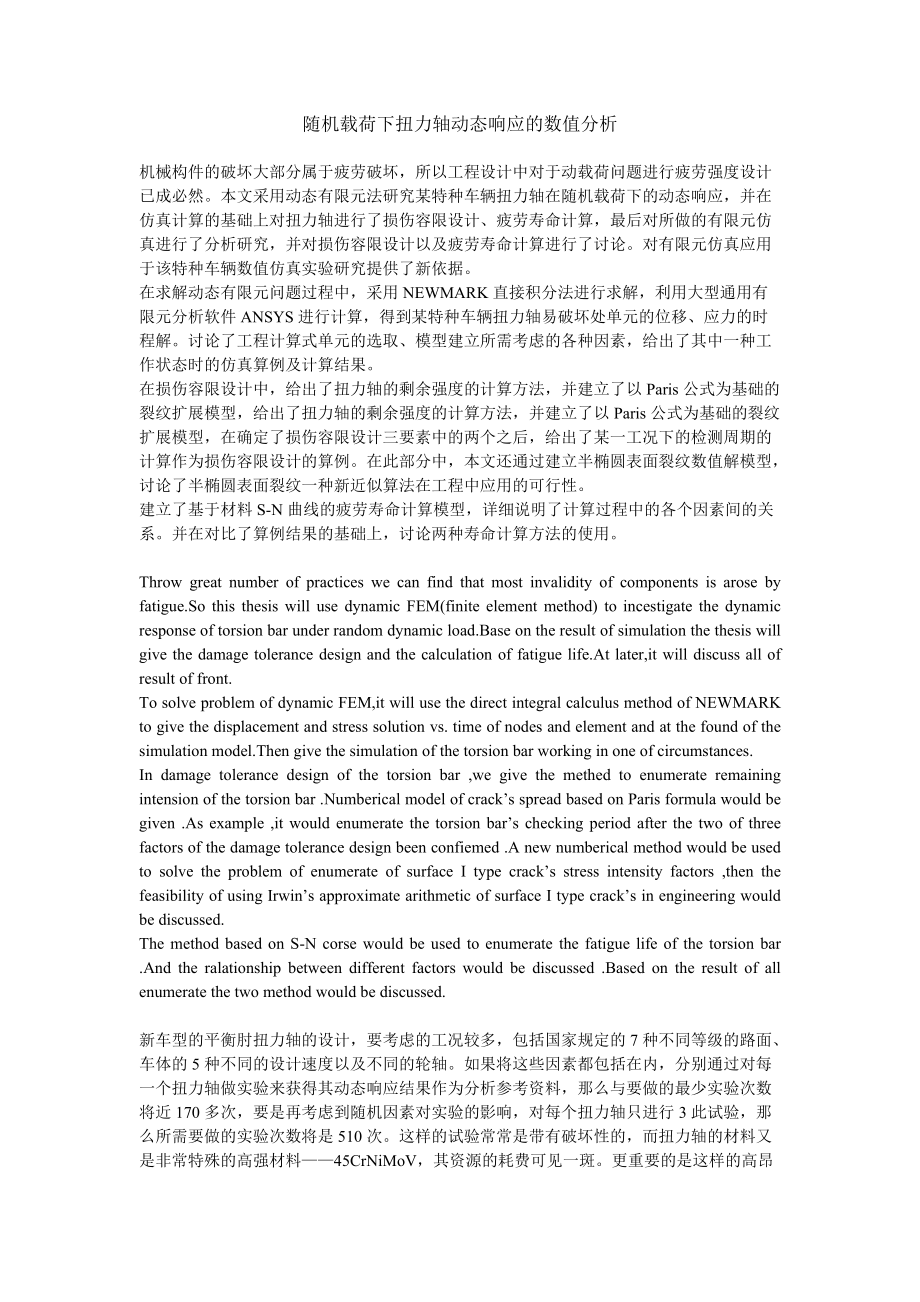



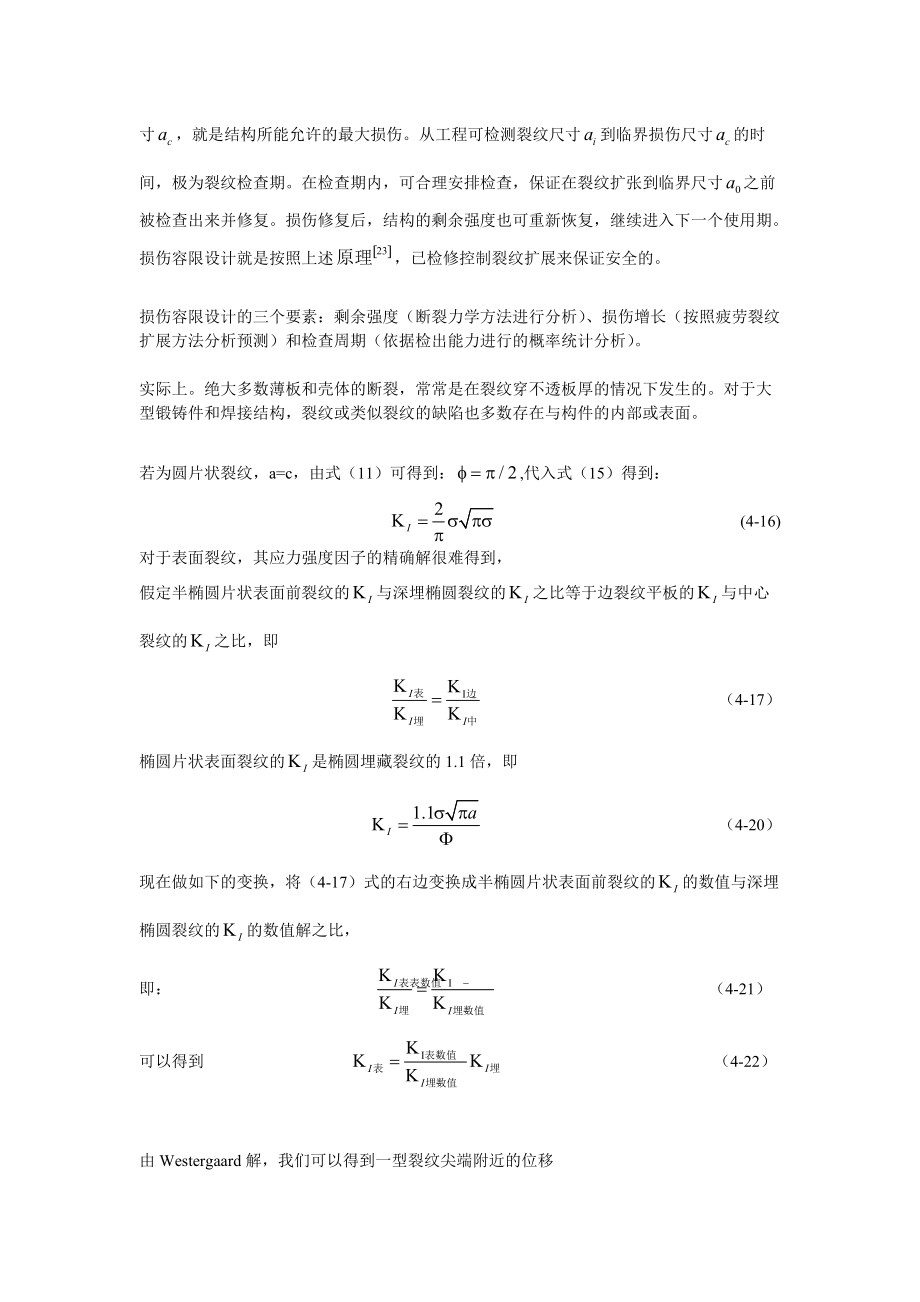
版权说明:本文档由用户提供并上传,收益归属内容提供方,若内容存在侵权,请进行举报或认领
文档简介
1、随机载荷下扭力轴动态响应的数值分析机械构件的破坏大部分属于疲劳破坏,所以工程设计中对于动载荷问题进行疲劳强度设计已成必然。本文采用动态有限元法研究某特种车辆扭力轴在随机载荷下的动态响应,并在仿真计算的基础上对扭力轴进行了损伤容限设计、疲劳寿命计算,最后对所做的有限元仿真进行了分析研究,并对损伤容限设计以及疲劳寿命计算进行了讨论。对有限元仿真应用于该特种车辆数值仿真实验研究提供了新依据。在求解动态有限元问题过程中,采用NEWMARK直接积分法进行求解,利用大型通用有限元分析软件ANSYS进行计算,得到某特种车辆扭力轴易破坏处单元的位移、应力的时程解。讨论了工程计算式单元的选取、模型建立所需考虑的
2、各种因素,给出了其中一种工作状态时的仿真算例及计算结果。在损伤容限设计中,给出了扭力轴的剩余强度的计算方法,并建立了以Paris公式为基础的裂纹扩展模型,给出了扭力轴的剩余强度的计算方法,并建立了以Paris公式为基础的裂纹扩展模型,在确定了损伤容限设计三要素中的两个之后,给出了某一工况下的检测周期的计算作为损伤容限设计的算例。在此部分中,本文还通过建立半椭圆表面裂纹数值解模型,讨论了半椭圆表面裂纹一种新近似算法在工程中应用的可行性。建立了基于材料S-N曲线的疲劳寿命计算模型,详细说明了计算过程中的各个因素间的关系。并在对比了算例结果的基础上,讨论两种寿命计算方法的使用。Throw great
3、 number of practices we can find that most invalidity of components is arose by fatigue.So this thesis will use dynamic FEM(finite element method) to incestigate the dynamic response of torsion bar under random dynamic load.Base on the result of simulation the thesis will give the damage tolerance d
4、esign and the calculation of fatigue life.At later,it will discuss all of result of front.To solve problem of dynamic FEM,it will use the direct integral calculus method of NEWMARK to give the displacement and stress solution vs. time of nodes and element and at the found of the simulation model.The
5、n give the simulation of the torsion bar working in one of circumstances.In damage tolerance design of the torsion bar ,we give the methed to enumerate remaining intension of the torsion bar .Numberical model of cracks spread based on Paris formula would be given .As example ,it would enumerate the
6、torsion bars checking period after the two of three factors of the damage tolerance design been confiemed .A new numberical method would be used to solve the problem of enumerate of surface I type cracks stress intensity factors ,then the feasibility of using Irwins approximate arithmetic of surface
7、 I type cracks in engineering would be discussed.The method based on S-N corse would be used to enumerate the fatigue life of the torsion bar .And the ralationship between different factors would be discussed .Based on the result of all enumerate the two method would be discussed.新车型的平衡肘扭力轴的设计,要考虑的工
8、况较多,包括国家规定的7种不同等级的路面、车体的5种不同的设计速度以及不同的轮轴。如果将这些因素都包括在内,分别通过对每一个扭力轴做实验来获得其动态响应结果作为分析参考资料,那么与要做的最少实验次数将近170多次,要是再考虑到随机因素对实验的影响,对每个扭力轴只进行3此试验,那么所需要做的实验次数将是510次。这样的试验常常是带有破坏性的,而扭力轴的材料又是非常特殊的高强材料45CrNiMoV,其资源的耗费可见一斑。更重要的是这样的高昂代价的实验数据不能用于其它型号的车体,由此可见,通过大量的实验来完成设计所需耗费的财力物力将是非常昂贵的。分析对象为某自行火炮平衡肘及扭力轴,分析内容为扭力轴在
9、动载荷下的响应及扭力轴的损伤容限分析计算、疲劳寿命分析。图3.4空缺图3.4为扭力轴的设计图,左端的齿轮花键固定在车体上,右端的齿轮花键固定在平衡肘上。随着产品的发展,一方面扭力轴的使用角度不断增大,所承受的负荷也就不断加重。扭力轴使用的最大角度为,承受的最大扭力矩多9000N.m,1992年开始研制的新扭力轴,其使用最大角度增至,所承受的最大扭力矩>10000N.m。另一方面扭力轴生产工艺相对比较落后,强化不足,固定端的花键向秆部过渡处过早发生疲劳断裂。这主要是由于花键与扭力轴的尺寸的过渡,应力出现集中,再加上过渡弧加工的表面精度的不够,似的裂纹多出现在花键与轴的连接处,扭力轴:材料为
10、:45CrNiMoV(45镉镍钼钒高强合金优质钢)热处理HB444-388(球痕直径d为2.9至3.1)硬度差不大于球痕直径0.1=1325Mpa,=1470Mpa虽然是高强材料,但是扭力轴在制作过程中增加了预扭工艺,测得材料的剪切模量模型按照统计原理的要求,以每百米为一个计算路程。不同的速度不同的路面将得到不同的载荷形式。即使相同的速度和路面,各平衡肘的载荷也不一样,下面以四级路面、四档速度(16.55m/s)为例,说明扭力肘的工作载荷情况:平衡轴扭力肘的载荷来源于如图3-1所示的多刚体动力学计算模型。轮子将地面对车体的作用力通过负重轮传递给扭力肘,经过前期的计算工作,得到了作用在扭力肘的负
11、重轮轴上的载荷,形式以一组随时间变化的集中力载荷(一系列时间间隔为0.005秒的一维数组)形式给出,作用于平衡肘的负重轮轴线上并垂直于轴线。将力分解为水平和垂直方向(可由图3-1中的坐标确定方向)后得到的是时间变化的载荷图谱如图3-4所示:平衡肘扭力轴的力学模型示意图,扭力轴与平衡肘连接的一端固定在套筒中,能自由的转动,另一端则固定在车体的另一侧,属固定约束。载荷施加在坐标图中坐标原点处。动态分析分为一阶和二阶系统分析。所谓的二阶系统,是指系统在时间上存在二阶状态。在结构分析中存在质量矩阵,它所对应的是位移的二阶导数(即加速度)。其方程为:在有限元中,求解这一类的动态问题主要有两种方法:前向差
12、时间积分(forward difference time intergration)法和纽马克时间积分法。前向差分法是一种显式方法;纽马克时间积分法是一种隐式方法,主要思路是把上述方程中自由度的导数项由相邻时间点的位移项代替。NEWMARK积分法实质上是线性加速度法的一种推广。它采用下列假设 (3-6) (3-7) 其中和是按积分精度和稳定性要求而决定的参数。当=1/2和=1/6时,(3-35)式和(3-36)式相应于线性加速度法,因为这是他们可以从下面时间间隔内线性假设的加速度表达式的积分得到 (3-8)其中0。Newmark方法原来是从平均加速度法这样一种无条件稳定积分方案而提出的,那时=
13、1/2和=1/4。内的加速度为 (3-9) 和中心差分法不同,Newark方法中时间的位移解答是通过满足时间的运动方程 (3-10)而得到的。为此首先从(3-36)式解得 (3-11)将上式代入(3-35)式,然后再一并带入(3-37)式,则得到从计算的公式的公式(3-12)至此,我们可将利用Newark方法逐步求解运动方程的算法步骤归结如下:1. 初始计算(1) 形成刚度矩阵K,质量矩阵M和阻尼矩阵C(2) 给定,和(3) 选择时间步长,参数和,并计算积分常数0.50,(4) 形成有效刚度矩阵:(5) 三角分解:2 .对于每一时间步长(1)计算式时间的有效荷载(2)求解时间的位移(3)计算时
14、间的加速度和速度 从Newark方法循环求解方程(3-41)式可见,有效刚度矩阵中包含了K,而一般情况下K总是非对角矩阵,因此在求解时,的求逆是必须的(当然,在线性分析中只需分解一次)。这是由于在到处(3-41)式,利用了t+t时刻的运动方程(3-39)式。这种算法称为隐式算法。当0.5,时,Newark方法是无条件稳定的,及时间步长t的大小可不影响解的稳定性。此时t的选取主要是根据解的精度确定。将原有的载荷进行适当的处理,去掉频率过高的震荡,并采用适当的时间步长。得到加在四号负重轮上的载荷有如图3.9的形式(四速、四级路面时的载荷)。图3.11为某一时刻在扭力轴的轴向剖切拉应图,从图中可以看
15、到,最大拉应力出现在花键于扭力轴过度的扭力轴的连接部,符合圆轴扭转应力分布规律,表面拉应力最大。图3.12是某一时刻扭力轴垂直于轴向的平面剖且拉应力分布图,基本是轴对称的分布,损伤容限设计,其方法首先假设结构中存在一个尺寸为的初始缺陷(的大小通常由制造质量,检测能力及实际使用经验等因素综合考虑确定),然后选择韧性较好的材料制造,保证这一结构在正常工作载荷作用下,损伤时缓慢增长的。在使用过程中,随着损伤(以裂纹尺寸表示)的增长,受损构件的剩余强度不断降低。为了保证安全,结构的剩余强度必须大于最大工作应力,故由剩余强度曲线和最大应力水平线的交点对应确定临界损伤尺寸,就是结构所能允许的最大损伤。从工
16、程可检测裂纹尺寸到临界损伤尺寸的时间,极为裂纹检查期。在检查期内,可合理安排检查,保证在裂纹扩张到临界尺寸之前被检查出来并修复。损伤修复后,结构的剩余强度也可重新恢复,继续进入下一个使用期。损伤容限设计就是按照上述,已检修控制裂纹扩展来保证安全的。损伤容限设计的三个要素:剩余强度(断裂力学方法进行分析)、损伤增长(按照疲劳裂纹扩展方法分析预测)和检查周期(依据检出能力进行的概率统计分析)。实际上。绝大多数薄板和壳体的断裂,常常是在裂纹穿不透板厚的情况下发生的。对于大型锻铸件和焊接结构,裂纹或类似裂纹的缺陷也多数存在与构件的内部或表面。若为圆片状裂纹,a=c,由式(11)可得到:,代入式(15)
17、得到: (4-16)对于表面裂纹,其应力强度因子的精确解很难得到,假定半椭圆片状表面前裂纹的与深埋椭圆裂纹的之比等于边裂纹平板的与中心裂纹的之比,即 (4-17)椭圆片状表面裂纹的是椭圆埋藏裂纹的1.1倍,即 (4-20)现在做如下的变换,将(4-17)式的右边变换成半椭圆片状表面前裂纹的的数值与深埋椭圆裂纹的的数值解之比,即: (4-21)可以得到 (4-22)由Westergaard解,我们可以得到一型裂纹尖端附近的位移 (I=1,2) (4-23)用时的裂纹张开位移值求,因为裂纹的张开位移比较显著,可以得到较为准确的近似值。此时 (4-24)在裂纹断面取不同的r值算出位移,代入式(4-2
18、4)得到对应的值后,在r很小的范围内,曲线才近似为一直线,此直线与纵坐标的焦点就是所要求的值。45CrNiMoV的断裂韧性的确定本文仅仅将根据五=研究所陈福态、张永信、等人的,保守的确定45CrNiMoV的动态断裂韧性。根据实验研究得到随(应力强度因子随时间的变化率)的增加而略有增加,随后有一个凹形趋势,而后显著上升,如图4.4所示图4.4空缺去最不利的作为45CrNiMoV的动态断裂韧性。即再由公式(4-17)推导临界裂纹尺寸的表达公式导出: (4-25)可以看到,在已经确定后,由、决定。以第三章有限元计算结果为例,在确定四级路面、四档速度行驶下的临界裂纹尺寸。从结果中找出最大载荷=421.
19、725Mpa与一同带入(4-20)得到: (4-26)裂纹只有在张开的情况下才能扩展,压缩载荷的作用将是裂纹闭合。因此应力循环的负应力部分对裂纹扩展无贡献,股疲劳裂纹扩展控制参量应力强度因子幅度定义为: R>0 (4-28) R<0 (4-28) 图4-3可以看出,由曲线可以分为低、中、高速率三个区域。1区:当小于时,可以认为裂纹不发生扩展。是反映疲劳裂纹是否扩展的重要参数,有实验得到。2区:是中速裂纹扩展区。大量的实验研究表明:中速率区内,曲线有良好的对数线性关系。3区:高速率区,裂纹扩展快,寿命短。其对裂纹寿命的贡献通常可以不考虑。在这一区域内,裂纹速率迅速的增大,裂纹尺寸迅速
20、的增加,断裂发生。由于本次分析中的模型的工作设计载荷变幅与2区相符,所以取曲线的关系表达式为 (4-29)上式即为著名的Paris公式的指数形式,其中C和m为材料的性能参数,描述了材料疲劳裂纹扩展性能,由试验给出。Paris公式的对数表达形式 (4-30)利用对数表达形式,可以做实验数据的最小二乘线性,即可确定材料参数C、m。对(4-29)积分,得到载荷幅载下的Paris公式积分表达式: (4-31)进而得到 , m2时 (4-32) ,m=2时 (4-33)其中初始裂纹长度。上述两式(4-32)和(4-33)给出恒载荷下疲劳裂纹扩展寿命估算的基本方程。用四档、四级路面对结果数值进行统计,得到
21、车辆每百米出现的不同数量记得及出现的次数,再用Miner累积损伤理论估计算出各量级对于损伤的贡献度。就可以得到车辆行驶每百米的裂纹扩展量。从而确定车辆的设计安全行驶路程,以完成损伤容限设计。结果的统计如下表所示:循环序号(Mpa)次数1202.053320.69912169.939328.5511346.395306.82314119.094335.1551560.335337.8481695.966329.48317100.369329.4831873.173339.88919144.754341.915110181.684321.253111124.937338.9031表4.5结果的统计
22、()现以高强材料常用的C、m值、3,并假设初始裂纹尺寸(一般由检测能力决定)为0.5mm,a/c=0.2。将这几个常数带入到(4-32)中 (单位取Mpa)将表4-5的统计计算结果代入上式,得到结果列于表4-6:循环序号(Mpa)可循环次数(次)损伤度1202.0532459731/2459732169.9394134331/413433346.395203175411/203175414119.09412011991/1201199560.33592379731/9237973695.96622957911/22957917100.36920067151/2006715873.1735178
23、8351/51788359144.7546689481/66894810181.6843383251/33832511124.93710404261/1040426百米累积损伤1.4013e-5安全循环次数71362安全行驶路程7136.2km表4.6 损伤度累积结果列表中可以看到,小于60Mpa时对损伤的影响度小于千万分之一,基本可以不考虑。所以在数值仿真中可以对一些微小的震荡加以简化,只考虑主要的载荷波形。简化的程度应该是材料的C、m而定,即在确定C、m的基础之上,通过(4-25)(4-26)的计算找到使N大于次循环的应力幅值,再将载荷中的相应的微小波动予以简化。在某点或某些点承受扰动应力
24、,且在足够多的循环扰动作用之后形成裂纹或完全断裂的材料中所发生的局部的、永久结构变化的发展过程,称为疲劳。循环系数R=-1时,对称横幅循环载荷控制下,试验给出的应力-寿命关系,用曲线表达,是对材料的基本疲劳性能曲线。描述材料S-N的最常用的形式是幂函数形式,即: (5-1)M与C是与材料、应力比、加载方式等有关的参数。两边取对数,有: (5-2)式中,材料参数A=lgC/m。(5-2)是表示应力S与寿命N之间有对数线性关系,这一点,可有观察着试验数据S、N在双对数图上是否线性而确定。由S-N曲线确定的,对应于寿命N的应力,成为寿命N的疲劳强度,记作,寿命N趋于无穷大时所对应的应力S的极限值,称
25、为材料的疲劳极限。特别的,R=-1的对称循环下的疲劳极限,记作,简记为。由于疲劳极限是由试验确定的,试验又不可能一直做下去,在许多实验研究的基础上,所谓的“无穷大”一般定义为:钢材次循环;焊接件,次循环;有色金属,次循环。满足S<的设计,即无限寿命设计。若疲劳极限和材料极限强度为已知,S-N曲线可用下述方法做偏于保守的估计:S-N曲线用双对数线性关系的幂函数形式(5-1)式表达,寿命N=1时,即单调载荷作用下,时间在极限强度下破坏或屈服。考虑到S-N曲线描述的是长寿命疲劳,不宜用于以下,故通常假定时有对于金属材料,疲劳极限所对应的循环次数一般为次,考虑到估计时的误差,做如下偏于保守的假定
26、:时, (5-3)式中,反应不同载荷作用形式的系数k,按照前述各式选取,即弯曲时,k取0.5;拉压时,k取0.35;扭转时,k取0.29。由S-N曲线可写出 (5-4)根据上述二式可求得参数如下:m=3/lg(0.9/k); (5-5)如此估计的S-N曲线,之应用于寿命为之间的疲劳强度估计,不宜外推。对于任意给定寿命的N,其关系曲线还可以画成如图5.4所示无量纲形式,这种图称为Haigh图。途中给予出了金属材料时的关系,分加紧用疲劳极限和进行了一化。显然,当=0时,就是R=-1时的疲劳极限,=1;当=0时,荷载成为静载,在极限强度下破坏,有或图5.4【空缺】等寿命条件下的关系可以表达为这是图中
27、的抛物线,称为Gerber曲线,数据点基本上在此抛物线附件。图中的直线,即 (5-6)上式称为Goodman直线,所有的实验点基本都在这一直线的上方。直线形式简单,且在给定寿命下,由此作出的关系估计是偏于保守,故在工程实际中常用。对于其他给定的N,只需将上述换成即可。,后者即使有基本S-N曲线给出的、N循环寿命所对应的疲劳强度。利用上述关系,已知材料的极限强强度和基本S-N曲线,即可估计出在不同应力比或平均应力下的疲劳性能。Miner线性累积损伤理论构件在某恒幅应力水平S下,循环至破坏寿命N,则可以定义其再经过n次循环式的损伤为:D=n/N构件在应力水平作用下,经受次循环的损伤为。若在k个应力水平下,各经受次循环,则可定义其总损伤为 (5-7)破坏准则为 (5-8)其中,是在作用下的循
温馨提示
- 1. 本站所有资源如无特殊说明,都需要本地电脑安装OFFICE2007和PDF阅读器。图纸软件为CAD,CAXA,PROE,UG,SolidWorks等.压缩文件请下载最新的WinRAR软件解压。
- 2. 本站的文档不包含任何第三方提供的附件图纸等,如果需要附件,请联系上传者。文件的所有权益归上传用户所有。
- 3. 本站RAR压缩包中若带图纸,网页内容里面会有图纸预览,若没有图纸预览就没有图纸。
- 4. 未经权益所有人同意不得将文件中的内容挪作商业或盈利用途。
- 5. 人人文库网仅提供信息存储空间,仅对用户上传内容的表现方式做保护处理,对用户上传分享的文档内容本身不做任何修改或编辑,并不能对任何下载内容负责。
- 6. 下载文件中如有侵权或不适当内容,请与我们联系,我们立即纠正。
- 7. 本站不保证下载资源的准确性、安全性和完整性, 同时也不承担用户因使用这些下载资源对自己和他人造成任何形式的伤害或损失。
评论
0/150
提交评论