汽车后悬置支撑座冲压模设计【全套含CAD图纸、说明书】
收藏
资源目录
压缩包内文档预览:(预览前20页/共53页)
编号:14542364
类型:共享资源
大小:3.55MB
格式:ZIP
上传时间:2019-02-11
上传人:机****料
认证信息
个人认证
高**(实名认证)
河南
IP属地:河南
30
积分
- 关 键 词:
-
全套含CAD图纸、说明书
汽车
悬置
支撑
支持
冲压
设计
全套
cad
图纸
说明书
仿单
- 资源描述:
-




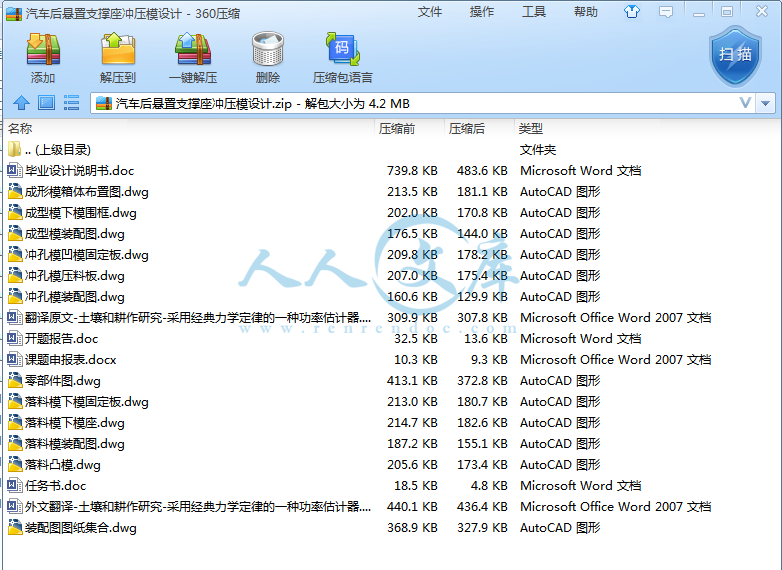



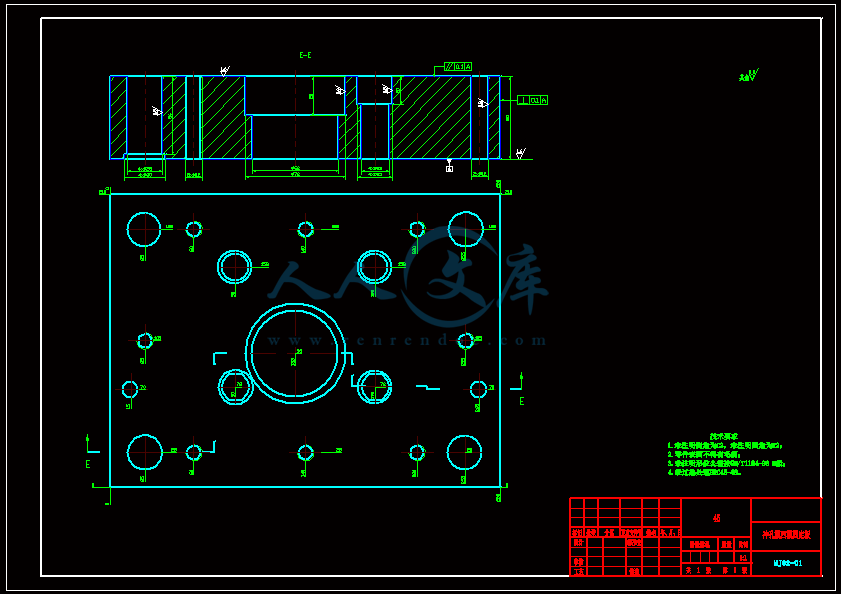

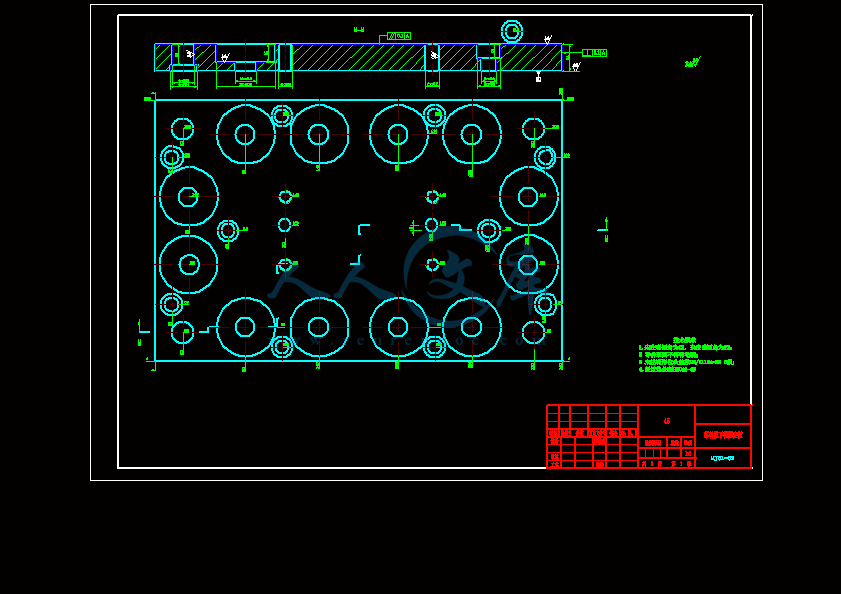
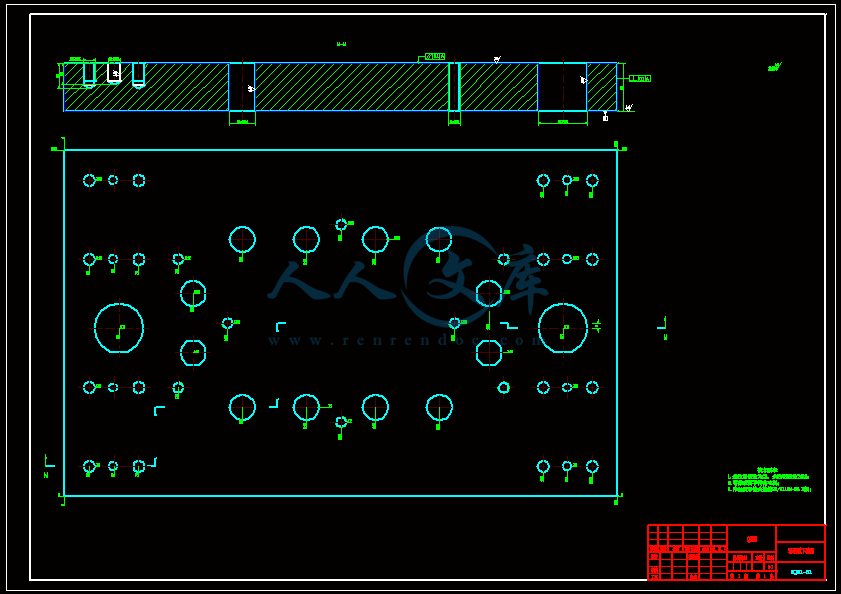

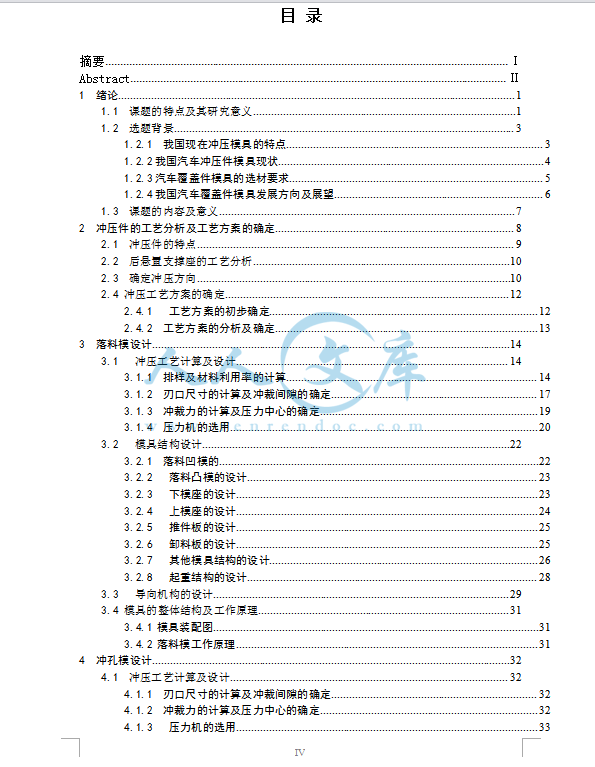
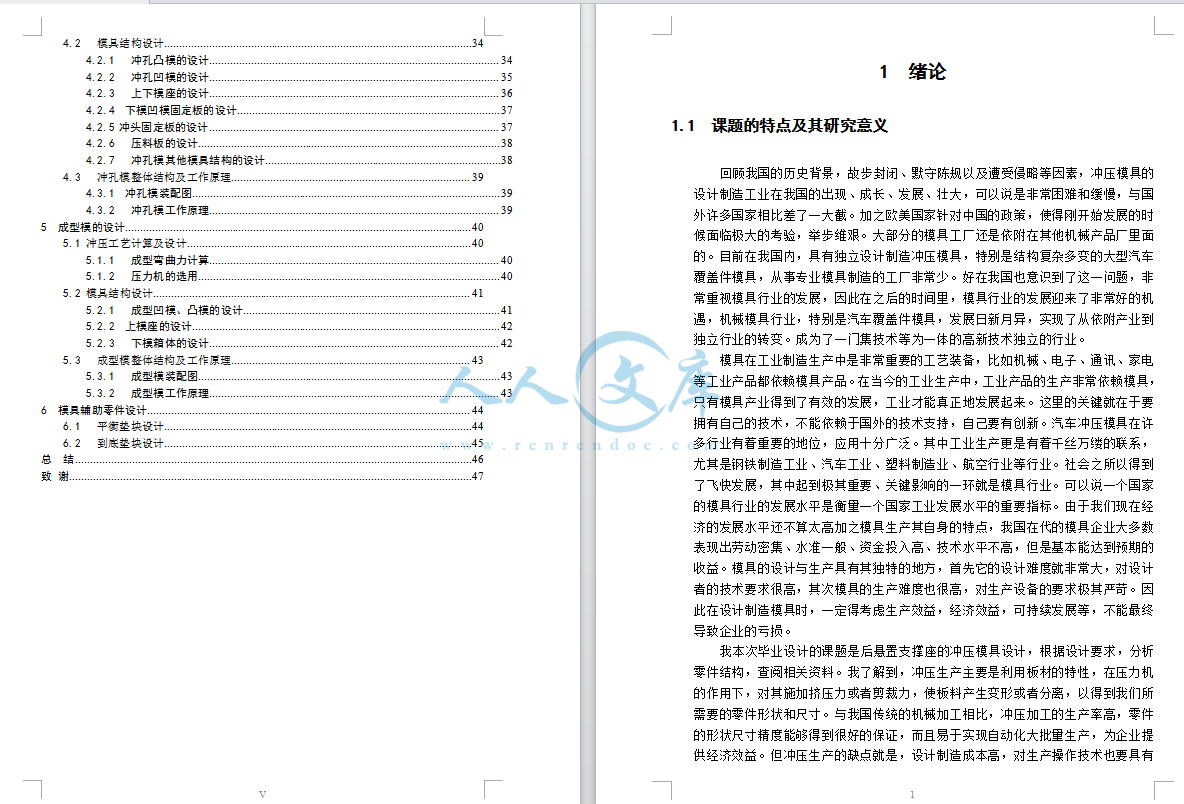

- 内容简介:
-
毕业设计说明书题 目:某型汽车后悬置支撑座冲压模具设计 系 别: 专业班级: 姓 名: 学 号: 指导教师: 摘 要冲压分冷冲压和热冲压两种,是一种先进常见的现代金属加工方法,其工作原理是根据金属塑性变形,利用冲模配合冲压设备对金属板料进行加工,以获得人们所需要的零件的形状及尺寸。冷冲压模,又是冲压生产中最常用的一种冲压件工艺装备,具有生产率高,便于实现自动化、操作简便,对工人的操作水平要求不高、产品尺寸精度稳定、加工制造成本低等一系列优点,应用领域小到钟表,大则是汽车,船舶等覆盖件生产。在此,我设计的主要内容是设计某型汽车后悬置支撑座冲压件模具设计,考虑成本、制造难易程度、厂房设备等因素,结合后悬置支撑座零件的结构特点,分落料、冲孔、成型三道工序,设计成单工序冲压模。在本次毕业设计中,依据后悬置支撑座结构特点及所选用的材料,经设计方案、工艺路线分析,通过严格的设计计算和相关资料的查询收集。使用UG三维建模设计软件,初步设计确定模具结构,选用合适的冲压设备。使用CAD二维软件绘制各个工序冲压模具中各零件图及装配图的二维图纸,完成修边冲孔工序模具的设计。【关键字】:冲压模、落料、冲孔、成型AbstractStamping cold stamping and hot stamping two, is an advanced common modern metal processing method, its working principle is based on the plastic deformation of metal stamping die, the use of complex equipment for processing of sheet metal, in order to obtain the shape and size of the parts we need. Cold punching die, and stamping production one of the most commonly used parts stamping process equipment, with high productivity, easy to realize automation, simple operation, to the workers operation level is not high, the product size precision processing, low manufacturing cost and a series of advantages, the application field of the small clock, large cars, ships and other cover production. The main contents of my design is the design of a car rear suspension seat design of stamping die, support cost, ease of manufacture, workshop equipment and other factors, combined with the structure characteristics of rear suspension supporting seat parts, blanking, punching, forming three processes, design the single stamping die in the process. Graduation design, based on the characteristics of rear suspension supporting seat structure and material selection, the design scheme, process analysis, through strict design calculation and related information query collection. Using UG 3D modeling software design, preliminary design to determine the mold structure, choose suitable stamping equipment. 2D drawings using 2D CAD software in the process of stamping die drawing various parts and assembly drawings, complete the design process of trimming and punching die.【Key words】Stamping die, blanking, punching, forming目 录摘要Abstract1 绪论11.1 课题的特点及其研究意义11.2 选题背景31.2.1 我国现在冲压模具的特点31.2.2我国汽车冲压件模具现状41.2.3汽车覆盖件模具的选材要求51.2.4我国汽车覆盖件模具发展方向及展望61.3 课题的内容及意义72 冲压件的工艺分析及工艺方案的确定82.1 冲压件的特点92.2 后悬置支撑座的工艺分析102.3 确定冲压方向102.4 冲压工艺方案的确定122.4.1 工艺方案的初步确定122.4.2 工艺方案的分析及确定133 落料模设计143.1 冲压工艺计算及设计143.1.1 排样及材料利用率的计算143.1.2 刃口尺寸的计算及冲裁间隙的确定173.1.3 冲裁力的计算及压力中心的确定193.1.4 压力机的选用203.2 模具结构设计223.2.1 落料凹模的223.2.2 落料凸模的设计233.2.3 下模座的设计233.2.4 上模座的设计243.2.5 推件板的设计253.2.6 卸料板的设计253.2.7 其他模具结构的设计263.2.8 起重结构的设计283.3 导向机构的设计293.4 模具的整体结构及工作原理313.4.1 模具装配图313.4.2 落料模工作原理314 冲孔模设计324.1 冲压工艺计算及设计324.1.1 刃口尺寸的计算及冲裁间隙的确定324.1.2 冲裁力的计算及压力中心的确定324.1.3 压力机的选用334.2 模具结构设计344.2.1 冲孔凸模的设计344.2.2 冲孔凹模的设计354.2.3 上下模座的设计364.2.4 下模凹模固定板的设计374.2.5 冲头固定板的设计374.2.6 压料板的设计384.2.7 冲孔模其他模具结构的设计384.3 冲孔模整体结构及工作原理394.3.1 冲孔模装配图394.3.2 冲孔模工作原理395 成型模的设计405.1 冲压工艺计算及设计405.1.1 成型弯曲力计算405.1.2 压力机的选用405.2 模具结构设计415.2.1 成型凹模、凸模的设计415.2.2 上模座的设计425.2.3 下模箱体的设计425.3 成型模整体结构及工作原理435.3.1 成型模装配图435.3.2 成型模工作原理436 模具辅助零件设计446.1 平衡垫块设计446.2 到底垫块设计45总 结46致 谢47IV1 绪论1.1 课题的特点及其研究意义回顾我国的历史背景,故步封闭、默守陈规以及遭受侵略等因素,冲压模具的设计制造工业在我国的出现、成长、发展、壮大,可以说是非常困难和缓慢,与国外许多国家相比差了一大截。加之欧美国家针对中国的政策,使得刚开始发展的时候面临极大的考验,举步维艰。大部分的模具工厂还是依附在其他机械产品厂里面的。目前在我国内,具有独立设计制造冲压模具,特别是结构复杂多变的大型汽车覆盖件模具,从事专业模具制造的工厂非常少。好在我国也意识到了这一问题,非常重视模具行业的发展,因此在之后的时间里,模具行业的发展迎来了非常好的机遇,机械模具行业,特别是汽车覆盖件模具,发展日新月异,实现了从依附产业到独立行业的转变。成为了一门集技术等为一体的高新技术独立的行业。模具在工业制造生产中是非常重要的工艺装备,比如机械、电子、通讯、家电等工业产品都依赖模具产品。在当今的工业生产中,工业产品的生产非常依赖模具,只有模具产业得到了有效的发展,工业才能真正地发展起来。这里的关键就在于要拥有自己的技术,不能依赖于国外的技术支持,自己要有创新。汽车冲压模具在许多行业有着重要的地位,应用十分广泛。其中工业生产更是有着千丝万缕的联系,尤其是钢铁制造工业、汽车工业、塑料制造业、航空行业等行业。社会之所以得到了飞快发展,其中起到极其重要、关键影响的一环就是模具行业。可以说一个国家的模具行业的发展水平是衡量一个国家工业发展水平的重要指标。由于我们现在经济的发展水平还不算太高加之模具生产其自身的特点,我国在代的模具企业大多数表现出劳动密集、水准一般、资金投入高、技术水平不高,但是基本能达到预期的收益。模具的设计与生产具有其独特的地方,首先它的设计难度就非常大,对设计者的技术要求很高,其次模具的生产难度也很高,对生产设备的要求极其严苛。因此在设计制造模具时,一定得考虑生产效益,经济效益,可持续发展等,不能最终导致企业的亏损。我本次毕业设计的课题是后悬置支撑座的冲压模具设计,根据设计要求,分析零件结构,查阅相关资料。我了解到,冲压生产主要是利用板材的特性,在压力机的作用下,对其施加挤压力或者剪裁力,使板料产生变形或者分离,以得到我们所需要的零件形状和尺寸。与我国传统的机械加工相比,冲压加工的生产率高,零件的形状尺寸精度能够得到很好的保证,而且易于实现自动化大批量生产,为企业提供经济效益。但冲压生产的缺点就是,设计制造成本高,对生产操作技术也要具有一定得专业技能,这就是目前制约我国模具行业发展壮大的主要因素,我们的许多中小模具厂无法承受这样的经济压力。随着我国的发展,人们生活水平逐步提高。对汽车的需求也越来越强烈。这就直接地促进了汽车行业的发展,间接促进了汽车覆盖件模具的发展,我国模具行业的发展迎来了第二次机遇。一辆车从表面的覆盖件到其内部的加强筋、支撑件等,他们的生产都离不开冲压模具。在这样的情形下,就导致了我国必须提高相应模具的设计制造生产水平。我国开始重视模具设计、制造、生产人才的培养。在高校近年来,开设了专门的模具设计制造专业,为企业将来模具的设计制造提高人才支援。在企业,积极促进企业对设计人员的培养,激励具有创新进取精神的员工。竞争的越来越激烈,汽车覆盖件模具的设计要求,更新换代速度加快,逐渐壮大到现在已经是一门高新技术产业。可以说模具行业的发展水平,直接制约着汽车的发展高度。怎么样提高模具的设计水平含量,怎么样在保证生产使用的前提下降低成本,提高生产效益及经济效益,已经成为现在模具行业的主要问题。模具是工业加工生产的重要工艺工具,可以说模具的发展水平就是衡量一个国家工业生产水平高低的重要指标。现在我国模具的主要结构有以下几个形式。模具的主要结构:(1)安装结构:根据模具的具体情况,选取的冲压设备进而确定相应的安装结构,压力机型号不同压板槽是不同的,模具的压板槽的分布和数量设定需要参照压力机及相关的标准确定的。有柄式、耳式和板式三种。(2)定位结构:比如背靠块,定位基准和设计基准一般要统一,以提高形状位置精度。定位机构的作用就是准确定位,设计不合理就会形成极大的偏差,造成冲压件不合格,无法完成产品的生产的,甚至损坏冲压设备。(3)导向结构:其作用是在模具开合摸时保证运动准确平稳,按照预定的方向运动。导向机构的设计需要根据覆盖件要求达到的精度等级要确定,导柱导套一般应用于精度等级要求高的模具,导板则是应用于精度等级一般的模具。(4)防护结构:开合模都有一定的行程,当出现意外时,防护结构就起到机器重要的作用,可以保证模具及操作人员的安全。主要有限位机构、安全侧销等。(5)平衡结构:为保证模具工作时安全可靠平稳,模具整体需要设计平衡结构,保证产品的合格率。合理的平衡结构可以使模具安全高效的运行,而不合理的平衡结构只会加重模具及冲压设备的负荷,得不偿失。1.2 选题背景现在,社会不断发展,文明不断进步,人们生活水平得以不断的提高,随着社会的高速发展,这也推动着科技、工业的发展,在模具行业表现得尤为明显,在我们身边各种产品,小的方面如保温瓶、不锈钢餐具、不锈钢水杯,大的如汽车覆盖件、飞机的外壳、船舶等都是通过冲压模具来知道生产制造的,冲压模具在许多行业有着重要的地位,应用十分广泛。其中工业生产更是有着千丝万缕的联系,尤其是钢铁制造工业、汽车工业、塑料制造业、航空行业等行业。社会之所以得到了飞快发展,其中起到极其重要、关键影响的一环就是模具行业。可以说一个国家的模具行业的发展水平是衡量一个国家工业发展水平的重要指标。由于我们现在经济的发展水平还不算太高加之模具生产其自身的特点,我国在代的模具企业大多数表现出劳动密集、水准一般、资金投入高、技术水平不高,但是基本能达到预期的收益。进入二十世纪以后,我国的工业得到了迅猛的发展,这很大一部分得益于我们模具行业的巨大进步。特别是在引进国外欧美的先进技术以后,我国模具设计制造方面有了全新的的认识与发展方向。我国模具行业,开始往高技术集成,高精度方向发展。紧随的模具加工工艺及设备的发展也越来越完善,模具行业前景非常乐观。但也面临着挑战,那就是我国的技术水平还跟不上市场的要求,导致了这一冲突的出现的原因在于我国这方面人才的不足。正因为这一矛盾冲突,才促使人才培养得到重视,模具设计由传统的设计途径,逐渐向计算机辅助设计方向发展。这种方式的设计,对设计的精度更加精确,而且容易保证。设计人员不需要长期待在车间,可以坐在办公室对模具进行远端计算机设计,以电子数据的形式指导生产。减轻了设计人员的工作负担。此外,当设计中出现问题时,查找检测错误环节更加方便,修改也更加快捷。这种设计方式的缺点就是,对设计者的专业文化水平要求非常高,严格要求具有严谨的专业技术水平。而且不允许在最后确定设计方案时有半点差错。1.2.1 我国现在冲压模具的特点随着汽车行业的兴起,市场对汽车冲压件的需求近年来与日俱增,很显然传统的机械加工方法已经无法满足巨大的市场需求,这就促使了企业必须寻求更加高效快捷的加工方法。在这种形式的趋势下,能够将计算机设计的数字信息转换成实际的加工轨迹的CAD、CAM终端加工技术就出现了。这种技术的优点就是不需要加工师傅对照着设计图纸指导生产过程,不需要绘制详细的加工图纸,而是直接将数字信息直接转换成加工轨迹,采用数控加工机床对模具型材进行加工,非常方便。而且避免了由于看图失误导致的没必要错误。缺点就是,加工设备要求高,需要操作人员拥有一定得专业知识。对于塑料板材或者较软的材料的汽车冲压模具的加工方法特点是,这种型材加工成型之后不存在回弹现象。因此在进行设计时,就不必考虑因为型材回弹带来的形状尺寸误差。但是对于金属板材就必须考虑回弹,否则最终得到的冲压件与实际想要的就存在很大的差异,特别是在精密冲裁方面,一点误差的出现都导致废品的出现。 有了完善的工艺方案和先进的加工设备,也不一定能够保证加工出合格的产品,还必须具有严格的管理系统,对整个加工过程进行跟踪监视,确保加工的正确顺利进行。在出现问题时能够及时发现,避免废品的重复出现,浪费成本及加工工时。这就要求整个加工过程是一个系统,与计算机相连接。系统中应该包含加工工时,送料机制,对于多工序还要包括各个工序的加工时间及流程,停工放料时间间隔。从而达到解决时间,提高生产效率,降低成本的目的。1.2.2我国汽车冲压件模具现状在我国,汽车制造业占模具使用比的三分之一,由此可知,汽车覆盖件模具的市场上升空间非常大,在未来的数年时间里肯定能够得到很大的发展。而其中大型复杂的汽车覆盖件模具是整个冲压件模具设计制造的重要部分,占据了冲压件模具的绝大部分。我国冲压件模具有以下几个特点:1.设计技术水平相比欧美国家较低欧美国家的模具设计生产起步早,而且得到了很好的发展,技术水平非常先进,他们的设计主要通过软件设计,其比例高达7090%,CAETE、CAD、UG、Solidworks等软件的应用十分普遍,可以说软件设计时这些国家的主要工具,之所以如此受青睐,主要是这种设计方式,能够很好地保证精度要求。而且利用软件对数据的收集、修改、转换方便快捷,对标准模具更是能够达到一键设计的快速。此外,对那些细小结构,复杂结构利用软件也能做到非常精确。反观我国,拥有软件设计水平的企业很少,大多集中在那些大型的模具厂,这就导致了我国模具行业的发展很难壮大,只是极少数的个体才能生存,因此必须要改变现状,重视中小企业的发展。积极虚心学习外国的先进技术,弃其糟粕,从中吸取对自身有用的部分,发展自身。2.生存制造工艺水平还不够完善目前我国在模具的生产制造工艺上与欧美国家相比较也存在着很大的差距。只有那些大型模具厂才能能力配备数控加工机床,采用自动生产,制定严格的加工工艺。中小模具厂的生产岌岌可危。可以说只是帮大型企业做点零碎的工作,很难发展壮大,像CAM等技术更是别想能够掌握。可以说在模具制造行业的应用非常少,是最近几年才星起的,因此跟国外存在着差异。工人操作水平普遍不高,还不熟悉这方面的加工操作,导致生产效率并没有想象中的高。特别是在复杂的汽车冲压件模具加工上,加工难度高,加之技术还不是很成熟,生产率低。好在我国大量引进数控机床进行分工序加工,降低了加工难度,但这也带来另一个问题,就是需要多套模具才能完成整个零件的生产,原料及成本都有所提高。3.标准化程度低下在标准化方面更是参差不齐,没有标准化可言。各个模具厂各行其事,都是按照适合自己现有设备资料的前提下,进行设计生产,拥有自己的设计标准及生产工艺流程。这也是没办法的,在模具行业起步的时候就存在了这样差异,后来就逐渐形成了现在的局面。欧美国家早早就发现了这一问题,他们非常重视模具的标准化,这也是他们模具行业发展如此快的重要原因。我希望随着我国的技术水平的不断提高,标准化在模具行业中得到重视并执行,以确保模具行业的正常发展。汽车覆盖件冲压模具标准化还不是很完善,汽车冲压件模具标准化程度低下,生产力、生产水平低,仅有极少部分企业采用了标准件,但是许多是依赖进口。相信这种现状在将来的数年之内一定能够得到解决。4.管理水平企业的生命在于质量,要保证良好的质量在于完善的管理机制。国外早已实现了信息化的管理体系,反观我国只有少数企业采用信息系统化管理。管理对一个企业来说极其关键,管理机制不完善,纵使它拥有多先进的技术、设备也不可能设计生产出完美合格的模具产品,相反地会导致一个企业的破产倒闭。因此,企业管理是一个重要的工作,必须完善管理机制,培养出色的管理人才,从成本、生产、销售等环节,严格管控,确保企业的活力。1.2.3汽车覆盖件模具的选材要求不同的汽车覆盖件生产过程有不同的工艺,但覆盖件的选材却有这基本的要求:第一、要求有较高的强度、刚度。为了保障驾乘人员的安全,汽车覆盖件都要求有较高的强度和刚度。只有这样在发生交通事故时,良好的强度和刚度就起到极其重要的作用,车身被碰撞的地方可以很好地吸收一定的动能,并且可以良好地避免了严重的变形,使车辆变形进而报废。第二、要有较好的抗腐蚀耐疲劳性能。现在的环境复杂多变,比如酸雨这种天气对汽车覆盖件的耐腐蚀疲劳性的考验就非常严苛,所以现代汽车覆盖件是一定要具备抗腐蚀性能的。第三、材料的密度不能太高。密度过大就会使车身的总体质量增加,能耗也随之增加,不符合可持续发展的理念。第四、要求材料成形性能好,因为覆盖件绝大部分都是冷冲压成形的,成形性能好才能得到好的成品。否则就会增加加工成本,产品质量也难以保证。第五、是要求材料表面光洁度好,并且容易着漆,因为汽车覆盖件绝大部分需要喷漆,以得到美观的外表。第六是要具有良好的焊接性能,覆盖件要经过焊接装配才能组合成汽车的车身。如果焊接性能不好,熔接痕存在缺陷,焊接处容易断裂,覆盖件就会失效,直接降低整车的刚性、挠性,危害驾乘人员的安全。1.2.4我国汽车覆盖件模具发展方向及展望1.发展巨头的同时,不忘拉动中小企业的发展现在我国大型模具厂,发展平稳基本上形成了一定得规模,朝着,高技术,高精度,高质量的路线发展,随着社会的进步,需求的增加,相信一定能够独挡一面。但我们也不能只顾发展龙头,还要带动个体小企业,没有了竞争的企业是危险的,只有竞争才是一个企业发展的动力及活力所在。只有这样才能真正实现产业的共同进步发展,资源的共享,社会的富强。2.发展技术密集型模具产业当前我国大部分模具设计制造生产等环节技术含量水平低,成劳动密集型。这种形式经济效益低下,成本高而且不利于模具行业的向前发展,发展技术密集型的模具产品刻不容缓。这就需要我国重视这方面专业人才的培养,以及对国外先进技术的大胆引进。3.实行标准化国外的许多先进实现了模具结构零部件的标准化,特别是在欧美国家标准化程度非常完善。我国目前模具的标准化程度不高,各个模具厂家之间存在着不同程度的差异,导致各个企业之间的交流存在困难,导致模具行业发展的受阻。4.完善模具产业管理管理是重中之重,再完美的设计方案,再好的工艺流程,没有完善的管理机制都不可能保证得到合格的模具产品。1.3 课题的内容及意义模具按照成型零件的类型通常可以分为,冲压模具和注塑模具两种,应用比较广泛的是冲压模具,可以将其分为冷冲裁及加热冲裁两种。冷冲裁应用十分广泛,一般是指在常温下利用模具的特定形状结构对目标材料,通过压力机施加一定的压力,让材料分离或者产生一定的变形,以获得具有一定形状和尺寸的制品。本次课题设计的课题内容是汽车后悬置支撑座冲压模具设计,课题是由柳州某模具厂提供。经过对冲压件的结构及工艺分析,要想完成后悬置支撑座的整个生产过程,需要经过三道加工工序,分别是落料、冲孔、成型。查阅冲压件模具设计相关资料,结合现在先进的设计技术,运用三维设计软件UG以及二维绘图软件CAD,进行了严谨的模具零部件结构设计,结合冲模设计标准,对模具整体强度、寿命、成本等进行分析,最终确定采用单工序模,冲件的材质为16MnREL(Q345),厚度5mm,大批量生产。本次设计检验了大学所学的专业知识,更加灵活深入地掌握专业知识,通过理论与实际的相结合可以看出我所欠缺的部分,明白了理论知识要正确有效地运用到实际中,还需要经过许多实践的积累。在设计工程中,了解了汽车覆盖件模具的结构及工作原理,更加灵活熟悉地使用UG、AutoCAD专业设计、作图软件。此外,模具是工业生产的重要部分,一个国家的模具的设计与制造水平代表了这个国家的工业水平。我国在过去的几年间,对外引进国外的先进技术,通过产业结构的调整与提升,改善设计技术水平。对内大力培养专业人才,走人才促进发展,科教兴国的道路,教学与实践相结合。但是我过在高端技术这一方面上与外国先进技术还存在着差距,甚至还是有很多缺陷,有待提升。但是这也恰恰说明了我国模具行业的发展还存在着很大的发展空间,不可否定,汽车覆盖件模具行业仍然有很不可忽视的重要地位。模具的设计与制造涉及到很多的方面,如材料、力学、工艺、分析等许多的内容。对工业生产的发展进步具有非常重要的作用。毕业设计选择汽车覆盖件模具设计,跟我毕业将要从事的工作有着密切的关系,有着重要的作用。2 冲压件的工艺分析及工艺方案的确定根据冲压件的结构要求及其结构特点,不同功能的冲压件也势必不一样,工艺路线也存在差异,要求的工艺也不一样,此外精度等级也存在不同,其成型的难易程度也不太相同,因此不能统一使用一样的方法对不同的冲压件。工艺方案对冲压件的质量影响极大,合理的工艺方案才能生产出质量合格的产品。工艺方案不合理,不仅会提升工厂的生产成本,增加生产难度及复杂程度,降低收益,而且还会影响工厂的整体生产效率,增加设备的负担。因此要详细分析冲压件的各个结构,进行结构特点的合理全方位地分析工件,掌握成型的工艺特点,确定分析冲压件所选用的材料,包括其力学性能及化学成分。此外还要按照冲压件所要达到的精度及性能等级以及加工的难易程度、车间设备是否满足要求,制订合理的工艺方案。总的来说,就是既要保证冲压件的使用要求,达到质量合格。又要尽量消减工序、节约能熬、降低加工难度,减轻对设备的要求,争取用最低成本取得最大的经济效益。冲压件工艺性方案好坏决定了冲压件的成型难易程度、形状位置精度、质量等级等,全方位地分析冲压件各部分的结构特点,结合大学所学的专业知识,我努力制定完美合理可行的冲压工艺方案,以确保冲压件生产的顺利进行,避免生产事故等意外的发生。而冲压工艺方案的优劣,直接决定了冲压件制造生产过程的可行性、冲压件成品的质量好坏、产品成本的高低,如果设计人员能力不足,错误采用了不合理的冲压工艺方案,这往往造成不可估算的损失,不仅是企业财产的亏损,甚至对操作工人造成生命威胁。这是绝对不允许出现的。因此在进行冲压模具设计前,必须按照冲压件的使用要求及结构特点,对冲压件进行认真合理的全面分析,确定合理可行的工艺方案。工艺分析一般从冲压件的实际使用要求,精度等级,形状结构入手,而后考虑选材的化学力学性能、加工难易程度、对设备的要求等,最终确定合理可行的工序方案。在保证冲压件使用要求、满足使用条件、质量等级合格的前提下,尽可能减少级工序数,选用性能合理,价格适当的材料,节约用料,降低成本。利用最少的成本,获得最大的经济效益。2.1 冲压件的特点本次课题研究的是某型汽车后悬置支撑座,材料为16MnREL(Q345),料厚5mm,屈服强度为345MPa抗拉强度为470630MPa,伸长率为22%。要求该冲压件的形状尺寸、孔径和孔位必须准确,不能超过误差范围,达到产品使用的设计要求。成形后表面要平整光滑,不能出现翘曲、回弹严重、出现褶皱、裂纹等严重的质量缺陷。如下图2-1、2-2为冲压件实体图:图2.1 正三轴零件图图2.2 零件仰视图板材的厚度为5mm,属于厚板冲压料,在冲压件中比较常见。本次课题的任务是后悬置支撑座冲压件模具设计,成型后的零件要达到本工序的要求:正确的形状尺寸,不能有偏差,孔径位置要准确,不能有毛刺,冲压件成型后的工件表面没有褶皱、开裂等现象,不能影响到整个零件的形状。从零件图可以看出后悬置支撑座形状相对比较复杂,而且此零件的外形不对称型,需要冲出多个孔,还要进行弯曲。为保证正确的形状位置精度,生产中常采用压料板,防止板料在加工过程中出现滑移,也可以避免褶皱的产生。在冲压生产实际中,结合后悬置支撑座的几何形状、精度要求和成形特点等情况,考虑冲压过程中失稳起皱及材料力学性能等,采用相应的防皱措施。弯曲时考虑滑移、拉裂及弯曲后回弹等可能现象的出现,在后悬置支撑座的结构上采取:工艺圆角半径尽量的大些、曲面形状在设计时,拉深方向的深度应设计得浅一些等措施。2.2 后悬置支撑座的工艺分析根据后悬置支撑座的结构特点及选材要求,对其进行工艺分析。发现后悬置支撑座的结构不是很发杂,结合各个方面的因素开始初步确定可行的工艺方案。冲压件加工过程不仅需要考虑设备是否能够满足生产要求,还要考虑冲压工艺方案的合理可行性,合理的工艺方案是保证生产可行性的前提保障。所谓的工艺可行性,就是指要生产的零件对根据这个零件的结构特点等制定的冲压工艺方案是否能够生产出合格的产品。在这里就是按照后悬置支撑座冲压件的尺寸大小及精度、形状结构特点、所选材料的要求等确定的工艺方案,是否能够生产出合格的产品,是否符合冲压件加工的工艺要求。通常情况下汽车冲压件都必须制定合理可行的工艺方案,其是衡量设计水平的重要指标。合理可行的工艺方案就是工序级数少、工序排列顺序正确可行、对模具结构的要求比较简单、对生产设备的要求及负荷低、整体成本最优。根据后悬置支撑座冲压件的零件图,对零件进行冲压工艺分析,首选从后悬置支撑座的尺寸大小、精度,以及结构特点出发,初步确定几个可行的工艺方案。然和结合零件的材料要求、车间设备、成本等,最终确定技能保证零件的使用要求,又能将成本奖到最低,收益最大的方案。由图2-1和2-2分析零件的结构,该零件的尺寸长宽(154110),材料较厚(5mm),形状相对复杂,整体需要落料、冲孔、成型(弯曲)三道工序。是一个曲面变化较少但工序需要多的单工序模具。横断面成U型,成型之后零件表面质量要求不是严格,主要是不允许表面出现严重回弹、弯曲处不能有拉裂现象、不允许出现皱纹等。因此设置了压料板。材料16MnREL是旧牌号,现在新牌号为Q345.性能指标:抗拉强度b/MPa:470630伸长率(%):22%屈服强度s/MPa:345弹性模量E=200210Gpa,塑性硬化指数n=0.22,硬化指数在钢材中是比较高的,材料成形极限较大。2.3 确定冲压方向对于大型的汽车冲压件,特别是车身表面的覆盖件,大多是形状复杂多变,空间曲面众多,制造成型往往都需要多个工序,而且模具结构复杂,才能完成整个零件的生产。因此确定冲压方向是不能只考虑单个工序的冲压,要统筹兼顾,多方协调。各个工序的冲压方向在确定时要统一,不能只考虑一道工序的冲压方向,要根据整个成型过程各道工序的具体体情况来具体分析。在整个覆盖件模具的设计过程中,冲压方向的确定要先确定,避免因为冲压方向不统一,造成工序多余,模具结构复杂,成本提高等设计上的基本问题。此外,实际生产中也要求同一个覆盖件的生产各道工序的冲压方向要一致。以便进行流水作业,避免需要人工翻转工件,使生产过程简单化,提高生产效率。冲压方向不一致还容易导致工件的位置精度出现偏差,出现没必要的误差,提高了废品出现的几率。本次课题天窗加强板的成型工序有拉延、修边、冲孔、整形等,各工序的冲压方向尽量要统一。冲压方向我在本次设计中落料、冲孔、成型三道工序,考虑采用单工序模,因此要分别确定落料、冲孔、成型三个工序的冲压方向,而且三个工序的冲压方向要统一。根据后悬置支撑座的数模,已经很明显地标出了落料的轮廓线、需要冲孔的位置及大小及成型的弯曲线。根据设计要求,理论上,冲压力的方向要与刀具刃口运动的方向一致。在实际生产中允许有微小的工艺偏差角度,但是该偏差角并不是随意确定的,而是根据实际情况有特定的限制。根据后悬置支撑座的各个工序的零件很快得出最好的冲压方向,如下图所示,冲压方向沿着图中标明的方向。冲压方向图2.3 落料冲压方向图2.4 冲孔图2.5 成型2.4 冲压工艺方案的确定冲压件的形状结构及工艺特点直接决定了冲压件的成型难易程度,详细具体全面地分析冲压件的工艺特点,才能建立完整合理可行的冲压工艺方案,冲压工艺方案的优劣,决定了冲压模的设计制造及成本等,继而影响冲压件的质量。因此必须对冲压件进行详细合理的工艺分析,分析冲压件的材料、结构、性能及加工难易程度,确定科学的、适合于实际的工序方案。并在保证产品的设计要求、满足使用条件的情况下尽量减少工序,采用适宜的材料,尽量节约用料,选择先进且合理的加工技术,力求冲压工艺方案做到最简化,利用最少的资源,生成最大的经济和社会效益。在保证一切生产合理合法的要求下实现利益最大化。模具CAE技术就是在设计制造模具之前,在计算机上模拟出冲压件在模具中成形的真实过程,向用户告知模具结构设计、工艺条件状况是否合理,并最终为用户提供出最佳的模具设计工艺方案,可靠性达到80%以上。从而缩短模具设计与制造周期2/5(对于复杂模具而言),并提高模具质量和产品合格率,进而可大幅度降低制造成本,增强产品的市场竞争力2.4.1 工艺方案的初步确定通过对后悬置支撑座零件进行分析,结构属相对复杂的零件,考虑模具制造难易程度、投资成本、设备等因素,分三个工序完成后悬置支撑座的加工,分别为落料、冲孔、成型。综合各个方面的考虑,初步设计了3个方案:方案一、落料 成型 冲孔方案二、冲孔 落料 成型方案三、落料 冲孔 成型2.4.2 工艺方案的分析及确定方案一、三道工序安排顺序不合理,成型工艺安排在冲孔工序之前,不符合生产的要求。成型工序应放在最后,要不然不能保证零件的最终型面符合产品的使用要求,故不采用。方案二、把冲孔工序放在首位,很难保证孔位精度,而且冲好的孔有可能在下一步的落料工序加工过程中出现变形,完成难以保证成型工艺,且对冲压机的负荷太大,故不采用。方案三、该方案安排合理明了,工序安排顺序正确,落料、冲孔没有一步进行,分开两步,减少了对冲压设备的要求及负荷,而且成型简单得多,放在最后,保证了产品最终的形状结构,综合考虑选择方案三。综上考虑,最终确定的冲压工艺方案为:落料 冲孔 成型 不仅符合汽车冲压件模设计规程,而且也符合实际生产要求。3 落料模设计利用设计要求制造出的模具,使板料或者型材分离的一种工序,我们统称为冲裁。其中包括落料、冲孔、切断、修边、切舌等,落料、冲孔是最为常见的两种冲裁工艺。本次课题研究的是落料冲裁模具设计。落料是利用冲裁模锋利的刃口,使板料或者型材沿封闭曲线相互分离,然后将封闭曲线以内的那一部分作为零件的一种冲压加工方法。冲裁变形分三个阶段:弹性变形阶段 指上模下行,凸模接触板料开始加工加压,上模继续下行对板料施加压力,板料在凸凹模作用下产生弹性压缩、变形、拉伸挤压等。此时板料的应力达到弹性极限。板料在模具中,凸模下面的一部分呈弯曲状,凹模的上面部分向上翘起。这样的变形主要取决于凸模跟凹模之间的间隙以及板料的厚度。塑性变形阶段 随着上模继续下行,板料受到的压力逐渐增加,当应力超过弹性极限时,板料开始产生塑性变形。板料随凸模,被压入凹模的量增大,塑性变形程度加大,应力变形区的加工硬化现象加剧。冲裁的变形力不断加大,板料开始出现微裂纹,塑性变形结束。断裂分离阶段 上模继续往下,在压力机的作用下,板料受到的压力继续增加,变性区的应力达到了破坏所需的极限,凸凹模图凹模之间侧面的变形区产生裂纹,上下裂纹逐渐扩张,直到两裂纹相遇,板料被切断分离。3.1 冲压工艺计算及设计3.1.1 排样及材料利用率的计算冲压件的面积与所用板料的面积的百分比叫材料的利用率。材料利用率是衡量材料利用是否合理的一个重要指标,理想的材料利用率可以大大降低成本,提高经济效益。冲压生产过程中,废料的类型有两种,一是结构废料,其是由冲压件的形状结构特征所产生的,二则是工艺废料,由冲压件之间以及冲件与板料侧边的间隙决定的。提高材料利用率主要从减少工艺废料入手,主要措施有:设计合理的排样方案设计选择合理的板料规格,利用废料制作尺寸小的零件,合理剪裁板料1.材料利用率计算一个步距内的材料利用率:A为一个步距内冲压件的实际面积(mm2);B为板料的宽度(mm);S为步距(mm)整个板料的利用率:n为整条板料的冲件数;A为一个冲件的实际面积(mm2);B为板料的宽度(mm);L为整张板料的长度(mm)按照落料零件的形状尺寸,如图3.1图3.1 落料零件图由图容易看出,零件应该采用直排样布置,排样图如下图3.2:图3.2 排样图2.搭边值的选择与板料宽度的确定(1)搭边值的确定:在设计冲压排样图时,冲压件与冲压件之间,冲压件与板料侧边之间的间隙叫做搭边值,它属于公益废料,合理正确的搭边值可以有效地提高材料的利用率,提高经济效益。另外搭边值还具有非常重要的作用:a.补偿定位误差及剪板误差,确保冲裁出合格的产品b.可以增加板料的强度、刚度c.方便送料,提高生产效率搭边值的大小对整个冲压生产过程有着非常巨大的影响。搭边值太大,材料利用率低,浪费资源,提高了成本,降低了效益。搭边值过小,又起不到设计搭边值的作用,严重影响冲压生产过程,直接导致废品的出现。更有甚者,由于搭边值过小,在工作过程中,搭边被拉入凸凹模间隙中,造成冲裁力不均匀,刃口磨损,破坏模具。因此搭边值的设计一定要合理,有一下几个设计原则:a.硬材料的搭边值可小些,软材料、脆性材料的搭边值要大一些b.冲压尺寸大或者有尖角形状复杂的零件,搭边值要大些c.厚材料冲裁搭边值取大一些d.手工送料、设计有侧压装置的搭边值可以小些参考冲压及塑料注塑模具课程设计指导与实例表3-1板料的厚度为5mm,结合实际,冲压件之间搭边值取6mm,冲压件与板料侧边之间取6mm。2.板料宽度的确定根据零件的外形尺寸及搭边值确定板料的宽度B=225mm,利用UG软件测量得,零件的实际面积为A=22461.5mm2,步距S=116mm;板料长度L=1166mm,则有:3.1.2 刃口尺寸的计算及冲裁间隙的确定凹模、凸模的刃口尺寸设计上有着严格的要求及设计原则,凸凹模刃口尺寸公差更是直接影响到冲压件的质量。模具的间隙值通常是靠凸凹模的刃口尺寸及公差来保证。设计计算刃口尺寸是整个模具设计过程中重要的一个环节,需要非常重视间隙值的选择。1.凸凹模刃口尺寸计算原则:质量合格的冲压件其光面应该得到很好的保证,测量及使用也是以光面为基准。落料的光面形状尺寸由凹模觉得,而冲孔则是由凸模决定,所以在设计计算时要分两种情况考虑。其原则如下:落料 冲压件的光面尺寸跟凹模的刃口尺寸基本保持一致,因此以凹模尺寸为基准进行设计计算,考虑实际生产过程中,凹模尺寸随着生产的进行,尺寸会越磨越大,为保证模具在使用一段时间后依然能够生产出合格的产品,因此在尺寸公差允许的范围内应该去较小的尺寸,落料凸模尺寸则按凹模尺寸减去最小间隙值。冲孔 冲压件的光面尺寸跟凸模的刃口尺寸基本保持一致,因此以凸模尺寸为基准进行设计计算,考虑实际生产过程中,凸模尺寸随着生产的进行,尺寸会越磨越小,为保证模具在使用一段时间后依然能够生产出合格的产品,因此在尺寸公差允许的范围内应该去较大的尺寸,落料凹模尺寸则按凸模尺寸加上最小间隙值。孔心距 当零件需要冲出多个孔位时,孔心距的尺寸精度靠凹模的空心距保证,凸凹模的磨损不影响孔心距。冲压模具的制造公差 凸凹模刃口尺寸精度的选择要保证零件的精度要求,保证模具的寿命。2.凸凹模刃口尺寸计算本次研究的是落料工序的冲压模具设计,以凹模尺寸为基准,计算公式如下:落料凹模刃口尺寸;落料凸模刃口尺寸3.凸凹模间隙的确定凸凹模间隙对断面的质量、零件尺寸精度有着重要的影响。间隙过小,在冲裁过程中会形成第二光面,影响冲件的整体美观。在断面处还会出现细长的毛刺,但可以清除还可以使用,只是花费了时间。间隙过大,光面断面减小,断面产生的毛刺不易除去,零件严重翘曲,影响冲压生产过程,决不允许出现。参考冲压工艺及冲模设计查表3-4根据零件的材料16MnREL(Q345),厚度t=5mm,可知最小间隙应该选择=(0.6800.780)mm考虑实际情况,这里选择=0.700mm3.1.3 冲裁力的计算及压力中心的确定1. 冲裁力的计算冲裁生产过程中,凸模受到的最大压力称为冲裁力。它包括对板料施加的正压力及摩擦阻力,冲裁力是选用压力机和设计模具的重要依据。现在研究的是冲压落料工序的模具设计,分析零件计算落料所需要的冲裁力,计算公式如下:式中,F为冲裁力(N);L为冲裁周边长度(mm);t为材料厚度(mm);为材料的抗剪强度(MPa);K为系数一般取1.3;为材料的抗拉强度(MPa)。利用UG三维绘图设计软件测量得L=715.8mm,查找有关资料可得=550MPa,则冲裁力为:2. 压力中心的确定模具的压力中心应该与压力机滑块的中心重合,冲压力合力的中心作用点叫做模具的压力中心。这里设计的落料单工序模设计有模柄,因此压力中心、滑块中心、模柄的中心,三心必须重合,在一条线上。否则,在冲压生产过程中,滑块就会收到偏心载荷,造成压力机产生附加载荷,损坏压力机。对于模具而言,导致导向机构,如导柱导套、导板等,出现不正常的磨损,影响模具的寿命。此外,凸凹模之间的间隙也得不到设计上保证,导致冲压过程中产生废品。考虑实际生产情况,在确定压力中心与模柄中心线是否重合时,必须不超过允许的公差范围。在这里主要让冲压落料模的模柄中心线在模具的装配过程中与压力机的滑块中心的重合度在误差允许的范围内即可。3.1.4 压力机的选用选择合适的压力机才能保证生产的顺利进行,才能够冲出合格的产品。压力机的选用整个是模具设计过程中很关键的一环,它关系到模具能否正确安装,能否达到设计的使用寿命,能否按照预期设想正常工作,产品是否达到使用要求等。此外,在整个覆盖件模具的设计过程整许多参数的选择都跟选用的压力机有关。压力机是一种结构精巧的通用性机器,广泛应用于切断、冲孔、落料、弯曲、成型等工艺。它的种类有很多,应用最为广泛的有曲柄压力机和液压机。曲柄压力机的主要部件就是曲柄滑块,起作用是将电动机的旋转运动转换为往复直线运动。而液压机的工作原理则是根据著名的帕斯卡原理,利用液体的压力传递能量,以完成各种成型加工。对于中小型模具一般采用曲柄压力机,灵活可靠,行程运动的速度相对较快,生产效率也高。液压机则是应用于大型模具的生产制造,工作稳定。1.计算总冲压力卸料力、推件力、顶件力是由压力机、卸料装置、或者顶件装置产生的。根据经验有以下计算公式:卸料力:推件力:顶件力:式中,F为冲裁力(N);n为同时梗塞在凹模内的工件数;、为系数,查阅冲压工艺及冲模设计表3-9可得:=0.035,=0.045,=0.05。由此可得: 本次落料模采用的是弹性卸料装置和上出料方式,则有:2.压力机的选用本次设计的是某型汽车后悬置支撑座冲压件落料工序的模具设计,冲裁总压力为2126KN,所需冲压力较大,因此考虑选用闭式双点压力机。经查阅有以下几种压力机的参数作参考;表3-1项目单位J36-200J36-2500J36-315J36-400公称力KN2000250031504000标称压力行程mm13131313滑块行程mm400400500500最大装模高度mm600700700800装模高度调节量mm250315315400工作台尺寸左右mm2350235028002800前后1250125015001500根据表中的数据,选择J36-250型闭式双点压力机。3.2 模具结构设计3.2.1 落料凹模的落料零件的形状尺寸由凹模决定,分析落料工序零件,考虑实际情况等因素的影响。通过严谨的计算,预留结构位置。本次设计由于后悬置支撑座零件整体尺寸不是很大,而且结构相对来说不是复杂多变,因此根据形状尺寸,进行凹模的结构设计。凹模落料轮廓,刃口形状必须要跟零件形状保持一致,按照凸凹模间隙的原则,要相互重合在一起。可以正确保证最终得到的产品的形状符合要求,避免了板料中零件可能部分不重合受压变形情况的发生。凹模上还必须在相应的位置上加工出相应的避让孔,避免安装其他部件时出现干涉现象。具体结构如下图:图3.3 落料凹模3.2.2 落料凸模的设计落料零件的形状尺寸由凹模决定,凸模形状尺寸根据凸凹模间隙设计原则设计,形状与凹模的一致.考虑装配连接,预留螺钉等连接件的位置以及到侧边的距离,足够保证凸模的整体强度及硬度,凸模作为落料成型的重要零件,属于工艺零件,凸模的形状尺寸精度,直接决定了后悬置支撑座质量的好坏。凸模通常好有几种形式,常见的有两种,整体式和组合式,在这里采用整体式的凸模,结构如下图:图3.4 落料凸模3.2.3 下模座的设计通常情况下大型的覆盖件磨具的模座采用整体铸造的方法,首先浇铸出模座的大体结构,预留足够的机加工余量。浇铸成型后只需要在需要机加工的地方,按照要求加工出具体的结构即可。考虑本次落料模的模座结构比较简单,按照要求裁取尺寸合适的板材,不能存在内部缺陷,否则在机加工及冲压生产过程就会出现问题,预留各个连接件的位置,在保证强度的前提下,这里设计下模座的整体结构尺寸为56035050,材料采用Q235,如图:图3.5 下模座3.2.4 上模座的设计一般情况上下模座的基本工艺要求相同,不同的地方就是上模座与压料板的配合处有特定要求,还有就是上模座主要是跟压力机的上工作台面相连,需要设计有连接结构。此外还要加工出导柱孔、螺钉过孔、销孔等。综合考虑分析后,结合工艺要求,最终确定了上模座的整体结构,如下图:图3.6 上模座3.2.5 推件板的设计推件板的作用是在冲压生产过程结束后,将产品从凹模中推出,完成卸料的作用。在合模的过程中,起到压料,防止板料翘曲的作用。后悬置支撑座落料工序设计的冲压模具中的推件板,是装在上模部分,采用下出件的方式,因此推件板的形状轮廓及尺寸要与凹模配作,设计合理的间隙,保证推件的顺利进行。推件板的压料作用是压住板料,防止在对型材加工时,不规则褶皱的出现,影响产品的质量。但是推件板的压边力也不能太大,否则板料不能顺畅地流进型腔内,这就会造成板料的拉裂,造成废品的出现,因此压料板的设计非常关键。采用的材料为45号刚,整体结构如下图所示:图3.7 推件板3.2.6 卸料板的设计本次设计采用倒装式,落料凸模装在下模上,因此卸料板也是设计在下模上,主要是起到压料及卸料的作用。本次实际的是弹性卸料装置,通过卸料螺钉连接固定于下模座上,下模座和卸料板之间安装有弹性元件,这里采用的是弹簧元件,弹簧设计有一定的行程缩量,用于在开模时提供卸料力。弹压卸料板还可提供压料力,防止条料不平或翘曲。在冲压成形和卸料过程中,弹性卸料板与凸模之间存在有相对运动。对薄料或精密件,要对弹性卸料板进行导向,即内导向。本次设计采用导柱导套导向,分别在四个拐角处设置,保证卸料的正确运动,确保废料能够顺畅推出。具体结构如下图:图3.8 卸料板3.2.7 其他模具结构的设计下模加高板、下模固定板、上模加高板、上模固定板等结构的设计,根据上面设计完成的零件,参考实际,保证功能强度的前提下,尽量节约成本,结构分别如下图:图3.9 下模加高板图3.10 下模固定板图3.11 上模加高板图3.12 上模固定板3.2.8 起重结构的设计汽车冲压件模具的整体重量很大,在需要搬动或者翻转时,车间常采用大型的起吊机。因此模具相应的位置要设计方便起吊模具的机构。起吊装置的设计不能损坏模具,大小位置要合理,而且还要有足够的强度刚度,足够承受整个模具的重量,不能在起吊过程中出现断裂现象,否则后果不堪设想。一、起重结构的类型根据汽车覆盖件模具不同实际情况,起重结构通常有三种:起重棒、起重孔、吊耳。各有其特点,如下:起重孔:在模具相应部件的底板打四个对称的孔,这就叫做起重孔,其结构承载能力较小,一般仅用于小型的模具,起重孔结构尺寸可见下图:DL承载重量(t)12300.2515400.52050125602306044070850801460100208012030 图3.13 起重孔起重棒:按照起重棒与相应部件的连接方式,有这几种类型,铸造式起重棒、镶嵌式起重棒。铸造式起重棒是在模具的相应位置直接铸造出来的,起重的吨位一般在12T之内。而镶嵌型起重棒针对于可手工搬动的模具,一般应用于小型模具。当一定要起重时吨位也不会超过6T。起重棒应用于小于1600mm中小型模具,承载能力大于起重孔小于吊耳。吊耳:吊耳起重结构由铸造出的孔与另外加工的起重销配套使用的,因此起重吨位比较大,可用于外形轮廓尺寸超过1600mm的模具,常应用在大中型模具。铸造出的双耳与模座是一体的,结构非常可靠稳定,强度刚度足够。另外吊耳的大小还可以根据模具的实际吨位来设计。如图:图3.14 吊耳本次落料模采用的就是吊耳起重机构。3.3 导向机构的设计导向机构故名思议就是上下模在运动时或者是模具内部推件板、压料板等具有相对运动零部件之间运动时,确保准确导向机构。导向机构的作用有:一是保证上下模开合模的准确,在合模时,导向机构引导模具准确运动,而后凸模和凹模再合模,避开上下模的瞬间碰撞。二是承受一定的侧向冲击载荷,在模具工作过程中由于零件轮廓的不规则,肯定会产生一定的侧向压力,这时导柱就能很好地避免因为侧向压力的作用可能导致模具工作不准确的现象。三是导向机构可以很好的保证模具在工作过程中平稳可靠。用于冲压模的导向机构的种类有很多种,其中最常见的有导向杆、导板、导钉、导柱导套,在汽车冲压模行业中应用最为普遍的就是导板、导柱导套。导柱跟导套通常是配套使用的,导柱与导套之间是间隙配合,在开合模的过程中保正模具的正确运动,引导模具按照设计的动作方向完成整个工作行程。导柱导套的表面粗糙度一般是Ra0.8Ra1.6的范围之内,位置精度则是00.02mm之间,导向精度为0.020.04mm。相比导板来说导柱导套的导向精度更高,工作更加平稳。但是导柱导套导向的缺点就是,承受侧向载荷的能力没有导板强,如果有侧向压力,导柱导套磨损很快,导向精度就下降,此外还有可能在模具工作时导致卡死。根据后悬置支撑座的结构特点及设计要求,在本次落料模设计中使用的导向机构嵌入式导柱导套,也是最常用的一种导向方式。如下图所示,导套、导柱之间采用的是间隙配合(H7/f6),保证导向准确,避免出现导套、导柱配合不严谨,间隙过小会导致卡死的现象,间隙过大,导致在使用的过程中发生震动的情况。导柱与模座、导套与模座之间采用的是过盈配合(H7/m6),保证紧密牢固。这种导向方式不足的地方,就是装配时需要将导柱经过特殊的冷冻处理,以使导柱缩小一定得尺寸,保证能够装配的上,有很大的装配难度,磨损后更换困难。因此在中小型模具等非大批量生产时才会用这种导向方式。图3.15 嵌入式导柱导套3.4 模具的整体结构及工作原理3.4.1 模具装配图经过前面各个零部件的设计,初步确定落料模的整体结构,下图为其装配图:图3.16 落料模装配图3.4.2 落料模工作原理开模时,上模跟下模相互分开,板料在送料机构的作用下送到上下模之间,然后在压力机的作用下,上模在导柱的导向下下行,推件板首先跟板料接触,起到压料的作用。上模继续下行,对板料施加剪裁力,将板料按照凹模的轮廓将板料冲出所需的形状,合模结束。在压力机的作用下,上模上行,推件板在弹簧的作用下降冲件从凹模中推出,而卸料版则是在弹簧的作用下,将板料顶起,以为下一个冲压过程做准备,整个冲压过程结束。4 冲孔模设计4.1 冲压工艺计算及设计4.1.1 刃口尺寸的计算及冲裁间隙的确定1.凸凹模刃口尺寸的计算在这里主要是冲孔工序的冲压模具设计,冲孔零件光面尺寸以凸模的形状尺寸决定,因此以凸模为基准,冲孔凹模的刃口尺寸为凸模刃口尺寸加上最小间隙值,计算公式如下:为冲孔凸模刃口尺寸,为冲孔凹模的刃口尺寸2.冲裁间隙的确定同上,参考冲压工艺及冲模设计查表3-4,根据零件的材料16MnREL(Q345),厚度t=5mm,可知最小间隙应该选择=(0.6800.780)mm考虑实际情况,这里选择=0.700mm4.1.2 冲裁力的计算及压力中心的确定冲裁力的计算本次冲孔工序需要冲孔的类型有两种,一种是直径为12mm,需要冲出四个:一种直径则是52mm。直径尺寸不一,根据冲裁力计算公式有:式中,F为冲裁力(N);L为冲裁周边长度(mm);t为材料厚度(mm);为材料的抗剪强度(MPa);K为系数一般取1.3;为材料的抗拉强度(MPa)。利用UG三维绘图设计软件测量得L=314.2mm,查找有关资料可得=550MPa,则冲裁力为:4.1.3 压力机的选用本次设计的是某型汽车后悬置支撑座冲压件落料工序的模具设计,冲裁力为864.05KN,所需冲压力较大,因此考虑选用闭式双点压力机。经查阅有以下几种压力机的参数作参考;表3-1项目单位J36-63J36-80J36-100J36-125公称力KN63080010001250标称压力行程mm891010滑块行程mm120130140140最大装模高度mm460480500装模高度调节量mm90100110120工作台尺寸左右mm710800900970前后480540600650根据表中的数据,选择J36-100型闭式双点压力机。4.2 模具结构设计4.2.1 冲孔凸模的设计此次设计的凸模有两种,一种是直径为12mm,一种是直径为52mm。直径为12mm的孔,为小孔冲裁,可考虑采用标准冲孔凸模。直径为52mm的孔,为较大孔的冲裁,考虑设计成非标准的冲孔凸模形式,为节省材料降低成本,采用冲头及冲头座这种形式。根据零件冲孔的孔径,设计计算出冲口凸模的结构如下图:图4.1 直径12mm的冲孔凸模图4.2 直径52mm冲孔凸模4.2.2 冲孔凹模的设计冲孔以凸模的刃口尺寸为基准,根据凸凹模间隙的原则设计凹模的刃口尺寸,考虑凹模与凹模固定板之间的配合,在这里设计成圆形嵌入式的凹模,采用的材料为Cr12MoV,以保证凹模的寿命及强度,保证生产的顺利进行,凹模的具体结构如下所示:图4.3 直径12mm的冲孔凹模图4.4 直径52mm的冲孔凹模4.2.3 上下模座的设计上模座安装在压力机的上工作台面,设计有连接固定的结构,此外在上模座上还需要作出螺钉孔、销钉孔、导柱孔等,还要兼顾强度问题,因此设计其结构如下图:图4.5 上模座下模座与上模的设计原理是一样的,如下图:图4.6 下模座4.2.4 下模凹模固定板的设计在这里因为需要将冲孔凹模嵌入到下模凹模固定板中,所以下模凹模固定板的厚度相应地设计得厚一点,以保证有足够的位置设计台肩用以固定凹模。还要钻出废料落下的废料孔以及各个连接螺钉的过孔,其结构如下:图4.7 下模凹模固定板4.2.5 冲头固定板的设计冲头固定板的作用主要是起到固定冲头的作用,在冲头的相应位置加高出沉孔以及螺钉、销钉的孔,结构如下:图4.8 冲头固定板4.2.6 压料板的设计设计压料板的目的在于,在冲孔过程中紧紧压住板料,确保在正确的位置冲出所需的孔位,压料板的动力主要由弹簧提供,其相对运动的导向是通过导柱导套,因此在压料板的四个角的合适位置设计有导套孔,按照公差要求严格加工,其结构如下图:图4.9 压料板4.2.7 冲孔模其他模具结构的设计起重机构、导向机构、加高板、垫板等的设计参考落料模部分的设计,在满足强度,使用要求的前提下,尽量降低成本,达到高收益的目的。4.3 冲孔模整体结构及工作原理4.3.1 冲孔模装配图经过严谨的计算设计,将冲孔模各个部分按装配关系整体装配起来,可以看出模具的整体结构,如图:图4.10 冲孔装配图4.3.2 冲孔模工作原理开模时,上模跟下模相互分开,板料在送料机构的作用下送到上下模之间,然后在压力机的作用下,上模在导柱的导向下下行,压料板首先缓慢跟板料接触,上模继续下行,然后冲头跟板料接触,对板料施加剪裁力,在相应的位置冲出孔,合模结束。在压力机的作用下,上模上行,压料板在弹簧的作用下回复在初始位置,为下一个冲孔过程座准备,整个冲压过程结束。5 成型模的设计5.1 冲压工艺计算及设计5.1.1 成型弯曲力计算分析零件可知,该零件为U形件弯曲,则有以下计算公式:式中,F为弯曲力(N);b为零件宽度(mm);r为零件弯曲内弯曲半径(mm);为材料抗拉强度(MPa);k为系数,一般取1.3,采用UG软件测得,r=4mm,b=110mm,则可得:5.1.2 压力机的选用本次设计的是某型汽车后悬置支撑座冲压件落料工序的模具设计,冲裁力为152.93KN,所需冲压力较大,因此考虑选用闭式双点压力机。经查阅有以下几种压力机的参数作参考:表3-1项目单位J36-63J36-80J36-100J36-125公称力KN63080010001250标称压力行程mm891010滑块行程mm120130140140最大装模高度mm460480500装模高度调节量mm90100110120工作台尺寸左右mm710800900970前后480540600650根据表中的数据,选择J36-125型闭式双点压力机。5.2 模具结构设计5.2.1 成型凹模、凸模的设计成型凸模的尺寸设计要根据零件的成型要求设计,加工要严格控制。成型凹模与凸模相互配作,具体结构如下:5.1成型凸模 5.2成型凹模5.2.2 上模座的设计上模座安装在压力机的上工作台面,设计有连接固定的结构,此外在上模座上还需要作出螺钉孔、销钉孔、导柱孔等,还要兼顾强度问题,因此设计其结构如下图:5.3上模座5.2.3 下模箱体的设计下模箱体的结构如下:5.4下模箱体5.3 成型模整体结构及工作原理5.3.1 成型模装配图5.3.2 成型模工作原理开模时,上模跟下模相互分开,板料在送料机构的作用下送到上下模之间,然
- 温馨提示:
1: 本站所有资源如无特殊说明,都需要本地电脑安装OFFICE2007和PDF阅读器。图纸软件为CAD,CAXA,PROE,UG,SolidWorks等.压缩文件请下载最新的WinRAR软件解压。
2: 本站的文档不包含任何第三方提供的附件图纸等,如果需要附件,请联系上传者。文件的所有权益归上传用户所有。
3.本站RAR压缩包中若带图纸,网页内容里面会有图纸预览,若没有图纸预览就没有图纸。
4. 未经权益所有人同意不得将文件中的内容挪作商业或盈利用途。
5. 人人文库网仅提供信息存储空间,仅对用户上传内容的表现方式做保护处理,对用户上传分享的文档内容本身不做任何修改或编辑,并不能对任何下载内容负责。
6. 下载文件中如有侵权或不适当内容,请与我们联系,我们立即纠正。
7. 本站不保证下载资源的准确性、安全性和完整性, 同时也不承担用户因使用这些下载资源对自己和他人造成任何形式的伤害或损失。

人人文库网所有资源均是用户自行上传分享,仅供网友学习交流,未经上传用户书面授权,请勿作他用。