汽车零件牛杆调整臂的模具设计【2套模具】【19张图纸】【优秀】
收藏
资源目录
压缩包内文档预览:
编号:274113
类型:共享资源
大小:579.53KB
格式:RAR
上传时间:2014-05-05
上传人:J****
认证信息
个人认证
方**(实名认证)
江苏
IP属地:江苏
50
积分
- 关 键 词:
-
汽车零件
牛杆调整臂
模具设计
图纸
- 资源描述:
-
汽车零件牛杆调整臂的模具设计
33页 16000字数+说明书+外文翻译+开题报告+19张CAD图纸【详情如下】
中期.doc
外文翻译--模具的发展.doc
汽车零件牛杆调整臂的模具设计开题报告.doc
汽车零件牛杆调整臂的模具设计论文.doc
设计图纸19张.dwg
目 录
1 绪论9
1.1 冲压制品设计概论9
1.1.1 模具的概念及其在工业生产中的作用9
1.1.2 冲压加工工艺及其应用9
1.1.3 冲压所用材料及其性能10
1.1.4 冲模的组成11
1.1.5 冲模的工作部分零件必须具备的性能11
1.1.6 冲模的成形特点11
1.2冲压模具加工过程中的问题与质量控制12
1.2.1 冷冲压模具安装的问题12
1.2.2 关于冷冲压模具加工过程中工艺改进措施12
1.3.1 模具零件的热处理13
1.3.2 冲裁凸模热处理方法13
1.3.3 冲裁凹模热处理方法14
2 工艺设计15
2.1 零件介绍15
2.2 零件工艺性分析15
2.3 工艺方案的确定16
3 排样设计17
3.1 毛坯排样设计17
3.1.1 条料搭边值的确定17
3.1.2 条料的宽度17
3.1.3 步距18
3.2 材料的利用率19
3.2.1 排样方式的确定19
3.2.2 送料进距的确定19
4 工艺计算20
4.1 冲压工艺力的计算20
4.1.1 冲裁力计算20
4.1.2 成型力的计算21
4.1.3 卸料、顶件力的计算22
4.2压力中心计算22
5 模具总体概要设计23
5.1 模具概要设计23
5.2 模具零件结构形式确定23
5.2.1 定位机构24
5.2.2 卸料机构24
5.2.3 导向机构24
6 模具详细设计25
6.1 工作零件25
6.1.1冲裁凸、凹模刃口尺寸计算25
6.1.2成型模工作部分尺寸的确定27
6.1.3 凸模高度设计27
6.2定位零件28
6.2.1 挡料零件28
6.3 出件零件28
6.3.1 卸料零件28
6.3.2 顶件零件29
6.4 导向零件29
6.5 其他零件30
7 设备选择31
7.1 设备吨位确定31
7.1.1 设备类型的选择31
7.1.2 设备规格的选择31
7.2 设备校核32
8 结 论33
参考文献34
致谢35
毕业设计(论文)知识产权声明36
毕业设计(论文)独创性声明37
摘 要
本文分析了支撑板的结构、尺寸、精度和原材料性能,并具体指出了该产品的成型难点;拟定了冲孔落料复合模和成型模冲压工艺方案;详细阐述了排样设计方法和过程,确定了该产品需要冲孔、落料、成型的二维和排样图;完成了所有必要的工艺计算,包括模具刃口尺寸、各工位冲压力、总的冲压工艺力、压力中心等;概述了模具概要设计方法,系统的阐述了模具主要零件的结构、尺寸设计及标准的选用。同时阐述了模具的工作过程、各成形动作的协调性并对设备选择和核算进行了较为细致的叙述。
关键词:成型制件;模冲孔落料复合模;成型模;工艺分析;模具设计冲模的工作部分零件必须具备的性能
冲模的工作部分零件又称成型零件,它主要包括凸模、凹模及凸凹模等。由于冲压有冷冲压与热冲压,而冲压工序又分为分离工序(冲裁)与成型工序(弯曲、拉深、成形)两大类。在分离工序的工作过程中,除承受使材料分离所需的冲压力外,还承受着与材料断面间的剧烈摩擦;在成形工序的工作过程中,冲模除承受材料塑性变形所需的冲压力外,其表面也受到材料的塑性流动而产生的强力摩擦。因此,这就要求冲模的工作部位要具备耐冲击、耐磨损的高强度、高硬度性能。而在材料加热状态下使用的冲模,工作零件还要求具有耐热性能,这样才能保证其冲模的耐用度及使用寿命。
根据冲模的上述要求,冲模的工作部分一般采用碳素工具钢或合金工具钢制成。对于高速冲压或要求高寿命的冲模,其工作部分可采用硬质合金制作。
1.1.6 冲模的成形特点
冲模是指在室温下把金属或非金属板料放在模具内,通过压力机和模具对板料施加压力,使板料发生分离或变形制成所需零件的模具。各类冷冲模的成形特点是:
1)冲裁模。冲裁模的成形特点是:将一部分材料与另一部分材料分离。落料冲裁模的成型特点是将材料封闭的轮廓分开,而最终得到的是一平整的零件。而冲孔冲裁模的成型特点是将零件内的材料与封闭的轮廓分离,使零件得到孔。
2)弯曲模。弯曲模的成形特点是:将板料或冲裁后的胚料通过压力在模具内弯成一定的角度和形状。
3)深模。拉深模的成形特点是:将经过冲裁所得到的平板胚料,压制成开口的空心零件。
4)形模。成形模的成形特点是:用各种局部变形的方法来改变零件或胚料的形
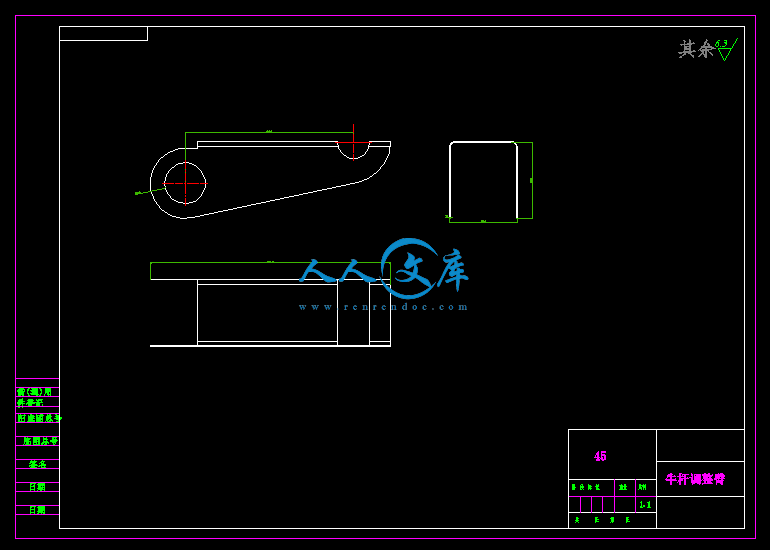
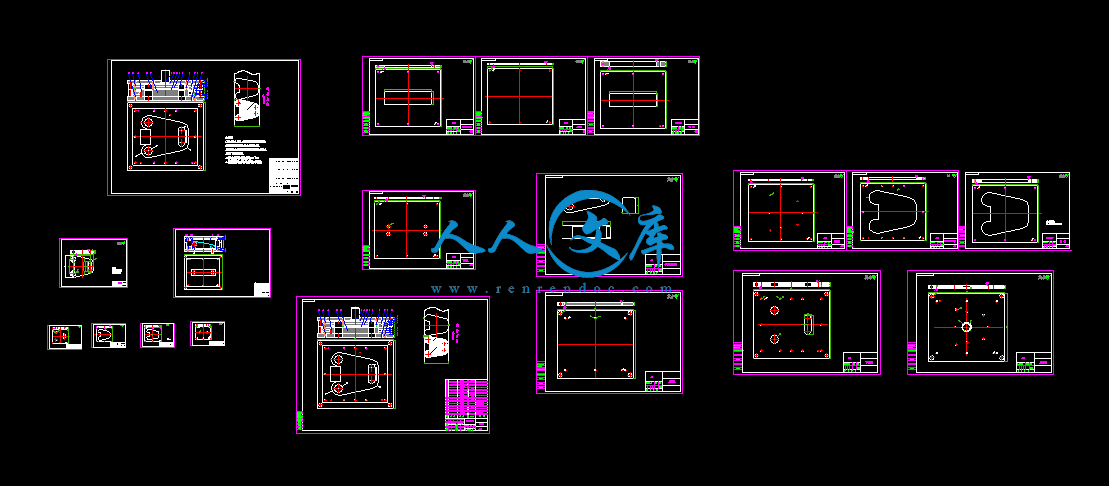
- 内容简介:
-
毕业设计(论文)中期报告题目:汽车零件牛杆调整臂的模具设计 系 别 机电信息系 专 业 机械制及其自动化 班 级 姓 名 学 号 导 师 20130年 3月 18日 一、论文总体概述 本次毕业设计的课题是:汽车零件牛杆调整臂的冲压模具设计。 冲压模具:由金属盒其他刚性材料制成的用于冲压成形的工具。其基本零部件包括凸模、凹模以及压边装置。模具设计与制造技术水平的高低,是衡量一个国家产品制造水平高低的重要标志之一,在很大程度上决定着产品的质量、效益和新产品的开发能力。二、设计进展状况 为了加深对本课题的认识,了解国外的技术层次,上网查询了外文资料文献,并做了部分摘要的翻译,为毕业设计的成功做出了铺垫。鉴于冲压模具于我是一门新的学科,很多知识需要现学现做,所以我选择了从基础开始。 1.冷冲压工序 冷冲压工序按工作性质分为分离工序和变形工序两大类。 分离工序主要是冲裁。而变形工序包括了弯曲、拉深、成形、挤压等步骤。 2.冷冲压模具的基本呢结构形式 (1)单工序冲模 (2)复合模 (3)连续模 3.冷冲模零件的分类 (1)冲模工艺零件 A.工作零件 B.定位零件 C.卸料、推件零件 (2)冲模辅助零件 A.导向零件 B.支持零件 C.紧固零件 D.供力零件 冲裁的部分。主要是了解认识了冲裁。 冲裁是利用模具使板料沿一定的轮廓形状产生分离的一种冲压工序,冲裁包括落料、冲孔、切口、切边等工序。其中冲裁间隙是冲裁中的一个重要部分。间隙的大小直接影响了冲裁力的大小,冲件精度和冲件断面质量。在冲裁过程有一个需要注意的地方,就是冲裁件毛刺的产生。冲裁间隙过大时出现拉断毛刺,而间隙过小时则出现挤压毛刺。同样的冲裁模的刃口变钝,也会产生毛刺。除了毛刺还有冲裁件的工艺性,排样搭边等需要注意的地方。冲裁这一步骤需要的计算,主要有凸、凹模刃口尺寸计算,冲裁力计算。 其中凸凹模刃口尺寸的计算有两种方法。 第一种应用在凸模和凹模分开加工的情况。我选择的是另一种方法,先按计算的尺寸制造凸模或凹模中的一件作为基准件,然后按基准件实际尺寸配制另一件。这种方法有以下特点:1.加工基准价时,可适当放宽公差,使其加工简单。2.模具间隙是在配作加工中保证,在计算中可以免去校核凸模与凹模的公差和小于等于最大间隙和最小间隙的差。3.尺寸标注简单,只需在基准件上标注尺寸和公差,配制件仅注明按基准件留出间隙配制即可。 冲裁力的计算 冲裁力的计算公式为:P0= Lt 式中:P0冲裁力,N; L 冲裁件冲切轮廓长度,mm; t 冲压材料厚度,mm; 材料抗剪强度,MPa。完成了冲裁部分后,紧接着又进行了弯曲部分的设计计算。 弯曲是指将材料弯成一定角度和形状,其中V形弯曲是最基本的一种。弯曲时的弯曲半径R越小,毛坯外表面变形程度就越大。如果弯曲半径过小,毛坯外边面变形可能会超过材料变形极限而产生裂纹,因此,弯曲工艺受到最小弯曲半径的限制。弯曲中也有很多的不确定因素, 比如弯曲时的回弹,偏移。不过这些不确定因素,也是可以尽可能避免的。例如材料的力学性能,相对弯曲半径,弯曲方式等诸多因素可以有效的避免回弹。同样偏移也可以采用压料装置,使毛坯在压紧状态下逐渐弯曲成型。 三、后期的工作安排 进一步完善前期的工作计算,编制冲压工艺规程。完成总装配图和零件图,制定模具加工工艺流程。进行毕业设计总结,整理毕业设计论文,为这次毕业设计答辩做好最终答辩准备,为自己的大学画一个完整的句号。 指导教师签字: 年 月 日Modo developmentThe current existence question and the disparity mainly display in following several aspects: (1) The total quantity falls short of demand Domestic mold assembling oneself rate only ,about 70%. Low-grade mold , center upscale mold assembling oneself rate only has 50% about . (2) The enterprise organizational structure, the product structure, the technical structure and the import and export structure does not gather Iin our country mold production factory to be most is from the labor mold workshop which produces assembles oneself (branch factory), from produces assembles oneself the proportion to reach as high as about 60%, but the overseas mold ultra 70% is the commodity mold. The specialized mold factory mostly is large and complete, small and entire organization form, but overseas mostly is small but, is specially small and fine. Domestic large-scale, precise, complex, the long life mold accounts for the total quantity proportion to be insufficient 30%, but overseas in 50% above 2004 years, ratio of the mold import and export is 3.7:1, the import and export balances the after net import volume to amount to 1.32 billion US dollars, is world mold net import quantity biggest country . (3) The mold product level greatly is lower than the international standard The production cycle actually is higher than the international water broad product level low mainly to display in the mold precision, cavity aspect and so on surface roughness, life and structure . (4) Develops the ability badly, economic efficiency unsatisfactory our country mold enterprise technical personnel proportion low The level is lower, also does not take the product development, frequently is in the passive position in the market. (1) Layout design of layout methods and take the boundary value a great impact on the die life, too small to take the boundary value, often causing rapid wear and convex mold, die bite wounds on the. Starting from material savings, take the boundary value smaller the better, but take the edge is less than some value, the cut surface of the mold and the quality of life adversely. There will be left behind in the blanking die Q-gap were to produce spare parts glitch, or even damage the die edge, reduce die life. Therefore, consider increasing the material utilization of the same time, parts must yield, quality and life expectancy to determine the layout methods and take the boundary.(2) die structure prone to stress concentration on the cracking of the die structure, composite structure can be used or mosaic structure, and prestressed structure to enhance the mold life.(3) the impact of clearance when the gap is too small, compressed extrusion of interest, increased friction, increased wear, the wear side of aggravated discharge and push pieces after blanking time, materials and convex, the friction between die will cause wear and tear than the end edge on the side of the grinding much, but also easily lead to convex, concave mold temperature is high, the adsorption of metal debris in the side edge to form a metal tumor, so that male and female die chipping or expansion occurs crack phenomenon. Therefore, the gap is too small to Die Life very bad. Gap is too large will increase the punch and the die face the edge of the concentration of stress, resulting in a sharp increase in stress, so blade edge quickly lose angular yield deformation. Therefore, addition of blanking force, thereby enabling faster edge edge wear, reduce die life. But in order to reduce the male and female die wear, extending mold life, while ensuring quality of stamping pieces under the premise that larger space designed properly it is necessary. Die-oriented structure of the life of a reliable guide for the working parts reduce wear, prevent male and female die bite wound is very effective. In particular, non-small-Q gap Q gap or Die, compound die and multi-position progressive die even more important. To improve the die life, must be based on processes and the demand of precision, the correct choice-oriented form and orientation accuracy, the choice should be higher than the accuracy-oriented convex, concave mold with precision.(5) the impact of cold stamping materials, cold stamping materials selected should meet the design requirements of workpieces and stamping process requirements, or easy to mold damage and reduce mold life. Poor surface quality of cold stamping, punching, cracking when the workpiece is also easy to scratch mold. Bad cold stamping plastic materials, deformation is small, easy to press when the workpiece rupture, but also easy to scratch mold. In addition, the material thickness tolerances shall comply with national standards. Die because of a certain thickness of material suitable for forming, bending, flanging, drawing die of the male and female die structure gap is directly determined by the thickness of the material. Therefore, uneven thickness, will result in waste generation and mold damage. Life of a mold material properties, chemical composition, structure, hardness and comprehensive reflection of metallurgical quality. Among them, the material properties and heat treatment affect the quality of the most obvious. Mold material properties on the impact of die life is great. If the same workpiece, using a different mold material of the bending test, the test results: The 9Mn2V material, the life of 5 million; with Crl2MoV nitriding, the life of up to 40 million. Therefore, the choice of materials, the batch size should be based on workpiece, rational use of mold materials. The hardness of the die parts to Die Life a great impact. But not the higher hardness, longer die life. This is because the hardness and strength, toughness and abrasion resistance are closely related. Some die demands of high hardness, long life. Such as the use of T10 steel dies, hardness 54 58HRC, only washed thousands of times a burr on the workpiece great. If the hardness to 60 64HRC, the grinding life of up to 2 to 3 million. However, if continue to improve hardness, fracture occurs earlier. Some die hardness should not be too high, as the die manufacturing using Crl2MoV 58 62HRC hardness, the general life of 2-3 million, invalid form of chipping and cracking, and if the hardness down to 54 58HRC, life expectancy increased to 5 60 000, but decreased to 50 53HRC hardness appears easy to blunt the die edge phenomenon. Thus, mold hardness must be based on material properties and failure modes may be. Should enable the hardness, strength, toughness and wear resistance, resistance to fatigue strength needed to achieve a particular stamping process the best match. The surface of the mold heat treatment to strengthen the quality and The surface of the mold heat treatment to strengthen the quality and The surface of the mold heat treatment to strengthen the quality and The surface of the mold heat treatment to strengthen the quality and impact on life impact on life impact on life impact on life . Mold heat treatment the nature and quality of life of the mold a great impact. Practice shows that the die parts of the quenching distortion and cracking, early fracture during use, while the metallurgical and materials quality, forging quality, mold structure and process related, but related more to die of heat treatment. According to statistical analysis of failure causes of mold, heat treatment failure due to improper accounting for more than 50%. Practice shows that the mold material must be accompanied by high heat treatment process properly, can really play a materials potential. Parts surface hardening mold work purpose is to obtain the effect of external hard tough inside, so be hardness, wear resistance, toughness, good resistance to fatigue with. Many ways to die surface hardening, surface treatment technology of new technologies developed rapidly. In addition to Nitrocarburizing and ion nitride, boride, seepage niobium, vanadium permeability, hard chrome plated and spark strengthening, the chemical vapor deposition (CVD) and physical vapor deposition (PVD) has been gradually adopted. By CVD and PVD treatment, the mold surface covered with super-hard material, such as TiC, TiN, etc. High hardness, wear resistance, corrosion resistance, adhesion is very good, can improve the die life several times to several times. 4. Manufacturing precision of the die parts of die lifeManufacturing precision of the die parts of die lifeManufacturing precision of the die parts of die lifeManufacturing precision of the die parts of die life Precision die manufacturing and life in it in particular, mold surface roughness on the mold a great impact. If using Crl2MoV steel blanking die, if the surface roughness value R = 1 m, its life span is about 30,000. Such as polished by the precision, surface roughness value R = 0.4 m, life can be increased to 4-5 million. Therefore, the working parts of the mold surface, the general must go through grinding, grinding, polishing and other finishing and fine processing. 5. Other aspects of the impact of die life Other aspects of the impact of die life Other aspects of the impact of die life Other aspects of the impact of die life. (1) Press the accuracy is not high, but also easy to make die damage. (2) die in the press or not installed properly and the operators technical level, on the tool life is also greatly affected. (3) dies in the custody and maintenance of good and bad, and the use of lubricant condition also affects mold life. Cold die clearances between control and adjusting Cold die clearances between control and adjusting Cold die clearances between control and adjusting Cold die clearances between control and adjusting methodmethodmethodmethod.Cold stamping mould convex, concave die size and distribution of the clearance degree directly affect the quality of the blanking pieces and the length of the service life of the die. In guarantee blanking pieces space is mould manufacturing assembly very important link, and assembly quality will directly influence the convex, concave die if the clearance between the uniform. Such as the process of convex, concave die size precision although already meet the requirements, but in assembling if adjustment is bad, can cause clearance does not even, rushed out of the spare parts of the raw edges. Even rushed out of unqualified parts. The mold assembly is key to control convex, concave die of relative positions, in order to ensure that the convex, concave die, uniform and the clearance between the right to rush out of qualified parts. 1. Die before assembly the problems that should be paid attentionDie before assembly the problems that should be paid attentionDie before assembly the problems that should be paid attentionDie before assembly the problems that should be paid attention Convex, concave die and mould parts itself is clearance of the precision, and the assembly of the assembly process is reasonable. In order to ensure that the position of the convex, concave die correctly and gaps even, mould design, processing to assembly from the whole link should pay attention to the following questions:(1)Convex, concave die design and manufacture of the right Design should be based on the above all when die cutting the section of a quality, service life of die factors such as the reasonable selection of convex, concave die clearance. And to consider the mould in the process of using that gap wear increases, general in the design the least reasonable clearance when mould. And in the manufacturing process can ensure the parts processing precision and quality, in the assembly process ensure convex, concave die gap even, this for processing complex shape is very key parts. (2)Assembly method the choice should be reasonable Die assembly method include roughly assembly method and direct with assembly method. Before the assembly must be carefully study mold assembly drawing, full consideration and analysis of the structure characteristics of punching die, die parts processing technology and processing accuracy etc, in order to choose convenient, accurate and reliable assembly method to ensure the quality of blanking pieces. 2. Convex, concave die gap between the control and adConvex, concave die gap between the control and adConvex, concave die gap between the control and adConvex, concave die gap between the control and adjustment of the justment of the justment of the justment of the methodmethodmethodmethod Convex, concave die clearance control, should according to die structure, clearance size, blanking pieces of quality and practical assembly condition to selected. Convex, concave die gap between the control and adjustment method have the following kinds. (1)Pervious to light method Will convex, concave die after molmerged, shone a light on the underside, observe the convex, concave die around through light and distribution to judge the size of the clearance and uniformity. If not even, to adjust to evenly between fixed again, this method is suitable for small gap plate stamping die. (2)Feeler method Will convex, concave die after molmerged, convex, concave die into the thickness of unilateral clearance feeler convex, concave die gaps in each direction. Then tighten the screw on mode. Finally put paper to stamping and will last mould seat and fixed on board with drilling, reaming positioning pin hole, and at a pin location. (3)Gaskets DiaoZhengFa Gasket adjustment method is simple, convenient, clearance is used widely. As shown in figure 1 shows, the mat with good contour mat iron, will gaskets wrapped in the punch to the punch into the concave mould, observe the convex, concave die clearance condition. If clearance does not even, with striking the protruding models of fixed plate method clearance adjustment, then tighten the screw on mode. Finally put paper to stamping, observation on paper cutting around burr and even rate to judge whether clearance convex, concave die even, to adjust the gap until cutting burr uniform so far. Finally the mould seat and the plate with drilling, reaming positioning pin hole, and enter the pin location. This method widely used cutting materials focusing thick large clearance and bending stamping, deep drawing mould clearance control. (4) Chemical method When the convex, concave die complex shape, the use of the above several methods more difficult to adjust the gap, the chemical method can be used to control the gap, the plating method is used. Plating method is the punch in the work surface coated with copper or zinc instead of washers. The plating thickness and unilateral gap is same, blade people concave die hole, and check the move without block phenomenon can assembly tighten. Coating in use process will die fall off naturally, need not removed. This uniform coating, can improve the uniformity of assembling clearance. (5) Technology DiaoZhengFa measures The main technological measures to adjust the gap between two kinds of the mould method:.1. Size method Processing of the punch, will the punch front-end appropriate lengthen, extended period of section size and sunken model hole processing to the same size. Assembly, make the punch into female model hole, natural form the cutting clearance, and then to the punch with fixed together with the punch mould seat on board with the pin for fixed and will last longer period of the punch front can remove form even clearance. 2. Positioning hole method Process positioning hole method and the inside of the progressive die principle about. Processing, the punch in fixed board and concave die on the same position processing two positioning hole, can will locate hole and the mold cavity a cut out. Assembly, in the positioning hole insert pins to ensure that gap. (6) Standard model method According to the drawing wedm in advance in processing a standard model or the qualified stamping parts, to adjust the assembly put it in between convex, concave die, upper and lower die relative motion can be reasonable degree when appropriate. (7) Measurement method Measuring method of the measuring tool have feeler. A feeler method after the adjustment convex, concave die clearance good uniformity, it is the commonly used method. Assembly, the punch in the concave die in the hole, convex, concave die according to the size of the clearance choose different specifications of the feeler insert convex, concave die clearance, inspection concave die around the blade gap everywhere, and according to the measured results adjustment. If the adjustment of the punch fixed board knock until adjust good so far. (8) Adjustment method of repair match means Die in use after period of time, because the convex, concave die normal wear and tear. To working parts inspection, if products produce burr, convex, concave die dull and collapse the blade factors, it is because of the convex, concave die clearance for wear changed, namely bigger or not even. To make the convex, concave die restored to the original gap value out of parts can use the following method to qualified for repair match means. 1. Convex, concave die clearance greaten repair match means method General dies in use after period of time, because normal wear will make convex, concave die gap increase gradually, thus to make the work and so on a series of problems produced burr. This kind of circumstance, can use first thickness is equal to one of the KuaiGui insert gap between the convex, concave die, if convex, concave die clearance does not too big, the grinding work part of the blade continue to use, can improve the quality of stamping. When gap value too big when, the recoverable high temperature heat of local forging the modification methods female die size make it restored to the original gap value. Workpiece cooling followed by the pressure seal the law to file to trim gap value, and with the flame hardening method to improve the blade surface hardness. 2. Convex, concave die clearance does not even repair match means method Dies after a period of using, clearance does not even can make blunt a local produce burr or the blade was edge chewed. In normal wear punching die, because after wearing precision guide device that reduce convex, concave die happen relatively migration, respectively in the guide pin and a guide to cover on the plating chromium layer the restored to its original size, again through the pressure seal the law will remove file high. If it is due to the pins loosening lose positioning function and cause different convex, concave die heart, and cause convex, concave die clearance does not even. Should first will convex, concave die gap adjusting well, to match for taper pin.Due to historical reasons for the formation of closed, big and complete enterprise features, most enterprises in China are equipped with mold workshop, in factory matching status since the late 70s have a mold the concept of industrialization and specialization of production. Production efficiency is not high, poor economic returns. Mold production industry is small and scattered, cross-industry, capital-intensive, professional, commercial and technical management level are relatively . According to incomplete statistics, there are now specialized in manufacturing mold, the product supporting mold factory workshop (factory) near 17 000, about 600 000 employees, annual output value reached 20 billion yuan mold. However, the existing capacity of the mold and die industry can only meet the demand of 60%, still can not meet the needs of national economic development. At present, the domestic needs of large, sophisticated, complex and long life of the mold also rely mainly on imports. According to customs statistics, in 1997 630 million U.S. dollars worth of imports mold, not including the import of mold together with the equipment; in 1997 only 78 million U.S. dollars export mold. At present the technological level of China Die & Mould Industry and manufacturing capacity, Chinas national economy in the weak links and bottlenecks constraining sustainable economic development. 1. Research on the Structure of industrial products moldResearch on the Structure of industrial products moldResearch on the Structure of industrial products moldResearch on the Structure of industrial products mold.In accordance with the division of China Mould Industry Association, China mold is divided into 10 basic categories, which, stamping die and plastic molding two categories accounted for the main part. Calculated by output, present, China accounts for about 50% die stamping, plastic molding die about 20%, Wire Drawing Die (Tool) about 10% of the worlds advanced industrial countries and regions, the proportion of plastic forming die die general of the total output value 40%. Most of our stamping die mold for the simple, single-process mode and meet the molds, precision die, precision multi-position progressive die is also one of the few, die less than 100 million times the average life of the mold reached 100 million times the maximum life of more than accuracy 3 5um, more than 50 progressive station, and the international life of the die 600 million times the highest average life of the die 50 million times compared to the mid 80s at the international advanced level.Chinas plastic molding mold design, production technology started relatively late, the overall level of low. Currently a single cavity, a simple mold cavity 70%, and still dominant. A sophisticated multi-cavity mold plastic injection mold, plastic injection mold has been able to multi-color preliminary design and manufacturing. Mould is about 80 million times the average life span is about, the main difference is the large deformation of mold components, excess burr side of a large, poor surface quality, erosion and corrosion serious mold cavity, the mold cavity exhaust poor and vulnerable such as, injection mold 5um accuracy has reached below the highest life expectancy has exceeded 20 million times, the number has more than 100 chamber cavity, reaching the mid 80s to early 90s the international advanced level. 2 .mold Present Status of Technologymold Present Status of Technologymold Present Status of Technologymold Present Status of Technology.Technical level of Chinas mold industry currently uneven, with wide disparities. Generally speaking, with the developed industrial countries, Hong Kong and Taiwan advanced level, there is a large gap. The use of CAD / CAM / CAE / CAPP and other technical design and manufacture molds, both wide application, or technical level, there is a big gap between both. In the application of CAD technology design molds, only about 10% of the mold used in the design of CAD, aside from drawing board still has a long way to go; in the application of CAE design and analysis of mold calculation, it was just started, most of the game is still in trial stages and animation; in the application of CAM technology manufacturing molds, first, the lack of advanced manufacturing equipment, and second, the existing process equipment (including the last 10 years 14the introduction of advanced equipment) or computer standard (IBM PC and compatibles, HP workstations, etc.) different, or because of differences in bytes, processing speed differences, differences in resistance to electromagnetic interference, networking is low, only about 5% of the mold manufacturing equipment of recent work in this task; in the application process planning CAPP technology, basically a blank state, based on the need for a lot of standardization work; in the mold common technology, such as mold rapid prototyping technology, polishing, electroforming technologies, surface treatment technology aspects of CAD / CAM technology in China has just started. Computer-aided technology, software development, is still at low level, the accumulation of knowledge and experience required. Most of our mold factory, mold processing equipment shop old, long in the length of civilian service, accuracy, low efficiency, still use the ordinary forging, turning, milling, planing, drilling, grinding and processing equipment, mold, heat treatment is still in use salt bath, box-type furnace, operating with the experience of workers, poorly equipped, high energy consumption. Renewal of equipment is slow, technological innovation, technological progress is not much intensity. Although in recent years introduced many advanced mold processing equipment, but are too scattered, or not complete, only about 25% utilization, equipment, some of the advanced functions are not given full play. Lack of technology of high-quality mold design, manufacturing technology and skilled workers, especially the lack of knowledge and breadth, knowledge structure, high levels of compound talents. Chinas mold industry and technical personnel, only 8% of employees 12%, and the technical personnel and skilled workers and lower the overall skill level. Before 1980, practitioners of technical personnel and skilled workers, the aging of knowledge, knowledge structure can not meet the current needs; and staff employed after 80 years, expertise, experience lack of hands-on ability, not ease, do not want to learn technology. In recent years, the brain drain caused by personnel not only decrease the quantity and quality levels, and personnel structure of the emergence of new faults, lean, make mold design, manufacturing difficult to raise the technical level. Our country each mold staff average year creation output value approximately ,ten thousand US dollars, overseas mold industry developed country mostly 15 to10,000 US dollars, some reach as high as 25 to10,000 US dollars, relative is our country quite part of molds enterprises also continues to use the workshop type management with it, truly realizes the enterprise which the modernized enterprise manages few To create the above disparity the reason to be very many, the mold long-term has not obtained the value besides the history in as the product which should have, as well as the most state-owned enterprises mechanism cannot adapt the market economy, but also has the following several reasons: (1) Country to mold industry policy support dynamics also insufficiently Although the country already was clear about has promulgated the mold profession industrial policy, but necessary policy few, carried out dynamics to be weak. At present enjoyed the mold product increment duty enterprise nation 185, the majority enterprise still the tax burden is only overweight. The mold enterprise carries on the technological transformations introduction equipment to have to pay the considerable amount the tax money, affects the technology advancement, moreover privately operated enterprise loan extremely difficult . (2) Talented person serious insufficient, the scientific research development and the technical attack investment too urine Mold profession is the technology, the fund, the work crowded industry, along with the time progress and the technical development, grasps the talented person which and skilled utilizes the new technology exceptionally short, the high-quality mold fitter and the enterprise management talent extremely is also anxious. Because the mold enterprise benefit unsatisfactory and takes insufficiently the scientific research development and the technical attack, the scientific research unit and the universities, colleges and institutes eye stares at is creating income, causes the mold profession invests too few in the scientific research development and the technical attack aspect, causes the mold technological development step not to be big, progresses not quick . (3) The craft equipment level to be low, also necessary is not good, the use factor low recent years our country engine bed profession progressed quickly, has been able to provide the quite complete precision work equipment, but compared with the overseas equipment, still had a bigger disparity. Although the domestic many enterprises have introduced many overseas advanced equipment, but the overall equipment level low are very more than the overseas many enterprises. As a result of aspect the and so on system and fund reason, introduces the equipment not not necessary, the equipment and the appendix not necessary phenomenon are extremely common, the equipment utilization rate low question cannot obtain the comparatively properly solution for a long time . (4) Specialization, standardization, commercialized degree low, the cooperation ability Because receives large and complete small and entire the influence since long ago, mold specialization level low, the specialized labor division is not careful, the commercialized degree is low. At present domestic every year produces mold, commodity mold minister 40% About, other for from produce uses for oneself. Between the mold enterprise cooperates impeded, completes the comparatively large-scale mold complete task with difficulty. Mold standardization level low, mold standard letter use cave rare is low also to the mold quality, the cost has a more tremendous influence, specially has very tremendous influence . (5) To the mold manufacture cycle) the mold material and the mold correlation technology falls The mold material performance, the quality and the variety question often can affect the mold quality, the life and the cost, the domestically produced molding tool steel and overseas imports the steel products to compare has a bigger disparity. Plastic, plate, equipment energy balance, also direct influence mold level enhancement . 模具的发展 寿命等因素选择合理的凸、凹模间隙。并要考虑到模具在使用过程中的磨损使间隙增大,一般在设计模具时采用最小合理间隙。并在制造过程中保证模具零件的加工质量和精度,在装配过程中确保凸、凹模间隙均匀,这对于加工复杂形状零件十分关键。 (2)装配方法的选择要合理冲模装配方法大致包括直接装配法和配合装配法。装配前必须仔细研究模具装配图,充分考虑和分析冲模的结构特点、冲模零件加工工艺和加工精度等,以选择方便、准确、可靠的装配方法以保证冲裁件质量。 凸、凹模间隙的控制与调整的方法,凸、凹模的间隙控制,应根据冲模结构、间隙大小、冲裁件的质量和实际装配条件来选定。凸、凹模间隙的控制与调整方法有以下几种。 (1) 透光法:将凸、凹模合模后,用光照射底面,观察凸、凹模刃口周围透过的光线和分布情况来判断间隙的大小和均匀性。如果不均匀,重新调整至间隙均匀后再固定,此法适用于薄板小间隙冲裁模。 (2) 塞尺法:将凸、凹模合模后,用凸、凹模单边间隙厚度的塞尺塞入凸、凹模各方向间隙中。然后拧紧上模固定螺钉。最后放纸试冲,最后将上模座与固定板配钻、铰定位销孔,并打人销钉定位。 (3)垫片调整法 垫片调整间隙法简便、应用广泛。如图1所示,合模后垫好等高垫铁,将垫片包在凸模上使凸模进入凹模内,观察凸、凹模的间隙状况。如果间隙不均匀,用敲击凸模固定板的方法调整间隙,然后拧紧上模固定螺钉。最后放纸试冲,观察切纸上四周毛刺均匀程度,从而判断凸、凹模间隙是否均匀,再调整间隙直至冲裁毛刺均匀为止。最后将上模座与固定板配钻、铰定位销孔,并打入销钉定位。这种方法广泛适用于冲裁材料较厚的大间隙冲模和弯曲、拉深成形模具的间隙控制。 (4)化学法:当凸、凹模的形状复杂时,用上述几种方法调整间隙较困难时,这时可用化学方法来控制间隙,常用的是电镀法。电镀法是在凸模工作端表面镀上一层铜或锌来代替垫片。镀层厚度与单边隙相同,刃人凹模孔内,检查上下移动无阻滞现象即可装配紧固。镀层在冲模使用过程中会自然脱落,无需去除。此法镀层均匀,可提高装配间隙的均匀性。(5)工艺措施调整法 采用工艺措施调整模具间隙主要有2种方法: 1.尺寸法:加工凸模时,将凸模前端适当加长,加长段截面尺寸加工到与凹模型孔尺寸相同。装配时,使凸模进入凹模型孔,自然形成冲裁间隙,然后将凸模连同凸模固定板一起与上模座配作销钉固定,最后将凸模前端加长段去除即可形成均匀间隙。 2.定位孔法:工艺定位孔法就和级进模里面的原理差不多。加工时,在凸模固定板和凹模相同的位置上加工两定位孔,可将定位孔与模具型腔一次割出。装配时,在定位孔内插入定位销来保证间隙。 (6) 标准样板法:根据零件图预先在线切割机床上加工一标准样板或采用合格冲压零件,装配调整时将其放在凸、凹模之间,使上、下模相对运动时松紧程度适当即可。 (7) 测量法:测量法采用的测量工具有塞尺。塞尺测量法调整后的凸、凹模间隙均匀性好,是常用的方法。装配时,在凸模刃口放入凹模孔内后,根据凸、凹模间隙的大小选择不同规格的塞尺插入凸、凹模间隙中,检查凹模刃口周边各处间隙,并根据测量结果进行调整。调整时只要敲击凸模固定板直至调整好为止。 (8)调整修配法:冲模
- 温馨提示:
1: 本站所有资源如无特殊说明,都需要本地电脑安装OFFICE2007和PDF阅读器。图纸软件为CAD,CAXA,PROE,UG,SolidWorks等.压缩文件请下载最新的WinRAR软件解压。
2: 本站的文档不包含任何第三方提供的附件图纸等,如果需要附件,请联系上传者。文件的所有权益归上传用户所有。
3.本站RAR压缩包中若带图纸,网页内容里面会有图纸预览,若没有图纸预览就没有图纸。
4. 未经权益所有人同意不得将文件中的内容挪作商业或盈利用途。
5. 人人文库网仅提供信息存储空间,仅对用户上传内容的表现方式做保护处理,对用户上传分享的文档内容本身不做任何修改或编辑,并不能对任何下载内容负责。
6. 下载文件中如有侵权或不适当内容,请与我们联系,我们立即纠正。
7. 本站不保证下载资源的准确性、安全性和完整性, 同时也不承担用户因使用这些下载资源对自己和他人造成任何形式的伤害或损失。

人人文库网所有资源均是用户自行上传分享,仅供网友学习交流,未经上传用户书面授权,请勿作他用。