曲轴工艺规程设计及系列夹具设计【铣端面+磨夹具】
43页 19000字数+说明书+任务书+开题报告+外文翻译+6张CAD图纸【详情如下】
V形架夹具图 A3.dwg
任务书.doc
外文翻译--机械设计.doc
工艺工序卡片19张
曲轴工艺规程设计及系列夹具设计开题报告.doc
曲轴工艺规程设计及系列夹具设计论文.doc
曲轴模夹具装配图 A0.dwg
磨夹具装配图3 A0.dwg
计划周记进度检查表.xls
过渡盘夹具图 A1.dwg
铣端面夹具装配图 A0.dwg
铸铁夹具图 A2.dwg
摘 要
本次设计的主要内容包括空压机曲轴的工艺规程设计和系列夹具设计的两大方面。
制定工艺规程设计的原始资料包括:零件的图样,产品验收质量标准,产品的年生产纲领和生产类型、毛坯图样、生产条件、零件材料等。制定工艺规程设计步骤如下:审查零件的图样,工艺方案的确定,对样品进行工艺分析,零件的毛坯选择以及毛坯图说明; 工艺设计过程(包括加工段的分析,工序的集中和分散,工序顺序的安排,定位基准的选择,零件表面加工方法的选择); 制定工艺路线(工艺方案,工艺方案的比较与分析),工序间尺、公差、表面粗糙度及毛坯尺寸的确定,加工余量、切削用量、工时定额的确定,填写工艺文件。夹具设计必须满足的要求有:保证加工精度,夹具的总体方案应与年生产纲领相适应,安全、方便、减轻劳动强度,排屑顺畅,具有良好的强度、刚度和结构工艺性。夹具设计包括工件的定位,定位误差的分析与计算,夹紧机构的确定,夹具力的确定(包括方向,作用点和大小)。
关键词:工艺规程设计;夹具设计;加工余量;定位误差
目 录
摘 要III
AbstractIV
目 录V
1 绪论1
1.1 本课题研究的内容及意义1
1.2 国内外发展情况1
1.3 本课题应达到的要求2
2 工艺方案的确定3
2.1 曲轴零件的结构特点3
2.2 曲轴零件的技术要求3
3 零件工艺分析4
3.1 根据零件图和产品装配图,对零件进行工艺分析4
3.2 计算零件的生产纲领,确定生产类型4
4 毛坯选择和毛坯图说明5
4.1 毛坯技术分析5
4.2 确定毛坯种类和制造方法5
4.3 确定毛坯总余量5
5 工艺设计过程6
5.1 加工阶段的划分6
5.2 工序的集中与分散6
5.3 工序顺序的安排6
5.4 定位基准的选择6
5.5 零件的表面加工方法的选择6
6 制定工艺路线7
6.1 工艺路线方案一7
6.2 工艺路线方案二7
6.3 工艺方案的比较与分析8
7 工序间尺寸、公差、表面粗糙度及毛坯尺寸的确定9
8 加工余量,切削用量,工时定额的确定10
8.1 工序一:铣两端面,打中心孔10
8.1.1 工步一:铣两端面10
8.1.2 工步二:两端面打中心孔10
8.2 工序二:粗车大端主轴颈及平衡块外轮廓11
8.2.1 工步一:粗车大端Φ40主轴颈外圆面及轴肩11
8.2.2 工步二:车平衡块Φ174外轮廓11
8.3 工序三:粗车小端外轮廓12
8.3.1 工步一:粗车小端Φ40主轴颈外圆面及轴肩12
8.4 工序四:半精车大端主轴颈及倒角12
8.4.1 工步一:半精车大端Φ40主轴颈外圆面及轴肩12
8.5 工序五:精车大端主轴颈及倒角13
8.5.1 工步一:精车大端Φ40主轴颈外圆面及轴肩13
8.5.2 工步二:精车大端主轴颈上1×45°倒角14
8.6 工序六:半精车Φ40外圆面及轴肩锥面、小端锥面14
8.6.1 工步一:半精车小端Φ40主轴颈外圆面及轴肩14
8.6.2 工步二:倒Φ40主轴颈上角15
8.7 工序七:铣键槽15
8.7.1 工步一:铣键槽15
8.8 工序八:精车Φ40外圆面及轴肩锥、小端锥面16
8.9 工序九:粗车连杆轴颈及其轴肩17
8.9.1 工步一:粗车连杆轴颈及其轴肩17
8.10 工序十:半精车连杆轴颈及其轴肩17
8.10.1 工步一:半精车连杆轴颈及其轴肩17
8.11 工序十一:精车连杆轴颈及其轴肩18
8.11.1工步一:精车连杆轴颈及其轴肩18
8.12 工序十二:打通孔及打M12螺纹孔并攻丝18
8.12.1 工步一: 打通孔18
8.13 工序十三:主轴颈、连杆轴颈淬火19
8.14工序十四:磨连杆轴颈外圆及其轴肩面19
8.15工序十五:磨大端主轴颈及其轴肩面20
8.15.1工步一:磨大端主轴颈及其轴肩面20
8.16工序十六:磨小端主轴颈及其轴肩面20
8.16.1工步一:磨小端主轴颈及其轴肩面20
8.17工序十七:去毛刺21
8.18工序十八:检验21
9 专用夹具设计22
9.1 机床夹具设计概述22
9.1.1 机床夹具概述22
9.1.2 机床夹具的分类22
9.1.3 机床夹具的组成和功用22
9.1.4 夹具总体方案设计23
9.2 夹具设计24
9.2.1 问题的提出24
9.2.2 定位方式与定位基准的选择24
9.2.3 夹具机构设计24
9.2.4 定位销长度的分析26
9.2.5 定位误差的分析与计算26
10 结论与展望32
10.1 结论32
10.2 不足之处与未来展望32
致 谢33
参考文献34
1 绪论
1.1 本课题研究的内容及意义
本课题研究的内容是:空压机曲轴工艺规程设计和系列夹具设计,包括零件机械加工的工艺过程卡片及各工序的工序卡片,主要机械加工工序的夹具总装配图及主要零件图,并有相关的计算和说明的说明书及专业外语文献翻译。
本课题研究的意义:
⑴工艺规程设计的意义:
1)指导生产的主要技术文件是工艺规程:机械加工车间生产的计划、调度,工人的操作,零件的加工质量检验,加工成本的核算,都是以工艺规程为依据的。处理生产中的问题,也常以工艺规程作为共同依据。如处理质量事故,应按工艺规程来确定各有关单位、人员的责任。
2)生产准备工作的主要依据是工艺规程:车间要生产新零件时,首先要制订该零件的机械加工工艺规程,再根据工艺规程进行生产准备。如:新零件加工工艺中的关键工序的分析研究;准备所需的刀、夹、量具(外购或自行制造);原材料及毛坯的采购或制造;新设备的购置或旧设备改装等,均必须根据工艺来进行。
3)新建机械制造厂(车间)的基本技术文件是工艺规程:新建(改、扩建)批量或大批量机械加工车间(工段)时,应按照在车间的布置和工艺规程确定所需机床的种类和数量,再由此确定车间的面积大小、动力和吊装设备配置以及所需技术等级、工人的工种、数量等。
此外,先进的工艺规程还起着交流和推广先进制造技术的作用。典型工艺规程可以缩短工厂摸索和试制的过程。因此,工艺规程的制订是对于工厂的生产和发展起到非常重要的作用,是工厂的基本技术文件。
⑵夹具设计的意义:
机床夹具是机械制造业中不可或缺的重要工业装备,可以保证机械加工质量、实现生产过程自动化、降低生产成本、提高生产效率、减轻劳动强度,使用专用夹具还可以改变原机床的用途和扩大机床的使用范围,实现一机多能,所以,夹具在机械加工中发挥着重要的作用。
1.2 国内外发展情况
曲轴制造技术/工艺的进展:曲轴的生产继QT800-2、QT900-2等几种牌号后,广西玉柴等经过攻关已能稳定生产QT800-6牌号的曲轴,为曲轴“以铁代钢”奠定了基础。
1 熔炼 高温低硫纯净铁水的获得是生产高质量球墨铸铁的关键。国内主要是以冲天炉为主的生产设备,铁水未进行预脱硫处理;其次是高纯生铁少、焦炭质量差。目前已采用双联外加预脱硫的熔炼方法,采用冲天炉熔化铁水,经炉外脱硫,然后在感应电炉中升温并调整成分。
2 造型 目前,国内已有一些曲轴生产厂家从日本、法国、加拿大等国引进气流冲击造型工艺,而且还引进了许多生产线的只有极少数厂家,如文登天润曲轴有限公司引进了德国KW铸造生产线。从总体上来讲,需改造和更新的陈旧的普通锻造设备多,同时,2 工艺方案的确定
2.1 曲轴零件的结构特点
曲轴类大部分的零件的主要作用用为承载载荷、支撑传动的零件和以及保证安装在曲轴上的零件(刀具)具有一定的回转精度空间。
曲轴在轴类零件的地位普通的属于异型轴,是空压机上以及其他机器的一个不可缺少的零件部分,能够承载多部分零件传输过来的力,并将活塞往复运动通过曲柄连杆机构变为旋转运动,将许多零件所做的有用功全输出去。曲轴在工作时所承受的是很大的扭转力矩以及大小和方向都有变化的弯曲力。
2.2 曲轴零件的技术要求
材质,金相组织,机械性能和表面缺陷均应符合 ZBJ72016~88 《 容积式压缩机用球墨铸铁技术条件》的规定。
铸件应经热处理,热处理后硬度为 HB190~269 。
加工后主轴径,曲拐径及圆弧过渡处均不允许有肉眼可见的毛刺,裂纹,折叠,凹痕,缩松,缩孔,夹杂物等缺陷存在。
圆弧过渡应均匀,光滑,无接痕。
曲轴加工后应探伤,其要求应符合 ZBJ72016-88 《 容积式压缩机用球墨铸铁技术条件》的规定。
锥面应进行着色检查,其接触面积不少于75%。
未铸造圆角R3—R5,保留中心孔。
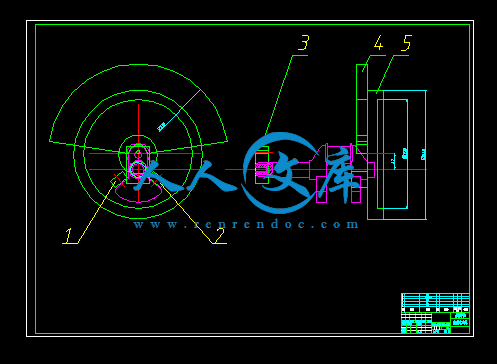
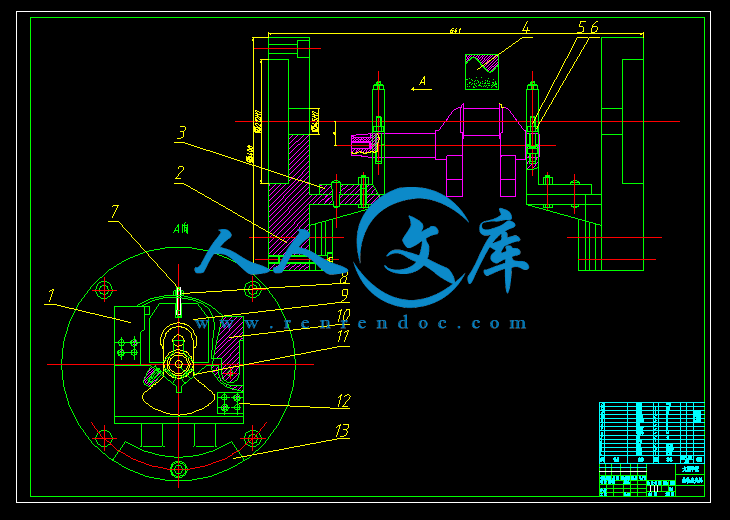
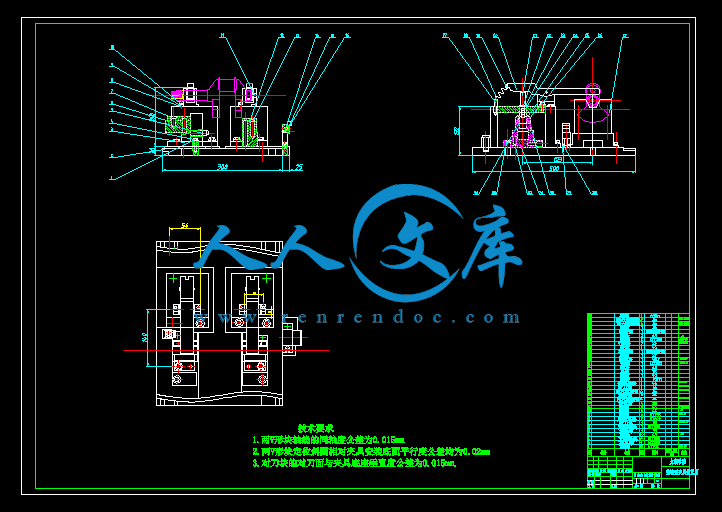