人人文库网 > 图纸下载 > 毕业设计 > 液压挖掘机正铲工作装置仿真设计[含三维PROE]【全套9张CAD图纸和WORD毕业论文】
英文翻译2A model of the working operatiors of a quarry excavator.pdf
液压挖掘机正铲工作装置仿真设计[含三维PROE]【全套9张CAD图纸和WORD毕业论文】
收藏
资源目录
压缩包内文档预览:
编号:324257
类型:共享资源
大小:5MB
格式:RAR
上传时间:2014-09-22
上传人:好资料QQ****51605
认证信息
个人认证
孙**(实名认证)
江苏
IP属地:江苏
50
积分
- 关 键 词:
-
液压
挖掘机
工作
装置
仿真
设计
全套
cad
图纸
word
毕业论文
- 资源描述:
-
【温馨提示】 购买原稿文件请充值后自助下载。
[全部文件] 那张截图中的文件为本资料所有内容,下载后即可获得。
预览截图请勿抄袭,原稿文件完整清晰,无水印,可编辑。
有疑问可以咨询QQ:414951605或1304139763
目录
1 前言 (1)
1.1课题研究的背景和意义 (1)
1.2 液压挖掘机研究现状及发展动态 (1)
1.2.1 国外的研究现状及发展动态 (2)
1.2.2 国内的研究现状及发展动态 (3)
1.3 本文研究的主要内容 (5)
2液压正铲挖掘机工作装置的运动分析 (6)
2.1 液压正铲挖掘机的基本组成和工作原理 (6)
2.2 工作装置结构方案的确定 (7)
2.3 工作装置运动分析 (10)
2.3.1动臂运动分析 (10)
2.3.2斗杆运动分析 (12)
2.3.3斗齿尖的几种特殊工作位置的计算 (13)
3 工作装置尺寸的设计确定 (17)
3.1应用举例 (17)
3.1.2动臂及斗杆长度确定 …………………………………………………(17)
3.1.2机构转角范围确定 (18)
3.2 油缸铰点及行程确定 (19)
3.2.1动臂油缸的铰点及行程确定 (19)
3.2.2 斗杆油缸铰点及行程确定 (19)
3.2.3 铲斗油缸铰点及行程确定 (19)
3.3工作装置的位置模型建立 (19)
3.3.1 动臂与平台铰点位置C的确定 (20)
3.3.2 动臂及斗杆长度的确定 (20)
3.3.3 机构转角范围确定 (20)
3.4工作装置油缸铰点及行程确定 (25)
3.4.1动臂油缸的铰点及行程确定 (25)
3.4.2斗杆油缸铰点及行程确定 (28)
3.4.3铲斗油缸铰点及行程确定 (31)
3.5液压正铲挖掘机三维模型 (32)
4 结论 (34)
参考文献 (35)
致谢 (36)
1 引言
1.1课题研究的背景和意义
目前我国露天矿的开采规模逐渐扩大,为了适应日益增大的矿用汽车铲装的需要,这就需要较大斗容的挖掘机,由于挖掘机愈大,每单位土石方的施工成本愈低,而液压挖掘机较机械式挖掘机有很多优点,但是国内对大型液压正铲挖掘机的研究较少,液压挖掘机工作装置是完成挖掘机各项功能的主要构件,其结构的合理性直接影响到挖掘机的工作性能和可靠性,对其研究是整机开发的基础,对工作装置进行优化,目的在于缩短研究和开发周期,降低产品成本,提高设计质量,本课题的任务就在于此。
现代化建设速度,在很大程度上取决于各种工程建设速度,而工程机械水平的高低,又直接对工程建设速度发挥着促进或抑制作用。传统研发管理及设计方法只是被动地重复分析产品的性能,而不是主动地设计产品的参数。作为一项设计,不仅要求方案可行、合理,而且应该是某些指标达到最优的理想方案。随着电子计算机的应用,在机械设计领域内,已经可以用现代化的设计方法和手段进行设计,来满足对机械产品提出的要求。利用优化设计方法,人们就可以从众多的设计方案中寻找出最佳设计方案,从而大大提高设计效率和质量。可靠性是我国工程机械的致命弱点,我们要正视差距,增强科研开发力度,提高技术水平,更多地发展具有自主知识产权的高质量产品,进一步促进工程机械的发展。
1.2 液压挖掘机研究现状及发展动态
挖掘机作为一种典型的土石方施工设备,在基础设施建设中起着十分重要的作用,因此加强对挖掘机的研究具有十分重要的意义,随着能源的紧缺和人们对环保意识的增强,节能技术研究成为同行学者关注的焦点没随着人类空间获活动的延伸,以及人类对挖掘机工作环境与功能要求的延伸,在遥控挖掘机和机器人化挖掘机研究方面正进行不懈努力,遥控挖掘机的研究离实用化已经不远,开发智能化的多功能挖掘机并使之成为真正的挖掘机器人还是人们追求的目标。由于挖掘作业中负载变化剧烈,有些学者已经开始将振动挖掘方式运用于减少挖掘阻力,减低功率消耗以及延长机器使用寿命方面的研究。近年来,随着人类对自然的开发,挖掘机也朝着大型化大功率化发展,从而满足人类对大型工程的需求。
1.2.1 国外的研究现状及发展动态
1)国外产品发展趋势
1950 年在意大利生产了第一台液压挖掘机,由于其挖掘能力强、生产率高、通用性好、操纵轻便等特点,在工程建设施工中起着重要的作用。六十年代,随着西方经济的发展,液压挖掘机需求数量急剧上升,但大多数属于中小型液压挖掘机。七十年代开始,随着科学技术的进步和大型水电工程及大型露天矿建设的需要,液压挖掘机向高速、高压、大斗容、大功率发展。随着液压挖掘机产量的提高和使用范围的扩大,世界上著名的挖掘机生产商纷纷采用各种高新技术,来提高产品的竞争力。国外的一些公司开始研制大型矿用液压挖掘机,其中以德国、法国产品居多。
在液压挖掘机产品功能方面,液压挖掘机工作装置向多功能化的方向发展。当液压挖掘机配置不同的作业装置时,可以用来吊、夹、推、刮、松、挖、装、铣削、拆除、清除和压实等作业,且大都采用快换装置,驾驶员在驾驶室内就可以完成作业装置的更换,一般在2分钟内就可以完成作业装置的更换。工作装置中动臂、斗杆结构变化多样,扩展了主机的使用功能。随着传统型和通用型产品样机减少,一些有特殊构造的、有特色的产品和多功能的产品备受用户的青睐,这些多用途作业装置大大扩展了液压挖掘机的功用,提高了产品的施工适用性。同时也体现了各厂家市场差异化的产品发展战略和各自的技术水平。所以,研究专业性的挖掘机设计理论、方法甚至是专用软件,以便缩短设计周期、提高产品性能和可靠性,快速响应市场和用户的要求。
2)国外液压挖掘机设计方法研究现状
(1)设计理论和方法研究及应用。国外生产企业在产品的设计和研制过程中,广泛推广采用有限寿命设计理论,以替代传统的无限寿命设计理论和方法,并将疲劳
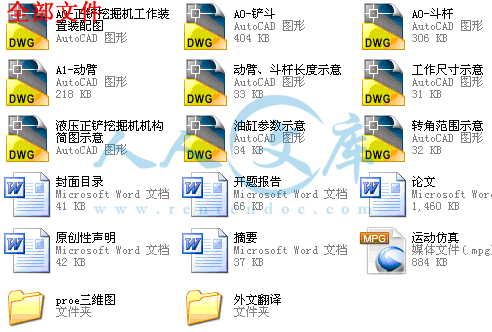
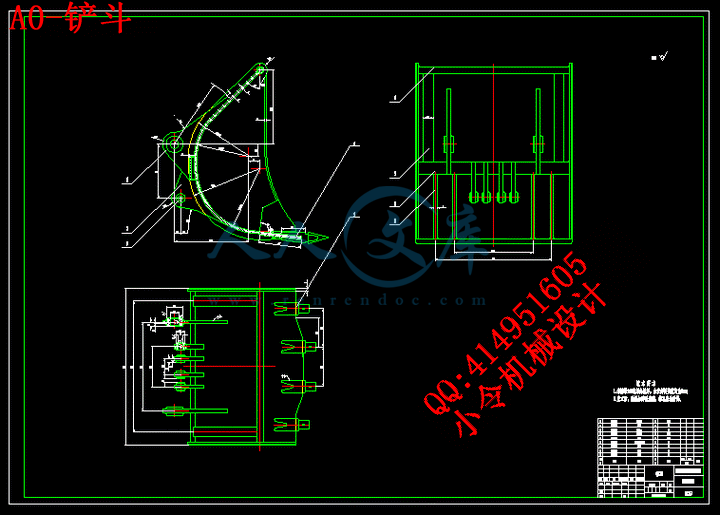

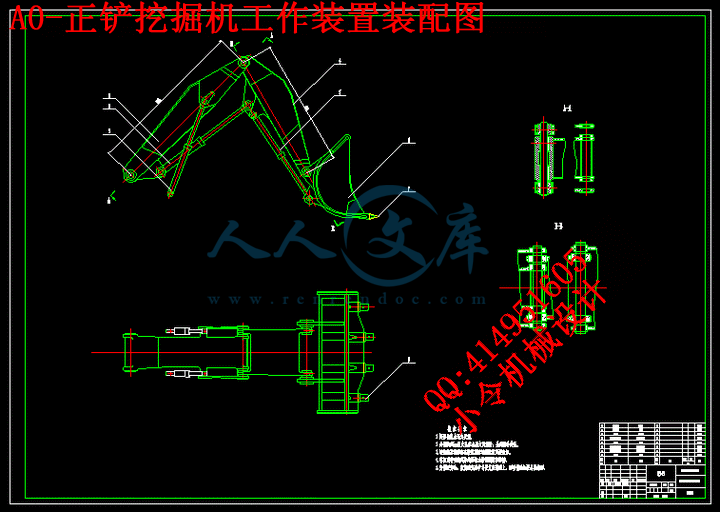
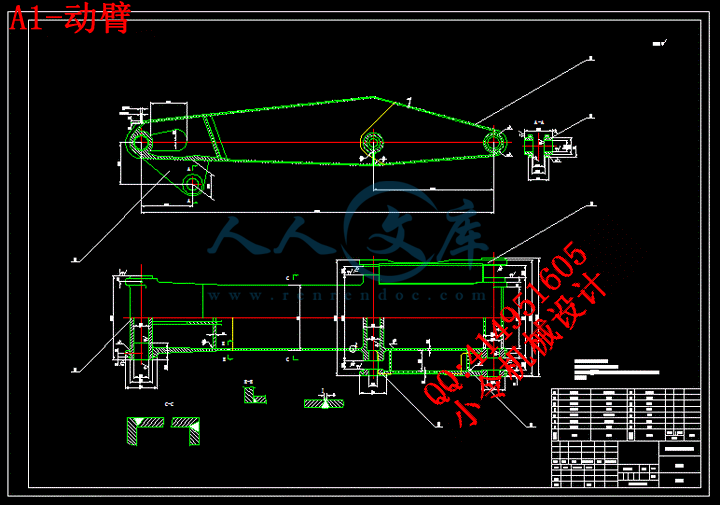
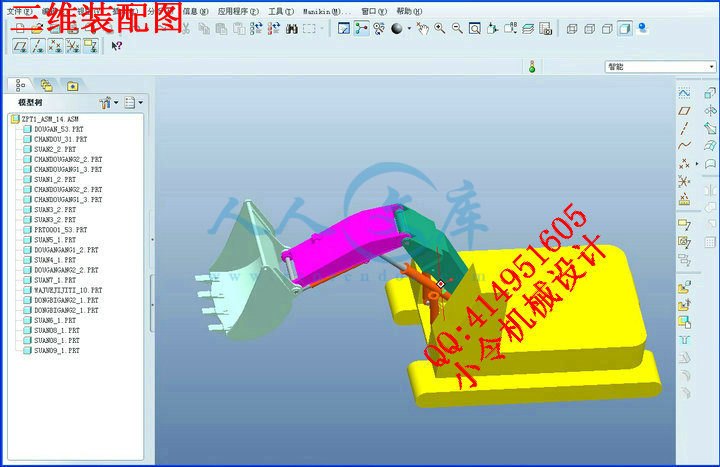
- 内容简介:
-
MECHANIZATION AND AUTOMATION OF MINING OPERATIONS A MODEL OF THE WORKING OPERATIONS OF A QUARRY EXCAVATOR E. V. Gaisler, A. P. Mattis, E. A. Mochalov, and S. V. Shishaev We develop a methematical model of the process of open-pit mining with a quarry ex- cavator using a bucket that has active blades driven by impact blocks installed in the front wall. The bucket operates as follows. When the bucket comes in contact with a rock area that can be broken by a force greater than the sum of the forces of friction of the tool on the sleeve and the force of activation of the starting device, the impact blocks are energized. The action of these blocks causes the bucket blades to enter the rock to a depth X, weakening the zone located directly under the blades and forming the so-called disrupted bonding zone i. This zone requires much less force to be broken than an in- tact mass. With such active buckets, strong rocks can be excavated without preloosening. The main parameters describing the movements of the bucket during excavation include the mechanical properties of the rock, the variation of these properties under the effect of the impact, the working characteristics of the drives of the actuator mechanisms, and the parameters of the equipment. Two types of destruction take place during the course of excavation: cutting and impact breaking. The geometric sum of forces acting on all the faces of a blade represents the resist- ance to intrusion. The projection of this sum onto the axis of the impact block is Pl; the projection onto the direction perpendicular to the axis is P2. The sum of forces act- ing perpendicularly to the bucket-traveling plane is equal to zero because block fracturing is mainly performed. The following assumptions are made for a mathematical model describing the motions of the bucket: ? - the center of mass of the rock in the bucket is stationary relative to the bucket; - chips are separated continuously; - the loads on the bucket blades are equal; - the blades penetrate the rock instantaneously upon impact; -the resistance to the bucket-filling is disregarded; - the moment of friction relative to the rotation axis of the arm is disregarded. With these assumptions, the motion of the bucket can be interpreted as the motion of a two-dimensional mechanism under the effect of external forces, which includes the force developed by the drives of the pressure mechanism and the lift mechanism, the gravity force, and the resistance force of the rock face. The position of the bucket at each point in time is defined by the coordinate r(t), the distance (OC), and (t) - the angle between the boom and the bucket stick. The kinetic energy of this mechanism is expressed as = ( + m) ,- + JT (1) where m 1 is the rock mass and the bucket; m 2 is the mass of the stick and the empty bucket; J is the moment of inertia of the bucket with rock and the stick relative to its rotation axis Institute of Mining, Siberian Branch, Academy of Sciences of the USSR, Novosibirsk. Trans- lated from Fiziko-Tekhnicheskie Problemy Razrabotki Po!eznykh Iskopaemykh, No. 2, pp. 60-67, March-April, 1991. Original article .submitted September 25, 1990. 0038-5581/91/2702-0131512.50 ?9 1992 Plenum Publishing Corporation 131 Y = ml (r + lCBii)+ J + mi(r- rl) 2 + IGA), (2) where J1 is the moment of inertia of an empty bucket and the stick relative to the center of mass and r - rl is the coordinate of the center of mass of the empty bucket with the stick. The rock mass in the bucket m depends on the path traveled by the front edge of the bucket and the initial shape of the rock face. In order to write an expression for the rate of mass increment, we will consider the scheme in Fig. 2. Suppose that the path traveled by the bucket edge by the time t is described by the curve f2(r2, 2) The ini- tial shape of the face by the curve f3(r3, 3), where r2, , r3, 3 are polar coordinates with the origin at zero. During the time dt the bucket edge travels a distance ICDI; in that case, since d 2 = d 3 the mass increment within the time dt is specified by I dm = T ,B (I OC l I OD I -I OA . I OB I) sin da 2, where 0 is the rock density and B is the width of the bucket edge. We see from the diagram that loci = r, ION = r= dr, IOAI = r, IOBI = r dr3. Considering that sinda da 2 and disregarding the squares of the infinitesimal variables, we write 1 a, = r,z (, - d) a. The increment d 2 is equal to the product at the angular speed of the stick at the time t and the increment dt, i.e., d 2 = da 3 = &dt. The rate of increment of the mass is now ex- pressed as dNl o , = .-7- = _ ,i (d - ,.:,) =. (3) The mass falling into the bucket during the time t is defined by ! m, = J s ()dT 0 This mass m I is only a function of the time t. Making use of the fundamental equation of the dynamics of a variable-mass point (Mesh- cherskiis equation), we can demonstrate that Lagrangian equations are applicable to the mechanical system that consists of variable-mass material points if the absolute velocity of the associated mass is equal to zero. Consider a mechanical system comprised of n material points with masses ml, m 2 . m i, ., m n, that move with velocities v i. Lagrangian equations for m i = const have been derived in 2, p. 340. Consider the case of m i = mi(t). In following 2, we introduce generalized coordinates q, such that i = ri(ql, q2, , qs, t), where r i is the position vector of the ith mass. Now, i = )1 )j, Oli Oi j I uqj Uqj Oq) where j is generalized velocity. The kinetic energy of the mechanical system at any time point is defined as 1 - T ?niViU i . We find partial derivatives of kinetic energy with respect to the generalized coordinate qj and the generalized velocity j: or = - oi aqj miUi -r- , i=l aqi 132 _ ih, i - Or i OT mivl mivi Oqj = i=1 Oqj i= Oqj We differentiate this expression with respect to time . Consider now the first sum, taking into account the fundamental equation of the dynamics of variable-mass point for the case where the absolute velocity of the associated mass is equal to zero 2, p. 143 , am v =F, m.-7 + - where P is the resultant of the forces applied to the point. For a nonfree material point with variable mass, we have elT, i dm - m l -77 + -d-f vi = F., + 7 , where Ri is the resultant of the reactions of constraints applied to the ith point. Now, 7, + m, - . , + 7, + 7, - , = i=1 S - - . Or i = (F+n)=Q+&. i=l The second sum is, in fact, 8T/Sqj 2, p. 342. We obtain dt = Qj + o + OT Oq) For a system with stationary perfect constraints QjR = 0 d OT 07 It is the Lagrangian equation for a mechanical system consisting of variable-mass material points under the assumption that the absolute velocity of the associated mass is equal to zero. As we see, it is identical to a Lagrangian equation derived for a constant mass of material points belonging to the mechanical system. The Lagrangian motion equations for this mechanism are r - u-7- = QJ 7 , ,A , - = Q (5) where QI, Q2 are generalized forces acting on displacements 6r and 6, respectively, l Q, = - , o, ( - /- ,-o., / o - + :,- ,.o I + + (m + m).gcos(- ), O, = l).r.sin(-OCD) r + I CDI/ ) .P.sin cos (n - OCD) / (6) 133 Fig. 1 Fig. i. Fig. 2. C D Fig. 2 Design scheme for an excavator with an active bucket. Evaluation of the increment of rock weight in the bucket. 12(t). t + P3, (10) where U is the coefficient of friction of the tool in the bucket sleeve Pa as the force of activation of the automatic starting device. The stroke is made at the time l= 11+ Tl+ T2, where T l is the actuation time of the device and T 2 is the impact cycle time. Upon impact, blades penetrate the rock to a length which is a function of the rock properties, the blade geometry, and the impact energy. Studies in situ and laboratory experiments measuring the penetration of the blade upon impact, conducted by the Institute of Mining, the iInstitute of Construction Machines, the Skochinski Institute, and the Karaganda Polytechnic 4-6, suggest the existence of some characteristic of the bed being fractured which can be used to assess the fracturing efficacy. For such a characteristic the specific energ 7 capacity of fracturing can be used and measured per a unit of strength of the bed, e.g., the rocks ultimate uniaxial compressive strength, i.e., i A.K E, = .,./,.% 2.78t(I -, (11) where A is the single-impact energy, J; K 0 is the transfer coefficient of the impact energy to the bed; x is the penetration of the blade in one stroke, m; F is the transverse cross sectional area of the fracturing track m2; and o 0 is the ultimate uniaxial compressive strength of the rock, kN/m 2. The value of E 0 depends on the mechanical properties of the bed and its condition. The range of specific destructive energy capacity per stroke in certain permafrost grounds with a tool shaped as a symmetric wedge, measured by a single stroke of the density gauge devised by the Road Construction Research Institute, is indicated in Table i. The pene- tration of a blade can be defined by A.K.2.78.10-7 E,I ?9 I:. % :33.3 Besides, E 0 can be measured experimentally or estimated from the data reported in 7-9. After the impact, the movement of the bucket is described again by Eqs. (2) and (8), but with the condition P = 0, P2 = 0, until the front edge of the bucket travels the dis- tance x. 135 g, deg 4 5 , sec Fig. 3. Bucket stick rotation angle vs. time (i - digging without adjust- ment for C weakening after impact, 2, 3 - linear and quadratic weakening of C, respectively; 4 - experimental data; i-3 - rock (f = 5; C l = 30 x 106 H/m2; = 0.5), 4 - siltstone f = 5-6, C I = (32-36)106 N/m2; = 0.5. The condition for transition to mode 3 in time appears as 2 2 1 2 (t) + r2 (l) - 2 .r, (4).r (/:). cos ( (l) - (t) x . ( 12 ) After (12) is satisfied, cutting in mode 3 begins. The rock resistance to destruction is generally described by the familiar expression = o.tgp+ C, (13) where o is normal pressure, 0 is the internal friction angle, and C is the rock cohesion. The Mohr-Coulomb criterion can be formulated as a function of principal stresses under destructive load i0: o, = o0+ 03 ?9 tg2(5 + p/2), (14) where o I is the largest principal stress corresponding to the maximum of the stress-strain curve. Expressing o I and o 2 in terms of T and o and solving simultaneously Eqs. (13) and (14), we obtain an expression of the uniaxial compressive ultimate strength o 0 as a function of cohesion C: Oo= 2 .C .tg(45+ 0/2). Expression (15) shows that the main characteristic of the alteration of rock properties after impact is a drop in cohesion. The cohesion in the bed is defined as (15) C = C,l, (16) where C I is rock cohesion in a lump; 11 is the structural weakening coefficient of the bed, which is a function of the average lump size, the main crack network, and the direction of the mine advance 8. After the impact, the cohesion C(t3) = C.2, where 12 is a coefficient representing additional weakening of the bed by impact loads. At the load application point, the material is crushed. According to Popov 7, k2 after the impact is reduced to 0.0005. As the blade moves through the disrupted bonding zone, the value rises to its initial level according to a certain pattern (studying the behavior of C = f(x) is a separate subject). In a first approximation, the size of the zone and the cohesion value can be estimated from the results of 7-9. The movement of the bucket in the disrupted bonding zone is described by (2)-(10), plus additional con- straints imposed on C (the rock cohesion). With increasing C, the values of Pl and P2 grow. The further movement of the bucket follows mode 1 or 2, depending on whether con- dition (i0) is met. 136 Equations (2)-(8) hold for all the modes of bucket movement, with the respective con- straints imposed on P1, P2, and C. Transitions between the modes occur depending on whether conditions (9) and (i0) are satisfied. A mathematical model composed of (4), (6), and (8), which describes the working process of an excavator with an active bucket, consists of a set of nonlinear differential equations. A modified Merson algorithm with an automatic step selection and accuracy control was used to solve this sytem. The model has been programmed for a computer in an interactive mode. In the course of solution, the trajectory of the bucket can be adjusted by selecting load characteristics of the drives of lift and pressure mechanisms, i.e., by choosing the appropriate functions fl(), f2(, &), which correspond to the actual process of excavator control. Several alternatives were computed to evaluate this model. The results are illustrated by solid plots in Fig. 3. In the first situation, the fracturing is caused entirely by impact loads. The energy of a single stroke is insufficient to create a disrupted bonding zone (curve i). The other two cases are characterized by different forms of weakening of cohesion in the dis- rupted bonding zone (2, linear weakening; 3, quadratic weakening). The modeling results were compared with the data of in situ experiments on siltstone in the Krasnogorsk section of Kemerovougol Enterprises (dashed line in Fig. 3). A qualitative similarity was observed between the model and the actual process (the data discrepancy did not exceed 30%). The smallest discrepancy was observed with the linear cohesion weakening in the disrupted bond zone. With his mathematical model one can investigate the parameters of the working process in various !excavation conditions for design of these machines to meet specific technical and economic characteristics and mining objectives. LITERATURE CITED i. A. I. Fedulov and V. N. Labutin, Impact Coal Destruction in Russianl, Nauka, Novo- sibirsk (1
- 温馨提示:
1: 本站所有资源如无特殊说明,都需要本地电脑安装OFFICE2007和PDF阅读器。图纸软件为CAD,CAXA,PROE,UG,SolidWorks等.压缩文件请下载最新的WinRAR软件解压。
2: 本站的文档不包含任何第三方提供的附件图纸等,如果需要附件,请联系上传者。文件的所有权益归上传用户所有。
3.本站RAR压缩包中若带图纸,网页内容里面会有图纸预览,若没有图纸预览就没有图纸。
4. 未经权益所有人同意不得将文件中的内容挪作商业或盈利用途。
5. 人人文库网仅提供信息存储空间,仅对用户上传内容的表现方式做保护处理,对用户上传分享的文档内容本身不做任何修改或编辑,并不能对任何下载内容负责。
6. 下载文件中如有侵权或不适当内容,请与我们联系,我们立即纠正。
7. 本站不保证下载资源的准确性、安全性和完整性, 同时也不承担用户因使用这些下载资源对自己和他人造成任何形式的伤害或损失。

人人文库网所有资源均是用户自行上传分享,仅供网友学习交流,未经上传用户书面授权,请勿作他用。
2:不支持迅雷下载,请使用浏览器下载
3:不支持QQ浏览器下载,请用其他浏览器
4:下载后的文档和图纸-无水印
5:文档经过压缩,下载后原文更清晰
|