连杆合件加工工艺及关键工序工装设计
41页 20000字数+论文说明书+任务书+25张CAD图纸【详情如下】
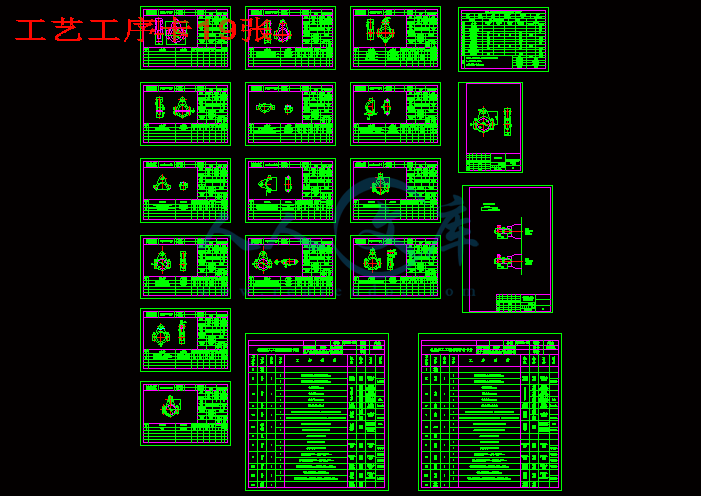


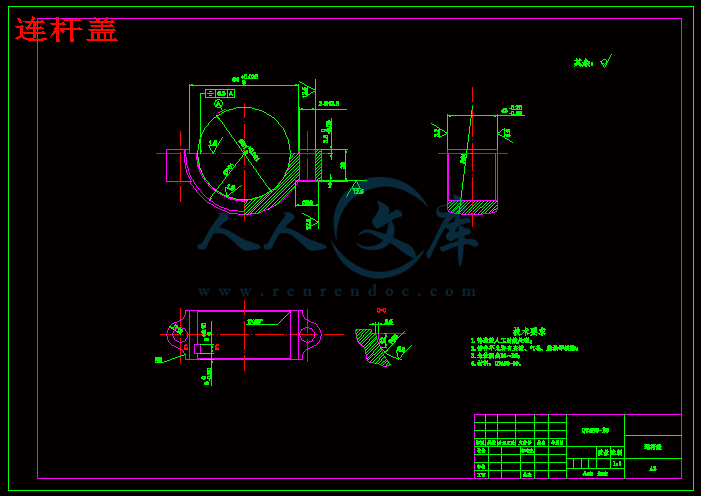





专用组合镗床加工示意图.dwg
任务书.doc
外文翻译--连杆内燃机.doc
工艺工序卡19张.dwg
工艺过程综合卡片.dwg
组合镗床联系尺寸图.dwg
连杆体.dwg
连杆合件加工工艺及关键工序工装设计开题报告.doc
连杆合件加工工艺及关键工序工装设计答辩稿.ppt
连杆合件加工工艺及关键工序工装设计论文.doc
连杆合体.dwg
连杆大头孔镗削用夹具装配图.dwg
连杆盖.dwg
目 录
1 绪论 1
1.1 毕业设计的目的 1
1.2 毕业设计要求 1
1.3 解决方案和技术路线 2
2 工艺设计 3
2.1 主要技术依据 3
2.1.1 生产纲领,生产类型 3
2.1.2 连杆的功用及主要结构参数 3
2.1.3 毛坯的选择及制备 4
2.2 工艺分析 5
2.3 加工方案 6
2.3.1 定位基准的选择 6
2.3.2 工艺路线方案的确定 8
2.3.3 加工质量的保证措施 10
2.4 工序设计 13
2.4.1 确定各工序的加工余量、计算工序尺寸及公差 13
2.4.2 确定各工序的切削用量、工时定额 15
2.5 工艺规程 20
2.6 连杆的检验 24
2.6.1 观察外表缺陷及目测表面粗糙度 24
2.6.2 连杆大、小头孔圆柱度的检验 24
2.6.3 连杆体、连杆盖结合面对大头孔中心线的对称度的检验 24
2.6.4 连杆大、小头孔平行度的检验 25
2.6.5 小头孔R67槽对连杆轴线的对称度的检验 25
3 夹具设计 26
3.1 夹具设计的要求 26
3.2 夹具设计 26
4 组合机床设计 29
4.1 组合机床设计的要求 29
4.2 组合机床总体设计 29
4.2.1 被加工零件工序图 29
4.2.2 加工示意图 30
4.2.3 机床联系尺寸总图 33
4.2.4 机床机床生产率计算卡 35
结束语 36
致 谢 37
参考文献 38
毕业设计说明书(论文)中文摘要
连杆是某企业产品中的关键零件之一,本文主要论述了连杆的加工工艺及其夹具设计及其加工用组合机床。连杆的尺寸精度、形状精度以及位置精度的要求都很高,而连杆的刚性却比较差,容易产生变形,因此安排工艺过程时,需要把各主要表面的粗精加工工序分开。逐步减少加工余量、切削力及内应力的作用,并修正加工后的变形,这样才能最后达到零件的技术要求。由于连杆的生产量比较大,为了保证产品质量,提高加工效率,需要对其加工工艺进行优化设计,并在关键工序使用组合机床或专用机床进行加工。
关键词 连杆 精度 加工工艺 夹具设计 组合机床
毕业设计说明书(论文)外文摘要
Title The Processing Technology Working Procedure Equipment Design of The Connecting Rod
Abstract
The connecting rod is one of the key parts of an enterprise products, this text expounds mainly the machining technology and the design of clamping device of the connecting rod and modular machine tool of the connecting rod .The precision of size, the precision of profile and the precision of position , of the connecting rod is demanded highly , and the rigidity of the connecting rod is not enough, easy to deform,so arranging the craft course, need to separate the each main and superficial thick finish machining process. Reduce the function of processing the surplus , cutting force and internal stress progressively , revise the deformation after processing, can reach the specification requirement for the part finally .As the output of the connecting rod is very large ,it is need to make optimal design for the machining technology and use modular machine tool for pivotal machining process ,to ensure product quality and to improve the processing efficiency.
Keywords Connecting Rod Precision Processing Technology Design of Clamping Device Modular Machine Tool
1 绪论
1.1 毕业设计的目的
连杆合件是某企业产品中的关键零件之一,生产量比较大。为了保证产品质量,提高加工效率,需要对其加工工艺进行优化设计,并在关键工序使用组合机床或专用机床进行加工。本课题即以此为背景,要求学生根据企业生产需要和连杆合件零件的加工要求,首先完成零件的加工工艺规程设计,在此基础之上,选择其关键工序之一进行专用夹具及加工用组合机床设计,并完成必要的设计计算。
通过这样一个典型环节综合训练,达到综合训练学生运用所学知识,解决工程实际问题的能力。
1.2 毕业设计要求
本设计要求学生在对连杆合件的加工要求、零件的结构工艺性进行认真分析的基础上,首先对零件的加工工艺规程做出优化设计,并对其关键工序之一进行专用夹具及加工用组合机床设计。具体任务及要求如下:
(1)调查研究、查阅及翻译文献资料,撰写开题报告;
(2)连杆合件加工要求、零件的结构工艺性分析;
(3)连杆合件加工工艺规程设计;
(4)连杆合件关键工序的专用夹具设计;
(5)连杆合件关键工序的组合机床设计;
(6)必要的设计计算与分析;
(7)文档整理、撰写毕业设计说明书及使用说明书。
设计技术要求包括:
(1)生产纲领:50000件/年;
(2)夹具采用液压驱动;
(3)组合机床采用液压滑台;
(4)每次加工一个零件。
1.3 解决方案和技术路线
本设计是连杆合件加工工艺及关键工序工装设计,并在此基础上选择关键工序之一进行专用夹具及加工用组合机床设计,因此需要研究和解决以下几个问题:
(1)连杆合件加工工艺及关键工序工装设计;
(2)关键工序之一的专用夹具设计;
(3)关键工序之一的加工用组合机床设计。
进行连杆合件加工工艺及关键工序工装设计时,应首先熟悉连杆合件的零件图,依据“先加工基准面,后加工其他表面”、“先加工平面,后加工孔”、“先加工主要平面,后加工次要平面”、“先安排粗加工,后精加工” [1],再结合工件的实际情况来安排工艺路线。工艺装备包含:刀具、量具、夹具、辅具。工艺装备的选用及设计得依据工序及工件的实际情况。
进行关键工序之一的专用夹具设计时,应首先熟悉本工序的内容及要求及零件尺寸、表面粗糙度的要求和形位公差的要求,了解夹具设计的原则、夹具的构成,依据工件的实际情况设计本工序的夹具[1]。
进行关键工序之一的加工用组合机床设计时,应首先了解机床的构成,依据机床设计的原则,工件、夹具的具体情况,本工序的加工要求,查阅相关资料来设计机床,并完成三图一卡的制作。
结束语
通过对汽车连杆合件加工工艺及关键工序工装的设计,使我扩充了自己的知识库和经验,同时增加了完成具体工程的信心。
连杆件外形较复杂,且刚性较差。且其加工技术要求很高,所以适当定位基准,是保证连杆能否正确加工的重要问题。在连杆的实际加工过程中,选用连杆的大小头端面及小头孔作为主要定位基面,同时选用大头部分作一般定位基准。
在设计的过程中我充分体会到了“先基准后一般”“先面后孔”“先主要表面后次要表面”的加工原则。连杆的主要加工表面为大小头孔及其两端面,连杆体和连杆盖得结合面。连杆机械加工的工艺路线是围绕主要加工表面来安排的。连杆加工路线按连杆的分合可以分为三个阶段:第一个阶段为连杆体和盖分离之前的加工;第二个阶段为连杆体和盖的切开加工;第三个阶段为连杆体和盖装配后的加工。
在夹具设计中,我设计的是连杆大头孔镗削加工的专用夹具。首先确定工件的定位基准及定位基面,之后确定位元件,再确定加紧力的方向和方式。针对连杆的加工特点及加工批量,本设计要求采用液压夹紧装置,本设计很有实用性!
在专用组合机床的设计中,我设计的是连杆大头孔镗削加工的专用组合镗床。专用组合镗床,突出了专用二字,即非通用,只适合本工序。切削力、切削转矩、切削功率是专用组合镗床设计的基础,求出以上几个量镗床最核心部位——镗削头就可以确定了,之后的设计围绕镗削头和工件的相对位置及其一些关键件尺寸来选择其它部件并确定它们的相对位置。
致 谢
毕业设计接近尾声,我的论文撰写也一并进入了尾声。在整个毕业设计的完成过程中,都得到了副教授的精心指导与热情的帮助。副教授严谨细致的作风,丰富的理论知识给了我很深的启迪,使我受益匪浅。
我的论文是在老师悉心指导和严格要求下完成的,我的每一点进步和提高都得益于老师的指导;同时也使得我在设计思路方面、考虑问题切入角度方面、解决问题方面等方面都得到了很好的锻炼。
同时还要感谢机械系老师教授知识的辛苦付出,没有知识的学习毕业设计也难以完成。还要感谢同学对我的信任和支持。
最后感谢我的父母,养育之恩,无以回报,祝你们永远健康快乐。
毕业设计即将结束,大学生活也走到尽头,但之后又是新的开始,明天的阳光依旧灿烂。
参 考 文 献
[1] 傅水根.机械制造工艺基础[M].北京:清华大学出版社,2004.
[2] 梁燕飞,潘尚峰.机械基础[M].第2版,北京:清华大学出版社,2005.
[3] 曹惟庆.连杆机构的分析与综合[M].北京:科学出版社,2002.
[4] 朱张校.工程材料[M].北京:清华大学出版社,2001.
[5] 严绍华.材料成形工艺基础[M].北京:清华大学出版社,2001.
[6] 王先奎,李旦.机械加工工艺手册[M].第2版,北京:机械工业出版社,2007.
[7] 王平嶂.机械制造工艺与刀具[M].北京:清华大学出版社,2005.
[8] 徐嘉元曾家驹.机械制造工艺学[M].北京:机械工业出版社,1998.
[9] 周世学.机械制造工艺与夹具[M].北京:北京理工大学,2006.
[10] 罗丽萍,京玉海.机械制造基础[M].北京:清华大学出版社,2004.
[11] 邹青.机械制造技术基础课程设计指导教程[M].北京:机械工业出版,2007.
[12] 徐学林.互换性与测量技术基础[M].长沙:湖南大学出版社,2007.
[13] 李庆余,张佳.机械制造装备设计[M].北京:机械工业出版社,2007.
[14] 陈日曜.金属切削原理[M].第2版,北京:机械工业出版社,1992.
[15] 李庆余,张佳.机械制造装备设计[M].北京:机械工业出版社,2007.
[16] 陈立德.机械制造装备设计[M].北京:高等教育出版社,2006.
[17] 姜永武,刘薇娜.组合机床设计[M].成都:西南交通大学出版社,2004.
[18] 大连组合机床研究所.组合机床设计参考图册[M].北京:机械工业出版社,1975.
[18] 大连组合机床研究所.组合机床设计参考图册[M].北京:机械工业出版社,1975.
[19] 谢家瀛.组合机床设计简明手册[M].北京:机械工业出版社,2002.
[20] 李庆余,张佳.机械制造装备设计[M].北京:机械工业出版社,2007.