性能的操控系统。深入来讲,为了适应元件公差及其在生产线上的普及,为传动控制系统中的最终调节提出了一个自动程序,用于对换挡质量进行客观分类并对其进行自动优化。该方法的适宜性在仪表化的车辆上做了彻底的测试。 关键词 :动力换档变速器 农用拖拉机 汽车系统 最终调整 一、 简介与动机 农用车要应对的工作条件比其他经验丰富的地面车辆复杂与艰巨 得多 10。事实上,农用车本质上是作为低速行进而提供大牵引力车辆而设计的。此外,在不平坦的土壤上轻易地移动使它们同样适合重型拖车运输。为保证个速度在运用中的最大灵活性以及在工作环境下充分利用发动机的最大功率,如今农业车辆往往配备了一个被称为动力换挡变速器的设备。这种变速器含有大量的齿轮(通常从 9 到 30)并且能够通过执行档使发动机与驱动轮之间没有(或者至少最小)功率损失。 通常,一个动力换挡变速器的特点是存在 2 个或更多(取决于齿轮的数量以及变速箱整体机械结构)连接到液压回路的湿离合器,液压回路的压力受比例电 磁阀控制。考虑到齿轮数量之大以及要达到最佳换挡的事实,正确的处理好一些控制变量是必要的,以使这种变速器得到适当的控制。 nts 3 / 19 设计出如此的一个控制系统不是一件简单的事情。在科学文献中,有一些处理基于路面车辆的动力换挡或者双离合器传动控制的研究,例如, 3-8,15,但是关于农用拖拉机的具体解决方案基本没有。这主要是因为广泛的工作条件以及变化的车辆载荷使农用车具有独特的性能规范,这种独特的性能规范就使得农用车最优换挡的定义不同于其他路面车辆。事实上,主要的限制因素是重复性的操作以及在所有作业路面上司机的舒适度,例 如从沥青泊油路到粗糙的越野地形。另外,拖拉机上的载荷分布与其他车辆有很大的不同,产生这些不同的原因可能是前面或者后面的附加载荷,而这些附加载荷源于不同作业任务所使用的各种作业设备。最后,还要注意变化的操作条件往往是无法用车载传感器测量的,因此需要功能强大的而且容易调节的变速控制器。这些事实使得在农用拖拉机上保证最优且可重复的换档这一问题成为一项非常具有挑战性的任务。 设计一个有效的传动控制系统,首先要确定影响换档品质的重要参数,例如, 2,16。此外,该变速控制系统必须最佳地处理好以下相冲突要求之间的平衡 : ( 1)、舒适换档; ( 2)、保证换挡过程中传到驱动轮的功率无损失; ( 3)、车辆传动寿命周期中造成最小的的机械零件磨损; 此外,在工业背景下,一旦控制设计段完成而且控制系统成为最终产品,便开始进入处理结构公差与扩大生产的最终调整阶段,这一阶段使得最终系统不同于原始系统并用于控制验证和测试。因此,这一阶段是针对控制参数进行优化,从而保证预期的换挡性能在所有的车辆上得以实现。通常这一阶段是进行人体测试,测试者根据个人驾驶喜好与驾驶经验对控制参数进行调整。因此,最终调整很明显是一个关键而又艰难的阶段。事实上, 由于没有客观的指数来评估换挡性能与舒适度,一个换档机构可能会被一个操作者认为是舒适的,但对另一个操作者来说却不是:这就意味着最终的调整可能导致不同车辆上同型换挡机构截然不同的换档行为。值得注意的是,换档nts 4 / 19 特性是车辆操纵品质的一个重要组成部分,而车辆操纵品质往往被看做是制造商的商标,提供具有相同操纵特点车辆的能力可以成为使客户满意并提升顾客对该品牌忠诚度的关键。另外,该种建议性做法的另一个显著优点在于减少与最终调整有关的工业成本,这种成本的减少是通过减少每辆车调整说需要的换档次数以及使该调整程序自动化,因此就不 需要经验丰富的操作者来完成了。 值得注意的是,该项工作中所提出的方法在超出所研究问题之外的方面仍具有有效性,尽管它最初是针对一个特定的应用,例如,上述所提到的设计步骤构成了一个可行的范例,可应用于许多不同的生产情况。事实上,本文是旨在使具有控制系统的工业应用中的最终调整正式化的贡献之一,针对所考虑的问题提出系统的方法。在这反面,文献 13, 16中的结论提供了上述方法论的其他应用,分别解决了通过数据量化驾驶风格与安全、农用拖拉机设计与客观地调整运动反演控制的问题。尽管相对于本文所考虑的问题有所不同,但两者共 享(所有或者部分)该项目所提出的体统方法,该方法由以下四个步骤构成: 建立定义目标系统质量的性能特性评价; 通过灵敏度分析实验指出待优化特征与重要变量之间的关系; 定义成本函数; 控制算法设计与成本函数优化基础上的最终调整程序的设计。 对于所有上述那些应用,这一方法论使得本文中的结论成为大众爱好,在这些应用中,必须设计并调试好一个控制系统用于解决生产扩大与公差中的离散问题,这些离散问题使得潜在设备(例如,最终车辆)不同于作为设计目的的设备。由此产生的研究方向需要控制理论与优化设计方面的工具,并结合具 体应用领域的知识。这里所提出的结论是基于米兰理工大学与道依茨法尔集团研发部的一项共同的研究项目( SAME, Lamborghini, Deutz-Fahr,Hrlimann, Adim Diesel and Deutz AG)。工作都集中在一个为大功率( 200 马力)农用拖拉机设计的动力换挡变速器上(见图一)。 nts 5 / 19 第一步致力于定义恰当的成本函数已经完成,该成本函数考虑了对换档舒适度与换挡品质的客观评估。然后,对所有相关的换档动力进行准确分析从而设计出一个简单而有效地传动控制策略。最后,为了在每辆生产车上获 得尽可能最好的换挡性能,提出自动调整阶段以保证令人满意的和可重复的换挡性能。 本文结构如下。第二部分液压与机械的角度介绍动力换挡传动系统。第三部分旨在介绍用来评价换挡质量的性能指标。第四部分介绍所推荐的动力换挡控制策略,无论是对单离合器换档还是对双离合器换档,还有与控制参数相关的性能指标灵敏度分析实验结果。最后,第五部分主要介绍最终自动调整和相关的实验结果。 二、 系统介绍 图二描述了动力换挡变速器的整个机械布局。如图所示,动力从发动机(图二的左边)依次通过两个不同的齿轮箱(由三个不同齿轮构成的 HML 组和由三个不 同比例大小齿轮构成的 123 组)流向驱动轮。该变速器还包括其他两部分,即运动逆变器和模式选择器。运动逆变器(见 11,16)是由两个离合器构成的电液系统,该系统可执行自动运动逆变,例如,司机仅仅动一下操纵杆就能使车辆从前进速度变成反向速度。模式选择器有三种不同的工作模式,即爬行模式、工作模式和运输模式,这些模式只有当拖拉机静止的时候才能改变。接下来,我们致力于换挡控制并且只考虑两个齿轮箱,同时假设没有进行运动逆变(注意,顺便提一下,在运动逆变时司机不能使nts 6 / 19 用操纵杆)并且一种固定的模式已经投入工作。 由于两个齿 轮箱是串联的,发动机与驱动轮之间有九种不同的传动比(不考虑比例固定部分的最终差别)。从概念上讲,虽然这两个齿轮箱存在机械上的不同,但对于控制设计目的的作用却是一样的。每个齿轮都与一个湿式离合器相连:要选择一个特定的齿轮,相应的离合器必须完全接合,使得由发动机传出的扭矩完全通过离合器传递。该项目中所使用的都是多盘湿式离合器,为了能够正常工作(以及以后选择相应的齿轮),摩擦盘表面之间必须紧密结合并且相互之间的的正压力要足够大以产生足够的摩擦力来保证摩擦盘之间不会产生相对滑动 。 图三是摩擦盘 间正压力与离合器油压之间具体关系的示意图。对于变速分析,必须考虑三个不同的区段。第一阶段(即,来自于大气压力),压力的增加对摩擦盘之间的正压力不产生影响。 当增加到所谓的转折点压力(见图三),相互之间距离减小为零的摩擦盘开始接合。从此点开始,正压力成比例的增加。在这一阶段,摩擦盘之间的摩擦力能够传递一定的传入扭矩,但是由于摩擦盘间存在一定的相对滑动,没有确定的传动比。 一旦达到工作压力(如图三),正压力已经足够大以至于离合器摩擦盘之间不存在相对滑动从而保证了精确的传动比。 nts 7 / 19 图四为液压系统示意图,该图解 释了离合器中的压力是如何被控制的。一个比例电磁阀控制六个定向启闭阀将每个离合器与掌控液压连接起来。该液压结构产生了如下离合器行为:当定向阀门开启时,离合器上的压力与主压力相等。由于这是一个单向阀,可知压力只能上升,尽管压力压力会降低。相反的,当定向阀关闭,离合器上的压力为零。因此,可用的控制变量如下: (1) 主液压力。注意,由于没有压力传感器,真正的控制变量就是电磁比例阀。这样的一个变量可以通过静态图与输出压力相连。接下来,我们将该压力视为控制变量,并切记上述所提到的电流到压力的转化必须完成; (2) 每个定向阀的启闭状 态。 为了用动力换挡变速器实现换档,将脱出离合器上的压力必须为零,而传入离合器上的压力必须为最大。注意,非动力换挡变速器是先使将脱出离合器脱出啮合然后再让传入离合器进入啮合,这样一来就存在一个时间间隔,在这一时间间隔内车辆处nts 8 / 19 于中间状态并且发动机传出的扭矩无法传递到驱动轮。在农用车辆中,这种中间状态是必须要避免的,因为超大负荷会导致停车。因此,保证换挡过程中有连续的扭矩传递到驱动轮是极其重要的,这是动力换档变速的一个主要特征。 为了对该系统描述进行总结归纳,表一列出了九种可用的齿轮组合以及与之相啮合的离合 器。可以看到,通常换档只需要变动一个离合器(例如,齿轮箱 HML 中的一个)。我们将这种换档称之为单离合换档。然而,当要在三档与四档或者六档与七档时间转换时就必须变动两个离合器(一个属于齿轮箱 HML,一个属于齿轮箱 123),使得下面将要描述的换挡控制器的设计更加复杂。我们将这种换档称为双离合器换档。 三、 换挡质量评估 正如第一部分所讨论的那样,定义一个客观地换挡质量评估会产生如下好处: ( 1) 为换档性能给出了一个特别而客观地指标,有助于比较不同的车辆和(或)不同的控制算法。 ( 2) 依靠适当性能指标的自动优化,最后调整阶段相 对容易和更少的资金投入。 定义最合适成本函数的关键问题在于决定被测信号与换档舒适度以及换档品质之间有意义的关系。一些在汽车方面进行的研究,在通过加速度测量评估舒适度方面显示出良好的研究结果,例如 9, 14。对于该项目中所考虑的类型车辆,很明显上述文献中的信号是不合适的,这是因为土壤引起的测量噪声掩盖了换档对车辆加速度的实际作用。此外,加速器并不是农用拖拉机上的车载标准传感器。因此,我们致力于nts 9 / 19 研究换挡品质与车辆速度的关系,车辆速度的测量通常可以通过车轮编码器获得。正如文献 16中所讨论的,这种信号可以用来 进行符合要求的舒适度评估。 为了理解质量指标设计的逻辑依据,图五展示了在三种不同换档情况下车辆速度与时间的关系,三种性能由一名专业司机评断:第一种(图五 a)被分为优秀级别,而剩下两种(图五 b 和 c)分别被分为中等级别和较差级别。上述三种换档情况下的速度性能如下:速度总是从一个恒定值增加(所有情况中都必须换高档)到一个较高的最终值,因为在换挡过程中发动机保持恒定且连续的转速,该终值只取决于最终传动比。真正使这几种换档产生不同的是速度提高时的平稳度。注意,事实上,换档品质好的图五 a 中,速度沿着平滑的斜线上升,而换 挡质量中等的情况下速度的提高只是分段线性的(如图五 b 椭圆框中的部分)并且在速度提高阶段有明显的初始负向脉冲。最后,换挡品质差的情况中速度特性非常不规则并伴随巨大的速度波动(如图五 c 中椭圆框中的部分)。 nts 10 / 19 基于这些考虑,性能指标被定义为: 该公式中, tvm 表示被测轮速, tvref 表示描述最优换当中速度特性的参考信号。被测轮速表示为: 式中 4,.,1, iti 是通过车轮传感器测得的车轮角速度, 4,.,1, iri 是车轮半径。 参考信号 tvref 被设计成有三部分组成(如图六)。第一部分由运动开始时的恒定速度,即 式中 reqt 表示司机换挡的时刻。运动最后的参考速度也是恒定的,表示为: 式中 reqeng t 是换档开始时的发动机速度(再次强调,换档过程中发动机速度是恒定且连续的), r 是车轮的平均半径, inc 是输入齿轮的传动比(当换档是由司机完成时,它也是已知的)。 在上述两个速度限制之间变化的参考速度被定义为 2refv ,趋于线性,表示为: nts 11 / 19 式中 1t 定义为: 即, 1t 是被测速度比初始参考速度 1refv 小的最后时刻,而时刻 2t 定义为: 因此 2t 表示被测速度初次到达参考速度终值 endrefv 的时刻。 可以看到,每个换档阶段超出参考信号的部分都暴露了一个与运动品质和舒适度相关的不同问题。尤其是,有三个有待控制系统解决的问题(再看看图六): ( 1) 换档开始时速度的负向变化; ( 2) 加速阶段的速度的波动; ( 3) 换档后速度稳定阶段速度的继续增大又相继减小。 这些问题的解决是通过对不同的控制变量进行适当调整。为进行如此调整,通过基于被测信号的可估客观性能参数来很好的把握这三种现象是很关键的。 为此,三个不同的成本函数 1J , 2J 和3J被考虑进来,分别对应于每个运动阶段,定义为: nts 12 / 19 式中固定区间的时间间隔已经被通过专门的灵敏度分析定义了,3J是在固定区间上算出来的。具体地,式( 10)中的3t表示为: 即,使在好坏两种换档情况下的3J差值最大化时的3t,该时刻的分类也由专业司机的水平决定。事实上,司机们都是从整体上来评判运动的。于是,在那些被认为低品质的换档中,那些换档情况系超过预定阀值的3J值被选择用来对3t进行调整,通过公式( 11)。 基于所获得的结果,一个 1.75 秒的间 隔被用来计算3J。为了对换挡质量评估的讨论进行总结,表二列出了图五中的三种换档所对应的 3,2,1, iJi值。可以看到,所选的成本函数正确地把握了运动质量,并且与专业四级的估计相符。 四、 换挡控制其设计 这部分介绍了换挡控制系统的设计。为实现所提出的方法,强调指出第二部分所描述的传动结构具有的一些固有局限性是很有必要,这些局限性必须予以考虑,正如文献 1,11,12中所述。具体如下: ( 1) 由于当启闭阀处于关闭状态时将脱出离合器上的压力为零,调整将脱出离合器上的压力是不可能的。此外,压力消失的具体时刻(即离合器松开的时刻)无nts 13 / 19 法知道,尽管压力力度的变化被认为是非常快的。 ( 2) 由于启闭阀是单向的,离合器上的压力只能升高; ( 3) 离合器中的油压无法测量。因此,压力值是通过一个将比例阀输入电流和离合器压力联系起来的静态关系来估计的。考虑到这一示意图对所有车辆来说都是独一无二的,以及每个离合器的行为的确都受到一些(数量未知)因素(例如,温度、表面磨损以及摩擦盘圆周速度)的影响,尚无法得到实际驱动扭矩的可靠估计, 正如文献 11, 12中所述。这一事实使得无法设计出一个闭环的压力控制器来解决换挡问题。 考虑到上述限制,一个开环控制器将被设计。因此,控制问题的核心就在于定义并优化一条恰当的参考压力曲线来指挥能获得预期换挡性能的比例阀。 4.1、单离合器换挡控制 回顾表一中的齿轮与离合器组合,单离合器换当中只涉及两个离合器:一个是将脱出离合器,一个是传入离合器。因此,在这种类型的换档中,控制算法在于定义主侧面压力以及恰当地选择将脱出离合器必须断开的时刻。图七展示了一种典型单离合换挡压力曲线。 司机执行换档后,主压力( 即传入离合器上的压力,该离合器上的启闭阀处于开启状态)逐渐上升至转折点( KP)压力值(如何自动定义这样一个液压阀将在第五部分讨论)。这一初级阶段使用来保证传入离合器已经能够传递扭矩(再看图三可知,当压力值低于转折点压力值时,驱动扭矩无法传递到车轮)。这一充盈期持续一个固定的nts 14 / 19 时间,实验证明为 500 毫秒。该数值对于传动系中所有离合器达到预想的转折点压力值已经足够了。接下来,动力换挡的核心阶段开始:在 Overlap 时间段内,传入离合器的压力增大,离合器所能传递的扭矩也随之增大。再往后,当时间到达 DOt 时,将脱出离合器断开(如图七虚线)。最后,主压力上升到最大值以使传入离合器进入完全工作状态。 具体来说,压力沿着斜线增加至一可调最大值,然后跃至最终的最大值。图七所示压力的最后阶段取决于传动系中液压回路的特性。更确切的说,在该压力区间上,调整图七中斜线终点所对应的压力终值实际上是可能的,尽管最后阶段实际上是由液压回路的一个安全控制所引起的(当压力值到达设定值时阀门机械关闭),该安全控制使得压力到达最大值,这样设计是为了保证离合器在任何(一些可能的反常情 况)运行状态下都不会断开。至于换挡控制不同部分的压力值,假设整个压力区间分从零到两兆帕;从开始到转折点压力大约占 0.4 兆帕(假设该数值是不同传动的平均值),调整区间(即斜线部分)上升到 1.8 兆帕。因此,压力增加但无法调节的最后阶段大约占 0.2 兆帕,相当于总压力变化的 10%。 注意到在 Overlap 区间内,将脱出离合器仍然处于啮合状态,因此给发动机增加了附加扭矩载荷。所以,当 Overlap 区间太短时,将导致传入离合器无法传递足够的扭矩进而使车辆产生所不希望的突然停车,当 Overlap 区间太长,拖拉机会由于附加 扭矩载荷而减速,这些都将给司机带来不适。另外,离合器表面的过度磨损会增加。对于转折点压力水平,也应做类似的考虑。换句话说,这两个参数值的调整对于获得最优换档起着决定性作用。为控制单离合换档选择最优参数值,选用 Eq( 8) 中的 1J 指标。实际上,控制参数与最优参数之间的偏差反映在换档开始时的显著减速,这将导致车辆前进速度的波动(例如,指标 1J 所具有的特点,见 Eq( 8) ) 基于 实验性灵敏度分析的最优化调整已经进行。图八显示了获得的结果,即,对于 1 2 和 2 3 两种换档,图八(上)和图八(下)中的 1J 指标的数值分别是充盈压nts 15 / 19 力与转折点压力偏差值和 Overlap 区间持续时间的函数。使充盈压力与转折点压力产生偏差中的权衡(即获得一个增加的 P)显而易见:正如所指,只有转折点压力的精确估计确定后才能获得最优换档。 对于 Overlap 区间的持续时间,这种权衡就没那么明显了:因为实验室在了低负荷条件下进行,那么,在这种情况下最 优 Overlap 区间的持续时间接近于零。 反之,在高负荷换档中,为该参数选择一个准确值是重要的:因此,原理上可以考虑一个预定控制器,该控制器根据当时的发动机功率(可以通过发动机控制器知道其值)为 Overlap 区间持续期选择最恰当的数值。 为评估控制器的效果,图九展示了未优化控制参数与已优化控制其参数的单离合换档中时间与被测车速的关系。未优化控制参数与已优化控制参数情况下相应的 1J 值分别为 12.86 和 1.48。图九中所显示换档的优化 后参数值为 48.0KP 兆帕,msOverlap 100 。 nts 16 / 19 图九 4 2、双离合器换档控制 在双离合换档中,两个齿轮机构中的离合器都参与进来:理想情况下,双离合换档的控制逻辑可以看做是和单离合换档一样。但实际上变速箱 HML 中液压回路的动态特性与变速箱 123 中的不同。具体来说,两个变速箱中离合器脱出所需要的时间是完全不同的,尽管两个变速箱的控制指令是同一时刻发出的。 两个变速箱中的不同是因为变速箱中 离合器尺寸的不同而使得其中的压力值不同。由于要处理不同的扭矩水平,不同尺寸的离合器是必要的。此外,变速器相对于主液压蓄能器的位置使得压力回路的长度不同,这也影响了变速箱中的压动力。 123变速箱中的压力较高。就这点而论,为了准确的实现双离合换档,需要先脱出变速箱123 再脱出变速箱 HML,以便将两者之间的不同考虑进去。具体地说,在将脱出离合器脱出之前,变速箱 123 需要更长的时间来补偿所要代替的更高的压力梯度。变速箱HML 延迟的时间已经调整以使变速箱 HML 脱出时两个变速箱的压力水平大致相同。 因此需要引进一个附加 控制参数。该新控制变量称为 DelayHML,它表示变速箱123 脱出时刻(123,DOt)与变速箱 HML 脱出时刻(HMLDOt ,)之间的时间间隔 (见图十 )。 如图十所示,为了将液压设备引起的延时考虑进来,将脱出 HML 组的脱出只有轻微的延时,等于 DelayHML。 nts 17 / 19 自从引进新的控制变量后,进行了一个专门的灵敏度分析来对其进行优化调整。在这种情况下, 1J 指标和 2J 指标都被考虑进来,见 Eqs.(8)和 Eqs.(9)。事实上,在操纵的一开始 1J 就正确地获得了速度脉冲,这主要是 KP 压力和 Overlap 持续区间的作用;而 2J 描述了加速阶段的振幅,这很大程度上取决于 DelayHML 的值。 最后,值得注意的是,在 t 大于HMLDOt ,后压力值最后的斜线阶段上升,此时传入离合器开始进入啮合阶段,但两个传入离合器可能不会同时进入啮合。基于所提到的控制方法,啮合阶段准确开始的途径是通过成本函数估计的,因此目前没有直接的啮合调整方法。 图十一描述了所得结果,显示了 1J 和 2J 的值, 1J 和 2J 是 Overlap 和 DelayHML 的函数。为简明起见,省略了 KP 压力的值的分析过程,因为所得结果与单离合换档所讨论的相似。 通过检验图十一,可以得到一些结论。 nts 18 / 19 首先注意到每个控制参数(即, Overlap 和 DelayHML)对一个单独的指标有显著的影响。即, Overlap 主要影响 1J 指标,而 DelayHML 主要影响 2J 指标。这一事实可以解耦优化阶段,并考虑两个连续单变量的优化问题,考虑到最后调
- 温馨提示:
1: 本站所有资源如无特殊说明,都需要本地电脑安装OFFICE2007和PDF阅读器。图纸软件为CAD,CAXA,PROE,UG,SolidWorks等.压缩文件请下载最新的WinRAR软件解压。
2: 本站的文档不包含任何第三方提供的附件图纸等,如果需要附件,请联系上传者。文件的所有权益归上传用户所有。
3.本站RAR压缩包中若带图纸,网页内容里面会有图纸预览,若没有图纸预览就没有图纸。
4. 未经权益所有人同意不得将文件中的内容挪作商业或盈利用途。
5. 人人文库网仅提供信息存储空间,仅对用户上传内容的表现方式做保护处理,对用户上传分享的文档内容本身不做任何修改或编辑,并不能对任何下载内容负责。
6. 下载文件中如有侵权或不适当内容,请与我们联系,我们立即纠正。
7. 本站不保证下载资源的准确性、安全性和完整性, 同时也不承担用户因使用这些下载资源对自己和他人造成任何形式的伤害或损失。

人人文库网所有资源均是用户自行上传分享,仅供网友学习交流,未经上传用户书面授权,请勿作他用。
2:不支持迅雷下载,请使用浏览器下载
3:不支持QQ浏览器下载,请用其他浏览器
4:下载后的文档和图纸-无水印
5:文档经过压缩,下载后原文更清晰
|