CA10B解放牌汽车后钢板弹簧吊耳的机械加工工艺及【钻直径37孔夹具设计】【带三维】
收藏
资源目录
压缩包内文档预览:(预览前20页/共26页)
编号:477703
类型:共享资源
大小:3.06MB
格式:ZIP
上传时间:2015-09-15
上传人:小***
认证信息
个人认证
林**(实名认证)
福建
IP属地:福建
20
积分
- 关 键 词:
-
ca10b
解放
汽车
钢板
弹簧
机械
加工
工艺
直径
37
夹具
设计
三维
- 资源描述:
-

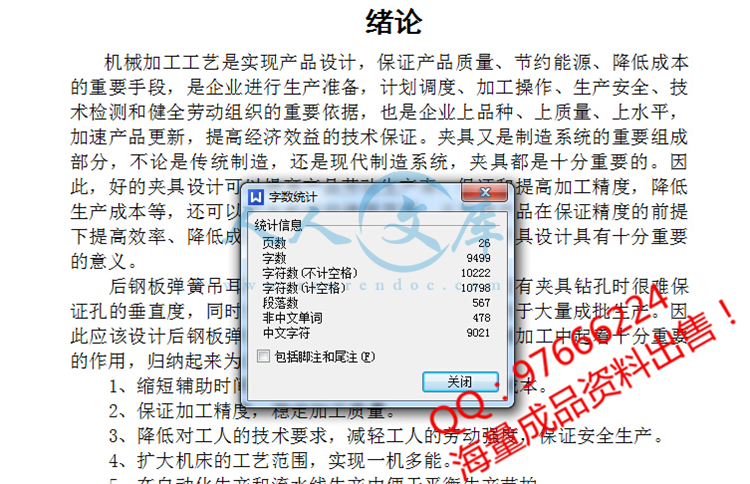






!【详情如下】【夹具课程设计课题】CAD图纸+word设计说明书.doc[10000字,26页]【需要咨询购买全套设计请加QQ97666224】.bat
UG三维
任务书.doc
设计说明书.doc[10000字,26页]
吊耳.dwg
工序卡10张
总图.dwg
毛坯图.dwg
零件图支架.dwg
零件图钻模板.dwg
摘要
本次设计是对后钢板弹簧吊耳零件的加工工艺规程及一些工序的专用夹具设计。后钢板弹簧吊零件的主要加工表面是平面及孔。由加工工艺原则可知,保证平面的加工精度要比保证孔的加工精度容易。所以本设计遵循先面后孔的原则。并将孔与平面的加工明确划分成粗加工和精加工阶段以保证加工精度。基准选择以后钢板弹簧吊耳大外圆端面作为粗基准,以后钢板弹簧吊耳大外圆端面与两个工艺孔作为精基准。主要加工工序安排是先以后钢板弹簧吊耳大外圆端面互为基准加工出端面,再以端面定位加工出工艺孔。在后续工序中除个别工序外均用端面和工艺孔定位加工其他孔与平面。整个加工过程均选用组合机床。
关键词 加工工艺;专用夹具;后钢板弹簧吊耳
不要删除行尾的分节符,此行不会被打印
目录
绪论1
第1章 零件的分析2
1.1 零件的分析2
1.1.1 零件的作用2
1.1.2 零件的工艺分析3
1.2 弹簧吊耳零件的技术要求3
第2章 确定毛坯,绘制毛坯图4
2.1 确定毛坯的制造形式4
2.2 确定毛坯的尺寸公差和机械加工余量4
2.3 吊耳毛坯尺寸公差及机械加工余量4
第3章 拟定弹簧吊耳工艺路线及机床、工艺装备的选用6
3.1 零件的加工定位基准6
3.2 零件表面加工方法的确定,吊耳各表面加工方案7
3.3 工序顺序的安排7
3.3.1 工艺方案一、工艺路线7
3.3.2 工艺方案二、工艺路线8
3.4 工艺方案的比较与分析8
3.5 确定吊耳工艺路线8
3.6 机床设备的选用9
第5章 加工余量,工序尺寸和公差的确定10
5.1 加工两端面的加工余量、工序尺寸和公差的确定10
5.2 吊耳各加工表面的机械加工余量11
5.3 确定切削用量及基本工时(机动时间)12
第6章 专用夹具设计16
6.1 加工工艺孔夹具设计16
6.2 定位方案的分析和定位基准的选择16
6.3 定位误差分析17
6.4 切削力的计算与夹紧力分析17
第7章 UG三维造型18
7.1 UG简介18
7.2 零件的三维建模18
7.3 整体装配19
结论20
参考文献21
致谢22
- 内容简介:
-
哈理工荣成学院 机 械 加 工 工 序 卡 产品型号 零(部)件图号 共 10 页 产品名称 零(部)件名称 支架 第 1 页 车 间 工序号 工序名称 材料牌号 金工 1 锻造 35 号钢 毛坯种类 毛坯外形尺寸 每毛坯件数 每台件数 铸件 1 设备名称 设备型号 设备编号 同时加工件数 1 夹 具 编 号 夹 具 名 称 切 削 液 定位销 定位轴 工序工时 准终 单件 夹具体 序号 工 步 内 容 工 艺 装 备 主轴 转速 (r/min) 切削 速度 (m/min) 进给 量 (mm/r) 切削 深度 (mm) 走刀次数 时间定额 机动 辅助 1 锻造 编制(日期) 审核(日期) 会签(日期) 标记 处数 更改文件号 签字 日期 标记 更改文件号 签字 日期 nts 哈理工荣成学院 机 械 加 工 工 序 卡 产品型号 零(部)件图号 共 10 页 产品名称 零(部)件名称 支架 第 10 页 车 间 工序号 工序名称 材料牌号 金工 10 清洗 终检 35 号钢 毛坯种类 毛坯外形尺寸 每毛坯件数 每台件数 铸件 设备名称 设备型号 设备编号 同时加工件数 夹 具 编 号 夹 具 名 称 切 削 液 定位销 乳化液 定位轴 工序工时 准终 单件 夹具体 序号 工 步 内 容 工 艺 装 备 主轴 转速 (r/min) 切削 速度 (m/min) 进给 量 (mm/r) 切削 深度 (mm) 走刀次数 时间定额 机动 辅助 1 清洗 2 终检 编制(日期) 审核(日期) 会签(日期) 标记 处数 更改文件号 签字 日期 标记 更改文件号 签字 日期 nts 哈理工荣成学院 机 械 加 工 工 序 卡 产品型号 零(部)件图号 共 10 页 产品名称 零(部)件名称 支架 第 2 页 车 间 工序号 工序名称 材料牌号 金工 2 划线 35 号钢 毛坯种类 毛坯外形尺寸 每毛坯件数 每台件数 铸件 1 设备名称 设备型号 设备编号 同时加工件数 1 夹 具 编 号 夹 具 名 称 切 削 液 定位销 定位轴 工序工时 准终 单件 夹具体 序号 工 步 内 容 工 艺 装 备 主轴 转速 (r/min) 切削 速度 (m/min) 进给 量 (mm/r) 切削 深度 (mm) 走刀次数 时间定额 机动 辅助 1 划线,分配余量 2 检验 编制(日期) 审核(日期) 会签(日期) 标记 处数 更改文件号 签字 日期 标记 更改文件号 签字 日期 nts 哈理工荣成学院 机 械 加 工 工 序 卡 产品型号 零(部)件图号 共 10 页 产品名称 零(部)件名称 支架 第 3 页 车 间 工序号 工序名称 材料牌号 金工 3 铣 削 35 号钢 毛坯种类 毛坯外形尺寸 每毛坯件数 每台件数 铸件 1 设备名称 设备型号 设备编号 同时加工件数 组合专业铣 床 X52 1 夹 具 编 号 夹 具 名 称 切 削 液 定位销 乳化液 定位轴 工序工时 准终 单件 夹具体 序号 工 步 内 容 工 艺 装 备 主轴 转速 (r/min) 切削 速度 (m/min) 进给 量 (mm/r) 切削 深度 (mm) 走刀次数 时间定额 机动 辅助 1 粗 铣 mm60 两外圆端面 ,保证尺寸mm5.79 X52; 高速钢圆柱形铣刀 169 33.4 0.8 3 1 2.3 0.51 2 粗 铣 mm60 两外圆端面 ,保证尺寸 mm78 X52; 高速钢圆柱形铣刀 169 33.4 0.8 3 1 2.3 3 精 铣 mm60 两外圆端面 ,保证尺寸mm77 2.0- 6.0- X52; 高速钢圆柱形铣刀 210 41.5 0.6 2 2 1.46 0.51 4 精 铣 mm60 两外圆端面 ,保证尺寸mm76 2.0- 6.0- X52; 高速钢圆柱形铣刀 210 41.5 0.6 2 2 1.46 编制(日期) 审核(日期) 会签(日期) 标记 处数 更改文件号 签字 日期 标记 更改文件号 签字 日期 nts 哈理工荣成学院 机 械 加 工 工 序 卡 产品型号 零(部)件图号 共 10 页 产品名称 零(部)件名称 支架 第 4 页 车 间 工序号 工序名称 材料牌号 金工 4 铣 削 35 号钢 毛坯种类 毛坯外形尺寸 每毛坯件数 每台件数 铸件 1 设备名称 设备型号 设备编号 同时加工件数 专用组合铣 床 X52 1 夹 具 编 号 夹 具 名 称 切 削 液 定位销 乳化液 定位轴 工序工时 准终 单件 夹具体 序号 工 步 内 容 工 艺 装 备 主轴 转速 (r/min) 切削 速度 (m/min) 进给 量 (mm/r) 切削 深度 (mm) 走刀次数 时间定额 机动 辅助 1 粗铣 R24 两内侧面,保证尺寸 mm77 047.00X52; 高速圆柱形铣刀 169 26.5 0.8 1.5 1 2.3 0.51 编制(日期) 审核(日期) 会签(日期) 标记 处数 更改文件号 签字 日期 标记 更改文件号 签字 日期 nts 哈理工荣成学院 机 械 加 工 工 序 卡 产品型号 零(部)件图号 共 10 页 产品名称 零(部)件名称 支架 第 5 页 车 间 工序号 工序名称 材料牌号 金工 5 铣 削 35 号钢 毛坯种类 毛坯外形尺寸 每毛坯件数 每台件数 铸件 1 设备名称 设备型号 设备编号 同时加工件数 铣 床 X52 1 夹 具 编 号 夹 具 名 称 切 削 液 定位销 乳化液 定位轴 工序工时 准终 单件 夹具体 序号 工 步 内 容 工 艺 装 备 主轴 转速 (r/min) 切削 速度 (m/min) 进给 量 (mm/r) 切削 深度 (mm) 走刀次数 时间定额 机动 辅助 1 粗铣 R24 两外侧面 X52; 高速钢圆柱铣刀 169 26.5 0.8 1.5 1 2.3 0.51 编制(日期) 审核(日期) 会签( 日期) 标记 处数 更改文件号 签字 日期 标记 更改文件号 签字 日期 nts 哈理工荣成学院 机 械 加 工 工 序 卡 产品型号 零(部)件图号 共 10 页 产品名称 零(部)件名称 支架 第 6 页 车 间 工序号 工序名称 材料牌号 金工 6 钻削 35 号钢 毛坯种类 毛坯外形尺寸 每毛坯件数 每台件数 铸件 1 设备名称 设备型号 设备编号 同时加工件数 钻床 Z3040 1 夹 具 编 号 夹 具 名 称 切 削 液 定位销 乳化液 定位轴 工序工时 准终 单件 夹具体 序号 工 步 内 容 工 艺 装 备 主轴 转速 (r/min) 切削 速度 (m/min) 进给 量 (mm/r) 切削 深度 (mm) 走刀次数 时间定额 机动 辅助 1 钻 孔到 mm35 Z3040; 麻花钻 233 25.6 0.45 1.25 1 0.94 0.54 2 扩孔到 mm8.36 Z3040; 扩孔钻 174 20.1 0.72 1.5 1 0.66 3 铰孔到 mm37 ,保证尺寸 mm37 03.00 Z3040; 铰刀 72 8 1.2 0.15 2 1.16 4 倒角 305.1 150锪钻 20.1 编制(日期) 审核(日期) 会签(日期) 标记 处数 更改文件号 签字 日期 标记 更改文件号 签字 日期 nts 哈理工荣成学院 机 械 加 工 工 序 卡 产品型号 零(部)件图号 共 10 页 产品名称 零(部)件名称 支架 第 7 页 车 间 工序号 工序名称 材料牌号 金工 7 钻削 35 号钢 毛坯种类 毛坯外形尺寸 每毛坯件数 每台件数 铸件 1 设备名称 设备型号 设备编号 同时加工件数 专用组合钻床 Z3040 1 夹 具 编 号 夹 具 名 称 切 削 液 定位销 乳化液 定位轴 工序工时 准终 单件 夹具体 序号 工 步 内 容 工 艺 装 备 主轴 转速 (r/min) 切削 速度 (m/min) 进给 量 (mm/r) 切削 深度 (mm) 走刀次数 时间定额 机动 辅助 1 钻 孔到 mm28 Z3040; 麻花钻 233 20.4 0.32 1.25 1 0.86 0.54 2 扩孔到 mm8.29 Z3040; 扩孔钻 233 21.8 0.6 0.5 1 0.4 3 铰 孔到 mm30 ,保证尺寸 mm30 043.00 Z3040;铰刀 96 9 1.2 0.125 2 0.82 4 倒角 451 90锪钻 233 编制(日期) 审核(日期) 会签(日期) 标记 处数 更改文件号 签字 日期 标记 更改文件号 签字 日期 nts 哈理工荣成学院 机 械 加 工 工 序 卡 产品型号 零(部)件图号 共 10 页 产品名称 零(部)件名称 支架 第 8 页 车 间 工序号 工序名称 材料牌号 金工 8 钻削 35 号钢 毛坯种类 毛坯外形尺寸 每毛坯件数 每台件数 铸件 1 设备名称 设备型号 设备编号 同时加工件数 专用组合钻床 Z525 1 夹 具 编 号 夹 具 名 称 切 削 液 定位销 乳化液 定位轴 工序工时 准终 单件 夹具体 序号 工 步 内 容 工 艺 装 备 主轴 转速 (r/min) 切削 速度 (m/min) 进给 量 (mm/r) 切削 深度 (mm) 走刀次数 时间定额 机动 辅助 1 钻 孔到 mm9 Z525; 麻花钻 772 21.8 0.2 0.85 1 0.76 0.54 2 扩孔到 mm5.10 Z525; 扩孔钻 772 25.4 0.4 1 1 0.38 编制(日期) 审核(日期) 会签(日期) 标记 处数 更改文件号 签字 日期 标记 更改文件号 签字 日期 nts 哈理工荣成学院 机 械 加 工 工 序 卡 产品型号 零(部)件图号 共 10 页 产品名称 零(部)件名称 支架 第 9 页 车 间 工序号 工序名称 材料牌号 金工 9 铣削 35 号钢 毛坯种类 毛坯外形尺寸 每毛坯件数 每台件数 铸件 1 设备名称 设备型号 设备编号 同时加工件数 专用组合铣床 X52 1 夹 具 编 号 夹 具 名 称 切 削 液 定位销 乳化液 定位轴 工序工时 准终 单件 夹具体 序号 工 步 内 容 工 艺 装 备 主轴 转速 (r/min) 切削 速度 (m/min) 进给 量 (mm/r) 切削 深度 (mm) 走刀次数 时间定额 机动 辅助 1 铣宽为 4mm 的开口槽 X52; 高速钢锯片铣刀 118 28.8 0.5 22 1 0.44 0.51 编制(日期) 审核(日期) 会签(日期) 标记 处数 更改文件号 签字 日期 标记 更改文件号 签字 日期 nts哈尔滨理工大学荣成学院 专科生毕业设计(论文)任务书 学生姓名: 辛海茹 学号: 1030310116 学 院: 荣成学院 专业:机械设计与制造 任务起止时间: 2013年 02月 25日至 2013年 06月 21日 毕业设计(论文)题目: 后钢板弹簧 吊 耳 工艺规程制订和工装设计 毕业设计工作内容: 1、实际调研,收集相关资料; 1 3周。 2、结合生产实际,制订零件的机械加工工艺; 3、填写 各 工序的工序卡; 4 7周。 4、设计指定工序的专用夹具,画出装配图 ; 8 11 周。 5、设计 所有零件的工作图; 12 13周。 6、撰写毕业设计论文;准备答辩。 14-16周。 注:要求全部用计算机绘图和打印文稿(交打印件和电子稿) 资料: 1、机械制造工艺学; 2、机床夹具设计及图册; 3、金属切削用量手册; 4、相关的技术资料。 指导教师意见: 签名: 2013年 2 月 24 日 系主任意见: 签名: 2013年 2月 25日 nts - I - 后钢板弹簧吊耳的加工工艺和夹具设计 摘要 本次设计是对后钢板弹簧吊耳零件的加工工艺规程及一些工序的专用夹具设计。后钢板弹簧吊零件的主要加工表面是平面及孔。由加工工艺原则可知,保证平面的加工精度要比保证孔的加工精度容易。所以本设计遵循先面后孔的原则。并将孔与平面的加工明确划分成粗加工和精加工阶段以保证加工精度。基准选择以后钢板弹簧吊耳大外圆端面作为粗基准,以后钢板弹簧吊耳大外圆端面与两个工艺孔作为精基准。主要加工工序安排是先以后钢板弹簧吊耳大外圆端面互为基准加工出端面,再以端面定位加工出工艺孔。在后续工序中 除个别工序外均用端面和工艺孔定位加工其他孔与平面。整个加工过程均选用组合机床。 关键词 加工工艺;专用夹具;后钢板弹簧吊耳 nts - II - 目录 绪论 . 1 第 1 章 零件的分析 . 1 1.1 零件的分析 . 2 1.1.1 零件的作用 . 2 1.1.2 零件的工艺分析 . 2 1.2 弹簧吊耳零件的技术要求 . 3 第 2 章 确定毛坯,绘制毛坯图 . 4 2.1 确定毛坯的制造形式 . 4 2.2 确定毛坯的尺寸公差和机械加工余量 . 4 2.3 吊耳毛坯尺寸公差及机械加工余量 . 4 第 3 章 拟定弹簧吊耳工艺路线及机床、工艺装备的选用 . 6 3.1 零件的加工定位基准 . 6 3.2 零件表面加工方法的确定,吊耳各表面加工方案 . 7 3.3 工序顺序的安排 . 7 3.3.1 工艺方案一、工艺路线 . 7 3.3.2 工艺方案二、工艺路线 . 8 3.4 工艺方案的比较与分析 . 8 3.5 确定吊耳工艺路线 . 8 3.6 机床设备的选用 . 9 第 5 章 加工余量,工序尺寸和公差的确定 . 10 5.1 加工两端面的加工余量、工序尺寸和公差的确定 . 10 5.2 吊耳各加工表面的机械加工余量 . 11 5.3 确定切削用量及基本工时(机动时间) . 12 第 6 章 专用夹具设计 . 16 6.1 加工 mm37 工艺孔夹具设计 . 16 6.2 定位方 案的分析和定位基准的选择 . 16 6.3 定位误差分析 . 17 6.4 切削力的计算与夹紧力分析 . 17 第 7 章 UG 三维造型 . 18 7.1 UG 简介 . 188 7.2 零件的三维建模 . 18 7.3 整体装配 . 19 结论 . 20 nts - III - 参考文献 . 21 致谢 . 22 nts - IV - nts - 1 - 绪论 机械加工工艺是实现产品设计,保证产品质量、节约能源、降低成本的重要手段,是企业进行生产准备,计划调度、加工操作、生产安全、技术检测和健全劳动组织的重要依据,也是企业上品种、上质量、上水平,加速产品更新,提高经济效益的技术保证。 夹具又是制造系统的重要组成部分,不论是传统制造,还是现代制造系统,夹具都是十分重要的。因此,好的夹具设计可以提 高产品劳动生产率,保证和提高加工精度,降低生产成本等,还可以扩大机床的使用范围,从而使产品在保证精度的前提下提高效率、降低成本。所以对 机械的加工工艺及夹具设计具有十分重要的意义。 后钢板弹簧吊耳孔的加工,不容易找正,如果没有夹具钻孔时很难保证孔的垂直度,同时也很麻烦,增加辅助时间,不利于大量成批生产。因此应该设计后钢板弹簧吊耳的专用夹具。 夹具在机械加工中起着十分重要的作用,归纳起来为以下几方面: 1、缩短辅助时间,提高劳动生产率,降低加工成本。 2、保证加工精度,稳定加工质量。 3、降低对工人的技术要求,减 轻工人的劳动强度,保证安全生产。 4、扩大机床的工艺范围,实现一机多能。 5、在自动化生产和流水线生产中便于平衡生产节拍。 夹具不同于其他环节,他在工艺系统中有着特殊地位,夹具的整体刚度对工件加工的动态误差产生着非常特殊的影响。当夹具的整体刚度远大于其他环节,工件加工的动态误差基本上只取决于夹具的制造精度和安装精度。因此设计夹具时,对夹具的整体刚度应给予足够重视。如因工艺系统其他环节的刚度不足而引起较大的系统动态误差时,也可以采取修正夹具定位元件的方法进行补偿。这就是夹具的能动作用。 nts - 2 - 第 1章 零件的分析 1.1 零 件的分析 1.1.1 零件的作用 题目给出的零件是解放牌汽车后钢板弹簧吊耳。后钢板弹簧吊耳的主要作用是载重,使钢板能够得到延伸,伸展,能有正常的缓冲作用。因此汽车后钢板弹簧吊耳零件的加工质量会影响汽车的工作精度、使用性能和寿命。汽车后钢板弹簧吊耳主要作用是减震功能、阻尼缓冲部分功能、导向功能。 图 1-1 后钢板弹簧吊耳零件图 1.1.2 零件的工艺分析 由后钢板弹簧吊耳零件图知可将其分为两组加工表面。它们相互间有一定的位置要求,现分析如下: 1、以 mm60 两外圆端面为主要加工表面的加工面。这一组加工表面包括: mm60 两外圆端面的铣削,加工 mm37 05.00 的孔,其中 mm60 两外 m6.1 Ra 。 nts - 3 - 2、以 0.045030孔为主要加工表面的加工面。这一组加工表面包括: 2个 0.045030的孔, 2 个 mm5.10 的孔、 2 个 0.045030孔的内外两侧面的铣削,宽度为 4mm 的开口槽的铣削,在 0.045030同一 中心线上数值为 0.01 的同轴度要求。其中 2 个 0.045030的孔表面粗糙度要求为 m6.1 Ra , 2 个 mm5.10的孔表面粗糙度要求为 m5.12 Ra , 2 个 0.045030孔的内侧面表面粗糙度 要求为 m5.12 Ra , 2 个 0.045030孔的外侧面表面粗糙度要求为 m50Ra ,宽度为 4mm 的开口槽的表面粗糙度要求为 m50Ra 。 1.2 弹簧吊耳零件的技术要求 根据后钢板弹簧 吊耳的具体应用场合、工作面、受力情况等,根据参考文献可知其加工的技术要求,如表 1-2 所示。 表 1-2 弹簧吊耳零件加工的技术要求 加工表面 尺寸及技术要 求 /mm 公差及精度 等级 表面粗糙度 Ra/m 形位公差 /mm mm60 两外圆端面 60mm IT12 6.3 mm37 05.00孔 mm30 05.00IT9 1.6 mm30 045.00孔内侧面 54mm IT12 12.5 mm30 045.00孔外侧面 54mm IT12 50 mm30 045.00孔 mm30 045.00IT9 1.6 0.01 A mm5.10 孔 mm30 045.00 IT12 12.5 开口槽 4mm IT12 50 nts - 4 - 第 2章 确定毛坯,绘制毛坯图 2.1 确定毛坯的制造形式 “后钢板弹簧吊耳”零件材料为 35 钢,硬度 HBS 为 149 187,首试生产类型为中批量生产。 考虑到该弹簧吊耳零件在工作过程中要承受压力冲击载荷,为增强弹簧吊耳零件的强度和冲击韧度,故毛坯选用锻件,零件材料为 35 号钢。由于生量已达到中批生产的水平 ,而且零件的轮廓尺寸不大,为提高生产效率和锻件精度,故可以采用模锻制造毛坯。 2.2 确定毛坯的尺寸公差和机械加工余量 由参考文献可知,要确定毛坯的尺寸公差及机械加工余量,应先确定如下各项 因素。 1、公差等级 由弹簧吊耳的功用及其技术要求,确定该零件的公差等级为普通级。 2、锻件重量 已知机械加工后弹簧吊耳的重量为 2.6kg,由此可初步估计机械加工前锻件毛坯的重量为 4kg。 3、锻件材质系数 该弹簧吊耳材料为 35 号钢,是碳的质量分数小于 0.65%的碳素钢,故该锻件的材质系数属 1M 级。 4、锻件分模线形状 根据该弹簧吊耳的形位特点,故选择零件高度方向的对称平面为分模面,属平直分模线,如图 2-2弹簧吊耳锻造毛坯图所示。 2.3 吊耳毛坯尺寸公差及机 械加工余量 由弹簧吊耳零件图可知,该零件各加工表面的粗糙度 Ra 均大于m6.1 。考虑到零件的公差等级、锻件重量、锻件材质系数、锻件分模线形状等因素,可查表确定该锻件的尺寸公差及机械加工余量,针对于该零件的特性以及加工的工艺规程,考虑要复合加工的实际情况,零件的本身特性,对于中批量的生产要求,满足产品的成品率,合格率,最大限度的满足零件的使用寿命,将零件设计出相应的,略宽的毛培图,以利于零件的加工和装夹,满足生产的最大优化。 针对于 以上要求,绘制 钢板弹簧吊耳锻造毛坯图 所得结果列于表 2-1 中。 nts - 5 - 图 2-1 后钢板弹簧吊耳锻造毛坯图 表 2-2 毛坯尺寸公差及机械加工余量 锻件重量 /kg 包容题体重量 /kg 形状复杂系数 材质系数 公差等级 4 6.4 S2 M1 普通级 项目 /mm 机械加工余量 /mm 尺寸公差 /mm 参考文献 宽度 76 5.1 7.02.2 表 2-10 2.0 2.2(取 2.0) 表 2-13 宽度 38.5 5.1 7.02.2 表 2-10 2.0 2.2(取 2.0) 表 2-13 宽度 22 4.16.00.2 表 2-10 2.0 2.2(取 2.0) 表 2-13 孔径mm37 05.00 5.1 7.02.2 表 2-10 2.6 表 2-14 孔径mm30 045.00 4.16.00.2 表 2-10 2.0 表 2-14 nts - 6 - 第 3章 拟 定弹簧吊耳工艺路线 3.1 零件的加工定位基准 由以上分析可知,该零件的主要加工表面是平面及孔系。一般来说,保证平面的加工精度要比保证孔系的加工精度容易。因此,对于该零件来说,加工过程中的主要问题是保证平面的尺寸精度以及孔的尺寸精度及位置精度,处理好孔和平面之间的相互关系。 该类零件的加工应遵循先面后孔的原则:即先加工零件的基准平面,以基准平面定位加工其他平面,然后再加工孔系。后钢板弹簧吊耳的加工自然应遵循这个原则。这是因为平面的面积大,用平面定位可以确保定位可靠、夹紧牢固,因而容易保证孔的加工精度。为提高孔 的加工精度创造条件,便于对刀及调整,也有利于保护刀具。 后钢板弹簧吊耳零件的加工工艺应遵循粗精加工分开的原则,将孔与平面的加工明确划分成粗加工和精加工阶段以保证孔系加工精度。由于后钢板弹簧吊耳的生产量很大,怎样满足后钢板弹簧吊耳生产率要求也是过程中的主要考虑因素。 1、粗基准的选择 1)粗基准的选择应以加工表面为粗基准。目的是为了保证加工面与不加工面的相互位置关系精度。如果工件上表面上有好几个不需加工的表面,则应选择其中与加工表面的相互位置精度要求较高的表面作为粗基准。以求壁厚均匀、外形对称、少装夹等。 2)选择加工余量要求均匀的重要表面作为粗基准。例如:机床床身导轨面是其余量要求均匀的重要表面。因而在加工时选择导轨面作为粗基准,加工床身的底面,再以底面作为精基准加工导轨面。这样就能保证均匀地去掉较少的余量,使表层保留而细致的组织,以增加耐磨性。 3)应选择加工余量最小的表面作为粗基准。这样可以保证该面有足够的加工余量。 4)应尽可能选择平整、光洁、面积足够大的表面作为粗基准,以保证定位准确夹紧可靠。有浇口、冒口、飞边、毛刺的表面不宜选作粗基准,必要时需经初加工。 5)粗基准应避免重复使用,因为粗基准的表面大 多数是粗糙不规则的。多次使用难以保证表面间的位置精度。 为了满足上述要求,基准选择以后钢板弹簧吊耳 mm60 外圆端面作为粗基准,先以后钢板弹簧吊耳大外圆端面互为基准加工出端面,再以端面定位加工出 mm37 5.00 工艺孔。在后续工序中除个别工序外均用端面和工艺孔定位加工其他孔与平面。 nts - 7 - 2、精基准的选择 精基准的选择主要考虑基准重合的问题,根据该弹簧吊耳零件的技术要求和装配要求,选择 加工后的 mm60 两外圆端面作为精基准。 3.2 零件表面加工方法的确定,吊耳各表面加工方案 根据弹簧吊耳零件图上各加工表面的尺寸精度和表面粗糙度,确定加工工件各表面的加工方法,如表 3-1 所示。 表 3-1 弹簧吊耳零件各表面加工方案 加工表面 尺寸精度等级 表面粗糙度 Ra/m 加工方案 mm60 两外圆端面 IT12 6.3 粗铣 mm37 05.00 孔 IT9 1.6 钻 -扩 -铰 mm30 045.00 孔内侧面 IT12 12.5 粗铣 mm30 045.00 孔外侧面 IT12 50 粗铣 mm30 045.00 孔 IT9 1.6 钻 -扩 -铰 mm5.10 孔 IT12 12.5 钻 开口槽 IT12 50 粗铣 3.3 工序顺序的安排 由于生产类型为大批生产,应尽量使工序集中来提高生产率,除此之外,定期对设备进 行维护和修养,将产品的合格率实现最优最大化。 3.3.1 方案一 、工艺路线 如表 3-2 所示。 表 3-2 工艺方案一表 工序 1 锻造,退火 工序 2 划线,分配余量,检验 工序 3 铣 mm60 两外圆端面 工序 4 钻,扩,铰 mm37 05.00 孔,倒角 1.5 30 o 工序 5 钻,扩 mm5.10 孔 工序 6 钻,扩,铰 mm30 05.00 孔,倒角 1 45 o 工序 7 铣 mm30 045.00 孔的内侧面 工序 8 铣 mm30 045.00 孔的外侧面 工序 9 铣宽度为 4mm 的开口槽 工序 10 终检 nts - 8 - 3.3.2 工艺方案二 、工艺路线 如表 3-3所示。 表 3-3 工艺方案二表 工序 1 锻造,退火 工序 2 划线,分配余量,检验 工序 3 铣 mm30045.00 孔的内侧面 工序 4 铣 mm30045.00 孔的外侧面 工序 5 钻,扩 mm5.10 孔 工序 6 钻, 扩,铰 mm30045.00 孔,倒角 1 45 o 工序 7 铣宽度为 4mm 的开口槽 工序 8 铣 mm60 两外圆端面 工序 9 钻,扩,铰孔 mm3705.00 ,倒角 1.5 30 o 工序 10 终检 3.4 工艺方案的比较与分析 上述两个工艺方案的特点在于:方案一是先加工 mm60 两外圆端面,然后再以此为基面加工 mm37 05.00孔,再加工 mm5.10 孔,mm30 045.00 孔,最 后加工 mm30 045.00 孔的内外侧面以及宽度为 4mm 的开口槽铣,则与方案二相反,先加工 mm30 045.00孔的内外侧面,再以此为基面加工 mm5.10 孔, mm30 045.00孔,宽度为 4mm 的开口槽,最后加工mm60 两外圆端面, mm37 05.00 孔。 经比较可见,先加工 mm60 两外圆端面,以后位置度较易保证,并且定位及装夹都较方便,但方案一中先加工 mm5.10 孔, mm30 045.00 孔,再加工 mm30 045.00 孔的内外侧面,不符合先面后孔的加工原则,加工余量更大,所用加工时间更多,这样加工路线就不合理,同理,宽度为 4mm的开口槽应放在最后一个工序加工。所以合理具体加工艺如下表 3-4。 3.5 确定吊耳工艺 路线 在综合考虑以上工序顺序安排原则的基础上,最终确定合理的后钢板弹簧吊耳工艺路线,如表 3-4。 nts - 9 - 表 3-4 最终工艺方案 工序 1 锻造,退火 工序 2 划线,分配余量,检验 工序 3 铣 mm60 两外圆端面 工序 4 铣 mm30 045.00 孔的内侧面 工序 5 铣 mm30 045.00孔的外侧面 工序 6 钻,扩,铰 mm37 05.00 孔,倒角 1.5 30 o 工序 7 钻,扩,铰 mm30 045.00孔,倒角 1 45 o 工序 8 钻,扩 mm5.10 孔 工序 9 铣宽度为 4mm 的开口槽 工序 10 终检 3.6 机床设备的选用 在大批生产的条件下,所选用的弹簧吊耳零件选用的设备如下。 表 3-5 吊耳工艺路线及设备、工装的选用 工序号 工序名称 机床设备 刀具 量具 1 锻造,退火 2 划线 3 粗铣 60mm 两外圆端面 立式铣床 X52 端铣刀 游标卡尺 4 铣 mm30 045.00 孔的内 侧面 立式铣床 X52 端铣刀 卡尺,塞规 5 铣 mm30 045.00 孔的外侧面 立式铣床 X52 端铣刀 游标卡尺 6 钻,扩,铰 03.0037 mm 孔, 倒角 1.5 30 立式铣床 X52 麻花钻,扩孔钻, 铰刀 游标卡尺 7 钻,扩,铰mm30 045.00 孔, 倒角 1 45 立式铣床 X52 麻花钻,扩孔钻, 铰刀 卡尺,塞规 8 钻,扩 10.5mm 孔 立式铣床 X52 麻花钻,扩孔钻 卡尺,塞规 9 铣宽为 4mm 的开口槽 立式铣床 X52 槽铣刀 卡规 ,深度游标卡尺 11 去毛刺,终检 塞规,卡尺 nts - 10 - 第 4章 加工余量,工序尺寸和公差的确定 4.1 加工两端面的加工余量、工序尺寸和公差的确定 1、第一道工序的加工过程为: 1)以 mm60 左端面 A 定位,粗铣 右端面 B,保证工序尺寸 1P ,余量1Z ; 2)以 mm60 右端面 B 定位,粗铣左端面 A,保证工序尺寸 2P ,余量2Z ,达到零件图设计尺寸 D 的要求, mm76 2.0 6.0 。 3)由图 5-1 所示加工方案,可以找出全部工艺尺寸链,如图 5-2 所示,求解各工序尺 寸及公差的顺序如下: 图 5-1 第 1 道工序加工方案示意图 a) b) 图 5-2 第 1 道工序工艺尺寸链图 从图 5-2的 a 图可知, mm76 2.0 6.02 DP ; 从图 5-2的 b 图可知, 221 ZPP ,其 中: 2Z 为粗铣余量 ,由于 B面的加工余量是经粗铣一次切除的,故 2Z 应等于 B面的毛坯余量,即mm22 Z , mm78276221 ZPP 。由参考文献1可知,该粗铣工序的经济加工精度等级为 IT=12,其公差 mm54.0 ,故mm)27.078(1 P 。为验证确定的工序尺寸及公差是否合理,还需对加工余量进行校核。 2、加工余量 2Z 的校核 在图 5-2的 b 图所示的尺寸链中 2Z 是封闭环,故: nts - 11 - mm54.273.7527.78m i n2m a x1m a x2 PPZ mm46.127.7673.77m a x2m i n1m i n2 PPZ 余量校核结果表明,所确定的工序尺寸及公差是合理的。将工序尺寸按“入体原则”表示: mm76 2.06.02 P, mm78 054.01 P。 4.2 吊耳各加工表面的机械加工余量 根据上述原始资料及加工工艺,分别确定各加工表面的机械加工余量,工序尺寸如下: 1)铣 mm60 两外圆端面 考虑其加工表面粗糙度要求为 m3.6 Ra ,粗铣就可以达到,根据上表2-4,取 2Z=4mm 已能满足要求 2)加工 mm37 05.00孔 其表面粗糙度要求较高为 m6.1 Ra ,其加工方式可以分为扩,铰两步,根据参考文献 4,确定工序尺寸及余量为: 钻孔: mm35 扩孔: mm8.36 2Z=1.8mm 铰孔: mm37 05.002Z=0.2mm 3)铣 mm30 045.00孔的内侧面 考虑其表面粗糙度要求为 m6.1 Ra ,只要求粗加工,取 2Z=4mm 已能满足要求。 4)铣 mm30 045.00孔的外侧面 考虑其表面粗糙度要求为 m50Ra ,只要求粗加工,取 2Z=4mm 已能满足要求。 5)加工 mm30 045.00 孔 其表面粗糙度要求较高为 m6.1 Ra ,其加工方式可以分为钻,扩,铰三步,根据参考文献 4,确定工序尺寸及余量为: 钻孔: mm28 扩孔: mm8.29 2Z=1.8mm 铰孔: mm30 045.00 2Z=0.2mm 6)加工 mm5.10 孔 其表面粗糙度要求较高为 m5.12 Ra ,其加工方式可以分为钻,扩,两步,根据参考文献 4,确定工序尺寸及余量为: 钻孔: mm8.9 扩孔: mm5.10 2Z=0.7mm nts - 12 - 4.3 确定切削用量及基本工时(机动时间) 工序 1:粗铣 mm60 两外圆端面 机床:立式铣床 X52。 刀具:端铣刀 63mmd 、粗齿数 6Z 。 铣削深度wa: mm2wa每 齿进给量fa:根据相参考文献 2可知,按机床功率为 KW105 取za f /mm08.0 。 铣削速度 V :根据参考文献可知 ,取 min/m9.44V 。 机床主轴转速 n : 01000Vn d ( 2-1) 取 V = min/45m , 0d= mm63 代入公式( 2-1)得: m in/47.227mm6314.3 m in/m451000 rn 根据参考文献 4可知,取 min/210 rn 。 实际铣削速度 V : m i n/m5.411000 m i n/210mm6314.31000 0 rndV 工作台每分进给量mf: m z wf f zn( 2-2) 取zf= 0.08fa , 6Z ,wn= min/210 rn 代入公式( 2-2)得: mf m in/mm8.100m in/210608.0 r在此取 min/mm100mf。 根据文献 4可得: 被切削层长度 l : mm60l 刀具切入长度 1l : mm41 l 刀具切出长度 2l : mm32 l 走刀次数为: 1 机动时间1jt:121jml l ltf 取 mm60l , mm141 l , mm32 l , min/mm100mf代入公式得: m in73.0m in/mm100 mm3mm14mm601 jt 以上为铣一个端面的机动时间,故本工序机动工时为: nts - 13 - m in46.1m in73.022 11 jtt 工序 2:钻、扩、铰 mm37 05.00孔,倒角 1.5 30 o 机床:立式 铣床 X52 刀具:麻花钻、扩孔钻、铰刀 1)钻 mm35 孔 切削深度pa: mm6.1pa进给量 f :根据参考文献 4,取 rf /mm60.030.0 由于本零件在加工 mm35 孔时属于低刚度零件,故进给量应乘系数 0.75,则 rrf /mm)45.0225.0(/mm75.0)60.030.0( 根据参考文献 2,取 rf /mm40.0 。 min/m24V 铣削速度 V : 取切削速度。取 V =24,0d=35 代入以下公式得: 机床主轴转速 n : 01 0 0 0 1 0 0 0 2 4 2 1 8 / m i n3 . 1 4 3 5Vnrd 根据参考文献 4,取 233 / m innr 。 实际切削速度 V : m in/m6.251000 2333514.31000 0 ndV 根据参考文献 4可得: 被切削层长度 l : mm76l 刀具切入 长度 1l : mm20l 刀具切出长度 2l : mm3l 走刀次数为: 1 机动时间jt:121j l l lt fn取 mm76l , mm20l , mm3l , 0.45f , 233n 代入以下公式得: 1jt 7 6 2 0 3 0 . 9 4 m i n2 3 3 0 . 4 52)扩 mm35 孔 切削深度pa: mm875.0pa进给量 f :根据参考文献 1可知, rrf /mm)84.063.0(7.0/mm)2.19.0( ,取 rf /mm8.0 。 切削速度 V :根据参考文献 2 ,取 min/mm58V 。取 V =58, 0d =36.8 代入以下公式 得: nts - 14 - 机床主轴转速 n : m in/5 0 28.3614.3 581 0 0 01 0 0 00rd Vn 根据参考文献 2可知,取 min/490 rn 。 实际切削速度 V : m i n/m6.561000 4908.3614.31000 0 ndV 根据参考文献 4可得: 被切削层长度 l : mm76l 刀具切入长度 1l mm41 l 刀具切出长度 2l : mm3l 走刀次数为: 1 取 mm76l ,1 4l ,2 3l , 8.0f , 490n 代入公式得: 机动时间1jt: m in21.04908.0 3476211 fn lllt j 3)铰 mm37 05.00孔 切削深度pa: mm075.0pa进给量 f : 根 据 参考 文 献 2 ,可 知 rf /mm)5.28.0( ,取rf /mm5.1 。 铣削速度 V : 根据参考文献 2,可知切削速度 min/m70V 。取 V =70, 0d=37 代入以下公式得: 机床主轴转速 n : m in/6033714.3 701 0 0 01 0 0 00rd Vn 根据参考文献 4可知,取 min/590 rn 。 实际切削速度 V : m in/m5.681000 5903714.31000 0 ndV 根据参考文献 4可得 : 被切削层长度 l : mm76l 刀具切入长度 1l : mm5l 刀具切出长度 2l : mm20l 走刀次数为: 1 取 76l , 1 5l , 2 20l , 5.1f , 590n 代入以下公式得: nts - 15 - 机动时间jt: m in11.05905.1 20576211 fn lllt j 4)倒角 1.5 30 o 采用 150 锪钻。为缩短辅助时间,取倒角是的主轴转速与扩孔时相同: min/490 rn ,手动进给。 同理,根据以上相同的计算过程可得出其它工序的机动时间为: 工序 3:粗铣 mm30 045.00孔的内侧面 m in02.151.022 11 jtt 工序 4:粗铣 mm30 045.00孔的外侧面 m in02.151.022 11 jtt 工序 5:钻、扩、铰 mm30 045.00孔,倒角 451 1)钻 mm28 孔 m in34.167.022 11 jtt 2)扩 mm8.29 孔 m in14.007.022 11 jtt 3)铰 mm30 045.00孔 m in1.005.022 11 jtt 工序 6:钻、扩 mm5.10 孔 1)钻 mm8.9 孔 m in08.154.02211 jtt2)扩 mm5.10 孔 m in14.007.02211 jtt工序 7:粗铣宽度为 4mm 的开口槽 m in05.01 1 6 0 23022211 mj flllt nts - 16 - 第 5章 专用夹具设计 5.1 加工 mm37 工艺孔夹具设计 为了提高劳动生产率,保证加工质量,降低劳动 强度,需要设计专用夹具。经过与指导老师协商,决定设计第道工序 钻 mm37 孔的钻床夹具。本夹具将用于 Z3040 摇臂钻床,刀具为高速钢锥柄麻花钻。 5.2 定位方案的分析和定位基准的选择 由零件图可知,两工艺孔位于零件 mm24R 孔内外侧面上,其有尺寸精度要求和表面粗糙度要求并应与侧面垂直。为了保证所钻、铰的孔与侧面垂直并保证两工艺孔能在后续的孔加工工序中使 mm5.10 孔的加工余量均匀。根据基准重合、基准统一原则。在选择两工艺孔的加工定位基准时,应尽量选择上一道工序即粗、精铣顶面工序的定位基准,以及设计基准作为其定位基准。因此加工工艺孔的定位基准应选择 mm60 外圆端面为主要定位基面以限制工件的三个自由度,以 mm37 孔限制工件的两个自由度。 以 mm37 孔和 mm37 孔的一个端面为定位基准,采用支承钉为辅助支承,同时为了缩短本工序的辅助时间,应设计一个可以快速更换工件的夹紧装置。 1、切削力和夹紧力的计算 刀具:高速钢锥柄麻花钻 , mm37 轴向力: 303133.1234.05.10600 7.010 FYFXFF KfdCF ( N) 扭矩: 93.111033.1234.05.1054.33310 38.09.130 MYFXFM KfdCM mN 在计算切削力时必须把安全系数考虑在内,安全系数计算公式: 321 KKKK 其中: 1K 基本安全系数,取 1.5; 2K 加工性质系数,取 1.1; 3K 刀具钝化系数,取 1.2。 所以 7 2 0 23 0 3 12.11.15.1 KFF (N) 2、夹紧力的计算 在此夹具中,只是为了防止工件在加工过程中的振动和转动,因此很小,在此忽略不计。 nts - 17 - 5.3 定位误差分析 定位尺寸公差的确定。夹具的主要定位元件是一根定位轴,该定位轴的尺寸与公差现定与本零件在工作时与其相配的轴的尺寸与公差相同 ,取其公差为 6n ,即 mm37 017.0033.0。定位轴与零件的最大间隙为: max=0.05-(-0.033)=0.083mm 而零件要求的最小偏差为: min=0-(-0.01)=0.01 因此最大间隙满足精度要求。 5.4 切削力的计算与夹紧力分析 由于本道工序主要完成工艺孔的钻、扩、铰加工,而钻削力远远大于扩和铰的切削力。因此切削力应以钻削力为准。由参考文献 3得: 钻削力的计算公式: 6.08.026 HBDfF ( 3-1) 钻削力矩的计算公式: 6.08.09.110 HBfDT ( 3-2) 其中: mm30D ; 1mm32.0 rf ; m a x m a x m i n11 1 8 7 1 8 7 1 4 9 1 7 433H B H B H B H B 代入公式( 3-1)和( 3-2)得 0 . 8 0 . 62 6 3 0 0 . 3 2 1 7 4 6 8 9 6FN mm5632017432.03010 6.08.09.1 NT 本道工序加工工艺孔时,夹紧力方向与钻削力方向相同。因此进行夹紧力计算无太大意义。只需定位夹紧部件的销钉强度、刚度适当即能满足加工要求。 nts - 18 - 第 6章 UG 三维造型 6.1 UG 简介 UG( Unigraphics NX)是 Siemens PLM Software 公司出品的一个 产品工程解决方案,它为用户的产品设计及加工过程提供了数字化造型和验证手段。 Unigraphics NX 针对用户的虚拟产品设计和工艺设计的需求,提供了经过实践验证的解决方案。 UG 是 Unigraphics 的缩写,这是 一个交互式 CAD/CAM(计算机辅助设计与计算机辅助制造 )系统,它功能强大,可以轻松实现各种复杂实体及造型的建构。它在诞生之初主要基于工作站,但随着 PC 硬件的发展和个人用户的迅速增长,在 PC 上的应用取得了迅猛的增长,目前已经成为模具行业三维设计的一个主流应用。 UG 为那些培养创造性和产品技术革新的工业设计和风格提供了强有力的解决方案。利用 UG 建模,工业设计师能够迅速地建立和改进复杂的产品形状, 并且使用先进的渲染和可视化工具来最大限度地满足设计概念的审美要求。 UG包括了世界上最强大、最广泛的产品设计应 用模块。 NX 具有高性能的机械设计和制图功能,为制造设计提供了高性能和灵活性,以满足客户设计任何复杂产品的需要。 UG 优于通用的设计工具,具有专业的管路和线路设计系统、钣金模块、专用塑料件设计模块和其他行业设计所需的专业应用程序。 UG 允许制造商以数字化的方式仿真、确认和优化产品及其开发过程。通
- 温馨提示:
1: 本站所有资源如无特殊说明,都需要本地电脑安装OFFICE2007和PDF阅读器。图纸软件为CAD,CAXA,PROE,UG,SolidWorks等.压缩文件请下载最新的WinRAR软件解压。
2: 本站的文档不包含任何第三方提供的附件图纸等,如果需要附件,请联系上传者。文件的所有权益归上传用户所有。
3.本站RAR压缩包中若带图纸,网页内容里面会有图纸预览,若没有图纸预览就没有图纸。
4. 未经权益所有人同意不得将文件中的内容挪作商业或盈利用途。
5. 人人文库网仅提供信息存储空间,仅对用户上传内容的表现方式做保护处理,对用户上传分享的文档内容本身不做任何修改或编辑,并不能对任何下载内容负责。
6. 下载文件中如有侵权或不适当内容,请与我们联系,我们立即纠正。
7. 本站不保证下载资源的准确性、安全性和完整性, 同时也不承担用户因使用这些下载资源对自己和他人造成任何形式的伤害或损失。

人人文库网所有资源均是用户自行上传分享,仅供网友学习交流,未经上传用户书面授权,请勿作他用。