多层钢筋混凝土框架设计
102页 19000字数+说明书+外文翻译+8张CAD图纸【详情如下】
3楼盖.dwg
4 多层钢筋混凝土框架恒荷载内力计算.doc
4横向框架.dwg
5 多层钢筋混凝土框架活荷载内力计算(屋面布雪荷载).doc
5楼梯.dwg
6 多层钢筋混凝土框架活荷载内力计算(屋面布活荷载).doc
6基础布置.dwg
7基础详图.dwg
7多层钢筋混凝土框架 风荷载内力计算.doc
8 多层钢筋混凝土框架地震作用内力计算.doc
8梁平法图.dwg
9 多层钢筋混凝土框架内力组合.doc
内力组合表格
参考文献.doc
外文翻译--应用新型延性纤维增强聚合织物对混凝土梁的加固 中文版.doc
外文翻译--应用新型延性纤维增强聚合织物对混凝土梁的加固 英文版.pdf
屋盖、楼盖表格
截面设计表格
摘要.doc
目录.doc
致谢.doc
1 工程概况.doc
10 多层钢筋混凝土框架截面设计.doc
11 多层钢筋混凝土框架楼梯设计.doc
12 多层钢筋混凝土框架基础设计.doc
1结构布置&模板.dwg
2 多层钢筋混凝土框架屋盖、楼盖设计.doc
2屋盖.dwg
3 多层钢筋混凝土框架框架结构布置及计算简图.doc

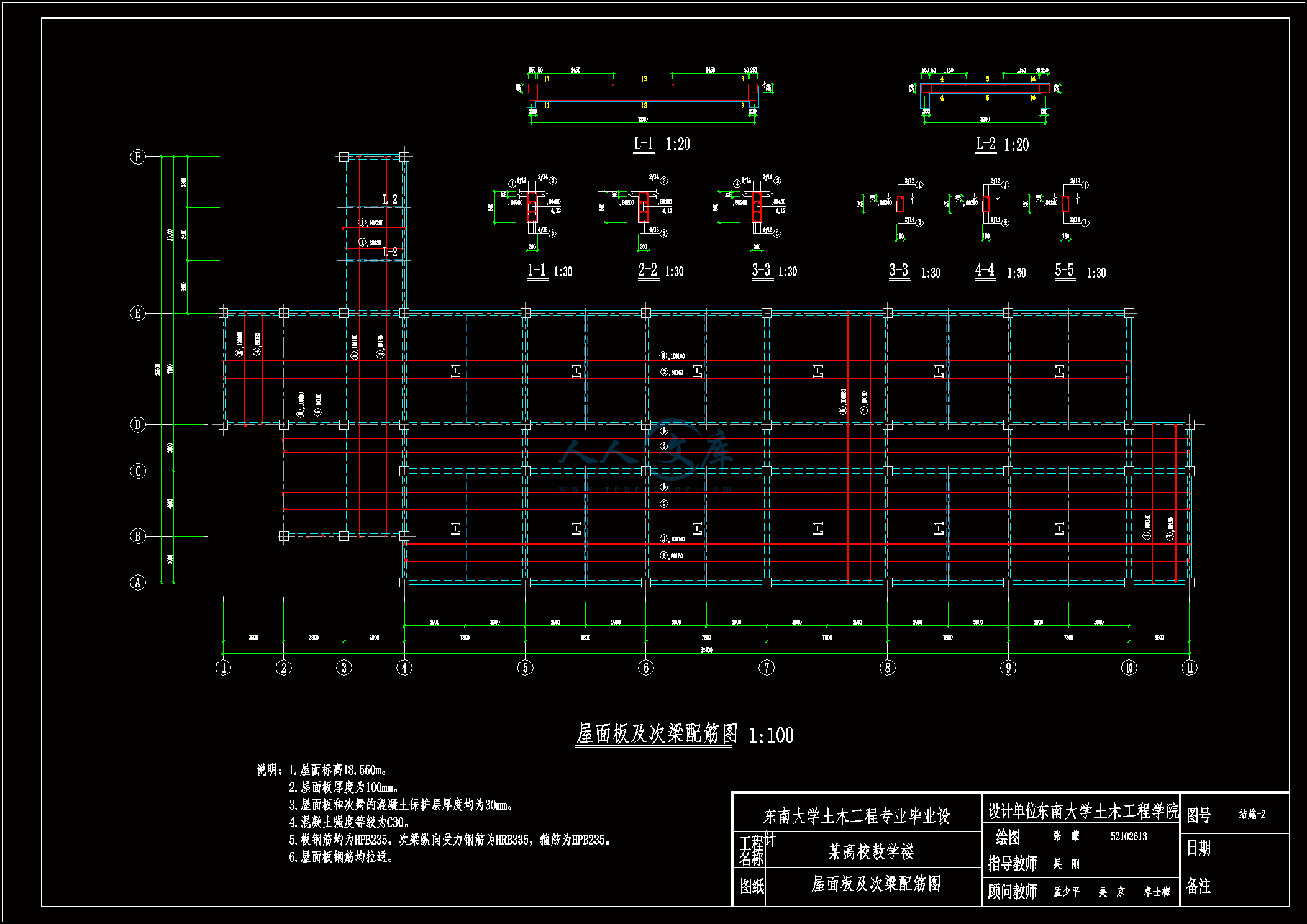
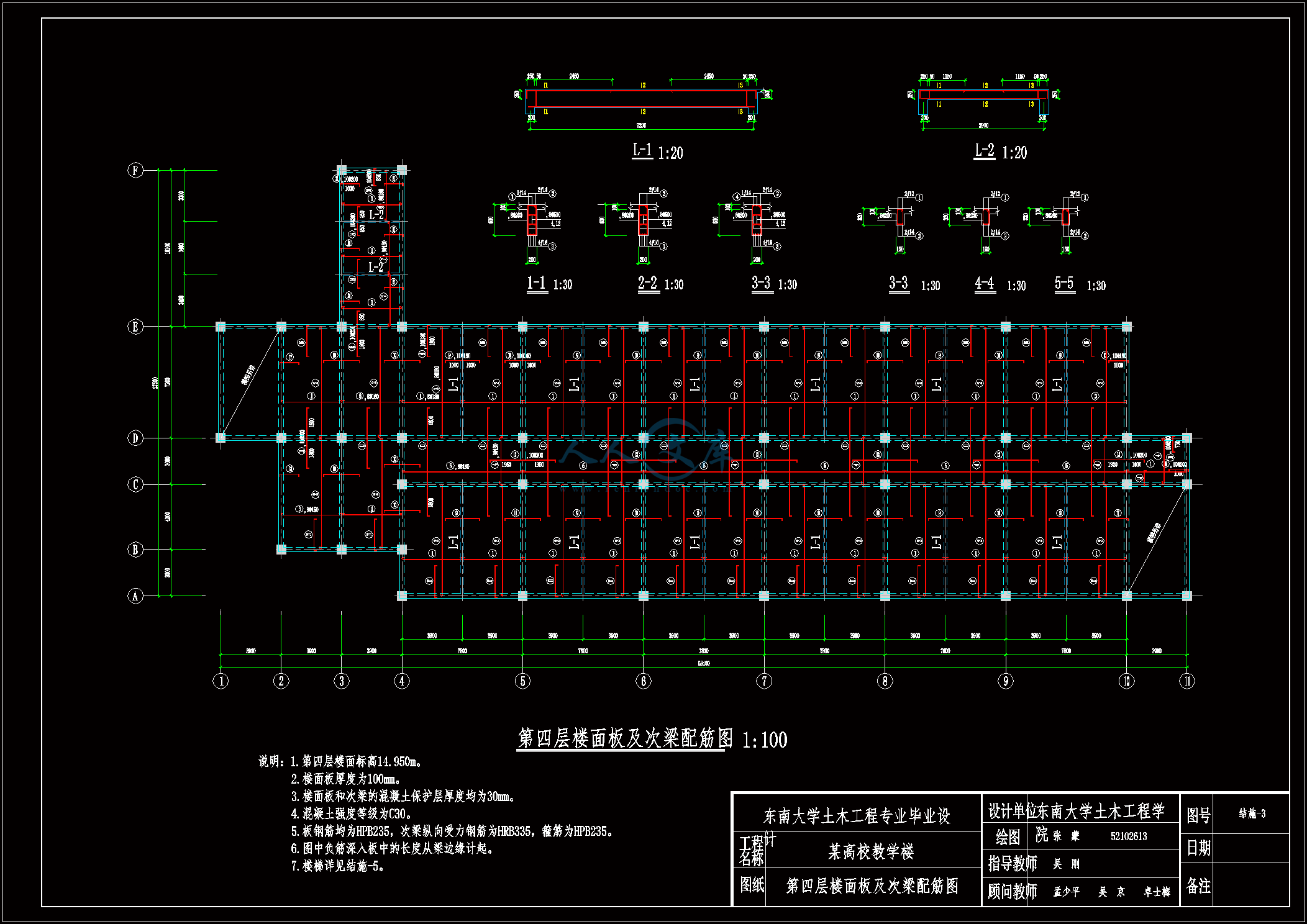
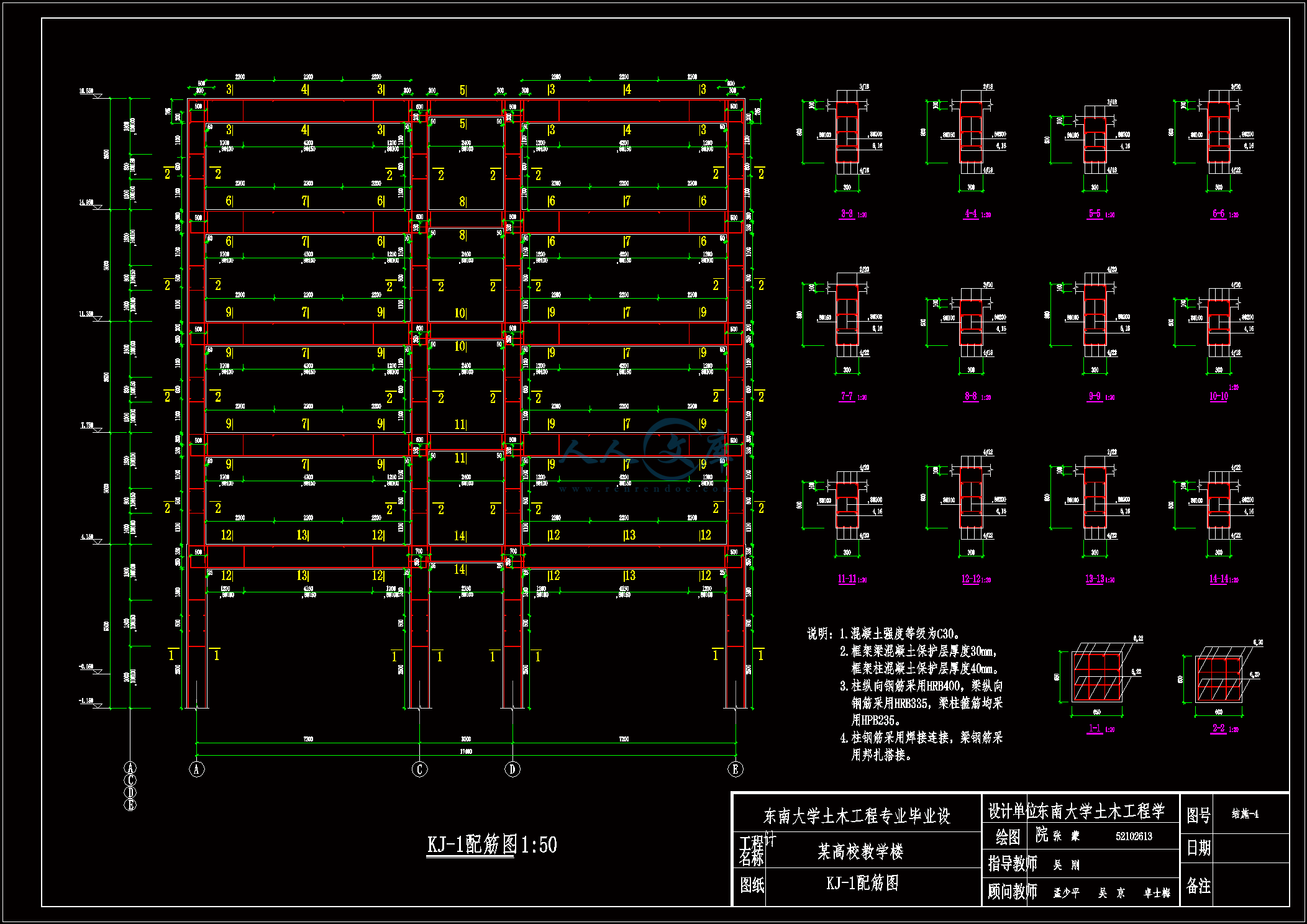
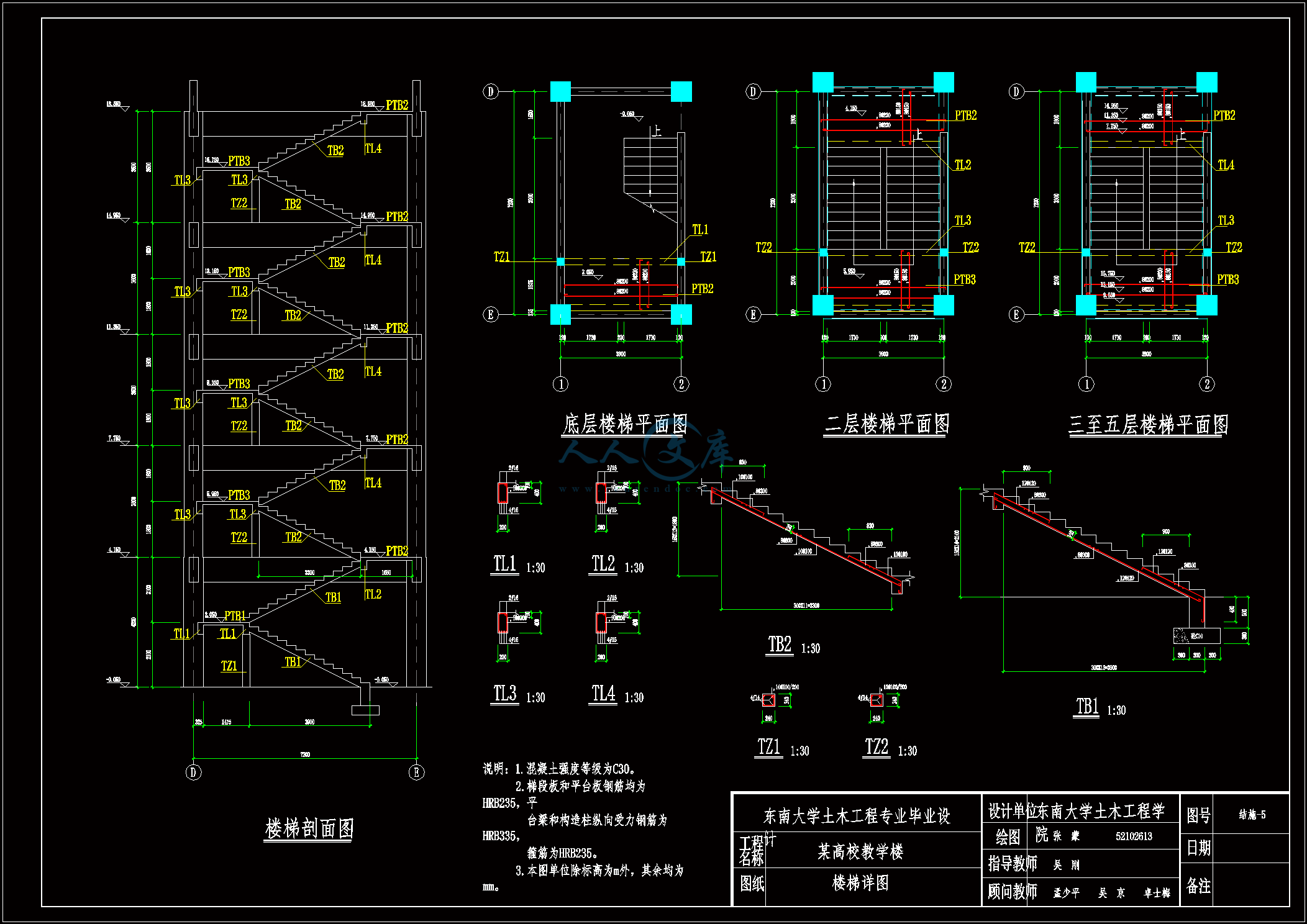
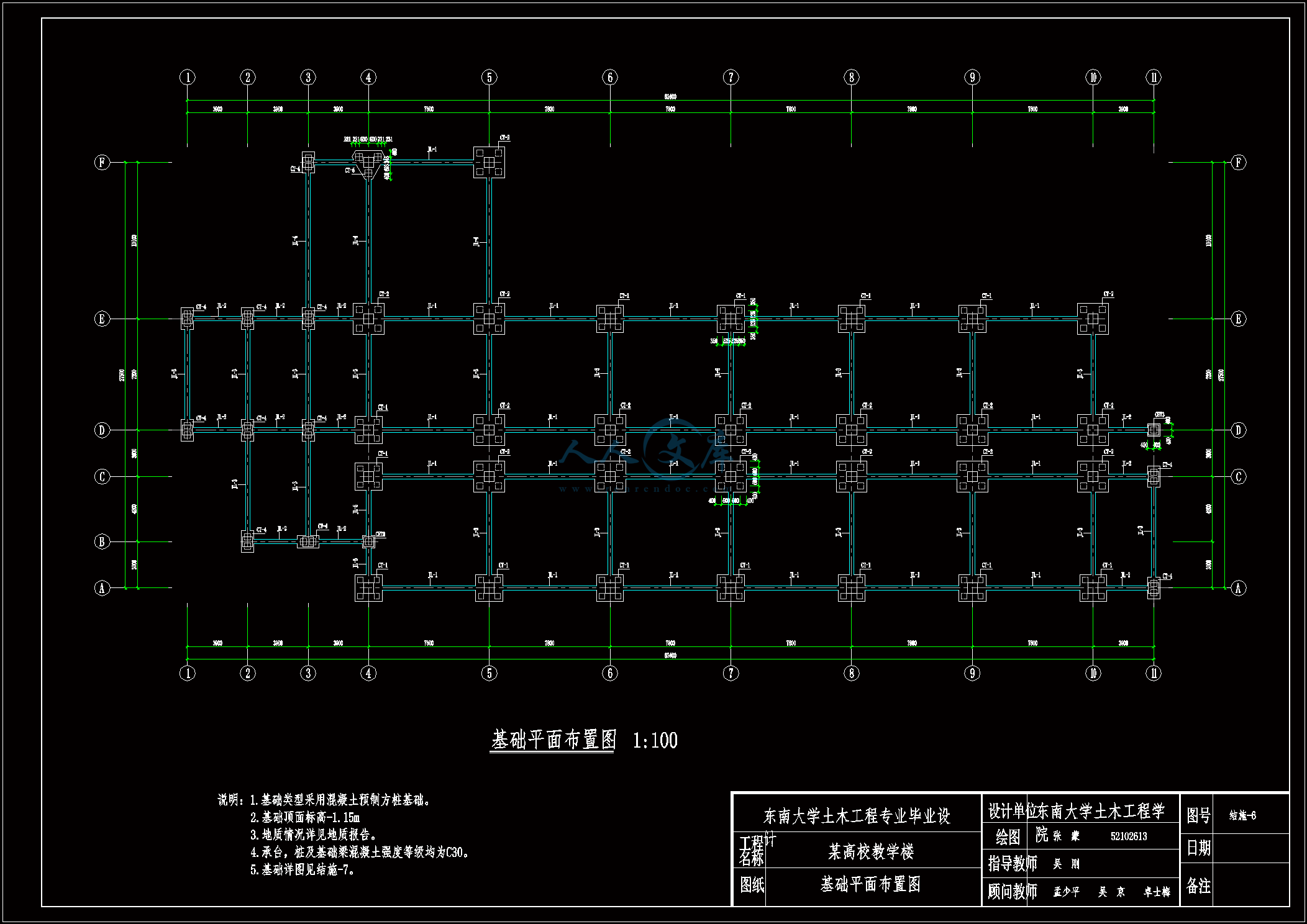
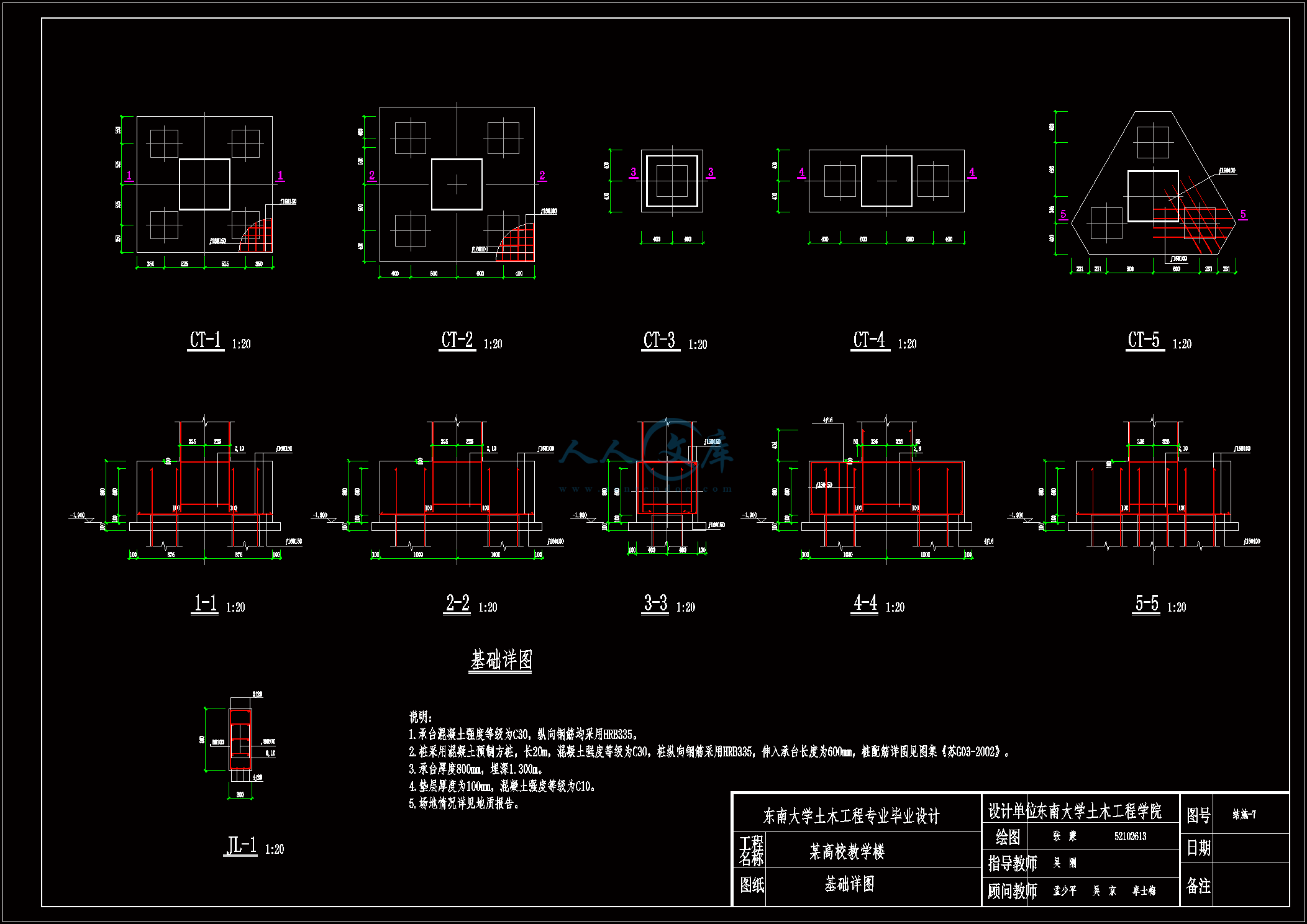
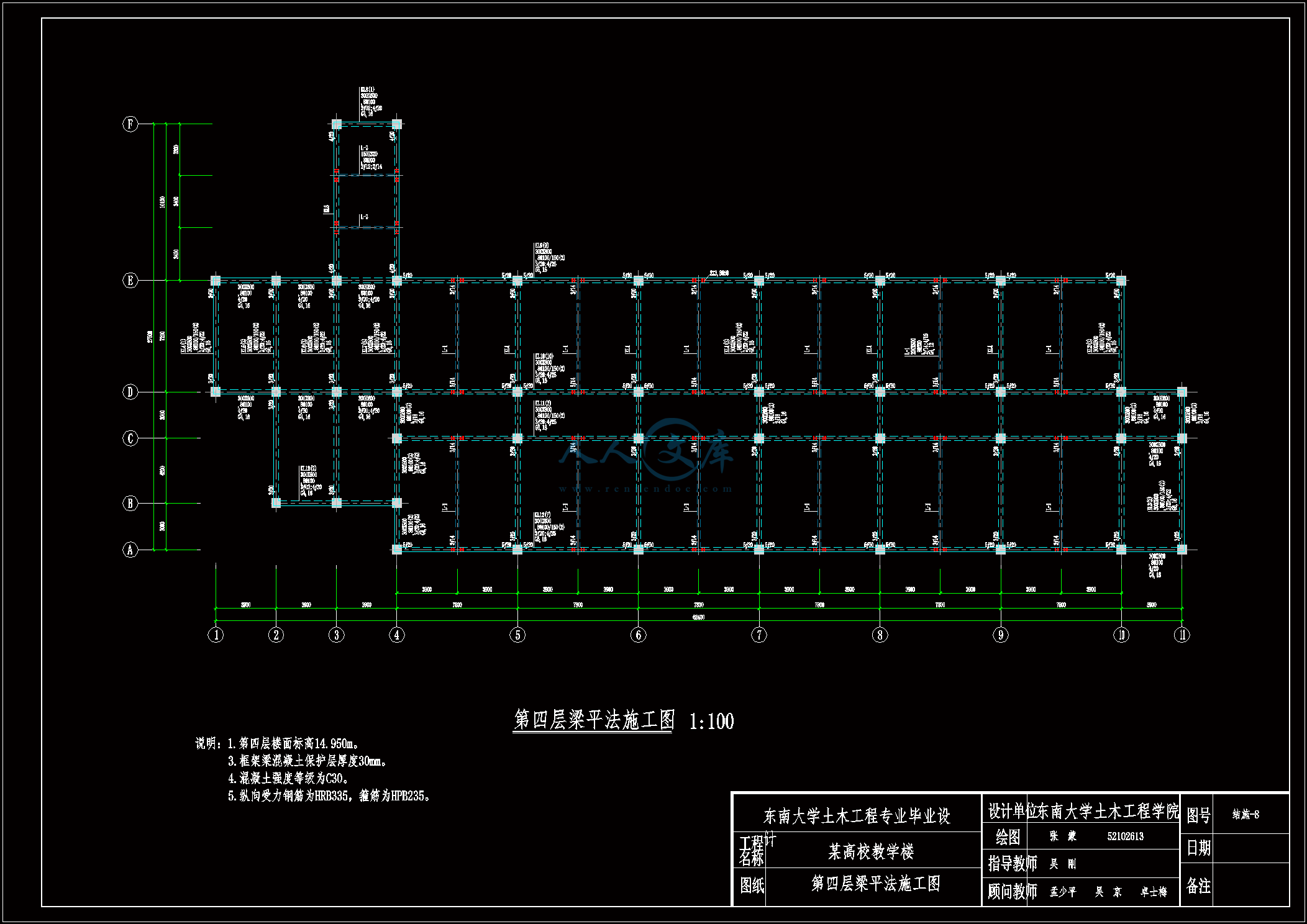
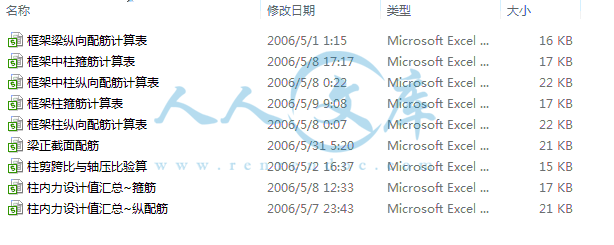
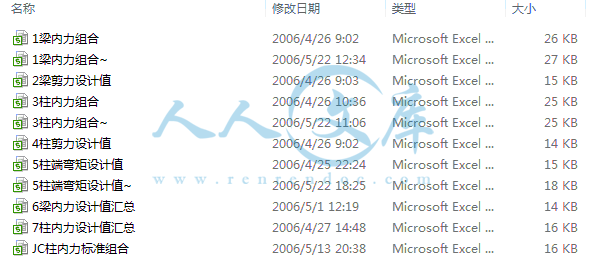

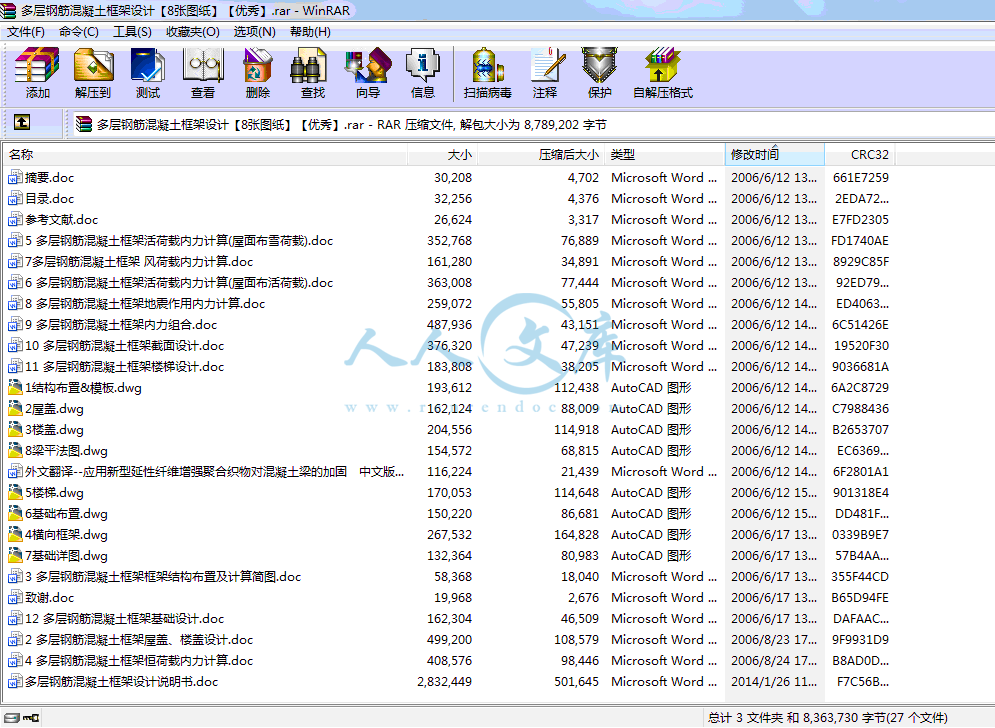
目 录
摘要…………………………………………………………………………………Ⅰ
一 工程概况…………………………………………………………………………1
二 屋盖、楼盖设计…………………………………………………………………2
(一)屋盖……………………………………………………………………………2
(二)楼盖……………………………………………………………………………10
三 框架结构布置及计算简图………………………………………………………19
(一)梁柱尺寸………………………………………………………………………19
(二)计算简图………………………………………………………………………19
四 恒荷载内力计算…………………………………………………………………21
(一)恒荷载计算……………………………………………………………………21
(二)恒荷载作用下内力计算………………………………………………………22
五 活荷载内力计算(屋面布雪荷载)……………………………………………33
(一)活荷载计算……………………………………………………………………33
(二)活荷载作用下内力计算………………………………………………………33
六 活荷载内力计算(屋面布活荷载)……………………………………………42
(一)活荷载计算……………………………………………………………………42
(二)活荷载作用下内力计算………………………………………………………42
七 风荷载内力计算…………………………………………………………………51
(一)风荷载计算……………………………………………………………………51
(二)内力计算………………………………………………………………………52
八 地震作用内力计算………………………………………………………………55
(一)重力荷载代表值计算…………………………………………………………55
(二)水平地震作用计算……………………………………………………………56
(三)一榀框架内力计算……………………………………………………………59
九 内力组合…………………………………………………………………………62
(一)梁内力组合……………………………………………………………………62
(二)柱内力组合……………………………………………………………………66
(三)内力设计值汇总………………………………………………………………70
十 截面设计…………………………………………………………………………72
(一)梁截面设计……………………………………………………………………72
(二)柱截面设计……………………………………………………………………75
十一 楼梯设计………………………………………………………………………81
底层楼梯设计………………………………………………………………81
其他层楼梯设计……………………………………………………………84
十二 基础设计………………………………………………………………………89
边柱基础……………………………………………………………………89
中柱基础……………………………………………………………………91
基础梁设计…………………………………………………………………93
致谢…………………………………………………………………………………95
参考文献……………………………………………………………………………96
多层钢筋混凝土框架结构设计
[摘要] 本工程是南京某高校教学楼。为多层钢筋混凝土框架结构。共五层,底层层高4.2米,其他层层高均为3.6米。建筑物总高度为18.6米。
本设计书包括如下部分:
工程概况;
屋盖、楼盖设计;
荷载计算;
框架结构的受力分析、计算和设计;
楼梯设计;
桩基础设计。
设计最终完成八张施工图。
[关键词] 钢筋混凝土,框架,结构设计一 工程概况
本工程为某高校教学楼。工程为五层现浇钢筋混凝土框架结构。屋面板顶面标高为18.6m。
工程所在地抗震设防烈度为7度,设计基本地震加速度为0.10g,设计地震分组为第一组,场地类别为Ⅱ类。
屋面做法:钢筋混凝土现浇板,20mm石灰砂浆抹底,20mm水泥砂浆找平,40~120厚(1%找坡)膨胀珍珠岩保温层,四层作法防水层(一毡二油上铺小石子)。
楼面做法:钢筋混凝土现浇板,20mm石灰砂浆抹底,20mm水泥砂浆找平,水磨石面层。
墙身做法:由普通砖砌筑而成,普通砖自重18kN/m3,厚度240mm。
门窗做法:门为木门,自重0.2 kN/m2,窗为钢窗玻璃窗,自重0.4 kN/m2。
风荷载标准值0.4kN/m2,雪荷载标准值0.65kN/m2。
活荷载:上人屋面均布活荷载标准值2.0kN/m2,楼面活荷载标准值2.0kN/m2。
本设计计算书包括屋盖、楼盖、框架主体结构、楼梯、基础等部分的计算和设计。
二 屋盖、楼盖设计
(一)屋盖
1.设计资料
1)屋面做法:钢筋混凝土现浇板,20mm石灰砂浆抹底,20mm水泥砂浆找平,40~120厚(1%找坡)膨胀珍珠岩保温层,四层作法防水层(一毡二油上铺小石子)
2)屋面荷载:均布活荷载标准值2kN/m2(上人屋面),雪荷载标准值为0.65kN/m2
3)材料:混凝土强度等级为C30;梁内受力纵筋为HRB335,其余为HPB235钢筋
三 框架结构布置及计算简图
(一)梁柱尺寸
1.梁高 hb=(1/12~1/8)lb
横向 hb=600~900mm,取800mm
纵向 hb=650~900mm,取800mm
过道 hb=250~375mm,考虑到次梁高度为600mm,也取为600mm
2.柱截面尺寸
本工程为现浇钢筋混凝土结构,7度设防,高度<30m,抗震等级为三级,取底层C6柱估算柱尺寸,根据经验荷载为15kN/m2:
N=15×7.8×(3.6+1.5)=2983.5kN
由轴压比限值得Ac≥==260795mm2
为安全起见,取底层柱截面尺寸为650mm×650mm,其他层为600mm×600mm
(二)计算简图(取轴线⑥处)
初步设计基础顶面离室外地面500mm,则底层层高为4.2+0.6+0.5=5.3m
框架结构计算简图
(三)梁柱线刚度
(其中E=3.0×104N/mm2)
AC、BC跨梁
i=2E××0.3×0.83/7.2=3.56×10-3E
BC跨梁