目录
第1章 绪论3
1.1 超声波电机的定义与发展历史3
1.2 超声波电机的基本工作原理5
1.3 超声波电机的分类6
1.4 超声波电机的特点和应用6
1.5 超声波电机技术的展望7
第2章超声波电机的运动机理8
2.1 椭圆运动的分析8
2.2 驻波的产生及行波的合成10
第3章 超声波电机的理论计算与设计13
3.1 定子谐振频率的计算13
3.2 压电陶瓷换能器的设计和制作16
3.2.1 压电陶瓷的设计16
3.2.2 压电陶瓷材料的选用17
3.2.3 压电陶瓷的接线方式17
3.3 定子的设计及制作19
3.3.1 定子尺寸与行波超声波电机输出特性的关系19
3.3.2 定子的内外径尺寸的选择21
3.3.3 定子的振动模态的选择21
3.3.4 定子的齿形齿数设计21
3.3.5 定子的结构设计22
3.3.7定子材料的选择23
3.4 转子的设计及制作24
3.4.1 超声波电机转子的柔性要求24
3.4.2 定转子径向弯曲配合25
3.4. 摩擦层的设计26
3.5 定转子设计的总结26
第4章 超声波电机的驱动控制技术27
第5章 超声波电机整体结构设计30
第6章 全文总结32
参考文献33
致谢34
附录 英文翻译译文35
超声波电机的设计
摘要:超声波电机是一种利用压电陶瓷的逆压电效应工作的新概念、新原理电机。与传统电磁型电机截然不同,其驱动力矩并非由电磁感应产生,它利用压电陶瓷的压电效应使定子产生超声波振动,通过定子和转子间的摩擦力来驱动转子。由于超声波电机特殊的工作原理,它具有很多传统电磁电机无法比拟的优越性能,如结构紧凑、低速大转矩、响应速度快、不受磁场影响、断电自锁、可直接驱动负载等。正是由于超声波电机具有许多的优点和广阔的应用前景,成为当前世界范围内的一门新兴前沿课题。
本文主要以超声波电机为研究对象,设计超声波电机的实验样机。研究的主要内容可概括如下:系统地总结国内外超声波电机的发展历史和重要意义,介绍了超声波电机的工作原理、分类、特点及其应用前景。在对超声波电机相关理论研究的基础上,从超声波电机定子设计着手,详细介绍了超声波电机的设计过程。
关键词:超声波电机 压电陶瓷
Design of Traveling Wave Ultrasonic Motor
Abstract:Ultrasonic motor is a use of the inverse piezoelectric effect of piezoelectric ceramic work of new concepts, new principles of motors. Very different from the traditional electromagnetic motor, the driving torque is not generated by the electromagnetic induction, which uses the piezoelectric effect to generate ultrasonic vibration of stator, through the friction between the stator and rotor to drive the rotor. Since the working principle of ultrasonic motors special, it has a lot of traditional electromagnetic motors can not match the superior performance, such as compact structure, low speed high torque, fast response, free from magnetic influence, power locking, can directly drive the load and so on. It is because of ultrasonic motor has many advantages and potential applications, become the world's a new frontier subject.
In this paper, a rotary traveling wave type ultrasonic motor for the study, designed the experimental prototype ultrasonic motor. The main content can be summarized as follows: The system sums up the history of the development of ultrasonic motor home and abroad and the importance of introducing the principle of ultrasonic motors, classification, characteristics and application prospects. In the theory of ultrasonic motors based on ultrasonic stator design from the start, ultrasonic motor described in detail the design and production process.
Key words: Ultrasonic Motor Piezoelectric ceramics
第1章 绪论
本章主要介绍超声波电机定义与发展历史、基本工作原理、分类、特点及其应用及对超声波电机技术的应用展望。
1.1 超声波电机的定义与发展历史
超声波电机(Ultrasonic Motor,简称USM)是一种新型的直接驱动型微电机,其原理完全不同于传统的电机,没有绕组与磁路,不以电磁作用传递能量,因而有很多不同于传统电机的特性。超声波电机一种利用超声波振动能作为驱动源的新原理电机,是电机制造、机械振动学、摩擦学、功能材料、电子技术和自动控制等学科综合交叉发展的产物,是利用压电材料的逆压电效应,把电信号加到压电陶瓷-金属构成的定子上,使定子表面的质点产生一定轨迹的机械振动,驱动转子运动的新型电机。由于定子的振动频率多数处在超声频范围,所以被称为超声波电动机。超声波电机具有能量密度大、响应快、结构紧凑、低转速、大力矩、不受电磁干扰、断电自锁等优点。 在微型机械、机器人、精密仪器、家用电器、航空航天、汽车等方面有着广泛的应用前景。
USM是20世纪80年代随着科学技术的发展才备受重视并得到应用的一种新型直接驱动电机,其发展史却可追溯到20世纪40年代。20世纪40年代,人们就知道了超声波电机的这个驱动原理,然而由于当时压电陶瓷材料以及超声波电机理论技术的滞后,超声波电机只能是“空中楼阁”,没有得以实现。一直到80年代初,具有高转换效率的压电材料出现以后,再加上电力电子控制技术的发展,才逐步研制出各种各样的超声波电机。
超声波电机的发展历史过程总结如下:
利用弹性振动获得动力的尝试是从钟表开始的。1961年,英国的Bulova Watch Ltd钟表 公司首次提出了用弹性体振动能量作为驱动力 的理论,并研制成音叉驱动的手表,在国际上引起了轰动。
1973年, IBM公司的H.V.Barth博士首先研制成功原理性超声波电机,如图1.1所示。该电机由一个转子和两个驱动振子构成,两个振子由PZT提供振动,其前部压置在转子上,保持摩擦接触。当振子(1)激振时转子顺时针方向回转,当振子(2)激振时,转子逆时针方向回转。与此同时,原苏联的V.V.Lavrinenco等人也研制出几乎与Barth具有相同原理的几种超声波电机,并给出了超声波电机结构简单、成本低、低速大转矩、单位质量功率大、运动精确、能量转换效率高等一些基本特性。1978年,前苏联的Vasiliev等成功地构造了一种能够驱动较大负载的超声波电机,
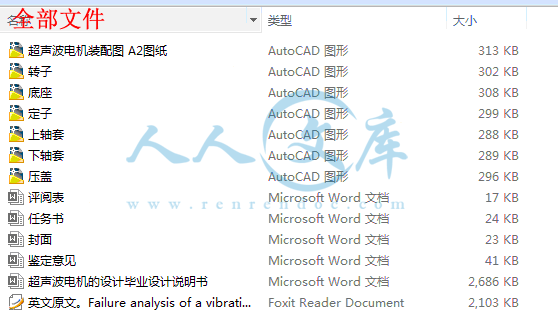
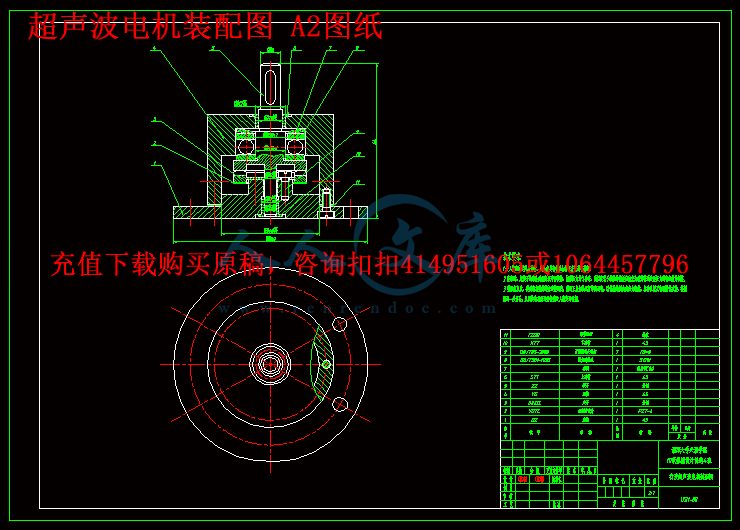

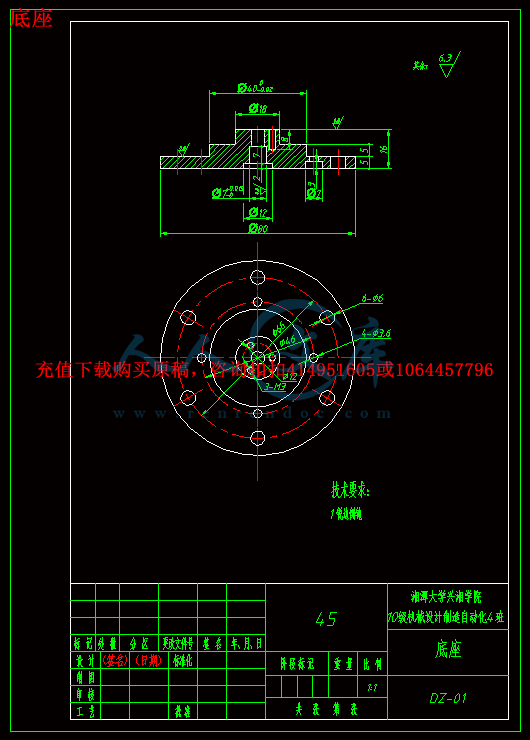



