!【详情如下】CAD图纸+word设计说明书.doc[12000字,36页]【需要咨询购买全套设计请加QQ97666224】.bat
任务书.docx
大致参数.docx
弯管机资料
设计说明书.doc[12000字,36页]
传动部图.dwg
大轴A3.dwg
大轴前端盖A3.dwg
大轴后端盖A3.dwg
大轴套A4.dwg
大轴承座A3-9.dwg
大齿轮A3.dwg
小轴A3.dwg
小轴前端盖A3.dwg
小轴后端盖A3.dwg
小轴套A4.dwg
小轴承座A3.dwg
小齿轮A3.dwg
挡料轴A3.dwg
控制电路图.dwg
盖板A3.dwg
驱动图.dwg
立式液压驱动数控滚弯机机械系统设计
目 录
目录………………………………………………………………………………………………1
第一章 绪论……………………………………………………………………………………2
1.1 弯管机在工业中的地位和各种弯管机的性价比……………………………………………2
1.2 弯管机的基本原理与选择……………………………………………………………………3
第二章 弯管机的设计……………………………………………………………………4
2.1 工件的工艺分析………………………………………………………………………………5
2.2 计算弯曲力矩…………………………………………………………………………………5
2.3 电机的选取……………………………………………………………………………………6
2.4 传动比的计算与各传动装置的运动参数……………………………………………………8
2.5 皮带与皮带轮的计算与选取…………………………………………………………………9
2.6 蜗轮蜗杆减速箱的计算与选取………………………………………………………………9
2.7 联轴器的计算与选取…………………………………………………………………………10
2.8 轴承的选取……………………………………………………………………………………10
2.9 轴的初步计算与设计及校核…………………………………………………………………14
2.10 齿轮的计算与设计……………………………………………………………………………17
2.11 大小齿轴前后端盖及轴承座的结构设计……………………………………………………18
2.12 轴套的结构设计………………………………………………………………………………19
2.13 盖板的结构设计与计算………………………………………………………………………20
2.14 机身的结构设计与计算………………………………………………………………………21
2.15 弯管机的主要参数……………………………………………………………………………22
第三章 挡料架的结构设计…………………………………………………23
3.1 挡料架的结构设计…………………………………………………………… 23
第四章 液压系统设计………………………………………………………24
4.1 动力设计计算22
4.1.1 压紧缸载荷分析并选定压紧缸缸径22
4.1.2计算切头缸载荷并选定切头缸缸径。22
4.1.3计算抓紧缸载荷并选定抓紧缸缸径23
4.1.4分析摆动缸载荷并选定摆动缸缸径26
4.1.4计算转动缸载荷并选定转动缸缸径26
4.1.6 分析移位缸载荷并选定移动缸缸径27
4.2 运动设计计算28
4.2.1 确定切头刀具工作角度:28
4.2.2 确定齿轮齿条模数及齿轮齿数29
4.2.3计算抓紧机构转位角度29
4.2.4计算转位缸行程并选定标准行程30
4.2.4计算切头缸工作行程并选定标准行程30
4.2.6分析压紧缸工作行程并选定压紧缸标准行程31
4.2.7选定抓紧缸标准行程31
4.2.8选定切头机构移动缸标准行程31
4.2.9计算切头机构摆动缸并选定标准行程32
4.2.10选定抽芯缸标准行程32
4.2.11选定定位缸标准行程33
设计总结……………………………………………………………………………34
参考文献………………………………………………………………………………35
第1章绪 论
1.1弯管机在自工工业中的地位和各种弯管机的性价比:
现今工业发达,无论是哪一种机器设备、健身器材、家具等几乎都有结构钢管,有导管,用以输油、输气、输液等,而在飞机、汽车及其发动机,健身器材,家具等等占有相当重要的地位。各种管型品种之多、数量之大、形状之复杂,给导管的加工带来了不少的困难。对于许多小企业,家庭作坊,或者大企业中需要配管的场合,如工程机械上的压力油管,机床厂的液压管道发动机的油管健身器材的弯管等等,这些场合可能不需要功能全的弯管机,且加工的管件的难度不高,简易手动型的弯管机很可能适应。这系列弯管机采用手动夹紧,机械弯曲,机器结构简单,控制元件极少,因此价格上比较容易被用户接受。
市面上现有的自动弯管机大多数是液压的,数控的(如图1-1,1-2),也有机械传动的,但它们的占地面积较大(长度在2.5~4m之间),价格昂贵(2~5万元人民币或更多),然而大多数用户都需求是是小占地面积小价格便宜使用方便的自动
本设计便是朝这方面的用途方面设计的自动弯管机,设计出一种价格便宜,占地面积少,使用方便的自动弯管机(长0.9M,宽0.8M,高1.1M,价格9000元人民币左右),并着手对弯管机的性能更进一步的强化,使其能弯曲不同口径或不同的钢型、采用制动电机以提高弯曲机的弯曲精度。大大的简化了电器控制系统,方便操作。

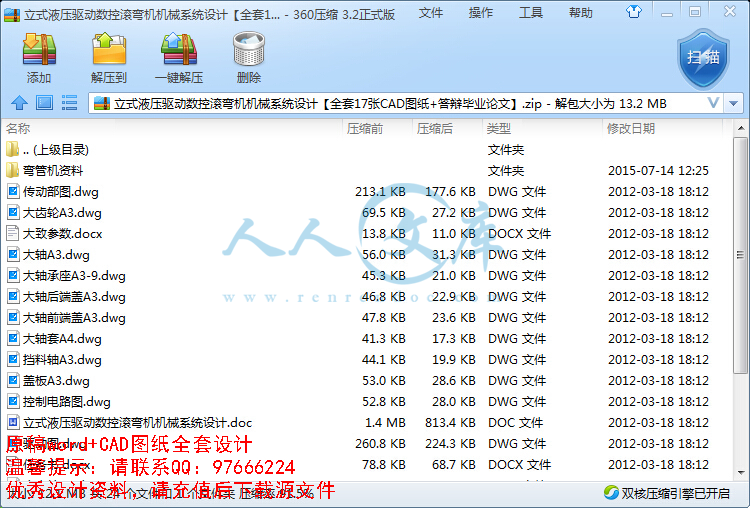












