文 献 综 述
凸轮轴是汽车发动机配气机构中重要的零件,凸轮轴的结构设计与加工质量好坏,直接影响着发动机的性能。近年来,因环境保护的需要,正在开发低油耗、低污染的发动机。为了解决汽车尾气无污染排放问题,实现发动机的高转速、高输出功率,许多发动机采用多气门及配气相位、气门升程可变的结构,这就增加了气门弹簧的载荷。同时,为了降低油耗及摩擦损耗,凸轮与摇臂间采用滚子结构,凸轮与滚子的接触面形成高压力区,这对凸轮轴运动的平稳性、动平衡、耐磨性能及抗扭强度提出了更高的要求。另外,为了达到汽车轻型化、低成本的目的,在不影响各个零件性能要求的前提下,应该使零件尽可能简化加工、降低重量,材料使用也更趋合理。
凸轮轴的构造
凸轮轴的主体是一根与气缸组长度相同的圆柱形棒体。上面套有若干个凸轮,另一端与驱动轮相连接。
凸轮的侧面呈鸡蛋形。其设计的目的在于保证气缸充分的进气和排气,尽可能在短时间内完成气门的开、闭动作。另外考虑到发动机的耐久性和运转的平顺性,气门也不能因开闭动作中的减速过程产生过多过大的冲击,否则就会造成气门的严重磨损、噪声增加或者其它严重后果。因此,凸轮和发动机的功率、扭矩输出以及运转的平顺性有很直接的关系。
一般来说,直列式发动机中,一个凸轮就对应一个气门。V型发动机或水平对置式发动机则是每两个气门共享一个凸轮。而转子发动机和无阀配气发动机由于其特殊的结构,并不需要凸轮。为了实现轻量化,易于加工且低成本,以及发动机的高转速、高输出功率,发动机部件,尤其是凸轮轴的设计必须重新考虑,要求其结构紧凑、功能高度集中、重量轻,能承受更高的接触压力。在目前的凸轮轴应用中,已经将缸盖润滑系统集中于中空式凸轮轴,将实现缸内直喷的燃油泵驱动组件在凸轮轴上实现,将VVT(可变正时气门)在凸轮轴尾端使用。在配气机构中,对凸轮轴各个部位的性能要求是不同的。对于凸轮和燃油泵驱动轮,要求耐磨损、耐胶着、耐点蚀;对于轴颈要求滑动性能好;对于轴则要求刚性、弯曲、扭转性能好[1-2]。
凸轮轴的国内外发展趋势
金属、塑料复合凸轮轴已在美国应用。将粉末金属成型并经磨削加工的凸轮片和中空钢轴放入模具内,在中空轴周围注射塑料。凸轮片和轴之间不再有金属直接接触,而是由塑料固定形成一体。这种凸轮轴的成本及重量均可减少40%,可降低发动机噪声,加工准备时间由原来的几小时缩短至几分钟。
装配式凸轮轴目前以较快的速度发展,主要应用于高性能发动机上。目前,世界上许多汽车工业发达的汽车制造厂正在越来越多使用装配式凸轮轴制造新技术,但因技术掌握的程度、方法不同,使用装配式凸轮轴的种类也不同。日本日野自动车工业株式会社在20世纪90年代初开发了热套和焊接组合的生产方式,凸轮采用碳钢,用冷精锻方法制造,轴颈采用高频淬火钢管制成,轴则采用冷拔碳钢管。日本丰田汽车公司也有相似的生产方式。日本精工株式会社用扩管法生产凸轮轴,产品的刚度较铸造产品提高1.7倍,累计生产已达300万根。日本柱塞环株式会社从20世纪80年代中期开始生产烧结连接式凸轮轴,1992年开始生产专门用于低能耗发动机的凸轮轴,凸轮采用烧结合金,具有非常好的耐磨损及耐点蚀性能。目前已生产了750万根。从20世纪90年代中期该公司开始研制刮削连接式凸轮轴。美国MTS2SA公司、TORINGTON公司、FEDERAL2MDOGUL公司、通用汽车公司、福特汽车公司都已将装配式凸轮轴应用于生产之中。德国的大众汽车公司、奔驰汽车公司、THYSSENK2RUPP公司,英国的T&NTechnology公司、GKNBoundBrook公司也都先后开发研制了装配式凸轮轴的生产工艺及设备。目前在我国仅上海大众汽车公司有1条生产装配式凸轮轴的生产线,其他企业还处于空白阶段。个别单位曾经研制了烧结连接式凸轮轴,但都没有实用化。吉林大学对装配式凸轮轴已经研制开发了多年,重点针对滚花连接方式进行了研究,对连接机理进行了探讨,应用计算机模拟方法对连接部位工作状态的应力应变做了模拟研究,并对装配力做了不同情况的试验分析。在连接试验的基础上开发了自动化装配机。装配式凸轮轴已发展二十多年,除了上述的方法外,正大力开发应用复合材料,例如陶瓷材料等制造凸轮轴。随着装配式凸轮轴生产技术的提高,性能更好、成本更低、技术多样化的装配式凸轮轴将会涌现出来[3]。


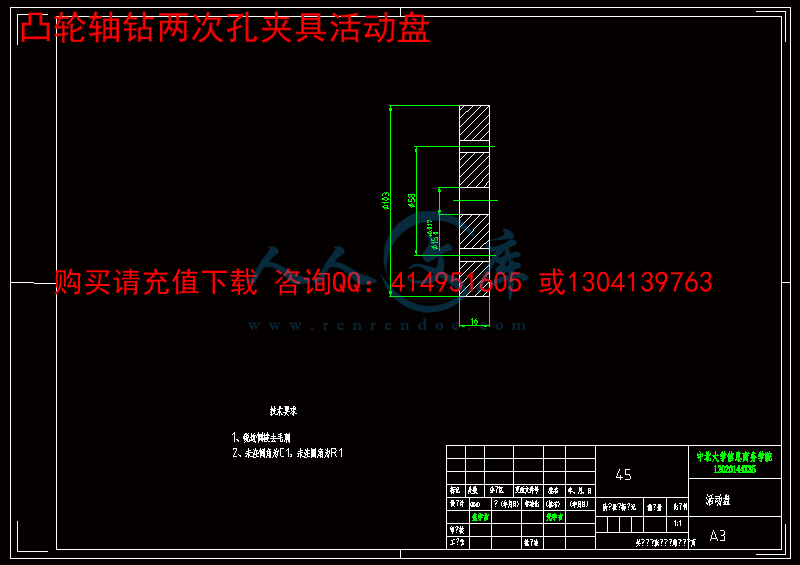


