电器外壳注塑模设计
51页 14000字数+说明书+任务书+开题报告+16张CAD图纸【详情如下】
中期检查表.doc
型芯1.dwg
型芯2.dwg
型芯底板.dwg
定模.dwg
电器外壳.dwg
电器外壳注塑模设计开题报告.doc
电器外壳注塑模设计说明书.doc
电器外壳装配图.dwg
表格.doc
设计任务书.doc
设计图纸16张.dwg
2011理科设计.doc
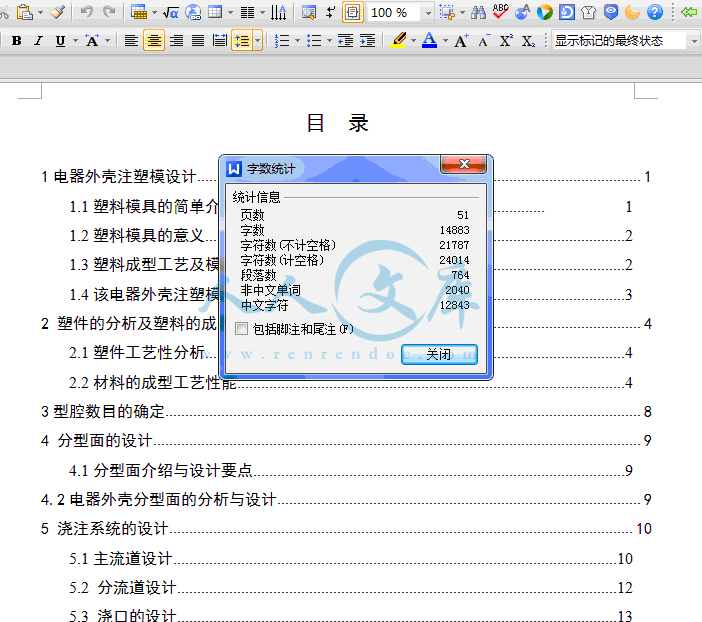
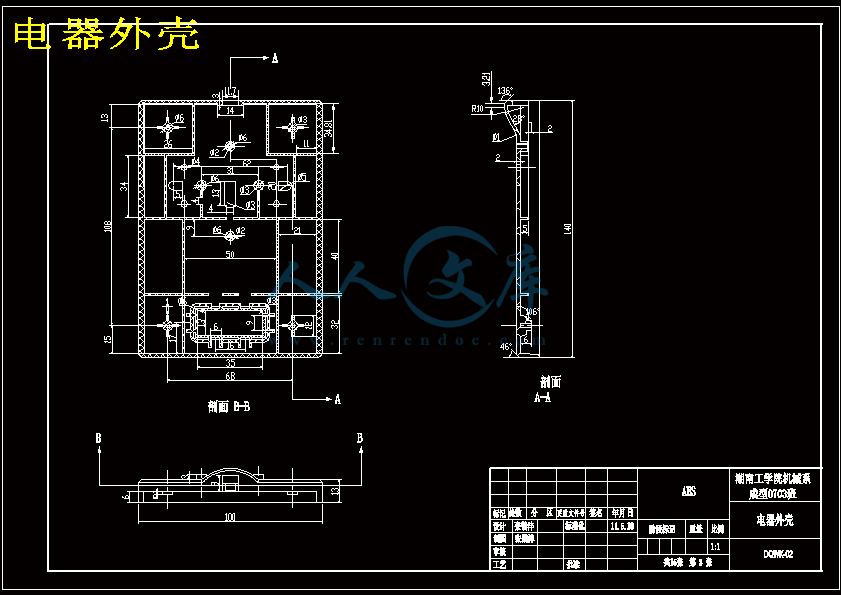



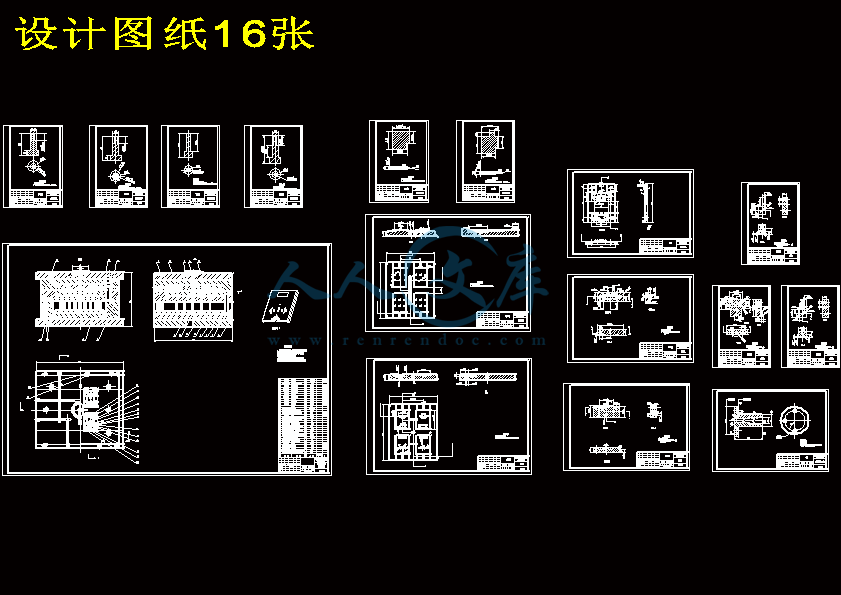
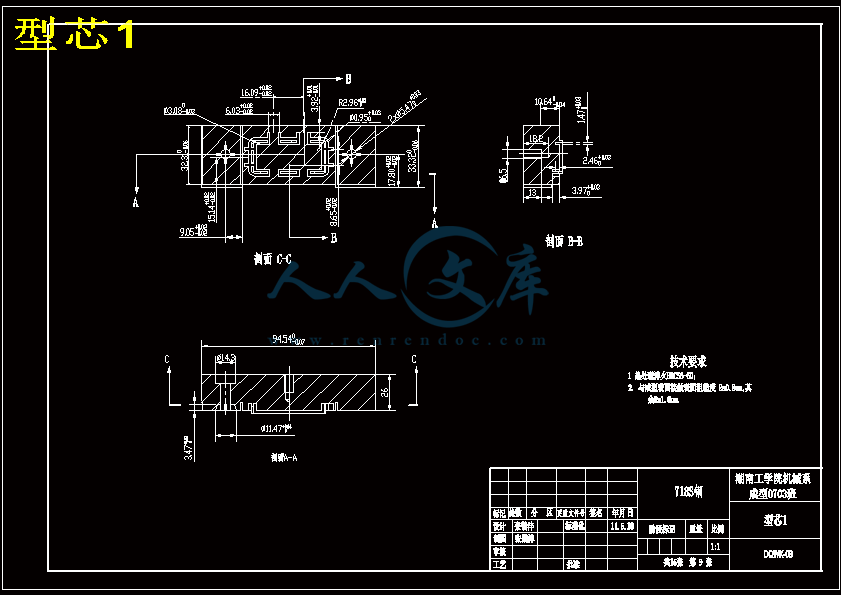
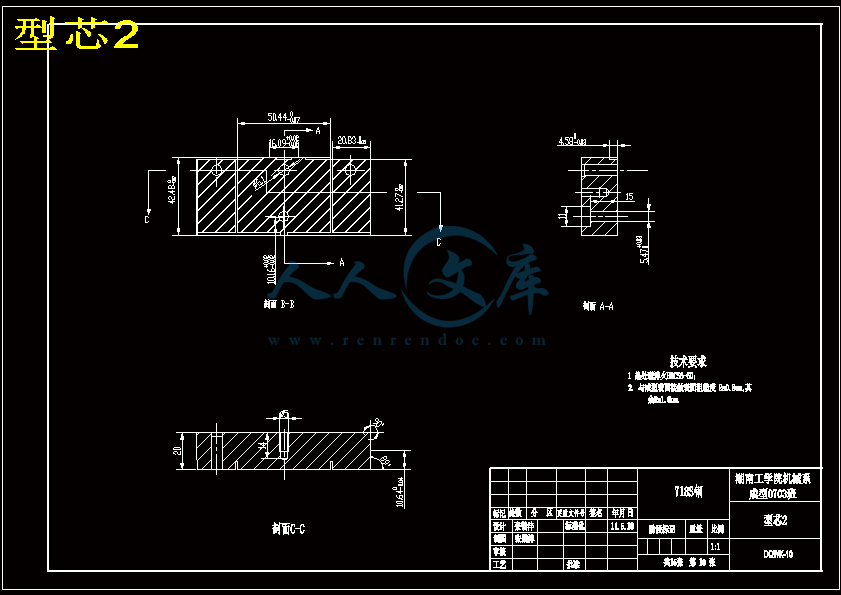

摘 要
如今,模具设计与制造是一种非常有前景的行业。中国模具企业一般都是中小型企业,模具加工技术相对发达国家还有很大的差距。学习模具专业的大学生,不仅仅要学习模具的先进技术,也要学习先进的模具管理技术。中国模具现在还极度缺乏高素质的人才,正是这个因素阻碍了中国模具质量的提升。
模具是制造业的重要工艺基础,在我国模具制造属于专用设备制造业.该篇论文是对一外壳塑件的模具设计。根据塑件的结构,选用了两侧带有斜顶机构的两板模,运用机动完成塑件的顶出,采用侧浇口完成进料。在整个设计过程中,查阅了大量的参考资料,深入分析设计内容,包括运用Proe软件对产品进行壁厚和拔模斜度的分析。塑件成型工艺性分析;拟定模具结构形式。
注射机型号的确定;浇注系统形式和浇口的设计;成型零件的结构设计和计算;模架的确定和标准件的选用;合模导向机构的设计;脱模推出机构的设计;斜顶机构的设计;冷却系统的设计。
通过该外壳塑料模具的设计使自己对塑料模具的设计流程有了更深一层次的认识,进一步体会到如 Proe, Moldflow,emx,Autocad等软件在模具各阶段设计过程中所扮演的角色和带来的便利,也深刻的体会到强大的CAD软件在缩短模具设计、生产周期、降低成本方面起了不可或缺的作用。虽然CAD设计软件拥有强大的分析处理功能,但也要有扎实的理论基础和实际经验才能将其发挥到极至。
关键词:拔模斜度;浇注系统;斜顶机构;合模导向机构
ABSTRACT
Nowdays , Mold design and manufacture is becoming a promising industry. The truth is there are still a lot of small factories in China. Compared with the developed country, the technology of mold design and manufacture is still far behind the developed country. As a graduate whose major is Mold design and Manufacture, I think we not only need to learn some advanced technology, we also need to learn some advanced experience. In China, a lot of high quality workers are needed. This is the main reason why mold technology is not highly promoted in China.
The mold is the manufacturing industry important craft foundation, in our country, the mold manufacture belongs to the special purpose equipment manufacturing industry. According to the structure of the plastical piece chose to use the two plates mold with two sidecores. make use of inclined lead pillar completion side core-pulling of the plasticalpiece and adopt side gate completion injection .Checked a great deal of reference in the whole design process, thorough analysis the design contents, include usage Proe software to carry on wallthinckness and draft analysis for the product。The craft analysis of mold;Draft the mold structure form.
The assurance of injection machine model ;design of injection system and gate;Model structure design and calculation of mold parts; The assurance of mold base with standard piece of choose to use; mold match and guide organization’s design;ejector organization’ s design;The design of side core ejector’s organization;The design of cooling system.
Through the design process of outer shell plastics mold makes me have more deep one layer understanding of the design process to the plastics mold and realize further like Proe, Moldflow, emx, Autocad etc. software are in each stage of mold design the role play with ,and the convenience which bring back, also deeply realize the strong CAD softwares have a necessary function in the aspects of shortenning a mold design、 producting period、reducing costly.Although the CAD design softwares own strong of analytical processing function, also only have firm theories foundation with actual experience then can develop it to the pole.
Key words Plasticalpiece Proe Wallthinckness Moldflow
目 录
1电器外壳注塑模设计1
1.1塑料模具的简单介绍 1
1.2塑料模具的意义2
1.3塑料成型工艺及模具技术的发展2
1.4该电器外壳注塑模的设计简单说明3
2 塑件的分析及塑料的成型工艺性能4
2.1塑件工艺性分析4
2.2材料的成型工艺性能4
3型腔数目的确定8
4 分型面的设计9
4.1分型面介绍与设计要点9
4.2电器外壳分型面的分析与设计9
5 浇注系统的设计10
5.1主流道设计10
5.2 分流道设计12
5.3 浇口的设计13
6 浇口套的设计14
7 浇口的设计15
8 冷料穴的设计17
9 脱模机构的设计17
10 排气系统的设计19
11 冷却系统的设计19
12 模架的选择20
13 成型部分的尺寸设计21
13.1型腔的内径计算22
13.2型腔深度尺寸计算23
13.3型腔成型中心矩尺寸23
13.4型芯底板径向尺寸计算24
13.5型芯底板深度尺寸计算24
13.6型芯1径向尺寸计算25
13.7、型芯1高度尺寸计算26
13.8型芯1中心到成型面之间间距计算26
13.9型芯2径向尺寸计算27
13.10型芯2高度尺寸计算27
13.11型芯2中心到成型面之间间距计算28
13.12型芯3径向尺寸计算28
13.13型芯3高度尺寸计算29
13.14型芯3中心到成型面之间间距计算29
13.15型芯4径向尺寸计算30
13.16型芯6高度尺寸计算30
13.17型芯4中心到成型面之间间距计算31
13.18型芯5径向尺寸计算31
13.19动模镶件1径向尺寸计算32
13.20动模镶件3圆柱体尺寸计算33
13.21动模镶件4高度尺寸计算34
13.22动模镶件6径向尺寸计算34
14 注射机的选择36
14.1注射量36
14.2 注射压力37
14.3 锁模力37
15 注塑机的校核38
15.1注射量,注射压力,锁模力的校核38
15.2模具厚度的校核38
15.3注射机开模行程的校核38
16 零件的加工工艺:39
16.1 动模型芯1 39
16.2动模型芯340
16.3行位40
17 模具加工工艺流程41
17.1凸模加工工艺过程如下41
17.2凹模加工工艺过程如下41
17.3模架的装配41
18.模具表面强化处理工艺特点及应用42
19总装的技术要求42
19.1试模42
参考文献43
设计体会44
致 谢45
2 塑件的分析及塑料的成型工艺性能
2.1塑件工艺性分析
1)塑件的尺寸稍大,精度等级高精度,性能要求一般,为大批生产,采用一模多腔来提高生产率。塑件壁薄,对制品不进行后加工。
2)浇口采用侧浇口,适用于一模多腔,大大提高生产率,浇口截面为矩形。
3)了方便加工和热处理,型腔与型芯部分用镶拼结构。
2.2材料的成型工艺性能
1)塑件采用ABS,ABS的主要工艺性能有:
①具有硬,韧,刚相均衡的优良力学性能,绝缘性好,耐化学腐蚀性好,适于注射成型。
②成型收缩率小,尺寸稳定性高,表面光泽性好,易涂装和着色,但耐热性不太好,耐候性较。
③为热塑性塑料
2)ABS注塑成型条件
密度(g/cm3) 1.05
计算收缩率(%) 0.3~0.8
预热温度(℃) 70~80
预热时间(h) 4
料筒温度 (℃)前段 200~210 中段 210~230
后段 180~200
模具温度 (℃) 50~70
注射压力(Mpa) 70~90
保压力(Mpa) 30~40
保压时间(s) 15~30
冷却时间(s) 15~30
成型周期(s) 40~70
适用注射机类型 螺杆式
由于塑件采用ABS,ABS的主要工艺性能有:
(1)不同品级的原料塑化温度略有差异,机筒温度可控制在160~220℃范围内,喷嘴温度在170~180℃范围内。
(2)注塑压力在60~120Mpa,壁厚、浇口截面较大时,注塑压力可略低一些;而薄壁、流道较长时,注塑压力可提高至130~150Mpa。
(3)注塑熔体流速缓慢一些为好,这对保证制品外观质量,改善制品强度有利。
(4)模具温度在60~70℃。较高的冷却温度,制品外表光泽,内应力小,但收缩率较大。由于流道截面较大,制品固化时间有些延长,为了缩短成型周期,一般制品的模具温度应低一些。
(5)制品的收缩率不大(0.3%~0.8%),但内应力较高。必要时应进行热处理,在70℃左右的热风循环中处理2~3h,缓慢冷却至室温,以消除制品的内应力。表1为常用塑料的收缩率。
表1 常用塑料的收缩率(部分)
塑料种类收缩率
聚乙烯1.5%~3.5%
聚丙烯1.0%~2.5%
ABS(抗冲)0.3%~0.8%
ABS(抗压)0.3%~0.8%
关于注射成型过程
(1)成型前的准备工作。对ABS的色泽、细度和均匀度等进行检验。由于ABS吸水率低,在室温水中浸泡一年,吸水率也不超过1%,所以在成型前不需要进行干燥。
(2)注射过程。塑料在注射料筒内经过加热、塑化达到流动状态后,由模具的浇注系统进入模具型腔成型,其过程可以分为充模、压实、包压、倒流和冷却5个阶段。
(3)塑件的后处理。制品的收缩率不大,但应力较高。必要时应进行热处理,在70℃左右的热循环中处理2~3h,缓慢冷却至室温,以消除制品的内应力。表2为常用塑料注射工艺参数(部分)17 模具加工工艺流程
1、 根据零件结构和制造工艺,模架的基本组成零件有两种:导柱、导套等回转零件;模板等平板零件。
导柱、导套的加工主要是内、外圆柱面加工,平板内零件的制造过程主要进行平面加工和孔隙加工,他们在模具中起定位的导向作用,保证凹凸模在工作时具有正确的相对置,除了要保证导柱,导套配合表面尺寸形状精度外,还应该保证导柱、导套各自配合面之间的同轴度要求。
导柱、导套一般采用低碳钢进行渗碳、淬火处理,也可选用碳素工具钢T10淬火处理,淬火处理硬度58-62HRC。
根据分析,导柱、导套加工艺过程如下:
备料——粗车、半精车内外圆柱表面——热处理——研磨导柱中心孔——粗磨、精磨配合表面——研磨导柱、导套重要配合表面。
17.1凸模加工工艺过程如下
下料——锻造——退火——粗加工——精磨基面准面——划线——工作型面半精加工——淬火、回火——磨削——修研。
17.2凹模加工工艺过程如下
下料——锻造——退火——粗加工六面——精磨基面准面——划线—型孔半精加工——型孔精加工——淬火、回火——精磨(研磨)
17.3模架的装配
导柱、导套与模板之间一般采用过盈配合,装配时可采用手动压力机将导柱压入动模板的导柱孔,复位机构的装配复位杆与固定板一般采用过度配合。模架的装配比较的简单,主要是用螺钉将装有导套的定模板连接起来。
18.模具表面强化处理工艺特点及应用
渗氮处理:渗氮处理是向模具零件表面渗入氮原子的过程,
模具渗氮前应加工到尺寸精度和表面粗糙度,最好是经过试模确认完全合格后再进行渗氮处理。根据模具的技术要求分别采用以下两种工艺路线:
精密模具:备料——锻造——退火或回火——粗加工——调质——半精加工——装配——试模——渗氮——研磨抛光——装配;
一般模具:备料——粗加工——调质——精加工——糁氮——研磨——装配;
19总装的技术要求
a、装配后的模具安装表面的平行误差不大于0.05;
b、模具闭合后分型面应均密合;
c、导柱、导套滑动灵活,推件时推杆和卸料板动作一致;
d、合模后动模部分和定模部分的型芯必须紧密接触
19.1试模
模具在装配完成之后,在交付生产时试模,其目的是检查模具在设计制造上是否存在缺陷,若有,则要求排除;对模具成型工艺条件进行试验以有利于模具成型工艺的确定和提高。
参考文献
[1]、国家标准总局编。《塑料模国家标准》 中国标准出版社,1999
[2]、陈万林编著《塑料模具设计与制作教程》北京希望电子出版社,2000
[3]、黄健求编《模具制造》 机械工业出版社,2001
[4]、黄毅宏编《模具制造工艺学》机械工业出版社,1996
[5]、王孝培编《塑料成型工艺及模具简明手册》机械工业出版社,2000
[6]、陈晓华、王秀英编《典型零件模具图册》机械工业出版社,2001
[7]、翁其金编 《塑料模塑工艺与塑料模设计》机械工业出版社,1999
[8]、塑料模具技术手册编委会 《塑料模具技术手册》机械工业出版社,1997
[9]、孙凤勤编 《冲压与塑压设备》机械工业出版社,1997
[10]、黄锐编 《塑料工程手册》机械工业出版社,2000
[11]、屈华昌编 《塑料成型工艺与模具设计》机械工业出版社,1995