资源目录
压缩包内文档预览:(预览前20页/共34页)
编号:7130131
类型:共享资源
大小:562.70KB
格式:RAR
上传时间:2018-01-09
上传人:优***
认证信息
个人认证
罗**(实名认证)
广西
IP属地:广西
45
积分
- 关 键 词:
-
液压
板机
系统
设计
- 资源描述:
-







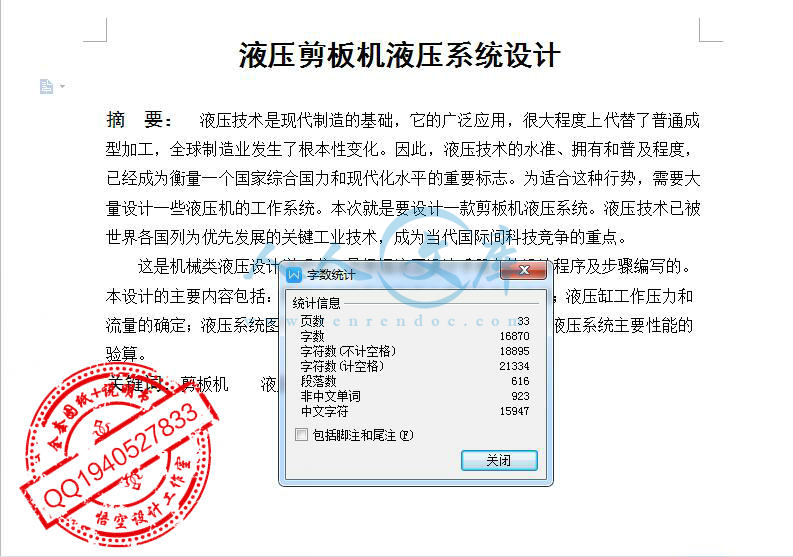
- 内容简介:
-
题目液压剪板机的液压系统设计院系专业姓名学号学习年限指导教师申请学位年月日液压剪板机液压系统设计摘要液压技术是现代制造的基础,它的广泛应用,很大程度上代替了普通成型加工,全球制造业发生了根本性变化。因此,液压技术的水准、拥有和普及程度,已经成为衡量一个国家综合国力和现代化水平的重要标志。为适合这种行势,需要大量设计一些液压机的工作系统。本次就是要设计一款剪板机液压系统。液压技术已被世界各国列为优先发展的关键工业技术,成为当代国际间科技竞争的重点。这是机械类液压设计说明书,是根据液压设计手册上的设计程序及步骤编写的。本设计的主要内容包括剪板机液压系统的设计课题及有关参数;液压缸工作压力和流量的确定;液压系统图的拟定;驱动电机及液压元件的选择;液压系统主要性能的验算。关键词剪板机液压缸液压泵系统压力HYDRAULICPLATESHEARSHYDRAULICSYSTEMDESIGNAUTHORSNAMEWANGPENGTUTORLICAILIANABSTRACTHYDRAULICTECHNOLOGYISTHEFOUNDATIONOFMODERNMANUFACTURING,ANDITSWIDERAPPLICATION,TOALARGEEXTENTREPLACEDTHEORDINARYFORMING,THEGLOBALMANUFACTURINGSECTORHASUNDERGONEFUNDAMENTALCHANGESTHEREFORE,THEHYDRAULICTECHNOLOGYSTANDARDS,POSSESSIONANDPENETRATION,HASBECOMEOFACOUNTRYSCOMPREHENSIVENATIONALSTRENGTHANDANIMPORTANTINDICATOROFTHELEVELOFMODERNIZATIONTHISTRIPISSUITABLEFORPOTENTIAL,ALOTNEEDSTODESIGNSOMEHYDRAULICSYSTEMOFWORKTHEDESIGNFORHYDRAULICMACHINERYDESIGNSPECIFICATIONISBASEDONHYDRAULICDESIGNMANUALONTHEDESIGNOFTHEPROCEDURESANDSTEPSTOPREPARETHEMAINCONTENTOFTHISBOOKINCLUDECUTTINGPLATEMACHINEHYDRAULICSYSTEMDESIGNISSUESANDRELATEDPARAMETERSHYDRAULICCYLINDERPRESSUREANDFLOWOFWORKTOBECONFIRMEDHYDRAULICSYSTEMOFTHEPLANDRAWNUPDRIVEMOTORANDHYDRAULICCOMPONENTSOFCHOICEHYDRAULICSYSTEMCHECKINGPERFORMANCEOFTHEMAJORDESIGNEXPERIENCEKEYWORDSCUTTINGPLATEMACHINEHYDRAULICCYLINDERHYDRAULICPUMPPRESS目录1引言111液压剪板机简介112液压剪板机的最新发展213液压传动技术的发展概况32任务分析421液压剪板机工作参数要求422液压系统的工作原理423剪板机液压系统的总体结构524主要机构组成525制定液压系统的基本方案73剪板机液压系统原理图731系统原理图732电磁铁动作顺表933剪板机液压系统的工作过程94液压系统的计算及液压元件的选择1041液压剪板机工作参数要求1042液压缸的设计1143油箱的设计1744管件的设计1945液压泵的选择1946阀的选择2147电机的选择与计算24总结与致谢26参考文献28附录2901引言11液压剪板机简介剪板机作为机械机床的一种形式,其主要应用于各种板材的剪切作业中,由于我国近年来科技水平的提高,剪板机的种类也随之增多。其中液压摆式剪板机、液压闸式剪板机都是较为明显的应用设备,它们具有一定的共同点,那就是这两种剪板机的传动系统都是液压系统,该系统的应用对于剪板机的生产效率具有一定程度的提升作用。液压摆式剪板机是目前市场中常用的一种剪板机设备,它能够剪切不同厚度的钢板材料,其性能也非常优良,因此该种剪板机深受消费者的青睐。据目前的液压摆式剪板机市场分析,我们可以知道,常用的剪板机分为平剪、滚剪及震动剪3种类型。平剪机是使用量最多的,剪切厚度小于10MM的剪板机多为机械传动,大于10MM的为液压传动。一般用脚踏或按钮操纵进行单次或连续剪切金属。随着现代科学的发展剪板机工艺也发生了很大变化,已由传统的手工操作发展到今天的全自动机械化。液压技术是现代制造的基础,它的广泛应用,很大程度上代替了普通成型加工,使全球制造业发生了根本性变化。液压技术已被世界各国列为优先发展的关键工业技术,成为当代国际间科技竞争的重点。因此,液压技术的水准、拥有和普及程度,已经成为衡量一个国家综合国力和现代化水平的重要标志。为适合这种行势,需要大量设计一些液压机的工作系统。本次就是要设计一款剪板机液压系统。剪板机是一种用于剪切金属板料的机床。大中型剪板机的主运动(剪刀上、下)多数采用液压传动,即采用液压缸带动剪刀(架)上下。为了防止板料翘起或移动,剪切时必须用压料脚将板材压紧。而为了减少送料时摩擦力,送料时采用拖料球支承板料。这些辅助动作用若干个小辅助缸完成。剪切时主缸的典型动作循环为空程下行剪切缓冲快速回程。在下行过程中主缸可随时停止运动并退回(点动)。剪板机剪切后应能保证被剪板料剪切面的直线度和平行度要求,并尽量减少板材扭曲,以获得高质量的工件。剪板机的上刀片固定在刀架上,下刀片固定在工作台上。工作台上安装有托料球,以便于板料的在上面滑动时不被划伤。后挡料用于板料定位,位置由电机进行调节。压料缸用于压紧板料,以防止板料在剪切时移动。护栏是安全装置,以防止发生工伤事故。112液压剪板机的最新发展金属切削机床是应用液压技术较广泛的领域之一。采用液压传动技术与控制的机床,可在较宽范围内进行无级调速,具有良好的换向及速度换接性能,易于实现自动工作循环,对提设计其高生产效率,改进产品质量和改善劳动条件,都起着十分重要的作用。液压系统的实就是液压站的设计,它是独立的液压装置,它按驱动装置要求供油,并控制油流的方向、压力和流量,它适合用于主机与液压装置分离的各种液压机械下。在用的时候只要将液压站与主机上的执行机构(油缸和油马达)用油管相连,液压机械即可实现各种规定的动作。液压传动相对于机械传动来说,是一门发展较晚的技术。自18世纪末英国制成世界上第一台水压机算起,液压传动技术只有二三百年的历史。直到20世纪30年代它才较普遍地用于起重机、机床及工程机械。20世纪60年代以来,液压技术随着原子能、空间技术、计算机技术的发展而迅速发展,并渗透到各个工业领域中。液压技术开始向高速、高压、大功率、高效率、低噪声、经久耐用、高度集成化的方向发展。同时,新型液压元件和液压系统的计算机辅助设计CAD、计算机辅助测试CAT、计算机直接控制CDC、机电一体化技术、可靠性技术等方面也是当前液压传动及控制技术发展和研究的方向。我国的液压工业开始于20世纪50年代,最初只应用于机床和锻压设备上,后来又用于拖拉机、剪板机和工程机械。现在,我国的液压元件随着从国外引进一些液压元件、生产技术以及进行自行设计,现已形成了系列,并在各种机械设备上得到了广泛的使用。尽管如此,我国的液压元件与国外先进的同类产品相比,在性能上,在种类上、在规格上仍存在着较大的差距。我国已瞄准世界发展主流的液压元件系列型谱,有计划地引进、消化、吸收国外最先进的液压技术和产品,大力开展产品国产化工作。我国的液压技术在21世纪必将获得更快的发展。目前的情况可以分析看出,单一技术的传动方式构成简单、传动可靠,适用于某些特定的场合和领域。而在大多数的实际应用中,这些传动技术往往不是孤立存在的,彼此之间都存在着相互的渗透和结合,如液力、液压和电力的传动装置中都或多或少的包含有机械传动环节,而新型的机械和液力传动装置中也设置了电气和液压控制系统。换句话说,采用有针对性的复合集成的方式,可以充分发挥各种传动方式各自的2优势,扬长避短,从而获得最佳的综合效益。值得注意的是,兼有调节与布局灵活性及高功率密度的液压传动装置在其中充当着重要角色。自20世纪90年代以来,工程机械进入了一个新的发展时期,新技术的广泛应用使得新结构和新产品不断涌现。随着微电子技术向工程机械的渗透,工程机械日益向智能化和机电一体化方向发展,对工程机械行走驱动装置提出的要求也越来越苛刻。近年来,液压技术迅速发展,液压元件日臻完善,使得液压传动在工程机械传动系统中的应用突飞猛进,液压传动所具有的优势也日渐凸现。可以相信,随着液压技术与微电子技术、计算机控制技术以及传感技术的紧密结合,液压传动技术必将在工程机械行走驱动系统的发展中发挥出越来越重要的作用。因此对于液压系统的应用于研究对于国民经济发展、提高工厂效益都有非常积极的作用。13液压传动技术的发展概况液压传动相对于机械传动来说,是一门发展较晚的技术。自18世纪末英国制成世界上第一台水压机算起,液压传动技术只有二三百年的历史。直到20世纪30年代它才较普遍地用于起重机、机床及工程机械。在第二次世界大战期间,由于战争需要,出现了由响应迅速、精度高的液压控制机构所装备的各种军事武器。第二次世界大战结束后,战后液压技术迅速转向民用工业,液压技术不断应用于各种自动机及自动生产线,从而使它在机械制造、工程机械、农业机械、汽车制造等行业得到推广应用。20世纪60年代以来,液压技术随着原子能、空间技术、计算机技术的发展而迅速发展,并渗透到各个工业领域中。液压技术开始向高速、高压、大功率、高效率、低噪声、经久耐用、高度集成化的方向发展。同时,新型液压元件和液压系统的计算机辅助设计CAD、计算机辅助测试CAT、计算机直接控制CDC、机电一体化技术、可靠性技术等方面也是当前液压传动及控制技术发展和研究的方向。我国的液压工业开始于20世纪50年代,最初只应用于机床和锻压设备上,后来又用于拖拉机、剪板机和工程机械。现在,我国的液压元件随着从国外引进一些液压元件、生产技术以及进行自行设计,现已形成了系列,并在各种机械设备上得到了广泛的使用。尽管如此,我国的液压元件与国外先进的同类产品相比,在性能上,在种类上、在规格上仍存在着较大的差距。3我国已瞄准世界发展主流的液压元件系列型谱,有计划地引进、消化、吸收国外最先进的液压技术和产品,大力开展产品国产化工作。我国的液压技术在21世纪必将获得更快的发展。自2O世纪9O年代以来,工程机械进入了一个新的发展时期,新技术的广泛应用使得新结构和新产品不断涌现。随着微电子技术向工程机械的渗透,工程机械日益向智能化和机电一体化方向发展,对工程机械行走驱动装置提出的要求也越来越苛刻。近年来,液压技术迅速发展,液压元件日臻完善,使得液压传动在工程机械传动系统中的应用突飞猛进,液压传动所具有的优势也日渐凸现。可以相信,随着液压技术与微电子技术、计算机控制技术以及传感技术的紧密结合,液压传动技术必将在工程机械行走驱动系统的发展中发挥出越来越重要的作用。2任务分析21液压剪板机工作参数要求设计要求主机中能完成空载启动,剪切、和快速回程动作。辅助动作包括剪切中途回程、点动向上、点动向下等动作。设计过程中液压元件所选用型号应正确、有理有据;整个液压系统设计科学、规范、合理。表21设计参数项目单位数值公称力KN1200最高工作压力MPA32单缸选用压力MPA16推程MM/S40主液压缸回程MM/S80顶出行程MM/S40夹紧液压缸回程MM/S8022液压系统的工作原理从电机输出的扭矩通过带传动传给液压泵使之运转,之后机床的运作应分为送料、定位、装夹、进刀、退刀,现在来分别分析以上运动的实现过程。1送料板料的传送主要靠皮带传动来实现。2定位4液压系统应设计一个挡料缸,主要用于阻碍板料的继续前进。在送料过程,当板料运行到挡料缸的位置时,与挡料缸上的行程开关碰撞,此时工件也不再向前运行,工件得到了定位。3装夹在完成板料的定位之后,由行程开关的作用,给电气液压联合控制系统一个信号,使夹紧液压缸进入工作状态从而夹紧工件。4进刀夹紧液压缸夹紧工件之后,液压系统的压力急剧上升,达到某一设定值之后,通往主液压缸的溢流阀打开,此时液压系统便开始向主液压缸供油。主液压缸与剪切板料的道具相接,通过主液压缸的运动来实现对板料的剪切。在此过程中选用两个主液压缸驱动刀具剪切。两个串联的液压缸不可能行程完全一致,这样容易产生误差使刀具倾斜,影响剪切的质量等,因此液压系统中应包含同步回路,以使两个主液压缸在每个行程中都能保持同步,消除相应的误差。5退刀(同时松夹)当主液压缸的活塞杆运行到规定的行程时,由于行程开关挡块的作用,不可能再向前运行,此时便完成了剪切。行程开关会给电液控制系统一个信号,通过电液控制系统的作用,使主液压缸反方向运动进行退刀,与此同时,主液压缸的活塞退了一定的行程时,又与活塞杆的端部上的行程挡块发生碰撞,此行程开关发出信号,使夹紧缸回油,板料被松开。当夹紧缸回程时又与行程开关碰撞,行程开关发出相应的信号,使整个液压系统回油,恢复到初始状态,以便于进行下一次剪切。23剪板机液压系统的总体结构剪板机液压系统主要由插装阀主阀、单向阀、电磁阀、梭阀、压力继电器等组成。它的工作流程空载启动空程下行剪切缓冲刀架回程轻压对线剪切中途回程点动上点动下液压剪板机由主机及动力机构两大部分组成。主机部分包括机身、主缸、顶出缸及充液装置等。动力机构由油箱、高压泵、低压控制系统、电动机及各种压力阀和方向阀等组成。电气装置按照液压系统规定的动作程序,选择规定的工作方式,在发出讯号的指令下,完成规定的工艺动作循环。动力机构在电气装置的控制下,通过泵和油缸及各种液压阀,实现能量的转换,5调节和输送,完成各种工艺动作的循环。24主要机构组成液压传动控制是工业中经常用到的一种控制方式,它采用液压完成传递能量的过程。因为液压传动控制方式的灵活性和便捷性,液压控制在工业上受到广泛的重视。液压传动是研究以有压流体为能源介质,来实现各种机械和自动控制的学科。液压传动利用这种元件来组成所需要的各种控制回路,再由若干回路有机组合成为完成一定控制功能的传动系统来完成能量的传递、转换和控制。从原理上来说,液压传动所基于的最基本的原理就是帕斯卡原理,就是说,液体各处的压强是一致的,这样,在平衡的系统中,比较小的活塞上面施加的压力比较小,而大的活塞上施加的压力也比较大,这样能够保持液体的静止。所以通过液体的传递,可以得到不同端上的不同的压力,这样就可以达到一个变换的目的。我们所常见到的液压千斤顶就是利用了这个原理来达到力的传递。图21液压传动基本原理液压传动中所需要的元件主要有动力元件、执行元件、控制元件、辅助元件等。其中液压动力元件是为液压系统产生动力的部件,主要包括各种液压泵。液压泵依靠容积变化原理来工作,所以一般也称为容积液压泵。齿轮泵是最常见的一种液压泵,它通过两个啮合的齿轮的转动使得液体进行运动。其他的液压泵还有叶片泵、柱塞泵,在选择液压泵的时候主要需要注意的问题包括消耗的能量、效率、降低噪音。液压执行元件是用来执行将液压泵提供的液压能转变成机械能的装置,主要包括液压缸和液压马达。液压马达是与液压泵做相反的工作的装置,也就是把液压的能量转换称为机械能,从而对外做功。液压控制元件用来控制液体流动的方向、压力的高低以及对流量的大小进行预期6的控制,以满足特定的工作要求。正是因为液压控制元器件的灵活性,使得液压控制系统能够完成不同的活动。液压控制元件按照用途可以分成压力控制阀、流量控制阀、方向控制阀。按照操作方式可以分成人力操纵阀、机械操纵法、电动操纵阀等。除了上述的元件以外,液压控制系统还需要液压辅助元件。这些元件包括管路和管接头、油箱、过滤器、蓄能器和密封装置。通过以上的各个器件,我们就能够建设出一个液压回路。所谓液压回路就是通过各种液压器件构成的相应的控制回路。根据不同的控制目标,我们能够设计不同的回路,比如压力控制回路、速度控制回路、多缸工作控制回路等。根据液压传动的结构及其特点,在液压系统的设计中,首先要进行系统分析,然后拟定系统的原理图,其中这个原理图是用液压机械符号来表示的。之后通过计算选择液压器件,进而再完成系统的设计和调试。这个过程中,原理图的绘制是最关键的。它决定了一个设计系统的优劣。液压传动的应用性是很强的,比如装卸堆码机液压系统,它作为一种仓储机械,在现代化的仓库里利用它实现纺织品包、油桶、木桶等货物的装卸机械化工作。也可以应用在万能外圆磨床液压系统等生产实践中。这些系统的特点是功率比较大,生产的效率比较高,平稳性比较好。液压作为一个广泛应用的技术,在未来更是有广阔的前景。随着计算机的深入发展,液压控制系统可以和智能控制的技术、计算机控制的技术等技术结合起来,这样就能够在更多的场合中发挥作用,也可以更加精巧的、更加灵活地完成预期的控制任务。25制定液压系统的基本方案根据实际生产对剪板机液压系统的各个功能的要求,挡料缸能对把板料进行定位,以控制板料的长度。液压泵首先向顶出缸供油,使板料被夹紧,以便于剪切。当板料夹紧之后,系统的压力自然上升,液压泵转而向与剪切刀具相连的主液压缸供油,从而驱动刀具下降,对板料进行剪切。剪切完毕之后,主液压缸上升,随后顶出缸的压力下降,从而进行下一次的剪切。该系统应用几个行程开关,从而根据动作要求完成系统的各个动作要求,并且可以对系统实现点动控制。由于剪刀有一定宽度,剪切刀架用两个主缸驱动。一般将两个活塞杆直接和剪切刀架固定连接,液压系统中采用保证两缸运动保持同步的回路,以保证剪切时刀具正常切割不出现误差。液压系统中有三个压料缸和三个托料缸,这样能增大板料被夹紧7的面积,能使剪切质量提高。这些缸都是单作用缸,即都利用弹簧实现回程。3剪板机液压系统原理图31系统原理图8图31剪板机液压原理图液压系统的特点1本系统仅采用了六个插装阀,系统较为简单。这特别使用于大流量系统。2阀1(及其盖板上控制阀8910等)和阀6(及其控制阀16)是典型的插装式力控制阀。前者用于实现多级压力控制,后者则用作顺序阀。93阀2345(及其控制阀)用于实现主缸换向。其中阀5兼作背压阀,用于在剪切刀架空称下行时平衡其直重。32电磁铁动作顺表表31电磁铁动作顺表电磁铁动作1DT2DT3DT4DT5DT启动空载启动空程剪切下行缓冲回程快速回程轻压对线剪切中途回程点动上辅助动作点动下注“”表示断电,“”表示通电。由于剪刀有一定宽度,剪切刀架用两个主缸驱动一般将两个活塞杆直接和剪切架固定连接,液压系统中不再用保证两缸运动保持同步的回路图中有三个压料缸个三个托料缸,这些都是单作用缸,即都利用弹簧实现回路33剪板机液压系统的工作过程1空载启动泵启动时电磁阀10处于中位,插装阀主阀1的弹簧腔直接通回油,泵卸荷2空程下行按下循环开始按钮时,电磁铁2DT3DT通电2DT通电时阀1的弹簧腔和回油路断开,阀1的开启压力亦即系统的最高压力由阀8调定3DT通电使阀2关闭,阀3开启,泵输出的压力油经阀3进入压料缸和托料缸,使板材压紧和托料球缩回当泵的供油压力回升至由主阀6和先导阀16组成的顺序阀的调定压力时,油液进入主缸上腔,这保证了只有在具有足够的压紧力时,剪刀刀架才能开始下行同时主缸下腔的压力必须达到由主阀5和先导阀15组成的压力阀调定压力时油10液才能排出主缸下腔形成背压,此背压起平衡剪切刀架自重的作用,使主缸空程下行的速度仅与泵的供油量有关。3剪切当空程下行至剪刀与被剪板料接触时,主缸上腔的压力进一步升高,压力继电器18发出信号,使4DT通电。此时主阀5的弹簧腔通过单向阀19和电磁阀12的左位和回油连接,主缸下腔又恢复背压,以避免剪切刀架的运动速度失控。4缓冲板料剪断后主缸上负载突然消失,主缸上腔压力降低,压力继电器18复位,4DT断电主缸下腔恢复背压,以避免剪切刀架的运动速度失控。5刀架回程刀架下行到终点时行程开关使3DT断电,2DT,5DT通电。此时阀1开启压力阀经阀4进入主缸下腔,而上腔则经单向阀7,主阀2回油,刀架回程运动。同时压料缸和托料缸(阀17右侧节门打开)进油腔也经阀2通回油,在弹簧作用下退回。当主卸退到原位时,原位行程开关全部电磁铁断电,油路恢复启动前状态,油泵卸荷。6轻压对线按下对刀按钮,电磁铁1DT3DT通电。此时除阀1开启压力(亦即系统的最高压力)由先导阀11调定外,其他情况和下行想同。由于将先导阀11的压力调整得较低,当剪刀接触工件,压力上升后,起剪切力不足以将板料剪断,故可以用来观察并调整板料。4液压系统的计算及液压元件的选择41液压剪板机工作参数要求设计要求主机中能完成空载启动,剪切、和快速回程动作。辅助动作包括剪切中途回程、点动向上、点动向下等动作。设计过程中液压元件所选用型号应正确、有理有据;整个液压系统设计科学、规范、合理。表41设计参数项目单位数值11公称力KN1200最高工作压力MPA32单缸选用压力MPA16推程MM/S40主液压缸回程MM/S80顶出行程MM/S40夹紧液压缸回程MM/S8042液压缸的设计421主液压缸、夹紧液压缸结构尺寸的计算液压缸是液压系统最为常用的执行件,本系统使用活塞缸。液压缸由于活塞两端的有效面积不一样,如果以同样的流量的压力油分别进入液压缸的左右腔,活塞移动的速度与仅有强的有效面积成反比,即油液进入无杆腔时有效面积大,速度慢,进入有杆腔的有效面积小,速度快;而活塞上产生的推力则与进油腔的有效面积成正比。1主液压缸参数设计(1)主液压缸内径D41M2481609457394573PF根据GB/T23461993,取标准值D250MM根据内径D250MM,由机械设计手册表2069可选用B型缸筒外径MM291D表42液压缸内径尺寸系列(摘自GB/T234893)MM810121620253240506380(90)100(110)125(140)160(180)200(220)250(280)320(360)400(450)5002主液压缸活塞杆外径2180/24VMS(42(4362DD12根据GB/T23461993,取标准值D165MM表43活塞外径尺寸系列(GB/T234893)MM4163680180518409020062045100220822501102501025561252801228631403201432701653603)主液压缸有效面积(44)2M016524131DA(4201D25)(420371643A6)(4主液压缸的推力3231106150984FPKN47(5液压缸的拉力由已知条件得2F(6主液压缸的工作力16MPAP顶出42208375RKNPAM顶回顶回顶(48)2夹紧液压缸参数设计(1夹紧液压缸内径221503571037936FKNDMPMPA顶顶顶(49)根据GB/T23461993,取标准值110MM顶D(2夹紧液压缸活塞杆径D顶134380/2VMS(410)178DD顶顶(411)根据GB/T23461993,取标准值80MM顶D(3夹紧液压缸有效面积223211095M4A顶顶(412)2232D847104D顶2顶(413)223280514A顶3(414)(4夹紧液压缸实际顶出力和回程力16MPA95030MM152KN(415)1PR顶出23液压缸运动中的供油量(1)主液压缸的进出油量主液压缸下行的进出油量(4SLVAQ/35401561主上回16)(4/412主下回17)主液压缸回程进出油量(4SLVAQ/438056421主回进18)(4S/642主回回19)(2)夹紧液压缸的进出油量夹紧液压缸顶出行程的进出油量33950148/SQAVL1顶出(41420)32347108/SQAVL顶回(421)夹紧液压缸退回行程的进出油量32471086/SQV回进(422)314957/AL回进(423)422液压缸主要零部件的设计1缸筒结构(1)缸筒分类缸筒的结构和端盖的连接形式、液压缸的用途、工作压力、使用环境以及安装要求等因素有关。端盖分为前端盖和后端盖。前端盖将液压缸的活塞杆腔封闭,并起着为活塞杆导向,防尘和密封的作用。后端盖将缸筒内腔一端封闭,并常常起着将液压缸与其它机件连接的作用。常用的缸筒与端盖的连接有多种形式。本设计采用法兰式连接。缸筒材料一般要求有足够的强度和冲击任性,根据液压缸的参数、用途和毛坯的来源等可选45钢。缸筒毛坯可采用退火的冷拔或热轧无逢钢管。(2)对缸筒的要求1)有足够的强度,能长期承受最高工作压力及短期动态试验压力而不致产生永久变形。2)有足够的刚度,能承受活塞侧向力和安装的反作用力而不致产生弯曲。3)内表面与活塞密封件及导向环的摩擦力作用下,能长期工作而磨损少,尺寸公差等级和形位公差等级足够保证活塞密封的密封性。总之,缸筒是液压缸的主要零件,它与缸盖、缸底、油口等零件构成密封的容腔,用以容纳压力油液,同时它还是活塞的运动“轨迹”。设计液压缸缸筒时,应该正确确定各部分的尺寸,保证液压缸有足够的输出力、运动速度和有效行程,同时还必须15具有一定的强度,能足以承受液压力、负载力和意外的冲击力;缸筒的内表面应具有合适的配合公差等级、表面粗糙度和形位公差等级,以保证液压缸的密封性、运动平稳性和耐用性。(3)对缸筒制造加工的要求1)缸筒内径D采用H7或H8级配合,表面粗糙度R值一般为016032UM,都需要进行研磨。2)热处理调质,硬度HB241285。3)缸筒内径D的圆度、锥度、圆柱度不大于内径公差之半。4)缸筒直线度公差在500MM长度上不大于003MM。5)缸筒端面T对内径的垂直度在直径100MM6)当缸筒为尾部和中部耳轴型时此外,还有通往油口、排气阀孔的内径口必须倒角,不允许有毛边、毛刺、以免划伤密封件。为便于装配和不损坏密封件,缸筒内孔口应倒角。需要在缸筒上焊O15接法兰、油口、排气阀座时,都必须在半精加工以前进行,以免精加工后焊接而引起内孔变形。如欲防止腐蚀生锈和提高使用寿命,在缸筒表面可以镀铬,再进行研磨抛光,在缸筒外表面涂耐油漆。(4)缸筒的计算缸筒壁厚计算根据缸筒内径D和额定工作压力初选缸筒壁厚30M缸筒壁厚验算液压缸的额定压力值应低于一定的极限值,保证工作安全NP221N490380035552SPMPA(424)6ANM故缸筒壁厚合适。(5)缸筒底部厚度计算缸筒底部为平面时,其厚度可以按照四周嵌柱的圆盘强度公式进行近似的计算。1604304328290NPDM(425)取25MM。2活塞的设计(1)活塞的结构形式16活塞根据压力、速度、温度等工作调节来选择密封件的型式,而选定的密封件型式决定了活塞的结构型式。常用的活塞的结构型式分为整体活塞和分体活塞,本机器采用前者。活塞的宽度一般有密封件、导向环(支撑环)的安装沟槽尺寸来决定。(2)活塞的密封活塞的的密封选用准则取决于压力、速度、温度和工作介质等因素。以往活塞常用的密封有间隙密封、活塞环,O型密封圈、Y型密封圈、U型密封圈和V型密封圈等橡胶密封件。近年来选用较多的是以O型密封圈或特殊的外形轮廓橡胶密封件作为副密封件和聚四乙烯(PTFE)主密封件组合在一起使用。活塞的密封件、导向环安装沟槽尺寸以及公差应根据密封件、导向环对沟槽的加工要求来设计。3活塞的材料无导向环的活塞选用高强度铸铁HT200300球墨铸铁和青铜QAL94等材料。有导向环的的活塞选用碳素钢20号、35号及45号,由于本机器有导向环结构,因此活塞选用的材料为45号碳素钢。活塞的加工要求1活塞外径D对内孔的径向跳动公差值按7级或8级精度选取。12端面T对内孔轴线的垂直度公差值按7级精度选取。3活塞D的圆柱度公差按9级、10级或11级精度选取。4如活塞有导向环是,则活塞外径D的公差、表面粗糙度等加工要求则较低。活塞杆活塞杆的结构活塞杆的杆体分为实心杆和空心杆两种,本机器采用前者。本机器的活塞杆外端结构采用外螺纹型。活塞杆的材料本机器活塞杆材料为45号碳素钢,MPAB60AS340热处理方法为调质,表面处理方法为镀铬活塞杆的加工要求13活塞杆的表面须镀硬铬,镀层厚度155,也有的要求镀层厚度300。防MM腐要求特别高的则要求先镀一层软铬或镍,镀后再镀硬铬抛光。活塞杆外径公差;直线度;表面粗糙度,精度要求高时则97FM102RA403。活塞杆外径D的圆柱度公差值,按8级精度选取。RA01活塞的导向环安装在活塞外圆的导向环,具有精确的导向作用,并可吸收活塞运动时产生的侧向力。导向环的主要优点17在缸筒内运动且带有导向环的活塞运动时是非金属接触,因此摩擦系数小,起动时无爬行。活塞安装了导向环后,能改善活塞与缸筒的同轴度,使间隙均匀,故减少了泄漏。导向环采用耐磨材料,使用寿命长,磨损后易于更换。能刮掉杂质,防止杂质嵌入密封圈。导向环用填充聚四乙烯或纤维复合材料制成,具有良好的承载能力。活塞的导向环型式其型式有嵌入式、浮动式和组合式三种型式。3活塞杆的导向、密封和防尘在液压缸的前端盖内有对活塞杆导向的内孔,有对缸筒有杆侧腔密封的密封件;有活塞杆内缩时刮除附着在表层的杂质,灰尘和水份的防尘圈活塞杆的导向活塞杆的导向有无导向套(环)、金属导向套和非金属导向套的三种结构型式。活塞杆的密封和防尘近年来活塞杆的密封件多选用组合式密封圈,一个是用聚四氯乙烯加青铜填料制造的阶梯型密封圈,另一个是O型密封圈。活塞杆的防尘,目前多采用既可以防尘又可以密封的双唇行防尘圈。4缓冲装置缓冲装置的工作原理是当活塞在到达行程终端之前的一定距离内,设法把排油腔内的油液的一部分或全部密封起来,使其通过节流小孔排出,从而使被密封的油液,产生适当的缓冲压力作用在活塞的排油侧上,与活塞的惯性力相对抗,以达到减速制动的目的。缓冲装置的结构形式,可根据节流小孔的流通面积,在缓冲过程中能否自动改变来分类,通常可分为恒节流型和变节流型。5密封件、防尘圈的选用液压缸工作中要达到零泄漏、摩擦小和耐磨损的要求,本机器选用的密封件为O型密封圈加弧型挡圈,而防尘圈选用的是A型橡胶防尘圈。滤油器及滤油装置滤油器是液压系统中对油液进行过滤净化的重要元件。过滤是目前应用最广泛的油液净化方法。过滤是利用多孔隙可透性介质滤除悬浮在油液中的固体颗粒污染物,其主要机制可归纳为直接阻截和吸附作用。按照结构和过滤原理,过滤介质可分为表面和深度型两类。滤油器的主要组成部分有壳体和过滤元件,有的滤油器带旁通阀和堵塞指示或发讯装置,滤芯是滤油器的关键元件,滤油器的性能主要取决于滤芯的结构参数和过滤材料的特性,液压系统用的滤芯有线隙式、片式、烧结式和折叠圆筒式18等结构形式,其中最广泛应用的是折叠圆筒式滤芯,本机选用即网式,名105WU义流量过滤精度为100。MIN50LM423液压缸的装配简图图41液压缸装配图43油箱的设计431油箱结构尺寸设计油箱的主要用途是贮存油液,同时也起到散热的作用,参考相关文献及设计资料,油箱的设计可先根据液压泵的额定流量按照经验计算方法计算油箱的体积,然后再根据散热要求对油箱的容积进行校核。油箱中能够容纳的油液容积按JB/T79381999标准估算,取时,求得其容7积为6258715VQL(426)查表44,取标准值V1600L。表44油箱容积(JB/T79381999)4631025406310018025031540050063080010001250160020003150400050006300可取油箱的长度40LM,宽度30WM,高度20HM。油箱采用普通钢板焊接即可,钢板的厚度分别为油箱箱壁厚3MM,箱底厚度5MM,因为箱盖上需要安装其他液压元件,因此箱盖厚度取为10MM。为了易于散热和便于对油箱进行搬移及维护保养,取箱底离地的距离为160MM。为了更好的清洗油箱,取油箱底面倾斜角度为。2O19432油箱油液温升验算液压传动系统在工作时,有压力损失、容积损失和机械损失,这些损失所消耗的能量多数转化为热能,使油温升高,导致油的粘度下降、油液变质、机器零件变形等,影响正常工作。为此,必须控制温升T在允许的范围内,如一般机床2530;数控机床25;粗加工机械、工程机械和机车车辆3540。液压系统的功率损失使系统发热,单位时间的发热量(KW)可表示为12P(427)式中系统的输入功率(即泵的输入功率)(KW);P1系统的输出功率(即液压缸的输出功率)(KW)。2若在一个工作循环中有几个工作阶段,则可根据各阶段的发热量求出系统的平均发热量。对于本次设计的组合机床液压系统,其工进过程在整个工作循环中所占时间比例为2109642T(428)因此系统发热和油液温升可用工进时的发热情况来计算。工进时液压缸的有效功率(即系统输出功率)为(429)KWFVP03761250这时大流量泵通过顺序阀10卸荷,小流量泵在高压下供油,所以两泵的总输出功率(即系统输入功率)为120418PQPQIP(430)由此得液压系统的发热量为037IIHKW(431)温升小于普通机床允许的温升范围,因此液压系统中不需设置冷却器。44管件的设计管路在液压系统中主要用来把各种元件及装置连接起来传输能量。用于液压系统中的管路,主要有金属硬管和耐压软管。对管路的基本要求是要有足够的强度,能承受系统的最高冲击压力和工作压力。管路与各元件及装置的各连接处要密封可靠,不20泄漏,决不能松动。管路在安装前必须清洗干净,管内不允许有锈蚀、杂质和粉尘等。在液压系统中,主要使用硬管,它比用软管安全可靠,而且经济。管内油液的推荐流速对吸油管道取(一般取以下)SM3160S1对压油管道取(压力高时取最大值,反之取最小值;管道较长752时取小值;油液粘度大时取小值,反之去大值)对矩管道及局部收缩处,可取S6275对回油管道可取S47145液压泵的选择液压泵是液压系统中主要的能量转换元件,液压泵把机械能转换成液压能。液压泵的主要参数1排量或)RCM3(L理论排量液压泵每转一周排出的液体体积,也叫几何排量。容载排量在规定最低工作压力下,泵每转一周排出的液体容积。有效排量在规定工况下泵每转一周实际排出的液体体积。2流量理论流量液压泵在单位时间内排出的液体体积,其值等于理论排量和泵的转速之乘积。有效流量在某种压力和温度下泵在单位时间内排出的液体体积,也叫实际流量。瞬间流量液压泵在运转中,在某一时间点排出的液体体积。平均流量根据在某一时间段内泵排出的液体体积计算出的,单位时间内泵排出的液体体积,其值为在该时间段内各瞬间流量的平均值。额定流量泵在额定工况下的流量。3压力额定压力液压泵在正常工作条件下,按实验标准规定能连续运转的最高压力。最高压力液压泵能按实验标准规定,允许短暂运转的最高压力。工作压力液压泵实际工作时的压力。4转速或角速度MINRSL额定转速在额定工况下,液压泵能长时间持续正常运转的最高转速。最大转速在额定工况下,液压泵能超过额定转速允许短暂运转的最高速度。21最低转速液压泵在正常工作条件下,能运转的最小转速。5功率PKW输入功率驱动液压泵运转的机械功率。输出功率液压泵输出液压功率,其值为工作压力与有效流量之乘积。6效率溶剂效率液压泵输出的有效流量与理论流量的比值。液压机械效率液压泵的液压转矩与实际输入转矩的比值。IM总效率液压泵输出的液压功率与输入的机械功率的比值。T设计的液压系统最高工作压力主液压缸工作行程,主液压缸的无PA61025杆腔进油量为IN182LVAQ进工主液压缸的有杆腔进油量为MI5632进回设选主液压缸工作行程工作压力最高()工件顶出后不需要高压。主PA6105液压缸工作行程(即压制)流量为735L/MIN,主液压缸工作回程流量为165L/MIN。本机选用定量式叶片泵。液压泵的流量是根据液压缸的最大体积流量和液控顺序阀的流量损失和三位四通M型电磁还向阀的流量损失三者之和算出来的。本机选用的液压泵的型号为2YBE排量10200ML/R压力16MPA转速6002000R/MIN46阀的选择461流量控制阀简介对流量控制阀的主要性能要求是1当阀前后的压力差发生变化时,通过阀的流量变化要小;2当油温发生变化时,通过节流阀的流量变化要小;3要有较大的流量调节范围,在小流量时不易堵塞,这样使节流阀能得到很小的稳定流量,不会在连续工作一段时阀后因节流口堵塞而使流量减小,甚至断流;224当阀全开时,液流通过节流阀的压力损失要小;5阀的泄漏量要小。对于高压阀来说,还希望其调节力矩要小。插装阀(逻辑阀),是一种较新型的液压元件,它的特点是通流能力大,密封性能好,动作灵敏、结构简单,因而主要用于流量较大系统或对密封性能要求较高的系统。根据计算,选用YF3E20B型阀,流量18L/MIN。图42插装阀逻辑单元A结构原理图;B图形符号图43插装阀的组成(1)先导控制阀(2)控制盖板(3)逻辑单元(4)阀块体23462插装阀的工作原理插装阀的结构及图形符号如图42所示。它由控制盖板、插装单元(由阀套、弹簧、阀芯及密封件组成)、插装块体和先导控制阀(如先导阀为二位三通电磁换向阀,见图43)组成。由于这种阀的插装单元在回路中主要起通、断作用,故又称二通插装阀。二通插装阀的工作原理相当于一个液控单向阀。图中A和B为主油路仅有的两个工作油口,K为控制油口(与先导阀相接)。当K口无液压力作用时,阀芯受到的向上的液压力大于弹簧力,阀芯开启,A与B相通,至于液流的方向,视A、B口的压力大小而定。反之,当K口有液压力作用时,且K口的油液压力大于A和B口的油液压力,才能保证A与B之间关闭。插装阀与各种先导阀组合,便可组成方向控制阀、压力控制阀和流量控制阀。463方向控制插装阀图44插装阀用作方向控制阀(A)单向阀;B二位二通阀;C二位三通阀D二位四通阀24图45插装阀用作压力控制阀(A)溢流阀;B电磁溢流阀插装阀组成各种方向控制阀如图44所示。图44(A)为单向阀,当PAPB时,阀芯关闭,A与B不通;而当PBPA时,阀芯开启,油液从B流向A。图44(B)为二位二通阀,当二位三通电磁阀断电时,阀芯开启,A与B接通;电磁阀通电时,阀心关闭,A与B不通。图44(C)为二位三通阀,当二位四通电磁阀断电时,A与T接通;电磁阀通电时,A与P接通。图44(D)为二位四通阀,电磁阀断电时,P与B接通,A与T接通;电磁阀通电时,P与A接通,B与T接通。根据计算,插装阀主阀1选用Z2AHQ164,实际流量735L/MIN。插装阀主阀2选用Z2AHQ164,实际流量735L/MIN。插装阀主阀3选用Z1AHQ16,实际流量735L/MIN。插装阀主阀4选用Z1AHQ164,实际流量735L/MIN。插装阀主阀5选用Z2AHQ164,实际流量735L/MIN。插装阀主阀6选用Z2AHQ164,实际流量165L/MIN。47电机的选择与计算目前,电动机的种类繁多,价格、性能差别比较大,本着经济、实用的指导思想对电动机类型及型号进行优化选择是十分重要的。选择电动机种类应在满足生产机械对拖动性能的要求下,优先选用结构简单、运行可靠、维护方便、价格便宜的电动机。电动机种类选择时应考虑的主要内容有1电动机的机械特性应与所拖动生产机械的机械特性相匹配;2电动机的调速性能(调速范围、调速的平滑性、经济性)应该满足生产机械的要求。对调速性能的要求在很大程度上决定了电动机的种类、调速方法以及相应的控制方法;3电动机的启动性能应满足生产机械对电动机启动性能的要求,电动机的启动性能主要是启动转矩的大小,同时还应注意电网容量对电动机启动电流的限制;254电源种类在满足性能的前提下应优先采用交流电动机;5经济性一是电动机及其相关设备(如启动设备、调速设备等)的经济性;二是电动机拖动系统运行的经济性,主要是要效率高,节省电能。根据机械的负载性质和生产工艺对电动机的启动、制动、反转、调速等要求选择电动机的类型。直流电动机可实现快速频繁的无级快速启动、制动和反转;具有过载能力大、能承受频繁的冲击负载,优良的调速性能,调速平滑、精确、方便和范围广等特点。电动机的工作环境是由生产机械的工作环境决定的。在很多情况下,电动机工作场所的空气中含有不同分量的灰尘和水分,有的还含有腐蚀性气体甚至含有易燃易爆气体;有的电动机则要在水中或其他液体中工作。灰尘会使电动机绕组黏结上污垢而妨碍散热;水分、瓦斯、腐蚀性气体等会使电动机的绝缘材料性能退化,甚至会完全丧失绝缘能力;易燃、易爆气体与电动机内产生的电火花接触时将有发生燃烧、爆炸的危险。因此,为了保证电动机能够在其工作环境中长期安全运行,必须根据实际环境条件合理地选择电动机的防护方式。电动机的外壳防护方式有开启式、防护式、封闭式和防爆式几种。选择电动机容量应进行一些必要的分析和计算,具体可按以下三个步骤进行1计算负载功率WP2根据负载功率,预选电动机的额定功率,使,尽量接近DPDWWP3校验预选电动机的发热、过载能力和启动能力。校验的方法较多,工作量很大,而且准确度也很难把握。在实际工作中常采用统计分析法和类比法。类比法就是在调查同类机械所采用电
- 温馨提示:
1: 本站所有资源如无特殊说明,都需要本地电脑安装OFFICE2007和PDF阅读器。图纸软件为CAD,CAXA,PROE,UG,SolidWorks等.压缩文件请下载最新的WinRAR软件解压。
2: 本站的文档不包含任何第三方提供的附件图纸等,如果需要附件,请联系上传者。文件的所有权益归上传用户所有。
3.本站RAR压缩包中若带图纸,网页内容里面会有图纸预览,若没有图纸预览就没有图纸。
4. 未经权益所有人同意不得将文件中的内容挪作商业或盈利用途。
5. 人人文库网仅提供信息存储空间,仅对用户上传内容的表现方式做保护处理,对用户上传分享的文档内容本身不做任何修改或编辑,并不能对任何下载内容负责。
6. 下载文件中如有侵权或不适当内容,请与我们联系,我们立即纠正。
7. 本站不保证下载资源的准确性、安全性和完整性, 同时也不承担用户因使用这些下载资源对自己和他人造成任何形式的伤害或损失。

人人文库网所有资源均是用户自行上传分享,仅供网友学习交流,未经上传用户书面授权,请勿作他用。