!【详情如下】【汽车车辆工程类课题】CAD图纸+word设计说明书.doc[24000字,59页]【需要咨询购买全套设计请加QQ97666224】.bat
外文翻译
设计说明书.doc[24000字,59页]
循环球式转向器.dwg
转向桥(1比3).dwg
转向系(1比4).dwg
摘 要
汽车在行驶过程中,经常需要改变行驶方向,汽车转向系是汽车转向运动的装置,该系统由操纵机构,转向器,传动机构三部分组成,作为整车的一个重要总成,是影响汽车操纵稳定性和行驶安全性的关键系统之一。本文即完成了与长城哈弗H5欧风版(两驱)独立悬架系统相配用的循环球式转向系统设计。
在城市SUV汽车循环球式转向系统设计过程中,首先确定汽车转向系统的结构型式为机械转向,明确转向系的主要设计要求,选择长城哈弗H5欧风版(两驱)作为设计的基础车型,参考该车型的主要技术参数,逐步确定了转向系的主要性能参数,例如转向系的力传动比、作用在方向盘上的手力N等。其次进行了循环球式转向器结构型式选择及其设计计算,确定了循环球式转向器的角传动比转向器的角传动比,完成了螺杆-钢球-螺母传动副及齿条-齿扇传动副的设计,并对循环球式转向器的重要零件进行了强度校核,如对钢球与滚道间的接触应力及转向摇臂轴强度的校核,结果均符合设计要求。最后设计了转向传动机构。长城哈弗H5欧风版(两驱)的前悬架系统采用了麦弗逊式独立悬架,所以本次设计相应采用分段式转向梯形机构,用图解法确定了转向横拉杆的断开点位置,并验证了内外轮转角关系,对转向系的转向梯形进行了优化设计,得到了良好的转向梯形特性,最终完成了循环球式转向系统设计,确保将该设计方案运用到车辆上时具有良好的转向性能。
关键词:城市SUV,转向系统,机械转向,循环球式转向器,断开式转向梯形
URBAN SUV RECIRCULATING BALL STEERING SYSTEM DESIGN
ABSTRACT
A car in motion need to change the direction of travel frequently. Automobile steering system is a vehicle steering movement device. The system consists of control mechanism, steering and transmission. As an important vehicle assembly, it is a critical system affecting vehicle handling and stability and driving safety. In this thesis I completed a recirculating ball steering system design matched with the Great Wall Motor Haval H5 European style (two-drive) independent suspension system.
Firstly, in the process of recirculating ball steering system design of urban SUV, I determined the structure type of automobile steering system as the mechanical steering, cleared the main design requirements of steering system and Selected the Great Wall Motor Haval H5 European style (two-drive) as the basis model of design, made the main technical parameters of this model as known parameters, gradually established the main steering system performance parameters, such as the steering force transmission ratio is, the practicing hand on the steering wheel is . Secondly, I proceed to select recirculating ball-style steering gear structure type and completed the design calculation of it, identified the recirculating ball steering angle transmission ratio , completed the design of the screw - ball - nut transmission pair and racks – teeth fan gear pair and made the strength check of ??important parts of the recirculating ball steering, such as the contact stress between balls and raceway and the steering arm shaft strength check. Finally, I designed the steering linkage. The front suspension of Great Wall Motor Haval H5 European style (two-drive) uses MacPherson independent suspension system. Therefore, this design corresponding uses a segmented steering linkage, determined disconnect position of steering tie rod graphically and verified the relationship between internal and external rotation angle, got a good feature of steering trapezoid, and then I completed the recirculating ball steering system design, ensure that the design can be applied to the vehicle with good steering performance.
KEY WORDS: Urban SUV, The Steering System, Mechanical Steering, Recirculating Ball Steering, The Separation Type Steering Trapezoid
目 录
第一章 转向系统概述1
§1.1 汽车转向系统1
§1.1.1 机械转向系1
§1.1.2 动力转向系2
§1.1.3 转向系的主要设计要求3
§1.2 转向器及转向操纵机构4
§1.2.1 转向器的传动效率及转向盘自由行程4
§1.2.2 循环球式转向器5
§1.2.3 转向操纵机构6
§1.3 哈弗H5欧风版(两驱)技术参数8
第二章 转向系的主要性能参数10
§2.1 转向系的效率10
§2.2 转向系的角传动比与力传动比11
§2.2.1 角传动比11
§2.2.2 力传动比12
§2.2.3 转向器角传动比的变化规律15
§2.3 转向器的传动间隙特性17
§2.4 转向系的刚度及转向盘的总转动圈数17
§2.4.1 转向系的刚度17
§2.4.2 转向盘的总转动圈数19
第三章 循环球式转向器结构型式选择及其设计计算20
§3.1 循环球式转向器的角传动比21
§3.2 螺杆-钢球-螺母传动副22
§3.3 齿条-齿扇传动副25
§3.4 循环球式转向器零件的强度计算32
§3.4.1 钢球与滚道间的接触应力32
§3.4.2 螺杆在弯扭联合作用下的强度计算35
§3.4.3 转向摇臂轴直径的确定36
第四章 转向传动机构设计37
§4.1 转向传动机构概述37
§4.2 转向梯形机构设计40
§4.2.1 整体式转向梯形机构设计40
§4.2.2 分段式转向梯形机构45
§4.3 转向传动机构的臂、杆与球销47
§4.3.1 转向摇臂的强度计算49
§4.3.2 转向纵拉杆与横拉杆的计算50
§4.3.3 球销的强度与耐磨性校核51
结 论52
参考文献53
致 谢54
参考文献
[1] 刘惟信. 汽车设计[M]. 北京:清华大学出版社, 2001. 617-620
[2] 林秉华. 最新汽车设计实用手册. 黑龙江:黑龙江人民出版社, 2005.
[3] 王望予. 汽车设计. 第4版[M]. 北京:机械工业出版社, 2012. 219-223
[4] 刘涛. 汽车设计[M]. 北京:北京大学出版社, 2008. 276-280
[5] 中国汽车技术研究中心. 汽车设计标准资料手册(标准件篇) . 长春:吉林科学技术出版社, 2000.
[6] 小林明. 汽车工程手册. 北京:机械工业出版社, 1984.
[7] 顾柏良. BOSCH 汽车工程手册. 第2版. 北京:北京理工大学出版社, 2004.
[8] 《汽车工程手册》编辑委员会. 汽车工程手册. 北京:人民交通出版社, 2001.
[9] 张宝生等. 汽车优化设计理论与方法. 北京:机械工业出版社, 2000. 167-171
[10] 阎邦椿. 机械设计手册. 第5版. 北京:机械工业出版社, 2010.
[11] 成大先. 机械设计手册. 第5版. 北京:化学工业出版社, 2008.
[12] 汪琪. 机械设计计算. 北京:中国致公出版社, 1998. 543-545
[13] 王三民. 机械设计计算手册. 北京:化学工业出版社, 2009.
[14] 张继东等. 机械设计常用公式速查手册. 北京:机械工业出版社, 2009.
[15] 张展. 实用齿轮设计计算手册. 北京:机械工业出版社, 2011.
[16] 林世裕. 循环球式转向器的强度计算[J]. 拖拉机, 1980, (4): 12-15
[17] 张玉莹. 循环球式转向器设计的几个问题[J]. 二汽科技, 1987, (5): 8-11
[18] 张静. 循环球转向器螺杆的可靠性计算[J]. 煤矿机械, 2006, (2): 20-22
[19] 周祥基. 汽车转向传动技术及其发展[J]. 机械制造与自动化, 2004, (6): 9-13
[20] 戴铭英. 日本NSK循环球式转向器的设计资料[J]. 国外汽车, 1980, (2): 69-72
[21] 中国汽车技术研究中心. 中华人民共和国国家标准. GB 17675—1999. 汽车转向系 基本要求[S]. 北京:中国标准出版社, 1999.
[22] 天津拖拉机制造厂. 中华人民共和国国家标准. GB 5911—86. 转向盘 尺寸[S]. 北京:中国标准出版社, 1986.
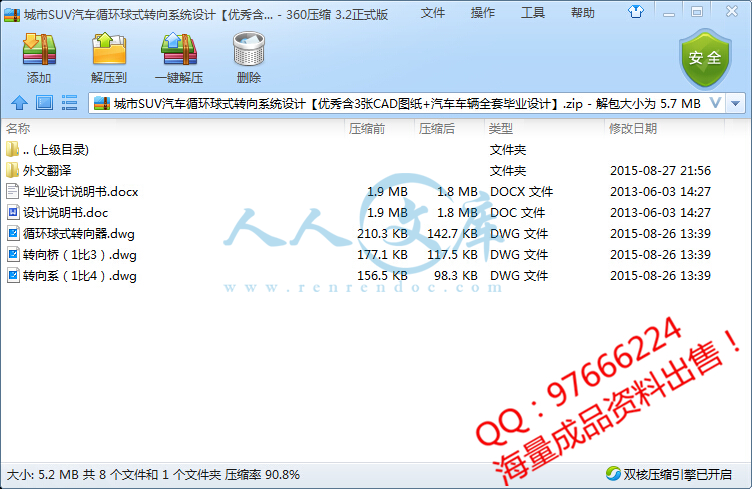
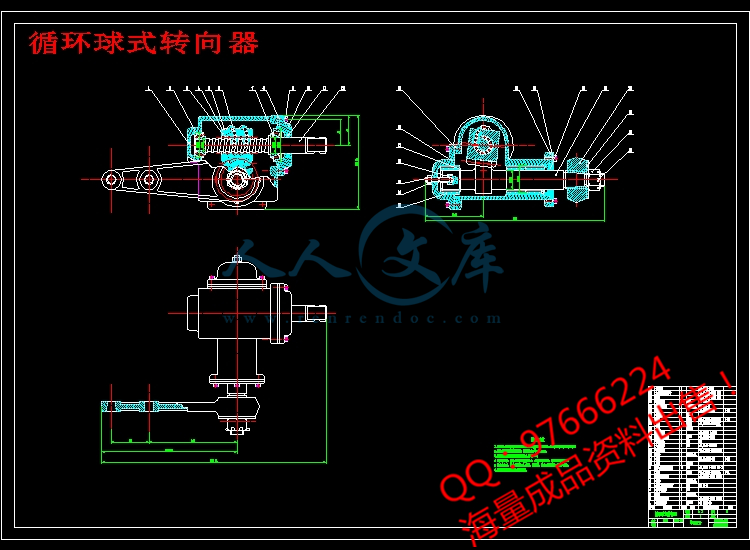




