目 录
摘要·····································································1
关键词···································································1
1 前言···································································1
2 花生脱壳机设计方案比较·················································2
3 剥壳方案的分析和确定···················································4
4 结构设计·······························································6
5 电动机选择·····························································7
6 脱壳装置设计···························································8
6.1 快慢轴辊皮带设计·····················································8
6.1.1 电动机带轮与快辊传动设计···········································9
6.1.2 电动机带轮与慢辊传动设计··········································11
7 换向齿轮传动设计······················································14
7.1 齿轮基本尺寸设计····················································14
7.2 齿轮接触疲劳强度校核················································16
7.3 齿轮弯曲疲劳强度校核················································17
7.4 齿轮设计小结······················································· 18
8 清选装置设计························································· 19
8.1 风机及装置选择······················································19
8.2 振动筛皮带设计······················································20
9 轴的设计······························································23
9.1 慢速辊轴设计························································23
9.1.1 轴的结构设计······················································23
9.1.2 轴的弯扭合成校核··················································24
10 轴承校核 键校核 润滑 装配使用·····································24
10.1 轴承校核与润滑·····················································24
10.2 键校核·····························································24
11 结论·································································25
参考文献································································26
致谢····································································27
摘 要:碎壳损伤是影响花生籽粒品质的重要因素之一,本文通过对滚筒栅条式花生脱壳机构、钢齿双辊筒式花生脱壳装置与锥体式花生剥壳机构的机构设计进行分析研究,通过对各种不同花生去壳机的分析比较,确定并设计出滚筒式花生剥壳分离机的设计方案,对传动及重要机构进行必要的计算和说明。
关键词:花生籽粒; 辊轮; 双辊筒式; 分离
Design of Peanut Shelling and Separating Device
Abstract: The impact of broken peanut shells injury is an important factor in grain quality, the paper type through the peanut shelling drum Rack bodies, steel tooth double cylindrical drum device and the cone-type peanut shelling peanut sheller analysis of mechanism design agency Research and Experimental Research by institutions shelling shelling against the three kinds of performance comparison, for us to further understand the basic principles of shelling peanuts, peanut injury for the design of new low-shelling machine provides a useful reference.
Key words: peanut seeds; trash rack roller-type; steel tooth double cylindrical drum; cone type
1. 前言
1.1花生脱壳机的简介
我国花生脱壳机的研制自1965年原八机部下达花生脱壳机的研制课题以来,已有几十种花生脱壳机问世。只进行单一脱壳功能的花生脱壳机结构简单,价格便宜,以小型家用为主的花生脱壳机在我国一些地区广泛应用,能够完成脱壳、分离、清选和分级功能的较大型花生脱壳机在一些大批量花生加工的企业中应用较为普遍。国内现有的花生脱壳机种类很多,如6BH一60型花生剥壳机、6BH一20B型花生剥壳机、6BH一20型花生脱壳机等,其作业效率为人工作业效率的2O~60倍。
花生脱壳机就是通过高速旋转的机体,把花生外壳脱掉,而且保持花生完整的机器。
要求:
1、脱壳干净、生产率高,对有清选装置的脱壳机,还要求有较高的清洁度。
2、损失率低、破碎率小。
3、结构简单,使用可靠,调整方便,功率消耗少,有一定的通用性,能脱多种作物,以提高机具的利用率。
4、对花生(皮果)的要求。花生干湿适宜,太干则破碎率高,太湿则影响工作效率。农村储存的花生(皮果)一般较干,为使其干湿适宜可采用下列方法。
①、冬季脱壳,脱壳前用10千克左右的温水均匀喷洒在50千克皮果上,并用塑料薄膜覆盖10小时左右,然后再在阳光下晾晒1小时左右即可开始脱壳,其他季节用塑料薄膜覆盖的时间为6小时左右,其余相同。
②、可将较干的花生(皮果)浸在大水池内,浸后立即捞出并用塑料薄膜覆盖1天左右,再在阳光下晾晒,待干湿适宜后开始脱壳。
5、对电压的要求及工作场所的选择。单相电动机要正常工作,电压需达到其额定电压。农村一般一个村庄只有一个变压器,而户户又分散,加之所用电线及电路不很标准,致使离变压器较远的用户电压不足,因此,工作场所应选择离变压器较近的地方。
1.2 花生脱壳机的工作原理
花生脱壳机有机架、风扇、转子、单相电机、入料斗、震动筛、三角带轮及其传动三角带等组成。机具正常运转后,将花生定量、均匀、连续地投入进料斗,花生在转子的反复打击、摩擦、碰撞作用下,花生壳破碎。花生粒及破碎的花生壳在转子的旋转风压及打击下,通过筛板,这时,花生壳、粒受到旋转风扇的吹力作用,重量轻的花生壳被吹出机体外,花生粒通过风机的筛选达到清选的目的。
2. 花生剥壳机设计方案比较
花生剥壳的原理很多,因此产生了很多种不同的花生剥壳机械。花生剥壳部件是花生剥壳机的关键工作部件,剥壳部件的技术水平决定了机具作业刚花生仁破碎率、花生果一次剥净率及生产效率等重要的经济指标。在目前的生产销售中,花生仁破碎率是社会最为关心的主要指标。
为了降低破碎率而探讨新的剥壳原理,研制新式剥壳部件,便成为花生剥壳机械的重要研究课题。从六十年代初,开始在我国出现了封闭式纹杆滚筒,栅条凹板式花生剥壳机。自1983年以来,在已有的花生剥壳部件的研制基础上,我国又相继研制了多种不同结构型式的新式剥壳部件,其主要经济技术指标,特别是破壳率指标大有改善。
以下介绍一下我国上个世纪几种主要的花生剥壳原理
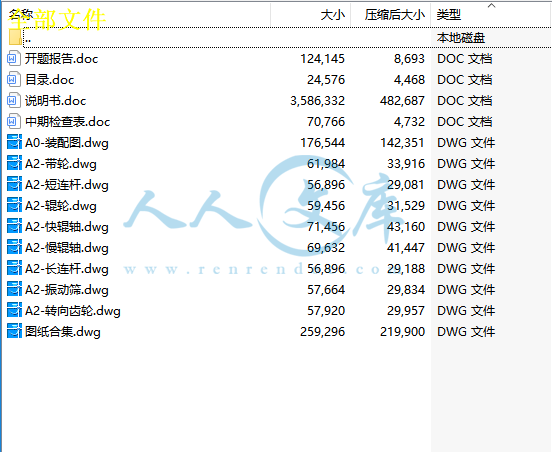

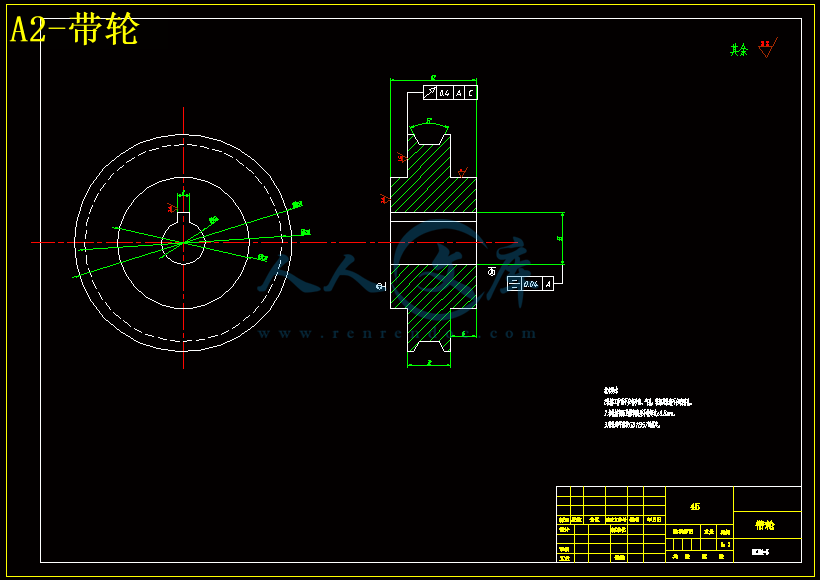
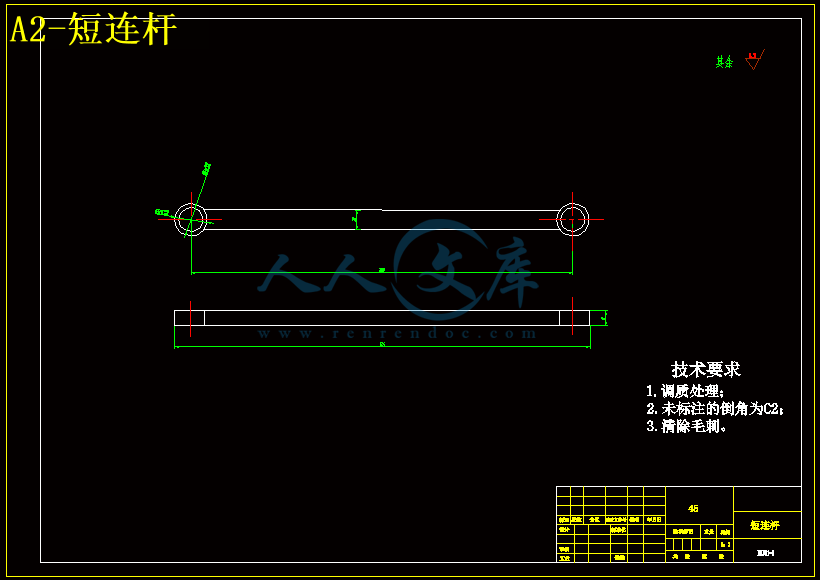







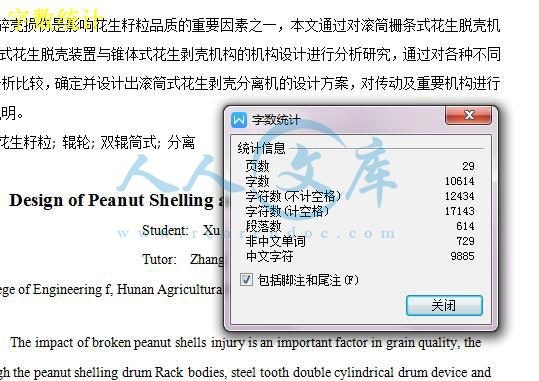