连接座加工工艺及左端面铣削夹具设计【4张图纸】【优秀】
收藏
资源目录
压缩包内文档预览:
编号:270036
类型:共享资源
大小:548.81KB
格式:RAR
上传时间:2014-03-17
上传人:上***
认证信息
个人认证
高**(实名认证)
江苏
IP属地:江苏
35
积分
- 关 键 词:
-
连接座
加工工艺
及左端面
铣削夹具
设计
- 资源描述:
-
连接座加工工艺及左端面铣削夹具设计
28页 10000字数+说明书+工艺卡片+工序卡片+4张CAD图纸
工序卡.doc
底板.dwg
底板.exb
过程卡.doc
连接座加工工艺及左端面铣削夹具设计说明书.doc
连接座毛坯图.dwg
连接座毛坯图.exb
连接座零件图.dwg
连接座零件图.exb
铣削夹具装配图.dwg
铣削夹具装配图.exb
摘要
本次课程设计的目的是通过课程设计,对所学习的知识进行一次综合性的应用,通过在课程设计中,不断发现问题,并且解决问题来提高自己的水平。
本次设计主要内容:设计连接座的机械加工工艺规程和铣削座端面的工艺装备并绘制出支架零件图、毛坯图、夹具装配图,夹具中的一个零件图,填写工艺卡片,编制课程设计说明书。
我主要铣削连接座的左端面,通过气压缸与圆盘对工件进行夹紧,用定位板以及定位销对工件进行定位,这样工件就会在稳定的状态下被加工。
目录
1.零件的工艺分析及生产类型的确定5
1.1零件的工艺分析5
1.2确定零件的生产类型7
2选择毛坯,确定毛坯尺寸,设计毛坯图8
2.1选择毛坯8
2.2确定毛坯尺寸8
2.3设计毛坯图9
3工艺规程的设计10
3.1选择定位基准10
3.2零件表面加工方法的选择10
4机械加工余量、工序尺寸的确定15
五、确立切削用量及基本工时17
5.1工序六17
5.2工序八19
5.3工序十21
5.4车φ40H7的端面及孔至φ39H821
5.5工序十四23
5.6工序十五24
六、夹具的设计25
心得体会26
参考文献27

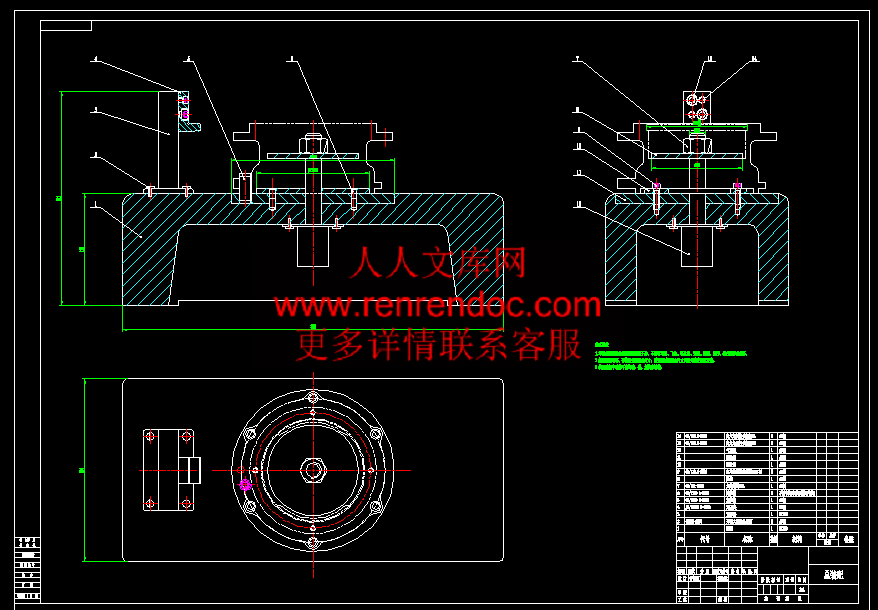
- 内容简介:
-
文件编号机械加工工序卡片产品型号零(部)件图号共13页产品名称连接座零(部)件名称第8页车间工序号工件名称材料牌号机加工7连接座HT200毛坯种类毛坯外形尺寸每坯件数每台件数铸件142*6911设备名称设备型号设备编号同时加工件数立式钻床X621夹具编号夹具名称冷却液铣模工序时间准终单件工步号工步内容工艺装备主轴转速/(r/min)切削速度 (m/min)进给量(mm/r)进给深度(mm)走刀次数工时定额描图基本辅助1精铣左端面高速钢直齿精密级三面刃铣刀37574.20.0181115.2描校底图号装订号编制审核会签标记处数更改文件号签字日期标记处数更改文件号签字日期机械加工工艺过程卡片机械加工工艺过程卡片产品型号零件图号产品名称连接座零件名称共1页第1页材料牌号HT200毛坯种类铸件毛坯外形尺寸158*73每坏件数1每台件数1备注工序号工序名称工序内容车间工段设备工艺装备工序时间准终单件1铸造通用夹具2时效处理通用夹具3粗车外圆121,右台阶面,外圆130,内端面C62卧式车床通用夹具4粗镗粗镗内圆40C62卧式车床通用夹具5粗车大端面,外圆125,台阶面C62卧式车床通用夹具6粗镗粗镗100H7C62卧式车床通用夹具7半精车右端面,外圆121,右台阶面,外圆130,内端面C62卧式车床通用夹具8半精镗半精镗40C62卧式车床通用夹具9半精车大端面,外圆125,右台阶面,C62卧式车床通用夹具10半精镗半精镗100H7C62卧式车床通用夹具11精车右端面,外圆121,右台阶面,外圆130,内端面C62卧式车床通用夹具12精镗精镗40C62卧式车床通用夹具13精车大端面,外圆125,右台阶面,100H,C62卧式车床通用夹具14精铣精铣B面X62卧式铣床通用夹具15粗铣粗铣100面X62卧式铣床通用夹具16精铣精铣100面X62卧式铣床通用夹具17打孔钻孔到10,扩钻到16,扩孔到17.4Z535通用夹具18精镗精镗孔至17.5T740通用夹具19钻孔在6个工位上钻孔7Z518专用夹具20攻螺纹在4个工位上钻孔4.5,攻螺纹4M5Z518专用夹具21在三个工位上钻孔7Z518专用夹具22去毛刺23终检按零件图要求全面检查装订号设计(日期)审核(日期)标准化(日期)会签(日期)韩明标记处数更改文件号签字日期标记处数更改文件号签字日期辽宁工程技术大学辽宁工程技术大学机 械 制 造 技 术 基 础课 程 设 计题 目:连接座加工工艺及左端面铣削夹具设计班级:加工09-1 班 姓名: 于智超 学 号: 0907070123 指导教师: 张兴元 完成日期: 2012-9-11 任 务 书一、设计题目:连接座加工工艺及左端面铣削夹具设计 二、原始资料(1) 被加工零件的零件图 1张(2) 生产类型:(中批或大批大量生产)三、上交材料1所加工的零件图 1张2毛坯图 1张3编制机械加工工艺过程卡片 1套4编制所设计夹具对应的那道工序的机械加工工序卡片 1套5绘制夹具装配图(A0或A1) 1张6绘制夹具中1个零件图(A1或A2。装配图出来后,由指导教师为学生指定需绘制的零件图,一般为夹具体)。 1张7课程设计说明书,包括机械加工工艺规程的编制和机床夹具设计全部内容。(约5000-8000字) 1份四、进度安排本课程设计要求在3周内完成。1第l2天查资料,绘制零件图。2第37天,完成零件的工艺性分析,确定毛坯的类型、制造方法,编制机械加工工艺规程和所加工工序的机械加工工序卡片。3第810天,完成夹具总体方案设计(画出草图,与指导教师沟通,在其同意的前提下,进行课程设计的下一步)。4第1113天,完成夹具装配图的绘制。5第1415天,零件图的绘制。6第1618天,整理并完成设计说明书的编写。7第19天21天,完成图纸和说明书的输出打印。答辩五、指导教师评语该生设计的过程中表现 ,设计内容反映的基本概念及计算 ,设计方案 ,图纸表达 ,说明书撰写 ,答辩表现 。综合评定成绩: 指导教师日期摘要本次课程设计的目的是通过课程设计,对所学习的知识进行一次综合性的应用,通过在课程设计中,不断发现问题,并且解决问题来提高自己的水平。 本次设计主要内容:设计连接座的机械加工工艺规程和铣削座端面的工艺装备并绘制出支架零件图、毛坯图、夹具装配图,夹具中的一个零件图,填写工艺卡片,编制课程设计说明书。我主要铣削连接座的左端面,通过气压缸与圆盘对工件进行夹紧,用定位板以及定位销对工件进行定位,这样工件就会在稳定的状态下被加工。AbstractThis course is designed through the curriculum design, to study the knowledge on a comprehensive application, through in the curriculum design, and constantly find out problems, and solves the problem to improve their level.This design main contents: the design of the seat connection machining process planning and milling seat face of process equipment and draw the support part drawing, blank drawing, clamp assembly drawing, fixture of one of the part drawing, fill in process card, compile curriculum design specification.I mainly milling connection seat left face, through the pneumatic cylinder and disc to workpiece clamping, with locating plate and positioning pin on the location, so that the workpiece will be in the stable state is processing.目录1.零件的工艺分析及生产类型的确定51.1零件的工艺分析51.2确定零件的生产类型72选择毛坯,确定毛坯尺寸,设计毛坯图82.1选择毛坯82.2确定毛坯尺寸82.3设计毛坯图93工艺规程的设计103.1选择定位基准103.2零件表面加工方法的选择104机械加工余量、工序尺寸的确定15五、确立切削用量及基本工时175.1工序六175.2工序八195.3工序十215.4车40H7的端面及孔至39H8215.5工序十四235.6工序十五24六、夹具的设计25心得体会26参考文献271.零件的工艺分析及生产类型的确定1.1零件的工艺分析题目所给的零件是离心式微电机水泵上的连接座。该零件的作用由其名称可知,是在两个机器部件中间起连接过渡作用的。通过连接座传递扭矩,以达到带动相连零件转动目的。零件图如下所示根据零件图,可以初步拟定零件的加工表面其间有一定位置要求。为此以下是此连接座需要机械加工的表面以及加工表面之间相对位置要求的分析,分述如下:1、 在零件图中,主视图上40H7的孔表面粗糙度上限值均为3.2um,有尺寸公差要求,其轴线为该零件形位公差的基准A;2、 在零件图中,主视图上的40H7的孔右端面的表面粗糙上限值为25um,无尺寸公差要求,且都无形位公差要求;3、 在零件图中,主视图上的121h7的外圆面,其表面粗糙度上限值为3.2um,与基准A之间有跳动要求,其公差为0.04mm;其左端台阶面的表面粗超度上限值为6.3um,与基准A之间有跳动要求,其公差为0.05mm;4、 在零件图中,主视图上17.5的孔,其表面粗糙度上限值为25um,无尺寸公差要求,也无形位公差要求;其孔的右端为深度1mm32的沉孔,其表面粗超度上限值为25um;5、 在零件图中,主视图上,125h6的外圆面,表面粗糙度上限值为3.2um,有尺寸公差要求,也有相对于基准A的形位公差跳动要求,公差值为0.05mm;其左端面和右端台阶面的表面粗糙度上限值都为6.3um,都有相对于基准A跳动形位公差要求,公差值为0.05mm;6、 在零件图中,主视图上,100H7的内孔面,表面粗糙度上限值为3.2um,有尺寸公差要求,也有相对于基准A的形位公差跳动要求,公差值为0.05mm;其孔的右端台阶面,表面粗糙度值上限值为25um;7、 在零件图中,左视图上,有6个7mm的孔,其表面粗糙度上限值为25um,无尺寸公差要求,也无位置度要求;8、 在零件图中,左视图上,有3个7mm的孔,其表面粗糙度上限值为25um,无尺寸公差要求,也无位置度要求;9、 在零件图中,左视图上,有4个7级精度的M5螺纹孔,螺纹底孔深度为12mm,螺纹深度为10mm,其表面粗糙度上限值为25um,无尺寸公差要求,也无位置度要求;10、 有零件的使用情况和加工要求可知,该零件的不加工表面为不去出材料,其表面粗糙度质量由铸造工艺保证;11、 零件的材料为 HT200灰铸铁;12、 零件毛坯通过铸造得到,不许有气孔、疏松、夹渣、裂纹等缺陷,并要求铸造后进行时效处理。根据各加工方法的经济精度及一般机床所能达到的位置精度,该零件没有很难加工的表面尺寸,上述表面的技术要求采用常规加工工艺均可以保证,对于这两组加工表面而言,可以先加工其中一组表面,然后借助于专用夹具加工另一组表面,并且保证它们的位置精度要求。1.2确定零件的生产类型零件材料为HT200。考虑零件在使用过程中所受冲击不大,零件结构又比较简单,故选择铸件毛坯。假定该零件的生产纲领是5000件每年。假设:Q=5000台/年,m=1件/台;结合生产实际,备品率a%和废品率b%分别取4%和7%。代入公式N=Qm(1+a%)(1+b%)得:N=5000台/年1件/台(1+10%)(1+1%)=5237件/年该连接座的重量约为3kg,由附表(1)知,连接座属轻型零件;由附表(2)知,该拨叉的生产类型为大批生产。附表(1)不同机械产品的零件质量型别表机械产品类型加工零件的质量/kg重型零件中型零件轻型零件电子工业机械3043050155020001002000100附表(2)机械加工零件生产类型的划分 零件特征年生产纲领/件生产类型产品类型重型零件中型零件轻型零件单件生产5以下20以下100以下成批生产小批51020200100500中批1003002005005005000大批30010005005000500050000大量生产1000以上5000以上50000以上2选择毛坯,确定毛坯尺寸,设计毛坯图2.1选择毛坯该零件材料为HT200,参照零件图上所给的该零件不加工表面的粗糙度要求,对于不进行机械加工的表面的粗糙度由铸造工艺保证,又由于该零件年产量为5000件,属大批生产,且该零件的外形尺寸不复杂,故采用金属型铸造。这从提高生产率,保证加工精度上考虑也是应该的。2.2确定毛坯尺寸 由参考文献1表5-1可知,该种铸件的尺寸公差等级CT为810级,加工余量等级由表5-5查得MA为DF级,故取CT为10级,MA为E级。参阅文献资料可知,可用查表得方法确定各加工表面的总余量,但由于查表确定的总余量值各不相同,一般情况下,除非有另有规定,要求的机械加工余量适用于整个毛坯铸件,即对所有需要机械加工的表面只规定一个值,且该值应根据最终机械加工后成品铸件的最大轮廓尺寸,在相应的尺寸范围内选取。由尺寸图可知,该零件的最大轮廓尺寸为156mm,由参考文献1表5-3查得,CT为3.6mm,由表5-4查得RMA为1.1mm。故取所有加工表面额单边余量为4mm。本零件的毛坯,虽然根据标准设计要求来说,机械加工余量应该是4mm,但有几个尺寸,根据零件的结构特征需要需要适当调整,比如125h6的毛坯外圆尺寸,由零件图可知,应该设计为138mm,121h7的毛坯外圆尺寸,由零件图可知,应该设计为130mm,17.5mm的孔,有铸造技术要求可知,应该铸造成实心的。9个7mm的孔及4个M5的螺纹孔,都铸造成实心的。无需考虑机械切削余量的设计。其毛坯图外型尺寸的公差要求及公差值详见毛坯图。2.3设计毛坯图 根据上面毛坯尺寸的确定,将零件图转变为毛坯图。详见毛坯零件图3工艺规程的设计3.1选择定位基准基面选择是工艺规程设计中的重要工作之一。基面选择得正确与合理可以使加工质量得到保证,生产率得以提高。1、粗基准的选择:对于零件而言,尽可能选择不加工表面为粗基准。而对有若干个不加工表面的工件,则应以与加工表面要求相对位置精度较高的不加工表面作粗基准。根据这个基准选择原则,选取零件的125h6mm外圆的左端端面为粗基准。2、精基准的选择:主要应该考虑基准重合的问题。当设计基准与工序基准不重合时,应该进行尺寸换算。3.2零件表面加工方法的选择由上诉的零件分析和查阅有关文献,根据本零件的加工面要求,主要用到的机床有铣床和钻床,铣床主要是用来铣削端面的,钻床是用来钻孔和攻丝的!根据零件的表面粗糙度质量要求和尺寸公差要求,对需要机械加工的各端面和孔,现制定加工方法如下:1、 对于125h6的左端面和121h6的右端面,其表面粗糙度上限值分别为6.3um和12.5um,根据附表(3)、(4)可知,这些端面可通过粗铣和半精铣能获得要求的表面粗糙度质量,这里采用铣削的原因是考虑到基准的确定及工艺方面的需求;2、 对于40H7的孔,其内表面的表面粗糙度上下值为3.2um,根据由附表(3)、(4)可知,此孔可通过粗车、半精车的加工方法,获得要求的表面粗糙度质量和尺寸公差要求;3、 对于17.5的孔,其内表面的表面粗糙度上限值为25um,根据由附表(3)、(4)可知,此孔可通过钻的加工方法,获得要求的表面粗糙度质量和尺寸公差要求;4、对于32深1mm的沉孔,其内表面的表面粗糙度上限值为25um,根据由附表(3)、(4)可知,此孔可通过扩孔的加工方法,获得要求的表面粗糙度质量和尺寸公差要求;5、对于121h7的外圆,其表面的表面粗糙度上限值为3.2um,根据由附表(3)、(4)可知,此外圆表面可通过粗车、半精车的加工方法,获得要求的表面粗糙度质量和尺寸公差要求;6、对于121h7外圆的左端台阶面,其表面的表面粗糙度上限值为6.3um,根据由附表(3)、(4)可知,此面可通过粗车、半精车的加工方法,获得要求的表面粗糙度质量和尺寸公差要求;7、对于125h6的外圆,其表面的表面粗糙度上限值为3.2um,根据由附表(3)、(4)可知,此外圆表面可通过粗车、半精车的加工方法,获得要求的表面粗糙度质量和尺寸公差要求;8、对于125h6外圆的右端台阶面,其表面的表面粗糙度上限值为6.3um,根据由附表(3)、(4)可知,此面可通过粗车、半精车的加工方法,获得要求的表面粗糙度质量和尺寸公差要求;9、对于100H7的内圆,其表面的表面粗糙度上限值为3.2um,根据由附表(3)、(4)可知,此外圆表面可通过粗车、半精车的加工方法,获得要求的表面粗糙度质量和尺寸公差要求;10、对于6-7的孔,其表面的表面粗糙度上限值为25um,根据由附表(3)、(4)可知,此孔可通过一次钻削的加工方法,获得要求的表面粗糙度质量和尺寸公差要求;11、对于3-7的孔,其表面的表面粗糙度上限值为25um,根据由附表(3)、(4)可知,此孔可通过一次钻削的加工方法,获得要求的表面粗糙度质量和尺寸公差要求;12、对于4-M5-7H的螺纹孔,可先用钻床钻削底孔,然后钳工攻丝获得。附表(3)平面加工的经济精度与表面粗糙度序号加工方法经济精度(IT)表面粗糙度选用范围1粗车1113126.3未淬硬钢、铸铁、有色金属端面加工2粗车-半精车896.33.23粗车-半精车-精车671.60.84粗车-半精车-磨削790.80.2钢、铸铁端面加工5粗刨(粗铣)-半精刨(半精铣)11126.31.6不淬硬的表面6粗刨(粗铣)-半精刨(半精铣)796.31.67粗刨(粗铣)-半精刨(半精铣)-精刨(精铣)783.21.68粗铣-拉690.80.2大量生产未淬硬的小平面9粗刨(粗铣)-精刨(精铣)-宽刃精刨670.80.2未淬硬的钢件、铸铁件及有色金属件10粗刨(粗铣)-半精刨(半精铣)-精刨(精铣)-宽刃精刨50.80.2附表(4)内圆表面加工的经济精度与表面粗糙度序号加工方法经济精度(IT)表面粗糙度Ra(m)适用范围1钻121312.5加工未淬硬钢及铸铁的实心毛坯,孔径(15-20)mm5钻-扩-粗铰-精铰781.60.86钻-扩-铰893.21.67钻-扩-机铰-手铰670.40.18钻-(扩)-拉791.60.1大批量生产,精度视拉刀精度决定9粗镗(或扩孔)111312.56.3毛坯有铸孔或锻孔的未淬火钢及铸件10粗镗(粗扩)-半精镗(精扩)9103.21.611扩(镗)-铣9103.21.612粗镗(扩)-半精镗(精扩)-精镗(铰)781.60.83.3制定工艺路线制定工艺路线,在生产纲领确定的情况下, 根据零件的几何形状、尺寸精度及位置精度等技术要求来制定工艺路线。可以考虑采用万能性机床配以专用工卡具,并尽量使工序集中来提高生产率。除此之外,还应当考虑经济效果,以便使生产成本尽量下降。根据老师给的参考工艺,现制定两种工艺路线:工艺路线一:工序一 铸造工序二 喷砂工序三 人工时效工序四 铣 以左端面为粗基准 粗铣右端面;工序五 铣 以右端面为精基准 铣左端面,保证总长70mm;工序六 半精铣 以左端面为精基准半精铣右端面;工序七 半精铣 以右端面为精基准半精铣左端面;工序八 车 以左端面及125h6的毛坯外圆定位夹紧,钻17.5的孔至图示尺寸,车40H7的端面及孔至图示尺寸。车321mm的沉台,倒角;工序九 车 以40H7的孔及其端面为定位基准,车125h6的端面及外圆至图示尺寸,车阶梯左端面9mm,车100H7的孔至图示尺寸,倒角;工序十 以100H7的孔及端面定位夹紧,车121h7的端面,保证总长69mm,车121h7的外圆及5mm的沉台,倒角;工序十一 以100H7的孔及端面定位,钻6-7的孔;工序十二 以121h7的孔及端面定位,钻3-7的孔;工序十三 以100H7的孔,钻4-M5的螺纹底孔,攻4-M5-7H深10的螺纹;工序十四 按图纸检验各部尺寸;工序十五 入库。工艺路线二:工序一 铸造工序二 喷砂工序三 人工时效工序四 对非加工表面涂刷防锈漆;工序五 划线 照顾各部尺寸,划线;工序六 铣 以左端面为粗基准,根据划线粗铣右端面;工序七 铣 以右端面为精基准,根据划线铣左端面,保证总长73mm;工序八 半精铣 以左端面为精基准半精铣右端面;工序九 半精铣 以右端面为精基准半精铣左端面,保证总长70mm;工序十 车 以左端面及125h6的毛坯外圆定位夹紧,钻17.5的孔至图示尺寸,车40H7的端面及孔至39H8;工序十一 车 以39H8的孔及右端面定位,车左端面,车125h6的外圆至128h8,并车其深度为8.5mm(同时车右端台阶面),车100H7的孔至99H8保证深度7mm;工序十二 车 调头,以99H8的孔定位,车121h7的右端面,保证总长69mm,车40H7的右端面,保证尺寸16mm及mm,车40H7的孔至尺寸,车32深度为1mm的沉孔,车121h7的外圆至尺寸,车其左台阶面至尺寸,倒角;工序十三 车 调头,以40H7的孔及其端面为定位基准,车125h6的端面及外圆至图示尺寸,车阶梯左端面9mm,车100H7的孔至图示尺寸,倒角;工序十四 以100H7的孔及端面定位,钻6-7的孔;工序十五 以121h7的孔及端面定位,钻3-7的孔;工序十六 以100H7的孔,钻4-M5的螺纹底孔,攻4-M5-7H深10的螺纹;工序十七 按图纸检验各部尺寸;工序十八 入库。对比工艺路线一和工艺路线二,显然是工艺路线二较为合理和细致,在工艺路线一中,很明显,对于基准A,是40H7的轴线,这个基准没有很好的进行确定。因为,在以125h6的毛坯外圆定位时,是以粗基准来确定基准A的,这样的基准由于装夹和加工误差较大,之后再以此基准加工其他表面时,必然会造成误差。而工艺路线二,采用了互为基准的原则,安排了粗精加工过程,这样先是粗基准的表面在一次互换后就变成了精基准,这样保证了各自的精度,从而保证了零件的质量。4机械加工余量、工序尺寸的确定连接座,零件材料为HT200,硬度157236HB,生产类型大批量,砂型铸造属型铸造毛坯。据以上原始资料及加工路线,分别确定各加工表面的机械加工余量、工序尺寸如下:4.1查机械制造工艺设计简明手册得:铣削加工余量为: 粗铣 2-4mm 半精铣 1-2mm 精铣 0-1mm 车削加工余量为: 粗 车 1-2mm 半精车 0.8mm 精车 0.3mm圆孔拉削余量为: D18-25 0.6mm D25-30 0.7mm D30-40 0.8mm镗孔加工余量为: 粗镗 0.3mm 半精镗 0.2mm 精镗 0.1mm4.2根据查机械制造工艺设计简明手册所得的加工余量可以确定毛配总加工余量如下表:工序号工步号加工内容加工余量/mm精度等级工序尺寸/mm表面粗糙度1铸造2喷砂3人工时效4对非加工表面涂刷防锈漆5照顾各部尺寸,划线6以左端面为粗基准,按划线粗铣右端面2.5IT974.512.57以右端面为精基准,按划线粗铣左端面2.5IT97212.58以左端面为粗基准,半精铣铣右端面1IT97112.59以右端面为精基准,半精铣铣左端面1IT97012.51001以左端面及125h6的毛坯外圆定位夹紧,钻17.5的孔至图示尺寸8.75IT917.52502车40H7的端面及孔至39H83.5IT839H86.31101以39H8的孔及右端面定位,车左端面0.5IT769.56.302车125h6的外圆至128h8,并车其深度为8.5mm(同时车右端台阶面)5IT8128h86.303车100H7的孔至99H8保证深度7mm2IT899H86.31201调头,以99H8的孔定位,车121h7的右端面,保证总长69mm0.5IT7696.302车40H7的右端面,保证尺寸16mm及mm,4TI91612.503车40H7的孔至尺寸,0.5IT740H73.204车32深度为1mm的沉孔,1IT93212.505车121h7的外圆至122,车其左台阶面至尺寸,倒角4.5IT8121h76.31301调头,以40H7的孔及其端面为定位基准,车125h6的端面及外圆至图示尺寸1.5IT7125h63.202车阶梯左端面9mm,车100H7的孔至图示尺寸,倒角0.5IT7100H73.214以100H7的孔及端面定位,钻6-7的孔;3.5IT972515以121h7的孔及端面定位,钻3-7的孔3.5IT972516以100H7的孔,钻4-M5的螺纹底孔,攻4-M5-7H深10的螺纹17钳工去毛刺18按图纸检验各部尺寸19入库五、确立切削用量及基本工时5.1工序六1 加工条件工件材料:HT200,b=157236MPa,铸造;加工要求:以零件的上左端面(在尺寸图中,主视图的左面)为定位基准,粗铣右端面;机 床:铣床,X62W卧式铣床。刀 具:高速钢圆柱铣刀。铣刀直径d=100mm,齿数为10,刀宽160mm,铣削宽度ae=8mm,铣削深度ap=160mm。故据参考文献1表5-143查得刀具的基本形状,由于加工铸铁b150HBS,故选前角o10后角o12,副后角o=6。已知铣削宽度ae=2.5mm,铣削深度ap=142mm。机床选用X62W型卧式万能铣床。2 切削用量(1)确定每齿的进给量fz根据参考文献1表5-144,X62W型卧式铣床的功率为7.5kW,工艺系统刚性为中等,细齿盘铣刀加工铸铁,查得每齿的进给量fz=0.150.3mm/z,现取fz=0.2mm/z。(2) 选择铣刀磨钝标准及耐用度根据参考文献1表5-148,用高速圆柱铣刀粗加工铸铁,铣刀刀齿后刀面最大磨损量为0.8mm,铣刀直径d=100mm,耐用度T=180min。(3)确定切削速度和工作台每分钟进给量fMZ其中 Cv=35,qv=0.2,xv=0.1,yv=0.4,uv=0.5,pv=0.1,m=0.2,kv=1.0。将上述数据带入公式可得V=13.1404m/min根据参考文献1表5-75,X62W型卧式铣床主轴的转速表,选择n=37.5r/min=0.625r/s,则实际切削速度v=0.19625m/s,工作台每分钟的进给量fMZ=0.21037.5=75mm/min根据参考文献表15-76,X62型卧式铣床工作台进给量表,选择fMZ=75mm/min,则实际每齿的进给量。(4) 校验机床功率 根据参考文献1表2-18中的计算公式,铣削是的功率(kW)为式中CF=650,xF=0.10,yF=0.72,uF=0.86,qF=0.86,ap=142mm,ae=2.5mm,fz=0.2,z=10,d=100mm,n=37.5r/min,kFC=0.63。将上述数据带入公式可得Fc=88.4NV=0.19625m/s,则Pc=0.0173kWX62W型卧式铣床主电动机功率为7.5kW,故所选用切削用量可以采用,所确定的切削用量为fz=0.2mm/z,fMZ=75mm/min,n=37.5r/min,v=0.19625m/s。3基本时间根据参考文献1表2-28,圆柱铣刀铣面的基本时间为则l1=19mm,l2=4mm,fMZ=75mm/min,i=1;Ti=2.2min,辅助时间5min。5.2工序八1、 加工条件工件材料:HT200,b=157236MPa,铸造;加工要求:以零件的上左端面(在尺寸图中,主视图的左面)为定位基准,精铣右端面;机 床:铣床,X62W卧式铣床。刀 具:高速钢圆柱铣刀。铣刀直径d=100mm,齿数为10,刀宽160mm,铣削宽度ae=8mm,铣削深度ap=160mm。故据参考文献1表5-143查得刀具的基本形状,由于加工铸铁b150HBS,故选前角o10后角o12,副后角o=6。已知铣削宽度ae=1mm,铣削深度ap=142mm。机床选用X62W型卧式万能铣床。2、 切削用量(1)确定每齿的进给量fz根据参考文献1表5-144,X62W型卧式铣床的功率为7.5kW,工艺系统刚性为中等,细齿盘铣刀加工铸铁,查得每齿的进给量fz=0.150.3mm/z,现取fz=0.2mm/z。(3) 选择铣刀磨钝标准及耐用度根据参考文献1表5-148,用高速钢盘铣刀粗加工铸铁,铣刀刀齿后刀面最大磨损量为0.8mm,铣刀直径d=100mm,耐用度T=180min。(3)确定切削速度和工作台每分钟进给量fMZ其中 Cv=35,qv=0.2,xv=0.1,yv=0.4,uv=0.5,pv=0.1,m=0.2,kv=1.0。将上述数据带入公式可得V=28.667m/min根据参考文献1表5-75,X62W型卧式铣床主轴的转速表,选择n=95r/min=1.583r/s,则实际切削速度v=0.4972m/s,工作台每分钟的进给量fMZ=0.21095=190mm/min根据参考文献表15-76,X62型卧式铣床工作台进给量表,选择fMZ=190mm/min,则实际每齿的进给量。(5) 校验机床功率 根据参考文献1表2-18中的计算公式,铣削是的功率(kW)为式中CF=650,xF=0.10,yF=0.72,uF=0.86,qF=0.86,ap=142mm,ae=1mm,fz=0.2,z=10,d=100mm,n=95r/min,kFC=0.63。将上述数据带入公式可得Fc=40.2NV=0.4972m/s,则Pc=0.02kWX62W型卧式铣床主电动机功率为7.5kW,故所选用切削用量可以采用,所确定的切削用量为fz=0.2mm/z,fMZ=190mm/min,n=95r/min,v=0.4972m/s。3、 基本时间根据参考文献1表2-28,圆柱铣刀铣面的基本时间为则l1=19mm,l2=4mm,fMZ=190mm/min,i=1;Ti=0.8684min,辅助时间5min。5.3工序十1、 加工条件工件材料:HT200,b=157236MPa,铸造;加工要求:以左端面及125h6的毛坯外圆定位夹紧,钻17.5的孔至图示尺寸,车40H7的端面及孔至39H8;机 床: C620-1车床刀 具: YG6硬质合金车刀,根据参考文献1表5-112,由于C620-1车床中心高为200mm,故选刀杆尺寸BH=16mm25mm(镗孔时,使用相同的刀片不同的刀杆),刀片厚度4.5mm。根据表5-113,选择刀具前角o12后角o6,主偏角Kr=90,副偏角Kr=10,刃倾角s=0,刀尖过渡圆弧半径R=0.8mm。及17.5mm的锥柄高速钢麻花钻头。5.4车40H7的端面及孔至39H8 1)、切削用量(1)确定被吃刀量粗车单边余量为ap=3.5mm(2)确定进给量 根据表5-114,镗刀刀杆尺寸为16mm, 工件孔的直径为3040mm时,根据参考文献1表5-115查得的进给量选择f=0.150.25mm/r。取进给量为f=0.25mm/r。(3)确定的进给量善需满足机床进给机构强度的要求,故需进行校验。根据表参考文献15-55,车床进给机构允许的进给力F=3530N。根据参考文献1表5-124, 、时,进给力。的修正系数1 , 1,1.17,故实际进给力为=11401.17=1333.8N,所选的进给量=0.25mm/r可用。(4)选择刀具磨钝标准及耐用度 根据参考文献1表5-119,车刀后刀面最大磨损量取 1mm,车到耐用度T=30min。(5)确定切削速度根据参考文献1表5-121 ,当用YG6硬质合金车刀加工 , ,切削速度。根据参考文献1表2-8,切削速度的修正系数为0.8,0.65,0.81,故=900.80.650.811.151=43.594m/min=355.99r/min按参考文献1表5-56车床转速,选择C620-1车床的标准转速,则实际切削速度。(6)校验机床功率由表5-126,当、时,切削功率的修正系数为, ,故实际切削时的功率为。根据参考文献1表5-59,当时,机床主轴允许功率,故所选切削用量可在C620-1车床上进行。最后确定的切削用量为, 2)、基本时间根据参考文献1表2-21,车削基本时间为则=14.3s,辅助时间3min。5.5工序十四1、 加工条件 工件材料:HT200,b=157236MPa,铸造; 加工要求:钻6-7mm的孔; 机 床:摇臂钻床Z3025。 刀 具:7mm的高速钢麻花钻钻头。2、选择切削用量 (1)决定进给量根据参考文献1表5-127,可查得进给量f=0.360.44mm/r,现取f=0.4mm/r (2)选择钻头磨顿标准及耐用度根据参考文献1表5-130,钻头后刀面的最大磨损量为0.8mm,耐用度T=60min。(3) 确定切削速度 根据参考文献1表5-133,查得v=13m/min,n=591.45r/min。根据Z3025摇臂钻床说明书选择主轴实际转速n=600r/min。则实际切削速度为v=13.188m/min 3、基本时间根据参考文献表12-26中的计算公式iL=8+5=13mm,f=0.4mm/r,n=600r/min,带入上式得,辅助时间5min。5.6工序十五1、 加工条件 工件材料:HT200,b=157236MPa,铸造; 加工要求:钻3-7mm的孔; 机 床:摇臂钻床Z3025。 刀 具:7mm的高速钢麻花钻钻头。2、选择切削用量 (1)决定进给量根据参考文献1表5-127,可查得进给量f=0.360.44mm/r,现取f=0.4mm/r (2)选择钻头磨顿标准及耐用度根据参考文献1表5-130,钻头后刀面的最大磨损量为0.8mm,耐用度T=60min。(4) 确定切削速度 根据参考文献1表5-133,查得v=13m/min,n=591.45r/min。根据Z3025摇臂钻床说明书选择主轴实际转速n=600r/min。则实际切削速度为v=13.188m/min 3、基本时间根据参考文献表12-26中的计算公式iL=10+5=15mm,f=0.4mm/r,n=600r/min,带入上式得,辅助时间5min。将前面进行的工作所得的结果,填入工艺文件。六、夹具的设计6.1夹具设计原理工件定位定位如图所示,Z轴方向,在夹具内部有气压缸,与气压缸连杆上有一圆盘,通过气压缸带动圆盘上下移动,可以限制Z轴方向的移动,在工件下方有一定位板,与工件间
- 温馨提示:
1: 本站所有资源如无特殊说明,都需要本地电脑安装OFFICE2007和PDF阅读器。图纸软件为CAD,CAXA,PROE,UG,SolidWorks等.压缩文件请下载最新的WinRAR软件解压。
2: 本站的文档不包含任何第三方提供的附件图纸等,如果需要附件,请联系上传者。文件的所有权益归上传用户所有。
3.本站RAR压缩包中若带图纸,网页内容里面会有图纸预览,若没有图纸预览就没有图纸。
4. 未经权益所有人同意不得将文件中的内容挪作商业或盈利用途。
5. 人人文库网仅提供信息存储空间,仅对用户上传内容的表现方式做保护处理,对用户上传分享的文档内容本身不做任何修改或编辑,并不能对任何下载内容负责。
6. 下载文件中如有侵权或不适当内容,请与我们联系,我们立即纠正。
7. 本站不保证下载资源的准确性、安全性和完整性, 同时也不承担用户因使用这些下载资源对自己和他人造成任何形式的伤害或损失。

人人文库网所有资源均是用户自行上传分享,仅供网友学习交流,未经上传用户书面授权,请勿作他用。