飞利浦放音机机壳注塑模设计【6张CAD图纸和说明书】
收藏
资源目录
压缩包内文档预览:(预览前20页/共50页)
编号:10106409
类型:共享资源
大小:319.01KB
格式:RAR
上传时间:2018-05-15
上传人:俊****计
认证信息
个人认证
束**(实名认证)
江苏
IP属地:江苏
30
积分
- 关 键 词:
-
飞利浦
放音机
机壳
注塑
设计
cad
图纸
以及
说明书
仿单
- 资源描述:
-
摘要
介绍了飞利浦放音机机壳的成型工艺及注射模结构。通过对塑料以及机身的研究,随着塑料制件在工业中应用日趋普遍,最终主要采用了(塑料)注射模的成型工艺,为了解决塑件三面侧孔的抽芯和复位,模具采用了斜导柱侧向抽芯结构与弹簧抽芯结构相结合的结构,可自动抽芯复位提高生产力。
关键词:注射模;斜滑块;抽芯。
目 录
引言 1
1概述 2
1.1塑料及塑料工业的发展 2
1.2模具在工业生产中的重要作用 2
1.3 塑料成型方法: 3
2 产品分析 4
3模具结构方案的确定 8
4 模具各部分的设计 10
4.1型腔数量及排列方式 10
4.2分型面的选择 10
4.3浇注系统与排溢系统的设计 12
4.3.1主流道的设计 12
4.3.2分流道的设计 13
4.3.3浇口的设计 14
4.3.4冷料穴的设计 15
4.3.5排溢系统的设计 15
4.4 成型零件的设计 15
4.4.1成型零件的结构设计 15
4.4.2成型零件工作尺寸的计算 17
4.5合模导向机构的设计 23
4.5.1导柱 23
4.5.2导套 24
4.5.3推出机构的设计 24
4.7侧向分型与抽芯机构的设计 25
4.7.1抽芯距的确定 26
4.7.2抽芯力的确定 26
4.7.3侧向抽芯机构的确定 27
4.7.4斜导柱的设计 27
4.7.5侧滑块设计 29
4.7.6导滑槽设计 29
4.7.7楔紧块设计 30
4.7.8滑块定位装置的设计 30
4.8 冷却系统的设计 31
5 选取模架和注射机及其工艺参数的校核 33
5.1选取模架 33
5.1.1应选择的关键参数 33
5.1.2模架选择步骤 33
5.2选取注射机 34
5.3 注射机有关工艺参数的校核 35
5.3.1锁模力的校核 35
5.3.2注射量校核 35
5.3.2模具厚度H校核 36
6 模具的工作原理 37
7 模具的加工工艺 38
8 总结 41
致 谢 43
参 考 文 献 44
飞利浦放音机机壳注塑模设计
引言
模具是生产中应用极为广泛的基础工艺装备。在电子电器、仪表通讯、交通运输、航空航天以及家电和轻工业等行业中,60%~80%的零件都要依靠模具成形。利用模具进行生产的产品所表现出来的精度高、一致性好、效率高、消耗低等一系列优点,是其他加工方法所不能比拟的。模具生产技术的高低,已成为衡量一个国家产品制造水平的重要标志。
目前,国内外模具工业发展很快,其产值已超过机床工业的产值。我国模具工业作为一个独立的、新型的工业,正处于飞速发展阶段,已成为国民经济的基础工业之一,其发展前景十分广阔。据预测,未来我国将成为世界的制造中心,这更加给模具工业带来前所未有的发展机遇和空间。
用塑料注射成型方法加工的塑料制品,具有生产效率高,能成型外形复杂、尺寸精确或带嵌件的注塑制品;对各种塑料的加工适应性强等优点,因此广泛地应用于国防工业、航空、交通、电气、机械、建筑、农业、文教、卫生、日用品等各个领域,一直是塑料加工领域中的重要方法。
塑料注射成型是塑料制品的高效率生产方法之一。注射成型获得的塑料制品在各种塑料制品中所占的比重很大。注射模具是实现注射成型加工的重要工艺装备,其结构的合理性,将直接影响塑性的成型质量、生产效率、劳动强度、模具寿命及成本等。而模具决定最终产品的性能、形状、尺寸和精度,为了周而复始地获得符合技术经济要求及质量稳定的产品,模具的结构特征,成型工艺及浇注系统的流动条件是影响塑料制件的质量及生产率的关键因素。因此,在了解并掌握塑料的成型工艺特性、塑料制件的结构工艺性及注射机性能等成型技术的基础上,设计出先进合理的注射模具,是一名合格的模具设计技术人员所必需达到的要求。




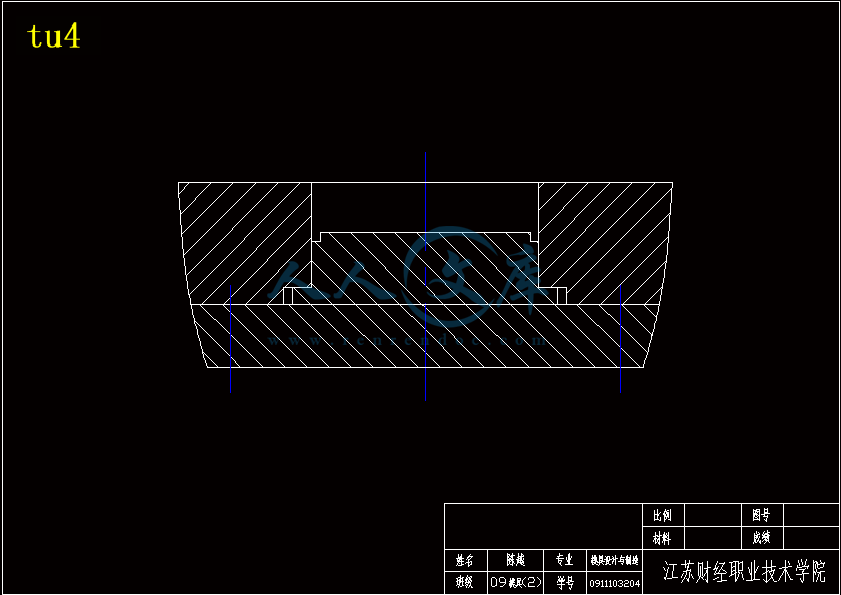


- 内容简介:
-
综合毕业实践说明书(论文)标题飞利浦牌放音机机壳模具设计系别机械与电子工程系专业学号姓名指导教师I2012年6月20日摘要介绍了飞利浦放音机机壳的成型工艺及注射模结构。通过对塑料以及机身的研究,随着塑料制件在工业中应用日趋普遍,最终主要采用了(塑料)注射模的成型工艺,为了解决塑件三面侧孔的抽芯和复位,模具采用了斜导柱侧向抽芯结构与弹簧抽芯结构相结合的结构,可自动抽芯复位提高生产力。关键词注射模;斜滑块;抽芯。I目录引言11概述211塑料及塑料工业的发展212模具在工业生产中的重要作用213塑料成型方法32产品分析43模具结构方案的确定84模具各部分的设计1041型腔数量及排列方式1042分型面的选择1043浇注系统与排溢系统的设计12431主流道的设计12432分流道的设计13433浇口的设计14434冷料穴的设计15435排溢系统的设计1544成型零件的设计15441成型零件的结构设计15442成型零件工作尺寸的计算1745合模导向机构的设计23451导柱23452导套24453推出机构的设计2447侧向分型与抽芯机构的设计25471抽芯距的确定26472抽芯力的确定26473侧向抽芯机构的确定27474斜导柱的设计27475侧滑块设计29II476导滑槽设计29477楔紧块设计30478滑块定位装置的设计3048冷却系统的设计315选取模架和注射机及其工艺参数的校核3351选取模架33511应选择的关键参数33512模架选择步骤3352选取注射机3453注射机有关工艺参数的校核35531锁模力的校核35532注射量校核35532模具厚度H校核366模具的工作原理377模具的加工工艺388总结41致谢43参考文献440飞利浦放音机机壳注塑模设计引言模具是生产中应用极为广泛的基础工艺装备。在电子电器、仪表通讯、交通运输、航空航天以及家电和轻工业等行业中,6080的零件都要依靠模具成形。利用模具进行生产的产品所表现出来的精度高、一致性好、效率高、消耗低等一系列优点,是其他加工方法所不能比拟的。模具生产技术的高低,已成为衡量一个国家产品制造水平的重要标志。目前,国内外模具工业发展很快,其产值已超过机床工业的产值。我国模具工业作为一个独立的、新型的工业,正处于飞速发展阶段,已成为国民经济的基础工业之一,其发展前景十分广阔。据预测,未来我国将成为世界的制造中心,这更加给模具工业带来前所未有的发展机遇和空间。用塑料注射成型方法加工的塑料制品,具有生产效率高,能成型外形复杂、尺寸精确或带嵌件的注塑制品;对各种塑料的加工适应性强等优点,因此广泛地应用于国防工业、航空、交通、电气、机械、建筑、农业、文教、卫生、日用品等各个领域,一直是塑料加工领域中的重要方法。塑料注射成型是塑料制品的高效率生产方法之一。注射成型获得的塑料制品在各种塑料制品中所占的比重很大。注射模具是实现注射成型加工的重要工艺装备,其结构的合理性,将直接影响塑性的成型质量、生产效率、劳动强度、模具寿命及成本等。而模具决定最终产品的性能、形状、尺寸和精度,为了周而复始地获得符合技术经济要求及质量稳定的产品,模具的结构特征,成型工艺及浇注系统的流动条件是影响塑料制件的质量及生产率的关键因素。因此,在了解并掌握塑料的成型工艺特性、塑料制件的结构工艺性及注射机性能等成型技术的基础上,设计出先进合理的注射模具,是一名合格的模具设计技术人员所必需达到的要求。11概述11塑料及塑料工业的发展塑料是以树脂为主要成分的高分子有机化合物,简称高聚物。塑料其余成分包括增塑剂、稳定剂、增强剂、固化剂、填料及其它配合剂。塑料制件在工业中应用日趋普遍,这是由于它的一系列特殊的优点决定的。塑料密度小、质量轻。塑料比强度高;绝缘性能好,介电损耗低,是电子工业不可缺少的原材料;塑料的化学稳定性高,对酸、碱和许多化学药品都有很好的耐腐蚀能力;塑料还有很好的减摩、耐磨及减震、隔音性能也较好。因此,塑料跻身于金属、纤维材料和硅酸盐三大传统材料之列,在国民经济中,塑料制件已成为各行各业不可缺少的重要材料之一。塑料工业的发展阶段大致分为一下及个阶段初创阶段30年代以前,科学家研制分醛、硝酸纤维和聚酰胺等热塑料,他们的工业化特征是采用间歇法、小批量生产。发展阶段30年代,低密度聚乙烯、聚氯乙烯等塑料的工业化生产,奠定了塑料工业的基础,为其进一步发展开辟了道路。飞跃阶段50年代中期到60年代末,塑料的产量和数量不断增加,成型技术更趋于完善。稳定增长阶段70年代以来,通过共聚、交联、共混、复合、增强、填充和发泡等方法来改进塑料性能,提高产品质量,扩大应用领域,生产技术更趋合理。塑料工业向着自动化、连续化、产品系列化,以及不拓宽功能性和塑料的新领域发展。我国塑料工业发展较晚。50年代末,由于万吨级聚氯乙稀装置的投产和70年代中期引进石油化工装置的建成投产,使塑料工业有了两次的跃进,于此同时,塑料成型加工机械和工艺方法也得到了迅速的发展,各种加工工艺都已经齐全。塑料由于其不断的被开发和应用,加之成型工艺的不断发展成熟于完善,极大地促进了成型模具的开发于制造。随者工工业塑料制件和日用塑料制件的品种和需求的日益增加,而且产品的更新换代周期也越来越短,对塑料和产量和质量提出了越来越高的要求。12模具在工业生产中的重要作用模具是工业生产中重要的工艺装备,模具工业是国民经济各部门发展的重要基2础之一。塑料模是指用于成型塑料制件的模具,它是型腔模的一种类型。模具设计水平的高低、加工设备的好坏、制造力量的强弱、模具质量的好坏,直接影响着许多新产品的开发和老产品的更新换代,影响着产品质量和经济效益的提高。美国工业界认为“模具工业是美国工业的基础”,日本则称“模具是促进社会繁荣富裕的劳动力”。近年来,我国各行业对模具的发展都非常重视。1989年,国务院颁布了“当前产业政策要点的决定”,在重点支持改造的产业、产品中,把模具制造列为机械技术改造序列的第一位,它确定了模具工业在国民经济中的重要地位,也提出了振兴模具工业的主要任务。塑料成型技术的发展趋势一副好的塑料模具与模具的设计、模具材料及模具制造有很大的关系。塑料成型技术发展趋势可以简单地归纳为以下几个方面。模具的标准化为了适应大规模成批生产塑料成型模具和缩短模具制造周期的需要,模具的标准化工作十分重要,目前我国标准化程度只达到20。注射模具零部件、模具技术条件和标准模架等有以下14个标准当前的任务是重点研究开发热流道标准元件和模具温控标准装置;精密标准模架、精密导向件系列;标准模板及模具标准件的先进技术和等向标准化模块等。加强理论研究塑料制件的精密化、微型化和超大型化新材料、新技术、新工艺的研制、开发和应用各种新材料的研制和应用,模具加工技术的革新,CAD/CAM/CAE技术的应用都是模具设计制造的发展趋势。13塑料成型方法塑料的成型方法有注射模、压缩模、压注模、机头与口模。此外还有中空吹塑模、真空成型模、浇注模等。注射模又称注塑模,主要用于热塑性塑料制品的注射成型,也可用于热固性塑料制品的注射成型。注射模一般结构复杂、造价高。压缩模又称压塑模或压模,主要用于热固性塑料制品的压制成型,有时也用于某些流动性较差的热塑性塑料制品的压缩成型。压注模又称传递模或挤塑模,主要用于热固性塑料制品的成型。压注模比压缩模多了加料腔、柱塞和浇注系统,结构上比压缩模复杂,造价高。3机头模与口模安装与挤出机上的模具,主要用于热塑性塑料制品的挤出成型。42产品分析该产品为耳机机身部分用于机芯的安装与固定。其外观要求较高,精度要求一般,装配精度要求较高。外表面粗糙度值较低,内表面粗糙度值较高。壁厚均匀,有侧向凹凸结构,属于矩形类零件,结构较为复杂。可以用注射模具一次成型。塑料的种类和性能塑料的种类繁多,大约有300多种,常用的塑料也有几十种,而且每一品种又有多种牌号。(1)按塑料的使用特性分为通用塑料、工程塑料和功能塑料。1)通用塑料通用塑料是指一般只能作为非结构材料使用,且产量大、用途广、价格低、性能普通的一类塑料;主要有聚乙烯、聚丙烯、聚氯乙烯、酚醛塑料和氨基塑料五大品种,约占塑料总产量的75以上。2)工程塑料工程塑料是指可以作为工程结构材料,且力学性能优良,能在教广温度范围内承受机械应力和在较为苛刻的化学及物理环境中使用的一类塑料。主要有聚酰胺(尼龙)、聚碳酸酯、聚甲醛、ABS、聚苯醚、聚砜、聚脂、及各种增强塑料。工程塑料与通用塑料相比产量少,价格较高,但具有优异的力学性能、电性能、化学性能、耐磨性、耐热性、耐腐蚀性、自润滑以及尺寸稳定性,即其具有某些金属性能,因而可代替一些金属材料用于制造结构零部件和传动结构零部件等。3)功能塑料功能塑料是指用于特种环境中,具有某一方面的特殊性能的塑料。主要有医用塑料、光敏塑料、导磁塑料、高耐热性塑料及高频绝缘性塑料等。这类塑料产量小,价格较贵,性能优异。(2)按塑料受热后呈现的基本特性分热塑性塑料和热固性塑料。1)热塑性塑料热塑性塑料是指在一定的温度范围内,能反复加热软化乃至熔融流动,冷却后能硬化成一定形状的塑料。这类塑料基本上是以聚合反应得到的线形或支链型树脂为基础得到的,在成型过程中只有物理变化,而无化学变化,因而受热后可多次成型,废料可回收再利用。如聚乙烯、聚氯乙烯、聚丙烯、聚苯乙烯、聚碳酸酯、ABS、聚甲醛、尼龙及有机玻璃等。2)热固性塑料热固性塑料是指加热温度达到一定程度后能成为不熔或不熔性物质,使形状固化下来不再变化的塑料。这类塑料基本上是以缩聚反应得到的,在成型受热时发生化学变化使线型分子结构转变为体型结构,废料不能再回收利用。如酚醛塑料、氨基塑料、环氧塑料、不饱和聚脂塑料、三聚氰胺塑料等。结晶和取5向只存在于具有线性结构的热塑性塑料中,不存在网状或体型结构的热固性塑料中。塑料的使用性能包括物理性能、化学性能、力学性能、热性能、电性能等。塑料的物理性能主要有密度、透湿性、透气性、吸水性、透明性等。塑料的化学性能主要包括耐化学性、耐候性、耐老化性、光稳定性、抗霉性等。塑料的力学性能主要包括抗拉强度、抗压强度、抗弯强度、断裂伸长率、抗冲击强度、耐蠕变性、摩擦系数、硬度及磨耗等。塑料的热性能主要包括线膨胀系数、导热系数、玻璃化温度、耐热性、热变形温度、熔体指数、热稳定性、热分解温度、耐燃性等。塑料的电性能主要包括表面电阻率、介电常数、介电强度、耐电弧性、介电损耗等,用这些指标衡量塑料在电作用下表现出来的性能。由上述分析,选产品的材料为ABS。ABS具有综合的优良性能(坚固、坚韧、坚硬),价格便宜,原料易得,因此发展很快,是目前产量最大、应用最广的一种工程塑料。ABS是微黄色或白色不透明粒料,无毒、无味。ABS的特性及用途ABS由于是三种组分组成的,故它有三种组分的综合性能,而每一组分又在其中起着固有的作用。丙烯腈可使ABS具有较高的强度、硬度、耐热性及耐化学腐蚀性;丁二烯可使ABS具有弹性和较高的冲击强度;苯乙烯则可使ABS具有优良的介电性能。因此,在机械性能方面,ABS具有质硬、坚韧、刚性等特性。ABS树脂的缺点是耐热性不高,耐低温性不好,而且不耐燃、不透明,耐候性不好,特别是耐紫外线性能不好。由于ABS具有上述综合性能,因而广泛用来制造电视机、收录机的外壳、旋钮、电话机壳、话筒、把手、铰链、塑料铭牌等。4ABS的成型特性(1)ABS粒料表面极易吸湿,使成型塑件表面出现斑痕、云纹等缺陷。为此成型前必须进行干燥处理。(2)ABS的比热容比聚烯泾低,在注射机料筒中能很快加热,因而塑化效率高,6在模具中凝固也比聚烯泾快,故模塑周期短。(3)ABS树脂的表现黏度强烈地依赖于剪切速率,因此模具设计中大都采用点浇口形式。(4)ABS树脂为非结晶形高聚物,所以成型收缩率小。(5)ABS树脂的熔融温度较低,熔融温度范围宽,流动性好,有利于成型。5)查参考文献1,表31得ABS的注射工艺参数如下表表21注射工艺参数注射机类型螺杆式螺杆转速(R/MIN)3060喷嘴形式直通式喷嘴温度(C)180190料筒温度(C)前200210中210230后180200模具温度(C)5070注射压力MPA7090保压力(MPA)5070注射时间(S)35保压时间(S)1530冷却时间(S)1530成型周期(S)4070查参考文献1表39得ABS的精度等级为表22ABS的精度等级塑料品种高精度一般精度低精度ABS345根据塑件的结构特性和作用,选取一般精度等级4级已能满足要求。查参考文献1附录B常用塑料的收缩率得ABS的为7表23ABS的收缩率塑料种类收缩率()ABS0308查参考文献1表311塑件脱模斜度得表24ABS的塑件脱模斜度脱模斜度塑料名称型腔型芯ABS351303040根据上表选ABS的脱模斜度为型腔选1,型芯选30。83模具结构方案的确定注射模的结构有多种,它的分类单分型面注射模单分型面注射模又称为两板式注射模。它是注射模中最简单的一种结构形式,其型腔由动模和定模构成。单分型面注射模的型腔一部分设在动模上,一部分设在定模上。其主流道设在定模一侧,分流道设在分型面上,开模后塑料制品连同流道凝料一起留在动模上。动模一侧设有推出机构,用以推出制品及流道凝料。多分型面注射模多分型面注射模是指具有两个以上分型面的注射模具。适用于制品的外表面、内侧壁不允许有浇口痕迹的场所。这种浇口采用点浇口,且制品由定距分型机构实现顺序分型,然后由推出机构推出。这种注射模结构较复杂,质量大,成本高,主要用于点浇口的单型腔或多型腔注射模,较少用于大型制品或流动性差的塑料成型。带有活动镶块的注射模由于塑料制品的结构特殊要求,如带有内侧凸、凹槽或螺纹孔等塑料制品,需要在模具上设置活动的型芯或对拼组合型腔等镶块。侧向分型抽芯的注射模当制品带有侧孔或侧凹时,在机动分型抽芯的模具里设有斜导柱或斜滑块等侧向分型抽型机构。带有嵌件的注射模当制品上带有嵌件时,为了保证嵌件在注射成型过程中不发生位移,避免合模时损伤模具,所以在设计这类模具时,应认真考虑嵌件的可靠、准确定位问题。在推出制品之前应先用手工抽出侧面型芯。该模具在嵌件处设推出机构,这样,在制品上不留下任何影响外观的顶出痕迹。自动卸螺纹的注射模对带有内外螺纹的制品,当采用自动卸螺纹时,在模具结构设计时,应设置可转动的螺纹型芯和螺纹型环,利用注射机的往复运动或旋转运动,或设置专门的原动机件(如电机、液压马达等)和传动装置与模具连接,开模后带动螺纹型芯或螺纹型环转动,使制品脱出。定模设置推出机构的注射模由于推出机构宜设在动模一侧,所以注射模开模后,制品应留在定模上(或有可能留在定模上),则应在定模一侧设置推出机构。开模时,由动模通过拉板或链条带动推出机构将制品推出。带定距分型拉紧机构的注射模带定距分型拉紧机构的注射模又称顺序开模机构的注射模。在注射成型中,模具有几个分型面,开模时需按一定顺序开模,在模具中需设置定距分型拉紧机构。9热流道注射模热流道注射模在每次注射成型后,只需取出制品而流道的料不取出,让流道里的料始终处于一种熔融状态,实现了无废料加工,大大节约了塑料用量,并且有利于成型压力的传递,保证产品质量,缩短成型周期,提高了劳动生产率,同时容易实现自动化操作。目前在聚烯泾类塑料制品生产中,国内较多单位采用热道模。但这种模具结构较复杂,造价高,模温控制要求严格,仅适用于大批量生产的场合。当制品侧壁上带有的与开模方向不同的内外侧孔或侧凹等阻碍制品成型后直接脱模时,必须将成型侧孔或侧凹零件作活动的,这种零件称为侧型芯(俗称活动型芯)。在制品脱模前必须先抽出侧型芯,然后再从模具中推出制品,完成侧型芯的抽出和复位的机构叫做侧向分型抽芯机构。因制件存在内凹外凸,而不能强制脱模,固应采用侧向分型与抽芯结构的模具。104模具各部分的设计41型腔数量及排列方式模具的型腔数可根据塑料制品的产量、精度高低、模具制造成本以及所选用注射机的最大注射量和锁模力大小等因素确定。小批量生产,采用单型腔模具;大批量生产,宜采用多型腔模具。但塑料制品尺寸较大时,型腔数将受所选用注射机最大注射量限制。由于多型腔模具的各个型腔的成型条件以及熔体到达各型腔的流程难以取得一致,所以制品精度较高时,一般采用单型腔模具。考虑到塑料制件的生产批量不大,交货期长,成型品种的工艺特性,塑件的形状及尺寸,塑料制件的成本等因素,初步确定采用单型腔模具结构。单型腔模具有以下优点(1)、塑料制件的形状和尺寸始终一致。(2)、工艺参数易于控制。(3)、模具的结构简单、紧凑,设计自由度大。(4)、制造成本低,制造周期短。42分型面的选择一副模具根据需要可能有一个或两个以上分型面。分型面可能是垂直于合模方向或倾斜于合模方向,也可能是平行于合模方向。分型面的形状有平面、斜面、阶梯面和曲面。分型面应尽量选择平面的,但为了适应塑料制品成型的需要和便于塑料制品脱模,也可以采用后三种分型面。后三种分型面虽然加工较困难,但型腔加工却比较容易。分型面选择的一般原则(1)应便于塑料制品的脱模为了便于塑料制品脱模,在考虑型腔总体结构时,必须注意到塑料制品在型腔中的方位,尽量只采用一个与开模方向垂直的分型面,设法避免侧向分型和侧向抽芯,以免模具结构复杂化。为了便于塑料制品脱模,在一般情况下应使塑料制品在开模时尽可能留在下模或动模部分,这是因为推出机构通常都设在下模或动模部分。对于自动化生产所用模具,正确处理塑料制品在开模时的留模问题更显得重要。如何使塑料制品留在下模或动模中,必须具体分析塑料制品与下模和上模,或动模和定模的摩擦力关系,做到摩擦力大的朝向下模或动模的一方,但不宜过大,否则又会造成脱模困难。(2)分型面的选择应有利于侧向分型与抽芯如果塑料制品有侧孔或侧凹时,11应尽可能地将侧芯设在动模部分,以便于抽芯;如侧芯设在定模部分,则抽芯比较困难。此外,除液压抽芯机构能够获得较大的抽拔距外,一般的侧向分型抽芯机构的抽拔距较小,所以在选择分型面时,应将抽芯或分型距离较大的放在开模的方向上,而将抽芯距离较小的放在侧向,因为侧向滑块合模时锁紧力较小,而对于大型塑料制品又需要侧向分型时,则应将投影面积大的分型面设在垂直于合模方向上,而将投影面积小的分型面作为侧向分型,则可能由于侧滑块锁不紧而产生溢料,侧滑块锁紧机构必须做得很大。(3)分型面的选择应保证塑料制品的质量为了保证塑料的质量,对有同轴度要求的塑料制品,应将有同轴度要求的部分设在同一模板内。分型面的选择应尽可能选在不影响塑料制品外观和产生飞边容易修整的部位。(4)分型面的选择应有利于防止溢料造成溢料多,飞边过大的原因就是分型免选择不当。当塑料制品在垂直于合模方向的分型面上的投影面积接近于注射机的最大注射面积时,就会产生溢料。(5)分型面的选择应有利于排气。(6)分型面的选择应尽量使成型零件便于加工。(7)选择分型面时,应考虑减少由于脱模斜度造成塑料制品的大小端尺寸差异。较高的且脱模斜度要求小的塑料制品,只要其外观无严格要求,可将分型面选在中间,为了顺利脱模,则脱模斜度应较大,从而使塑料制品大小端尺寸差异较大。综上所述,可选取平直分型面如下图41。图411243浇注系统与排溢系统的设计浇注系统的作用将熔体平稳地引入型腔,使之按要求填充型腔的每一个角落;使型腔内的气体顺利地排除;在熔体填充型腔和凝固过程中,能充分地把压力传到型腔各部位,以获得组织致密,外形清晰、尺寸稳定的塑料制品。浇注系统分为普通浇注系统和热流道浇注系统两类。浇注系统设计是注射模设计的一个重要环节,它直接影响注射成型的效率和质量。浇注系统设计的基本原则分析塑件的成型性能,分析浇注系统对塑料熔体流动的影响以及在充填、保压补缩和倒流的各阶段中,型腔内塑料的温度、压力的变化情况,使设计出的浇注系统适应所用塑料的成型性能,保证制品的质量。有利于型腔中气体的排出。避免塑料熔体直接冲击型芯或嵌件,以防其变形或移位。尽量缩短流程和减少拐弯,减少熔体压力和热量的损失,保证充填压力和速度,减少塑料的用量,提高熔接强度。防止塑料制品的变形,设计时应注意由于冷却收缩的不均匀或多浇口进料、浇口收缩等原因引起制品的变形。浇注系统在分型面上的投影面积应尽量小。浇注系统的位置应尽量与模具的中心对称。浇口的去除、修整应方便,保证制品外观质量。选用普通流道浇注系统,其一般由主流道、分流道、浇口和冷料穴等四部分组成。431主流道的设计表41主流道的尺寸符号名称尺寸(MM)D主流道小端直径注射机喷嘴径051SR主流道球面半径喷嘴球面半径12H球面配合高度3513主流道锥角主流道长度尽量60D主流道大端直径D2LTG/2432分流道的设计分流道是指主流道末端与浇口之间这一段塑料熔体的流动通道。(1)、分流道的形状及尺寸为了便于机械加工及凝料脱模,分流道大多设置在分型面上。常用的分流道截面形状一般可分为圆形、梯形、U形、半圆形及矩形等。分流道截面形状应尽量使其比表面积(流道表面积与体积之比)最小,以减少热量和压力损失。由此可得,圆形截面分流道的比表面积最小,但需开设在分型面两侧,且对应两部分须吻合,加工不便;梯形及U形截面分流道加工较容易,且热量损失和流动均不大,为最常用形式;半圆形和矩形截面的分流道则因比表面积较大不常采用。考虑塑料制件的结构,所用塑料的工艺特性、成型工艺条件及分流道的长度等因素,采用半圆形截面的分流道。查参考文献1表53可得分流道的直径推荐值为4795。因ABS的流动性为中等,故分流道的直径一般取中间值。但考虑到截面过大,不仅积存空气增多,塑件容易产生气泡,而且增大塑料耗量延长冷却时间。但若截面过小,会降低单位时间内输送的塑料熔体流量,使填充时间延长,导致塑件常出现缺料,波纹等缺陷。经综合考虑,取分流道的直径为5MM。(2)、分流道的长度分流道要尽可能地短,且少折弯,便于注射成型过程中最经济地使用原料和注射机的能耗,减少压力的损失和热量损失。结合模具结构考虑。分流道长度LF通常为主流道大端直径的125倍,一般取830MM。(3)、分流道的表面粗糙度由于分流道中与模具接触的外层塑料迅速冷却,只有中心部分的塑料熔体的流动状态较为理想,因而分流道的内表面粗糙度RA不要求很高,一般取RA16M即可。这样表面稍不光滑,有助于塑料熔体的外层冷却皮层固定,从而与中心部位的14熔体之间产生一定的速度差,以保证熔体流动时具有适宜的剪切率和剪切热。433浇口的设计浇口是连接分流道与型腔的通道。大多数情况下(除直接浇口外)浇口是整个浇注系统中截面积最小的部分。通常,浇口截面积约为分流道截面积的003009倍,表面粗糙度RA04M。浇口设计时常取较小的截面尺寸,然后通过试模修改增大。浇口的基本作用是加速从分流道来的熔体,以便快速充满型腔。当熔体通过狭小的浇口时,剪切速率高,摩擦生热使熔体温度升高,结果使熔体黏度降低,流动性变好,有利于填充型腔,获得外形清晰的制品。由于浇口小,所以总是首先凝固,能防止熔体倒流,便于流道凝料与制品分离。浇口的类型直接浇口、中心浇口、侧浇口、点浇口、潜伏式浇口和护耳浇口。直接浇口虽然具有流动阻力小、料流速度快及补缩时间长的特点,但注射压力直接作用在塑件上,容易在进料处产生较在的残余应力而导致塑件翘曲变形,浇口痕迹也较明显,影响塑件的外观,故不可用直接浇口。中心浇口是直接浇口的变异形式,熔体直接从中心流向型腔。它具有与直接浇口相同的优点,但去除浇口较直接浇口方便。当制品内部有通孔时,可利用该孔设分流锥,将浇口设置于制品的顶端。这类浇口一般用于单型腔注射模,适用于圆筒形、原环形或中心带孔的制品成型。可见它也不可用。用点浇口,虽然成型塑件,去除浇口后残余痕迹小,易取得浇注系统的平衡,也利于自动化操作,但压力损失过大,收缩大,塑件易变形,同时在定模部分需另加一个分型面,以便烧口凝料脱模。因此用点浇口也不是很理想。因潜伏式浇口也是由点浇口演变而来,而护耳浇口专用于透明度高和一切无应力的制品。它们也不太合适。用侧浇口,侧浇口的截面形状多为矩形狭缝(也有半圆形的注入口),调整其截面的厚度和宽度可以调节熔体充模时的剪切速率及浇口封闭时间。侧浇口加工容易,修整方便,并可根据塑件的形状特征灵活地选择进料位置,对各种塑料的成型适应性均较强;但是有浇口痕迹存在,会形成熔接痕、缩孔、气孔等塑件缺陷。根据塑件的结构,模具的结构,对上述浇口的相互比较,综合考虑,选择搭接式侧浇口。如下图41。15图41434冷料穴的设计冷料穴是用来接收冷料,防止冷料进入烧注系统的流道和型腔,同时还是在开模时将主流道和分流道的冷凝料勾住,使其保留在动模一侧,便于脱模的功能。常见冷料穴拉料结构的类型带钩形头(Z字形头)拉料杆和底部带推杆的冷料穴、带球头形(或菌形头)拉料杆的冷料穴、无拉料杆的冷料穴。冷料穴设计在主流道对面的动模板上,其标称直径与主流道大端直径相同或稍大一些,深度约为直径的115倍,最终要保证冷料的体积小于冷料穴的体积。选用端部为Z字形拉料杆形式的冷料穴。435排溢系统的设计注射模成型时的排气有如下四种方式用分型面排气;利用配合排气通常中小型模具的简单型腔,可利用推杆、活动型芯以及双支点的固定型芯端部与模板的配合间隙进行排气;在分型面上开设排气槽排气;强制性排气在气体滞留区设置排气杆或利用真气泵抽气,这种方法很有效,只是会在塑件上留有杆件的痕迹,因此排气杆设置在塑件内侧。分析塑件的结构,模具的结构,可利用推杆、活动型芯以及双支点的固定型芯端部与模板的配合间隙进行排气,其间隙为003005MM。44成型零件的设计441成型零件的结构设计1凹模16凹模是成型塑件外表面的主要零件,按结构不同,可分为整体式和组合式。方案一整体式凹模的特点是由整块材料加工而成,牢固,使用中不易发生变形,不会使塑件产生拼接线痕迹。但由于加工困难,热处理不方便,所以整体式凹模只用在形状简单的中、小型模具上。方案二嵌入式组合凹模,这种凹模改善了加工工艺性能,减少了热处理变形,节约了模具贵重钢材,但结构复杂,装配比较麻烦,塑件表面可能留有镶拼痕迹,组合后的型腔牢固性较差。这种凹模形状及尺寸的一致性好,更换方便,加工效率高,可节约贵重金属,但模具体积较大,需用特殊加工方法。方案三底部镶拼式凹模,为了便于机械加工、研磨抛光和热处理,整个凹模可由几个部分镶拼而成,镶拼式结构简单,但结合面要求平整,以防挤入塑料,飞边加厚,造成脱模困难,同时还要求底板应有足够的强度和刚度,以免变形而挤入塑料,采用圆柱形配合面,塑料不易挤入,但造价比较费时。形状复杂的型腔底部设计成镶拼式。综上所述,采用底部镶拼式凹模,简化了复杂凹模的加工工艺,减少了热处理变形,拼合处有间隙利于排气,便于模具维修,节省了贵重的模具钢。因此采用方案三,把凹模做成底部镶拼式凹模。如下图42。图422凸模和型芯凸模是指在压缩模中承受或传递压机压力,与型腔有配合段,直接接触塑料,成型塑料制品内表面或上、下端面的零件。型芯是指注射模中成型塑料制品有较大内表面的凸状零件,它又称主型芯。凸模或主型芯也可分为整体式和组合式两大类。17方案一采用整体式主型芯,结构牢固,成型的塑料制品质量较好,但不便加工,消耗的模具钢多,主要用于工艺试验模或小型模具上的形状简单的型芯。方案二对于形状复杂的大型凸模,为了机械加工,可采用组合式的结构,如采用整体式结构,必然造成加工困难。而采用将型芯单独加工,再镶入模板中。采用通孔凸肩式,凸模用台肩和模板连接,再用垫板螺钉紧固,连接牢固。通过比较,分析塑件结构,选用方案二的凸模结构。如下图43。图43小型芯也单独制造,再嵌入模板中。也都采用凸肩固定。多个互相靠近的不型芯,用凸肩固定时,如果凸肩发生重迭干涉,可将凸肩相碰的一面磨去,将型芯固定板的台阶孔加工成大圆台阶孔或长腰圆形台阶孔,然后再将型芯镶入。或采用单边凸肩固定。442成型零件工作尺寸的计算1、型腔和型芯工作尺寸的计算以下计算公式都是由参考文献1第五章第三节查得。1、型腔和型芯的径向尺寸型腔径向尺寸1SLSX0ZLZ0L为模具型腔的基本尺寸Z为模具成型零件的制造公差S为塑料的平均收缩率SSMAXSMIN/20308/205518LS为塑件的基本尺寸,其公差为负偏差X为修正系数修正系数X在塑件的尺寸较大,精度级别较低时,取X05;当塑料制件尺寸较小,精度级别较高时,取X075;为塑件公差查参考文献1表38得基本尺寸LS1145MM的公差050MMLS885MM的公差044MM。而模具成型零件的制造公差一般取塑件公差的1/31/4或取IT7IT8级作为模具制造公差,这里取塑件公差的1/3作为模具的制造公差。Z11/300500167MMZ21/30440147MM这里X都取05则L1145105511450505001671148800167MML885105588505044001478877MM型芯径向尺寸L0Z1SLSX0Z式中L为型芯的基本尺寸LS为塑件孔的径向基本尺寸其它符号的意义同前。查参考文献1表38得基本尺寸LS1101MMR的公差050MM;LS682MM的公差038MMLS138MMR的公差020MM;LS713MM的公差038MM;LS1115MM的公差050MM;Z取塑件公差的1/3则Z11/30500167MMZ21/30380127MMZ31/30200067MM19Z41/30380127MMZ51/30500167MM尺寸1101MM、1115MM、682MM、713MM的修正系数X取05;尺寸138MM的修正系数X取075。则L11051055110105050001671109600167MML68210556820503800127687700167MML138105513807502000067140300067MML71310557130503800127718800127MML11151055111505050001671123600167MM2、型腔深度尺寸和型芯高度尺寸型腔深度尺寸H0Z1SHSX0Z式中H为模具型腔的深度尺寸HS为塑件高度基本尺寸其它符号意义同前。查参考文献1表38得基本尺寸HS202MM的公差024MMHS83MM的公差016MMHS115MM的公差018MMZ取塑件公差的1/3。则Z11/30240080MMZ11/30160053MMZ11/30180060MM修正系数取X05。20则H20210552020502400080201900080MMH83105583050160005382700053MMH11510551150501800060114700060MM型芯高度尺寸H0Z1SHSX0Z式中H为模具型芯高度尺寸HS为塑件深度基本尺寸其它符号意义同前。查参考文献1表38得基本尺寸HS183MM的公差022MMHS68MM的公差016MMZ取塑件公差的1/3。则Z11/30220073MMZ21/30160053MM修正系数X取X05则H18310551830502200073185100073MMH68105568050160005369200053MM3、中心距尺寸的计算C1SCSZ/2式中C为模具上成型零件中心距的基本尺寸CS为塑件中心距的基本尺寸其它符号意义同前。查参考文献1表38得基本尺寸CS425MM的公差028MM;CS753MM的公差038MM;CS103MM的公差050MM;CS78MM的公差21038MM;CS108MM050MM的公差;CS6MM的公差014MM;CS18MM的公差020MM;CS32MM的公差026MMCS58MM的公差032MM;CS60MM的公差032MM;模具的制造误差Z取塑件公差的1/4;则Z11/40280070MMZ21/40380095MMZ31/40500167MMZ41/40380095MMZ51/40500167MMZ61/40140035MMZ71/40200050MMZ81/40260065MMZ91/40320080MMZ101/40320080MMC42510554250070/242730035MMC75310557530095/2757100475MM取C73575710048MMC10310551030125/21035700625MM取C103103570063MMC781055780095/2784300475MM取C7878430048MMC10810551080125/21085900625MM取C108108590063MMC6105560035/260300175MM取C66030018MMC181055180050/218100025MMC321055320065/2321800325MM取C3232180033MM22C581055580080/258320040MMC601055600080/260330040MM4、模具型腔侧壁和底板厚度的计算与确定型腔侧壁厚计算确定型腔的壁厚尺寸,一般根据经验予以确定。但对于一些主要成型零件应按其受力情况作必要的计算,以使型腔在成型压力下不至于变形。理论分析和生产实践表明,大尺寸的模具型腔,刚度不足是主要矛盾,型腔壁厚应以满足刚度条件为准;而对于小尺寸的模具型腔,在发生大的弹性变形前,其内应力往往超过了模具材料的许用应力,因此强度不足是主要矛盾,设计型腔壁厚应以强度条件为准。因该模具型腔为小尺寸的型腔,其长边尺寸L11488MM,短边尺寸为B8877MM,故在此按强度条件计算。查参考文献1,得按强度条件型腔侧壁的计算式为SPH1L2/2H1/2式中S为型腔侧壁厚度MMP为型腔内熔体的压力(MPA),一般为2545MPA;为承受熔体压力的侧壁高度(MM)L为型腔侧壁长边长(MM)H为型腔侧壁总高度MM;为模具材料的许用应力MPA;取P35MPA、2019MM、30MM、S352019114882/2/30/1601/23117MM考虑模具结构和导柱孔的位置,参考文献1表517矩形型腔壁厚尺寸MM表42镶拼式型腔矩形型腔内壁短边B整体式型腔侧壁厚S凹模壁厚模套壁厚809048551314404523取总的侧壁厚度为S425MM。底板厚度的确定因模具的型腔底板为模座板,故不用再计算,其厚度即为模座板的厚度。5、动模支承板厚度的计算动模支承板两端由模脚支撑着,动模支承板在成型压力作用下发生变形时,导致塑件高度方向尺寸超差,或在分型面发生溢料现象。组合式型腔底板就是动模支承板,当已选定的动模支承板厚度通过校验不够时,可在支承板和动模底板之间设置支柱,故其厚度选择较自由。根据参考文献1表518的经验数据来确定动模友承板的厚度。塑件在分型面上的投影面积为114588522761425MM27614CM2(MM)表43塑件在分型面上的投影面积(CM2)支承板厚度501002530取动模支承板的厚度为25MM。45合模导向机构的设计导向机构起到定位作用、导向作用和承受一定的侧向压力。由于该模具的侧向压力不是很大,所以采用导柱导向机构。451导柱导柱的结构形式随模具结构大小及塑件生产批量的不同而不同。目前,在生产中常用结构有台阶式导柱注射模常用的标准台阶式导柱一般有两类,一类是带头导柱,另一类是有肩导柱。带头导柱一般用于简单模具。有肩导柱一般用于大型或精度要求高、生产批量大的模具。铆合式导柱导柱的固定不够牢固,稳定性较差,铆合式导柱结构简单,加工方便,但导柱损坏后更换麻烦,主要用于小型简单的移动式模具。合模销应用在垂直分型面的组合式型腔中。因此,导柱的结构形式采用带头导柱,其结构简单,加工方便。导柱的长度导柱的导向部分的长度要比凸模端面高出812MM。导柱的形状导柱的前端做成锥台形,便于导柱顺利地进入导向孔。24导柱的材料采用碳素工具钢T10经淬火处理,硬度为5055HRC。数量及布置导柱应合理均匀分布在模具分型面的四周,注射模采用等直径的4根导柱不对称布置,且应保证民导柱中心线到模具边缘距离为导柱直径的115倍。配合精度导柱固定端与模板之间采用或的过渡配合;导柱的67MHK导向部分采用或的间隙配合。7FH8452导套注射模常用的标准导套有直导套和带头导套两大类。直导套的结构简单,制造方便,用于小型简单模具。带头导套结构复杂,加工较难,主要用于精度要求高的大型模具。因此,导套的结构形式采用带头导套,即II型导套。导套的形状导柱孔作成通孔,为使导柱顺利进入导套,在导套前端面倒圆角。导柱孔最好做成通孔,以利于排出孔内空气及残渣废料。导套的材料采用与导柱相同的材料,但其硬度要低于导柱硬度,以减轻磨损,防止导柱或导套拉毛。导套的固定形式及配合精度用或配合镶入模板。67MHK453推出机构的设计推出机构的作用是推出留在型腔内或型芯上的制品。推出机构的设计要求尽量使塑料制品留在动模上。保证塑料制品不变形不损坏。保证制品外观良好。结构可靠。采用型推杆与推管组合的推出机构,选用直径为4的推杆7根,直径为5的为推杆6根,直径为6的推杆7根,和4根5的推管,推管同时起着成型的作用。其布置形式如下图所示25图45推杆直径D与模板上的推杆孔采用H8/F7H8/F8的间隙配合。推杆装入模具后,其端面应与型腔底面平齐,或高出型腔底面00501MM。推杆的固定采用固定板固定的形式,推杆固定端与推杆固定板采用单边05MM的间隙,这样既可降低加工要求,又能在多推杆的情况下,不因由于各板上的推杆孔加工误差引起的轴线不一致而发生卡死现象。推杆的材料用10碳素工具钢,热处理要求硬度HRC50,工作端配合部分的表面粗糙度RA08M。因该模具的推出距离不是很大,所以推管采用型芯固定在模具底板上的形式。推管的内径与型芯配合,因直径较小,所以选用H8/F7的配合;推管外径与模板孔相配合,因直径较小,故选用H8/F8的配合。推管与型芯的配合长度要比推出行程大35MM;推管与模板的配合长度一般取推管外径的115倍。推管的材料选用T10碳素工具钢,热处理要求硬度HRC50,工作端配合部分的表面粗糙度RA08M。47侧向分型与抽芯机构的设计侧向分型机构和抽芯机发类型手动侧向分型抽芯机构手动侧向分型抽芯机构又分为螺纹抽芯机构,齿轮齿条抽芯机构,活动镶块抽芯机构,其他形式抽芯机构。机动侧向分型抽芯机构机动侧向分型抽芯机构又分为斜导柱分型与抽芯机构,斜滑块分型与抽芯机构,齿轮齿条抽芯机构,其他形式抽芯机构。263)液压或气动侧向分型抽芯机构471抽芯距的确定抽芯距是指侧芯从成型位置抽到不妨碍制品取出位置时,侧型芯在抽拔方向所移动的距离。抽芯距一般应大于制品的侧孔深度或凸台高度的23MM。根据塑件的侧孔、侧凹的深度为25MM,可得抽芯距S25234555MM;取S5MM。472抽芯力的确定塑料制品在冷凝时收缩时对型芯产生包紧力,抽芯机构所需的抽拔力,必须克服因包紧力所引起的抽拔力及机械滑动的摩擦力,才能把活动型芯抽拔出来。对于不带通孔的壳体制品,抽拔时还需克服表面大气造成的阻力。在抽拔过程中,开始抽拔的瞬时,使制品与侧型芯脱离所需的抽拔力称为起始抽芯力,以后为了使侧型芯抽到不妨碍制品推出的位置时,所需的抽拔力称为相继抽芯力,前者比后者大。因此,计算抽芯力时应以起始抽芯力为准。1、影响抽芯力的因素(1)侧型芯成型部分的表面积及其几何形状;(2)塑料的收缩率;(3)制品的壁厚;(4)塑料对型芯的摩擦系数;(5)在制品同一侧面同时抽芯的数量;(6)成型工艺主要参数。2、抽芯力的计算由参考文献1得抽芯力FC的计算式为FCCHPCOSSINFC为抽芯力NC为侧型芯成型部分截面的平均周长MH为侧型芯成型部分的高度MP为塑件对侧型芯的收缩应力,一般情况下,模内冷却的塑件,P0812107MPA;模外冷却的塑件,P2439107MPA。为塑料在热状态时对钢的磨擦系数,一般015020;为侧型芯的脱模斜度27经计算C11934MM01934M;H112MM0012M;C21877MM01877M;H212MM0012M;C31277MM01277M;H310MM0010M;取015;由于侧向成型塑件高度不大,所以不设计脱模斜度,0;P取P1107;则FC101934001211070151034812N38412KNFC201877001211070151033786N33786KNFC301277001011070151019155N19155KN473侧向抽芯机构的确定方案一三个侧向抽芯都采用斜导柱侧向分型与抽芯机构。斜导柱侧向分型与抽芯机构是利用斜导柱等零件把开模力传递给侧型芯或侧向成型块,使之产生侧向运动完成抽芯与分型动作。其特点是结构紧凑、动作安全可靠、加工制造方便,是设计和制造注射模抽芯时最常用的机构。但它的抽芯力和抽芯距受到模具结构的限制,一般使用于抽芯力不大及抽芯距小于6080MM的场合。方案二采用弹簧侧向抽芯机构。弹簧侧向抽芯机构与斜导柱侧向抽芯机构对比其特点是省去了斜导柱,使模具结构简化。但其只适用于侧向成型零件所需的抽芯力和抽芯中都不大的抽芯机构。方案三结合方案一和方案二,抽芯力较大的两个采用斜导柱侧向分型与抽芯机构,抽芯力较小的一个采用弹簧侧向抽芯机构。综合分析,选用方案三较好。474斜导柱的设计(1)、斜导柱的结构设计斜导柱形状多为圆柱形,为了减少其与滑块的摩擦,可将其圆柱面铣扁,斜导柱工作端的端部可采用锥台形或半球形,锥体角应大于斜导柱的倾角,以避免斜导柱有效工作长度部分脱离滑块斜孔之后,锥体仍有驱动作用。但半球形加工时较困难,所以采用锥台形的结构,其斜角2,以免端部锥台也参与侧抽芯,导致滑块停留位置不符合原设计计算的要求。28斜导柱的材料用T10A碳素工具钢,由于斜导柱经常与滑块摩擦,热处理要求硬度HRC55,表面粗糙度RA08M。斜导柱与其固定的模板之间采用H7/M6的过渡配合,由于斜导柱在工作过程中主要用来驱动侧滑块作往复运动,侧滑块运动的平稳性由导滑槽与滑块之间的配合精度保证,而合模时滑块的最终准确位置由锲紧块决定。为了运动的灵活,滑块上斜导孔与斜导柱之间保留051MM的间隙。此间隙使滑块运动滞后于开模动作,且使分型面处打开一缝隙,使塑件在活动型芯未抽出前获得松动,然后再驱动滑块抽芯。(2)、斜导柱倾角的确定斜导柱轴向与开模方向的夹角称为斜导柱的倾斜角,它不仅决定了开模行程和斜导柱长度,并且对斜导柱的受力状况有着重要的影响。在确定斜导柱倾斜角时,通常抽芯距短时可适当取得小些,抽芯距长时取大些;抽芯力大时,可取小些,抽芯力小时可取大些。另外,还应注意,斜导柱在对称布置时,抽芯力可相互抵消,可取大些;而斜导柱非对称布置时,抽芯力无法抵消,宜取小值。由参考文献1得斜导柱的倾角一般小于25,常用为1222。由于抽芯距短,而抽芯力又小,斜导柱对称布置,抽芯力可相互抵消,综合分析,取斜导柱的倾角18。(3)、斜导柱的直径的确定斜导柱的直径必须根据抽芯力、斜导柱有效工作长度和斜导柱的倾角来确定。由于计算比较复杂,在实际生产中,根据斜导柱斜角及所承受最大弯距力,可直接用查表法得出斜导柱直径。按抽芯力FC和斜导柱斜角查参考文献1表520得斜导柱的最大弯曲力F14KN、F24KN。根据最大弯曲力F和侧型芯
- 温馨提示:
1: 本站所有资源如无特殊说明,都需要本地电脑安装OFFICE2007和PDF阅读器。图纸软件为CAD,CAXA,PROE,UG,SolidWorks等.压缩文件请下载最新的WinRAR软件解压。
2: 本站的文档不包含任何第三方提供的附件图纸等,如果需要附件,请联系上传者。文件的所有权益归上传用户所有。
3.本站RAR压缩包中若带图纸,网页内容里面会有图纸预览,若没有图纸预览就没有图纸。
4. 未经权益所有人同意不得将文件中的内容挪作商业或盈利用途。
5. 人人文库网仅提供信息存储空间,仅对用户上传内容的表现方式做保护处理,对用户上传分享的文档内容本身不做任何修改或编辑,并不能对任何下载内容负责。
6. 下载文件中如有侵权或不适当内容,请与我们联系,我们立即纠正。
7. 本站不保证下载资源的准确性、安全性和完整性, 同时也不承担用户因使用这些下载资源对自己和他人造成任何形式的伤害或损失。

人人文库网所有资源均是用户自行上传分享,仅供网友学习交流,未经上传用户书面授权,请勿作他用。