资源目录
压缩包内文档预览:(预览前20页/共40页)
编号:1284201
类型:共享资源
大小:2.18MB
格式:ZIP
上传时间:2017-06-21
上传人:机****料
认证信息
个人认证
高**(实名认证)
河南
IP属地:河南
50
积分
- 关 键 词:
-
板料
折弯
液压
系统
设计
全套
cad
图纸
- 资源描述:
-




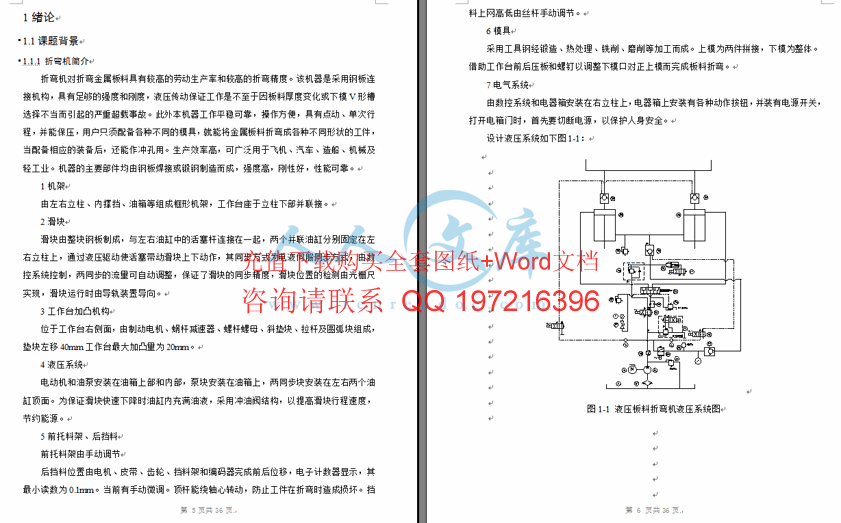


- 内容简介:
-
第 1页共 36 页 板料折弯机液压系统设计 摘要: 折弯机对折弯金属板料具有较高的劳动生产率和较高的折弯精度。当折弯不同厚度的板料时,应选择不同开口的 V 槽,若采用不同形状的上下模具,可折弯成各种形状的工件。 本设计主要设计折弯机的液压系统,在整个设计过程中,不影响设计要求的情况下,本设计能用标准件的在尽量采用标准件,从而提高整个折弯机的性价比。因而本设计主要对液压系统中的液压缸和油箱进行了设计。 在设计过程中我参考了很多设计手册。使我学会了很多知识,让我了解到作为一个设计工程师所必须作的事。而且我又在不影响液压缸性能的前提下进行 了一些创新,使缸的制造成本有些降低。但对缸的某些复杂结构进行了简化,对于油箱的设计,我在遵守设计手册要求的前提下,增加了一些辅助功能,使油箱更趋于完善、合理。以使我在本次设计中得到更多的锻炼,更适应将来的工作。 此次设计对于提高工作效率节约工作时间具有较好的意义,为向数控和智能化折弯机进行设计打好基础。 关键词: 液压系统;液压缸;油箱 板料折弯机液压系统设计 第 2 页共 36页 he it on we If I my to if s so So do is of of of of to Of my I my to of It is a us to 第 3页共 36 页 目录 1 绪论 .题背景 . 折弯机简介 . 设计内容简介 .压传动的基本知识 . 液压系统的概念 . 液压传动的组成 . 液压系统的优点 . 液压系统设计 . 系统元件设计 .压缸的设计 . 设计液压折弯机的技术参数 . 负载分析和运动分析 . 液压缸主要零部件结构 ,材料与技术要求 .压泵的选择 . 液压泵的性能参数及计算公式 . 轴向柱塞泵的工作原理 . 轴向柱塞泵的工作要求 . 油泵的选择 .箱的设计 . 油箱的功能 . 油箱的类型 . 油箱的设计要求及结构 . 油箱附件 .统其它元件的选用 . 蓄能器的选用 .料折弯机液压系统设计 第 4 页共 36页 机的选择 . 结论 .考文献 .录 .谢 .第 5页共 36 页 1 绪论 题背景 弯机简介 折弯机对折弯金属板料具有较高的劳动生产率和较高的折弯精度。该机器是采用钢板连接机构,具有足够的强度和刚度,液压传动保证工作是不至于 因板料厚度变化或下模 V 形槽选择不当而引起的严重超载事故。此外本机器工作平稳可靠,操作方便,具有点动、单次行程,并能保压,用户只须配备各种不同的模具,就能将金属板料折弯成各种不同形状的工件,当配备相应的装备后,还能作冲孔用。生产效率高,可广泛用于飞机、汽车、造船、机械及轻工业。机器的主要部件均由钢板焊接或锻钢制造而成,强度高,刚性好,性能可靠。 1 机架 由左右立柱、内撑挡、油箱等组成框形机架,工作台座于立柱下部并联接。 2 滑块 滑块由整块钢板制成,与左右油缸中的活塞杆连接在一起,两个并联油缸分别固定在左右立柱 上,通过液压驱动使活塞带动滑块上下动作,其同步方式为电液伺服同步方式,由数控系统控制,两同步的流量可自动调整,保证了滑块的同步精度,滑块位置的检测由光栅尺实现,滑块运行时由导轨装置导向。 3 工作台加凸机构 位于工作台右侧面,由制动电机、蜗杆减速器、螺杆螺母、斜垫块、拉杆及圆弧块组成,垫块左移 40作台最大加凸量为 20 4 液压系统 电动机和油泵安装在油箱上部和内部,泵块安装在油箱上,两同步块安装在左右两个油缸顶面。为保证滑块快速下降时油缸内充满油液,采用冲油阀结构,以提高滑块行程速度,节约能源。 5 前托料架、后挡料 前托料架由手动调节 后挡料位置由电机、皮带、齿轮、挡料架和编码器完成前后位移,电子计数器显示,其最小读数为 前有手动微调。顶杆能绕轴心转动,防止工件在折弯时造成损坏。挡板料折弯机液压系统设计 第 6 页共 36页 料上网高低由丝杆手动调节。 6 模具 采用工具钢经锻造、热处理、铣削、磨削等加工而成。上模为两件拼接,下模为整体。借助工作台前后压板和螺钉以调整下模口对正上模而完成板料折弯。 7 电气系统 由数控系统和电器箱安装在右立柱上,电器箱上安装有各种动作按钮,并装有电源开关,打开电箱门时,首先要切断电源,以保护人身安全。 设 计液压系统如下图 1 211542316图 1压板料折弯机液压系统图 第 7页共 36 页 计内容简介 本次设计主要涉及板料折弯机的液压系统。因液压系统中很多零部件已标准化,所以在设计过程中只对标准件进行选型,没有进行设计。对于非标准件,像油缸、油箱等进行了设计。 在设计油缸的过程中,我参考设计手册的同时,也有自己的创新。比如。我把活塞的密封件、导向环、支撑环放在一起,这样不但对活塞加工大大简化,而且可以增加活塞的强度;在油箱的设计中,在不影响油箱的功能的前提下,我把空气过滤器和注油孔放在一起。同时对电机和油泵的 放置进行了设计。 液压传动发展非常迅速,特别是近年来随着加工技术的提高,更是为液压技术的发展铺平了道路。虽然国内液压传动发展很快,但与国外其他国家相比还是比较落后的。具体表现在,液压系统承受压力不高,传递介质泄漏等。整体表现为整个液压系统的性价比明显低于国外同行。液压传动在实现工业自动化方面与电配合有了很大发展,所以液压传动的发展前景还是很广阔的。 压传动的基本知识 压系统的概念 ( 1)液压传动:它是以液压油为工作介质,通过动力元件(油泵)将原动机的机械能变为液压油的液压能,在通过控制 元件,然后借助执行元件(油缸或油马达)将压力能转化为机械能,驱动负载实现直线或回转运动,且通过对控制元件遥杆操纵和对流量的调节,调定执行元件的力和速度。当外界对上述系统有扰动时,执行元件的输出量一般要偏离原有调定值,产生一定的误差。 ( 2)液压控制:和液压传动一样,系统中也包括动力元件、控制元件和执行元件,也是通过油液的传递功率。二者不同之处是液压控制具有反馈装置,反馈装置的作用是执行元件的输出量(位移、速度、力等机械量)反馈回去与输出量(可以是变化的也可以是恒定的)进行比较,用比较后的差值来控制系统,使执 行元件的输出随输入量的变化而变化或保持恒定。它是一种构成闭环回路的液压传动系统,也叫液压随动系统或液压伺服系统。 液压传动系统中用的是通断式或逻辑控制元件,就其控制目的,是保持被调定值的稳定或单纯变换方向,也叫定值和顺序控制元件。 板料折弯机液压系统设计 第 8 页共 36页 液压控制系统中用的是伺服控制元件,具有反馈结构,并用电气装置进行控制,有较高的控制精度和响应速度,所控制的压力和流量连续变化。输出功率可放大。 比例控制是介于上述二者之间的一种控制,所用比例控制阀是通断式控制元件和伺服控制元件的基础上发展起来的一种新型的电 备了上述 两类元件的一些特点 ,用于用手调的通断式控制不能满足要求,但也不需要伺服阀对液压系统那样严格的污染控制要求的场合。 压传动的组成 一个完整的液压传动系统包括五个基本组成部分,即动力元件、执行元件、控制元件、辅助元件和工作液体。 动力元件是将原动机所提供的机械能转变为工作液体的液压能的机械装置,通常称为液压泵或油泵。它是液压系统中的液压能源,是组成液压系统的心脏,用它向液压系统输送足够量的压力油。 按结构不同液压泵可以分为齿轮泵、叶片泵、柱塞泵和螺杆泵; 按其压力不同又可分为低压泵、中压泵、中 高压泵、高压泵和超高压泵; 按其输出流量能否调节又分为定量泵和变量泵。 执行元件是将液压泵所提供的工作液体的液压能转变为机械能的装置。做直线往复运动的执行元件称为液压缸或油缸,做连续旋转运动的执行元件成为液压马达或油马达。 控制元件是对液压系统中工作液体的压力、流量和流动方向进行调节控制的机械装置。根据不同的功能分为压力控制阀、流量控制阀和方向控制阀。压力控制阀又分为溢流阀、减压阀、顺序阀、压力继电器等。流量控制阀包括节流阀、调整阀和分流阀等。根据控制方式不同可分为开关控制阀、比例控制阀、伺服控制阀和数字控 制阀。 辅助元件包括邮箱、管道、管接头、密封件、滤油器、蓄能器、冷却器、加热器以及各种液体参数的监测仪。 工作液体是液压传动中能量传递载体。有各种矿物油、乳化液和合成型液压油等几大类。 压系统的优点 在目前四大类传动方式(电气、机械、液压和电气)中,没有一种动力传动是十全十美的,而液压传动具有下述极其明显的优点: ( 1)从结构上看,其单位重量的输出功率和单位尺寸输出的功率在四类传动方式中力压 第 9页共 36 页 群芳的,有很大的力矩惯量比,在传递相同的功率的情况下液压传动装置的体积小、重量轻、惯性小、结构紧凑、布局灵 活。 ( 2)从工作性能上看,速度、扭矩、功率均可无级调节,动作响应快,能够迅速换向和变速,调速范围宽,调速范围可达 100: 1 到 2000: 1;动作快速性好,控制、调节比较简单省力,便于电气控制相配合,以及与 算机)的连接,便于实现自动化。 ( 3)从使用维护上看,元件的润滑性好,易实现过载保护与保压,安全可靠;元件易实现系列化、标准化、通用化。 ( 4)所有采用液压技术的设备安全可靠性好。 ( 5)经济:液压技术的可塑性和可变性强,可以增强柔性生产的柔度,和容易对生产程序进行改变和调整,液压元件相对来说制 造成本也不高,适应性比较强。 ( 6)液压易于微机控制等技术相结合,构成“机 液 体化以为成为世界的潮流,便于实现数字化。 板料折弯机液压系统设计 第 10 页共 36页 2 液压系统设计 根据板料折弯机的使用要求及对加工板料的特殊要求,我们考虑采用液压传动作为板料折弯机的主要传动形式。由机器的特性可知,在机器工作时尚模块必须有以下几个动作:快速向下、慢速向下、向下点动、保压、快速向上。机器工作时,为了节约能源,在滑块距被加工工件较远时,滑块采用快速向下的动作。这样不仅节约能源,而且可以提高劳动生产率;当滑块距被加工工件很近 时(通常为 20滑块的下移速度会明显降低。此时,主要是因为上模将要接触工作,为了避免有较大的刚性冲击其下降速度减小,即为滑块的慢速向下阶段;当上模块接触被加工工件时,考虑到加工板料的特殊要求,上模块必须向下点动的形式来加工工件,以避免板料应力在短时间内迅速增大,损坏被加工工件;保压过程是板料折弯机工作过程不可缺少的。刚刚压制好的工件会因为应力的存在而有恢复原来形状的本性,为了保证加工精度,折弯机在压制过程结束后必须进行保压过程。保压时间的长短要根据具体情况具体分析,一般情况下,加工板料越厚保压时 间越长,反之亦然;当压制工作全部完成以后,为了节约能源和提高劳动生产效率,上模块即滑块采用快速向上动作,以便开始下一个工作过程的开始。 其工作原理为: 油泵启动: 如图 1动机按泵的标注的箭头方向旋转,即顺时针方向旋转,带动轴向柱塞泵,浆滤清的油液通过吸油管进入阀板和电磁溢流阀回油箱, 19 号阀封闭 20 号油缸下腔油液,使滑块停在任意位置上。 滑块快速向下: 当 9 号 24 号 13 号 17 号 磁铁工作时,滑块快速下降 ,下降速度由 18 号阀调整, 20 号油缸下腔的油通过 19 号、 18 号、 17 号闯入油箱,油缸上腔的油由油箱通过 21 号阀灌满。 滑块慢速向下: 当滑块下降撞到限位开关时, 9 号 8 号 11 号 13 号 24 号 泵输入的油经过阀门进入油缸,滑块进入工作速度。如滑块不同步时,由 15号阀自动纠正,滑块下降位置由油缸中的机械挡块的螺母限止。 第 11页共 36页 滑块点动向上或向下: 由脚踏开关或按钮控制 9 号 8 号 11 号 13 号 24 号 磁铁工作的时间长短,实现滑块下降时点动距离,滑块下降的速度由 16 号阀调整,滑块向上由11 号 24 号 磁铁工作,同样电磁铁工作时间的长短,实现滑块向上点动距离。 滑块回程: 在回程的瞬时要求 8 号 磁铁先复位 2 秒钟实现泄压,随后 11 号 24 号 块回程,回程速度是恒定的。 机器的压力调整: 6 号高压溢流阀、 11 号电磁溢流阀保证机器的额定力(见技术参数表)。 14 号溢流阀使机器的回程力可调至 15至因过载而损害机器,液压系统中的工作压力可以从 7 号压力表中读出,使 用时不准超过。用户可通过安装在立柱侧面的 12 号远程调正阀调整所需的压力。 10 号蓄能器充氮压力为 4要是操纵 19 号、 21 号阀所需压力 . 各个电磁阀动作规范表 2 2电磁阀动作规范表 启动位置 快速向下 慢速向下 向下点动 保压 向上 板料折弯机液压系统设计 第 12 页共 36页 3 系统元件设计 压缸的设计 计液压折弯机的技术参数 表 3弯机的技术参数 工作台长度 立柱间距 喉口深度 主电机功率 最大折弯力 滑块重力 G 41006500010005000N 快速下降的速度 速加压的速度 速上升的速度 速下降的行程 速加压的行程 速上升的行程 20mm/s 7mm/s 80mm/s 190515 负载分析和运动分析 折弯机滑块做上下直线运动,且行程较小,可选单杆双作用液 压缸作执行器(取液压缸的执行效率为 表 3载分析 工况 计算公式 外负载 /N 说明 快速下降 启动加速 G/g t 917 ( 1) F G/g v 1 / t=15000/(120103 /917N; m/s; ( 2)由于忽略滑块导轨摩擦力,故快速下降等速时外负载为 0; ( 3)折弯时压头上的工作负载可分为两个阶段:初压阶段:负载力缓慢的增加,约达到最大折弯力的 5%,其行程为 15压阶段,负载力急剧增加到最大折弯力,上升规律 近似于直线,行程为 5 ( 4) F 2i =G/g v 2 / t=15000/(80103 / m/s 等速 0 慢速折弯 初压 5% 50000 终压 1000000 快速回程 启动 G=G/g+G 速 F=G 15000 制动 g t 第 13页共 36页 表 3动分析 工况 计算式 时间 /s 说明 快速下行 t=1 弯时分为两个阶段,初压阶段 22为5速折弯 初压 t=2 压 t=2 速上升 t=3 液压缸主要零部件结构,材料与技术要求 ( 1)缸筒与端盖:缸筒与端盖连接用法兰形式连接,前端盖用螺纹连接,后端盖用焊接连接。 ( 2)缸筒的材料一般要求有足够的强度和冲击韧性,能长期承受最高工作压力及短期动态实验压力而不致产生永久变形;有足够的刚度,能承受活塞侧向力和安装的反作用力而不致产生弯曲。 根据缸筒内径,选用 45 号钢,抗拉强度 b=700服强度 s=600 650长率为 4%、硬度 210 220。 技术 要求: ( 1) 缸筒内径选用 10配合。内径的表面粗糙度,当活塞密封采用橡胶密封件时,取 m,当采用活塞环密封时,则取 缸筒端面 级精度。 缸筒内径的圆度和圆柱度公差可选取 8级或 9级精度。 缸筒端部用螺纹连接时,螺纹应选用 6级精度的细牙螺纹。 当液压缸的安装方式为耳环型,后端盖的耳孔 缸筒内孔轴线的垂直度可取 9 级精度。 为了防止腐蚀以及其它使用的特殊要求,缸筒内表面可镀铬,镀层厚 度为 30 40 m,并研磨抛光。 ( 2) 活塞的结构主要考虑与缸筒内壁的滑动和密封,以及与活塞杆之间的连接和密封。活塞的结构形式取决于密封件的形式米饭见的形式由压力、速度温度来决定。 活塞的密封:活塞与缸筒常用的密封有间隙密封,活塞环 用组合密封装置。活塞与活塞杆之间为间隙密封、配合之间的密封为固定密封,采用 第 14 页共 36页 塞杆上。 活塞的导向:导向环(支撑环)的作用:具有精确的导向作用,并可吸收活塞运动时产生的侧向力。 带导向的活塞在缸筒内为非金属接触,摩擦系数小,无爬行;导向能改善活塞与 缸筒的同轴度,使间隙均匀,减少泄漏;导向套用耐磨材料,使用寿命长,且具有良好的承载能力。采用组合型导向环。 组合型导向是由密封圈、挡圈和导向组成,它们安装在同一沟槽内,具有密封、导向双重作用。 活塞的材料:选用碳素钢 45号。 技术要求 :对内径 级。 对内径 级精度选取。 的圆柱度公差按 9 11级精度选取。 ( 3)活塞杆: 活塞杆外端连接形式采用单耳环形式。 活塞杆的导向、密封和防尘:活塞杆的导向、密封和防尘结构全部在前端盖内, 具体结构见液压缸图。 活塞杆采用非金属导向环,前端盖用碳素钢制成,其内孔安装用聚四氟乙烯等非金属耐磨材料制成的导向环,为活塞杆导向。活塞杆与前端盖为非金属接触摩擦阻力小,使用寿命长。导向的沟槽加工容易,磨损后更换导向套也很方便,应用比较普遍。 活塞的密封,以往多采用 些密封圈形式由于活塞杆与密封圈之间是干摩擦,摩擦阻力大,磨损快。因此,近年来较多选用组合式密封圈,如方形圈(格来圈)、阶梯圈(斯特封)。它们具有摩擦阻力小,启动时无爬行,较低的泄漏量和耐磨等优点。 活塞杆的防尘,以 往多采用无骨架防尘圈。目前多采用既可以防尘,又可以密封的双唇型防尘圈。外唇起防尘作用,保证活塞杆表面清洁,内唇起密封作用。当活塞杆外伸时,通过主密封圈留在活塞杆表面的油膜,即被防尘圈的内唇刮下,这样,在主密封圈和防尘圈之间保留一层油膜,起润滑作用,提高了密封圈的使用寿命。 活塞杆的材料:由专业厂生产的高精度冷拔活塞杆,可直接选用。 第 15页共 36页 活塞杆的技术要求: 层厚度为 15 25微米或 30 50微米。防腐要求特别高的则先镀一层铬或镍,然后再镀铬并抛光。 蚀性极强的工作环境中 ,活塞杆喷涂一种名为 强度、抗腐蚀性和抗磨损等方面,比硬铬更优。 7 19;直线度 00面粗糙度 精确度要求更高者, 8级精度选取。 ( 4)液压缸的结构设计 液压缸的设计 : 液压缸是液压传动的执行元件 ,它与主机和主机上的工作机构有着直接的联系 ,对于不同机种和机构 ,液压缸具有不同的用途和工作要求 ,因此在液压缸设计前应做好调查 . 工作负载 R: 液压缸的工作负载 以一定的加速度启动时对液压缸产生的总阻力 ,即 :R=m+中 工作机构的荷重及自重对液压缸产生的作用力 工作机构在满载启动时的静摩擦力 工作机构满载启动时惯性力 由设计方案知 :最大折弯力为 1000作时由两个相同的液压缸同时工作 ,所以 00导轨摩擦载荷于平导轨 , ( G+ (对于 V 型导轨 , 2 ((式中 G 运动部件所受的重力( N) ; 摩擦系数; V 型导轨的夹角,板料折弯机液压系统设计 第 16 页共 36页 一般为 90o) . 本设计中选择平导轨 : ( G+ (查机 械设计设计手册知: 由设计方案知 00于活塞和活塞杆以及滑块重力进行估算取 G 值为 15即性载荷gR=gGt(式中 g 重力加速度, g= ; 速度变化量( m/s) ; t 启动或制动时间( S),一般机械 t =此取 t =设计方案知 :取 最大时 , =N 所以工作负载 R=500 N +N =N 缸筒内径 D: 在确定 D 时,必须保证液压缸在系统所给定的工作压力下,具有足够的牵引力来驱动工作负载。对于双作用单活塞杆液压缸,当活塞杆是以推力驱动工作负载时,即压力油输入无杆腔时,工作负载 R 为: R= F =4 D= pp 24(式中: R 液压缸的工作负 载 F 活塞杆的最大推力 机械效率,常取 =P 工作压力 p 回油背压,若回油直接通油箱,可取 p 0, d 活塞杆直径,当活塞杆是以拉力驱动工作负载时,则压力油输入有杆腔。则 第 17页共 36页 R= F =4 D= pp 24(对于双作用活塞杆,缸筒内径应取按公式 1 和 2 计算结果的较大值,然后进行数据圆整。 由于 R=N ,所以 F=N ,缸筒内径 D 应按 计算,即 D= 24 (由活塞杆直径 d 的推荐值:当活塞杆受拉时, d=( D;当活塞受压时 d=( d=125 所以其工作压力 P 为: P= 224 = (在此计算功率 W= 241 W 最小导向长度 H 的确定 : 当活塞杆全部外伸时,从活塞支撑面中点到导向套滑动面中点的距离成为最小导向长度H,对单活塞液压缸,一般 H220 式中 L 活塞最 大工作行程 D 缸筒内径 由设计方案知: L=215 所以 H220 ,即 H a当 D/ 10 时,为薄壁,则 2,圆整数据得 =18 缸筒壁厚的验算: 证工作安全。 (将缸 筒内径 ,缸筒外径 +2 =入上式 整数据得 = 液压缸进出口布置前后端盖上 ,采用螺纹连接。 根据国标 2878定的液压缸进出口螺纹尺寸。选用螺纹为 ,即 , 2。螺纹精度为 6H。 a由公式 1 ( 式中 D 缸筒内径 d 活塞杆直径 速 度 比 。( 速 度 比 为 活 塞 两 侧 有 效 面 积 比 。 即 :22222111) 本设计中取 入式中可得 活塞杆强度计算 一般以液压缸活塞杆端部和缸筒端盖均为耳环铰接安装方式情况来考虑,而且当活塞杆全部伸出时, 活塞杆端和负载的连接点到液压缸支撑点间的距离假定为 由液压缸实际情况及活塞杆直径可知 0 ,故主要验算活塞杆压缩和抗拉强度。即2 式中 d 活塞杆直径 F 液压缸的最大推(拉)力 s 材料的屈服强度 板料折弯机液压系统设计 第 20 页共 36页 安全系数,一般取 4 将 , F=n=4 代入可得; 较可 知符合要求 密封件的选择 活塞与缸筒的密封选用组合密封件,详见图纸,活塞与活塞杆的密封选用 0 型密封圈,密封圈内径为 136开在活塞杆上,活塞杆密封件选用: Y 型橡胶密封圈,由活塞杆直径为 140用尺寸详见中国机械设计大典第五分册机械控制系统设计的538 页。防尘圈根据国标 择,由活塞杆直径为 140用 A 型,具体尺寸见表 3尘圈尺寸( d D s l 基本尺寸 极限偏差 基本尺寸 极限偏差 基本尺寸 极限偏差 基本尺寸 极限 偏差 75 压泵的选择 压泵的性能参数及计算公式 额定压力 正常工作条件下,根据实验结果推荐的允许连续运行的最高压力。额定压力值与液压泵的结构形式及其零部件的强度、工作寿命和容积效率有关。 最高压力 实验标准规定超过额定压力而允许短暂运行的最高压力,其值主要取决于零件及其相对摩擦副的极限强度。 工作压力 P 液压泵进口处的压力,自吸泵的吸入压力低于大气压力,一般用吸入高度衡量。当液压泵的安装高度或吸油阻力过大时,液压泵的进口压力将因低于极限吸入压力而导致吸油不充分,而在吸油区产生气穴或气蚀。吸入压力的大小与泵的结构型式有关。 液压泵的转速 额定转速 n 第 21页共 36页 在额定压力下,根据实验结果,推荐能长时间连续运行并保持较高运行效率的转速。 最高转速 额定压力下,为保证使用寿命 和性能所允许的短暂运行的最高转速。其值主要与液压泵的结构形式及自吸能力有关。 最低转速 保证液压泵可靠工作或运行效率不至过低所允许的最低转速。 液压泵的排量及流量 排量 V 液压泵主轴转一周所排出的液体体积,排量的大小取决于液压泵的结构和几何尺寸,有时又称为理论排量。 理论流量 考虑泄露,液压泵单位时间内所排出的液体体积( m3/s) 10310*60 6 (式中: n 液压泵的转度( r/ V 液压泵排量( r) 实际流量 q 在实际运行时在不同压力下液压泵所排出的流量。实际流量低于理论流量,其差值q=压泵的泄露流量。 额定流量 额定压力、额定转速下,液压泵所排出的实际流量。 瞬时理论流量 于运动学机理,液压泵的流量往往具有脉动性,液压泵某一瞬间所排的理论流量称为瞬 时理论流量。 流量不均匀系数 q 在液压泵的转速一定时,因流量脉动造成的流量不均匀速度。 113)()( m a x q 液压泵的功率 P 板料折弯机液压系统设计 第 22 页共 36页 液压泵的输出功率( 其流量 q 和出口压力 p 或进口压力差 p 表示 12310* 3 ( 式中: q 液压泵实际流量 p 液压泵进出口压力差,通常液压泵的进口压力近似为零,因此液压泵进出口压力差可用其出口压力表示。( 输出功率 液压泵的输出功率即原动机的输出功率。 总效率 液压泵的输出功率 于输入功率之比。 133/ ( 容积效率 v 在转速一定的条件下,液压泵的实际流量与理论流量之比。 14311 nV qq ( 式中: q 液压泵的泄露量,在液压泵结构型式、几何尺寸确定后,泄露量 q 的大小主要取决于泵的出口压力,与液压泵的转速(对定量泵)或排量(对变量泵)无多大关系。因此液压泵在低转速或小排量下工作时,其容积效率将会很低,以致无法正常工作。 机械效率 m 对液压泵,除容积泄露损失都归于 机械损失,因此 153 ( 液压泵的噪声 液压泵的噪声通常用分贝( 量,液压泵的噪声产生的原因包括:流量脉动、流量冲击、零部件的震动和摩擦以及液压冲击等。 液压泵按照泵的工作形式不同可分为:齿轮泵、叶片泵、和柱塞泵。根据本设计所需压 第 23页共 36页 力和放置油泵的体积,初步选定轴向柱塞泵 向柱塞泵的工作原理 轴向柱塞泵是柱塞泵线与缸体轴线平行且在缸体孔内作往复运动来改变柱塞底部 容积大小实现吸油和压油的柱塞泵。轴向柱塞泵不仅额定压力高,而且可以实现多种形式的变量,因此应用极广在液压泵中占有及其重要的位置。 轴向柱塞泵柱塞实现往复运动的方式分为斜盘式和斜轴式。斜盘式是利用斜盘对柱塞的约束反力和弹簧力的共同作用使柱塞泵缩回或外伸;斜盘式利用缸体轴线相对泵轴存在一个摆角而被连杆强制的实现柱塞的往复运动。 斜盘式轴向柱赛泵又按以下几种分类方法分类: (1)按泵轴的支承方式分为通轴式和非通轴式。通轴式的泵轴穿过缸体,两端有轴承支承,此时斜盘位于泵轴的输入端,因此又称前置斜盘式。非通轴式的泵轴 的输入端由轴承支承,另一端为花键,与缸体内花键连接,其轴承位于缸体的外圆,此时斜盘处于泵轴的尾端,因此由称后置斜盘。 (2)按柱塞球头与斜盘的接触方式分为点接触式和滑稽式。点接触的接触式的柱塞球头直接与斜盘接触,二者接触应力大。滑稽式在柱塞球头加滑稽后由滑稽底面与斜盘接触,使接触应力大大减小,其额定压力大大提高。 (3)按配流方式分为配流盘和阀式配流,配流盘上开有两个腰圆形窗口,当缸体旋轴时,缸体底部窗口交替与配流窗口相通,实现配流(吸油和压油)。阀式配流的向柱塞泵的缸体不旋转,当泵轴带动斜盘带动斜盘旋转时 ,每个柱塞底部的容腔通过一个进油阀和一个排油阀实现吸油和压油,因此排油阀或球阀、密封性好、因此阀式配流用于超高压且多为定量泵。 斜盘式和斜轴式柱塞泵的排量公式为: V= 163 (式中: d 柱塞直径 D 柱塞分布圆直径 Z 柱塞孔的数目 a 斜盘倾角 显然,改变斜盘倾角 大小可以改变排量,若斜盘倾角固定不能改变则为定量泵。 板料折弯机液压系统设计 第 24 页共 36页 向柱 塞泵的工作要求 ( 1)轴向柱塞泵与原动机之间要求用弹性连轴器连接,两轴的同轴要求在 内。 ( 2)轴向柱塞泵在最高处设计有外进油口,泵在起动前应由油口向壳体内灌满清洁的工作介质,排净壳体的空气,泵工作时泄露油由此油口单独引回油箱。为避免空气侵入,泄露管应插入液面以下,轴向柱塞泵的壳体最低处开有一放油口,泵工作时此口螺柱堵上,维修泵时先由此油口将壳体内的油液放光,然后再拆卸零部件。 ( 3)配流盘配流的柱塞泵的自吸高度应小于 最好是液面高度高于泵的吸油口,以改善吸油性能。 ( 4)轴向柱塞泵若配流盘采用非对称性结构,则必须按指定的方向旋转。 ( 5)轴向柱塞泵对工作介质的过滤精度要求较高,为 10 m,对于回油系统采用全部回油过滤。吸油口不宜装过滤器;对闭式系统进排油都要进行过滤。 ( 6)轴向柱塞泵的传动轴的径向载荷和轴向载荷不得超过说明书或工厂的有关规定。 ( 7)轴向柱塞泵的工作介质必须具有相容性,若系统所用工作介质为非矿物质油,应特别予以说明。 泵的选择 根据所设计液压缸所须额定压力为 考虑到液压管路损失和压力储备。故选择额定压力为 轴向柱塞泵。其型号为 10术参数;称排量为 10r;额定转速为 1500r/动功率 10积效率 量 20 箱的设计 箱的功能 (1)存储供油系统工作循环所需的油量。 (2)散发系统工作过程中产生的一部分热量。 (3)促使油液中的空气分离及消除泡沫。 (4)为系统提供元件的安装位置。 箱的类型 液压系统中的油箱有整体式和分离式两种,整体式油箱利用主机内腔作为油箱,这种油 第 25页共 36页 箱结构紧凑,各处漏油易于回收,但增加了设计和制造的复杂性,维修不便。散热条件不好,且会使主体产生热变形。 分离式油箱单独放置,与主机分开,减少了油箱发热和液压原震动对主机工作精度的影响;综合以上两种形式的油箱的优缺点,及考虑设计液压系统的应用环境,故在此设计中选用分离式油箱。 根据液压泵与油箱相对安装位置不同,又可分为上置式、下置式和旁置式。上置式油箱将液压泵等装置安装在油箱的上盖板上,结构紧凑,应用最普遍;下置式油箱是将液压泵置于油箱底下,这种安装方式,常将油箱架高到使人能够在油箱底下自由通过,既减少安装的设备面积,有可使液压泵的吸入性大为改善;旁置式油箱将液压泵等装置安装在油箱旁
- 温馨提示:
1: 本站所有资源如无特殊说明,都需要本地电脑安装OFFICE2007和PDF阅读器。图纸软件为CAD,CAXA,PROE,UG,SolidWorks等.压缩文件请下载最新的WinRAR软件解压。
2: 本站的文档不包含任何第三方提供的附件图纸等,如果需要附件,请联系上传者。文件的所有权益归上传用户所有。
3.本站RAR压缩包中若带图纸,网页内容里面会有图纸预览,若没有图纸预览就没有图纸。
4. 未经权益所有人同意不得将文件中的内容挪作商业或盈利用途。
5. 人人文库网仅提供信息存储空间,仅对用户上传内容的表现方式做保护处理,对用户上传分享的文档内容本身不做任何修改或编辑,并不能对任何下载内容负责。
6. 下载文件中如有侵权或不适当内容,请与我们联系,我们立即纠正。
7. 本站不保证下载资源的准确性、安全性和完整性, 同时也不承担用户因使用这些下载资源对自己和他人造成任何形式的伤害或损失。

人人文库网所有资源均是用户自行上传分享,仅供网友学习交流,未经上传用户书面授权,请勿作他用。