0045-汽车玻璃升降器落料拉深复合模设计【全套12张CAD图+说明书】
收藏
资源目录
压缩包内文档预览:(预览前20页/共52页)
编号:925410
类型:共享资源
大小:2.16MB
格式:ZIP
上传时间:2016-11-27
上传人:hon****an
认证信息
个人认证
丁**(实名认证)
江苏
IP属地:江苏
30
积分
- 关 键 词:
-
汽车玻璃
升降
器落料拉深
复合
设计
全套
12
十二
cad
- 资源描述:
-
摘 要
这份报告主要研究的是作为汽车零部件之一的活塞销的流动缺陷。在联合冷挤压制活塞销的工艺中,起皱就是一种流动缺陷,它是由死金属区引起的。具有这种缺陷的部件带有很明显的外部特征,特征是被一微小而且厚的块状物嵌入材料中,这种缺陷对保证尺寸精度和降低材料损失是不利的,活塞销的这种缺陷对于其强度和疲劳寿命也有不利的影响。因此,在工艺设计的早期预测并防止这种缺陷是非常重要的。防止其产生的最好方法就是通过控制材料流动来限制或减少死金属区。有限元模拟分析方法被应用于流动缺陷研究分析当中,这份研究报告提出了通过去除死金属区防止产生流动缺陷的新工艺方法——有限元分析法。将有限元分析的结果与实验结果做比较,结果表明有限元分析的结果与实验结果相符合。
关键词:流动缺陷;活塞销钉;材料流动控制;前后双向冷挤压;死金属区;有限元分析








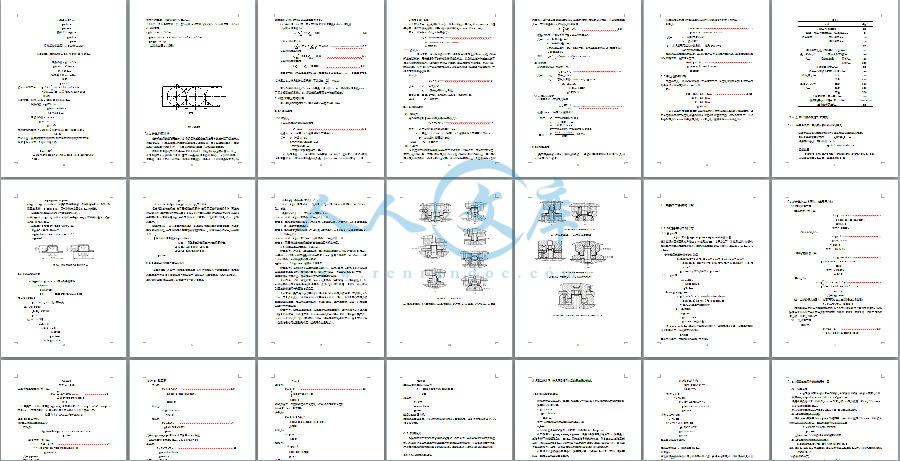

- 内容简介:
-
说明书 玻璃升降器复合拉深 模的设计 1 摘 要 这份报告主要研究的是作为汽车零部件之一的活塞销的流动缺陷。在联合冷挤压制活塞销的工艺 中,起皱就是一种流动缺陷,它是由死金属区引起的。具有这种缺陷的部 件带有很明显的外 部特征,特征是 被一微小而且厚的块状物嵌入材料中,这种缺陷对保证尺寸精度和降低材料损失是不利的,活塞销的这种缺陷对于其强度和疲劳寿命也有不利的影响。因此,在工艺设计的早期预测并防止 这种缺陷是非常重要的。防止其产生的最好方法就是通过控制材料流动来限制 或减少死金属区 。有限元模拟分析方法被应用于流动缺陷研究分析当中, 这份研究报告提出了通过去除死金属区防止产生流动缺陷的新工艺方法 有限元分析法。将有限元分析 的结果与实验结果做比较,结果表明有限元分析的结果与实验结果相符合 。 关键词 : 流动缺陷; 活塞销钉 ;材料流动控制;前后双 向冷挤压;死金属区;有限元分析 2 of a in In of a a is a of by is in a to be is to of in of it is to in of is or of to of E in 2003 FE 3 目 录 1 前言 . 6 1 1 玻璃升降器的功用及拉深模的设计要求 . 6 2 冲裁工艺设计 . 8 冲裁工艺计算 . 8 工艺力和功的计算 . 8 压力机的选择 . 10 模具总体设计 . 10 模具类型的确定 . 操作方式的确定 . 定位、联接型式的确定 . 模具压力中心的确定 . 12 模具精度的确定 . 12 具闭合高度的初定 . 12 定位装置 . 12 卸料装置 . 12 卸料装置的选择 . 13 弹性元件的设计 . 13 落料凹凸模的设计 . 14 凸模结构的确定 . 14 凹模结构确定 . 15 凹凸模工作部分尺寸设计 . 15 凸凹模工作表面技术要求 . 17 凸凹模材料 . 17 导向装置 . 17 导向装置的选择 . 17 导向装置尺寸确定 . 17 模具其它主要零部件的设计 . 19 板料定位装置的设计 . 19 4 栓和销钉的选用 . 20 3 工艺方案选择 . 21 冲压件的工艺确定 . 21 压件的工艺分析 . 21 零 件材料的分析 . 23 定工艺方案和模具形式 . 24 料尺寸的计算 . 25 定排样方案 . 26 定排样、裁板方案 . 26 算拉深次数 . 28 深冲压力的计算 . 29 料过程 . 29 深过程 . 30 型过程 . 31 压设备的选择 . 32 析比较和确定工艺方案 . 33 算毛坯尺寸需先确定翻边前的半成品尺寸。 . 33 算拉深次数 . 34 . 35 4 主要工艺参数的计算 . 39 定各中间工序尺寸 . 39 算各工序压力,选用压力机 . 40 具设计 . 44 具结构形式选择 . 44 料弹簧的选择 . 45 具工作部分尺寸和公差计算 . 45 具其它零件的结构尺寸计算 . 47 作原理: . 48 次拉深 . 48 次拉深 . 48 次拉深 . 48 5 . 48 结论 . 50 致 谢 . 51 6 1 前言 1 1 玻璃升降器的功用及拉深 模的设计要求 现在许多轿车门窗玻璃的升降 (关闭和开启 )已经抛弃了摇把式的手动升降方式,一般都改用按钮式的电动升降方式,即使用电动玻璃升降器来控制,也就是常说的 “ 电动门窗 ” 。 轿车用的电动玻璃升降器多是由电动机、减速器、导绳、导向板、玻璃安装托架等组成。因导绳的材料或制作工艺方式不同,又分为绳轮式、软轴式和塑料带式三种电动玻璃升降器。前二种是用钢丝绳做为导绳,后一种是用塑料带做为导绳。 以普遍使用的绳轮式电动玻璃升降器为例,它是由电动机、减速 器、钢丝绳、导向板和玻璃安装托架等零部件组成,安装时门窗玻璃固定在玻璃安装托架上,玻璃导向槽与钢丝绳导向板平行。 开启电动机,由电动机带动减速器输出动力,拉动钢丝绳移动玻璃安装托架,迫使门窗玻璃作上升或下降的直线运动。而塑料带式电动玻璃升降器的导绳采用塑料带,带上有孔,用来移动和定位塑料带,控制门窗玻璃的升降。 电动玻璃升降器结构的关键是电动机和减速器,这两者是组装成一体的,其中电动机采用可逆性永磁直流电动机,电动机内有两组绕向不同的磁场线圈,通过开关的控制可做正转和反转,也就是说可以控制门 窗玻璃的上升或下降。 电动机是由双联开关按钮控制,设有升、降、关等三个工作状态,不操纵时开关自动停在 “ 关 ” 的位置上。操纵电路设有总开关(中央控制)和分开关,两者线路并联。总开关由驾车者,控制全部门窗玻璃的开闭,而各车门内把手上的分开关由乘员分别控制各个门窗玻璃的开闭,操作十分便利。 电动机的质量直接关系到电动玻璃升降器的正常工作,它一定要具有体积小、重量轻、防护等级高、噪声低、电磁干扰小、运行可靠等特点。现代轿车已广泛应用微电子技术,电机工作会发射电磁波干扰其它电器件的工作;前几年通用汽车公司一篇售后分析报告显示,近 40%的电动玻璃升降器故障是由电动机密封性差引起的。因此,减少电磁干扰和解决电机密封性问题巳成为近年汽车电机技术的热门话题。 90 年代中期以来,电动玻璃升降器的控制机构技术发展很快,电子模块控制形式大量应用于批量装车,并设有安全保护装置。例如博世公司生产的电动玻璃升降器系统,在电动机中埋植磁环,感应电机转速,在电子模块中埋植霍尔元件,感应 7 电流,并通过电子模块控制对电动机的过流、过压及过热保护,而且当玻璃上升途中遇到人力障碍时会自动识别而反向运行,防止乘员夹伤。 8 2 冲裁工艺设计 冲裁工艺计算 工艺力和功的计算 冲裁力是指冲裁过程中的最大抗力,它是合理地选用冲压设备吨位和校检模具强度的重要依据。影响冲裁力的因素很多,主要有材料的机械性能、厚度、冲裁件周边长度、模具间隙以及刃口锋利程度等。 ( 1) 冲裁力的计算 采用平刃凸模和凹模冲裁时,其冲裁力的计算公式 0 中 0P 冲裁力; L 冲裁件的周长( 材料厚度( 材料的抗剪强度。 如图(一)所示,工件尺寸为, k=260,L=284,05,44,则 4)1 4 21 3 0( 查附表 1 2/500 ,工件厚度 ,故 虑到模具刃口的钝化,凹模和凸模间隙不均匀,材料性能的波动和材料厚度的偏差等因素,实际所需冲裁力还应增加 30%,即 P 则 2 7 476 40 5 9 ( 2) 卸料力和推件力的计算 当冲裁工作完成以后,冲下的工件(或废料)沿径向发生弹性收缩,同时,工件废料还要力图恢复弹性穹弯。这两种弹性恢复的结果导 致工件(或废料)硬塞在凹模内,废料(或工件)箍紧在凸模上。从凸模上将工件(或废料)卸下来的力叫卸料力。从凹模内顺着冲裁方向将工件(或废料)推出的力叫推料力。很显然,这些力在选择压力机的吨位和设计模具时必须加以考虑。影响这些力的因素很多,主要有:材料的力学性能和厚度、工件形状和尺寸、模具间隙、排样的搭边大小及润滑情况等。由于这些因素的影响规律很复杂,难以准确计算。生产中常采用下列公式 中 P, 分别是卸料力、推件力( N) K , 分别是卸料力系数、推件力系数 P 冲裁力( N) n 同时梗塞在凹模内的工件数 参 见表 2h 取为 8,则 ( 3) 冲裁功的计算 选择冲裁设备时,除了要计算冲裁力,使压力机的公称压力大于冲裁力以外,还要进行冲裁功的验算,使压力机的每次行程功不超过额定的数值,以保证其电极不过载,飞轮转速不致下降太多。平端刃口的冲裁功按下式计算 1000/ 中 W 冲裁功 (t 材料厚度( P 冲裁力( N) m 系数,一般取为 10 0 0/ 2 7 2 0 0/ 压力机的选择 冲压设备选择是冲压工艺过程设计的一项重要内容,它直接关系到设备的安全和使用的合理,同时也关系到冲压工艺过程的顺利完成及产品质量、零件精度、生产效率、模具寿命、材料的性能与规格、成本的高低等一系列重要的问题。 ( 1) 设备类型的选择 设备类型的选择要依据冲压件的生产批量、零件尺寸的大小、工艺方法与性质及冲压件的尺寸、形状等要求来进行,除此之外,还应考虑到设备的精度与刚度以及生产现场的实际可能。压力机的刚度是由床身刚度、传动刚度和导向刚 度三部分组成。如果刚度较差,负载终了和卸载时模具间隙会发生很大的变化,影响冲压件的精度和模具寿命。综合考虑以上各因素后参照表 7和表 7,并结合工厂现有设备情况,此冲模选用开式双柱可倾压力机。 ( 2) 设备规格的选择 在选定设备类型后,进一步根据冲压件的大小、模具尺寸及变形力来确定设备规格。冲裁时,压力机必须大于或等于冲裁各工艺力的总和,本工件冲裁模采用弹压卸料装置和下出件的模具,故 6 0 4 1 3 6 9 5 2 7 2 81选 为了提高设备的工作刚度、冲压零件的精度及延长设备的寿 命,要求设备容量留有 4030%的余 ,并结合工厂现有设备情况选用吨位为 100号为 模具总体设计 总体设计的任务包括: (1)模具类型的确定; (2)操作方式、进料方式的确定; (3)定位、联接等型式的确定; (4)模具压力中心的确定; (5)模具闭合高度的初定。 11 模具类型的确定 根据冲压件的形状、尺寸、精度要求等确定模具类型。 根据 料件的形状(如图所示),是有四段圆弧组成的椭圆形件,形状比较简单,呈中心轴对称,尺 寸精度要求也不高为 此可以考虑选用简单模。 操作方式的确定 虽然该冲压件是进行大批量生产的,但考虑到工厂的现有生产条件,为了降低产品的生产成本,而且落料件的尺寸精度要求不高,所以采用手工操作方式或半自动操作方式。 定位、联接型式的确定 为了保证模具正常安全工作,模具中的定位和联接件一定要可靠。 ( 1) 模板 在上下模板上安装全部模具零件,构成模具的总体和传递压力。模板不仅应该具有足够的强度,而且还要有足够的刚度。本模具将上模板与凸模、凸模固定板及垫板等装配成一体,用 四个螺钉紧固构成模具的上部分;下模板则与凹模等组成模具的下模不分。此外上下模两部分还分别各对称低用两个圆柱销销紧,以防转动和错位。上下模架均采用标准模架,是用 造而成。 ( 2) 模柄 模具的上部分通过模柄固定在冲床滑块上。模柄的结构形式很多,常见的结构形式有带凸缘模柄、压入式模柄、旋入式模柄、浮动式模柄等等。本模具选用压入式模柄,通过压配合和附加的销钉与模板固定联接以防转动与松动。模柄材料选用优质碳素钢中的 45号钢。 ( 3) 凸模固定板与垫板 用凸模固定板将凸模联接固定在模板的正确位置上。凸模 固定板有圆形和矩形两种,考虑到模具的总体结构这里选用凸模固定板。固定板与凸模采用过渡配合,压装后将凸模尾部与固定板一起磨平。凸模固定板用 45号钢加工。 ( 4) 坯料的定位和定向 见 12 模具压力中心的确定 根据图( 1) 所示的落料件可知,落料件形状呈轴对称,其压力中心即为工件的几何中心,因此不需要进行模具压力中心的计算。 模具精度的确定 落料件的精度要求不高为 照表 2定模具可按 具闭合高度的初定 据 知,模 具选用 开式双柱可倾压力机,此压力机所允许的最大装模高度为 380小装模高度为 250定模具闭合高度在 270, 375范围之内即可。 定位装置 为了保证模具正常工作并冲出合格的制件,要求在送进的平面内,坯料(块料、条料)相对于模具的工作零件处于正确的位置。坯料在模具中的定位分两个方面:送料方向上的定位(控制送料的进距)称挡料和在与送料垂直方向上的定位称送进导向。常见的送进导向方式有导销式和导尺式,而限定条料送进距离的方式有挡料销定距和侧刀定距。本模具采用导料销 方式来对条料进行导向和挡料销方式来对条料送进进行定距。导料销的结构简单,制造容易,只要保持条料沿导料销一侧送进,即可保证条料的正确的送进方向。这里把首次冲裁定距的挡料销和后续冲裁的定距用挡料销设计为一整体,其结构形式如图()所示,而且要注意把其正上方的卸料板挖空,其工作原理是:利用弹簧的可压缩性来获得第一次定距和后续定距的距离差,当模具进行第一次冲裁时,只要把条料沿导料销往里送料,碰到挡料销时使挡料销条料一起运动而压缩弹簧,当挡料销运动到不可继续运动的的时候即可完成条料的第一次定距,而在后续的冲裁中只要条料 搭边碰到挡料销就不需要继续往前运动,即可完成后续冲裁的定距。这样设计的挡料销尾柄远离凹模刃口有利于凹模强度,对坯料的定距既方便又准确,且结构也不复杂。 卸料装置 设计卸料装置的目的,是将冲裁后卡箍在凸模上或凸凹模上的冲件或废料卸掉, 13 保证下次冲压正常进行。常用的卸料方式有刚性卸料和弹性卸料两种。刚性卸料是采用固定卸料板结构,常用于较硬、较厚且精度要求不高的工件冲裁后卸料。当卸料板只起卸料作用时,与凸模的间隙随材料厚度的增加而增大,单边间隙取( t,当固定卸料板还要起到对凸模的导向作用 时,卸料板与凸模的间隙应小于冲裁间隙。弹性卸料板具有卸料和压料的双重作用,主要用在冲裁料后在 下的板料,由于有压料的作用,冲裁件比较平整。弹压卸料板与弹性元件、卸料螺钉组成弹压卸料装置。卸料板与凸模之间的单边间隙选择( t,若弹压卸料板还要起到对凸模导向作用时,两者的配合间隙应小于冲裁间隙。 卸料装置的选择 本冲裁件的板料厚度 t=为了保证冲裁件平整,使工件在下一道工序中容易定 位,这里选用弹性卸料装置。由于本模具已选用了标准导向模架,不需要卸料板对凸模起导向作用,所以卸料板与凸模的间隙可取大一点,单边间隙取0 . 1 6 m 80 . 20 . 2 。 弹性元件的设计 弹性元件通常选用弹簧和橡皮,但考虑到模具结构的 具体情况,这里选用弹簧作为卸料装置中的弹性元件。卸料装置中的弹簧,一般不进行强度设计,而是按标准选用。 由 料力 1) 据模具结构初定 4根弹簧,每根分担的卸料力 29 88 . 45 3 . 7/ 4/P 5 nP 每根弹簧的预压力 9 9 5 5预 ( 2) 据预压力 P 预 和模具结构尺寸,由附表 6选 84弹簧,其 8 83 4 0 01 均。 ( 3) 检验弹簧是否满足总1,参照附表 6弹簧负荷曲线,计算出弹簧特性数据如表 2 表 2弹簧的规格 14 综上所述,序号 851 F 总 ,但是序号 85弹簧最合适,因其它弹簧太长,会使模具高度增加,特别是使凸模 增高。 由附表 65弹簧规格见表 5 表 285 号弹簧规格 由此可知,弹簧的装配高度为 F 预 =120 12=108 ( 落料凹凸模的设计 凸模结构的确定 凸模结构通常分为两大类。一类是镶拼式,另一类式整体式整体式中,根据加工方法的不同,又分为直通式和台阶式。根据落料件的外形尺寸和形状,凸模采用台阶 式。凸模简图如图示 此落料模式采用弹压卸料装置的简单模,落料凸模长度应按下式确定 211 中 1h 凸模固定板长度 2h 卸料板厚度 H 弹簧的自由长度 弹簧序号 H/1/1= 预 / 总 /4 5 6 7 8 9 = F 预 + F 工作 + F 修模 , F 工作 = +3= F 修模 =5簧外径 D 材料直径 d 最大负荷 由高度 H 最大压缩量 距 t 600400N 12015 1H 弹簧握座的深度 h 卸料板下平面高出凸模下平面的距离 212201 2 028 L 138 凹模结构确定 常用凹模洞口类型如图 5中( a, b, c)型为直筒式凹模,其特点是制造方便,刃口强度高,刃后工作部分尺寸不变, d, e 型锥筒式刃口,在凹模内不补给材料,修壁磨损小,但刃口强度差,刃磨后刃口径向尺寸略有增大。落料件使用材料为 锈钢,强度高,加工硬化显著,对凹模洞口强度要求高,且此模具采用下出件 方式,故选用 凹凸模工作部分尺寸设计 冲裁件的精度主要取决于凸模和凹模刃口的尺寸和公差。和的间隙值也靠它来保证。因此,正确计算凸模和凹模刃口的尺寸和公差,是冲裁模设计只中的一项重要工作。计算时综合考虑模具的磨损规律,冲裁变形规律,冲裁件的精度要求和模具制造的特点。 从生产实践中可以发现: ( 1)于凸模与凹模之间存在间隙,使落下的料或冲出的孔都带有锥变。且在冲裁过程中落料件的大端尺寸等于凹模尺寸,冲孔件的小端尺寸等于凸模尺寸。 ( 2)在测量和使用中,落料外径是以大端尺寸为基准,冲孔件 以小端尺寸为基准 ( 3)冲裁时凸模和凹模要与工件或废料发生摩擦,磨损的结果时凸模尺寸变小,凹模尺寸变大,间隙总是增大的。 计算凸模与凹模刃口尺寸和公差时,应遵循下述原则: ( 1)料模时,应以凹模尺寸为基础,靠缩小凸模尺寸以获得间隙;设计冲孔模时,应以凸模尺寸为基准,靠扩大凹模尺寸获得间隙 ( 2)根据冲裁模在使用过程中的磨损规律:凹模的磨损使落料件轮廓尺寸增大,故设计落料模时,必须使凹模内径的基本尺寸接近或等于工件的最小极限尺寸;凸模的磨损使冲孔件径向尺寸减小,故设计冲孔模时,必须使凸模外径接近或等于工件的最 大极限尺寸。 ( 3)无论是落料或冲孔,模径磨损后间隙总是增大的,为了使模具在合理间隙 16 范围内有较大磨损量,新模具应取最小合理间隙值。 ( 4)选择冲孔模刃口制造公差时,应考虑工件的公差要求。如果对刃口公差要求过高,会使模具制造困难,增加生产成本,延长制模周期。如果要求过低,则生产出来的工件可能不合格,降低了模具的寿命。 由于模具加工方法不同,凸模和凹模刃口部分尺寸的计算公式与制造公差的标准也不同,刃口尺寸的计算方法可分为两种情况:凸模与凹模分开加工和凸模与凹模配合加工。由于冲压件的形状不规则,为了保证凸凹模间有 一定的间隙值,采用配合加工。根据以上原则,以凹模为基准靠缩小凸模尺寸获得间隙,且凹模工作部分的尺寸均属第一类尺寸 1,即凸模或凹模磨损后会增大的尺寸,故按下式计算 0m a x( ) 中 工件的基本尺寸( 落料凸或凹模的刃口尺寸( 工件的公差; x 系数,为了避免多数冲裁件尺寸都极限尺寸。 落料件公差等级为 表 工件外形尺寸的极限偏差值为 见表 2 d,按工件精度由表 2 75.0x , 故 凹模的工作尺寸: 尺寸为 284时, )(凹D 尺寸 为 260时, )(凹D 尺寸为 288时, )(凹D 尺寸为 210时, )(凹D 所以凹模的基本尺寸分别为 , , 查表 1此冲裁模合理得间隙范围为 17 落料凸模的基本尺寸与凹模相同,分别为 : , , 以 双面间隙与落料凹模配做。 凸凹模工作表面技术要求 凸凹模加工后的工作表面,应该平整圆滑,特别是侧面,由于存在着两种不同尺寸的四个平面共同组成,其两个平面之间的过渡一定要圆滑,不允许有尖角存在,其他部分不允许有影响使用的砂眼,裂纹和机械损伤等缺陷。 凸模工作表面,特别是凸模的 端面处,在冲裁过程中对材料的摩擦阻力有助于冲裁。因此,在不影响零件表面质量的情况下,凸模端面的粗糙度此凸模选用 aR m凸模工作圆柱面粗糙度为 m凹模工作表面对材料的摩擦阻力对冲裁是有害的,应尽量减少和避免,所以凹模工作型腔表面粗糙度要求比较高,这里取aR m 凸凹模材料 根据模具的工作条件和性能要求,同时考虑到工厂锻造、热处理和机械加工的具体情况,凸凹模的材料均选用 导向装置 导向装置的选择 为保证模具工业工作时凸凹模间的间隙分布均匀 ,延长模具使用寿命 ,便于模具安装和冲压生产的安全 ,这里使用了具有导向装置的标准模架。 生产中常用的模架有对角导柱模架,后侧导柱模架,两侧导柱模架和四角导柱模架。为了使用操作比较方便,而且落料件,简单 ,中型,参照表 2用对角导柱模架。这种模架使用操作方便,横向送料和纵向送料均可,而且导向比后侧导柱模架稳定。 导向装置尺寸确定 根据 确定的凹模周界尺寸 396D 外,参照附表 8用0为2 9 02 4 54 0 04 0 0 A 型模架, 2305023045 和 号 B 型导柱, 5314045 和5314050 号 18 ( 1)上模座主要尺寸 参照附表 8上模座主要尺寸列表如下: 表 2模座主要尺寸 ( 2)下模座主要尺寸 参照附表 8下模座主要尺寸列表如下: 表 2模座主要尺寸 ( 3)导柱和导套主要尺寸 参照附表 8导柱主要尺寸列表如下: H h 1 2 S 5 45 410 410 560 560 475 475 65 100 h 1 2 S 5 45 410 410 560 560 475 475 65 100 19 表 2柱主要尺寸 参照附表 8套主要尺寸列表如下: 表 2套主要尺寸 模具其它主要零部件的设计 板料定位装置的设计 为了保证模具正常工作并冲出合格的制件,要求在送进的平面内,坯料(块料、条料)相对于模具的工作零件处于正确的位置。坯料在模具中的定位分两个方面:送料方向上的定位(控制送料的进距)称挡料和在与送料垂直方向上的定位称送进导向。常见的送进导向方式有导销式和导尺式,而限定条料送进距离的方式有挡料销定距和侧刀定距。本模具采用导料销方式来对条料进行导向和挡料销方式来对条料送进进行定距。导料销的结构简单,制造容易,只要保持条料沿导料销一侧送进,即可保证条料的正确的送进方向。这里把首次冲裁定距的挡料销和后续冲裁的定距用挡料销设计为一整体,其结构形式如图()所示,而且要注意把其正上方的卸料板挖空,其工作原理是:利用弹簧的可压缩性来获得第一次定距和后续定距的距离差,当模具进行第一次冲裁时,只要把条料沿导料销往里送料,碰到挡料销时使挡料销条料一起运动而压缩弹簧,当挡料销运动到不可继续运动的的时候即可完成条料的第一次定距,而在后续的冲裁中只要条料搭边碰到挡料销就不需要继续往前运动,即 可完成后续冲裁的定距。这样设计的挡料销尾柄远离凹模刃口有利于凹模强度,对坯料的定距既方便又准确,且结构也不复杂。 d l 0 0 230 65 d D L H l 油槽数 140 53 20 3 20 栓和销钉的选用 模具中广泛使用内六角螺钉和带槽的柱头螺钉。螺钉和销钉的头部应倒角或者倒圆,还应淬火处理提高材料的硬度,以保证使用寿命;销钉与孔采用 H7/壁的表面粗糙度应达 ( 1)上模板于固定板之间的固定 查表 8 ,选用 28 内六角形螺钉四个, 35 号钢,热处理硬度面氧化。
- 温馨提示:
1: 本站所有资源如无特殊说明,都需要本地电脑安装OFFICE2007和PDF阅读器。图纸软件为CAD,CAXA,PROE,UG,SolidWorks等.压缩文件请下载最新的WinRAR软件解压。
2: 本站的文档不包含任何第三方提供的附件图纸等,如果需要附件,请联系上传者。文件的所有权益归上传用户所有。
3.本站RAR压缩包中若带图纸,网页内容里面会有图纸预览,若没有图纸预览就没有图纸。
4. 未经权益所有人同意不得将文件中的内容挪作商业或盈利用途。
5. 人人文库网仅提供信息存储空间,仅对用户上传内容的表现方式做保护处理,对用户上传分享的文档内容本身不做任何修改或编辑,并不能对任何下载内容负责。
6. 下载文件中如有侵权或不适当内容,请与我们联系,我们立即纠正。
7. 本站不保证下载资源的准确性、安全性和完整性, 同时也不承担用户因使用这些下载资源对自己和他人造成任何形式的伤害或损失。

人人文库网所有资源均是用户自行上传分享,仅供网友学习交流,未经上传用户书面授权,请勿作他用。