摘 要
根据水下鱼形机器人的设计方案进行仿真,分析运动规律及校核机构。利用UG中三维建模、运动仿真及设计仿真等模块,对已经设计好的机器鱼进行系统仿真,并比较输出数值和计算数值的关系,从而完善设计过程。主要对机器鱼的四个部分进行分析,分别是驱动机构、沉浮机构、转向机构、充电机构。其中,驱动机构由尾部摆动机构实现,鱼身后半部和鱼尾的两节做有相位差的摆动,通过摆动来击打水从而推动鱼身前进。沉浮功能由鱼身前半部分的侧鳍通过转动一定角度来实现的。转向功能,由鱼身前半部分的鳍通过转动一定的角度来实现的,鳍与鱼身竖直方向的夹角的改变使其受到水的推动力的向左或者向右的分力,从而使鱼身可以绕其重心进行旋转。外形设计是根据金枪鱼的外形进行多次拟合而归纳而成的。最终对整个机器鱼进行配重,使重力中心和浮力中心在一条直线上,保证机器鱼能在水中平稳正常运动,同时控制模块中植入远程通信功能。
关键词:水下鱼形机器人;运动仿真;远程通信
ABSTRACT
According to the underwater fish-shaped robot to simulate the design, analysis and verification body movement. UG in the use of three-dimensional modeling, motion simulation and design of simulation modules, the fish have been designed machine system simulation, and compare the output value and the numerical calculation, in order to improve the design process. The main fish-machine analysis of four parts, namely the drive mechanism, ups and downs mechanism, steering, charging mechanism. Among them, the drive mechanism from the rear swing institutions, fish and fish tail behind the first half there are two of the swing phase, through the swing to hit the water in order to promote the fish forward. Rise and Fall of the functional from the first half of the fish lateral fins rotate through a certain angle to achieve. Shift function, by the fish through the latter part of the pelvic rotation to achieve a certain point of view, the ventral fin fish vertical with the angle between the direction of change to be the driving force of water to the left or the right of the play, so that fish can rotate around its center of gravity. Design is based on the shape of tuna and summarized a number of fitting together. Eventually the whole fish weight machines, so that center of gravity and buoyancy in a straight line, the fish can assure a smooth and normal movement in the water. Control to transplant long range correspondence in the mold piece function in the meantime.
Keywords: Fish-shaped underwater robot; motion simulation; communication
目 录
摘 要 III
ABSTRACT IV
第1章 绪论 1
1.1 引言 1
1.2 水下鱼形机器人技术的基本概念 1
1.2.1 鱼类游动方式的分类 1
1.2.2 仿鱼鳍机器鱼的特点 2
1.3 仿生机器鱼研究概况 2
1.4 目前研究热点及未来发展方向 5
1.5 本课题研究内容 5
第2章 UG中运动仿真和有限元分析模块功能介绍 7
2.1 运动仿真介绍 7
2.1.1 运动仿真模块 7
2.1.2 运动仿真模块能执行何种类型分析 7
2.1.3 如何创建运动仿真 7
2.1.4 运动仿真的机构运动方式 8
第3章 水下鱼形机器人机构确定 9
3.1 沉浮机构的确定 9
3.2 转向机构的确定 13
3.3 舵机选择 13
3.4 整体结构位置设计及外形确定 14
3.4.1 整体结构尺寸确定 14
3.4.2 外形结构尺寸确定 15
第4章 基于UG的鱼形机器人的运动仿真 16
4.1沉浮机构运动仿真 17
4.1.1 计算 17
4.1.2 三维建模 17
4.13 最终结果分析 18
4.2 转向机构的运动仿真 20
4.2.1 计算 20
4.2.2 三维模型 20
4.2.3 最终结果分析 20
第5章 鱼形机器人远程通信 23
5.1 通信模块的选用 23
5.2 具体实现 23
5.2.1系统总体设计 23
5.2.2 模块设计 23
5.2.3软件设计 24
第6章 基于UG的鱼形机器人动力学分析 26
6.1 机器鱼浮力中心和重力中心的估算 26
6.2 基于UG的机器鱼浮力中心和重力中心计算 28
6.2.1 浮力计算 28
6.2.2 重力计算 28
第7章 结论与展望 30
7.1 结论 30
7.2 不足之处及未来展望 30
参考文献 31
第1章 绪论
1.1 引言
随着人类的发展,对资源的需求不断增加。陆上资源的日益紧缺,让我们把目光投向海洋。21世纪是海洋开发的世纪,水下机器人在海洋环境研究、海洋资源探测和开发等民用领域和海洋军事方面具有广阔的应用前景和巨大的潜在价值,吸引了人们更多的注意力。利用仿生学原理,开发类似海豚或金枪鱼的操纵与推进技术是一个很有前途的研究方向之一。
上世纪三十年代起,人类开始对鱼类游动进行观察,提出了大量关于鱼类游动机理的解释。近年来,随着人类对鱼类游动机理了解的加深,同时伴随着仿生学、流体力学、机器人学的进步,计算机、传感器和智能控制技术的快速发展,以及新型材料的不断涌现,对仿生水下机器人技术的研究达到了一个新的顶峰,涌现了大量基于鱼类游动机理的仿生水下机器人。
1.2 水下鱼形机器人技术的基本概念
1.2.1 鱼类游动方式的分类
鱼类游动方式多种多样,1926年Breder根据鱼类推进运动的特征不同,将鱼类游动方式划分为两大类:
1)身体(和/或)尾鳍推进(BCF locomotion);
2)中间鳍(和/或)对鳍推进(MPF locomotion).
当然鱼类还有其它运动方式,如喷流推进、滑行等。据估计,大约只有15%的鱼类采用第一种方式以外的其它方式推进。由于MPF推进方式速度慢、效率低,因此我们把重点放在研究BCF推进方式上。Breder将BCF推进继续细化为五种,如图1.1所示。图中反映了不同推进方式下鱼体推进部分的变化。
图1.1 BCF推进
图1. l中鲹科结合月牙形尾鳍推进方式(Thunniform)是效率最高、速度最快的推进方式,海洋中游速最快的“鱼类”(金枪鱼、海豚、鲨鱼)都采用该种方式。
该方式中推进运动限制在身体后三分之一,仅通过尾部(坚硬的月牙形尾鳍和尾柄)的运动产生超过90%的推力;同时鱼体的形状和重量分布保证了身体前三分之二横向移动和转轴极小。在游动过程中,月牙形尾鳍做横移和左右摆动(或升沉和上下摆动)的一种复合运动,并随着鱼体前进划出波浪形的轨迹。研究表明,月牙形尾鳍的展弦比、形状、硬度、摆动都对该推进方式的效率产生影响。
由于相比之下具有高速、高效的特点,结合月牙形尾鳍推进方式很适合用于水下机器人。目前,己有多个机器人较成功的采用了这种方式。





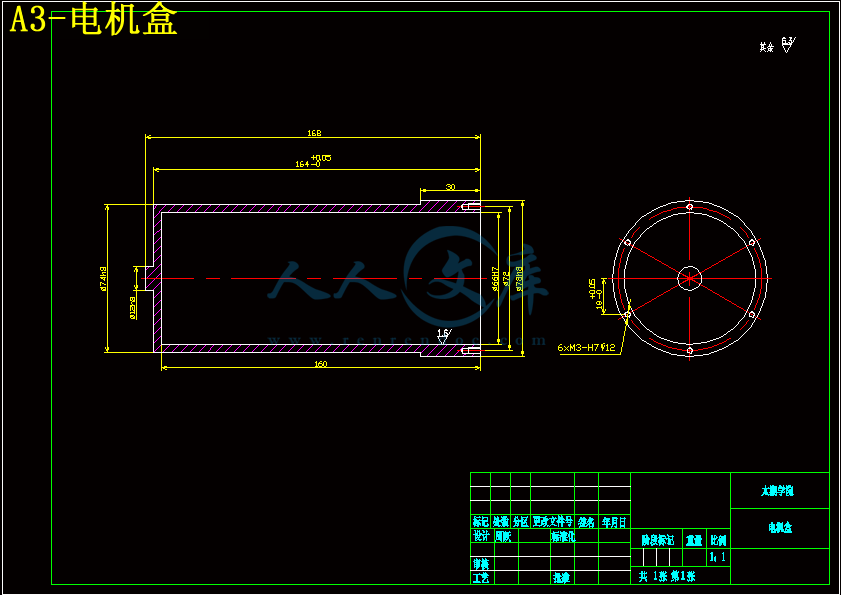



