0283-汽车前灯罩冲压成形工艺及落料拉伸复合模具设计【全套8张CAD图+说明书】
收藏
资源目录
压缩包内文档预览:(预览前20页/共35页)
编号:965002
类型:共享资源
大小:1.42MB
格式:ZIP
上传时间:2016-12-31
上传人:hon****an
认证信息
个人认证
丁**(实名认证)
江苏
IP属地:江苏
30
积分
- 关 键 词:
-
汽车
灯罩
冲压
成形
工艺
拉伸
复合
模具设计
全套
cad
- 资源描述:
-
汽车前灯罩的冲压模具设计
摘要: 本文介绍了汽车前灯罩的冲压模具设计。设计内容包括产品零件工艺分析、模具设计以及主要零件制造工艺的确定等。
此零件结构复杂,需要多道工序完成,基本工序包括落料、拉深、冲孔、弯曲、翻边等。针对此产品件,应明确设计路线,确定设计方案,构思模具结构。首先对产品进行结构和尺寸分析,利用AUTOCAD绘出零件的三向视图,确定尺寸;之后确定优选的工艺方案(落料、拉深—胀形、冲孔—胀形、冲孔—修边、冲孔—弯曲—冲孔、翻边);然后再进行必要的工艺计算和尺寸计算,利用AUTOCAD完成第一道工序—落料拉深复合模装配图,并绘出各非标零件;然后同样用AUTOCAD完成第二道工序—胀形冲孔复合模;对其它工序进行分析,确定每道工序的细节工作;最后完成设计。
关键词:灯罩 冲压 模具 工艺 设计

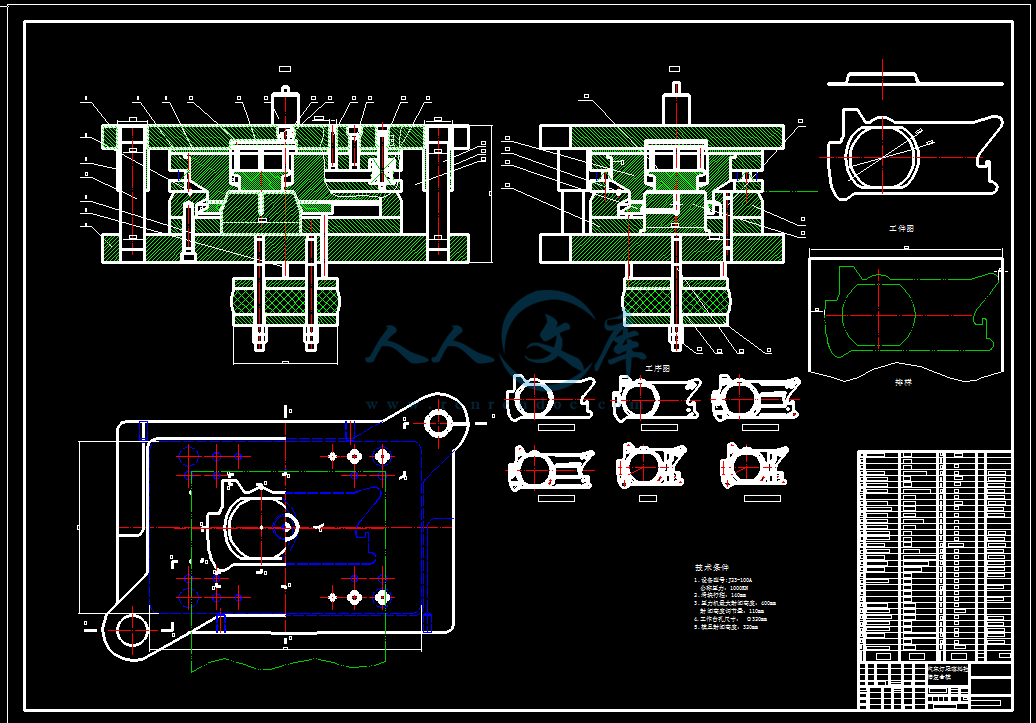

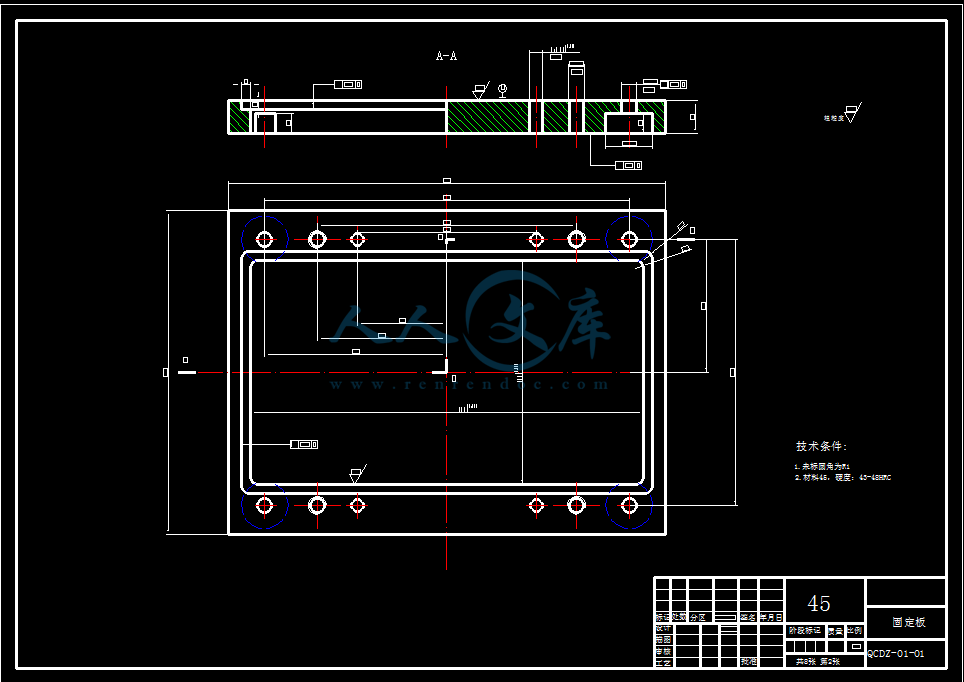








- 内容简介:
-
1 目录 前 言 . 3 1 绪论 . 4 国冲压模具业发展现状 . 4 国冲压模具制造技术发展趋势 . 4 2 汽车前灯罩成形工艺分析 . 7 析制件的冲压工艺性 . 7 料 . 7 构分析 . 7 寸精度与表面粗糙度 . 7 定冲压工艺方案 . 7 具形式 . 8 坯展开计算 . 8 深部分 . 8 曲部分 . 9 它部分 (直接由 . 9 3 落料拉深复合模设计 . 10 样 . 10 定冲压方向和冲压中心 . 10 定冲压方向 . 10 定压力中心 . 11 定拉深次数 . 12 定冲裁力和拉深力 . 13 裁力 . 13 边力 . 13 深力的计算 . 13 择压力机 . 14 用标准模架 . 15 作部分尺寸计算 . 15 深工作部分尺寸 . 15 料工作刃口部分尺寸计算 . 16 具总体设计 . 18 作零件 . 18 它主要零件 . 20 具结构尺寸验算 . 24 4 胀形冲孔复合模设计 . 25 形部分 . 25 形力与冲裁力的计算 . 26 形变形力 . 26 2 裁 力 . 27 定压力中心 . 27 择压力机 . 28 用标准模架 . 29 作部分刃口尺寸计算 . 29 冲裁刃口尺寸进行计算 . 29 形刃口尺寸的说明及确定 . 29 具结构设计 . 30 要工作零件 . 30 它零件设计 . 31 结 论 . 33 参考文献 . 34 致谢 . 35 3 前 言 模具在汽车、拖拉机、飞机、家用电器、工程机械、 动力机械、冶金、机床、兵器、仪器仪表、轻工、日用五金等制造业中,起着极为重要的作用,模具是实现上述行业的钣金件、锻件、粉末冶金件、铸件、压铸件、注塑件、橡胶件、玻璃件和陶瓷件等生产的重要工艺装备。采用模具生产毛坯或成品零件,是材料成形的重要方式之一,与切削加工相比,具有材料利用率高、能耗低、产品性能好、生产效率高和成本低等显著特点。 大学几年所学对于知识的海洋来说也许还不够说沧海一粟,但是对于具体的个人来说却是会算有很大收获的。此次毕业设计不仅是对自己所学的一次全面总结,而且是对我们所具备的综合能力 的一次考查,更是我们将理论与实践相结合的实际运用前的一次实际应用。 此次设计所依据的工件是在工厂实际进行生产的。在参观了工厂已采用的生产方式和生产设备、并在老师认真、耐心的指导下进行了此次设计。为了高质量的完成此次设计我用了大量的时间和精力查阅了很多资料,包括模具设计手册、冷冲模设计、模具设计大典和模具图册等,相信对我以后在实际工作中的应用会有很大益处。 因我个人经验和水平有限,设计之中难免会存在不合理之处,请各位老师多多批评指正。 这次设计是在指导老师的精心指导和严格要求下 完成的。老师的严谨求实的治学态度,待人以诚的宽广胸怀以及渊博的知识为我们树立了榜样。在此向老师致以最诚挚的谢意! 4 1 绪论 国冲压模具业发展现状 改革开放以来,随着国民经济的高速发展,市场对模具的需求量不断增长。近年来,模具工业一直以 15%左右的增长速度快速发展,模具工业企业的所有制成分也发生了巨大变化,除了国有专业模具厂外,集体、合资、独资和私营也得到了快速发展。浙江宁波和黄岩地区的“模具之乡”;广东一些大集团公司和迅速崛起的乡镇企业,科龙、美的、康佳等集团纷纷建立了自己的模具 制造中心;中外合资和外商独资的模具企业现已有几千家。 近年许多模具企业加大了用于技术进步的投资力度,将技术进步视为企业发展的重要动力。一些国内模具企业已普及了二维 陆续开始使用 别厂家还引进了 成功应用于冲压模的设计中。 以汽车覆盖件模具为代表的大型冲压模具的制造技术已取得很大进步,东风汽车公司模具厂、一汽 模具中心等模具厂家已能生产部分轿车覆盖件模具。此外,许多研究机构和大专院校开展模具技术的研究和开发。经过多年的努力,在模具提高模具质量和缩短模具设计制造周期等方面做出了贡献。 例如,吉林大学汽车覆盖件成型技术所独立研制的汽车覆盖件冲压成型分析件,华中理工大学模具技术国家重点实验室开发的注塑模、汽车覆盖件模具和级进模 件,上海交通大学模具 件等在国 内模具行业拥有不少的用户。 虽然中国模具工业在过去十多年中取得了令人瞩目的发展,但许多方面与工业发达国家相比仍有较大的差距。例如,精密加工设备在模具加工设备中的比重比较低;多先进的模具技术应用不够广泛等等,致使相当一部分大型、精密、复杂和长寿命模具依赖进口。 国冲压模具制造技术发展趋势 模具技术的发展应该为适应模具产品“交货期短”、“精度高”、“质量好”、“价格低”的要求服务。达到这一要求急需发展如下几项: (1) 全面推广 模具 术是模具设计制造的发展方向。随着微机软件的发展和进5 步,普及 术的条件已基本成熟,各企业将加大 术培训和技术服务的力度;进一步扩大 术的应用范围。计算机和网络的发展正使企业、跨院所地在整个行业中推广成为可能,实现技术资源的重新整合,使虚拟制造成为可能。 (2) 高速铣削加工 国外近年来发展的高速铣削加工,大幅度提高了加工效率,并可获得极高的表面光洁度。另外,还可加工高 硬度模块,还具有温升低、热变形小等优点。高速铣削加工技术的发展,对汽车、家电行业中大型型腔模具制造注入了新的活力。目前它已向更高的敏捷化、智能化、集成化方向发展。 (3) 模具扫描及数字化系统 高速扫描机和模具扫描系统提供了从模型或实物扫描到加工出期望的模型所需的诸多功能,大大缩短了模具的在研制制造周期。有些快速扫描系统,可快速安装在已有的数控铣床及加工中心上,实现快速数据采集、自动生成各种不同数控系统的加工程序、不同格式的 据,用于模具制造业的“逆向工程”。模具扫描系统已在汽车、摩托车、 家电等行业得到成功应用,相信在“十五”期间将发挥更大的作用。 (4) 电火花铣削加工 电火花铣削加工技术也称为电火花创成加工技术,这是一种替代传统的用成型电极加工型腔的新技术,它是有高速旋转的简单的管状电极作三维或二维轮廓加工 (像数控铣一样 ),因此不再需要制造复杂的成型电极,这显然是电火花成形加工领域的重大发展。国外已有使用这种技术的机床在模具加工中应用。预计这一技术将得到发展。 (5) 提高模具标准化程度 我国模具标准化程度正在不断提高,估计目前我国模具标准件使用覆盖率已达到30%左右。 国外发达国家一般为 80%左右。 (6) 优质材料及先进表面处理技术 选用优质钢材和应用相应的表面处理技术来提高模具的寿命就显得十分必要。模具热处理和表面处理是否能充分发挥模具钢材料性能的关键环节。模具热处理的发展方向是采用真空热处理。模具表面处理除完善应发展工艺先进的气相沉积 (、等离子喷涂等技术。 (7) 模具研磨抛光将自动化、智能化 模具表面的质量对模具使用寿命、制件外观质量等方面均有较大的影响,研究自6 动化、智能化的研磨与抛光方法替代现有手工操作,以提高模具表面质 量是重要的发展趋势。 (8) 模具自动加工系统的发展 这是我国长远发展的目标。模具自动加工系统应有多台机床合理组合;配有随行定位夹具或定位盘;有完整的机具、刀具数控库;有完整的数控柔性同步系统;有质量监测控制系统。 7 2 汽车前灯罩成形工艺分析 析制件的冲压工艺性 料 08钢 材料厚度 t=1冲压模具设计与制造技术 1 抗拉 b 335 450( N/ ) 抗剪 260 360( N/ 弹性模数 E 190000 (N/ 屈服点 s 200 ( N/ ( %) 32% 构分析 该零件是汽车前灯的壳罩,形状特征包括弯曲面,拉深面,压凸包,加强筋,外沿边等,并且是非对称结构,较为复杂。产品零件需要经过多道工序才能完成,基本工序应包括拉深、冲孔、弯曲、胀形、翻边等。且制件水平方向有不同层次的水平面,都是通过拉深、弯曲、胀形工序制成,表明成形工序较为复杂。拉深底部冲出一大孔,尺寸精度相对比较高。制件应注意尺寸之间的影 响,以及工序之间相互的影响。 寸精度与表面粗糙度 尺寸精度按 表面粗糙度 定冲压工艺方案 根据产品零件的外形结构和尺寸精度要求,首先确定是不能用级进模工作,因为如果用级进模,工作零件会发生相互的干涉现象,模具结构也相当复杂,并且不能保证零件的尺寸精度和位置精度。那么将其成形过程分为单工序完成。每工序可以设计为复合模或单工序模工作,以确保能够生产出合格的产品零件。 该零件成形的基本工序包括落料、拉深、冲孔、胀形、弯曲、修边、翻边。比较如下三个方案: 方案一 :先落料冲孔,后拉深,再胀形,最后弯曲翻边; 方案二:先落料拉深,后冲孔,再胀形,再冲孔,最后弯曲翻边; 8 方案三:先落料拉深,再胀形冲孔,再胀形冲孔,最后弯曲翻边。 方案一如果先冲孔后拉深,肯定会影响拉深的质量和孔之间的定位尺寸,并且会影响其后的成形工序,提高了经济成本。那么对于此件上的孔应该分开冲,比如胀形上的孔,拉深底部的大孔。为了保证零件的质量,方案一的成形工序还不足。 方案二单从模具结构来看过于简单,中间三步都是简单的单工序模。而且方案也不完善,从零件的结构来看,胀形部分不能一步完成。需要从两个方向 分别胀形,才能保证零件的质量 方案三解决了前两个方案的缺点,但所生产的零件的尺寸精度不高。 总结以上三种方案,得出方案四: 落料、拉深 胀形、冲孔 胀形、冲孔 修边、冲孔 弯曲 冲大孔、翻边 方案四虽然分六步工序完成,简单的说需要六套模具。对于模具制造工作比较繁重,成本也比较高。但是由于是批量生产,而且根据零件外形和尺寸精度来说,这是优佳的方案。 具形式 成形过程分六步完成,即需六套模具。 第一套:落料、拉深倒装复合模; 第二套:胀形、冲孔复合模; 第三套:胀形、冲孔复合模; 第四套:修 边、冲孔复合模; 第五套 : 弯曲单工序模; 第六套:冲孔、翻边复合模; (由于工作量的原因,主要设计前两套模具) 坯展开计算 深部分 2 21221 ( 1= 85+74) =159 = 21222 ( 1 =1/2 3 A =1/2 9 32101 22 ( 1 =故:拉深部分面积 曲部分 1 1 3303 6 A ( 1 =( 113=43203 6 0677753 6 0622 A ( 1 =( 7+=2102 它部分 (直接由 出) A 总面积: 030201 ( 1 =考虑到修边情况,以及工序之间产生的尺寸 影响,取 A=50000 10 3 落料拉深复合模设计 样 由中国模具设计大典 用轧制薄钢板 1 500 1500 单行直排 a= 轮廓尺寸: 04 条料宽: B=a+毛坯修边量 = 进距: 条数: 00/(余 每条个数: 500/(余 ) 总个数: N= 利用率: =( 7 62117) /( 500 1500) =定冲压方向和冲压中心 定冲压方向 确定冲压方向应考虑的问题 保证凸模能够进入凹模; 开始拉深时凸模与拉深毛坯接触面积要大; 开始拉深时凸模与拉深毛坯的接触面应靠近中间; 开始拉深时凸模与拉深毛坯的接触面要大,要分散; 压料面各部分进料阻力力求均匀。 根据零件的形状特征和上述的要求,确定为反向拉深,水平放置。 11 定压力中心 图 据零件形状的复杂性, 利用解析法求出压力中心 如图 按 1: 1的比例画出凸模工作部分剖面的轮廓图,取了 21个重心点,其各坐标( x,y)和长度 01( 02( 3( 04( 5( 06( 7( 08( 9( 010( 11( 012( 13( 014( 15( 016( 17( 018( 2 019( 020( 6 021( : 2121212122110 ( 2 =(312 由: 2121212122110 ( 2 =(:确定出压力中心为 00( 如图 示 定拉深次数 余量 h/d=70=d 凸 /d=156/150= 得出: =的计算 22232121 )()2( ( 2 222 1501762)8574( =216 毛坯相对厚度 t/d=1/200 100= h/d=以应采用压边圈 t/D 100=1/200 100=0.5 d 凸 /d=156/150= 2 表 4h1/ : h/d=50=然 h/6 18 30 6 10 22 36 10 18 27 43 18 30 33 52 30 50 39 62 50 80 46 74 80 120 54 87 120 180 63 100 具结构设计 要工作零件 冲孔凸模材料为 度要求 58 62阶底面应压入后磨平。凸模刃口部分设计成为方孔形,是因为成形孔是方孔。而把安装部分设计成圆柱形,其主要目的是避免钳工在安装凸模时划伤自己,便于安装。 两冲孔凸模都是依靠凸模固定板固定,采用过盈配合 H7/以凸模固定板孔的配合尺寸是 。 ( 1)凸模长度尺寸计算 因为是选用非标准 凸模,所长度尺寸由磨具结构确定,需要考虑:凸模固定板厚度 料板厚度 模进入凹模的深度,以及由凸模修磨量和在模具闭合状态下固定板与压料板之间的安全距离等因素需要增加的高度 h,即: 31 321 ( 3 那么有: 1 1 03412550 L 2)凸模强度校核 对于此类结构的凸模,必须进行承压力和稳定能力的校核。 承压能力校核 冲裁时凸模承受的有平均压应力和刃口的接触应力 k 两种。当此凸模断面宽度 B=7于材料厚度 t=,接触应力 k 大于平均压应力,因而强度校核的条件是接触应力 p: 由: ( 3 式中: k 凸模刃口接触应力( L 冲件轮廓长度( A 冲件平均面积( m); p 凸模材料的许用压力( 那么有: M P 1569981(17149 300128 复合条 件 稳定能力校核 按确定压杆临界力的欧拉公式计算,把凸模的一端视作为固定端,另一端根据导向形式或视作为自由端,或视作为铰支端或者是固定端的压杆。 由公式: m ( 3 式中: 凸模允许的最大自由长度( E 凸模材料弹性模量( 重建材料抗剪强度( 那么有: 3 03 0 013 4 33 0 2 1 0 0m a x 复合条件 本模具设有四个胀形凸模,材料为 度要求 58 62是整体式结构。胀形凸模刃口处加工成零件所需胀形的外形,装配处加工成矩形,这样便于凸模和凸模固定板的加工。胀形凸模依靠凸模固定板固定,之间按 H7/ 它零件设计 此套模具设计定位零件的作用是用来确定毛坯零件在模具中准确位置,保证冲出合格的制件。根据定位零件的设计原则:定位至少应有三个支承点,即两个导向点和一个定距点。根据零件的结构,零件内部有一个拉深部分,上下对称是直平面。那么32 可以在直 平面处加两块定位块,将零件的纵向定位,并且用螺钉和销钉把定位块稳定在胀形凹模上,其结构如 向的定位用两个固定的定位销定位,定位销靠过盈配合,固定在凹模上。 定位块材料为 45,硬度要求 43 48宽厚度 =402030 固定定位销材料为 45,硬度要求 43 48D=8d=4压力机下压时,胀形凸模将工件压入凹模内,材料会发生起皱或者胀形的效果不是很好。因为胀形从局部来看就是变薄拉深工序,所以需要压料装置。当冲压过程完成后,由于钢板 的回弹作用,压料板还能起到把工件从凹模中带出来,容易取件。 压料装置由压料板、弹簧和压料螺钉组成: 压料板 长宽厚度 =54040025料为 45,硬度要求为 4348 弹簧 弹簧的选择主要考虑能否将压料板弹开的高度要大于胀形部分的最大深度,压力机下压时压料板能压住周边,能很好的成形。 选用弹簧: d=8t=200N, 5h=55n=3, L=707料为 60度要求 43 48 压料螺钉 材料为 45,热处 理硬度 35 40 4. 固定零件 ( 1)模柄 同样,为了将固定上模座于压力机滑块上时,且使模具的压力中心与压力机的压力中心保证一致,加设模柄。根据所选开式压力机的模柄孔尺寸 6575择标准凸缘式模柄( 81),材料 45。 ( 2)凸模固定板 凸模固定板采用材料为 45,硬度要求为 43 48宽厚度 =540400 50内加工带台阶方孔,按 H7/ ( 3)垫板 冲压时,由于冲压力作用在凸模和凹模上,为了避免磨伤了凸模和凹模,需要分别在上 下加垫板。材料 45,硬度要求 43 48宽厚度 =54040010 33 结 论 我的设计是汽车前灯罩 的 冲压模具设计。设计任务一到手,就开始对零件结构进行分析,查阅有关专业书籍,完成了零件的二维图,包括尺寸的测绘。然后对零件毛坯展开计算,确定出工艺方案。零件的成形包括拉深、胀形、弯曲、冲孔、翻边等多道基本工序,考虑到成形工序的合理性和之间的相互影响,方案的确定在设计过程中要有所调整,使工作量增大;在设计第一套模具过程中,同样遇到了一些困难,都在老师的指导和自己的努力下,一一解决。对 于零件的加工,包括对工作零件的加工工序及方法的掌握不是很全面,表明还是缺乏专业知识,还需进一步学习总结;第一套模具设计完成后,开始设计第二套模具,由于有老师的指导,第二套模具顺利完成;最后写说明书,总结设计。当然设计中还存在不足处,希望在以后的工作实践中加以学习改进。 通过毕业设计,是对 大学 课程的一个总结,也是对专业知识学习的检验。四个月的毕业设计就此结束,从中我收获很多,而且得到很多快乐。为我大 学 学习画上圆满句号! 34 参考文献 1 肖祥芷,王孝培主编 西科学出版社 ,2 王孝培主编 第二版 械工业出版社 ,3 王芳主编 机械工业出版社 ,1998 4 王春武,齐广霞,揭钱发编著 北京:兵器工业出版社 ,5 陈炎嗣,郭景仪主编 北京:北京出版社 ,1991 6 杨玉英主编 北京:机械工业出版社 ,2005 7 廖念
- 温馨提示:
1: 本站所有资源如无特殊说明,都需要本地电脑安装OFFICE2007和PDF阅读器。图纸软件为CAD,CAXA,PROE,UG,SolidWorks等.压缩文件请下载最新的WinRAR软件解压。
2: 本站的文档不包含任何第三方提供的附件图纸等,如果需要附件,请联系上传者。文件的所有权益归上传用户所有。
3.本站RAR压缩包中若带图纸,网页内容里面会有图纸预览,若没有图纸预览就没有图纸。
4. 未经权益所有人同意不得将文件中的内容挪作商业或盈利用途。
5. 人人文库网仅提供信息存储空间,仅对用户上传内容的表现方式做保护处理,对用户上传分享的文档内容本身不做任何修改或编辑,并不能对任何下载内容负责。
6. 下载文件中如有侵权或不适当内容,请与我们联系,我们立即纠正。
7. 本站不保证下载资源的准确性、安全性和完整性, 同时也不承担用户因使用这些下载资源对自己和他人造成任何形式的伤害或损失。

人人文库网所有资源均是用户自行上传分享,仅供网友学习交流,未经上传用户书面授权,请勿作他用。