注塑模具毕业设计-手机电池盖注塑模具设计(全套含CAD图纸)
收藏
资源目录
压缩包内文档预览:(预览前20页/共40页)
编号:997117
类型:共享资源
大小:17.18MB
格式:RAR
上传时间:2017-01-23
上传人:机****料
认证信息
个人认证
高**(实名认证)
河南
IP属地:河南
50
积分
- 关 键 词:
-
注塑
模具
毕业设计
手机电池
模具设计
全套
cad
图纸
- 资源描述:
-




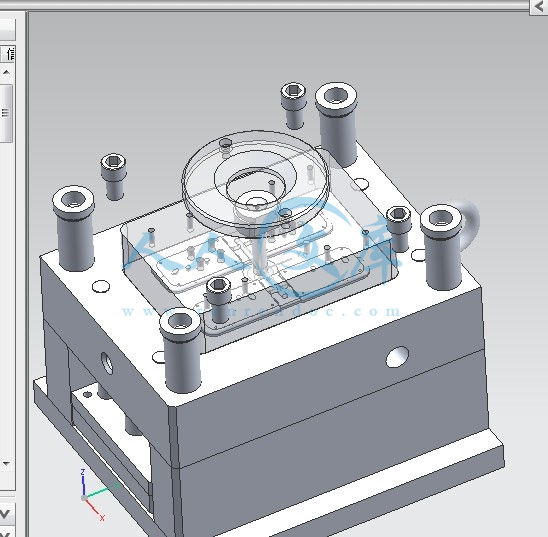


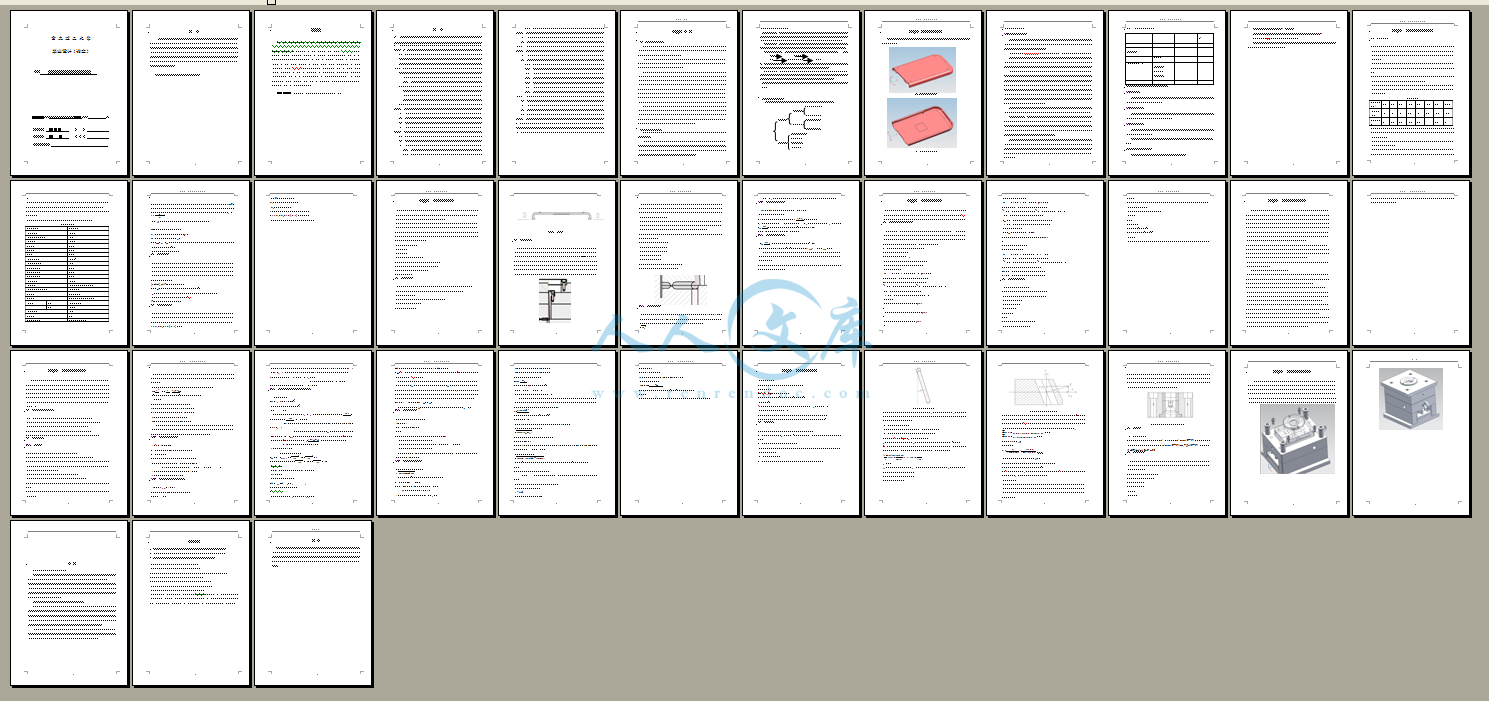

- 内容简介:
-
5轴数铣中心下注塑模具自动抛光过程材料加工技术杂志Xavier Pessoles, Christophe Tournier*LURPA, ENS Cachan, 61 av du pdt Wilson, 94230 Cachan, Francechristophe.tournierlurpa.ens-cachan.fr, Tel : 33 147 402 996, Fax : 33 147 402 211【摘要】注塑模具的制造过程包括抛光作业时关键的表面粗糙度或镜面效果必须出示透明部分。这抛光进行手动操作主要是通过技术工人进行分步完成。在本文中,我们提出一个5轴铣削自动抛光技术中心,以加工生产使用相同的手段和抛光方式来降低成本。我们开发的特殊算法来计算5轴刀具位置上自由形式的溶洞,为了模仿工人的技能。这是基于两填充曲线和摆线曲线。抛光力是基于一个力传感器的校正设置来保证被动刀具本身的位移与力量。刀具的精密运动有助于避免在5轴数控中心下对刀具的运动误差的影响。在表面的条款效力的方法粗糙度的质量和执行简单的是通过5轴数控加工过程实验证明的。【关键词】自动抛光,5轴铣削中心,镜面效果,表面粗糙度,希尔伯特曲线,摆线曲线几何参数CE (XE, YE, ZE)刀具起始点(u, v)参数空间坐标的摆线参数曲线s 横坐标曲线C(s) 导数参数方程P(s) 轨迹参数方程n (s)法向量p 步轨迹Dtr 轨迹直径A 轨迹线的幅度Step循环加强轨迹技术参数D 刀具半径Deff 抛光刀具有效直径E 磨带振幅e 刀具偏差值刀轴倾斜角u (i, j, k) 刀具坐标系f 导线切矢量Cc 摆切线加工参数N 主轴转速Vc 切速度Vf 进给速度fz 进给量ap 切削厚度at 加工点T 运转时间表面粗糙度参数Ra 表面算术平均差(2D)Sa 表面高度平均差(3D)Sq 表面均方根差Ssk 偏态分布幅值Sku 偏态分布峰值1简介 在高速加工(HSM)的发展极大地改变了注塑模具和模具制造商。特别是高速加工已使人们有可能以减少更换电火花加工模具制造周期 在许多情况下。尽管在这些演变,HSM是不能使消除抛光从操作的过程。在本文中,我们处理的表面与实现高质量的表面处理及镜面效果的行为。这就意味着,部分必须绝对光滑,无条纹反射。这样的质量,例如在必要的塑料注射,以获得完全光滑或模具腔的COM -pletely透明的塑料零件。从经济角度来看,是一个漫长和抛光烦人的过程,需要很多经验。因为这个过程是昂贵的价格上和模具停机,自动抛光已经研制成功。我们的目标是使用相同的生产加工手段,抛光,从而降低成本。该文件的目的,因此,建议在5轴的自动抛光方法机床。文学提供各种自动抛光实验。通常,抛光进行一人形机器人,1。拟人机器人是用于两个主要的原因。第一,他们的轴数,使他们有一个容易进入的任何地区 复杂的表格。第二,它可以附加的工具种类繁多,尤其是主轴配有抛光力控制机制。自动抛光研究也已进行了3个或5轴数控铣床特别设计的工具 管理抛光力2以及对并联机器人3。事实上,抛光力是一个过程的关键参数。磨损率折痕抛光时的压力增大4。但正如上文3联系压力取决于抛光力,也对部分的几何变化。一个适当的抛光力促进了尖头和条纹去除左侧部分 粉碎过程中或上抛光作业。不过,要接触应力尽可能避免过度抛光和尊重的偏差公差不变。因此,许多作者都选择了发展使磨料系统动态管理,常驻代表团将抛光力量。 5永田等。使用下面的力量阻抗模型控制,调整局部与接触力的打磨工具。 6,榈等基地。已经开发出一种被动的工具,使用一个气缸提供履约和 表面之间的接触压力恒定的部分。被动机制亦使用7。接触力,给出了一个弹簧的压缩力。为了进行自动抛光,重要的是要使用适合的工具轨迹。根据文献8,抛光路径应多向,而不是默notonic,以均匀的覆盖面和模具生产较少起伏错误。此外,多向抛光路径是接近了什么是手动。如果我们观察手动抛光机,我们可以看到,他们回去表面地区雅高丁各种形态,如摆线抛光路径(或摆线编织路径8(图1)。因此,它可能是有利可图的遵循这样一个过程,以便获得所需的零件质量。比如,有的论文使用类似分形轨迹的皮亚诺分型曲线,它是一个空间填充曲线的例子沿并行机10。这种文献的简要回顾表明,没有采用5大难题轴与被动机自动抛光工具。本文旨在展示自动抛光的可行性用5轴机床,并提出一些抛光战略。在第一部分中,我们揭露自动抛光可以使用5轴高速加工中心。特别是,我们目前的被动和灵活的工具的特点使用。一个具体的注意支付给施加位移之间的相关性由此产生的工具和抛光力量。一旦可行性5轴自动波利,成证明,各种专用抛光我们发展战略的详细在第2。这些战略从过去的经验已作为大部分从刀具轨迹的分形机器人化抛光或摆线编织未来路径代表手工抛光。在第3,我们的方法的有效性进行测试 利用各种测试部分表面。所有的零件都是精抛光,然后在同一亲duction是指:1 5轴铣削中心米克朗UCP710。在文学,成效抛光评估,并利用算术粗糙度Ra 2。不过,因为它是一个2D参数,这个标准是不是真的适合,以正确反映三维表面抛光质量。因此,我们建议通过三维资格的抛光表面光洁度参数。这一点在上一节讨论和比较的表面粗糙度自动获得使用与该抛光获得使用手册抛光,这一点在文献中很难处理。三维表面粗糙度测量是否进行了使用非接触式测量系统。 2实验过程 2.1工具的特点 正如以前所说,我们的目的是发展和盈利的一个非常简单的系统。因此,使用的工具是较手工抛光所用的相同。在波利-成计划分为两个步骤,预抛光和抛光加工。预抛光与磨料光碟进行安装在一个适当的支持。磨料粒度是由欧洲的磨料磨具标准(FEPA)生产者联合会。这种支持是一种变形的一部分,在一个钢轴固定一橡胶材料制成允许安装在主轴。因此,我们处理一个被动的工具。因此,我们做没有一个力反馈控制,但一个位置1。我们研究了关系光盘之间的支持和抛光偏转力应用到的部分。为了建立这种关系,我们使用了石英力传感器安装在一奇石乐9011A特别设计的部分持有人。该传感器连接到充电器本身功过一个数据采集装置链接到计算机以节约数据采集时间。该实验系统,如图2所示。此外,所用的传感器一个动态的传感器。因此,必须改变这种努力随着时间的推移,否则将有1漂移的措施。为此,该运动在实施一段时间的工具是一个三角形信号。了确保在抛光的微芯片,并保证疏散在非零磨损部分之间的联系速度和工具,刀具轴U是相对倾斜的正常载体表面的抛光n和对料的方向。倾斜角定义如下图(图3)所示:u = cos n + sin f (1)抛光试验已进行了3个不同的倾斜角度考虑(5,10,15)轴之间的工具和正常向量方向,在饲料表面。该扰度之间的刀具和抛光力的相关性如图4所示绿色曲线(5度)被中断,因为unstick研磨盘时工具挠度过大。在这种配置,倾斜角度太低,身体磁盘的支持,这是更严格,进来的工件,其接触恶化,unsticks磁盘。有10或15度倾角,这种现象对于出现变形的工具价值较高,外图。然而,低倾斜角配置允许更快的工具运动以来的5轴机床的旋转轴工具提示是少11。此外,它已表明,摆线刀具路径需要一个动态的机床进给速度要尊重程序12。然后在5轴配置,抛光时间,将与低倾斜角度更大。在此外,刀具的灵活性,将有助于减少或避免的5轴运动误差13。事实上,由工具和部分interfences可能发生,因为巨大的刀具轴接连两个刀具位置的方向演变。因此,该光盘支持偏转可避免的模具表面的变化。如果一个人认为,普雷斯顿14法律,在抛光的材料去除速率H是成比例的接触,磷平均压力,以及刀具的速度相对于工件。五:h = KPPV在金伯利进程是一个包括所有其他参数不变(部分材料,磨料,lubrification等)。因此,为了达到足够的接触压力,我们必须增加刀具偏转,因此我们提出了剪应力和磁盘unsticks。从运动学行为的观点来看,低旋转轴的运动,以减少导致抛光时间。因此,我们必须使用一个相当低的倾斜角度(5-10度)和一个相当高的工具偏转,以确保材料去除的精度。2.2 5轴抛光刀具路径规划 要生成抛光刀具路径,刀具的路径在5个经典的描述 - 轴一平头立铣刀铣削使用。这导致界定的工具轨迹下肢点行政长官,以及刀具的轴(i和j,k)的沿刀具路径方向。随着问候抛光战略,我们使用摆线刀具路径,以模仿 运动传递到主轴的工人。为了避免标志或特定的模式上的部分,我们选择生成的分形曲线摆线刀具路径,以弥补表面一multidirectionnal方式。我们使用更多的特别希尔伯特曲线,是的皮亚诺的曲线的特例。这些曲线是用于加工,因为他们 在覆盖整个表面上,他们已生成15的优势。我们将制定低于希尔伯特曲线是用来描述一个指导曲线为摆线曲线那么我们会研究摆线曲线本身。 2.2.1希尔伯特曲线的定义 分形轨迹的使用提出了两个重大的意义。第一个是工具路径不遵守它保证了统一的抛光具体指示。第二一个是联系在一起的刀具路径规划。事实上,刀具路径的计算 参数空间u时,表面的五,即限制在0,1 2间隔。希尔伯特曲线被称为填充曲线,涵盖了在参数空间的充分单位正方形16,因此,希尔伯特的曲线填补三维表面进行抛光。希尔伯特曲线可以用递归算法定义。n阶曲线定义如下:一二三阶希尔伯特曲线如下图(图5)所示为了保持沿着希尔伯特曲线相切的连续性,是指导摆线刀具路径的曲线,我们决定对鱼片的角落抛光分形。否则,在每分形曲线,抛光方向的改变刀具路径将是不连续的。造成希尔伯特曲线描绘在图6。基于在此表示,该曲线很容易操作。例如,一个项目可以这直接在三维空间的参数表示,或者利用它的指导曲线建设(图7)可以在未来的一段时间摆线曲线。2.2.2数学定义的摆线曲线的基础上,在17,我们定义提出摆线曲线描述一摆线曲线如下。设C(S)是二维参数曲线,其中s是曲线的长度(图8)。C(s) = (s, f(s) 是摆线曲线和N(s)的正常载体引导曲线该曲线C(s)在考虑点。P是摆曲线的一步,我们表示Dtr为它的直径。该摆线曲线的参数方程是:现在的问题是连接摆线曲线参数的抛光参数。在阿的摆线曲线振幅等于其直径的两倍阿= 2 数据传输速度。从刀具轨迹生成的角度来看,我们更感兴趣的信封的工具振幅比摆线曲线的振幅。一个建模的困难刀具的运动包络面是工具本身,研磨抛光工具安装在灵活的支持。刀具抛光幅度取决于接触表面之间的工具和零件。这个联络是受倾斜角度,刀具直径D和E的位移施加工具能够抛光表面。事实上,当刀具接触面积是一个磁盘,这可以看到如图9。接触面积是一个光盘的一部分。这就产生的参数Dtr定义调整,以建立摆线曲线。2.2.3刀具路径生成无论所考虑的表面性质,抛光刀具路径生成包括三个步骤:在参数空间,计算刀具轨迹的计算在3D的空间和刀轴方向产生的刀具路径计算。刀具路径生成依赖于如上所述摆线曲线。该轨迹定义discretly。唯一的困难是计算法向量。我们现在描述为计算工具的轴(图方向的方法3)。在第一种方法只用在平面倾斜角(定义f;n),F是切向量指导曲线,即希尔伯特曲线和n正常载体已加工表面。刀具轴U是倾斜相对于希尔伯特曲线的切线f而不是向摆线曲线,以减少各运动的振幅机床旋转轴。下面的表达式是使用:刀具的肢体CE,这是在加工过程中驱动点的位置取决于抛光模式通过参数定义2.3实验在塑胶模具注塑方面,我们研究更多的,特别是在注射电气设备的模具,如电源插座和开关(图10)。因此,我们处理小细面。为了测试我们的方法,我们使用两个单斑贴试验面,一个平面和凸曲面,其曲率大于一点点模具的曲率。这是在加工50x50mm取得了第块的X38CrMoV5钢。零件的洛氏硬度为53HRC后热处理。该部分是对加工的5轴机床米克朗UCP710达成铣床抛光整理状态之前。我们使用四个预抛光磨料不同等级(FEPA 120,240,600,1200)。磨料粘结在直径为18mm磁盘上的灵活支持。120,240和600等级,磨料是由三氧化二铝(Al2O3)的内高分子材料纸碳化硅为1200级。最后抛光,我们使用三种,等级9m合成钻石膏3m和1m的。关于工具路径,摆线轨迹的基础上进行最后的抛光和基于希尔伯特曲线预抛光直线使用。铣床,抛光序列总结表1。为了实现在高进给速度抛光,功能的优化西门子SINUMERIK 840D系统控制器都被激活。特别是,实时运动学变换(TRAORI)以及实时多项式插值(COMPCURV)产生平滑轴向运动。3结果与讨论 工业上,造成的抛光表面质量第一验证的波利, 舍尔目测检查自己。接触表面粗糙度测量装置是严禁以避免表面损伤。然而,新的非接触测量科技研究 logies允许根据对部分和数据处理三维地形扫描国际标准的三维表面粗糙度。国际标准的18目的是通过各种特征参数的三维表面粗糙度。其中, 重要的是要确定哪些是最适当的限定一个镜面效果行为。据我们所知,有没有3D参数设置功能的镜面效果表面。工业实践表明只有大约20纳米镭。 按苏等人的研究。 19表面纹理参数显示,Sa和SQ参数都不足以识别表面划伤。他们建议使用参数SSK、Hilerio等。 20也作出了标准的SSK的解释 和SKU在人工膝关节的抛光控制范围内。 SSK的代表配置文件的对称性: - SSK= 0:配置文件是对称的中线, - SSK 0:轮廓更比谷峰, - SSK 3:分布广泛(而不是平面的表面), - SKU的3:分布tighted(表面有一种倾向,目前波峰 或波谷)。 一旦部分抛光,我们会表现三维表面粗糙度测量使用 非接触式测量系统(TALYSURF轮廓CCI 6000)。我们进行测量的波利,棚与我们的办法(平面与凸面部位),在飞机上已被擦亮的一个专业(图11手动)。测量结果公布 在表2。可以观察到的凸表面自动抛光呈现较大的地缘以及较高的沙和SQ比那些对平面上观察度量偏差。轨迹是在(u和v)参数空间相同。有几种解释此行为。首先,用抛光模式,生成参数化的空间,是而比在平面凸部分面积较大的表面一样。其结果是较低的覆盖率。这也可以解释为机kinemati -卡尔行为在每个部分抛光。表面抛光的平面与3轴运动而凸表面需要5轴同时进行插补机床。在加工过程中,两者的工具和零件的相对进给速度不符合程序1由于5轴加工缓慢旋转轴(15rpm; :20rpm)11。这导致了慢,不流畅的轨迹,减少抛光效率。Sa和SQ较大的凸表面抛光,但部分提供了一面镜子反正效果的行为。这证实了19和20中提到的言论,以及“平均影响这些参数”。镜面效果的行为似乎取决于SSK和SKU的参数。事实上,他们的价值观的凸表面是adequation这些平面的表面,也提供镜面效果的行为观察。雷加,丁的高峰和低谷,这三个例子展出同一数量级用手动抛光小优势参数的SKU。的数值对应相当不错的意见。最后,我们可以假设抛光 要优化过程有关SSK和SKU参数之前,Sa和平方米参数。 4结论 在这篇文章中,我们提出了一个解决方案,生产出表面抛光镜面效果5轴机床,通常致力于模具的加工。被动使用的简单工具实施。使我们的初步标定关联的力量和抛光刀具偏差。我们还开发了抛光刀具路径类似的模式用手工抛光,以避免对抛光的一部分标记。抛光质量是可比的手工方法和抛光时间是相似的。然而,在为了保持恒定的覆盖率,我们应该考虑到有效对部分地区进行抛光时产生的(u和v)面的刀具路径。从表面粗糙度来看,炮管过程必须减少幅度峰值和由一个SKU的参数优于三特点山谷。对于复杂的形状机床运动学性能非常重要,以保证刀具进给速度尽可能平稳高,从而导致材料的优良率减少。特别是,旋转轴必须十分服从执行程序进给速度。现在我们寻求更好的措施,使抛光面积小于注塑模具的半径混合表面。附录:三维表面粗糙度参数Sa:算数平均表面高度Sq :根均方误差的表面。这是一个分散的参数定义为根平均面积的表面离散方值。Ssk:偏态分布曲线,这是不对称值关于平面平均偏差。Sku:地形高度分布的峰度。这是一个平衡峰值参考资料:1 X. Wu and Y. Kita and K. Ikoku, New polishing technology of free form surface byGC, Journal of Materials Processing Technology, 187-188, 81-84 (2007).2 J.P. Huissoon and F. Ismail and A. Jafari and S. Bedi, Automated Polishing of DieSteel Surfaces, International Journal of Advanced Manufacturing Technology, 19(4),285-290 (2002).3 A. Roswell and F. Xi and G. Liu, Modelling and analysis of contact stress for au-tomated polishing, International Journal of Machine Tools and Manufacture, 46(3-4),424-435 (2006).4 S-C. Lin and M-L. Wu, A study of the effects of polishing on material removal rate andnon-uniformity, International Journals of Machine Tools and Manufacture, 42, 99-103(2002).5 F. Nagata and Y. Kusumoto and Y. Fujimoto and K. Watanabe, Robotic sandingsystem for new designed furniture with free-formed surface, Robotics and Computer-Integrated Manufacturing, 23(4), 371-379 (2007).6 B-S. Ryuh and S.M. Park and G. R. Pennock, An automatic tool changer and inte-grated software for a robotic die polishing station, Mechanism and Machine Theory, 41,415-432 (2006).7 Y. Mizugaki and M. Sakamoto, Development of a Metal-Mold Polishing Robot Systemwith Contact Pressure Control, Annals of the CIRP, 39(1), 523-526 (1990).8 M. J. Tsai and J. F. Huang, Efficient automatic polishing process with a new compliantabrasive tool, International Journal of Advanced Manufacturing Technology, 30, 817-827 (2006).9 Y. Mizugaki and M. Sakamoto, Fractal Path Generation for a Metal-Mold PolishingRobot System and Its Evaluation by the Operability, Annals of the CIRP, 41(1), 531-534(1992).10 H-Y. Tam and O.C Hang Lui and A.C.K. Mok, Robotic polishing of free-form surfacesusing scanning paths, Journal of Materials Processing Technology, 95, 191-200 (1999).11 S. Lavernhe and C. Tournier and C. Lartigue, Kinematical performance predictionin multi-axis machining for process planning optimization, International Journal ofAdvanced Manufacturing Technology, 37, 534-544 (2008).12 M. Rauch and JY. Hascoet, Rough pocket milling with trochoidal and plungingstrategies, International Journal of Machining and Machinability of Materials, 2, 161-175 (2007).13 M. Munlin and S.S. Makhanov and E.L.J. Bohez, Optimization of a 5-axis millingmachine near stationary points, Computer-Aided Design, 36, 1117-1128 (2004).14 F. Preston, The theory and design of plate glass polishing machine, Journal of theSociety of Glass Technology, 11, 214-256 (1927).15 J.G Griffits, Toolpath based on Hilberts curve, Computer-Aided Design, 26, 839-844(1994).16 H. Sagan, Space-Filling Curves, Springer-Verlag, New York, 1994.17 Yates, 1952 R. Yates, A Handbook on Curves and Their Properties, Edwards Bro-thers, Inc., Ann Arbor (1952).18 ISO/DIS 25178-2, Geometrical product specifications (GPS) Surface texture : Areal Part 2 : Terms, definitions and surface texture parameters, 2008.19 A. Y. Suh and A. A. Polycarpou and T. F. Conry, Detailed surface roughness cha-racterization of engineering surfaces undergoing tribological testing leading to scuffing,Wear, 255, 556-568 (2003).20 I. Hilerio and T. Mathia and C. Alepee, 3D measurements of the knee prosthesissurfaces applied in optimizing of manufacturing progress,Wear,257,1230-1234 (2004)arXiv:1003.5062v1 physics.gen-ph 26 Mar 2010Automatic polishing process of plastic injection molds on a 5-axismilling centerJournal of Materials Processing TechnologyXavier Pessoles, Christophe Tournier*LURPA, ENS Cachan, 61 av du pdt Wilson, 94230 Cachan, Francechristophe.tournierlurpa.ens-cachan.fr, Tel : 33 147 402 996, Fax : 33 147 402 211AbstractThe plastic injection mold manufacturing process includes polishing operations whensurface roughness is critical or mirror effect is required to produce transparent parts. Thispolishing operation is mainly carried out manually by skilled workers of subcontractorcompanies. In this paper, we propose an automatic polishing technique on a 5-axis millingcenter in order to use the same means of production from machining to polishing andreduce the costs. We develop special algorithms to compute 5-axis cutter locations onfree-form cavities in order to imitate the skills of the workers. These are based on bothfilling curves and trochoidal curves. The polishing force is ensured by the compliance ofthe passive tool itself and set-up by calibration between displacement and force based ona force sensor. The compliance of the tool helps to avoid kinematical error effects on thepart during 5-axis tool movements. The effectiveness of the method in terms of the surfaceroughness quality and the simplicity of implementation is shown through experiments ona 5-axis machining center with a rotary and tilt table.KeywordsAutomatic Polishing, 5-axis milling center, mirror effect, surface roughness, Hilbertscurves, trochoidal curves1Geometric parametersCE(XE,YE,ZE)tool extremity point(u,v)coordinates in the parametric spaceTrochoidal curve parametersscurvilinear abscissaC(s)parametric equation of the guiding curveP(s)parametric equation of the trochoide curven(s)normal vector of the guiding curvepstep of the trochoidDtrdiameter of the usefull circle to construct the trochoidAamplitude of the trochoidStepstep between two loops of trochoideTechnological parametersDtool diameterDeffeffective diameter of the tool during polishingEamplitude of the envelope of the polishing stripedisplacement induced by the compression of the tooltilt angle of the tool axisu(i,j,k)tool axisftangent vector of the guide curveCcpoint onto the trochoidal curveMachining parametersNspindle speedVccutting speedVffeed speedfzfeed per cutting edgeapcutting depthatworking engagementTmachining time2Surface roughness parametersRaarithmetic average deviation of the surface (2D)Saarithmetical mean height of the surface (3D)Sqroot-mean-square deviation of the surfaceSskskewness of topography height distributionSkukurtosis of topography height distribution31IntroductionThe development of High Speed Machining (HSM) has dramatically modified the or-ganization of plastic injection molds and tooling manufacturers. HSM in particular hasmade it possible to reduce mold manufacturing cycle times by replacing spark machiningin many cases. In spite of these evolutions, HSM is not enable to remove the polishingoperations from the process. In this paper, we deal with the realization of surfaces withhigh quality of surface finishing and mirror effect behavior. This means that the partmust be perfectly smooth and reflective, without stripes. Such a quality is for examplenecessary on injection plastic mold cavities in order to obtain perfectly smooth or com-pletely transparent plastic parts. From an economic point of view, polishing is a long andtiresome process requiring much experience. As this process is expensive in terms of priceand downtime of the mold, automatic polishing has been developed. Our objective is touse the same means of production from machining to polishing, leading to cost reduction.The aim of the paper is thus to propose a method of automatic polishing on a 5-axismachine tool.Literature provides various automated polishing experiments. Usually, the polishing iscarried out by an anthropomorphic robot, 1. Anthropomorphic robots are used for twomain reasons. First, their number of axes enables them to have an easy access to any areaof complex form. Second, it is possible to attach a great variety of tools and particularlyspindles equipped with polishing force control mechanisms. Automatic polishing studieshave been also carried out on 3 or 5-axis NC milling machine with specially designed toolto manage polishing force 2 as well as on parallel robots 3.Indeed, the polishing force is a key parameter of the process. The abrasion rate in-creases when the polishing pressure increases 4. But as mentioned in 3 the contactpressure depends on the polishing force and also on the geometrical variations of the part.An adequate polishing force facilitates the removal of cusps and stripes left on the partduring milling or previous polishing operations. Nevertheless, the contact stress has tobe as constant as possible to avoid over-polishing and respect form deviation tolerances.Many authors have thus chosen to develop abrasive systems allowing a dynamic manage-ment of the polishing force. In 5, Nagata et al. use an impedance model following forcecontrol to adjust the contact force between the part and the sanding tool. In 6, Ryuh etal. have developed a passive tool, using a pneumatic cylinder to provide compliance and4constant contact pressure between the surface and the part. A passive mechanism is alsoused in 7. The contact force is given by the compressive force of a spring coil.In order to carry out an automatic polishing, it is important to use adapted tooltrajectories. According to 8, polishing paths should be multidirectional rather than mo-notonic, in order to cover uniformly the mold surface and to produce fewer undulationerrors. Moreover, the multidirectional polishing path is close to what is made manually.If we observe manual polishers, we can notice that they go back on surface areas accor-ding to various patterns such as trochoidal polishing paths (or cycloidal weaving paths8 (fig 1). Therefore, it could be profitable to follow such a process in order to obtainthe required part quality. For instance, some papers use fractal trajectories like the PeanoCurve fractal 9, which is an example of a space-filling curve, rather than sweepings alongparallel planes 10.ElementarypatternElementarypatternMultidirectionalpolishingMultidirectionalpolishingFigure 1 Manual polishing patternsThis brief review of the literature shows that there is no major difficulty in using a 5-axis machine for automatic polishing with a passive tool. This paper aims at showing thefeasibility of automatic polishing using 5-axis machine tools and proposing some polishingstrategies. In the first section, we expose how automatic polishing is possible using a 5-axisHSM center. In particular, we present the characteristics of the passive and flexible toolsused. A specific attention is paid to the correlation between the imposed displacement ofthe tool and the resulting polishing force. Once the feasibility of 5-axis automatic poli-shing is proved, the various dedicated polishing strategies we have developed are detailedin section 2. These strategies are for the most part issued from previous experiences asfor fractal tool trajectories coming from robotized polishing or cycloidal weaving paths5representative of manual polishing. In section 3, the efficiency of our approach is testedusing various test part surfaces. All the parts are milled then polished on the same pro-duction means : a 5-axis Mikron UCP710 milling centre. In the literature, the effectivenessof polishing is evaluated using the arithmetic roughness Ra 2. However, as it is a 2Dparameter, this criterion is not really suited to reflect correctly the 3D polished surfacequality. We thus suggest qualifying the finish quality of the polished surface through 3Dparameters. This point is discussed in the last section as well as the comparison of thesurface roughness obtained using automatic polishing with that obtained using manualpolishing, a point hardly addressed in the literature. 3D surface roughness measurementsare performed using non-contact measuring systems.2Experimental Procedure2.1Characteristics of the toolsAs said previously, our purpose is to develop a very simple and profitable system.Therefore, the tools used are the same than those used in manual polishing. The poli-shing plan is divided into two steps, pre-polishing and finishing polishing. Pre-polishing isperformed with abrasive discs mounted on a suitable support. The abrasive particle sizeis determined by the Federation of European Producers of Abrasives standard (FEPA).This support is a deformable part made in an elastomer material fixed on a steel shaftthat allows mounting in the spindle. We thus deal with a passive tool. Hence, we donot have a force feedback control but a position one. We have studied the relationshipbetween the deflection of the disc support and the polishing force applied to the part.To establish this relationship, we use a Quartz force sensor Kistler 9011A mounted on aspecially designed part-holder. The sensor is connected to a charger meter Kistler 5015itself connected to the computer through a data-collection device Vernier LabPro to savethe data. The experimental system is depicted in figure 2. In addition, the used sensor isa dynamic sensor. The effort must therefore change over time otherwise there would be adrift of the measure. To do so, the movement imposed on the tool over time is a triangularsignal.6Figure 2 Experimental set-upIn order to ensure the evacuation of micro chips during the polishing and guarantee anonzero abrasion speed at the contact between the part and the tool, the tool axis u istilted relatively to the normal vector to the polished surface n and to the feed directionf. The tilt angle (figure 3) is defined as follows :nuqfvCeCcWorkpieceCLFigure 3 Tool axis tilting7u = cos n + sin f(1)Polishing tests have been conducted considering three different tilt angles (5,10,15)between the tool axis and the normal vector to the surface in the feed direction. Thecorrelation between the tool deflection and the polishing force is shown in figure 4.Polishing?force0246810121416180,000,150,300,450,600,750,901,051,20Displacement?(mm)Force?(N)5?inclination?angle10?inclination?angle15?inclination?angleFigure 4 Polishing forces vs displacementThe green curve (5 deg) is interrupted because the abrasive disks unstick when thetool deflection is too large. In this configuration, the tilt angle is too low and the bodyof the disk support, which is more rigid, comes in contact with the workpiece, whichdeteriorates and unsticks the disk. With a 10 or 15 degrees tilt angle, this phenomenonappears for a higher value of tool deflection, outside the graph. However, low tilt angleconfigurations allow faster tool movements since the rotation axes of the 5-axis machinetool are less prompted 11. Furthermore, it has been showed that trochoidal tool pathsrequire a dynamic machine tool to respect the programmed feedrate 12. Then in si-multaneous 5-axis configurations, polishing time will be greater with low tilt angles. Inaddition, the flexibility of the tool will help to reduce or avoid 5-axis kinematic errors 13.Indeed, interfences between the tool and the part could happen because of great tool axis8orientation evolutions between two succesive tool positions. Therefore, the disc supportdeflection would avoid the alteration of the mold surface.If one considers the law of Preston 14, the material removal rate h in polishing isproportional to the average pressure of contact, P, and to the tool velocity relative to theworkpiece, V :h = KPPV(2)where KPis a constant (m2sN) including all other parameters (part material, abrasive,lubrification, etc.). Hence, in order to reach an adequate contact pressure, we must increasethe tool deflection and consequently we raise the shear stress and the disk unsticks. Froma kinematical behavior point of view, low rotational axes movements lead to decrease thepolishing time. So we must use a rather low tilt angle (5-10 degrees) and a quite high tooldeflection to ensure a satisfactory rate of material removal.2.25-axis polishing tool path planningTo generate the polishing tool path, the classical description of the tool path in 5-axis milling with a flat end cutter is used. This leads to define the trajectory of the toolextremity point CEas well as the orientation of the tool axis u (i,j,k) along the tool path.With regards to polishing strategy, we use trochoidal tool paths in order to imitate themovements imparted by the workers to the spindle. To avoid marks or specific patterns onthe part, we choose to generate trochoidal tool path on fractal curves in order to cover thesurface in a multidirectionnal manner. We use more particularly Hilberts curves whichare a special case of the Peanos curve. These curves are used in machining as they havethe advantage of covering the entire surface on which they have been generated 15. Wewill develop below the description of the Hilberts curve which is used as a guide curvefor the trochoidal curve then we will examine the trochoidal curve itself.2.2.1Hilberts curve definitionThe use of fractal trajectories presents two major interests. The first one is that toolpaths do not follow specific directions which guarantees an uniform polishing. The secondone is linked to the tool path programming. Indeed, tool paths are computed in the9parametric space u,v of the surface, that is restricted to the 0,12interval. Hilbertscurves are known as filling curves, covering the full unit square in the parametric space16, and consequently, the Hilberts curves fill the 3D surface to be polished. Hilbertscurves can be defined with a recursive algorithm, the n-order curve is defined as follows : If n = 0 :x0= 0y0= 0(3) Else :xn=0.50.5 + yn10.5 + xn10.5 + xn10.5 yn1yn=0.50.5 + xn10.5 + yn10.5 + yn10.5 xn1(4)It is then easy to compute first, second or third-order and so Hilberts curves (fig 5).-0.4-0.200.20.4-0.4-0.200.20.4-0.5-0.3-0.10.10.30.5-0.4-0.200.20.4-0.5-0.3-0.10.10.30.5-0.5-0.3-0.10.10.30.5Figure 5 Hilberts curves (first, second and third order curve)In order to maintain a tangency continuity along the Hilberts curve which is the guidecurve of the trochoidal tool path, we have decided to introduce fillets on the corners of thepolishing fractals. Otherwise, at each direction change on the fractal curve, the polishingtool path would be discontinuous. Resulting Hilberts curve is depicted in figure 6. Basedon this representation, the curve is easy to manipulate. For example, one could projectthis parametric representation directly in the 3D space or use it as the guide curve forbuilding trochoidal curves (fig 7) as can be seen in the next section.2.2.2Mathematical definition of trochoidal curvesBased on the description of trochoidal curves proposed in 17, we define a trochoidalcurve as follows. Let C(s) be a 2D parametric curve, where s is the curvilinear length (fig8).10Figure 6 Fourth order cornered Hilberts curvef(s)CciCinirCDTROiCjnjCcjOjqiqjFigure 7 Polishing trajectories on a convex free formC(s) = (s,f(s) is the guide curve of the trochoidal curve and n(s) the normal vectorto the curve C(s) at the considered point. p is the step of the trochoidal curve and wedenote Dtrits diameter. The parametric equation of the trochoidal curve is the following :P(s) = C(s) +p2n(s) + Dtrcos(2sp)sin(2sp)sin(2sp)cos(2sp)n(s)(5)The issue is now to link the trochoidal curve parameters to the polishing parameters.The amplitude A of the trochoidal curve is equal to twice its diameter A = 2Dtr. However,11Figure 8 Trochoidal curve parametersfrom a tool path generation point of view, we are more interested in the tool envelopeamplitude than in the trochoidal curve amplitude. One of the difficulties of modellingthe envelope surface of the tool movement is the tool itself, as abrasive polishing toolsare mounted on flexible supports. The tool polishing amplitude depends on the contactsurface between the tool and the part. This contact is influenced by the tilt angle , thetool diameter D and the imposed tool displacement e to be able to polish the surface.Indeed, when the tool is laid flat, the contact area is a disk, as can be seen in figure 9.However, when the tool is tilted and a given displacement e is imposed to the tool, thecontact area is a disc portion.ZDDeffleZequFigure 9 Contact area between the tool and the partThe effective tool diameter can be computed with the following expressions :12Deff= 2s?D2?2 (l)2(6)with :l =D2sin etan(7)and :E = A + 2Deff2= 2Dtr+ Deff(8)This yields to the definition of the parameter Dtradjusted to build the trochoidalcurve.Dtr=E Deff2=Deff6=13vuut?D2?2 D2tan etan!2(9)2.2.3Tool path generationWhatever the nature of the considered surface, the polishing tool paths generationconsists of three steps : computation of the tool path in the parametric space, computationof the resulting tool path in the 3D space and computation of the tool axis orientation.Tool path generation relies on the trochoidal curve as described above. The trajectory isdefined discretly. The only difficulty is to calculate the normal vector. This is done byusing the points Ci1and Ci+1and by calculating the next cross product :ni= Z Ci1Ci+1(10)We now describe the method for calculating the direction of the tool axis u (figure3). In a first approach we only use the tilt angle defined in the plane (f;n) where f isthe tangent vector to the guide curve, i.e., the Hilberts curve and n the normal vector tothe machined surface. The tool axis u is tilted in relation to the Hilberts curve tangentf rather than to the trochoidal curve in order to minimize the movements amplitude ofthe rotational axes of the machine tool.In order to compute the tangent vector fiat the contact point CCibetween the tooland the part, the following expression is used :fi= n CCiCC(i+1) n| CCiCC(i+1)|!|z(11)13The location of the tool extremity CE, which is the driven point during machining,depends on the polishing mode, i.e., by pulling or pushing the tool. The polishing modeis defined by the parameter : OCE= OCC+ r n + (R r) v r u e z(12)with :v =u n|u n| u(13)by noting = 1 when 0 and = 1 when 0 : profile has more peaks than valleys, Ssk 3 : the distribution is wide (the surface is rather plane), Sku 3 : the distribution is tighted (the surface has a tendency to present peaksor valleys).Once the parts are polished, we perform 3D surface roughness measurements using anon-contact measuring system (Talysurf CCI 6000). We perform measurements on poli-shed parts with our approach (the plane and the convex surface) and on a plane that hasbeen polished manually by a professional (figure 11). Measurement results are reportedin table 2.It can be observed that the convex surface automatically polished presents larger geo-metric deviations as well as a higher Sa and Sq than those observed for the planar surface.In other words, the rate of material removal is not as good as on the planar surface while16Figure 11 3D surface roughness : convex surface (top), planar automatic (middle),planar manual (bottom)OperationsNVcV ffzapatTToolrpmm/minmm/minmm/toothmmmmminparallel planes94388980000,0570,20,0335End mill ( 3)Operations ToolsAStepV fNeTmmmmmm/minrpmdegmmminP grade 120 ( 18)1211000200030,415P grade 240 ( 18)1211000200030,415P grade 600 ( 18)1211000200030,415P grade 1200 ( 18)1211000200030,415Diamond abrasive emulsion (9m) ( 6)1211000200030,315Diamond abrasive emulsion (3m) ( 6)1211000200030,315Diamond abrasive emulsion (1m) ( 6)1211000200030,315Table 1 Milling and polishing operationsSurfaceSaSqSskSkuConvex Autom.7.619 nm9.543 nm-0.23142.92Plane Autom.1.085 nm1.346 nm0.1032.713Plane Manual1.014 nm1.307 nm-0.59413.748Table 2 3D Roughness parameters17trajectories are the same in the (u,v) parametric space. There are several explanationsfor this behavior. First, the used polishing pattern, generated in the parametric space, isthe same than the planar surface whereas the surface area of the convex part is greater.The result is a lower coverage rate. This can also be explained by the machine kinemati-cal behavior during polishing for each part. The planar surface is polished with a 3 axeskinematic while the convex surface requires simultaneous interpolation of the 5 axes ofthe machine tool. During machining, the relative feedrate between the tool and the partdoes not match the programmed one due to the slow rotary axes of the 5-axis machining(A : 15rpm; C : 20rpm) 11. This leads to a slower and less smooth trajectory, reducingthe polishing efficiency.Sa and Sq are larger for the convex surface but the polished part provides a mirroreffect behavior anyway. This confirms the remarks mentioned in 19 and 20 as well asthe ”mean effect” of these parameters. Mirror effect behavior seems to depend on theSsk and Sku parameters. Indeed, their values for the convex surface are in adequationwith those observed for planar surfaces, which also provide mirror effect behavior. Regar-ding the peaks and valleys, the three examples exhibit the same order of magnitude forthe parameter Sku with a small advantage for manual polishing. The numerical valuescorrespond fairly well with the observations. Finally, we can suppose that the polishingprocess should be optimized regarding the Ssk and Sku parameters prior to the Sa andSq parameters.4ConclusionIn this article, we propose a solution to produce mirror effect polished surfaces on a5-axis machine tool normally dedicated to molds milling. The passive tool used is simpleto implement. A preliminary calibration allows us to correlate the polishing force andthe tool deviation. We have also developed polishing tool paths similar to the patternsused in manual polishing in order to avoid marks on the polished part. The polishingquality is comparable to the manual method and polishing time is similar. However, inorder to maintain a constant coverage rate, we should take into consideration the effectivearea of the part to be polished when generating the tool paths in the (u,v) plane. Fromroughness point of view, the polishing process must reduce the amplitude of the peaks18and valleys which is characterized by a Sku parameter superior to 3. For complex shapes,kinematic performances of the machine tool are very important in order to guarantee atool feedrate as high as possible and smooth, thus leading to a good rate of materialremoval. In particular, rotary axes have to be very performing to respect the programmedfeedrate. We seek now to develop polishing strategies that allow the polishing of smallradius blending surfaces on the injection moulds.19Appendix : 3D surface roughness parametersSa : Arithmetical mean height of the surface.Sa =1AZZZ(x,y)dxdy(14)Sq : Root-mean-square deviation of the surface. This is a dispersion parameter definedas the root mean square value of the s
- 温馨提示:
1: 本站所有资源如无特殊说明,都需要本地电脑安装OFFICE2007和PDF阅读器。图纸软件为CAD,CAXA,PROE,UG,SolidWorks等.压缩文件请下载最新的WinRAR软件解压。
2: 本站的文档不包含任何第三方提供的附件图纸等,如果需要附件,请联系上传者。文件的所有权益归上传用户所有。
3.本站RAR压缩包中若带图纸,网页内容里面会有图纸预览,若没有图纸预览就没有图纸。
4. 未经权益所有人同意不得将文件中的内容挪作商业或盈利用途。
5. 人人文库网仅提供信息存储空间,仅对用户上传内容的表现方式做保护处理,对用户上传分享的文档内容本身不做任何修改或编辑,并不能对任何下载内容负责。
6. 下载文件中如有侵权或不适当内容,请与我们联系,我们立即纠正。
7. 本站不保证下载资源的准确性、安全性和完整性, 同时也不承担用户因使用这些下载资源对自己和他人造成任何形式的伤害或损失。

人人文库网所有资源均是用户自行上传分享,仅供网友学习交流,未经上传用户书面授权,请勿作他用。