【温馨提示】 购买原稿文件请充值后自助下载。
[全部文件] 那张截图中的文件为本资料所有内容,下载后即可获得。
预览截图请勿抄袭,原稿文件完整清晰,无水印,可编辑。
有疑问可以咨询QQ:414951605或1304139763
毕业设计主要内容和要求:
完成一个基于PLC控制的带式输送机自动张紧装置的设计。输送机的输送能力为,输送煤的密度为,最大煤块尺寸为,运输距离为,提升高度为,输送机采用头尾双驱动。
具体要求如下:
1、要完成毕业设计图纸3张零号图纸;
2、按学校统一要求打印、装订设计说明书,说明书正文70页左右;
3、中英文摘要400字;
4、参考文献20篇左右。
院长签字: 指导教师签字:
中国矿业大学毕业设计指导教师评阅书
指导教师评语(①基础理论及基本技能的掌握;②独立解决实际问题的能力;③研究内容的理论依据和技术方法;④取得的主要成果及创新点;⑤工作态度及工作量;⑥总体评价及建议成绩;⑦存在问题;⑧是否同意答辩等):
摘 要
本设计主要是带式输送机全自动液压张紧装置的设计。它是在吸收国、内外输送机张紧技术的基础上,根据国内带式输送机的运行特点及要求研制的。它采用比例控制技术及可靠性较高的可编程控制技术,可以对张紧力进行多点控制,根据不同工作情况随时调节张紧力的大小。能最大程度的延长皮带的寿命,大大节约了成本。在设计中,用一个动滑轮使液压缸的行程减少了一半,避免使用行程较长的液压缸,减少了制造液压缸的难度。同时,系统中增加了若干个蓄能器,可以最大限度的吸收液压冲击,减小对皮带的冲击力提高胶带的使用寿命。
本设计在总结其它常规皮带张紧装置的基础上,设计了能够满足皮带机的皮带长度变化较大时的皮带拉紧装置。此装置在皮带机启动阶段,能提供足够大的启动张力;启动完毕后, 又可使皮带的张力恢复到额定值以维持皮带机的正常运行。本文根据液压自动张紧装置的液压原理,详细阐述了自动张紧装置的结构组成、控制原理及功能特点,并阐明了控制系统的设计关键在于压力值和最大拉力值的设定。
介绍了带式输送机运行系统要求,并运用PLC可编程控制技术对带式输送机的起动、制动和拉紧部分实时监控,完全实现了带式输送机自动控制运行方式,构成了一个高可靠性的设备运行控制系统。
关键词:带式输送机; 自动液压张紧装置; 自动控制; 可编程控制PLC
ABSTRACT
This design is mainly about full automatic hydraulic tension station for belt conveyer. It is designed on the foundation of opening technology in and outside, according to the domestic operation characteristic of belt conveyer and requirement. The equipment is also made on domestic belt-type conveyer movement characteristic and requestment. It uses the proportional control technology and the reliable higher programmable control technology, It may carry on the multi-spots control to strict the strength, adjusts pressing the strength size as necessary according to the different working condition.It can be the greatest degree lengthen the leather belt the life, greatly saved the cost. In the design, It causes the hydraulic cylinder with a movable pulley the stroke to reduce one half, and avoides using a stroke longer hydraulic cylinder.In this way,it reduces difficulty of the hydraulic cylinder’s produce. At the same time, it increases certain accumulators in the system, and limits absorption hydraulic pressure impact,which reduces the leather belt impulse and enhances the adhesive tape’s life.
In this issue ,the belt conveyer device whose tension force varied greatly is desiged to satisfy the re2 quirement s of the st ressed belt in varied length. It s tersion is greater in starting state ,and smaller in normal state moving. In the basis of working principle of automatic hydraulic tensioning device , st ructure composing , cont rol principle and function characteristics of the device were int roduced in this paper. It also expounded the design key of the cont rol system is to set pressure value and maxim drawing value.
Introduces requirement of belt conveyer operating system. PLC is utilized to monitor the drive , brake and tension part of belt conveyer in real time and to realize autocontrol operating mode completely, constructing a control system with super reliability for equipment operation.
Key words:Belt-type conveyer; full automatic hydraulic tension station; automatic control; programmable control
目 录
1 概述 1
1.1张紧装置的作用 1
1.2张紧装置的类型及其介绍 2
1.3液压张紧装置的基本介绍及其特点 2
1.3.1液压张紧装置的特点 2
1.3.2新型自动控制液压张紧装置的主要技术特点 3
1.3.3液压传动的特点 3
1.4带式输送机张紧装置的PLC控制系统介绍 4
1.4.1 PLC的介绍 4
1.4.2带式输送机张紧装置的控制原理 6
2 带式输送机的工作原理 9
2.1带式输送机的组成及工作原理 9
2.1.1带式输送机的组成 9
2.1.2带式输送机的工作原理 11
2.2带式输送机的驱动原理——摩擦传动原理 11
2.2.1单滚筒驱动情况 12
2.2.2多滚筒驱动情况 16
3 带式输送机的选型设计计算 21
3.1设计参数 21
3.2带式输送机的机型选择 21
3.3输送带的选择设计 21
3.3.1选取带速 21
3.3.2选择带宽 22
3.4运行阻力的计算 23
3.5输送带张力的计算 25
3.6校核 27
3.7张紧行程及张紧力的计算 28
3.7.1张紧行程 28
3.7.2张紧力 28
3.8机型布置 30
3.8.1布置原则 30
3.8.2布置形式 30
3.9滚筒的选择 31
3.10电机、减速器的选型及有关驱动装置部件的选用 33
3.10.2减速器的选型 33
3.10.3有关驱动装置部件的选用 35
4 带式输送机的起动分析 37
4.1带式输送机的起动曲线 37
4.2起动时的动张力计算 39
4.3起动时间 42
5 张紧装置选择方案 43
5.1张紧装置的类型 43
5.2方案比较与选择 44
6 张紧装置的设计 48
6.1张紧装置组成 48
6.2主要技术问题 49
6.3张紧装置参数的确定 49
6.3.1张紧力和张紧行程 50
6.3.2启动加速度 50
6.3.3起动时间 50
6.4液压站及有关元件的设计与选用 50
6.4.1液压油缸的设计 50
6.4.2齿轮泵及电机 54
6.4.3蓄能器 54
6.4.4液压油箱的设计 55
6.4.5电液比例溢流阀及其放大器 55
6.4.6电磁换向阀、单向阀 57
6.5机械结构设计 57
6.5.1张紧车架 57
6.5.2滑轮 58
6.6注意事项与要求 58
6.6.1张紧装置的振动 58
6.6.2设备使用要求 58
7 电控系统 59
7.1控制系统的硬件组成 59
7.1.1 PLC及扩展模块 59
7.1.2测速传感器 61
7.1.3压力变送器 62
7.1.4 PLC控制系统的硬件配置图 64
7.2软件设计 64
7.2.1思路及流程图 65
7.2.2输入输出点地址分配 65
7.2.3参数设定 65
7.2.4带式输送机张紧装置PLC程序 68
结 论 75
参考文献 76
英文原文 77
中文译文 99
致 谢 104
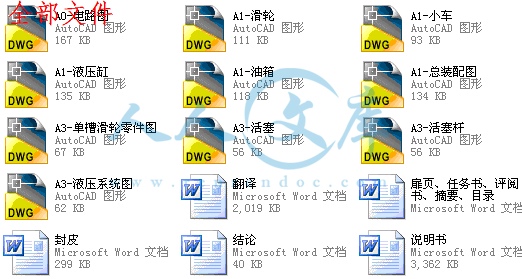




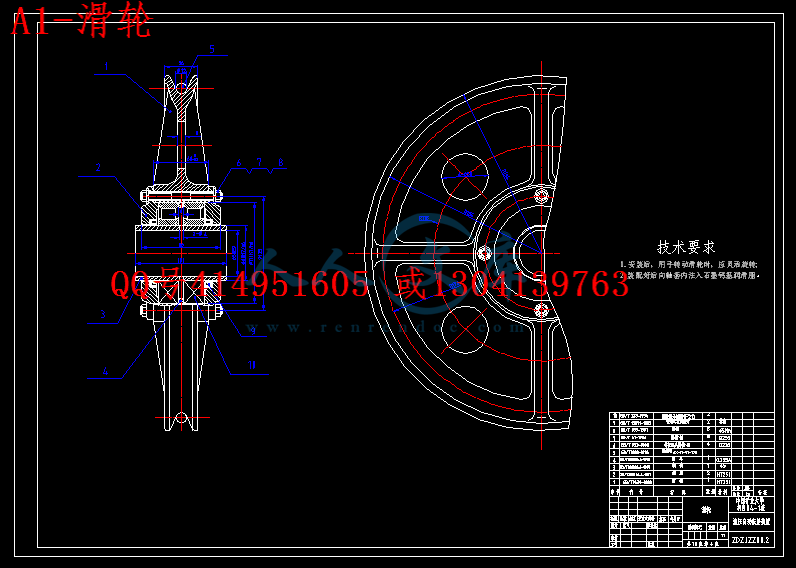
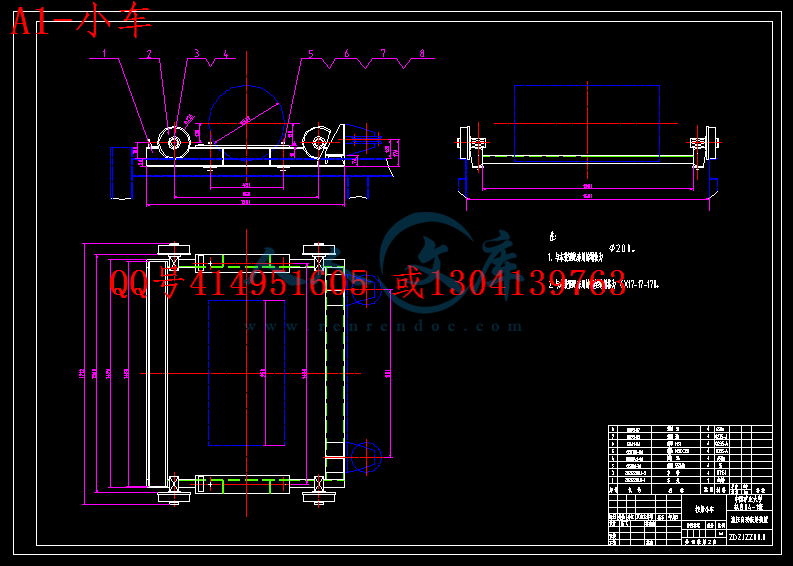
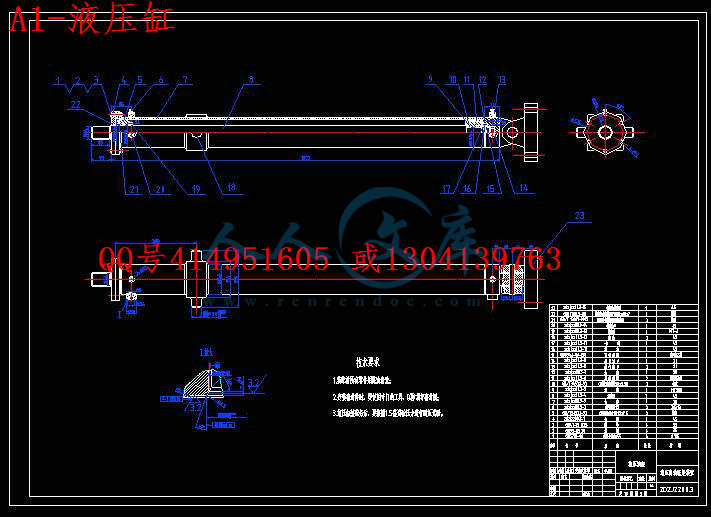
