新科MP4上盖模具设计及型腔仿真加工
摘要:本课题是关于MP4上盖模具设计及型腔仿真加工。通过运用模具设计基础和PRO/E、AutoCAD等这些课程的知识去做一次模具设计的实践,并在这次实践中锻炼自己用理论知识来解决实际问题的能力。
本次模具设计主要是对MP4上盖注射成型模的结构设计和模具加工制造。前者包括分型面、型腔布置、浇注系统、排气系统、加热冷却系统、抽芯机构、顶出机构、脱模机构以及主要零部件的设计。后者运用PRO/E进行三维造型设计并对注塑模模具进行装配,对MP4上盖模具定模板型腔的加工工艺进行了分析,并利用MASTERCAM软件进行了仿真加工,其切削过程直观,切削参数得以体现,不合理的参数可以改进,能最大限度地降低能源和材料消耗,提高加工效率。经生产验证,该模具结构设计巧妙、操作方面、使用寿命长、塑件达到技术要求。
关键词:MP4;PRO/E;AutoCAD;注塑模具;模具设计
Tne design of the roof of new MP4 mould And
The simulation processing of the mold cavity
Abstract :This topic is to design the above of MP4 mold design and process simulation process of the cavity. Through use the foundation of design and Proe, AutoCAD such as the knowledge to do the work of these courses a mold design practice, and practice in this exercise with their theoretical knowledge to solve practical problems.
The mold design mainly cover the structure design mould assist designing for manufacturing, and the working process of the injection mould of the roof of the MP4 were introduced. The former involve parting plane, cavity layout, old systems, heating cooling systems, the core pulling mechanism structure, prop up the organization, drawing patterns and the design process of the main work pieces. The later use Proe to construct carries on the three dimensional modeling and to assemble the injection mould. The processing craft of the cavity of fixed plate of the base of the mp4 are analyzed, and the simulation process are carry out with the software of MasterCAM,which can observe the geometric figure of the process of cutting very visually, the machine parameters users setting have been fully reflected to improve the unreasonable parameters, to minimize consumption of energy and materials and to improve processing efficiency. The mould was proved to be a clever design by production practice , the mould could be operated easily , the service life of the mould was long or and the plastics parts produced by the mould could meet the technical requirement.
Keywords: MP4;PRO / E;AutoCAD;injection mold; mold design
目录
1 前言1
1.1 课题背景1
1.2 本产品特点1
1.3 播放器的主要功能1
1.4 课题意义1
1.5 设计前提及主要问题2
1.6预期成果和实际价值2
2总体方案论证3
3 造型设计4
3.1 产品主要尺寸的确定4
3.2 MP4的造型方法与步骤5
3.3 MP4上壳的造型过程5
4 材料的选择8
4.1塑料的基本概念8
4.1.1塑料的定义及组成8
4.1.2组成8
4.1.3 辅助材料8
4.2 制品材料8
4.3 影响聚合物取向的主要因素(以注射成型为例)8
4.3.1 温度的影响8
4.3.2 注射压力和保压压力9
4.3.3 浇口冻结时间9
4.3.4模具温度9
4.4 常用塑料分析和数据选取9
4.4.1 根据以下表格和结合实际情况选取数据9
4.4.2模具材料的选择10
5 模具设计11
5.1 注塑机的校核11
5.1.1注塑机设备的确定11
5.1.2注塑机有关工艺参数的校核11
5.2分型面的设计13
5.3浇注系统的设计14
5.3.1浇注系统的设计原则14
5.3.2主流道的设计14
5.3.3分流道及其平衡布置14
5.3.4 浇口的设计15
5.3.5 冷料穴的设计15
5.4 冷却系统的设计16
5.4.1在设计冷却系统时,应从多方面考虑:16
5.4.2 冷却计算16
5.5 顶出系统的设计17
5.5.1 推出机构设计17
5.5.2 顶出行程17
5.5.3 复位杆17
5.5.4 顶出杆的形状和尺寸选择18
5.5.5 导向装置位置的布置18
5.5.6 浇注系统零件的设计18
5.6 模架的设计19
5.7凹凸模的造型19
5.8 型腔加工工艺分析及加工仿真23
5.8.1零件的工艺审查23
5.8.2 毛坯选择23
5.8.3 拟定加工方案23
5.8.4 型腔数控仿真加工23
6 结论26
参考文献27
致 谢28
附录29
1 前言
1.1 课题背景
我的专业是数字化制造,在学习和实习中常常接触很多的数码产品,包括随身听、CD机、DVD机、MP4播放器、翻译机等等。我选择设计MP4播放器上盖。这样有利于我的设计与实践更加紧密结合。
1.2 本产品的特点
(1) 结构简单,但功能强大,实用性强,
(2) 体积小巧携带方便,
(3) 显示屏大,大大提高其可观性,
(4) 其功能键为圆形,美观实用且按键舒适。
1.3 播放器的主要功能
(1)一般具有可视化功能,
(2)相同的空间能存储更多的信息,
(3) 不存在防震问题,更加适合运动时欣赏音乐,
(4) 能随心所欲编辑自己喜爱的歌。
1.4 课题意义
模具是工业生产的重要工艺设备,它被用来成型具有一定形状和尺寸的各种
制品。在各种材料加工工业中广泛地使用各种模具,每种材料成型模具按成型方
法不同又分为若干种类型。其中塑料模具的发展是随着塑料工业的发展而发展
的。近年来,人们对各种设备和用品轻量化要求越来越高,这就为塑料制品提供
了更为广阔的市场。塑料制品要发展,必然要求塑料模具随之发展。模具作为发
展新产品的重要装备,不仅市场需要量大,而且技术含量高。对于模具的精度、
寿命、交货期等要求也非常务实,模具行业的竞争也非常激烈。本课题是MP4上盖制品进行测绘、模具设计、模具型腔仿真加工及数控编程。课题来源于生产实践。基于生产实践之上的对MP4上盖制品的模具设计以及仿真加工。在设计过程中要解决MP4上盖制品测绘、模具设计、在模具设计时对分型面的选择、浇口形式与位置的确定、型腔位置的安排、定模冷却水道的设置、工艺分析及数控编程及加工仿真等问题。本专业是机械设计制造及其自动化,对制品的模具设计使得我们把以前所学的相关知识都运用到其中了,对模具设计手册、机械设计手册、模具制造工艺、中国模具工程大典的查找使得我对设计有了更进一步的认识和了解,能熟练运用PRP/E软件进行制品的造型和模具的装配,还有Mastercam型腔的仿真加工都得到了掌握。



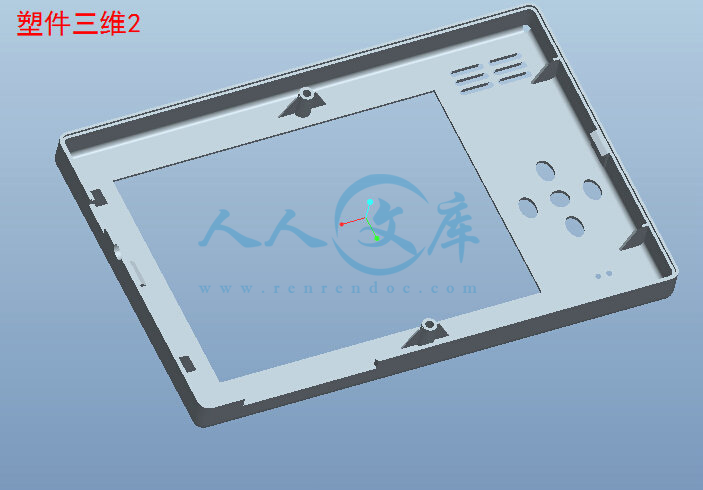

