目录
1 引言
1.1模具生产的重要性.........................................1
1.2我国塑料模具技术现状.....................................1
1.3 模具技术的发展趋势.......................................2
2 电磁继电器外壳注塑模具设计
2.1 制品工艺性能分析.........................................7
2.2 PS的加工工艺及成型性能..................................9
2.3 分型面的选择............................................10
2.4 型腔数目的确定..........................................11
2.5 浇注系统的设计..........................................11
2.5.1 浇注系统的组成......................................11
2.5.2 浇注系统的布置......................................12
2.5.3 主流道的设计........................................12
2.5.4 分流道的设计........................................13
2.5.5 浇口的设计..........................................13
2.6 注塑机的选择............................................14
2.6.1 最大的注塑量........................................14
2.6.2 注塑压力............................................14
2.6.3 锁模力..............................................15
2.6.4 模板尺寸的确定......................................16
2.6.5 模具安装板的校核....................................17
2.6.6 开模行程的校核......................................17
2.7 侧抽芯与侧分型面机构的设计..............................17
2.8 排气问题................................................18
2.9 合模导向机构的设计......................................19
2.9.1 导向机构的作用......................................19
2.9.2 模架的选择..........................................20
2.9.3 导柱导向机构的设计..................................20
2.10 顶出机构的设计.........................................21
2.10.1 顶出机构的驱动方式..................................22
2.10.2 顶出机构的设计原则..................................22
2.10.3 顶出行程............................................23
2.10.4 顶出位置的设置......................................23
2.10.5 脱模力的计算........................................24
2.10.6 导向装置............................................24
2.10.7 顶杆的形式..........................................24
2.11 复位机构的设置.........................................24
2.12 温度调节系统对塑料件质量的影响.........................25
2.13 模具的作用原理.........................................27
结论......................................................... 28
致谢......................................................... 29
参考文献.................................................. 30
1.引言
1.1 模具生产的重要性
模具生产水平的高低已成为衡量一个国家产品水平高低的重要标志,因为模具在很大程度上决定着产品的质量、效益、和新产品的开发能力。随着我国加入WTO,我国模具工业的发展将面临新的机遇和挑战。
我国的模具工业的发展,日益受到人们的重视和关注。“模具式工业生产的基础工艺装备”也已经取得了共识。在电子、汽车、电机、电器、仪器、仪表、家电和通信等产品中,60%~80%的部件都要依靠模具成型。用模具生产制件所具备的高精度、高复杂程度、高一致性、高生产效率和低消耗,是其它加工制造方法所不能比拟的。模具又是“效率放大器”,用模具生产的最终产品价值,往往是模具自身价值的几十倍、上百倍。目前全世界模具年产值约为1000亿美元,日、美等工业发达国家的模具工业产值已超过机床工业。近几年,我国模具工业一直以每年15%左右的增长速度发展,2009年,我国模具总产值超过800亿元人民币。
1.2 我国塑料模具技术现状
1)塑料模
今年来,我国塑料模有很大的进步。在大型塑料模方面,已能生产34英寸大屏幕彩电塑壳模具,6kg大容量洗衣机全套塑料模具及汽车保险杆和整体仪表板等塑料模具。在精密塑料模具方面,已能生产多型腔小模数齿轮模具和600腔塑封模具,还能生产厚度仅为0.08mm的1模2腔的航空杯模具和难度较高的塑料门窗挤出模等。内热式或外热式热流道装置得以采用,少数单位采用了具有世界先进水平的高难度针阀式热流道模具,完全消除了制件的浇口痕迹。气体辅助注射技术已成功得到应用。在精度方面,塑料模具制造精度可达0.02~0.05mm(国外可达0.005~0.01mm),分型面接触间隙为0.02mm,模板的弹性变形为0.05mm,型面的表面粗糙度值为Ra0.2~0.25μg,塑料模具寿命已达100万次(国外可达300万次),模具制造周期仍比国外长2~4倍。这些标志着模具总体水平的参数指标与国外相比尚有较大差距。
2)模具CAD/CAE/CAM
模具CAD/CAE/CAM技术是改造传统模具生产方式的关键技术,能显著缩短模具设计与制造周期,降低生产成本,提高生产质量。它使技术人员能借助于计算机对产品、模具结构、成形工艺、数控加工及成本等进行设计和优化。以生产家用电器的企业为代表,陆续引仅了相当数量的CAD/CAM系统,实现了CAD/CAM集成,并采用了CAE技术对成型过程进行计算机模拟等,数控加工的使用率也越来越高,取得了一定的经济效益,促进和推动了我国模具CAD/CAE/CAM技术的发展。
近年来,我国自开发的有上海交大的冲裁模CAD/CAM系统;北京北航海尔软件有限公司的CAXA系列软件;吉林金网络模具工程研究中心的冲压CAD/CAE/CAM系统等,为进一步普及模具CAD/CAM技术创造了良好条件。目前我国计算机辅助技术软件开发,尚处于较低水平,需要知识和经验的积累。
3)模具标准件
模具标准件对缩短模具制造周期,提高质量,降低成本,能起很大作用。因此,模具标准件越来越广泛地应得到采用。模具标准件主要有冷冲模架、塑料模架、推杆和弹簧等。新型弹性元件如氮气弹簧亦已在推广应用中。
4)模具材料与热处理
模具材料的质量、性能、品种和供货是否及时,对模具的质量和使用寿命以及经济效益有着直接的重大影响。近年来,国内一些模具钢生产企业已相继建成和引进了一些先进工艺设备,使国内模具钢品种规格不合理状况有所改善,模具钢质量有较大程度的提高。但国产模具钢钢种不全,不成系列,多品种、精料化、制品化等方面尚待解决。另外,还需要研究适应玻璃、陶瓷、耐火砖和地砖等成型模具用材料系列。
模具热处理使关系能否充分保证模具钢性能的关键环节。国内大部分企业在模具淬火时仍采用盐熔炉或电炉加热,由于模具热处理工艺执行不严,处理质量不高,而且不稳定,直接影响模具使用寿命和质量。近年来,真空热处理炉开始广泛用于模具制造。

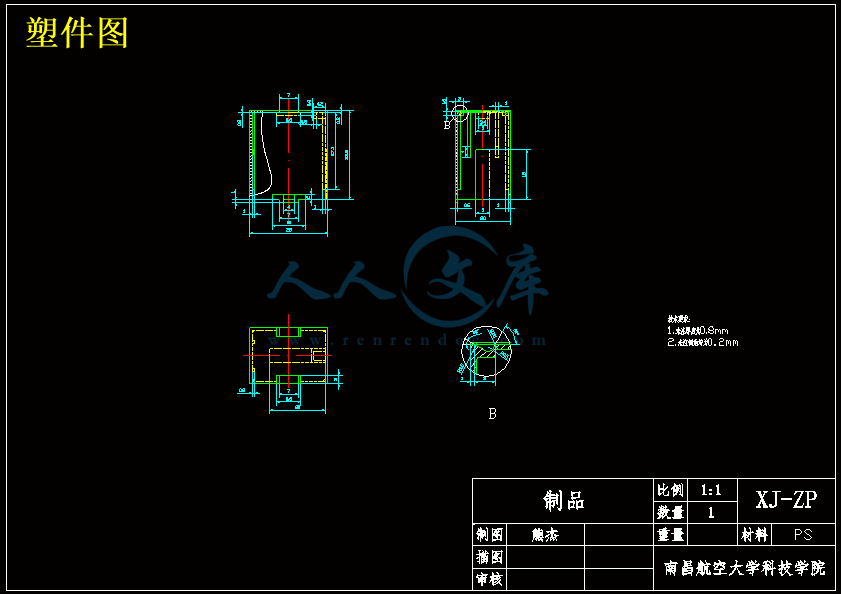
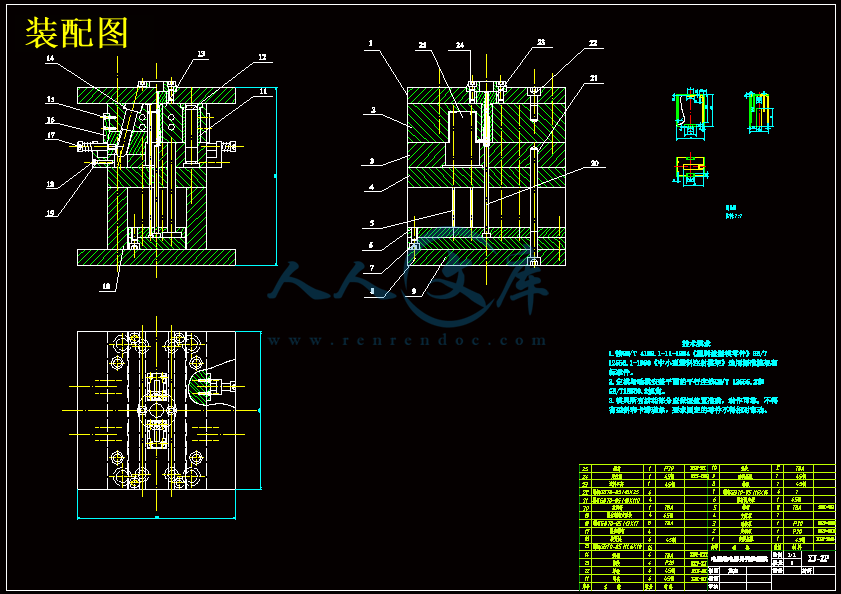
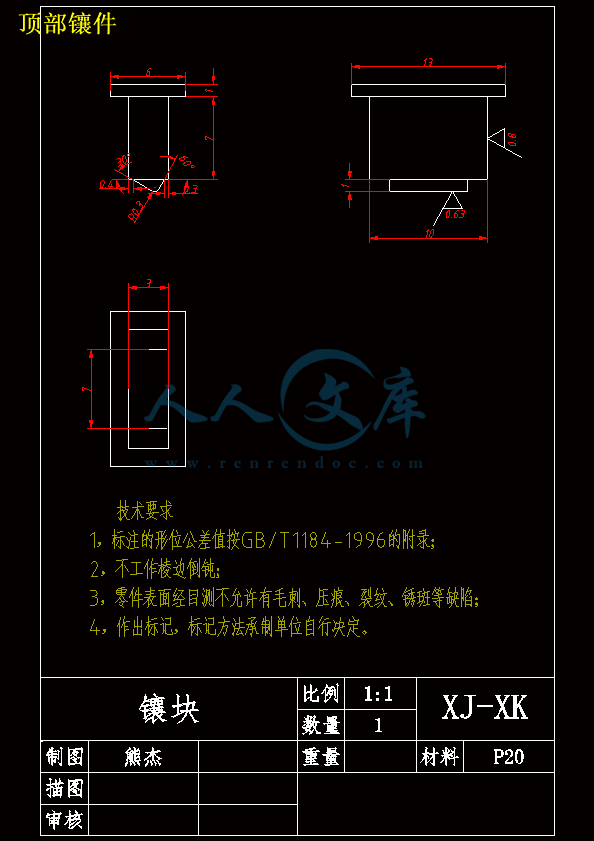


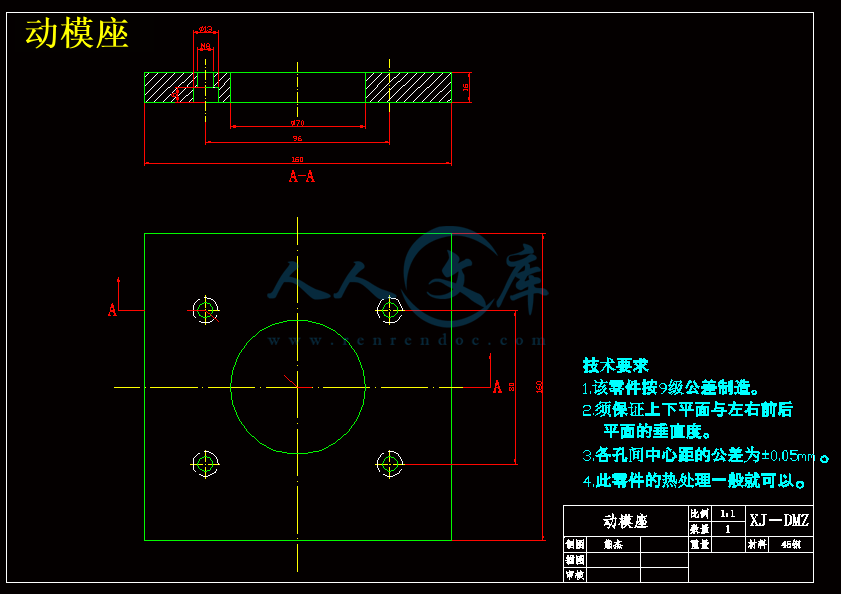
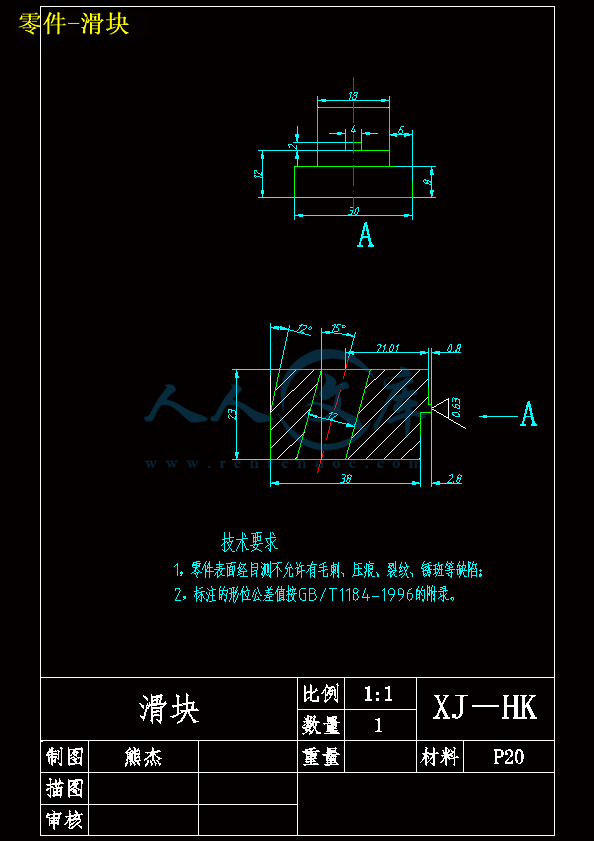







