微型货车驱动桥设计【含CAD图纸、三维模型图纸和仿真】
收藏
资源目录
压缩包内文档预览:
编号:81604026
类型:共享资源
大小:83.87MB
格式:ZIP
上传时间:2020-05-28
上传人:机****料
认证信息
个人认证
高**(实名认证)
河南
IP属地:河南
100
积分
- 关 键 词:
-
含CAD图纸、三维模型图纸和仿真
微型
货车
驱动
设计
CAD
图纸
三维
模型
仿真
- 资源描述:
-
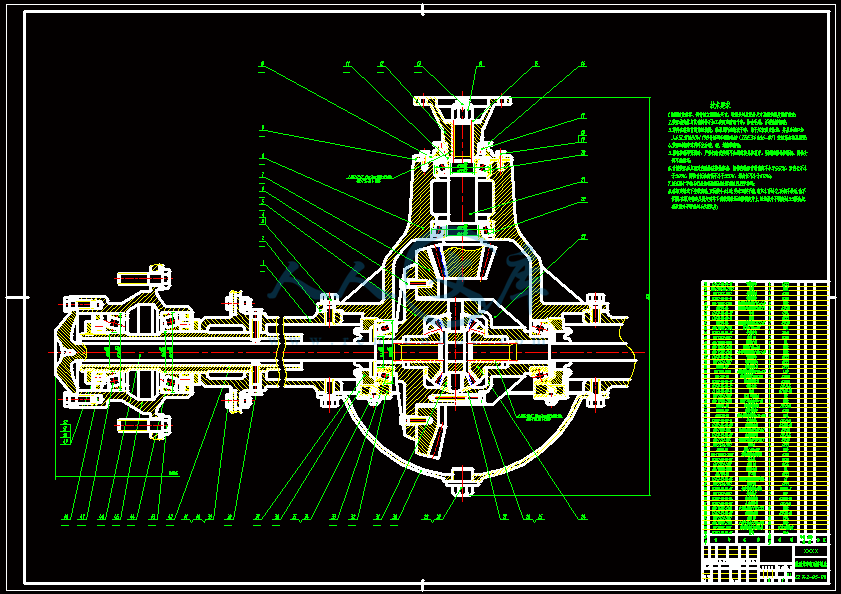
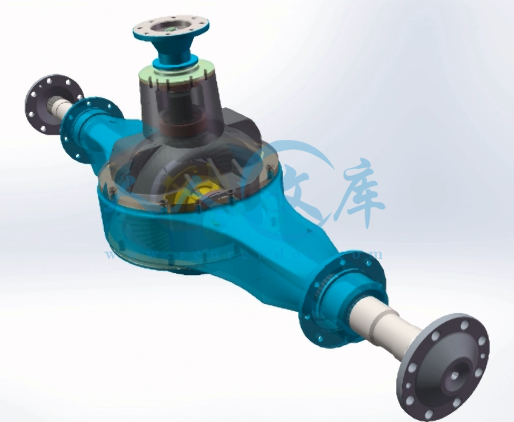
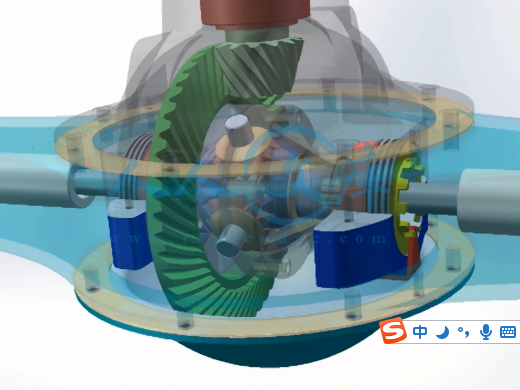
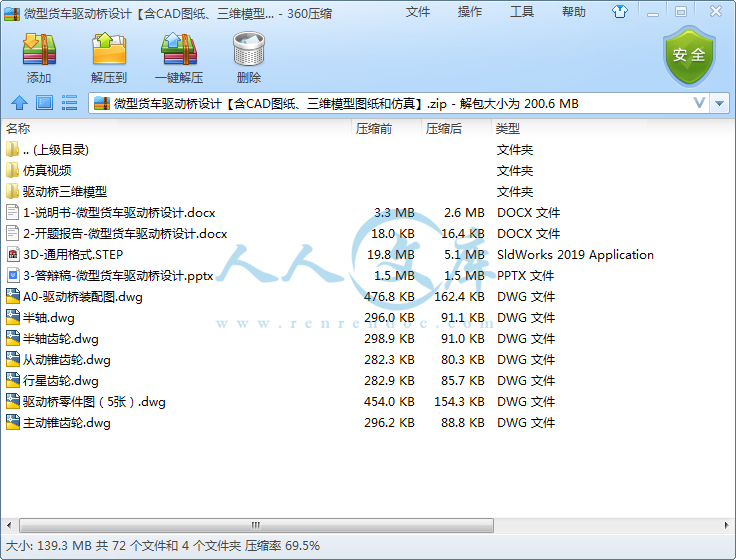
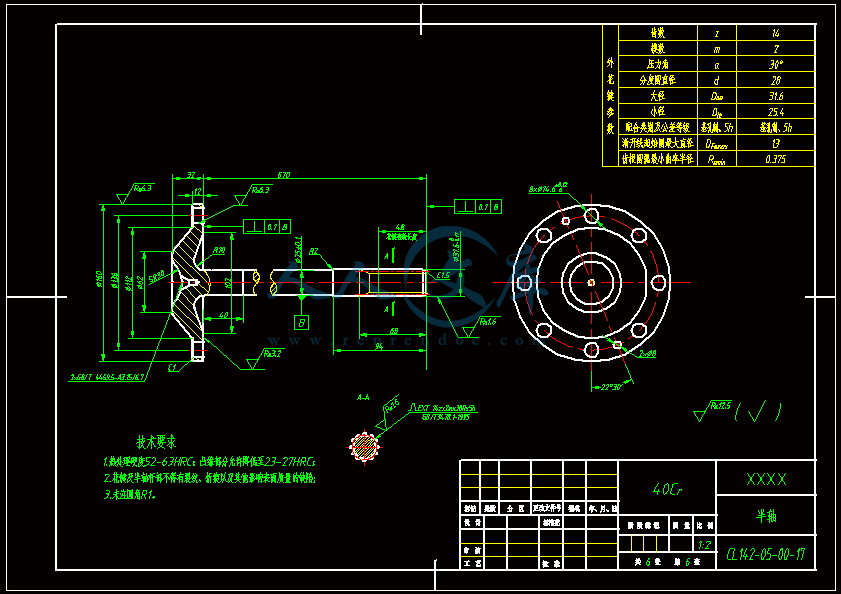
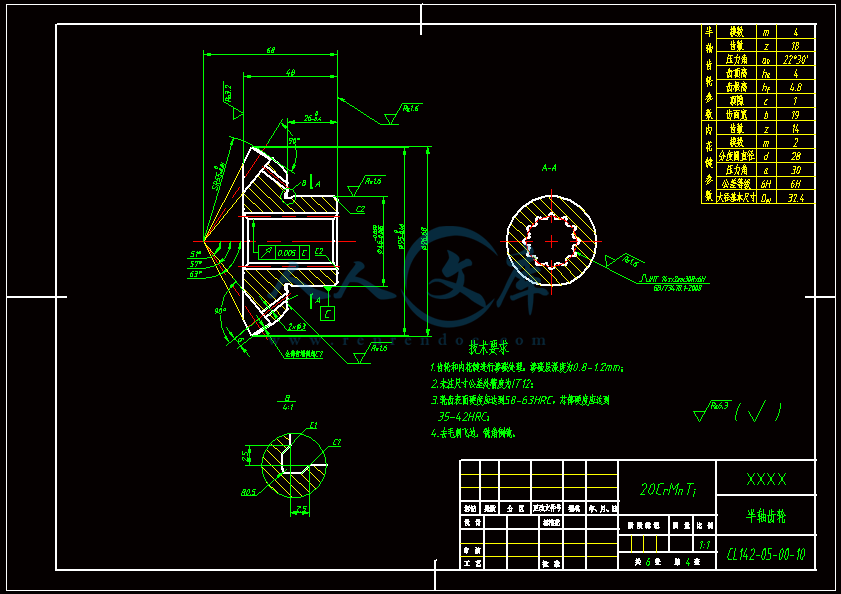
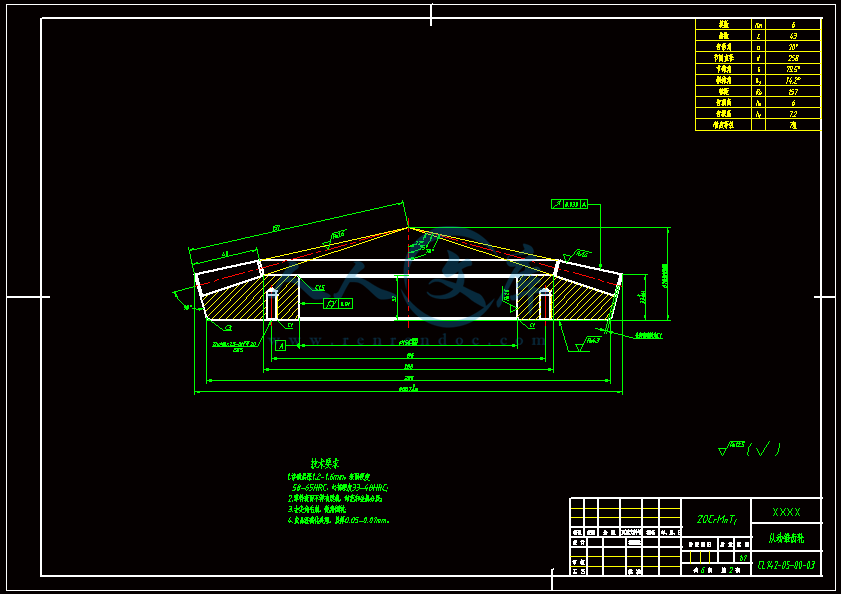
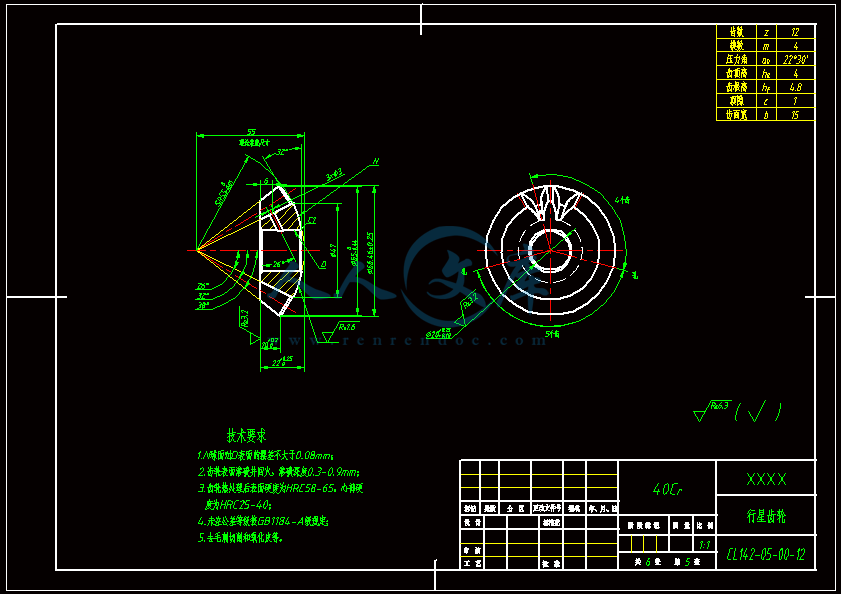
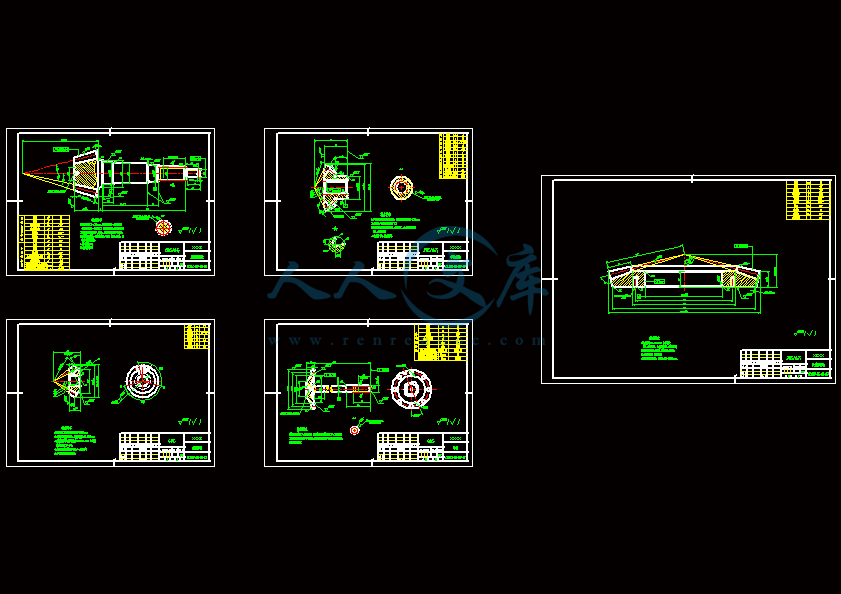
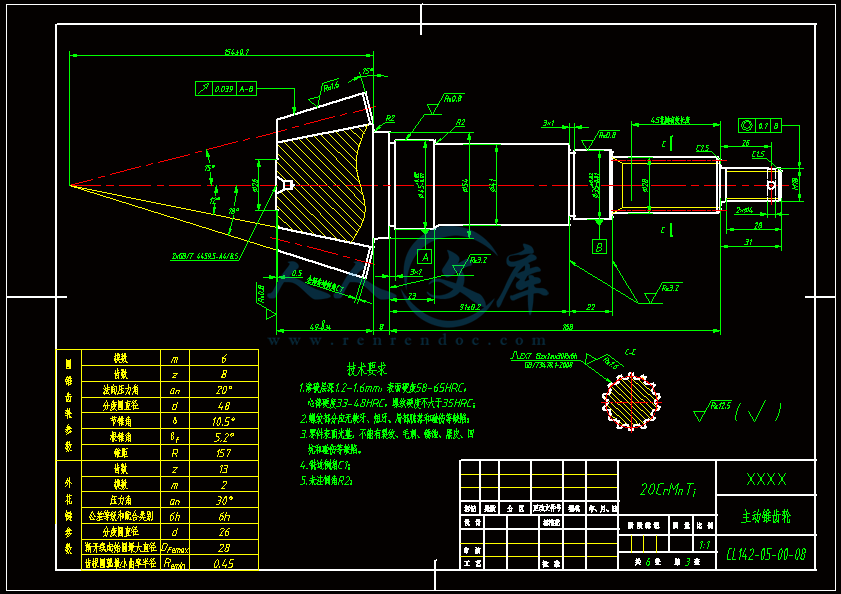
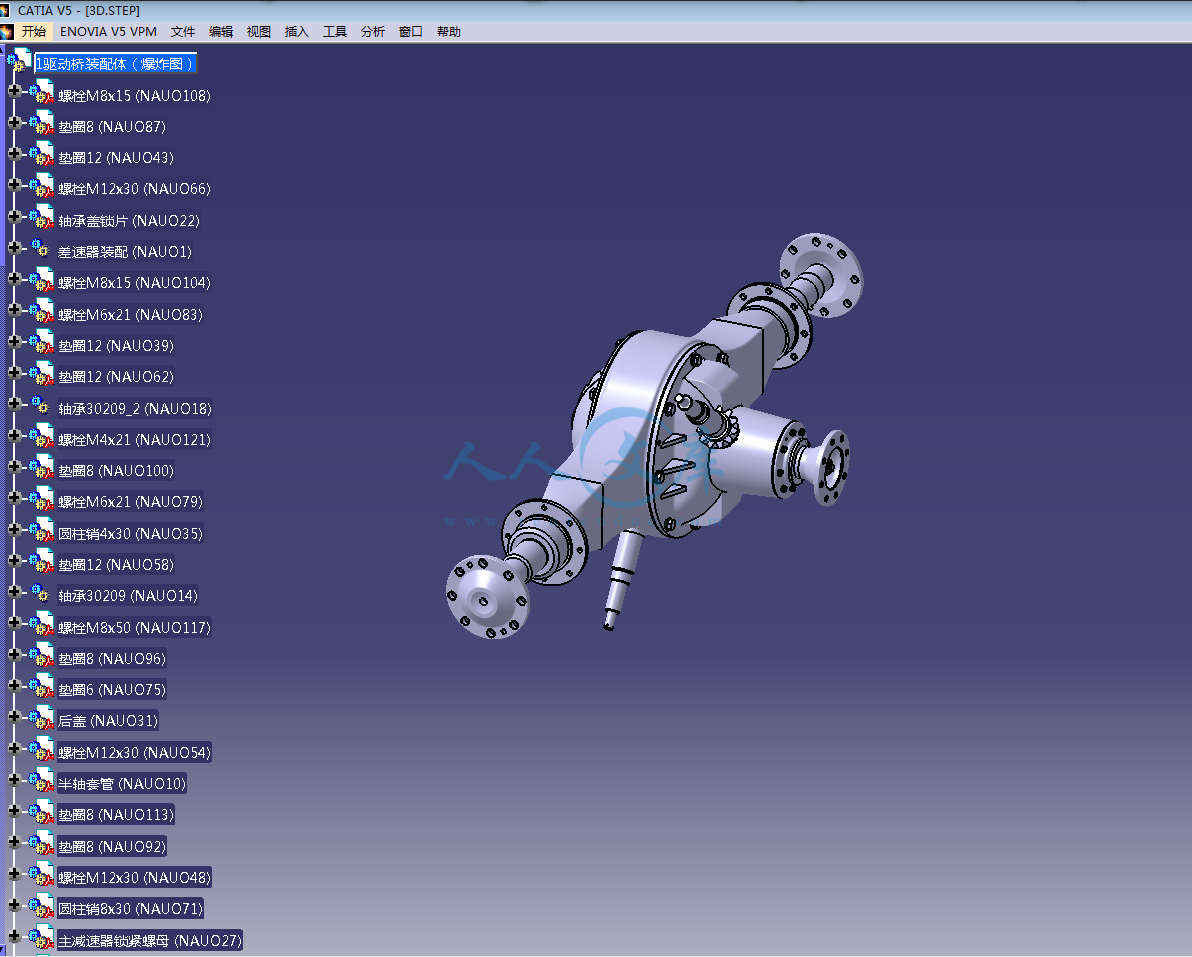
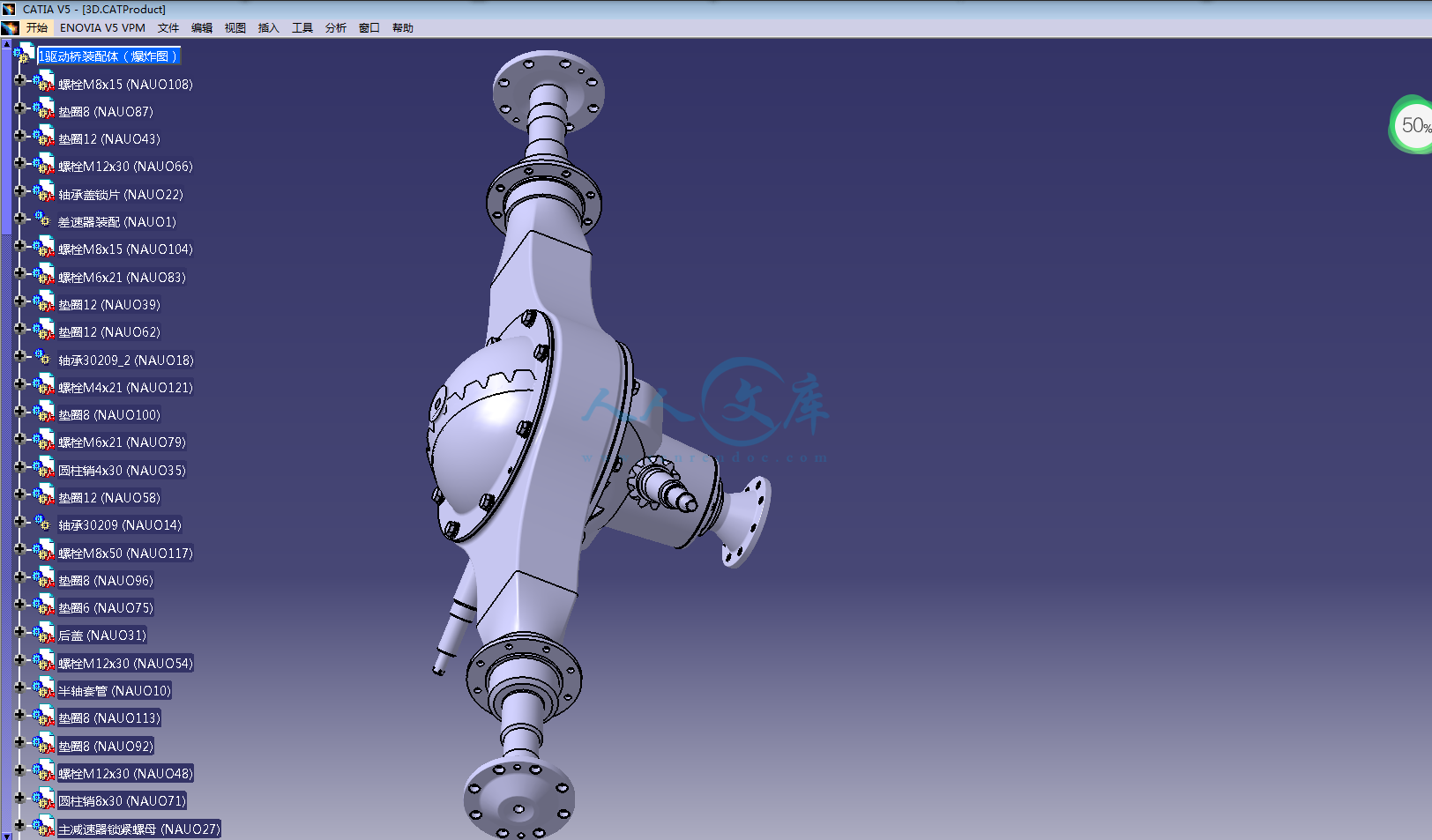
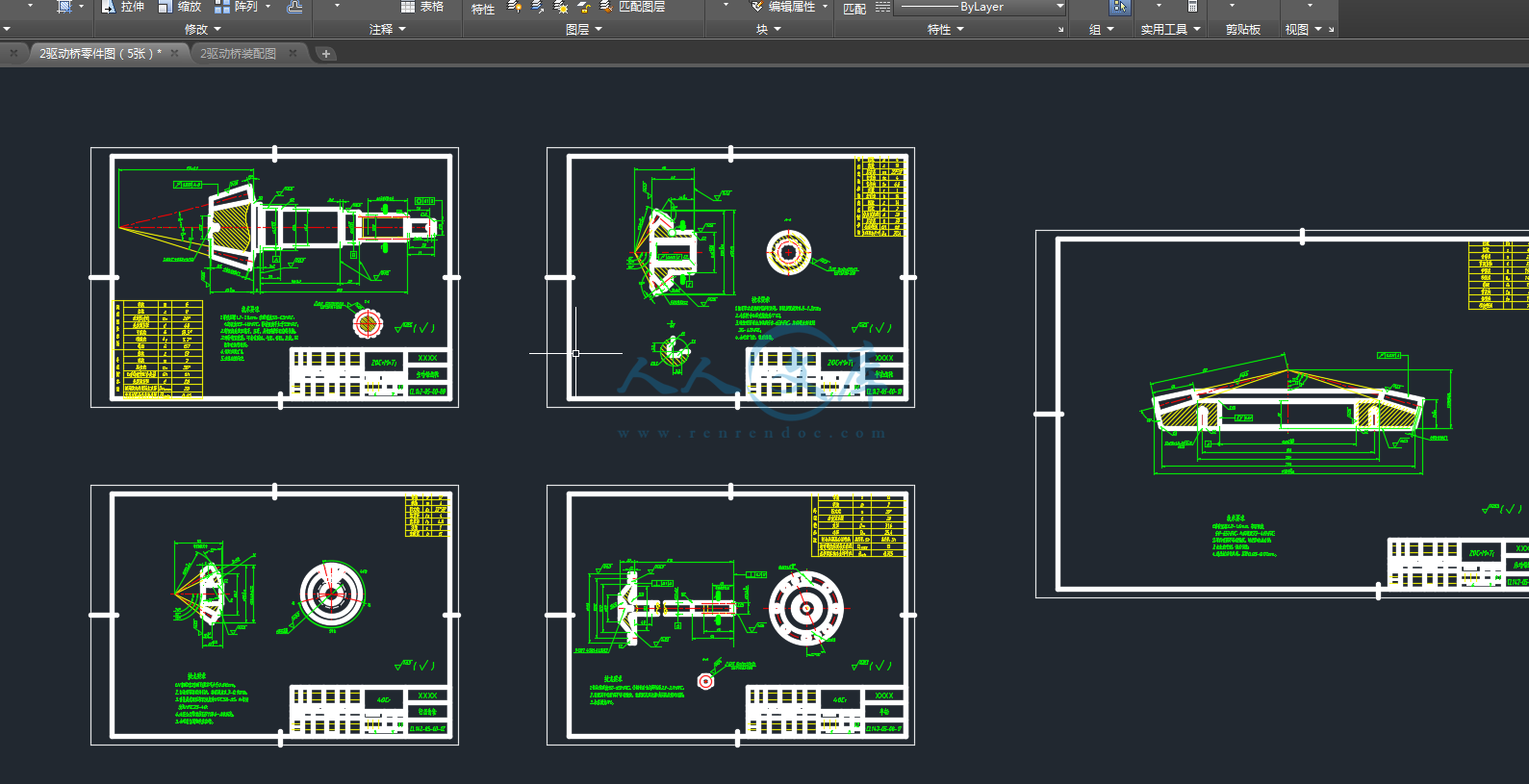
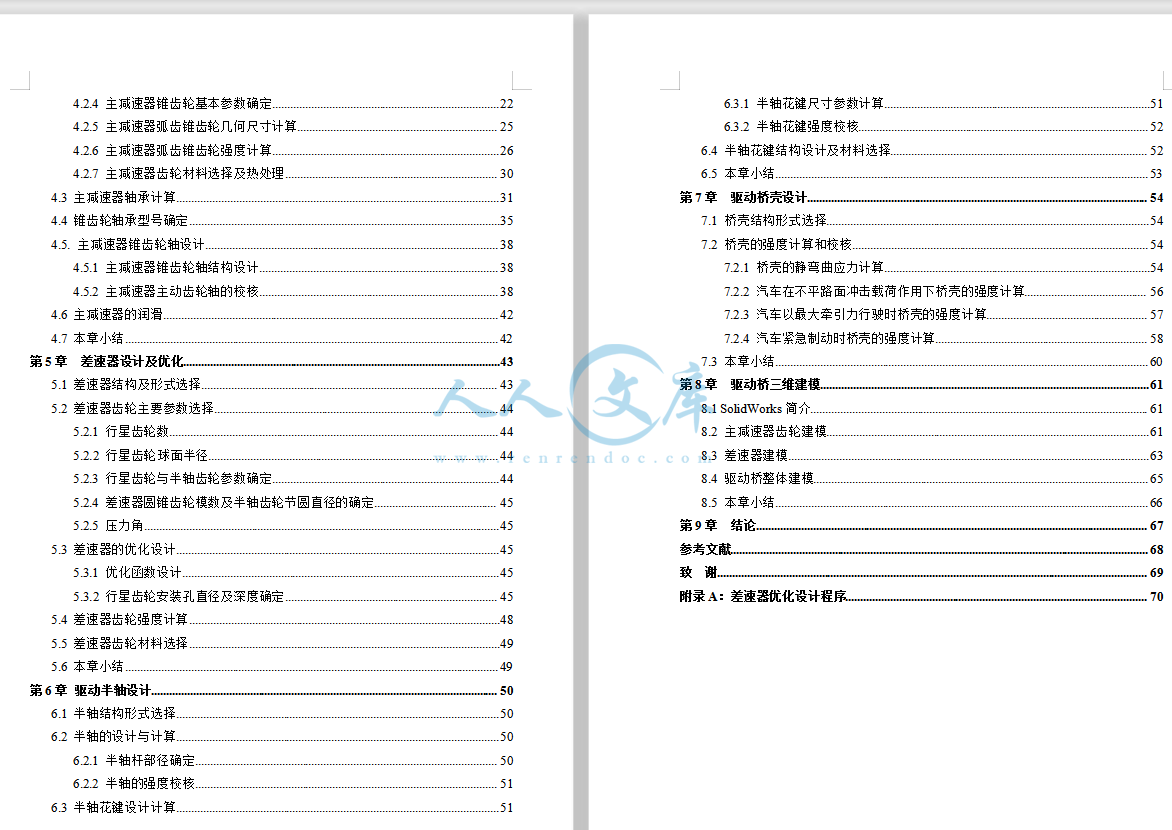
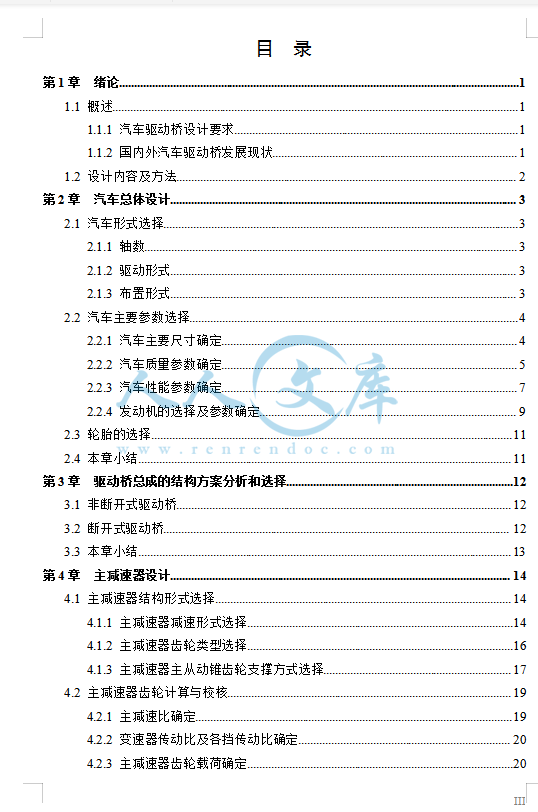
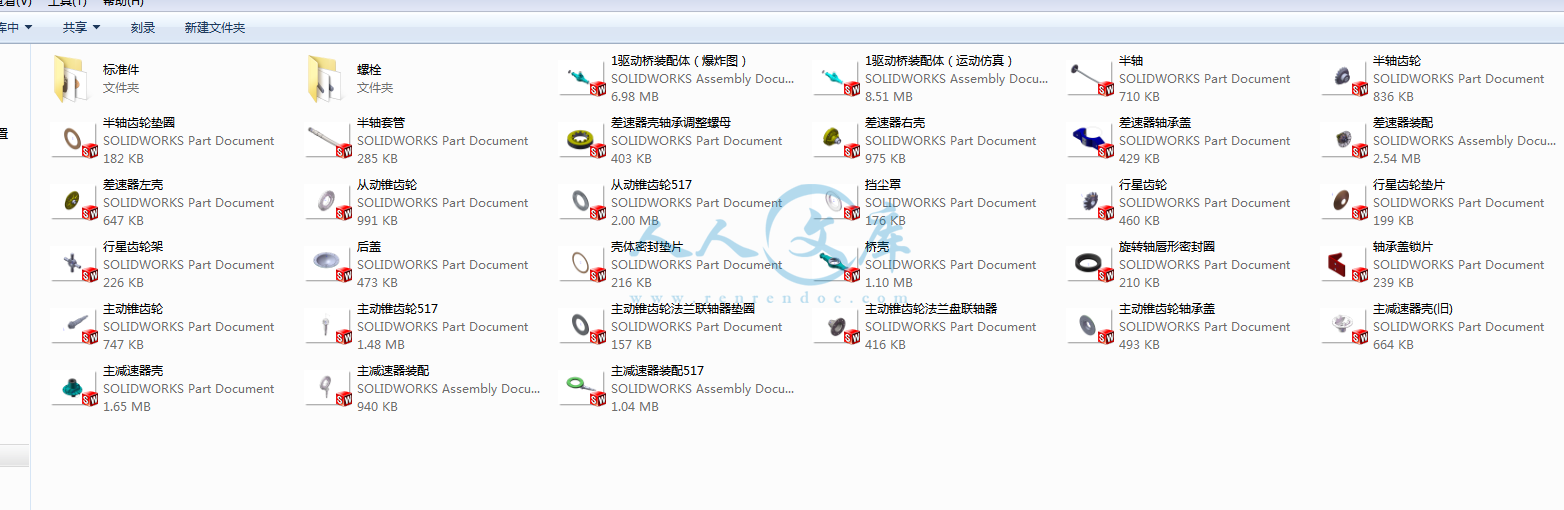
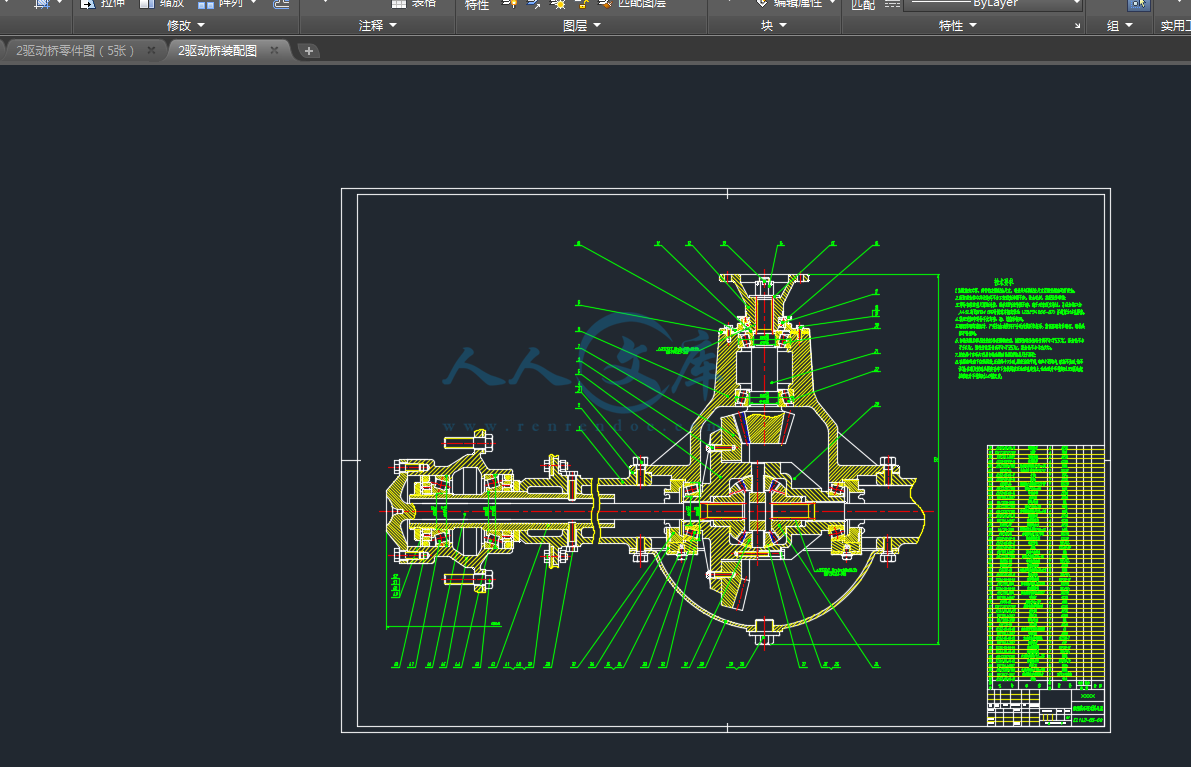
- 内容简介:
-
压缩包内含CAD图纸和三维建模及说明书,咨询Q 197216396 或 11970985摘 要驱动桥是汽车传动系的重要组成部分,它主要由主减速器、差速器、半轴和桥壳等组成。其主要作用是降低转速、增大转矩,以及实现汽车行驶运动学所要求的差速功能,并且还要承受作用于路面与车架或车身之间的垂直力、纵向力和横向力等。根据类似车型并参考汽车设计汽车理论等书籍确定了驱动桥各部件的设计方案。本次设计车型为微型货车,采用非断开式驱动桥、单级主减速器、对称式锥齿轮差速器、全浮式半轴、整体铸造式桥壳。在本次设计中完成了主减速器、差速器、半轴、桥壳及轴承的设计计算及校核。利用MATLAB对差速器进行优化,结果差速器的体积减少16%。利用AutoCAD绘制了驱动桥零件及总成的二维图,利用SolidWorks软件对驱动桥进行了三维建模。该驱动桥结构简单、工作可靠、制造成本低。关键词:微型货车,整体式驱动桥,差速器优化,SolidWorks三维建模ABSTRACTThe drive axle is an important part of the automotive powertrain. It is mainly composed of the main reducer, differential, axle and axle housing. Its main role is to reduce the speed, increase the torque, and to achieve the required differential function of the vehicle kinematics, and also to withstand the vertical force, longitudinal force and lateral force acting between the road and the frame or body.According to similar models reference car design car theory and other books to determine the design of the drive axle components. The design of this model is a mini-van, using a non-disconnected drive axle, a single-stage main reducer, a symmetric bevel gear differential, a full-floating axle shaft, and an integrally cast axle housing. In this design, the design, calculation and verification of the final reducer, differential, axle, axle housing and bearing were completed. Using MATLAB to optimize the differential, the result is a 16% reduction in the volume of the differential. The two-dimensional maps of the drive axle parts and assembly were drawn using AutoCAD, and the three-dimensional modeling of the drive axle was performed using SolidWorks software. The drive axle has a simple structure, reliable operation and low manufacturing cost.Keywords: mini-truck,integral drive axle,differential optimization,SolidWorks 3D modeling目 录第1章 绪论11.1 概述11.1.1 汽车驱动桥设计要求11.1.2 国内外汽车驱动桥发展现状11.2 设计内容及方法2第2章 汽车总体设计32.1 汽车形式选择32.1.1 轴数32.1.2 驱动形式32.1.3 布置形式32.2 汽车主要参数选择42.2.1 汽车主要尺寸确定42.2.2 汽车质量参数确定52.2.3 汽车性能参数确定72.2.4 发动机的选择及参数确定92.3 轮胎的选择112.4 本章小结11第3章 驱动桥总成的结构方案分析和选择123.1 非断开式驱动桥123.2 断开式驱动桥123.3 本章小结13第4章 主减速器设计144.1 主减速器结构形式选择144.1.1 主减速器减速形式选择144.1.2 主减速器齿轮类型选择164.1.3 主减速器主从动锥齿轮支撑方式选择174.2 主减速器齿轮计算与校核194.2.1 主减速比确定194.2.2 变速器传动比及各挡传动比确定204.2.3 主减速器齿轮载荷确定204.2.4 主减速器锥齿轮基本参数确定224.2.5 主减速器弧齿锥齿轮几何尺寸计算254.2.6 主减速器弧齿锥齿轮强度计算264.2.7 主减速器齿轮材料选择及热处理304.3 主减速器轴承计算314.4 锥齿轮轴承型号确定354.5. 主减速器锥齿轮轴设计384.5.1 主减速器锥齿轮轴结构设计384.5.2 主减速器主动齿轮轴的校核384.6 主减速器的润滑424.7 本章小结42第5章 差速器设计及优化435.1 差速器结构及形式选择435.2 差速器齿轮主要参数选择445.2.1 行星齿轮数445.2.2 行星齿轮球面半径445.2.3 行星齿轮与半轴齿轮参数确定445.2.4 差速器圆锥齿轮模数及半轴齿轮节圆直径的确定455.2.5 压力角455.3 差速器的优化设计455.3.1 优化函数设计455.3.2 行星齿轮安装孔直径及深度确定455.4 差速器齿轮强度计算485.5 差速器齿轮材料选择495.6 本章小结49第6章 驱动半轴设计506.1 半轴结构形式选择506.2 半轴的设计与计算506.2.1 半轴杆部径确定506.2.2 半轴的强度校核516.3 半轴花键设计计算516.3.1 半轴花键尺寸参数计算516.3.2 半轴花键强度校核526.4 半轴花键结构设计及材料选择526.5 本章小结53第7章 驱动桥壳设计547.1 桥壳结构形式选择547.2 桥壳的强度计算和校核547.2.1 桥壳的静弯曲应力计算547.2.2 汽车在不平路面冲击载荷作用下桥壳的强度计算567.2.3 汽车以最大牵引力行驶时桥壳的强度计算577.2.4 汽车紧急制动时桥壳的强度计算587.3 本章小结60第8章 驱动桥三维建模618.1 SolidWorks简介618.2 主减速器齿轮建模618.3 差速器建模638.4 驱动桥整体建模658.5 本章小结66第9章 结论67参考文献68致 谢69附录A:差速器优化设计程序7089XXXX学院XX设计第1章 绪论1.1 概述驱动桥是汽车传动系的重要组成部分。它位于传动系的末端,其基本功用首先是增扭、减速,改变转矩的传递方向,并允许左右车轮以不同的转速旋转,即增大由传动轴或直接从变速器传来的转矩,并将转矩合理地分配给左、右驱动车轮;其次,驱动桥还要承受作用于路面和车架或车身之间的垂直力、纵向力和横向力,以及制动力矩和反作用力矩等。汽车驱动桥结构型式和设计参数除对汽车的可靠性与耐久性有重要影响外,也对汽车的行驶性能如动力性、经济性、平顺性、通过性、机动性和操动稳定性等有直接影响。另外,汽车驱动桥在汽车的各种总成中也是涵盖机械零件、部件、分总成等的品种最多的大总成。例如,驱动桥包含主减速器、差速器、驱动车轮的传动装置(半轴及轮边减速器)、桥壳和各种齿轮。因此,通过对汽车驱动桥的设计,能够更好地掌握汽车与机械之间更为全面的知识。1.1.1 汽车驱动桥设计要求设计驱动桥时应当满足如下基本要求:1、选择适当的主减速比,以保证汽车在给定条件下具有最佳的动力性和燃油经济性。2、外廓尺寸小,保证汽车具有足够的离地间隙,以满足通过性要求。3、齿轮及其他传动件工作平稳,噪声小。4、在各种载荷和转速工况下有高的传动效率。5、具有足够的强度和刚度,以承受和传递作用于路面和车架或车身间的各种力和力矩;在此条件下,尽可能降低质量,尤其是簧下质量,以减少不平路面的冲击载荷,提高汽车行驶平顺性。6、与悬架导向机构运动协调;对于转向驱动桥,还应与转向机构运动协调。7、结构简单,加工工艺好,制造容易,维修、调整方便。1.1.2 国内外汽车驱动桥发展现状目前我国正在大力发展汽车产业,采用后轮驱动汽车的平衡性和操作性都将会有很大的提高。后轮驱动的汽车加速时,牵引力将不会由前轮发出,所以在加速转弯时,司机就会感到有更大的横向握持力,操作性能变好。维修费用低也是后轮驱动的一个优点,尽管由于构造和车型的不同,这种费用将会有很大的差别。如果变速器出了故障,对于后轮驱动的汽车就不需要对差速器进行维修,但是对于前轮驱动的汽车来说也许就有这个必要了,因为这两个部件是做在一起的。所以后轮驱动必然会使得乘车更加安全、舒适,从而带来可观的经济效益。目前国内研究的重点在于:从桥壳的制造技术上寻求制造工艺先进、制造效率高、成本低的方法;从齿轮减速形式上将传统的中央单极减速器发展到现在的中央及轮边双级减速或双级主减速器结构;从齿轮的加工形式上车桥内部的的主从动齿轮、行星齿轮及圆柱齿轮逐渐采用精磨加工,以满足汽车高速行驶要求及法规对于噪声的控制要求。总之,我国汽车驱动桥的研究设计与世界先进驱动桥设计技术还有一定的差距,我国车桥制造业虽然有一些成果,但都是在引进国外技术、纺制、再加上自已改进的基础上了取得的。个别比较有实力的企业,虽有自己独立的研发机构但都处于发展的初期。在科技迅速发展的推动下,高新技术在汽车领域的应用和推广,各种国外汽车新技术的引进,研究团队自身研发能力的提高,我国的驱动桥设计和制造会逐渐发展起来,并跟上世界先进的汽车零部件设计制造技术水平。1.2 设计内容及方法本设计的主要内容及方法包括以下六个方面:(1)驱动桥和主减速器、差速器、半轴、驱动桥桥壳的结构形式选择;(2)主减速器的参数选择与设计计算及主减速齿轮强度校核;(3)差速器的设计与计算,并利用MATLAB对差速器进行优化;(4)半轴的设计与计算;(5)驱动桥桥壳的结构设计及强度校核;(6)CAD绘制装配图、零件图;(7)利用SolidWorks建立三维模型 。第2章 汽车总体设计2.1 汽车形式选择不同形式的汽车,主要体现在轴数、驱动形式以及布置形式上有区别。2.1.1 轴数汽车可以有两轴、三轴、四轴甚至更多的轴。影响选取轴数的因素主要由汽车的总质量、道路法规对轴载质量的限制和轮胎的负荷能力以及汽车的结构等。随着设计汽车的乘员数增多或装载质量增加,汽车的整备质量和总质量也增大。在汽车轴数不变的情况下,汽车总质量增加以后,使公路承受的负荷增加。当这种负荷超过了公路设计的承载能力以后,公路会被破坏,使用寿命也将缩短。为了保护公路,有关部门制定了道路法规,对汽车的轴载质量加以限制。当所设计的汽车总质量增加到轴荷不符合道路法规的限定值时,设计师可选择增加汽车轴数来解决。汽车轴数增加以后,不仅轴,而且车轮、制动器、悬架等相应增多,使整车结构变得复杂,整备质量以及制造成本增加。若转向轴数不变,汽车的最小转弯直径又增大,后轴轮胎的磨损速度也加快,所以增加汽车轴数是不得已的选择。总质量小于19t的商用车一般采用结构简单、成本低廉的两轴方案。总质量在1926t的,一般采用三轴形式,总质量更大的汽车宜采用四轴和四轴以上的形式1。由于本车的最大总质量为3.1t,故采用两轴式。2.1.2 驱动形式 汽车的驱动形式有很42、44、62、64、66、84、88等,其中前一位数字表示汽车车轮总数,后一位数字表示驱动轮数。汽车的用途、总质量和对车辆通过性的要求等,是影响选取驱动形式的主要因素。增加驱动轮数能够提高汽车的通过能力,驱动轮数越多,汽车的结构越复杂,整备质量和制造成本也随之增加,同时也使汽车的总体布置工作变得困难。乘用车和总质量小些的商用车,多采用结构简单、制造成本低的42驱动形式。总质量在1926t的公路用车辆,采用62或64驱动形式。对于越野车,为提高其通过性,可采用44、66、88的驱动形式1。本设计微型货车采用结构简单、制造成本低的42后双胎的驱动形式。2.1.3 布置形式汽车的布置形式是指发动机、驱动桥和车身(或驾驶室)的相互关系和布置特点而言。汽车的使用性能除取决于整车和各总成的有关参数以外,其布置形式对使用性能也有很重要影响。本车采用平头式货车,发动机前置后桥驱动设计。2.2 汽车主要参数选择汽车的主要参数包括尺寸参数、质量参数和汽车性能参数。2.2.1 汽车主要尺寸确定汽车的主要参数有外廓尺寸、轴距、轮距、前悬、后悬、车头长度和车厢尺寸等。1、外廓尺寸汽车的主要尺寸参数有外廓尺寸、轴距、轮距、前悬、后悬、货车车头长度和车厢尺寸等。汽车的长、宽、高称为汽车的外廓尺寸。影响确定汽车外廓尺寸的因素除法规和汽车的用途外,还有载客量或装载质量及涵洞和桥梁等道路尺寸条件。汽车长度尺寸小些不仅可以减少形式期间需要占用的道路长度,同时还可以增加车流密度,在停车时占用的停车面积也小。除此之外,汽车的整备质量相应减少,这对提高比功率,比转矩和燃油经济性有利。GB1589-1989汽车外廓尺寸限界规定如下:货车、整体式客车总长不应超过12m,单铰接式客车不超过18m,半挂汽车列车不超过16.5m,全挂汽车列车不超过20m;不包括后视镜,汽车宽不超过2.5m;空载、顶窗关闭状态下,汽车高不超过4m;后视镜等单侧外伸量不得超过最大宽度处250mm;顶窗、换气装置开启时不得超出车高300mm1。根据设计要求,并参考同类车型,本车的外廓尺寸如下:53001735 2050(mm)。2、轴距 轴距L对整备质量、汽车总长、汽车最小转弯直径、传动轴长度、纵向通过半径等有影响。原则上对发动机排量大的乘用车、载质量或载客量多的货车或客车,轴距取得越长。对机动性要求高的汽车,轴距宜取短些。根据本车设计要求,汽车总质量3000kg,参考表2-1,取轴距L=2800 mm。表2-1 汽车的轴距和轮距车型类别轴距L/mm轮距B/mm4x2货车1.86.023003600130016506.014.036005500170020003、前轮距和后轮距改变汽车轮距B会影响车厢或驾驶室内宽、汽车总宽、总质量、侧倾刚度、最小转弯直径等因素发生变化。受汽车总宽不得超过2.5m限制,轮距不宜过大。但在选定的前轮距范围内,应能布置下发动机、车架、前悬架和前轮,并保证前轮有足够的转向空间,同时转向杆系与车架、车轮之间有足够的运动间隙。在确定后轮距时,应考虑车架两纵梁之间的宽度、悬架宽度和轮胎宽度及它们之间应留有必要的间隙。根据表2-1并参考同类型车。取前轮距,后轮距。4、前悬和后悬前悬尺寸对汽车通过性、碰撞安全性、驾驶员视野、前钢板弹簧床度、上车和下车的方便性以及汽车造型等均有影响。初选的前悬尺寸,应当在保证能布置总成、部件的同时尽可能短些。后悬尺寸对汽车通过性、汽车追尾时的安全性、货箱长度或行李箱长度、汽车造型等有影响,并取决于轴距和轴荷分配的要求。总质量在1.814.0t的货车后悬一般在12002200mm之间。参考同类车型并根据本车特点确定前悬:=1200mm,后悬:=1300mm。5、货车车头长度货车车头长度系指从汽车的前保险杠到驾驶室后围的距离。车身形式,即长头型还是平头型对车头长度有绝对影响。此外,车头长度尺寸对汽车外观效果、驾驶室居住性、汽车面积利用率和发动机的接近性等有影响。平头型货车一般在14001500mm之间。参考同类车型并根据本车特点确定本设计车头长度为1450mm。6、货车车厢尺寸对于能达到较高车速的货车,使用过宽的车厢会增加汽车迎风面积,导致空气阻力增加。车厢内长应在满足运送货物达到额定吨位的条件下尽可能取短些,以利于减小整备质量。根据本车设计和参考其他同类型货车,取长为3.4mm。2.2.2 汽车质量参数确定1、质量系数质量系数是指汽车载质量与整车整备质量的比值,即。该系数反映了汽车的设计水平和工艺水平,值越大,说明该汽车的结构和制造工艺越先进。根据表2-2可知装汽油机的货车为0.801.10,则取=1.00。表2-2 货车的质量系数车型 参数总质量/t货 车1.80.801.106.0100km/h的汽车,加速时间常用加速到100km/h所需的时间来评价。对于低于100km/h的汽车,加速时间可用加速到60km/h所需的时间来评价。 (3)上坡能力 用汽车满载时在良好路面上的最大坡度阻力系数来表示汽车的上坡能力。因乘用车、货车、越野汽车的使用条件不同,对它们的上坡能力要求也不一样。通常要求货车能克服30%坡度,越野汽车能克服60%坡度。(4)汽车比功率和比转矩 比功率是汽车所装发动机的标定额定功率与汽车最大总质量之比,即。它可以综合反映汽车的动力性,比功率达的汽车加速性能、速度性能要好于比功率小些的汽车。比转矩是汽车所装发动机的最大转矩与汽车总质量之比,=/。它能反映汽车的牵引能力。2、燃油经济性参数汽车的燃油经济性用汽车在水平的水泥或沥青路面上,以经济车速或多工况满载行驶百公里的燃油消耗量(L/100km)来评价。该值越小燃油经济性越好。未来的发展趋势是百公里燃油消耗量继续减少,如正在研制的超经济型乘用车的目标百公里燃油经济消耗量为3L/100km。货车有时用单位质量的百公里油耗量来评价,如表2-5所示。表2-5 货车单位质量百公里燃油消耗量总质量/t汽油机柴油机6122.682.821.551.86122.502.601.431.533、转向盘转至极限位置时,汽车前外转向轮轮辙中心在支承平面平面上的轨迹元直径,成为汽车最小转弯直径。它是用来描述汽车转向机动性,是汽车转向能力和转向安全性能的一项重要指标。货车的最小转弯直径见表2-6。表2-6 货车的最小转弯直径车 型级 别/m商用货车最大总质量/t1.88.012.01.86.010.019.06.014.013.021.04、通过性几何参数总体设计要确定的通过性几何参数有:最小离地间隙、接近角、离去角、纵向通过半径等。货车的通过性参数视车型和用途而异,其范围见表2-7。表2-7 汽车通过性的几何参数车 型/mm/( )/( )/m42货车180300406025452.36.044货车、66货车260350456035451.93.6根据上表中的范围,可分别取最小离地间隙=200、接近角=50、离去角=30、纵向通过半径=4.0。5、操作稳定性参数(1)转向特性参数为了保证有良好的操纵稳定性,汽车应具有一定程度的不足转向。通常用汽车以0.4g的向心加速度沿定圆转向时,前、后侧偏角之差作为评价参数。此参数在13为宜。(2)车身侧倾角汽车以0.4g的向心加速度沿定圆等速行驶时,车身侧倾角控制在3以内较好,最大不允许超过7。(3)制动前俯角为了不影响乘坐舒适性,要求汽车以0.4g的减速度制动时,车身的前俯角不大于1.5。6、制动性参数汽车制动性是指汽车在制动时,能在尽可能短的距离内停车且保持方向稳定,下长坡时能维持较低的安全车速并有一定坡道上长期驻车的能力。GB7258-1997机动车运行安全条件中规定的路试检验行车制动和应急制动性能要求,列于表2-8中。表2-8 路试检验行车制动和应急制动性能要求车 辆 类 型行 车 制 动应 急 制 动制动初车速(km/h)制动距离/mFMDD/(m/s)试车道宽度/m踏板力/N制动初车速(km/h)制动距离/mFMDD/(m/s)操纵力/N()其他总质量的汽 车满载502.570030182.6手600脚700空载4507、舒适性汽车应为乘员提供舒适的乘坐环境和方便的操纵条件,称之为舒适性。其中,汽车行驶平顺性常用垂直振动参数评价,包括频率和振动加速度等,此外悬架动挠度也用来作为评价参数之一。货车的悬架动挠度、静挠度和偏振见表2-9。表2-9 悬架的静挠度、动挠度和偏振n车 型参 数静挠度/mm动挠度/mm偏振n/Hz货 车5011060901.52.22.2.4 发动机的选择及参数确定1、发动机最大功率和相应转速根据所设计汽车应达到的最高车速(km/h),用式(2-2)估算发动机最大功率 (2-2)式中:发动机最大功率(kw);传动效率,为五挡变速器传动效率,为辅助变速器传动效率,为单级减速主减速器传动效率,为传动轴的万向节传动效率;汽车总质量3100kg;g重力加速度9.8m/s;滚动阻力系数,对乘用车,对货车取0.02,矿用自卸车取0.03,用代替,=100km/h,;空气阻力系数,乘用车取0.300.35,货车取0.801.00,客车取0.600.70,取=1;A汽车正面投影面积,A=1.7352.05=3.577。把=0.86、=3100kg、g=9.8m/、=0.02、=100km/h、=1、A=3.577代入式(2-2)中,算得=73kw。货车还能根据同样总质量与同样类型车辆的比功率统计数据,选择发动机的功率。查汽车理论第五版图3-1a)可得,当汽车总质量为3.1t时,对应的汽车比功率为20kw/t,故。综上所述,选择发动机的最大功率为73kw。最大功率对应转速的范围如下:汽油机的在30007000r/min,因乘用车最高车速高,值多在4000r/min以上;总质量小些的货车的值在40005000r/min之间,总质量居中货车的值更低些。柴油机的值在18004000r/min之间。乘用车和总质量小些的货车用高速柴油机,值取在32004000r/min之间;总质量大些的货车的柴油机值在18002600r/min之间。由于本次设计的货车总质量为3100kg,故取值为5000r/min。2、发动机最大转矩及相应转速按式(2-3)计算 (2-3)式中:最大转矩();转矩适应性系数,一般在1.11.3之间选取,取=1.1;为发动机最大功率(kw);最大功率转速(r/min)。将=1.1、=74kw、=5000r/min代入式(2-3)算得。根据以上计算得出的数据选择发动机的型号为五菱柳机LJ469Q-AE8,对应的最大输出功率=74kw、=5000r/min。2.3 轮胎的选择轮胎及车轮用来支撑汽车,承受汽车重力,在车桥(轴)与地面之间传力,驾驶人员经操纵转向轮可实现对汽车运动方向的控制。子午线轮胎的特点是滚动阻力小、温升低、胎体缓冲性能和胎面附着性能都比斜交轮胎要好,装车后油耗低、耐磨损寿命长、高速性能好。因此,选择子午线轮胎。根据前面对轴荷的分配可知本车型为42后轮双胎平头式,满载时前轴为30%,后轴为70%,则:前轴单轮:后轴单轮:式中,=3100kg,n为汽车轮胎数。根据,选择子午线轮胎,轮胎型号为185/65 R14,胎压为320kpa,层数为6层,轮胎使用直径480mm。2.4 本章小结对汽车的总体布局进行设计,并确定了一些所需要的参数,为后面驱动桥的设计作出了铺垫。本章中所设计出的汽车的参数都符合实际情况,故对于后续的内容设计更为明了。第3章 驱动桥总成的结构方案分析和选择3.1 非断开式驱动桥普通非断开式驱动桥,由于结构简单、造价低廉、工作可靠、维修方便,所以广泛用在各种载货汽车、大型客车和公共汽车上。非断开式驱动桥的桥壳是一根支撑在左右驱动车轮上的刚性空心梁,主减速器、齿轮车速器和半轴安装在空心钢梁里面,这样的话,驱动桥、驱动车轮均属簧下质量,从而增大了簧下质量,故而车桥要承受不平路面的冲击载荷,从而不利于汽车的平顺性、通过性和操纵稳定性,这是其缺点。非断开式驱动桥结构如图3-1所示。图3-1 非断开式驱动桥1-主减速器;2-套筒;3-差速器;4、7-半轴;5-调整螺母;6-桥壳3.2 断开式驱动桥断开式驱动桥与非断开式驱动桥的区别在于,断开式驱动桥没有一个连接左右驱动车轮的刚性整体外壳或梁。断开式驱动桥的桥壳是分段的,并且彼此之间可以做相对运动,两侧的驱动车轮还可以相对与车架或车厢做上下摆动。所以这种驱动桥有较高的通过性、平顺性和乘坐舒适性,另外它基本上全是与独立悬架相匹配,故又为独立悬架驱动桥。那么在这种桥的中段,主减速器和差速器等是悬置在车架横梁或车厢的底板上,或与脊梁式车架相连接,所以主减速器、差速器与传动轴及一部分驱动车轮装置的质量均为簧上质量,从而大大减少了簧下质量。汽车悬架总成的类型及减震装置的工作特性是影响汽车行驶平顺性的主要原因,而簧下质量的大小对其平顺性也有显著影响。由于断开式驱动桥簧下质量小,由于独立悬架相匹配,致使车轮与地面的接触情况和适应各种地形路况较好,由此可大大减少汽车在不平路面上行驶时的振动和车箱倾斜度,从而提高了汽车的行驶平顺性和平均速度,减少了车轮和车桥上的动载荷及零件的损坏。但是由于断开式驱动桥及想配合的独立悬架结构复杂,成本高,故这种结构主要用于对行驶平顺性要求较高的部分轿车和越野车上。断开式驱动桥结构如图3-2所示。图3-2 断开式驱动桥综上所述,考虑到所设计的是微型载货汽车的载重和各种设计要求,故本设计采用非断开式驱动桥。3.3 本章小结分析非断开式驱动桥和断开式驱动桥特点,确定了本设计采用非断开式驱动桥。第4章 主减速器设计4.1 主减速器结构形式选择主减速器的结构形式主要是根据主动齿轮和从动齿轮的安装方法、齿轮类型以及减速形式的不同而不同。4.1.1 主减速器减速形式选择主减速器的减速形式分为单级减速、双级减速、双数减速、单机贯通、双级贯通、主减速及轮边减速器等。1、单级主减速器 如图4-1所示为单级主减速器、由于单级主减速器结构简单、质量小、尺寸紧凑及制造成本低等的优点,故而广泛用在主加速比各种中小型汽车上。单级主减速器大部分是采用一对螺旋锥齿轮或双曲面齿轮传动,当然也有采用涡轮传动。 图4-1 单级主减速器 图4-2 双级主减速器2、双级主减速器如图4-2所示为双速主减速器,有两级减速齿轮组成,其结构复杂、质量大制造成本也较高,因此此主减速器主要用于主减速比在7.612,且采用单级主减速器不能满足既定的主减速比的重型汽车上。3、双速主减速器双速主减速器主要用于载荷及道路状况变化大、只用条件非常复杂和恶劣的重型载货汽车。其中低速大传动比,主要用于车辆满载并牵引车辆爬陡坡或通过坏路面时具有足够的动力性;高速小传动比,主要用于车辆在良好的硬质路面高速行驶,从而保证其有良好的经济性,当然也提高了车辆的适应性。但因其增加了复杂结构和操纵机构,从而加大了驱动桥的质量,提高了制造成本,因此,有时也被多挡变速器所取代。4、单级贯通式主减速器单级贯通式主减速器主要用于多桥驱动汽车的贯通桥上,其优点是结构相对简单、主减速器尺寸紧凑、质量较小,并可以使用后桥的大部分的零件,尤其是桥壳半轴等主要零件,所以其通用性较好。5、双级贯通式主减速器主要用于传动比以上的中型汽车的贯通桥上。主要有锥齿轮-主齿轮式和圆柱齿轮-锥齿轮式两种结构形式。其中,锥齿轮-圆柱齿轮双级贯通式主减速器的特点是有较大的主减速比,其结构的高度尺寸大,主动锥齿轮的工艺性差,然而从动锥齿轮有需要采用悬臂安装,导致支撑刚度差、同时拆卸也不方便。那么圆柱齿轮-锥齿轮式双级贯通式主减速器它结构紧凑、高度尺寸小,但是其第一级斜齿圆柱齿轮副的减速比较小,为此,在采用这种布置形式时的汽车,为了增大驱动桥的减速比,须增加轮边减速器。6、单级(或双级)主减速器附轮边减速器此类主减速器还是主要用于矿山、水利及其他大型工程等所有的重型载货汽车上,还有工程和军事上用的重型牵引越野汽车及大型公共汽车上等,要求有较高的机动性,和较强的通过性,而车速可相对较低,所以其抵挡的传动比都比较大。在重型汽车、大型公共汽车的驱动桥的设计时,为了使分动器、减速器、车速器、传动轴等总成不因承受过大的转矩而使他们的尺寸和质量过大,应将传动系的传动比尽可能多的分配给驱动桥,从而会导致其主减速比要求会过大。当其值12时,就需采用单级(或双级)主减速器附加轮边减速器的结构形式,将驱动桥一部分减速比分给安装在轮毂中间或轮边减速器。从而这样就减小了驱动桥中部主减速器的轮廓尺寸、增加了离地间隙,还可得到大的驱动桥减速比。但是加装轮边减速器的车桥会使驱动桥的结构复杂、成本提高,因此只有当驱动桥的主减速比大于12时才采用轮边减速器。综上所述,由于本设计是微型载货汽车,要求的传动比小于7,且由于单级主减速器具有结构简单。质量小、尺寸紧凑以及制造成本低的优点,故本设计采用单级主减速器驱动桥传动。4.1.2 主减速器齿轮类型选择按照齿轮副的结构形式分类,主减速器的齿轮传动可分为弧齿锥齿轮传动、双曲面齿轮传动、圆柱齿轮传动(可分为轴线固定式齿轮传动和轴线旋转式齿轮传动也就是行星齿轮传动)和蜗杆涡轮传动等形式1,如图4-3所示。a)弧齿锥齿轮传动 b)双曲面齿轮传动 c)圆柱齿轮传动 d)蜗杆-涡轮传动图4-3 减速器齿轮传动形式1、弧齿锥齿轮传动弧齿锥齿轮传动的特点是主、从动齿轮的轴线是相较于一点的,轴交角是可以任意选取的,但是大多数都是选择轴交角为90度的布置方案。由于齿轮端面重叠的影响,在齿轮啮合传动时至少是有两对以上的齿轮同时啮合参与传动,再加之齿轮不是在齿的全长上同时啮合,而是逐渐由齿的一端连续而平稳的转向另一端,因此,弧齿锥齿轮承受载荷大,传动平稳,噪音和振动小,但其对啮合的精度要求高,锥顶稍有不吻合就会使工作条件恶化,从而加剧此轮的磨损,噪音变大1。2、双曲面齿轮传动双曲面齿轮传动的特点:双曲面齿轮传动时其主、从动齿轮的轴线是不相较于一点,而是呈空间交叉,即主动齿轮轴线相对于从动齿轮轴线向上或向下偏移了一定的距离E,称为偏移距1。当偏移距达到一定的程度,就可以使一个齿轮轴从另一个齿轮轴旁通过,这样可以在每个齿轮的两边布置尺寸更加紧凑的支撑,从而可以增强支撑刚度、保证齿轮正常啮合,以提高齿轮的寿命。双曲面齿轮的偏移距使得其主动齿轮的螺旋角大于从动齿轮的螺旋角。因此,双曲面传动齿轮副的法向模数或法向周节虽相等,但端面模数或端面周节是不相等的。因为主动齿轮的端面模数大于从动齿轮,这一情况就使得双曲面齿轮传动的主动齿轮比弧齿锥齿轮传动的主动齿轮有更大的直径和刚好的刚度与强度。其增大的程度与偏移距有关。另外,由于双曲面齿轮传动的主动齿轮的直径和螺旋角都比较大,所以相啮合齿轮的当量曲率半径较相应弧齿锥齿轮大,从而降低了齿面间的接触应力。随偏移距的不同,双曲面齿轮与接触应力相当的螺旋锥齿轮比较,负荷可提高至175%。双曲面主动齿轮的螺旋角较大,还可减少不发生跟切的最小齿数,从而有利于增大传动比。当要求传动比较大而轮廓尺寸又有限时,采用双曲面齿轮传动比较合理。当两种传动的主动齿轮直径一样时,则双曲面从动齿轮的直径要比弧齿锥齿轮的要小,这对于主减速比的传动有优势。当传动比小于2时,双曲面主动齿轮相对于螺旋锥齿轮就显得过大,这是选用螺旋锥齿轮更加合理,因为后者具有更大的差速器利用空间。因为双曲面主动齿轮螺旋角的增大,导致进去啮合的平均齿数增加,因而双曲面齿轮传动要比螺旋锥齿轮传动更加平稳、噪音更加低、强度也相应增大。双曲面齿轮还可以给汽车的总体布置带来方便,如:“当主减速器采用下偏置的双曲面车轮时,可降低轿车传动轴的高度,从而可以降低车厢里面地板的高度,从而提高舒适性,并降低轿车的外形高度”。3、圆柱齿轮传动 圆柱齿轮传动广泛用于发动机横直,且是前置前驱的乘用车驱动桥上和双级主减速器驱动桥以及轮边减速器上。此时,齿轮皆应采用斜齿轮,以增大重合度,使齿轮在啮合传动时更加平稳、噪音更加小。4、蜗杆-涡轮传蜗杆-涡轮传动简称蜗轮传动。主要是用在有较大的传动比的载重汽车上,与其他齿轮传动相比较,她具有质量及体积均较小、传动比大、工作稳定、无噪音、便于布置在贯通式多级驱动桥上,易于汽车的总体布置,还有结够简单、传递载荷大、使用寿命长 、拆卸方便、调整容易等有点,但其缺点是:要用昂贵的有色金属青铜,故而成本高,还有传动效率低。综上:基于本设计的是微型载货汽车,传动比小于7,为中等传动比设计传动,故本设计采用弧齿锥齿轮传动。4.1.3 主减速器主从动锥齿轮支撑方式选择 1、主动锥齿轮的支撑主减速器必须保证主、从动齿轮具有良好的啮合状况,才能使他们彼此很好的工作。齿轮的正确啮合,除了与齿轮的加工质量、装配调整以及轴承、主减速器壳体的刚度有关外,还与齿轮的支撑刚度有关。现代汽车主减速器主动齿轮的支撑形式主要有以下两种:(1)悬臂式图4-4 悬臂支撑如图4-4所示,悬臂式支撑的结构特点是,在锥齿轮大端一侧有较长的轴,并在上面安装一对圆锥滚子轴承。为了改善支撑刚度,因减小悬臂长,并增加两端支撑的距离b,还应使两端圆锥滚子轴承的大端朝外,是作用在齿轮上离开锥顶的轴向力又靠近齿轮的轴承承受,而反向轴向力有另一轴承承受。为了进一步增加支撑刚度,支承距离b应大于2.5倍的悬臂长度,且应比齿轮节圆直径的70%还大,另外靠近齿轮的轴径应不小于尺寸。为了方便拆装,靠近齿轮的轴承轴径比另一轴承的支撑轴径要打一些。悬臂式支撑其特点是结构简单,支承刚度较差,用于传递转矩较小的主减速器上、轻型货车的单级主减速器及许多双级主减速器上。(2)跨置式图4-5 跨置式支撑如图4-5所示,齿轮两端都是以轴承支撑,故又称为两端支撑。那么跨置式支撑的特点是:在锥齿轮的两端上均有轴承,这样的话可以大大增加支撑刚性,又使轴承负荷较小,齿轮的啮合条件就得到了改善,因此齿轮的承载能力是要高于悬臂式支撑。由于此轮大端一侧轴径上的两个相对安装的圆锥滚子轴承指间距离很小,可以缩短主动齿轮轴的长度,使布置更加紧凑,并可减小传动轴的夹角,有利于整车布置。2、从动锥齿轮的支撑从动锥齿轮多采用圆锥滚子轴承支撑如图4-6所示。为了增加支撑刚度,两轴承的圆锥滚子大端应向内,以减小尺寸c+d,为了是从动锥齿轮背面的差速器壳体处有足够的位置设置加强肋,以加强支撑刚性和稳定性。c+d应不小于从动锥齿轮大端分度圆直径的70%。为了使载荷能够均匀的分配两轴承上,应是c大于d。图4-6 从动锥齿轮支撑形式4.2 主减速器齿轮计算与校核主减速比,驱动桥的离地间隙和计算载荷,为汽车主减速器设计的原始数据,在汽车总体设计时已经确定了。4.2.1 主减速比确定主减速比对汽车主减速器的结构形式、质量大小、轮廓尺寸以及变速器处于最高档位时汽车的动力性和燃油经济性都有直接的影响。的选择应在汽车总体设计时和传动系的传动比一起由整车动力计算来确定。通过优化设计,对发动机和传动系参数作最佳匹配的方法来选择值,可以使汽车获得最佳的动力性和燃油经济性。对于具有很大功率储备的轿车、长途汽车,尤其是竞赛车来说,在给定发动机最大功率及其转速的情况下,所选择的值应能保证这些汽车有尽可能高的车速。此时应按照式(4-1)来确定: (4-1)式中:车轮的滚动半径,; 最高车速(公里/小时);最大功率时的发动机转速(转/分);变速器最高档传动比,。将以上数据带入式(4-1)中得对于货车而言,为了得到足够的功率储备而使最高车速稍有下降,一般选得比上式求得的大10%25%,故的取值变为4.955.62,取=5.3。按以上所得出的主减速器的传动比还需根据主减速齿轮可能有的齿数予以校正。4.2.2 变速器传动比及各挡传动比确定在确定变速器传动比时,需考虑驱动条件和附着条件。1、为了满足驱动条件,其值应符合式(4-2)的要求: (4-2)式中,G为汽车总质量31009.8=30380N;为滚动阻力系数,取0.02;为最大爬坡度对应的角度,取为16.7,为车轮滚动半径,取为0.24m;为发动机最大转矩,取为153Nm;为主减速器传动比,取为5.3;为传动系的传动效率,取为0.86。将数据G=30380N、=0.02、=16.7、=0.24m、=153Nm、=5.3、=0.86代入上式算得。2、为了满足附着条件,其值应符合式(4-3)的要求: (4-3)式中,驱动轮所承受的静载荷,;为轮胎与地面的附着系数,取为0.8。把数据=21266N、=0.8、=0.24m、=153Nm、=5.3、=0.86代入式(4-3)算得5.85。取得。 按等比数列分配其他各挡传动比,则,=5,=3.3,=2.2,=1.46,=1。4.2.3 主减速器齿轮载荷确定1、从动锥齿轮的转矩计算主减速器计算载荷通常是将发动机最大转矩来匹配传动系最低挡传动比时和驱动轮打滑时这两种情况下,作用于主减速器从动齿轮上的转矩的较小值,作为载货汽车和越野汽车在强度计算中用以验算主减速器从动齿轮最大应力的计算载荷。根据发动机最大转矩和最低档传动比计算转矩,按式(4-4)计算。 (4-4)式中:计算转矩,; 发动机最大转矩,; 计算驱动桥数; 分动器的传动比,因无分动器,故; 主减速器传动比; 变速器最低档传动比; 发动机到万向传动轴之间的传动效率,一般取; 液力变矩器变矩系数,因无液力变矩器,故; 由于猛抬离合而产生的动载荷系数,。将、代入式(4-4)得:2、由驱动轮打滑转矩确定从动锥齿轮的计算转矩,按式(4-5)计算: (4-5)式中:汽车满载时一个驱动桥给水平地面的最大负荷,;汽车最大加速度时后轴负荷转移系数,对于商用车,在此取1.1;轮胎的附着系数,对于安装一般轮胎的公路 用汽车,取;轮胎的滚动半径,;,分别是有所计算的主减速器从动齿轮到驱动齿轮之传动效率和减速比(如:轮边减速器)。该车无轮边减速器,故取将数据代入式(4-5)得:3、上述所获得的计算载荷,是在最大转矩时而不是在正常持续运转下的转矩,故不能用作疲劳损坏的依据。对于公路车来说,按照汽车日常行驶时的平均转矩来确定从动锥齿轮的计算转矩,按式(4-6)计算。 (4-6)式中:汽车日常行驶平均牵引力,(其中为满载总重,为汽车正常使用时的爬坡能力,一般轿车取0.08;载货汽车和公共汽车取0.050.09;长途汽车取0.060.10;越野车取0.090.30。在此取0.08;为性能系数,取为0)故;、见式(4-3)和(4-4)。将,等参数代入式(4-6)得:由于,所以主减速器主动齿轮的转矩计算按式(4-7)和式(4-8)确定 (4-7) (4-8)式中:,从动锥齿轮最大转矩和平均转矩;主减速比;主、从动锥齿轮间的传动效率,对于弧齿锥齿轮取:0.95.4.2.4 主减速器锥齿轮基本参数确定主减速器锥齿轮的主要参数有主、从动齿轮的齿数、,主、从动锥齿轮大端分度圆直径、端面模数,主、从动锥齿轮齿面宽、,中点螺旋角、法向压力角等。1、主、从动锥齿轮齿数和的选择。对于单级主减速器,当较大时,则应该使主动齿轮的齿数取得较小一点,以增加驱动桥的离地间隙。当时,最小值可以取5,但是为了使啮合平稳和提高疲劳强度,最好大于5;当较小时,即时,可取712,但是这常会因主、从动齿轮齿数太多,尺寸太大而影响所要求车桥的最小离地间隙。为了使两次轮磨合均匀,主、从动齿轮的齿数、之间应避免有公约数;另外得到理想的齿面重叠系数,其齿数之和对于货车来说应不小于40,对于轿车应不小于50。本设计的汽车的主减速比为5.3,主减速比较小,选择,因为,所以:,取因此实际的主减速比为5.375;,所以满足要求。2、从动齿轮大端分度圆直径和端面模数的确定。对于单级减速器,增大尺寸就会影响驱动桥壳的最小离地间隙,减小又会影响跨置式主动齿轮的前端支撑座的安装空间以及差速器的安装。根据式(4-9)初选: (4-9)式中:从动锥齿轮的节圆直径,mm; 直径系数,一般取1316; 从动锥齿轮的就算转矩,。代入数据得:又因为要满足式(4-10): (4-10)同时,还要满足式(4-11): (4-11)式中:模数系数,取0.30.4。代入数据得:取:,代入式(4-10)得:,在范围之内,满足条件。3、主、从动锥齿轮齿面宽度和的确定。锥齿轮齿面过宽的话并不能增大齿轮的强度和刚度,反而会导致因齿轮轮齿小端齿沟变窄引起的切削刀头顶面过窄及倒圆角过小,这样不但会减小齿根圆角半径,还增加了集中应力,降低了刀具的使用寿命。另外,因为安装时有位置偏差或由于制造、热处理变形等原因会使齿轮工作时载荷集中于齿轮小端,从而引起齿轮小端过早损坏和疲劳损伤。齿面过宽会引起装配空间减小,齿面过窄齿轮表面的耐磨性和齿轮的强度会降低。对于从动锥齿轮的齿面宽度,推荐不大于其节锥距的0.3倍,而且应满足,一般也推荐,取。一般习惯是锥齿轮的小齿轮齿面宽比大齿轮稍大,使其在大齿轮额两端都超过一定的宽度,通常小齿轮的齿面宽度加大到大齿轮的齿面宽度的10%较为合适,所以在此取。4、中点螺旋角的确定。螺旋角沿齿宽是变化的,齿轮大端的螺旋角更大,齿轮小端的螺旋角最小,弧齿锥齿轮的中点螺旋角是相等的。那么在选择时我们应充分考虑他对齿面重合度的影响,还有齿轮强度和轴向力大小的影响,越大,则越大,同时啮合的齿数就越多,那么传动就越平稳,噪音也就越低,并且齿轮的强度也就越高。汽车主减速器锥齿弧齿轮的平均螺旋角为,然而商用车应选择较小的螺旋角值,以防止轴向力过大,通常选取。5、主减速器主、从动齿轮螺旋方向的选择。如图4-7所示,对于锥齿轮的螺旋方向,那么从锥顶来看,齿形从中心线上半部分向左倾斜为左旋,向右倾斜为右旋。主、从动锥齿轮的螺旋方向是相反的,另外锥齿轮螺旋方向与锥齿轮的旋转方向会影响其所受轴向力的方向。档变速挂前进挡时,应使主动锥齿轮的轴向力离开锥顶方向,这样的话可使主、从动锥齿轮有分离的趋势,防止轮齿因卡死而损坏。所以主动齿轮选择为左旋,从锥顶方向看为逆时针方向运动,这样从动锥齿轮就为右旋,从锥顶方向看为顺时针。图4-7 弧齿锥齿轮的螺旋方向及轴向力6、法向压力角加大法向压力角是可以增加齿轮的强度,以减少齿轮不发生跟切的最小齿数,但是对于较小尺寸的齿轮来说,压力角过大会容易使齿顶变尖以及刀尖宽度过小,并会使齿面重合度下降,因此,对于轻负荷工作的齿轮一般情况下采用小压力角,可以使齿轮平稳运转、噪音低。对于弧齿锥齿轮,乘用车的一般选用或,商用车的选用或。在本设计之中,由于是微型货车,即商用车,因此选择压力角为。4.2.5 主减速器弧齿锥齿轮几何尺寸计算 主减速器弧齿锥齿轮几何尺寸计算见表4-1表4-1 主减速器弧齿锥齿轮的几何尺寸计算表序号目录计算公式计算结果1主动齿轮齿数82从动齿轮齿数433端面模数64齿面宽度 5法向压力角6轴交角7分度圆直径 8螺旋角9节锥角10节锥距11齿根角12齿顶高13齿根高14齿顶圆直径15齿根圆直径16根锥角 4.2.6 主减速器弧齿锥齿轮强度计算在完成了主减速器齿轮的几何计算之后,应该对其强度进行计算,以保证其有足够的强度和寿命以及安全可靠的工作。在进行齿轮的强度的计算之前,应先了解齿轮被破坏的形式以及其影响因素。齿轮的损坏形式常见有齿轮折断、齿面点蚀、齿面胶合、齿面磨损等。在此轮的设计当中,通常需要对齿轮的单位齿长圆周力、齿轮弯曲强度和齿面接触强度进行强度校核,在实际设计当中还要依据台架和道路试验以及实际使用情况来检验。1、单位齿长圆周力在汽车主减速器齿轮的表面耐磨性,常常用其在齿轮上的假定单位压力,即单位齿长圆周力;按式(4-12)计算。 (4-12)式中:作用在齿轮上的圆周力(N) 从动齿轮的齿面宽,。按发动机最大转矩计算时,由式(4-13)计算。 (4-13)式中:猛接离合器所产生的动载系数,取为1;发动机的最大转矩,为;液力变矩器变矩系数,取为1;变速器一挡传动比,取为5;分动器传动比,取为1;发动机到万向传动轴之间的传递效率,取为0.9;主动锥齿轮中点分度圆直径,取为48mm;把以上数据代入式(4-13)算得。见表4-2。表4-2 单位齿长圆周力许用值汽车类型参数/()(按发动机最大转矩计算时)/()(按驱动轮打滑转矩计算时)轮胎与地面的附着系数商用车货车一挡二挡直接挡1429一25014290.85按驱动轮打滑的转矩计算时,由式(4-14)计算。 (4-14)式中:满载状态下驱动桥上的静载荷,取为21266;汽车最大加速度时的后轴负荷转移系数,乘用车=1.21.4,商用车=1.11.2,本设计取1.1;轮胎与地面间的附着系数,对于安装一般轮胎的公路用汽车,在良好的混凝土或沥青上,可取0.85,对于安装防侧滑轮胎的乘用车,可取1.25,对于越野车,值变化较大,一般取1,故取0.85;车轮滚动半径,取为0.24m;从动锥齿轮的分度圆直径,取为258mm;从动锥齿轮齿面齿宽40mm;主减速器从动齿轮到车轮之间的传动比,取为1;主减速器主动齿轮到车轮之间的传动效率,取为1。把数据代入式(4-14)得:式(4-14)算出来的一挡单位齿长圆周力小于其对应的许用值,故符合要求。虽然最大附着力距产生的p很大,但由于发动机最大转矩的限制p只有1429可知校核结果满足要求。2、齿轮的弯曲强度计算汽车主减速器齿轮的齿根弯曲应力按式(4-15)计算。 (4-15)式中:该齿轮的计算转矩,;超载系数;在此取:;尺寸系数,反应材料的不均匀性,其与齿轮尺寸和材料热处理有关,当时,在此;齿面载荷分配系数,跨制式结构:=1.01.1,悬臂式结构:=1.001.25,取为1.0;质量系数,对于载货汽车驱动齿轮而言,当齿轮接触良好,周节及经向跳动精度高时,可取1.0;计算齿轮的齿面宽度:齿轮端面模数,mm;响计算弯曲应力的综合系数(或几何系数),它应综合考虑了齿形系数、载荷作用点的位置、载荷的齿间分布、有效齿面宽、应力集中系数及惯性系数等对弯曲应力的影。参照图4-8取,。图4-8 齿轮计算用弯曲综合系数J代入数据得:主动锥齿轮: 从动锥齿轮: 根据表4-3得汽车驱动桥齿轮的最大许用弯曲应力为,经过上述验算知:,所以主减速器齿轮满足弯曲强度要求。 表4-3 汽车驱动桥齿轮的许用应力计算载荷许用弯曲应力许用接触应力差速器齿轮的许用弯曲应力最大计算转矩7002800980平均计算转矩210.91750210.93、齿轮的接触强度计算:锥齿轮的齿面接触应力按式(4-16)确定。 (4-16)式中:主动锥齿轮大端分度圆直径,;主动锥齿轮的计算转矩;材料的弹性系数,对于钢制齿轮副取;,见式(4-15)下的说明;尺寸系数,它考虑了齿轮的尺寸对其淬透性的影响,在此取1.0;表面质量系数,决定于齿面最后的加工性质(如铣齿、磨齿等),表面覆盖层的性质(如镀铜、磷化、喷丸处理等)以及表面粗超度,一般情况下,对于制造精确的齿轮可取1.0;计算接触应力的综合系数(或称几何系数)。它综合考虑了啮合齿面的相对曲率半径,载荷作用位置、齿轮间的分配系数、有限齿宽以及惯性系数的影响,按图4-9选取图4-9 锥齿轮接触计算用综合系数按照计算得:按照计算得:上诉按照min计算的最大接触应力不应超过2800MPa;按计算的疲劳接触应力不应超过1750MPa,主、从动齿轮的齿面接触应力是相同的。所以齿轮强度满足设计要求。4.2.7 主减速器齿轮材料选择及热处理在汽车的行驶传动过程当中,驱动桥锥齿轮的工作条件是比较恶劣的,与传动系其他齿轮相比,其具有载荷大、作用时间长、变化多、还有冲击等一些特点。因此,得加强传动系中主减速器锥齿轮的表面硬度以及耐磨性。所以,主减速器锥齿轮的材料应满足以下条件要求:(1)具有高度的弯曲疲劳强度和表面接触疲劳强度,齿面有很高硬度,以保证齿轮表面有高的耐磨性;(2)齿轮材料应有良好的锻造性能、切削加工性能以及热处理性能,并且在热处理之后变形小,变性规律易控制。(3)齿轮芯部应有良好的韧性,以适应冲击载荷,避免在冲击载荷下齿根被折断;在选择齿轮合金材料时,要尽量少选用含镍、铬等的材料,而是选用含锰、硼、钛、钼、硅钒等元素的合金钢。汽车主减速器锥齿轮和差速器锥齿轮目前常用合金钢制造,主要有、和等。渗碳合金钢的优点是,经过渗碳后其表面可以得到含碳量较高的渗碳硬化层,具有相当高的耐磨性和抗压性,而芯部又较软,具有良好的韧性。因此,这类材料的弯曲强度、表面接触强度和承受冲击的能力均较好,另外由于钢材本身有较低的含碳量,使其具有良好锻造性能和切削加工性能。但也有缺点,就是热处理的费用较高,表面硬化层以下的基底较软,在承受很大压力时可能产生塑性变形,还有如果渗碳层与芯部的含碳量相差过多时,便会引起表面硬化层脱落。为了改善新齿轮的磨合,防止其在工作初期出现早期磨损、擦伤、胶合或咬死等损伤,在锥齿轮进行热处理后,要作 厚度为的磷化处理或镀铜、镀锌处理。对齿面要进行应力喷丸处理,可以提高齿轮的寿命。对于滑动速度高的齿轮还可以进行渗硫处理以提高耐磨性,渗硫处理时温度低,度不会引起齿轮变形,渗硫处理后摩察系数可以显著降低,故即使是润滑条件不良时,也可以防止齿轮胶合、咬死或擦伤等现象产生。4.3 主减速器轴承计算1、锥齿轮齿面上的的作用力为计算作用在齿轮上的圆周力,首先需要确定齿轮轴上的计算转矩。实践表明,轴承的主要损坏形式一般为疲劳损伤,所以应按照输入的当量转矩进行计算。作用在主减速器主动锥齿轮上的当量转矩可以按照式(4-17)计算: (4-17)式中:,;,可以参考表4-4选取;表4-4 及的参考值挡位变速器车型轿车公共汽车载货汽车挡挡带超速挡带超速挡挡挡挡挡挡超速挡19901420750.82.51680.7262765141550-301311850.53.5759-300.5251577.5挡挡挡挡挡超速挡60605073656060656050507070606070706060-755060706050607070-705060707060将数据带入式(4-17)得:齿宽中点处的圆周力F,按式(4-18)计算。 (4-18)式中:,;主动锥齿轮分度圆直径,其中,代入得。根据:,上的圆周力是相等的。锥齿轮上的轴向力和径向力:图4-10 主动锥齿轮齿面的受力图如图:4-10主动齿轮的螺旋方向为左旋,从锥顶看为逆时针方向,为作用在节锥面上的齿面宽中点A处的法向力,在A点处的螺旋方向的法平面内,将分解为两个相互垂直的力,垂直于且位于所在的平面,位于以为切线的节锥切平面内。在此平面内又可以分为沿切线方向的力和沿节圆母线方向的力。与之间的夹角为螺旋角,与之间的夹角为法向压力角,这样有: (4-19) (4-20) (4-21)如式(4-24)和式(4-25)所示 (4-22) (4-23)如式(4-24)和式(4-25)所示 (4-24) (4-25)上述七式中: ; 。将参数代入上述四式得:2、主减速器轴承的载荷计算(1)主动锥齿轮轴承载荷计算当锥齿轮面上所受的圆周力、轴向力和径向力计算确定后,根据主减速器齿轮轴承的布置尺寸,即可求出轴承所受的载荷。图4-11 主减速器轴承的布置尺寸如图4-11,在锥齿轮轴承的布置上,应使两轴承支撑中心之间的距离比锥齿轮面宽中点的悬臂长度大2.5倍以上,同时尺寸应比齿轮节圆直径的还大,另外靠近齿轮的轴径应不小于尺。由于主动锥齿轮的轴向齿宽,以及中等宽度系列轴承内圈宽度估算出悬臂长,初选。轴承的内径必须大于,有前面对锥齿轮的受力结果可知,主动锥齿轮所受到的轴向力要比径向力大得多,因此应采用大锥角圆锥滚子轴承。由于,所以根据轴径初选轴承(靠近锥齿轮的轴承)的型号为,其额定动载荷,判断系数;为了保证拆装维修方便轴的内径应该比轴承的内径要大,所以初选轴承(远离锥齿轮端)的型号为,其额定动载荷,判断系数。由此可以得到:,其中为锥齿轮的实际宽度,、均为轴承30209的安装尺寸,为轴承内圈支撑凸台宽度。轴承:径向力按式(4-26)计算: (4-26) 轴向力按式(4-27)计算: (4-27) 轴承:径向力按式(4-28)计算: (4-28)轴向力按式(4-29)计算: (4-29)(2)从动锥齿轮轴承载荷计算从动锥齿轮的布置形式如图4-11,为了增加支撑刚度,两轴承的圆锥滚子大端应向内,以减小尺寸c+d,为了是从动锥齿轮背面的差速器壳体处有足够的位置设置加强肋,以加强支撑刚性和稳定性。c+d应不小于从动锥齿轮大端分度圆直径的70%。为了使载荷能均匀分配到两轴承上,应是c小于d。因为,所以,所以初选,。所以:从动齿轮中点分度圆直径:轴承:径向力按式(4-30)计算: (4-30)轴向力按式(4-31)计算: (4-31)将各参数代入(4-30)和(4-31)得:轴承: 径向力: (4-32) (4-33)将各参数带入(4-32)和(4-33)得:4.4 锥齿轮轴承型号确定1、主动锥齿轮轴承的确定轴承:径向力: 轴向力:计算当量动载荷:查阅文献2,锥齿轮圆锥滚子轴承30307的计算系数e=0.31,由上式可知,由此可得:,。当量动载荷:轴承 (4-34)式中:轴承计算转速,r/min;,分别为主、从动锥齿轮的计算转速,对于载货汽车的平均行驶速度可取,在这里取;车轮滚动半径;则,所以; ; ; 对于滚子轴承,。将各参数代入式(4-34)得: 若大修里程定位公里,可计算出预期寿命按式(4-35)计算: (4-35)经过比较,因为,故轴承符合要求。轴承:径向力: 轴向力:计算当量动载荷:查阅文献2,锥齿轮圆锥滚子轴承30209的计算系数e=0.31,由上式可知,由此可得:,。所以当量动载荷:将轴承各参数带入式(4-35)得:由式(4-35)知:,显然,。2、从动锥齿轮轴承的确定轴承: 径向力: 轴向力:计算当量动载荷:,以及上式可知,由此可得:,。当量动载荷: (4-36)式中:、见式(4-34)可知;由式(4-32)知:,所以轴承的额定工作寿命为:,所以:将轴承的数据带入式(4-36)得:由,查阅参考文献2选轴承为,其动载荷为满足要求。轴承: 径向力: 轴向力:计算当量动载荷:,以及上式可知,由此可得:,。当量动载荷:将轴承的各参数代入式(4-36)得:由,查阅参考文献2选轴承为,其动载荷为满足要求。4.5. 主减速器锥齿轮轴设计4.5.1 主减速器锥齿轮轴结构设计主动锥齿轮轴采用与齿轮相同的材料,为锻造合金钢。根据前面所设计出来齿轮的参数尺寸和轴承的大小以及装配时所要求对的间隙等,再参照现有车型对轴进行结构设计。如图4-12所示:轴的各段尺寸分别为:图4-12 主动锥齿轮轴的结构设计第1段:主动锥齿轮端,宽度为;第2段:与轴承B配合轴肩部分,宽度为;第3段:与轴承配合段,宽度为;第4段:直径为,宽度为;第5段:与轴承配合段,宽度为;第6段:花键段,直径为,宽度为;第7段:螺栓连接段,;4.5.2 主减速器主动齿轮轴校核1、齿轮和轴承上的载荷(1)齿轮上的载荷由前面可知,齿轮的圆周力,齿轮上轴向力,齿轮上的径向力(2)轴承上的载荷轴承: 轴向力: 径向力:轴承:轴向力: 径向力:图4-13 主动锥齿轮轴受力图如图4-13,因轴受到的轴向力和径向力与轴承受到的轴向力和经向力别为一对作用力和反作用力。如图规定齿轮受到的轴向力和经向力为正,前、后轴承给轴的力的方向分别为与圆锥此轮受的力方向相反,则为负;径向力为正,为负。后面的花键轴和螺栓轴可以不校核,其结果影响不大。2、轴承上的支反力(1)水平面上:受力图如图4-14所示: 图4-14 水平面上受力图支反力按式(4-37)和式(4-38)计算: (4-37) (4-38)代入数据得: 求出水平面的弯矩:水平面弯矩图如图4-15所示: 图4-15 水平面上弯矩图(2)垂直面上:受力图如图4-16所示:图4-16 垂直面上的受力图支反力按式(4-39)和式(4-40)计算:(4-39)(4-40)代入数据得:求出垂直面的弯矩:轴向力产生的转矩:按照逆时针为正得垂直面弯矩为负:垂直面弯矩图如图4-17所示:图4-17 垂直面弯矩图转矩:转矩图如图4-18所示: 图4-18 转矩图合成弯矩:合成弯矩图如图4-19所示: 图4-19 合成弯矩图由图4-19知危险界面出现在处,计算危险截面上轴的直径,轴的材料为,经过调制等处理后弯曲应力为,按式(4-41)计算: (4-41)式中:为危险截面合成玩弯矩;危险截面轴径;将数据代入式(4-41)得:因为,所以轴的设计满足要求。4.6 主减速器润滑主加速器及差速器的齿轮、轴承以及其他摩擦表面均需润滑,其中尤其应注意主减速器主动锥齿轮的前轴承的润滑,因为其润滑不能靠润滑油的飞溅来实现。为此,通常是在从动齿轮的前端靠近主动齿轮处的主减速壳的内壁上设一专门的集油槽,将飞溅到壳体内壁上的部分润滑油收集起来再经过近油孔引至前轴承圆锥滚子的小端处,由于圆锥滚子在旋转时的泵油作用,使润滑油由圆锥滚子的下端通向大端,并经前轴承前端的回油孔流回驱动桥壳中间的油盆中,使润滑油得到循环。这样不但可使轴承得到良好的润滑、散热和清洗,而且可以保护前端的油封不被损坏。为了保证有足够的润滑油流进差速器,有的采用专门的倒油匙。为了防止因温度升高而使主减速器壳和桥壳内部压力增高所引起的漏油,应在主减速器壳上或桥壳上装置通气塞,后者应避开油溅所及之处。加油孔应设置在加油方便之处,油孔位置也决定了油面位置。放油孔应设在桥壳最低处,但也应考虑到汽车在通过障碍时放油塞不易被撞掉。4.7 本章小结对所设计的中型汽车的减速器结构形式进行了方案的选择,并对减速器的设计作出了详细的设计与计算,包括齿轮的选取与计算,轴承的选择与校核,花键的设计等一些列必需的零件设计。根据所设计处的主减速器的参数校核,满足了疲劳强度计算以及其它的校核都得到了满足,故本次设计合理。第5章 差速器设计及优化5.1 差速器结构及形式选择差速器的结构形式选择,应从所设计汽车的类型以及使用条件出发,以满足该型汽车在给定的实用条件下的使用性能要求。(1)对称式圆锥行星齿轮差速器图5-1 普通对称式圆锥行星齿轮差速器1,12-轴承;2-螺母;3,14-锁止垫片;4-差速器左壳;5,13-螺栓;6-半轴齿轮垫片;7-半轴齿轮;8-行星齿轮轴;9-行星齿轮;10-行星齿轮垫片;11-差速器右半壳如图5-1,普通的对称式行星齿轮差速器由差速器左、右壳,2个半轴齿轮,4个行星齿轮,行星齿轮轴,半轴齿轮及行星齿轮垫片组成。由于其结构简单、工作平稳、制造方便、用在公路汽车上可靠性高等优点,最广泛的用在轿车、客车和各种公路用的载货汽车上,也有一些越野车用这种结构,但要采用防滑措施。(2)强制锁止式防滑差速器强制锁止式防滑差速器就是在普通圆锥齿轮差速器上加装差速锁,必要时将差速器锁止。此时左、右驱动车轮可以传递有附着力决定的全部转矩。当汽车驶入较好路面时,差速器的锁止机构应及时松开,否则将产生与无差速器时一样的问题。(3)自锁式差速器为了充分利用汽车的牵引力,保证转矩在驱动车轮间的不等分配以提高抗滑能力,并避免上述强制锁死止差速器的缺点,创造了各类型的自锁式差速器,常见的有滑块-凸轮式、蜗轮式、自由轮式等。用以评价自锁式差速器性能的主要参数,是它的锁止系数。为了提高汽车的通过性,锁止系数越大越好,但是过大的锁止系数如前所述,不但对汽车转向操纵的轻便灵活性、行驶稳定性、传动系的载荷、轮胎磨损和燃油经济性等都有不同程度的影响,并且无助于进一步提高驱动车轮抗滑能力。因此设计高通过性能汽车的差速器时,应正确选择锁止系数值。经上述方案和查阅文献1,本设计选用对称式圆锥行星齿轮差速器。5.2 差速器齿轮主要参数选择5.2.1 行星齿轮数轿车常用2个行星齿轮,载货汽车和越野车常用4个行星齿轮,少数汽车采用3个行星齿轮。在本设计当中采用4个行星齿轮。5.2.2 行星齿轮球面半径行星齿轮轮半径反映了差速器锥齿轮节锥距的大小和承载能力,可由式(5-1)来确定 (5-1)式中:行星齿轮球面半径系数,=2.53.0,对于有四个行星齿轮的乘用车和商用车取最小值,对于有两个行星齿轮的乘用车及四个行星齿轮的越野车和矿用车取最大值,本设计中取2.5;差速器计算转矩(Nm),=3649Nm。将数据代入上式得=38.49mm。行星齿轮节锥距可按式(5-2)计算 (5-2)带入数据求得=37.7238.10mm,取=38mm。5.2.3 行星齿轮与半轴齿轮参数确定为了得到较大模数从而使齿轮有较高的强度,应使行星齿轮的齿数尽量少,但一般不应少于10.半轴齿轮的齿数采用。半轴齿轮与行星齿轮的齿数比多在的范围内。同时考虑到在任何行星齿轮差速器中,左、右两半轴齿轮之和必须能被行星齿轮的数目所整除,否则将不能安装。在本设计当中取行星齿轮参数,因为,所以根据此比值得,取。5.2.4 差速器圆锥齿轮模数及半轴齿轮节圆直径确定(1)先确定行星齿轮和半轴齿轮的节锥角,按式(5-3)和式(5-4)计算 (5-3) (5-4)式中:。将参数代入式(5-3)和式(5-4)得: (2)确定圆锥齿轮大端模数由式(5-5)初步确定圆锥齿轮的大端模数: (5-5)将参数代入得:取标准值(3)确定圆锥齿轮节圆直径直径由式(5-6)计算: (5-6)行星齿轮节圆直径:半轴齿轮节圆直径:5.2.5 压力角汽车差速器齿轮大都采用压力角为、齿高系数为0.8的齿形。某些总质量较大的商用车采用25压力角,以提高齿轮强度。在本设计中差速器齿轮采用的压力角,齿高系数为0.8。5.3 差速器的优化设计5.3.1 优化函数设计1、目标函数的设计差速器体积可以近似用行星齿轮和半轴齿轮的体积和来代替。因此,目标函数表达式如式(5-7)所示: (5-7)式中:C行星齿轮个数,取为4;m齿轮的模数;z行星齿轮与半轴齿轮的齿数。根据上述公式可知有四个变量,故记作式(5-8) (5-8)2、约束函数的设计(1)行星齿轮齿数条件:;(2)半轴齿轮齿数条件:;(3)模数条件:;(4)齿轮模数与齿宽、齿数的关系式为(5)装配条件:由于所设计的差速器的行星齿轮数为2,对应的两半轴齿轮的齿数和肯定能被行星齿轮数整除。则其装配条件一定满足,故该约束条件不用给出。(6)行星齿轮孔径条件:为了保证工艺性,行星齿轮小端齿根圆至内孔也应有足够厚度,并满足条件如式(5-9) (5-9)式中:行星齿轮小端齿根圆直径,;R锥距,;行星齿轮大端齿根圆直径,;行星齿轮分度圆直径,;行星齿轮径向变位系数齿顶间隙,;行星齿轮小端齿根圆至内孔的最小厚度,=1.6m;D行星齿轮孔径(其中,为差速器的计算转矩,取为3649Nm;为允许挤压应力,取为98MPa;n为行星齿轮个数,取为4;为行星齿轮支承面中点到锥顶的距离,为半轴齿轮分度圆直径,=)(7)半轴齿轮孔径条件:为了保证强度要求,半轴齿轮小端齿根圆到花键孔外径应有足够的厚度,并满足下列条件 式中:半轴齿轮小端齿根圆直径,;半轴齿轮大端齿根圆直径,;半轴齿轮径向变位系数,;半轴齿轮小端齿根圆至花键内孔外径的最小厚度,取=1.6m;半轴齿轮轴径,取为46mm;(8)强度条件:由于差速器齿轮的啮合次数比传动系其它齿轮少得多,很少因为齿面点蚀而损坏。因此不必检验接触强度,只需要计算弯曲强度。轮齿弯曲应力为:式中:n行星齿轮数,取为4;J综合系数,取为0.224;半轴齿轮的齿宽;半轴齿轮大端分度圆直径;半轴齿轮计算转矩,此处取,且;参考主动锥齿轮轮齿弯曲强度校核处的值,分别取为、1.0、1.0。根据以上所列的八个约束条件,化简出对应的非线性不等式约束条件如下:(1)(2)(3)(4)(5)(6)(7)(8)(9)(10)(11)3、主函数的设计利用MATLAB进行编程,调用优化工具箱中的最优化函数fmincon,并将其结果输出在命令行里,具体的程序如图5-2所示。得出的优化结果为=12,=18,m=4,b=13mm。图5-2 MATLAB优化主函数根据以上所优化后的数据,和最初设计的数值进行比较,对优化后的数据而言,从差速器的体积可以看出,优化设计值比原设计值的体积小16%,故可知之前所设计的数据不是最优解。因此,采用优化方法进行设计比用传统方法提高了设计水平。5.3.2 行星齿轮安装孔直径及深度确定行星齿轮的安装孔的直径与行星齿轮轴的名义尺寸相同,可由式(5-10)确定。 (5-10)式中:,; ,; ,; 支撑面许用挤压应力,取为。代入数据得:;行星齿轮的安装孔的深度就是行星齿轮在其轴上的支撑长度,通常取:5.4 差速器齿轮强度计算差速器齿轮的尺寸受结构限制,且承受载荷较大,它不像主减速器齿轮那样经常处于啮合传动状态,只有当汽车在转弯或左、右行驶不同的路程时或一侧车轮打滑时,差速器齿轮才能有啮合传动的相对运动。因此,对于差速器齿轮主要应进行弯曲强度校核。齿轮弯曲应力如式(5-11)。 (5-11)式中; ;半轴齿轮齿宽,取为13mm;。代入参数到式(4-8)得:得按照文献1,差速器齿轮的,;(2)根据文献1,差速器齿轮的,。5.5 差速器齿轮材料选择差速器齿轮与主减速器一样,基本上都用渗碳合金钢制造,目前用于差速器齿轮的材料有,此处选用。5.6 本章小结主要对差速器的结构进行设计,设计出了对应的所需要的差速器数值,并利用Matlab软件对差速器进行优化,虽然优化后体积相应的增大,但是在结构上更为合理。第6章 驱动半轴设计6.1 半轴结构形式选择驱动车轮的传动装置位于传动系的末端,其基本功用是接受从差速器传来的转矩并将其传给车轮。对于断开式驱动桥和转向驱动桥,驱动车轮的传动装置为万向传动装置;对于非断开式驱动桥,驱动车轮传动装置的主要零件为半轴。而半轴根据其车轮端的支承方式不同,可分为半浮式、3/4浮式、全浮式三种形式,各自的特点有所不同。本次设计为微型货车,故选取为全浮式半轴。它的结构特点是:半轴外端的凸缘用螺钉与轮毂相连,而轮毂又借用两个圆锥滚子轴承支承在驱动桥壳的半轴套管上。理论上来说,半轴只承受转矩,作用于驱动轮上的其他反力和弯矩全部由桥壳承受。6.2 半轴的设计与计算设计半轴的主要尺寸是其直径的设计,在设计时首先可根据对使用条件和载荷工况相同或相近的同类汽车同形式的半轴的分析比较,大致选定从整个驱动桥的布局来看比较合适的半轴半径,然后对它进行强度校核。6.2.1 半轴杆部径确定 1、全浮式半轴计算载荷按式(6-1)确定: (6-1)式中:,;将参数代入(6-1)式得:2、全浮式半轴杆部直径按式(6-2)确定: (6-2)式中:;,在此取。所以初选半轴杆部直径为。6.2.2 半轴的强度校核 1、全浮式半轴扭转应力按式(6-1)确定: (6-3)式中:;半轴扭转切应力,可取为。将数据代入上式求得。在保证安全系数在1.31.6范围内,半轴的许用应力。故设计满足要求。6.3 半轴花键设计计算6.3.1 半轴花键尺寸参数计算半轴、半轴齿轮一般都采用渐开线花键连接,由于本设计为载重汽车,故花键内部直径的大小应不小于其杆部直径,所以选模数为2、压力角为、齿数为的圆柱渐开线花键齿轮,并对花键进行切应力和挤压应力校核,半轴花键尺寸计算见表6-1。表6-1 半轴花键尺寸计算序号项目计算公式计算结果1齿数2模数23压力角4分度圆直径5基圆直径6内花键大径尺寸7内花键小径尺寸8作用齿槽宽9外花键大径尺寸10外花键小径尺寸6.3.2 半轴花键强度校核 1、半轴花键的剪切应力按式(6-1)计算 (6-4)式中:;,取;2、半轴花键的挤压应力按式(6-1)计算 (6-5)式中:;当传递最大转矩时,半轴花键传递的剪切应力不得超过,半轴花键承受的挤压应力不得超过,由上述计算可得,故本设计满足要求。6.4 半轴花键结构设计及材料选择为了使半轴花键的内径不小于其杆部直径,故将花键的端部加工得粗一些,并适当减少花键槽的深度,因此得相应的增加花键的齿数。半轴的破坏形式多为扭转疲劳破坏,因此在结构设计上应将量增大过过渡段的圆角半径以减少应力集中。在现代汽车半轴上,渐开线花键用的比较广泛,但也有采用矩形或梯形花键的。对于半轴的材料现在多采用晗铬的中碳合金钢制造,如:、40CrMnMo、等,本设计采用,其实我国研制出的新钢种,作为半轴材料效果很好。半轴热处理,过去都采用调制处理的方法,调制后要求杆部硬度为(凸缘部分可降至)。近年来多采用高频、中频淬火,这种处理方法可使半轴表面淬硬达,硬化层深达其半径的1/3,芯部硬度可定为;不淬火区域(突圆)的硬度可定在的范围内。由于硬化层本身的强度较高,加之在半轴表面形成较大的残余压应力,以及采用喷丸处理,滚压半轴突圆根部采用过渡圆角等工艺,使半轴的静强度和疲劳强度大为提高,尤其是疲劳强度提高得十分显著。综上:本设计半轴材料选用,半轴热处理为高频、中频淬火。6.5 本章小结本章根据所设计的微型货车选择了全浮式半轴,并对其进行了结构上的设计。第7章 驱动桥壳设计7.1 桥壳结构形式选择1、可分式桥壳可分式桥壳的整个桥壳由一个垂直结合面分为左右两部分,每一部分均由一个铸件壳体和一个压入外端的半轴套管组成。半轴套管与壳体用铆钉连接。在装配主减速器和差速器后左右两半桥壳是通过在中央结合面处的一圈螺栓连接成一个整体。其特点是桥壳制造工艺简单、主减速器轴承支撑刚度好等,但对与主减速器的装配、调整及维修都不方便,桥壳的强度和刚度也比较低。过去这种两端可分式桥壳多用于轻型汽车上,但由于上述的缺点,现在已经不使用了。2、整体式桥壳整体式桥壳的特点是,将整个桥可制成一个整体,桥壳犹如一个整体的空心梁,其强度以及刚度都比较好,且桥壳与主减速器壳分作两体,主减速器齿轮和差速器均装在独立的主减速器壳体内,构成单独的总成,调整好以后再由桥壳中部前面装入桥壳内,并与桥壳用螺栓固定在一起。从而使主减速器和差速器的拆装、调整、维修、保养等都十分方便。整体式桥壳按其制造工艺的不同又可分为铸造整体式、钢板冲压焊接式和钢管扩张成形式三种。3、组合式桥壳组合式桥壳是将主减速器壳与部分桥壳铸成一体,而后用无缝钢管分别压入壳体两端,两者之间用塞焊或销钉固定。它的优点是从动齿轮的轴承支撑刚度较好,主减速器的装配比可分式桥壳方便,但是,要求有较高的加工精度,故常用于乘用车和总质量较小的商用车上。综上:考虑到本设计的是载重汽车,故本设计采用钢板冲压焊接式整体桥壳。7.2 桥壳的强度计算和校核 驱动桥的桥壳是汽车的主要承载构件之一,形状复杂,汽车的行驶条件复杂多变。而我国通常推荐计算时将桥壳的复杂受力状简化成三种典型的计算工况,只要在这三种典型的工况下桥壳的强度得到了保证,就可以认为该桥壳的强度满足其在各种行驶条件下的可靠性。7.2.1 桥壳的静弯曲应力计算1、在两钢板弹簧座之间的弯矩按式(7-1)确定。 (7-1)式中:;桥壳的危险截面在钢板弹簧附近,由于远远小于,且设计时不易准确预计,故取;驱动车轮的轮距,取1.223m;将数据代入式(7-1)得:2、车桥的载荷计算和弯矩图(1)车桥载荷计算由设计及参数可知,车桥的左右车轮载荷均匀分布 ,所以此时左右车轮载荷为,同理在钢板弹簧位置处的载荷为。(2)车桥受力图和弯矩图a车桥受力图如图7-1所示:图7-1 车桥受力图b车桥弯矩图如图7-2所示:图7-2 车桥弯矩图3、危险截面弯曲应力的计算危险截面弯曲应力按式(7-2)计算: (7-2)式中:两钢板弹簧之间的弯矩;如表7-1所示。表7-1 抗弯截面系数断面形状垂直及水平弯曲截面系数、扭转截面系数初步确定方管的断面为矩形,其中、,厚度都为,则垂直、水平面内的弯曲截面系数分别为: 所以弯曲应力为:7.2.2 汽车在不平路面冲击载荷作用下桥壳的强度计算此时桥壳在动载荷下的弯曲应力按式(7-3)所示: (7-3)式中:动载荷系数,对轿车、客车取1.75,对货车取2.5,本设计使用车型为微型货车,故取;将参数代入(7-3)式得:7.2.3 汽车以最大牵引力行驶时桥壳的强度计算1、地面最大切反力此时不考虑侧向力,那么作用在左、右车轮上除了垂直反力外,还有切反力,地面最大切反力按式(7-4)计算: (7-4)式中:;传动系最大传动比,;将所有数据代入式(7-4)得:2、垂直面内弯矩驱动桥壳在两钢板弹簧座之间的垂直弯矩按式(7-5)确定。 (7-5)式中:见式(7-1); ;将数据代入式(7-5)得:3、水平面弯矩驱动桥壳在两钢板弹簧座之间的水平弯矩按式(7-6)计算: (7-6)将数据代入式(7-6)得: 此时在两钢板座之间桥壳承受的转矩按式(7-5)计算: (7-7)式中:见式(7-4);将数据代入式(7-7)得:4、受力弯矩图如图7-3,图7-4,图7-5所示图7-3 垂直面弯矩图7-4 水平面弯矩图7-5 桥壳承受的转矩5、弯曲应力和扭转应力桥壳则在该断面处的弯曲应力和扭转应力按式(7-8)和式(7-9)计算: (7-8) (7-9)将数据代入式(7-8)和式(7-9)得: 桥壳的许用应力为,许用扭转应力为,由上述计算可得:,所以本设计中的桥壳在汽车以最大牵引力行驶时的强度满足设计要求。7.2.4 汽车紧急制动时桥壳的强度计算此时不考虑侧向力,那么作用在左、右车轮上除了垂直反力外,还有切反力,即地面对驱动车轮的制动力。1、垂直面内的弯矩紧急制动时驱动桥壳在两钢板弹簧座之间的垂直弯矩按(7-10)计算: (7-10)式中:汽车制动时汽车质量移动系数;对于载货汽车后驱动桥可取此时取0.85; ; 见式(7-1);将数据代入式(7-10)得:2、垂直面内的弯矩紧急制动时驱动桥壳在两钢板弹簧座之间的水平弯矩按式(7-11)计算: (7-11)式中:见式(7-1);。将数据代入式(7-11)得: ;所以转矩按式(7-12)计算: (7-12)将数据代入式(7-12)得: 3、受力弯矩图如图7-6,图7-7,图7-8所示图7-6 垂直面弯矩图7-7 水平面弯矩图7-8 桥壳所受转矩4、弯曲应力和扭转应力桥壳在钢板弹簧座附近的危险断面为矩形断面时,则在该断面处的弯曲应力和扭转应力分别按式(7-13)和式(7-14)计算: (7-13) (7-14)将数据代入式(7-13)和式(7-14)得:桥壳的许用应力为,许用扭转应力为,由上述计算可得:,所以本设计在紧急制动时满足要求。7.3 本章小结对驱动桥壳的结构进行了分析,并选择了一种方案。根据计算强度公式,对桥壳在几种形式下进行了强度计算,并都达到了一定的强度要求。第8章 驱动桥三维建模8.1 SolidWorks简介SolidWorks是达索系统(Dassault Systemes S.A)下的子公司,专门负责研发与销售机械设计软件的视窗产品。Solidworks软件功能强大,组件繁多。有功能强大、易学易用和技术创新三大特点,这使其成为领先的、主流的三维CAD解决方案。它能够提供不同的设计方案、减少设计过程中的错误以及提高产品质量。本次设计采用SolidWorks 2018建立驱动桥的三维模型。8.2 主减速器齿轮建模1、从动锥齿轮建模启动SolidWor
- 温馨提示:
1: 本站所有资源如无特殊说明,都需要本地电脑安装OFFICE2007和PDF阅读器。图纸软件为CAD,CAXA,PROE,UG,SolidWorks等.压缩文件请下载最新的WinRAR软件解压。
2: 本站的文档不包含任何第三方提供的附件图纸等,如果需要附件,请联系上传者。文件的所有权益归上传用户所有。
3.本站RAR压缩包中若带图纸,网页内容里面会有图纸预览,若没有图纸预览就没有图纸。
4. 未经权益所有人同意不得将文件中的内容挪作商业或盈利用途。
5. 人人文库网仅提供信息存储空间,仅对用户上传内容的表现方式做保护处理,对用户上传分享的文档内容本身不做任何修改或编辑,并不能对任何下载内容负责。
6. 下载文件中如有侵权或不适当内容,请与我们联系,我们立即纠正。
7. 本站不保证下载资源的准确性、安全性和完整性, 同时也不承担用户因使用这些下载资源对自己和他人造成任何形式的伤害或损失。

人人文库网所有资源均是用户自行上传分享,仅供网友学习交流,未经上传用户书面授权,请勿作他用。