目录
第1章 塑料模具 2
1.1 塑料模具的基本概念 2
1.2 塑料模具的类型 2
1.2.1 注射模具 2
1.2.2 其他类型的塑料模具 3
第2章 照相机外壳注塑模具设计 4
2.1 照相机前面板设计 4
2.1.1 数码相机的发展与未来 4
2.1.2 黄金分割点 (golden section ratio) 4
2.1.3 注塑件结构分析.技术分析.注塑成型工艺分析 5
2.1.4 产品资料 6
2.2 注塑成型设备选择 6
2.2.1 概述 6
2.2.2 注塑成型设备的分类 7
2.2.3 选注塑机 8
2.3 浇注系统的设计 10
2.3.1 浇注系统设计的原则 10
2.3.2 主流道设计 11
2.3.3 冷料井的设计 13
2.3.4 分流道的设计 15
2.3.5 浇口的设计 19
2.4 模具成型零件的设计 21
2.4.1 型腔数目的确定 21
2.4.2 确定型腔的排列方式 22
2.4.3 分型面的设计 24
2.4.4 成型零部件的结构设计 27
2.4.5 确定成型零部件的工作尺寸 29
2.5 导向及脱模机构的设计 33
2.5.1 概述 33
2.5.2 脱模机构的设计 33
2.5.3 导向机构的设计 39
2.6 侧向抽心机构的设计 42
2.6.1 确定侧向抽芯机构的类型 42
2.6.2 斜导柱抽芯机构的设计 43
2.6.3 抽芯块的设计 44
2.6.4 开模行程和抽芯距的确定 48
2.6.5 斜导柱直径的确定 49
2.6.6 斜导柱长度的确定 50
2.7 温度调节系统的设计 50
2.7.1 温度调节的必要性 51
2.7.2 冷却系统的设计原则 52
2.7.3 冷却回路的设计 53
2.7.4 确定冷却管道的布局方式 56
2.8 其他模具零件的确定 57
2.8.1 定模导向镶块 57
2.8.2 动模导向镶块 57
2.9 确定模具总体尺寸以及参数校核 58
2.9.1 确定模具总体尺寸,选购标准模架 58
2.9.2 注塑机参数校核 58
第3章 结论 61
参考文献: 62
致 谢 63
第1章 塑料模具
1.1 塑料模具的基本概念
塑料模具是利用其特定形状去成型具有一定形状和尺寸的塑料制品的工具,它对塑料零件的制造质量和成本起着决定性作用。
那么,究竟什么是塑料模具?首先,得从塑料说起,塑料是由从石油生产出来的合成树脂加入增塑剂、稳定剂、填料等物质组成的,原料为小颗粒状或粉状。如果将这些小颗粒状塑料加热熔化成液体,注入到一个具有所需产品形状的型腔中,待塑料冷却后取出来,就得到了与型腔形状一样的塑件,这个具有型腔的东西称为模具,因为它专门用于制作塑料件,所以通常称为塑料模具。
现代塑料制品的生产中,合理的加工工艺、高效的设备和先进的模具是必不可少的三项重要因素,尤其是塑料模具对实现塑料加工工艺要求,塑料制品使用要求和造型设计起着重要的作用。高效率的全自动设备只有配上相应的先进模具才能发挥出其应有的作用,随着塑料制品的品种和产量需求的增大,对塑料模具也提出了越来越高的要求,促使塑料模具不断向前发展。
1.2 塑料模具的类型
塑料的种类很多,其成型方法也有很多,不同的塑料成型方法所要求的模具的原理和结构都不相同,按照成型方法的不同,可以将塑料成型模具分为以下几种类型.
1.2.1 注射模具
注射成型技术的基本概况
注射成型又称注射模塑,是热塑性塑料制件的一种主要成型方法。除个别热塑性塑料外,几乎所有的热塑性塑料都可以用此方法成型。近年来,注塑成型也成功地用来成型很多热固性塑料制件。
注射成型可成型各种形状的塑料制件,它的特点是成型周期短,能一次成型外形复杂、尺寸精密、带有嵌件或侧孔的塑料制件,且生产效率高,易于实现自动化生产,所以广泛用于塑料制件的生产中,据有关资料统计,注射成型在当今塑料制品成型中占有大约50%的比重,世界上塑料成型模具的产量半数以上是注塑模具。但是,由于注射成型的设备及模具制造费用较高,还不适合单件及小批量生产的塑件。
注射成型所用的设备是注射机。目前注射机的种类很多,但实际生产中普遍采用的是柱塞式注射机和螺杆式注射机。注射机的类型的确定一般参照注射的原料(塑料)的种类。
注射成型工艺过程
注射成型工艺过程包括:成型前的准备、注塑成型过程和塑件的后处理三个阶段。
1.成型前的准备
为了使注射过程能够顺利的进行并保证塑件的质量,在成型前应进行一系列必要的准备工作。包括原料外观的检验和工艺性能的测定、物料的预热和干燥、嵌件的预热、料筒的清洗(柱塞式料筒可使用拆卸清洗法,而螺杆式料筒可采用对空注射法清洗)、脱模剂的选用。
2.注射成型过程
注射成型过程包括加料、加热塑化、加压注射、保压、冷却定型、脱模等工序。但从实质上讲主要是塑化、注射充模和冷却定型这几个基本过程。应该指出的是,若冷却速度过快或模温不均,则塑件会由于冷却不均匀而导致各部分收缩不一致,使塑件产生内应力,因此,冷却速度必须适当,这个很大程度上取决于冷却系统的设计是否合理。
3.塑件的后处理
由于塑件不均匀或由于塑料在型腔内的结晶和冷却不均匀,或由于金属嵌件的影响和塑件的二次加工不当等原因,塑件内部不可避免的存在一些内应力,从而导致塑件在使用过程中产生变形或者开裂。为了解决这些问题,要对塑件进行适当的后处理,主要方法是退火和调湿处理。退火处理主要是消除塑件内应力,调湿处理主要是使制品到达吸湿平衡,使塑件的颜色、性能以及尺寸得到稳定。
1.2.2 其他类型的塑料模具
压缩成型模具(又称压塑模),吹塑模具,挤出模具(又称挤出机头),除以上四种塑料模具外,还有压注模具、泡沫塑料成型模具等。
第2章 照相机外壳注塑模具设计
2.1 照相机前面板设计
2.1.1 数码相机的发展与未来
照相机自1839年由法国人发明以来,已经走过了将近200年的发展道路。在这200年里,照相机走过了从黑白到彩色,从纯光学、机械架构演变为光学、机械、电子三位一体,从传统银盐胶片发展到今天的以数字存储器作为记录媒介。笑看浮云遮望眼,瞬间沧海变桑田,数码相机的出现正式标志着相机产业向数字化新纪元的跨越式发展,人们的影像生活也由此得到了彻底改变。????






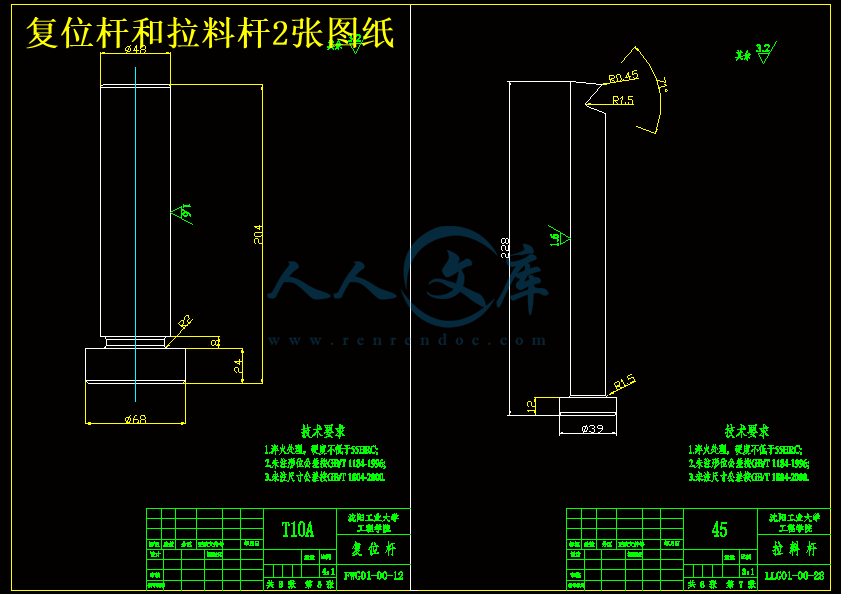


